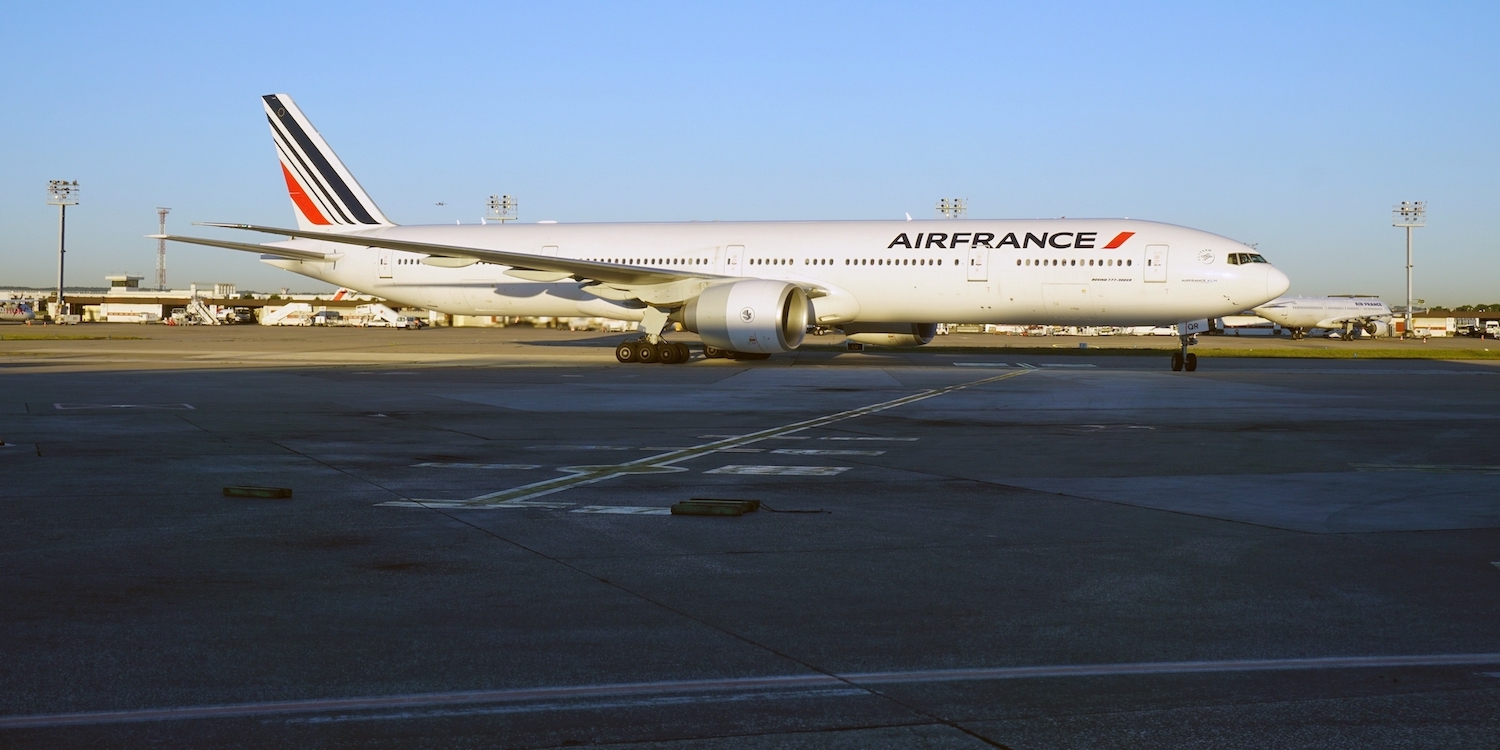
When lean takes off
NOTES FROM THE GEMBA – The author visits the Parisian airport of Orly to learn about a pilot project (pun intended) that aims to tackle the late departure of flights using lean thinking.
Words: Catherine Chabiron, lean coach and member of Institut Lean France.
