
The “mangineer” and people development
FEATURE – Sometimes you just need to get creative: as part of its flexible manufacturing model, Esquel introduced a new role on its shop floor – the “mangineer”.
Words: Dr. Marcus Chao, President, Lean Enterprise China
Over the past couple of decades, global textile companies have faced a dilemma. On the one hand, they can automate operations to mass-produce tons of standard yarns for general purposes; on the other, they can establish a flexible manufacturing system to meet increasing customer needs for special yarns to be produced in low volumes by mixing various raw and colored fibers.
Determined to meet the needs of both markets, Esquel made the strategic decision of establishing its Esquel Specialty Spinning (ESS) operation. They used an automated process in one factory to produce standard yarns in large quantities and a semi-automated flexible manufacturing process for specialty yarns at another site.
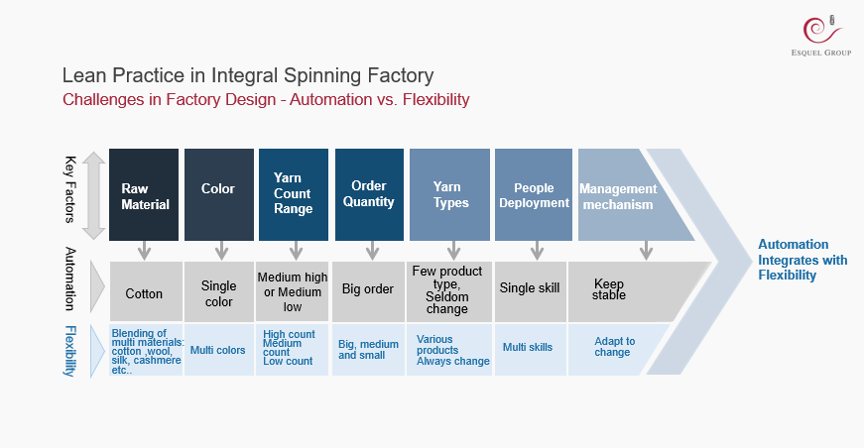
The problem for ESS was to find a cost-effective and flexible manufacturing process to produce specialty yarns.
The answer was a flexible manufacturing model based on three key elements: automated equipment, decentralized management, and a team of “mangineers” responsible for various tasks on the shop floor. The creative figure of the mangineer combines engineering capability with floor management skills to manage routine, every-day tasks as well as condition-triggered, contingent ones.
A new management model was required to carry out the strategy through organizational and people development.
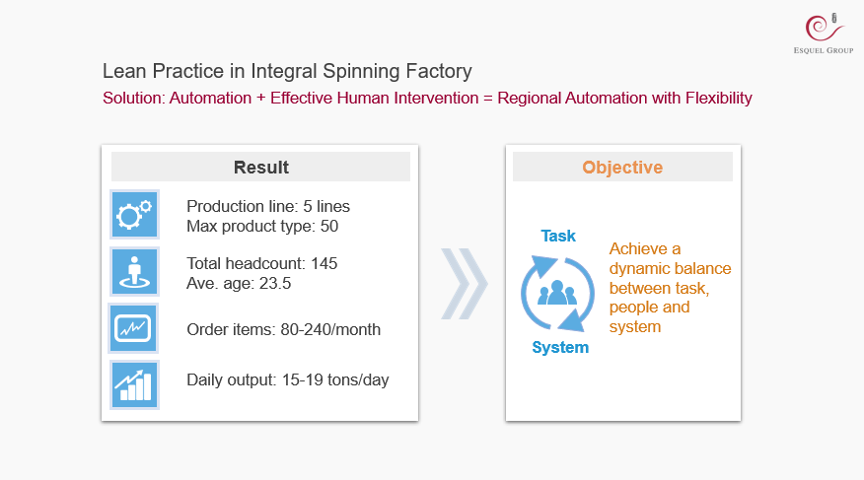
ESS hired 60 engineering college trainees to launch the “Mangineer training program” in 2018 at one of its old Guilin, China factories. The group of trainees went through a one-year classroom-based and hands-on training that entailed rotating through different functions and roles to develop various skills (i.e. planning, processing, production, quality and management, etc).
