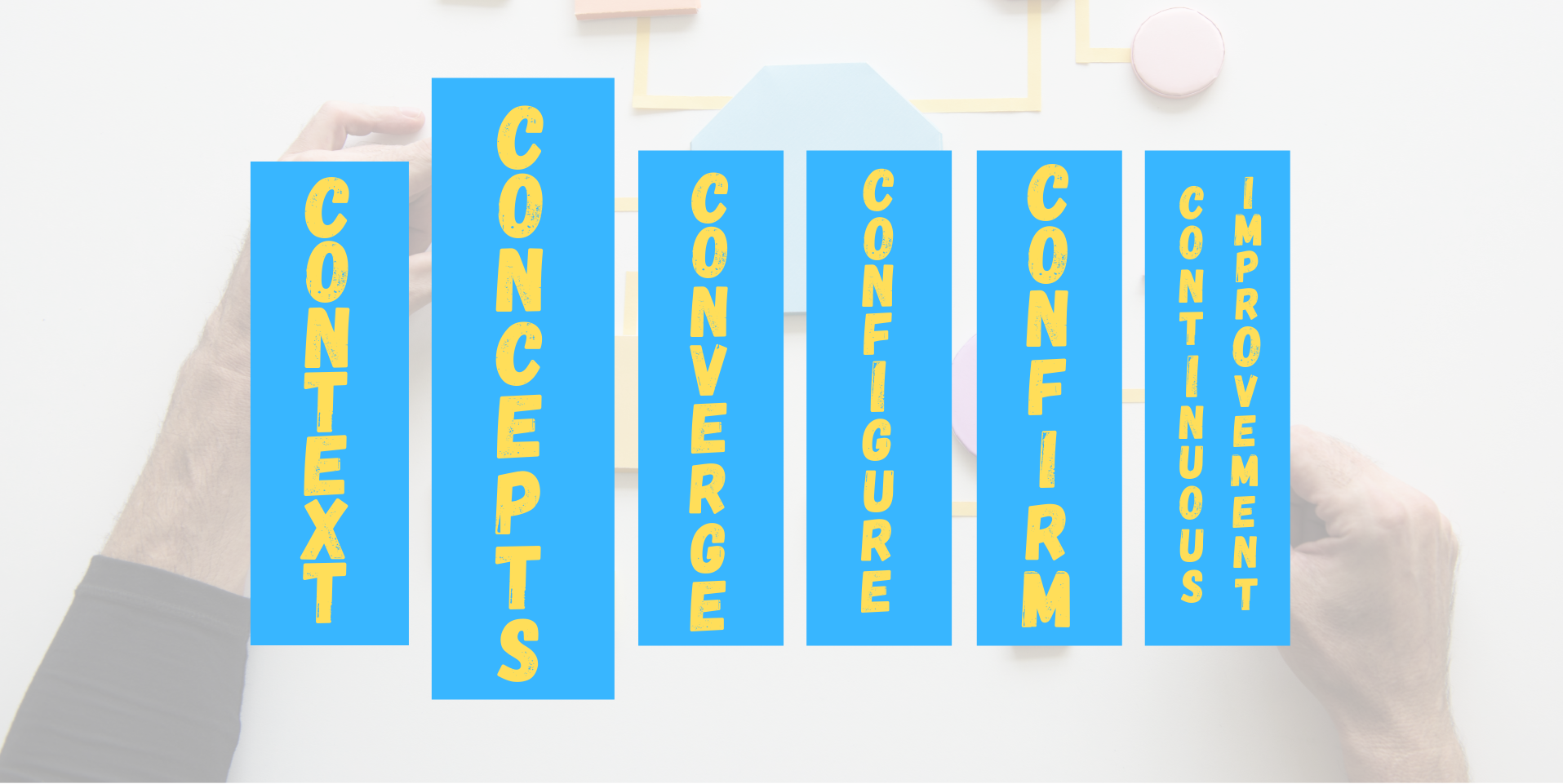
The value of testing multiple concepts at once
SERIES—The authors discuss Concepts, the second of six elements in their process development model, discovering the key knowledge gaps and exploring multiple process design options to facilitate learning.
Words: Eric Ethington and Matt Zayko
“Imagination is the beginning of creation.”