Photo credit: EQRoy / Shutterstock.com
How do you rate an airport? Do you look at the efficiency of the check-in process? The speed at which luggage is delivered as you step out of the airplane? Do you evaluate the shopping experience or the ability to effortlessly transfer to another flight? Do you take into account the ratio of lost luggage and the transportation facilities to and from the airport? Do you consider on-time departures or on-time landings? Whatever criteria surveys use to rate and rank airports, one thing is clear: French airports seldom make it to the top.
Agnès Nicolas, who is in charge of lean at Orly Airport, south of Paris, decided in early 2018 that on-time departure was the metric the airport should focus on every day. After all, this is what airports do: make sure airlines safely fly people from one place to another at a set time, and weather conditions or high traffic in the most visited country in the world for number of arrival are no excuse from the passenger’s point of view.
AGREEING ON THE PROBLEM TO SOLVE
ADP (Aéroports de Paris) has recently launched a major facility overhaul of Orly – with a terminal expansion and enhanced rail connections to the centre of Paris, targeting the 2024 Olympic Games). Investment was long overdue in an airport that opened to commercial traffic back in 1946 and saw its number 1 spot taken away by Roissy Charles de Gaulle (located north of the French capital) starting in 1974. To this major investment, we can add significant organizational change, with the two terminals (Orly South, covering Southern Europe and Africa, and Orly West, covering domestic traffic) being combined to harmonize the quality of service for passengers, get one entry point for airlines and cut costs through synergies.
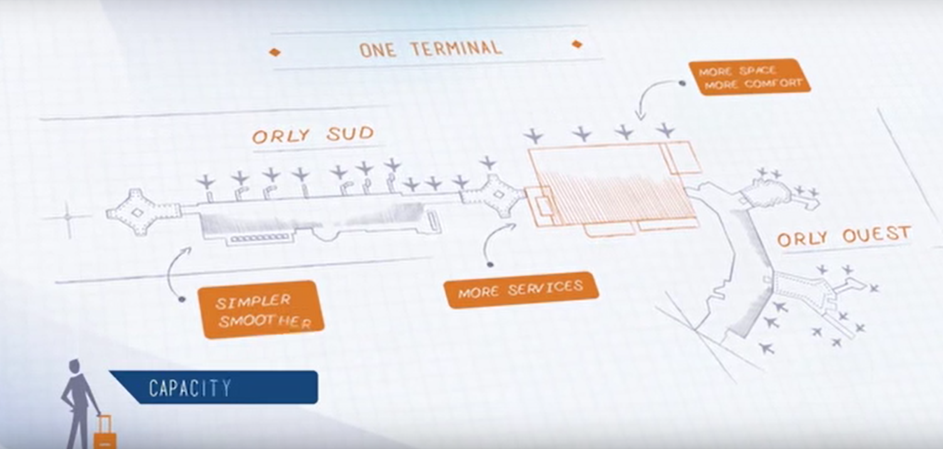
For Agnès, the context was not optimal: such a major change comes with the risk that management’s attention will be diverted away from passengers as daily operational concerns take over.
Another concern of hers was the common preconception that late departures are mostly caused by excessive air traffic. Surveys, however, indicate that this accounts for only 15% of the delays recorded in Europe. The average delay on departure in Europe was 11 minutes in 2016, with France accounting for one third of all European delays. This is partly explained by France’s geographical position at the center of Europe and by the fact that every year the country welcomes a really high volume of tourists. Nonetheless, a simple look at a flight tracking App reveals that the center of gravity of European air traffic is further north. Add to the above the fact that a one-minute delay is known to cost an airline €80 to €100: multiply that by the 11 minutes of average delay flights in Europe experience and by the number of flights airlines handle each day and you will soon reach the millions of euros.