They were also required to work on the manufacturing floor to learn about equipment handling and maintenance, essential technical skills and management skills for different operations. Their mission is to achieve a dynamic and optimized balance of tasks, people, and system to manage the work in their assigned zones. For this innovative process, ESS harnessed the power of Lean Thinking.
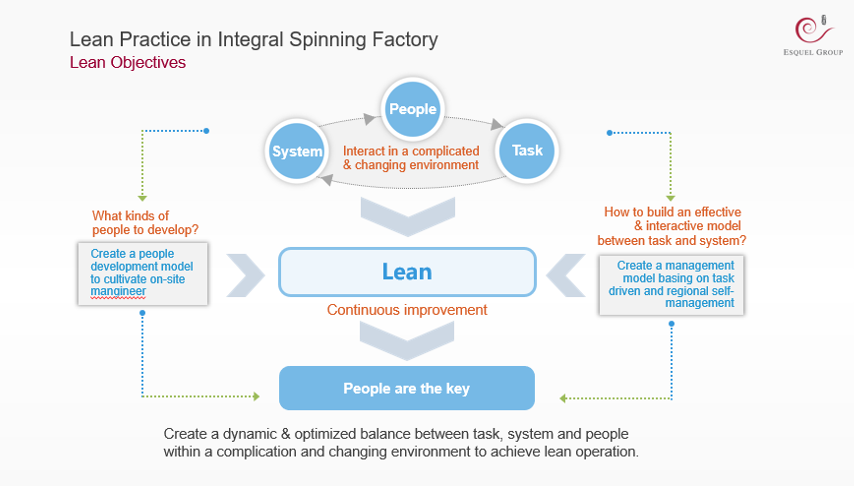
After one year of training, the group of trainees reached T2 level (T6 being the highest ranking). In 2019, the mangineers were deployed at the ESS’s new Integral spinning factory in Guilin, consisting of two stories with four zones each, all operating over three shifts. Between four and six mangineers were assigned to each zone, depending on the tasks that need to be completed. Day shifts tend to be busier with production work, while night shifts typically see more maintenance.
Compared with the old operation, the flexible manufacturing model only required a quarter of the people to carry out the same amount of work. For example, a changeover of product type that previously entailed 10 steps and took 59 minutes with multiple heads now required only four steps, 25 minutes and one mangineer. That’s how impactful the new decentralized management model was!
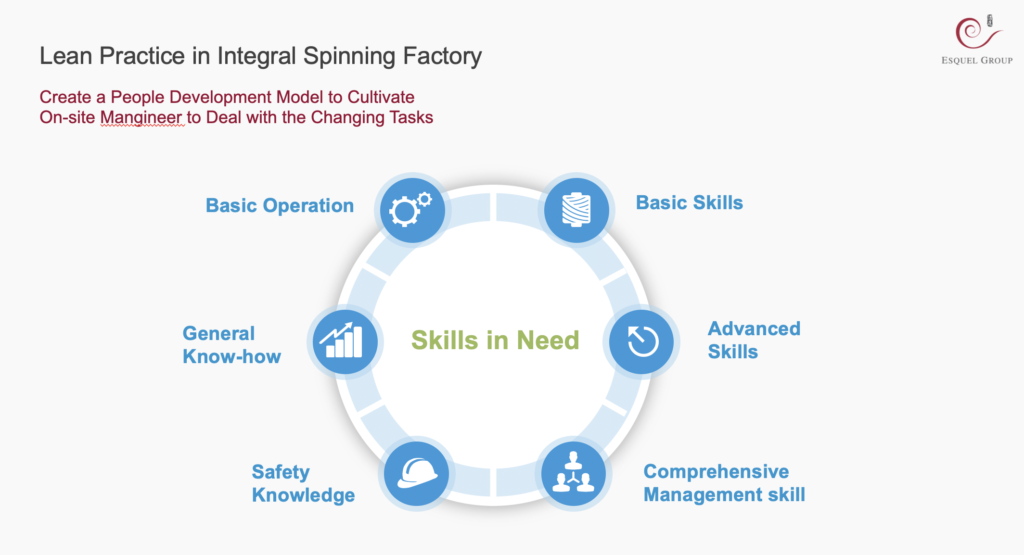
The decentralized management model was coupled with a task management software system that centrally assigned mangineers to different tasks on the shop floor based on order size, forecast, task urgency, skills, and so on. Whenever a complicated situation occurred, the system quickly dispatched mangineers to the site where support was needed based on their workload, location, and capabilities. The standard training enabled mangineers to flexibly work as a team to support each other and accomplish tasks within a required timeframe.