- George Bernard Shaw -
(DELAYED) LEARNING ABOUT OUR PROCESS… AFTER LAUNCH
“What is Lean?” This can be an interesting discussion question to pose to any team. The answers vary, of course, but the ideas of value and resources are always mentioned, whether we work in healthcare, manufacturing, engineering, R&D, HR, or other areas. One definition we came to appreciate was, “the never-ending matching of resources to demand to generate value for the customer.” Illustrated in the figure below, this was an early step to understanding that today’s countermeasures would be tomorrow’s history. Or, in our case, that today’s cell design will be tomorrow’s history.
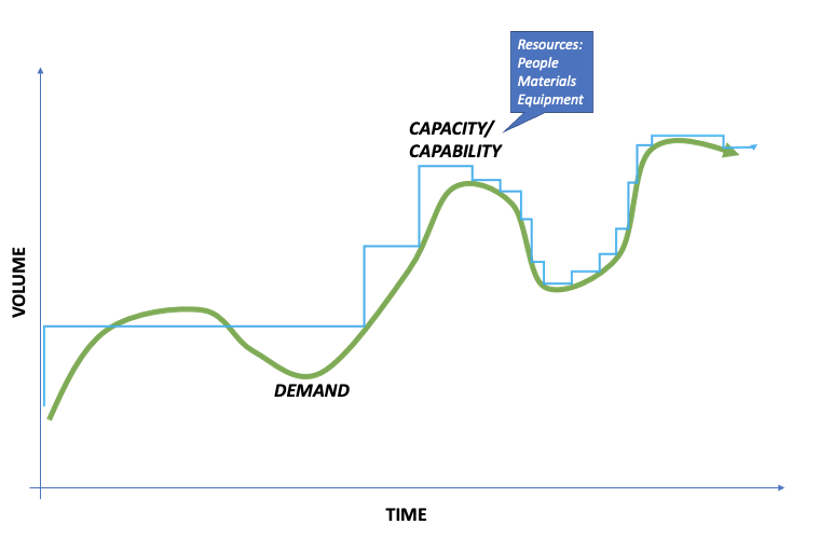
Early in our careers, our operations were given an E-shaped cell dominated by a conveyor belt for “pacing” and large containers of incoming materials. We attempted a premature U-shaped cell, which was nothing more than stitching together a bunch of lean concepts we had read about but had none of the benefits of U-cells touted in the books.
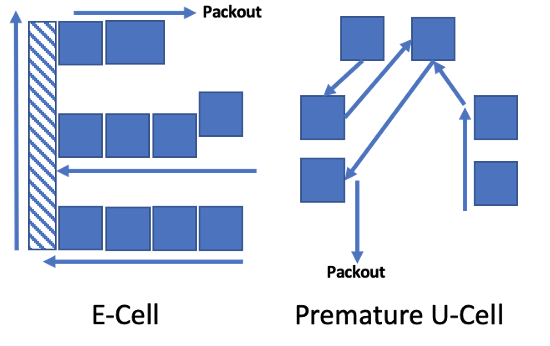
At the advice of our sensei, we took a step back, simply removed the conveyor from the old E-cell and watched. It turned out the “pacing” conveyor was interfering with the flow, and we could now see how imbalanced stations 5 and 6 were compared to the rest of the cell. So, we opted to isolate those stations to the side of the line and combine them into one operation. The T-Cell was created.
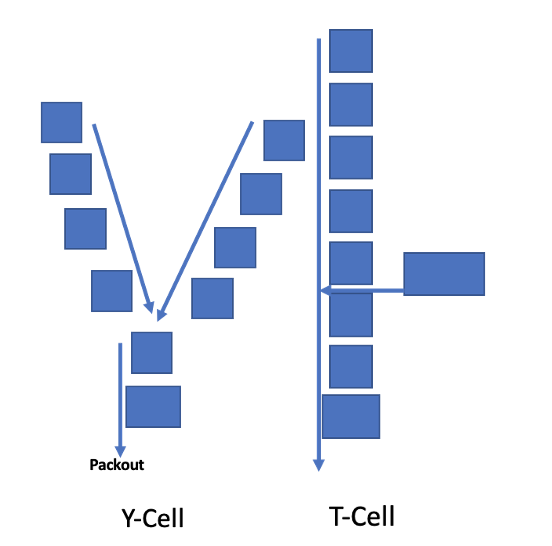
Through observation and learning, we could see that, even combined, stations 5 and 6 were still outpacing the main flow – when they should be able to supply multiple lines. At that point, our engineers and team members creatively figured out how to combine operations 9 and 10 without increasing the cycle time or complicating the equipment. That’s when the I-Cell was created, with the sub-assembly from operations 5 and 6 being delivered into the cell as a component part.
