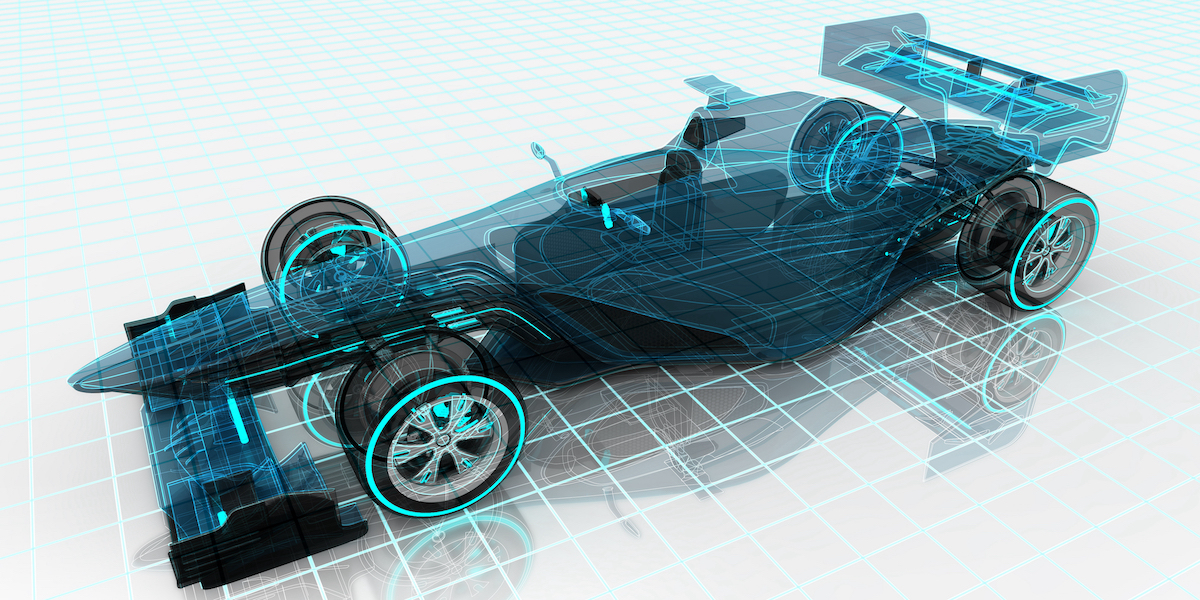
Getting started with lean process development
SERIES – In the final article in their series on lean process development, the authors discuss what it takes to get started with their 6CON process development model.
Words: Eric Ethington and Matt Zayko
“Reasoning draws a conclusion, but does not make the conclusion certain, unless the mind discovers it by the path of experience.” - Roger Bacon
As with any new model or framework, the most difficult part is knowing where or how to start. In this article, we will provide some guidance on setting off down your own unique path to building traction to integrate process development earlier in the overall development cycle.
What is your current condition?
The best place to start is to deeply understand your current situation and to gain alignment on the current challenges or problems you are facing. Use a recently launched process to map out the steps taken to develop it from beginning to end. This will allow your organization to truly grasp the reality of how well it designs new processes. This reflection and learning will be highly valuable, because as time passes we tend to forget many of the critical items and to connect cause and effect of certain decisions.
What is the capability of the recently launched process?
As part of this reflection with a recently launched process or one that is close to launching, use a standard score card to collect data and facts about the capability that is currently being experienced. In the Confirm section of our book, we introduced a standard qualification score card, which is a great template to use. With clear data collection assignments for every team member, this is an effective means to objectively understand the true process capability. As you gain experience in process development, this score card should be changed to better support your unique circumstances. Nevertheless, it is a good place to start.