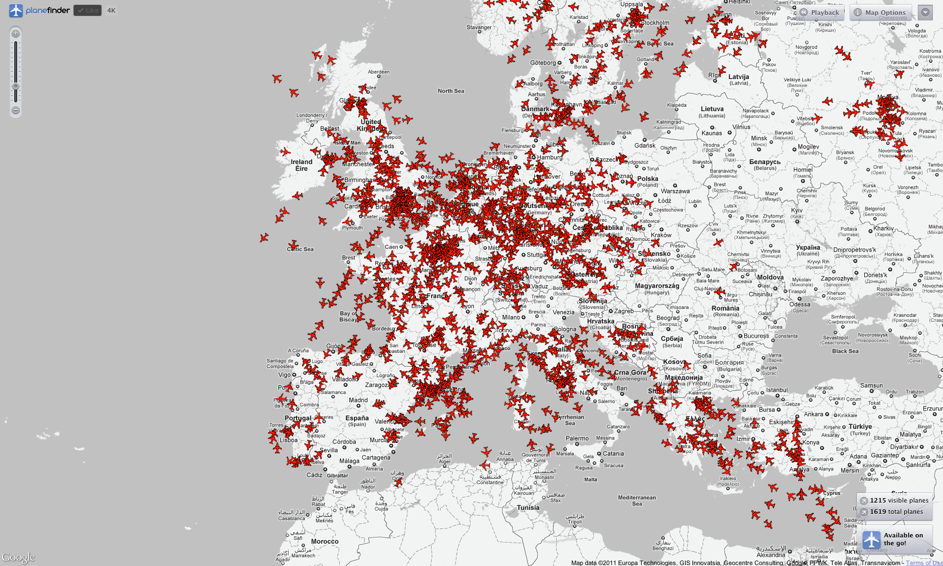
Agnès decided to stick to her idea of improving on-time departure and convinced the Executive Committee to try out a pilot project to investigate the causes of late departures and learn from the experiment. The partner selected for the pilot was a new budget airline called French Bee (IATA code name BF) and the chosen route was Paris – Réunion (from 300 to 400 passengers per flight). The target was to consistently increase the 16-minute punctuality of that route from 42% to 85% (this indicator was at around 18% at the beginning of 2018). The 16-minute punctuality means that if the planes pushes back from the boarding gate at H+16 minutes, it won’t be late, while it will be at H+17 minutes.
GENCHI GENBUTSU
Now, how do you improve punctuality? You start by walking the gemba and segmenting out the different steps and associated risks of generating a delay.
Check-in -> Luggage drop-off -> Security check -> Border control (if any required) -> Boarding -> Pushback at gate
Agnès and I get ready for the walk, which starts at the check-in area. Check-in for the 16:30 flight that day is supposed to close soon and Agnès frowns as a dozen passengers who are still lining up. “This does not necessarily mean we will be late, but it is not an encouraging sign,” she says.
The first attempt at collecting all the steps along a timeline starting at H-4 (time for gate pushback minus 4 hours) didn’t add up, Agnès recalls. From a mathematical point of view, there was no way the plane could be ready to go in four hours. The plane would simply never start on time the way tasks had been initially represented. It took some time to collect all the data from observation and get it right.
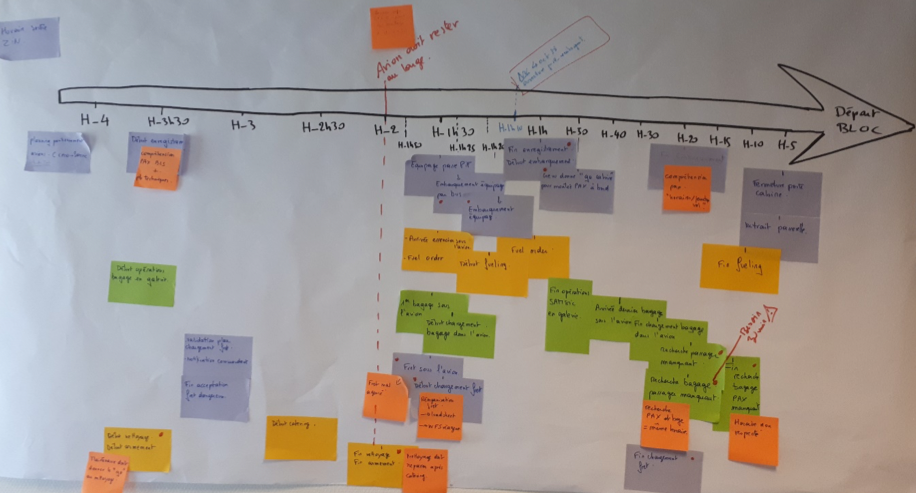
As we go through Border Control and walk towards the gate, Agnès tells me how they started their genchi genbutsu. Quick wins were clearly needed to gain the trust of people and have all parties on board. It took quite a bit of nemawashi to go and visit each stakeholder and collect frustrations and suggestions from each of them. The top 2 topics that were unearthed were the information process between key players (schedules, gates, etc...) and missing passengers (those who check-in but do not reach the boarding gate on time). If they check in with luggage and do not board, this adds an additional delay as their luggage must be retrieved from the plane for obvious security reasons.