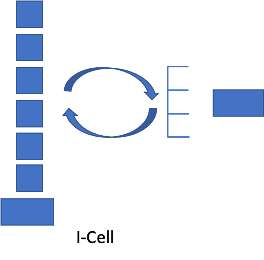
All told, this progression took a lot of effort, from just about every function, across 18 months – with production running, of course. We learned a tremendous amount, but it would have been even better to learn as much as we could long before the first E-Cell was delivered to our factory floor. We had effectively missed out on 18 months of better safety, quality, delivery, productivity, and employee engagement on a product line that, at high volume, would have a total lifecycle of four years.
PULLING THE LEARNING FORWARD… DURING DEVELOPMENT AND BEFORE LAUNCH
The second element of the 6CON Model, as described in our book The Power of Process, is Concepts. The Concepts frame is the beginning of this type of early process learning, where multiple ideas are developed – ideally while the product is also being developed. The case study we share in the book is similar in spirit to the example above, the difference being a compressed timeline – six months spent learning and improving before launch versus 18 months of re-working a poor process design after launch. We learned how the latter is often referred to as “touzen” – engineering rework of poor upfront design, disguised as kaizen.
What does it mean to develop multiple ideas at ones? How many concepts is “multiple”? There are different lines of logic here, all with their benefits, but three is certainly not enough. In manufacturing, with three options, you typically see a manual U-Cell, something completely automated, and something in-between these two options. This same pattern can be observed in just about any industry: the “new and latest” technology, a basic manual version, and something in-between. We prefer to see at least four concepts, which forces the teams to be very deliberate as to why the in-between concepts are different from one another, understanding the trade-offs. Once options are developed and trade-offs understood, the team can start to move to the next 6CON frame of Convergence, which will be discussed in next month’s article.
COMPARING CONCEPTS WHEN DATA IS SCARCE
When developing many options, a key challenge for the team is to have an objective means to compare them. We prefer to use a lean-style cost model that is a mix of attributes and total lifecycle cost factors. For example, as stressed above, flexibility is important to be able to match the capacity of the process to the ever-changing demand. Therefore, it is critical to have a measure of the process flexibility as an early proxy for demand performance. Another important measure is total lifecycle cost, based on the forecasted volume over the product lifecycle. This can be an early proxy for capital and labor costs. The point is to identify key measures of a successfully launched new process and then ask yourself, “what can I measure early in the development cycle that will be indicators for those measures?”
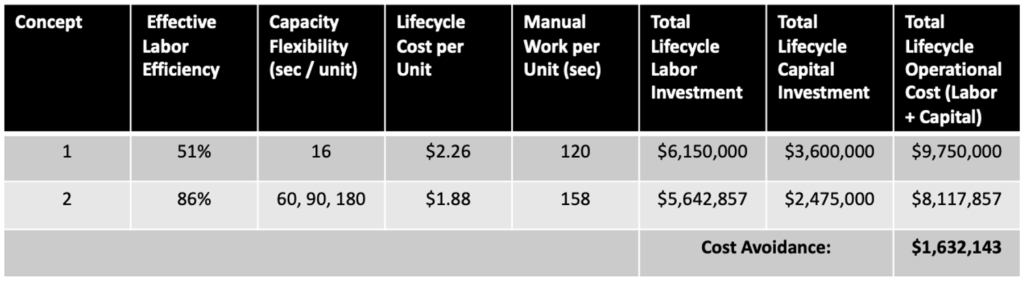
©2022 Ethington/Zayko, The Power of Process, Productivity Press
LEARNING TO MOVE UPSTREAM
Luckily, the deep learning that occurred from seeing the transition from the initial, poorly designed E-Line to a smoothly flowing, flexible rate I-Line at much higher performance was the catalyst that our organization needed. We moved the process development work further upstream, well before launch, and closely tied it to product-development activities.