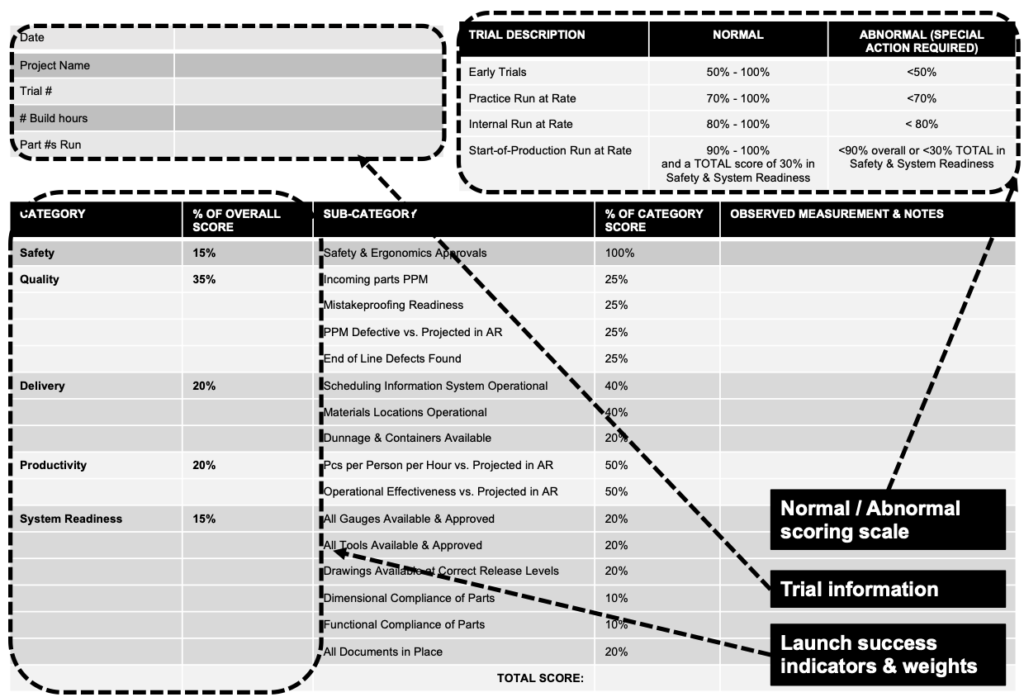
Example Score Card for Launch Process Readiness
How much waste and cost could have been avoided with better upfront process design?
With the reflection and learning that the team gathers, it is also important to capture and summarize the tangible waste, customer impact, delays, and costs that could have been avoided with proper, upfront process design. This is a valuable insight into the cost of poor process design, which can be used to help justify the earlier investment in new process development resources.
What are your key enablers for Lean Process Creation?
Before the team jumps to designing their shared vision for how to do future process development work, they will need to challenge their existing mental models. Successful process design teams incorporate a handful of key enablers into their way of working. These questions help to determine the enablers for your own situation:
- What is the System Architect or Chief Process Engineer role for your organization? Who should have this role?
- What is the Operational Declaration? How is this different from the charter? Who owns it?
- How will you gain alignment on how the actual work will be organized to provide the value, from idea to production start? (Product & Process Development Value Stream Map)
- Where will you use “Set-based” Design concepts to maximize the learning early on during the Study Phase? How will you identify and manage Knowledge Gaps to de-risk the back end?
- Where will you use the Obeya Space for effective visual management to see abnormal from normal?
- What are the key Milestone Integration Points? What are the Design Review types during the development of your new product?
- What is the Management System Routine for Plan-Do-Check-Adjust (PDCA) when developing a new product?
How will your leadership team support, engage, and learn with the team?
As noted in our Planet Lean article series, it is not enough for the leadership team to “declare” their desires, but rather they will need to actively engage and tangibly support the process design team during this pivotal time. Great process creation includes a clear, cadenced role for leadership with regular engagements and a clear escalation path for highlighting and resolving issues.
***
In conclusion, change is not easy in any organization, and big change is even more difficult. If you are able to align the team around a shared reason for needing to change, however, that is a great place to start. This could be related to a need to reduce process development lead-times drastically for a customer, improve process readiness at the start of production, or another urgent need. Once you have this alignment, start to build momentum by setting aggressive goals and targets in order to be the best in your industry from the customer’s perspective. Avoid getting paralyzed by indecision or caught up in a cycle of trying to “boil the ocean” of problems or challenges that face your organization.