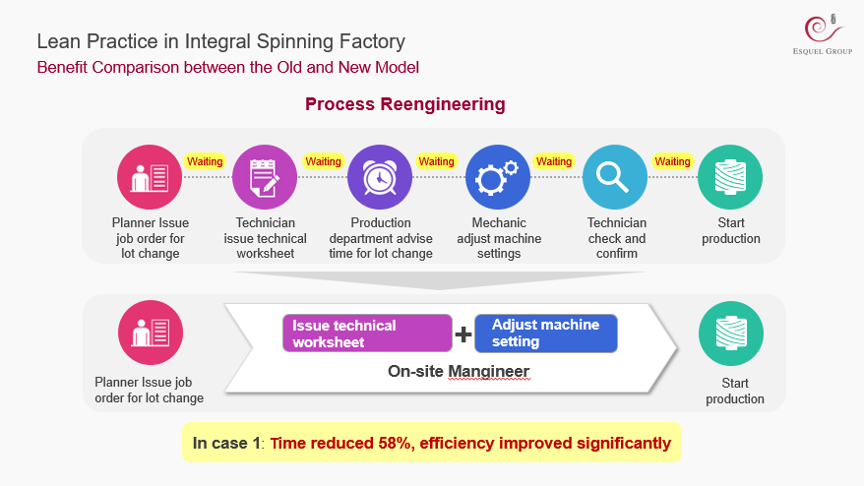
The overall benefits of this model can be summarized by looking at three KPIs:
- Output saw a 329% increase (from 30 kg/person/day to 130 kg);
- 74% less workers are needed per 10,000 spindles (from 146 to 38), showing opportunities for a more efficient use of resources;
- The time to reach T3 skill level was cut by 70% (from 5 years to 1.5 years).
The initial success boosted the confidence of the Esquel management team, who decided to retain a team of 150 mangineers at various levels. A training program for mangineers was set up, with 188 elements covering safety, operations, general know-how, basic and advanced technical skills, and comprehensive management. With the training program in place, the ESS team was keen to develop an assessment process and career advancement plans. Overall, it took four years to fulfill the requirements from T1 to T6 depending on the individual’s background and passion for learning.