Never again did we want to launch a poor process that we would then frantically try to improve for one-two years, only to repeat the cycle two years later when the next new product launched into manufacturing. We had realized the lost value and high costs that would keep occurring if we did not move upstream in our development cycle with lean process development.
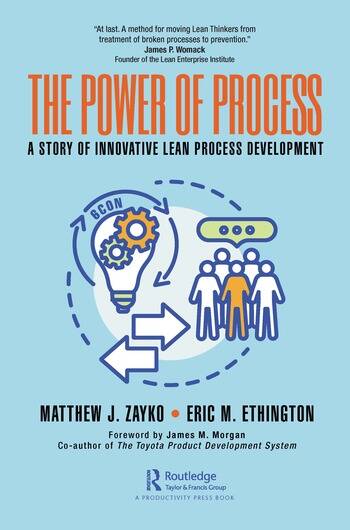
For more details, please visit www.thepowerofprocess.solutions
THE AUTHORS
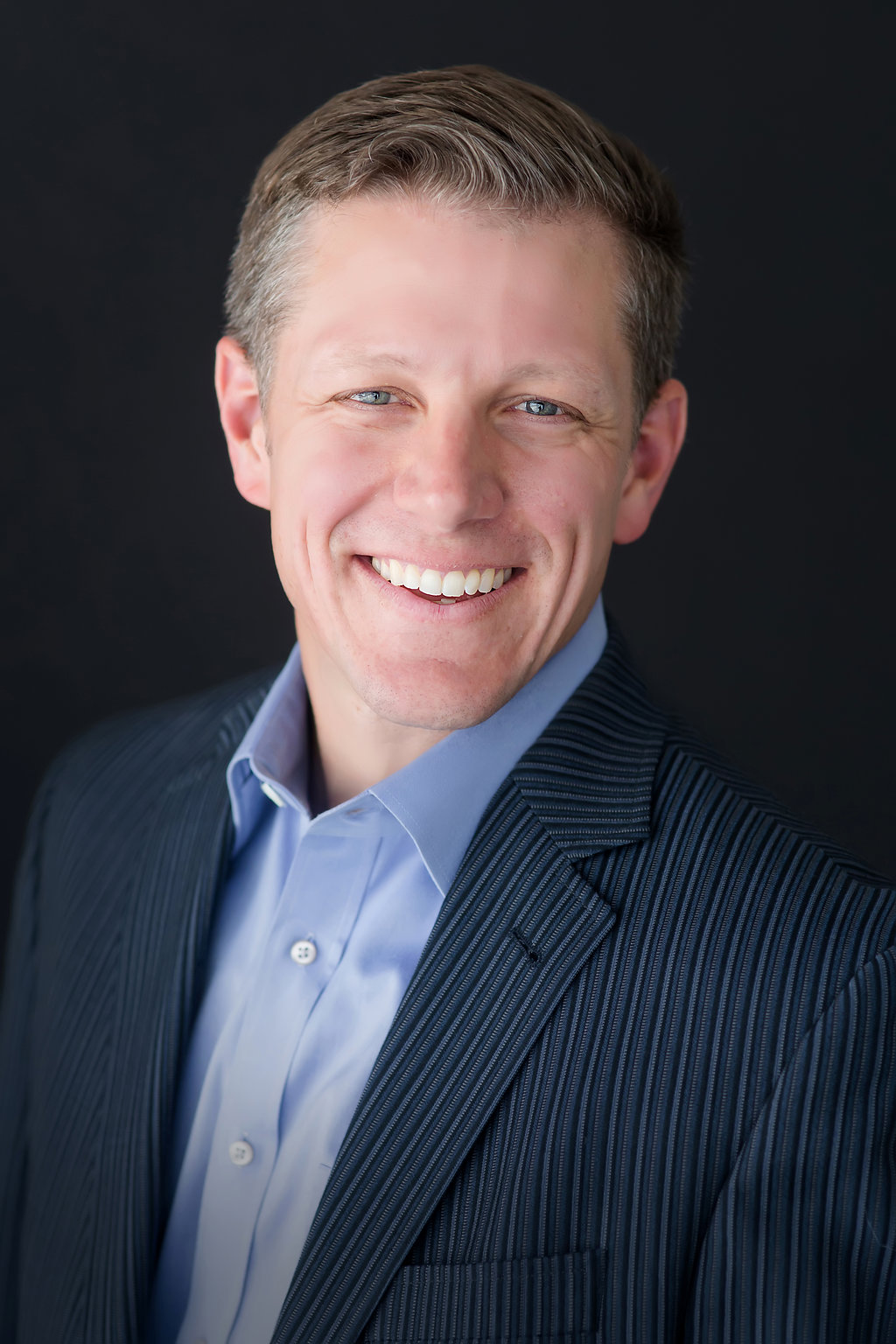

Read more