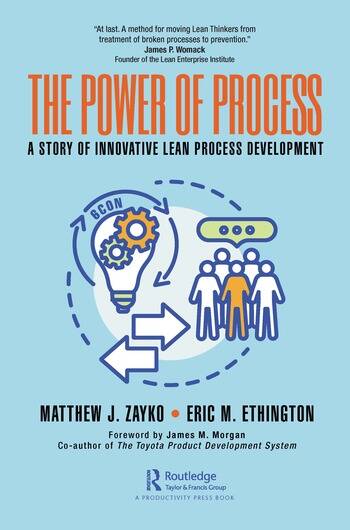
For more details, please visit www.thepowerofprocess.solutions
THE AUTHORS

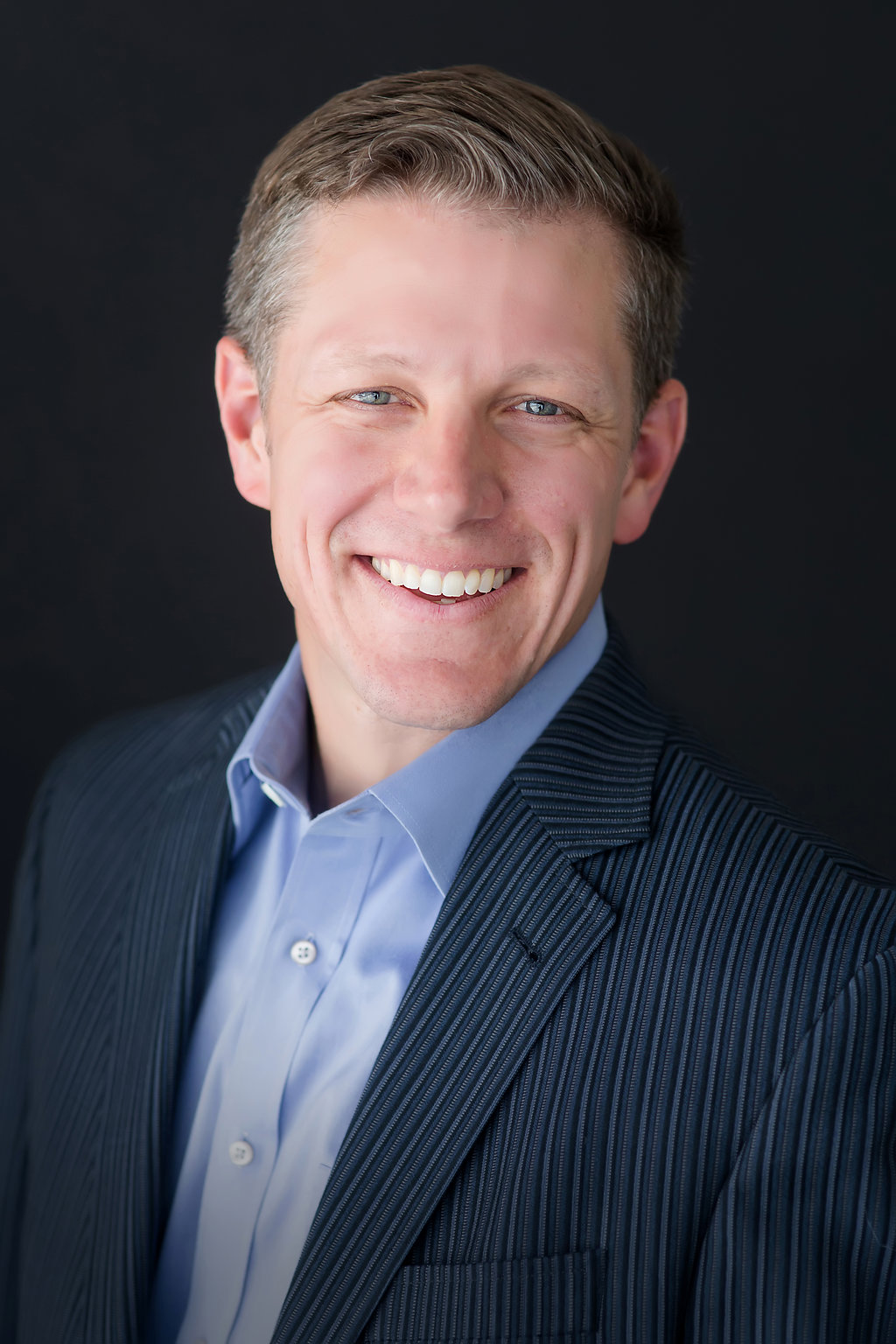
Read more
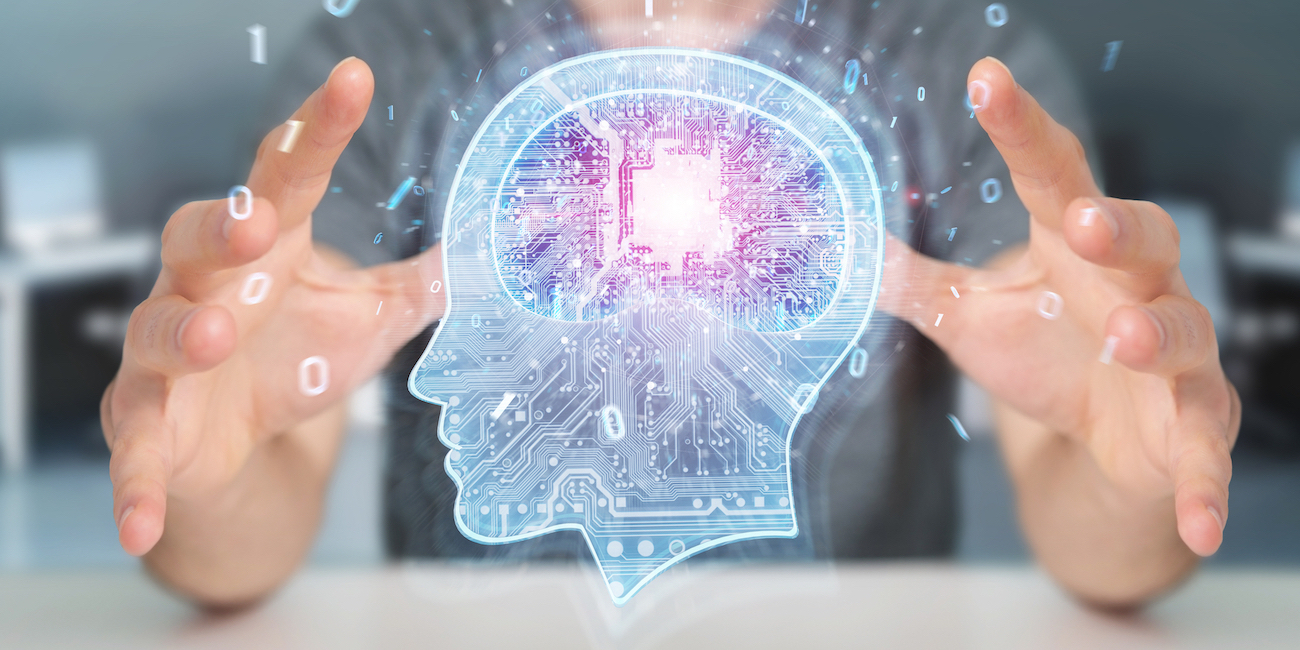
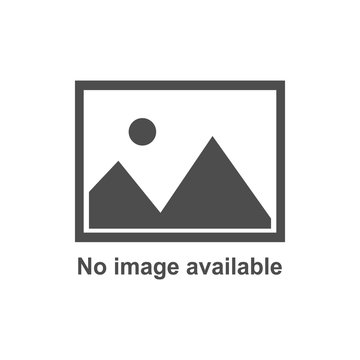
FEATURE – By looking at two practical examples, the authors discuss the cognitive