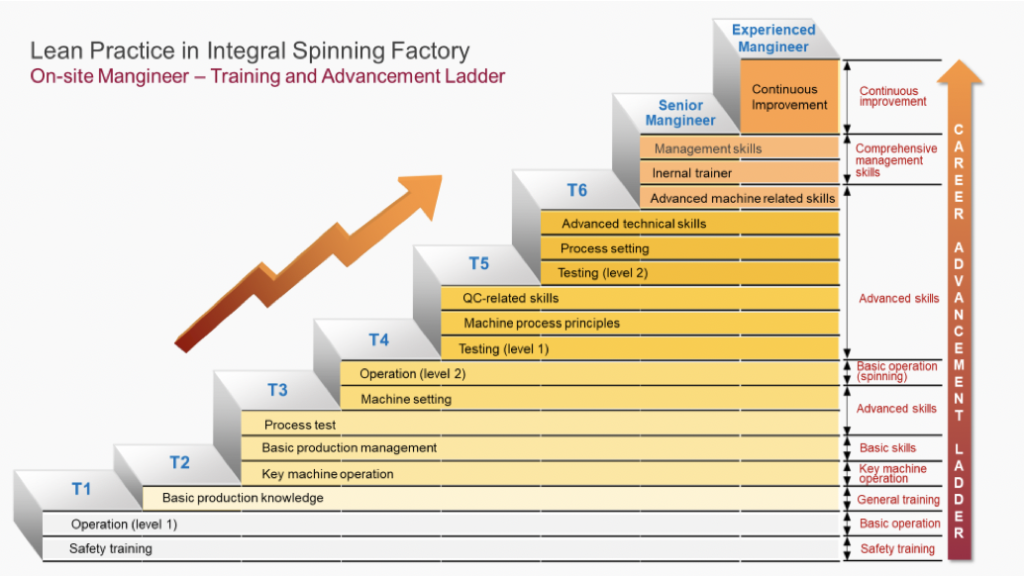
After three years of practice, 10% of the mangineers were promoted to different technical and managerial positions at ESS, but also in other business units and at headquarters. The turnover rate was less than 5%. The feedback the mangineers shared mentioned that the training was challenging but that the opportunities for career advancement were appreciated.
By balancing process improvement and people development, this experiment enabled Esquel to acquire additional high-variety and low-volume yarn orders to generate revenue.
The approach the company adopted echoes the one in the Lean Transformation Framework (LTF), which teaches us that a company can only achieve its vision and goal by working