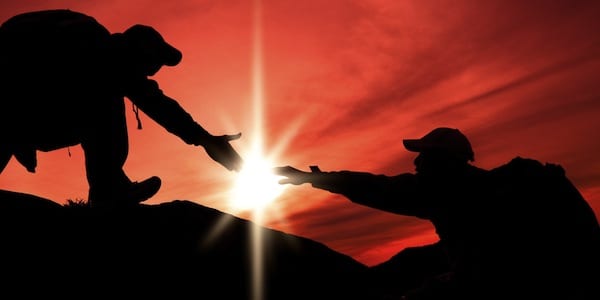
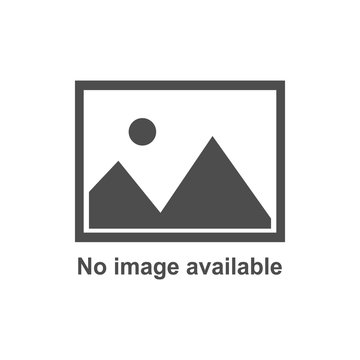
FEATURE - Two weeks ago, the authors shared their thoughts on mindset. In part 2, they discuss how to grasp the true spirit of lean.
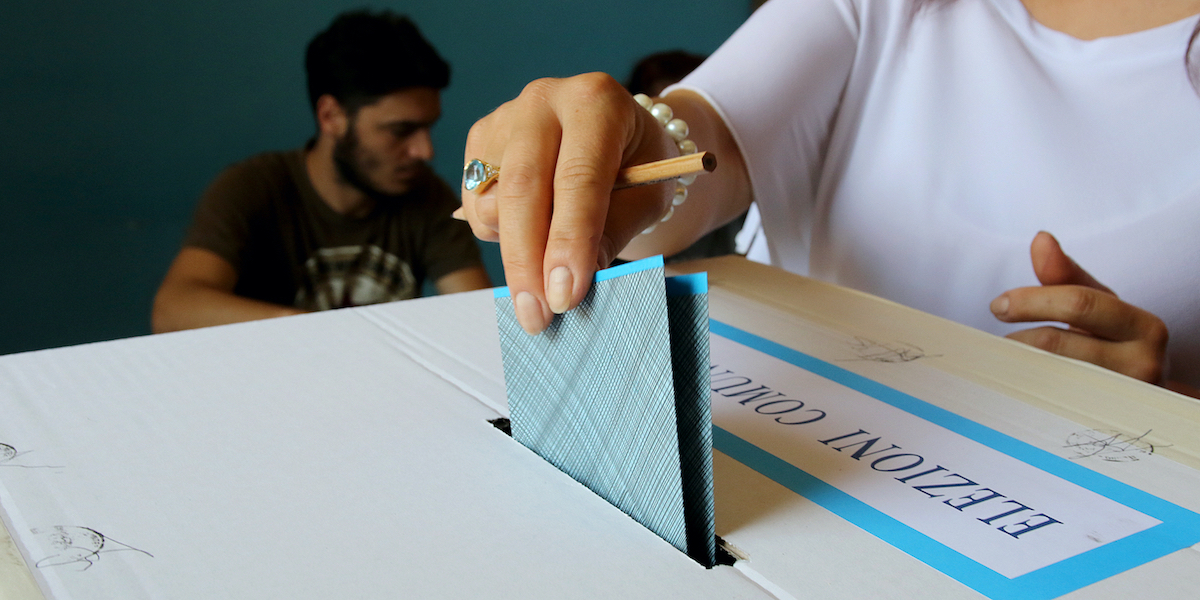
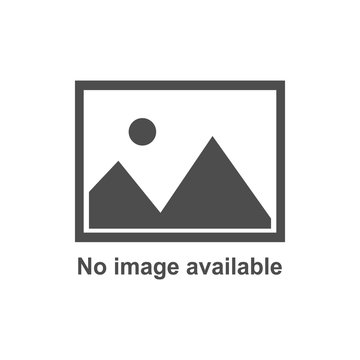
CASE STUDY – Have you ever considered how Lean Thinking could apply to politics? The author explains how the result of a mayoral race in southern Italy was ultimately determined by the lean approach adopted by one of the candidates.