shift towards learning and continuous improvement that takes place in a lean transformation.
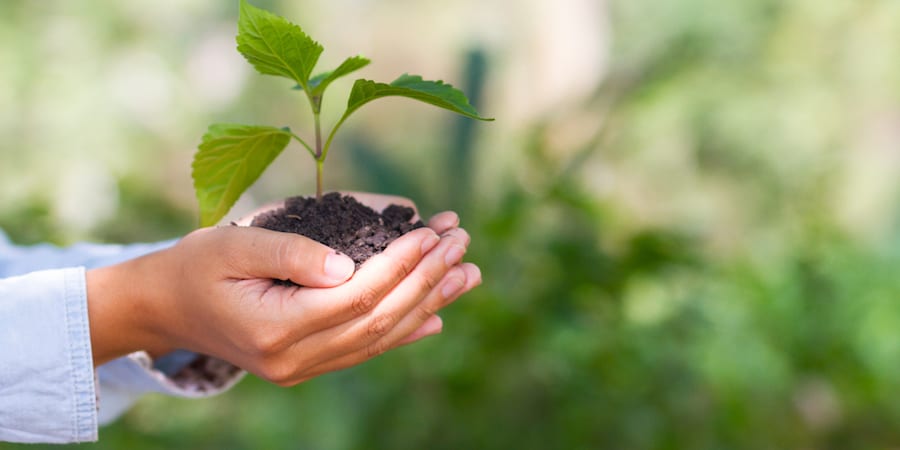
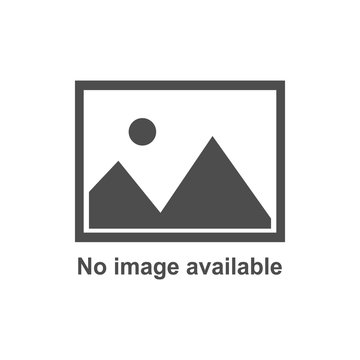
WOMACK’S YOKOTEN – Ahead of the holidays, for his last column of the year, the author reminds us of the power of sharing. Go out and spread the lean word!