As the team investigated the details of the first topic, it soon turned out that the information and signals needed to get a plane to take off on time are a permanent source of frustration and misunderstandings. This stems from the fact that Orly provides the infrastructure but the actual check-in, maintenance, cleaning, police, boarding activities are outsourced to a vast number of partnering companies – not to mention the airlines themselves. When ADP (the airport) talks to French Bee (the airline) about check-in, they have to include GEH (the airline assistant, in charge of the actual check-in and boarding) who in turn has outsourced the luggage and flight coordination to SAMSIC. With different partners come different systems, Excel sheets, forms. The signals can be confusing, if not wrong (as an example, the plane is expected to be at gate 1 and is found to be at gate 2).
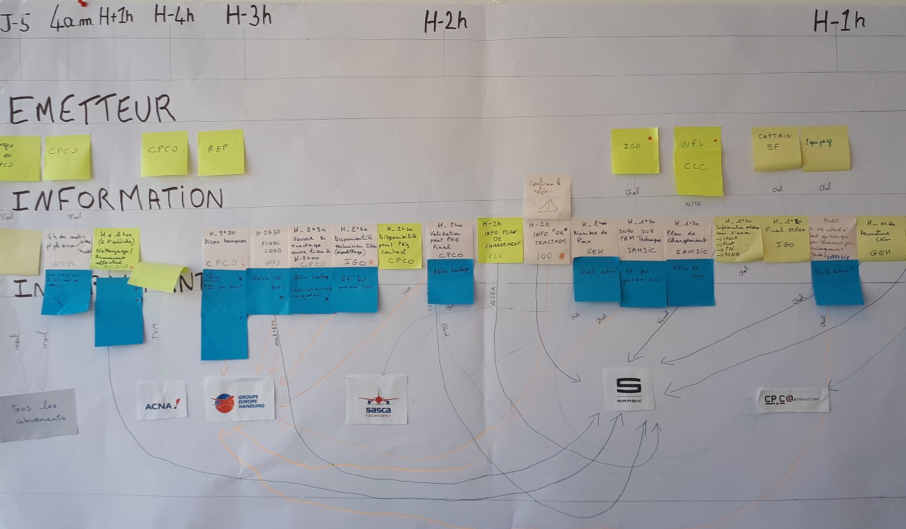
This led to a thorough 5S exercise on the information process (for instance, adding omitted key people to the mailing lists or clarifying details on what information needs to be shared), but also to additional communication by phone as most of the information is orally transmitted.
For the missing passengers, the first assumption was that people checking in at the last minute were the main source of the problem. As a countermeasure, the last set of checked-in luggage would only be loaded when the owners had actually boarded the plane. But Agnès was not totally convinced that this was the real problem and the team decided to go to the gemba and ask questions. It turned out that missing passengers are more likely to be early checkers, who are not aware of the boarding time limit (22% of those questioned did not know they had to be at the gate maximum 20 minutes before departure) or had not realized the time it takes to walk to the gate (we timed it as we walked: it was 10 minutes from Border Control). Of those surveyed, 59% had no clue it took that long. Interestingly, 50 % of the passengers traveling from Orly South are flying for the first time (a rate that is much lower at Orly West, from which domestic flights are operated and where business travellers are more frequent).