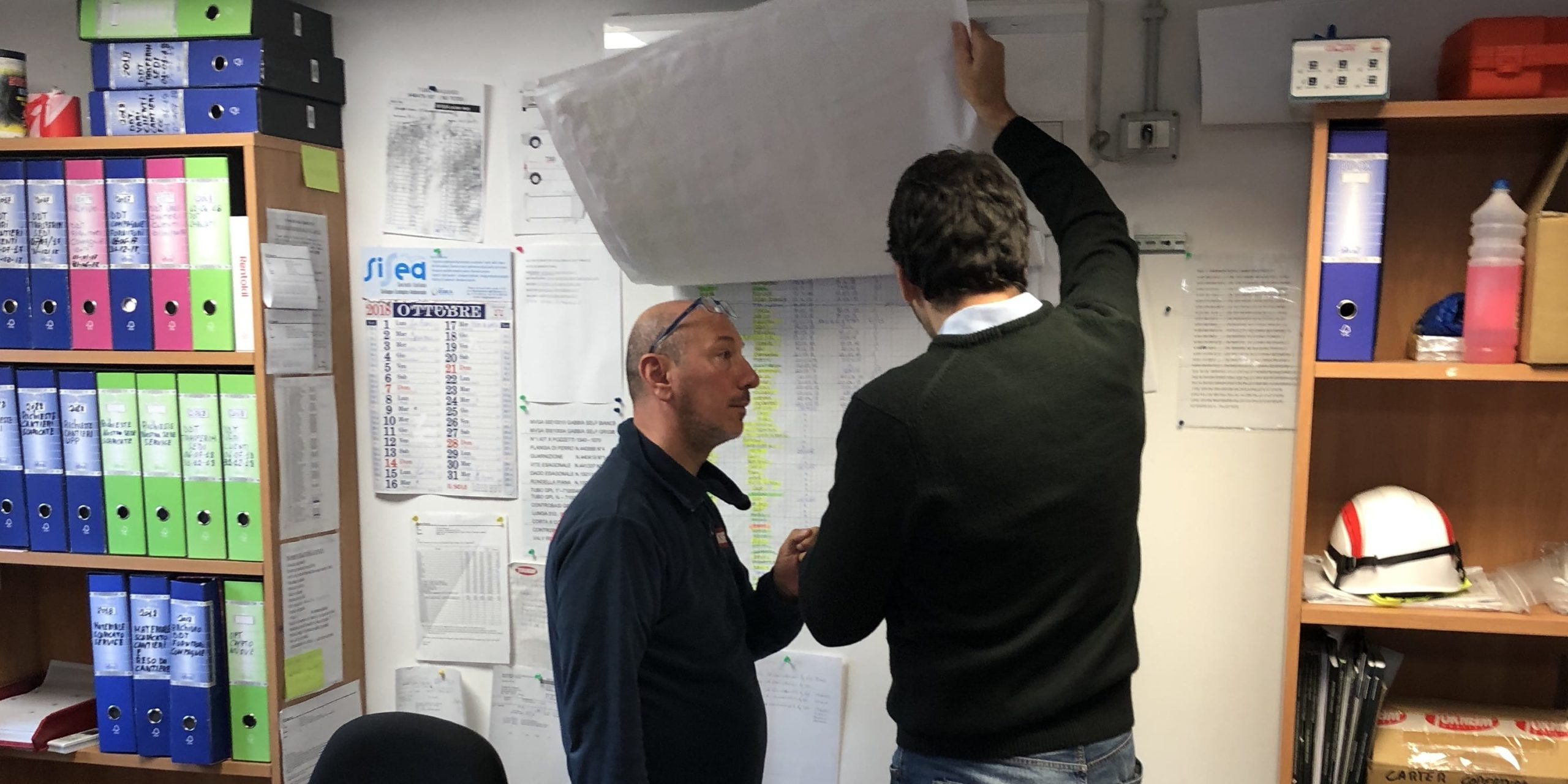
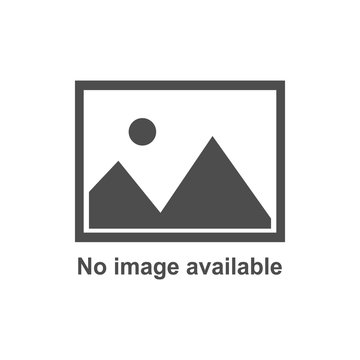
FEATURE – Innovation is a process and lean thinking allows that process to take place, by empowering everyone in the company to think creatively about solving customer problems.