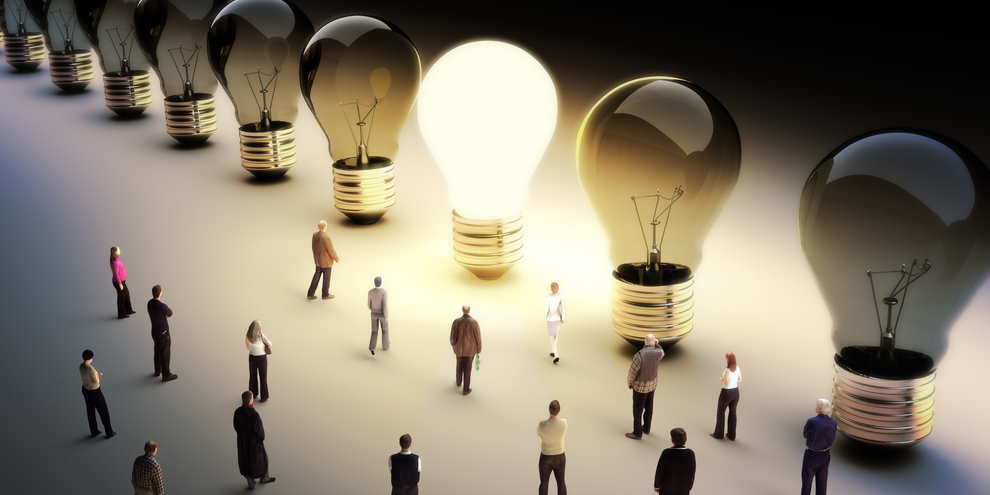
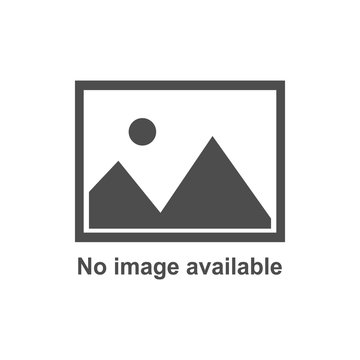
FEATURE – In this compelling theoretical piece, the author reminds us how in a lean organization relations are structured around learning opportunities rather than execution. This is what ultimately enables a company to grow.
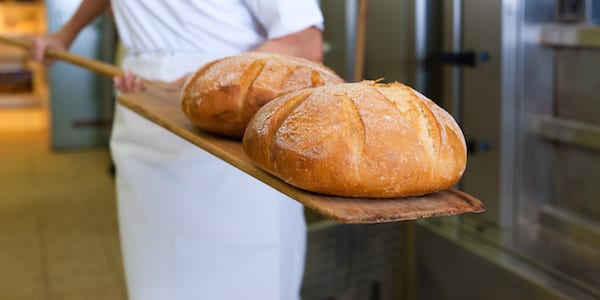
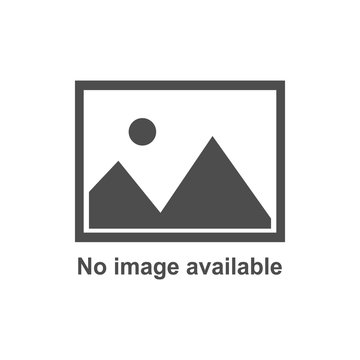
CASE STUDY – A very lean system that runs like clockwork and constant attention to customer service enable Barcelona-based 365.café to achieve the impossible: supplying 55 bakeries out of a 650-sqm factory.