on both processes and people – the two pillars of the LTF house. Without the innovative flexible shop floor management model deployed at ESS, the mangineers won’t be able to demonstrate their power; in the same way, a shop floor with no mangineers won’t deliver the necessary results. People and processes are intertwined and drive continuous improvement together.
A few weeks ago, Planet Lean published another article of mine on the transformation in Esquel’s garment manufacturing operations. Both in that story and in this one, the message to the textile and apparel industry is clear: Lean Thinking provides a lot of opportunities to improve and become more competitive. You just need to follow Esquel’s example!
THE AUTHOR
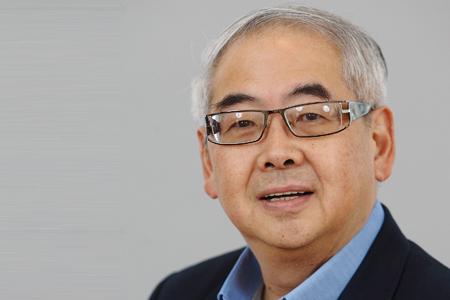
Read more
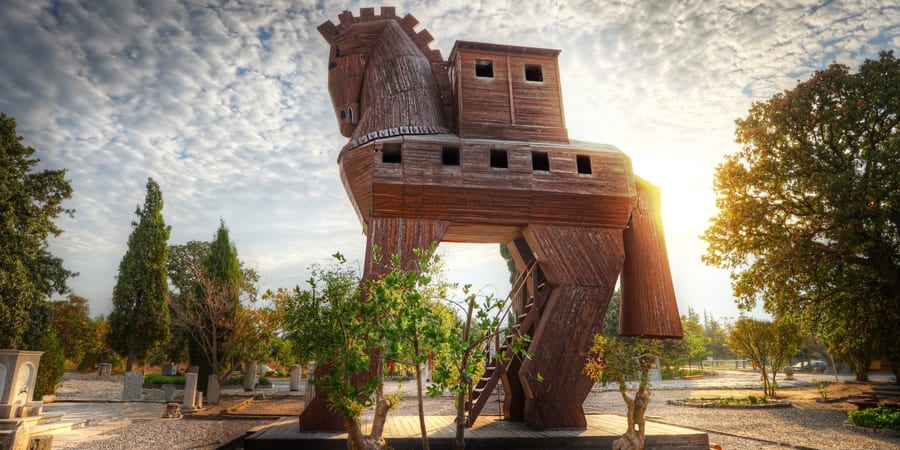
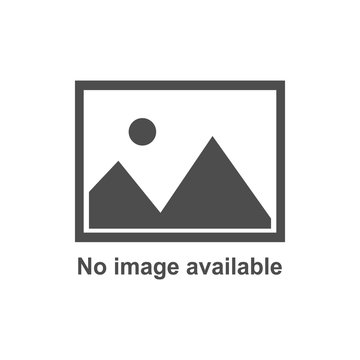
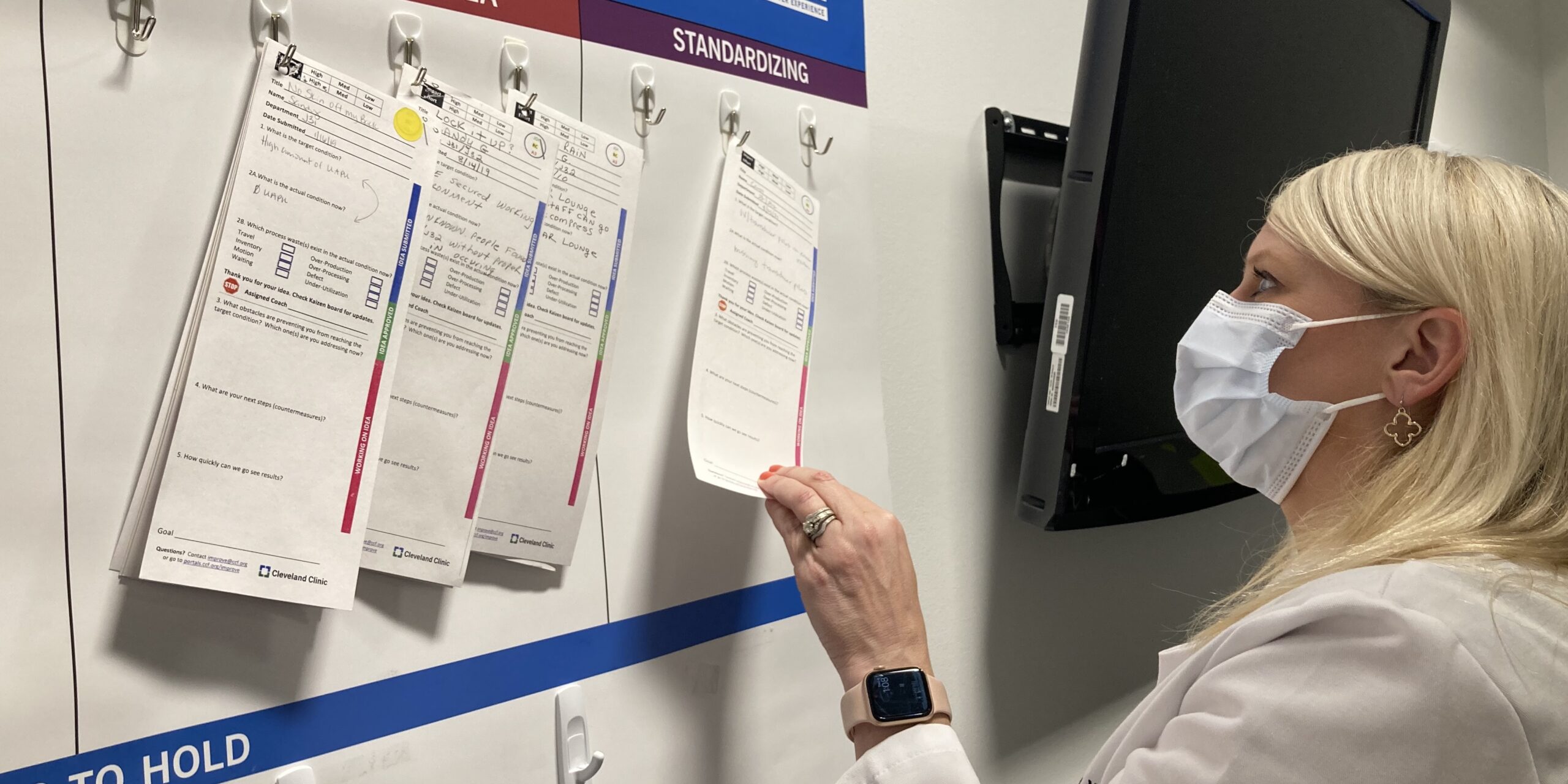
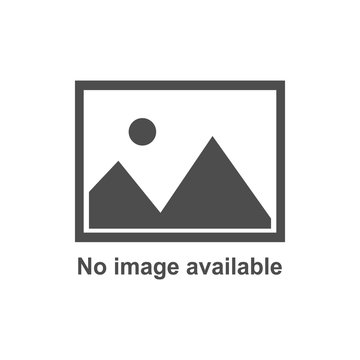
INTERVIEW – Cleveland Clinic has been on a lean journey for a few years now. In this interview, their Chief Improvement Officer and Chief Nursing Officer talk continuous improvement, metrics, and sustaining results.
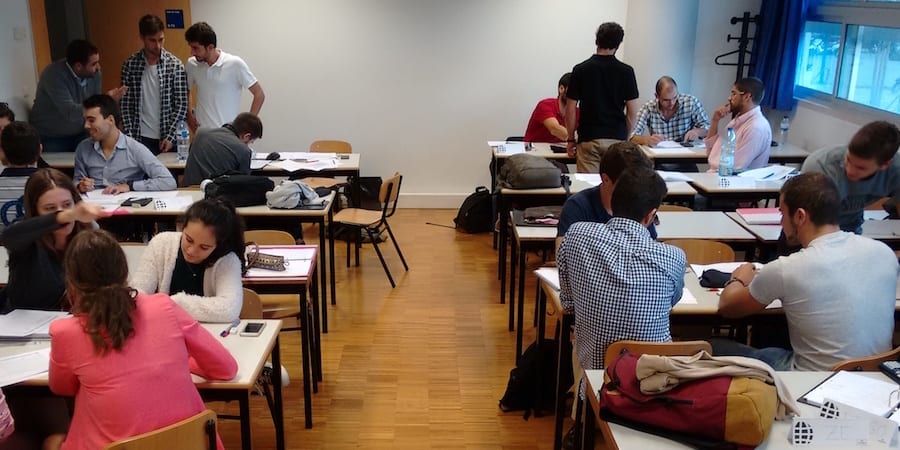
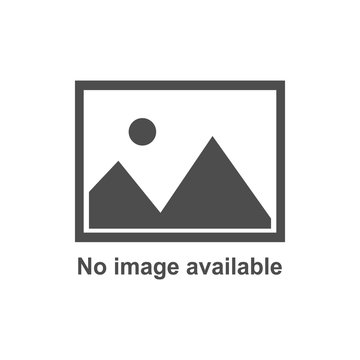
CALL TO ARMS – Despite the spread of lean principles across the world, only a handful of universities have included the methodology in their programs. This article is a call-to-arms telling us why we have an obligation towards future generations.