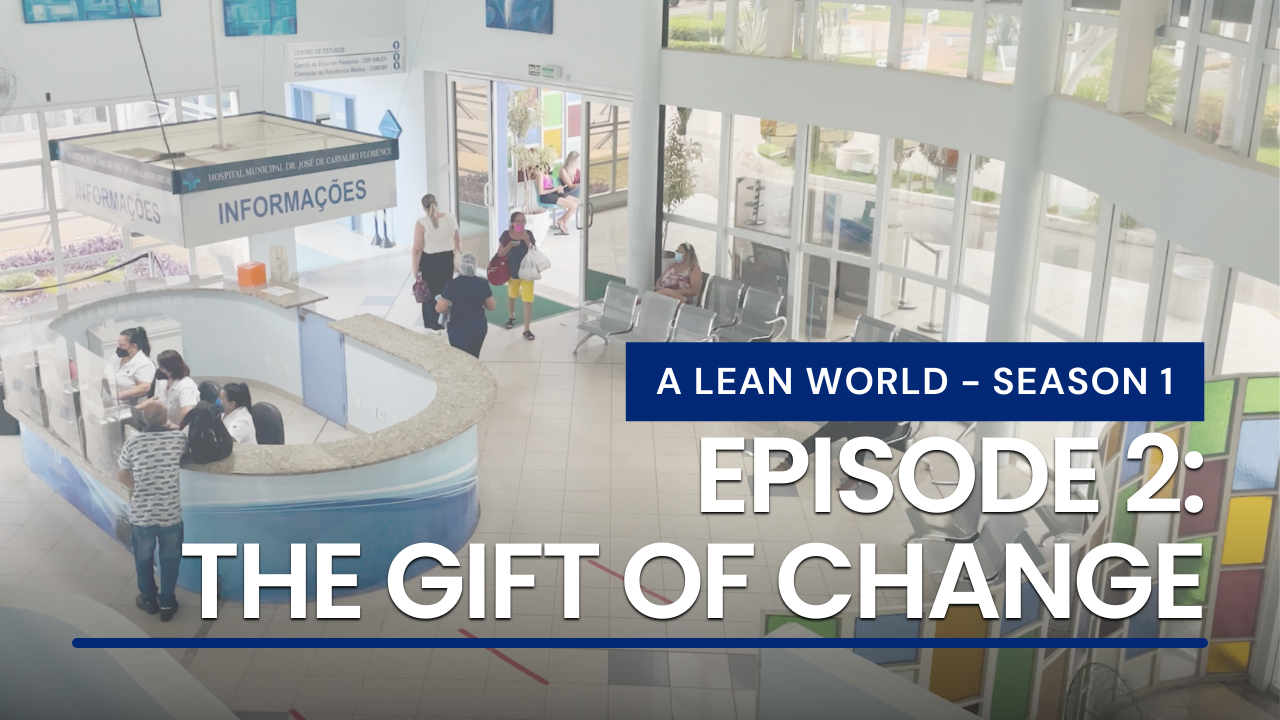
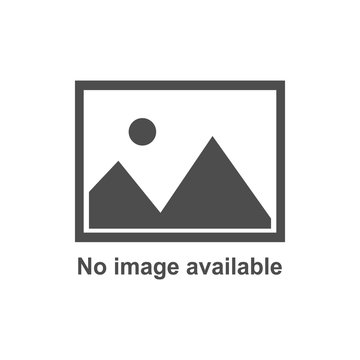
WEB SERIES – In Episode 2 of our docuseries on lean in Brazil, we learn how the pioneering efforts of a cancer clinic have inspired the city of São José dos Campos to transform into a lean healthcare cluster.