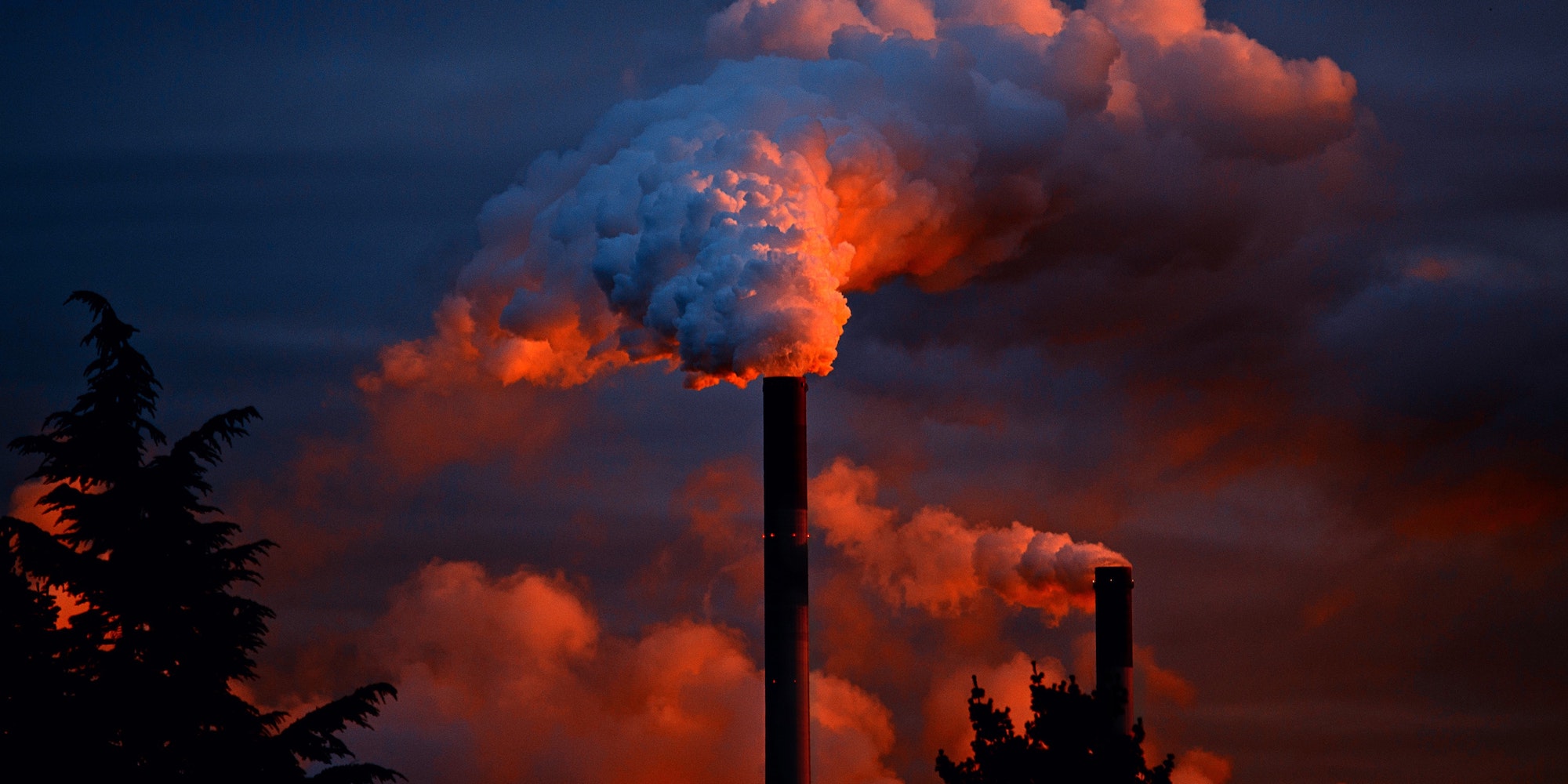
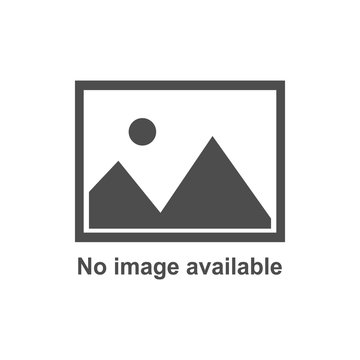
FEATURE - Imagine targeting a quarter of the world’s greenhouse gas emissions by setting our lean minds to it? The authors discuss building better, circular supply chains and designing sustainable products.