A first countermeasure for this double issue was to add a red sticker on the boarding pass indicating the boarding time limit. It worked: the number of the passengers unaware of that limit went down from 22% to 4%. But as French Bee promotes automated check-in at kiosks, where boarding passes do not carry the red sticker, there is a risk that the current countermeasure will not represent a lasting solution. Discussions are underway to improve the signage in this aging airport (“Walking time to gates XX from here: estimated 10 minutes”).
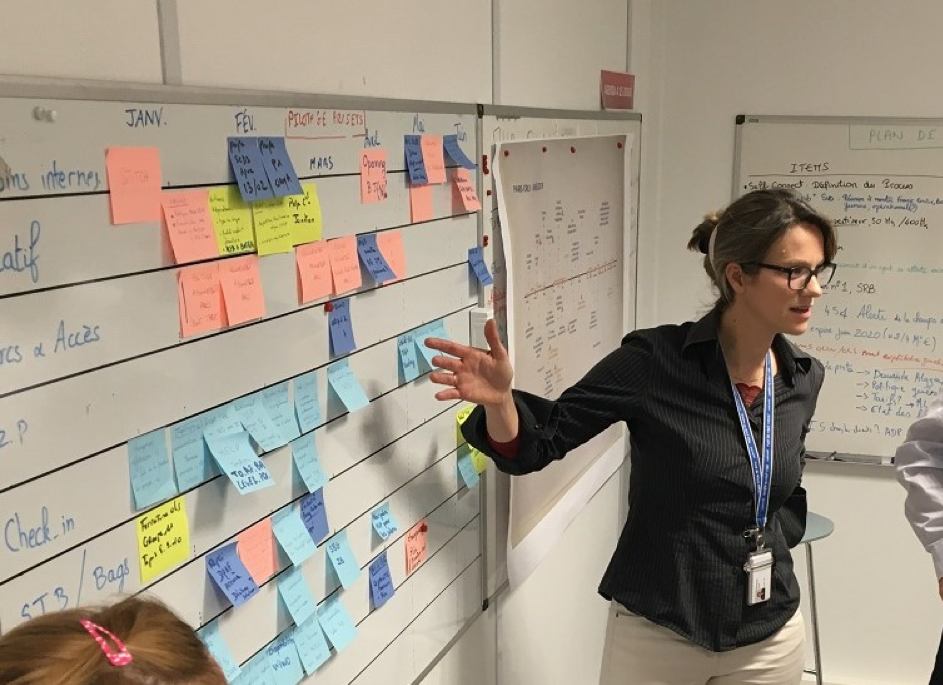
LEARNING FROM EACH FLIGHT
The team went down the list of issues and also worked on the logistics and the sequence of the different functions involved in the process (pushing the plane to the gate, maintenance, fuelling, cleaning, and so on). If, for example, no push is available to take the plane from the parking spot to the gate two hours before departure, this is a sure sign that the plane will not depart on time and the only way to catch-up the delay is to leave the plane where it is and board it by bus.
As we arrive at the gate, we have a great opportunity to see that – on that day – the rule was not being followed. The flight is supposed to take off at 16:30 and at 15:30 boarding hasn’t started. The staff hasn’t even boarded (they should have done so at 15:10), because of the plane’s late arrival at the gate. Upon investigating further, we are told that no push was available at H-2 but, because they had managed to get one a few minutes later, they decided to push to the gate anyway. It will later turn out that, while the rule was not strictly followed, the late boarding will not be an issue.
At 15:50, the cleaning of the plane is complete. Boarding starts at 15:52 (38 minutes left till the scheduled departure time, with 409 passengers to board). Twenty-eight minutes later, boarding is complete and no passengers are missing (the combined effect of the red stickers and the late boarding, probably).
We walk down the gangway to see the last passengers get in and observe the final details of the departure from there. Right in front of the plane cockpit, and visible from the gangway, a panel reminds everyone (including the pilot and the flight coordinator) of the departure time (SOBT – Scheduled Off Block Time). There are 4 minutes left, but Agnès and her colleague Laure shake their heads. “Fuelling is not finished yet and the push is not in place. The plane won’t leave on time. Any minute now, the flight coordinator will ask for a delay,” she sentences.
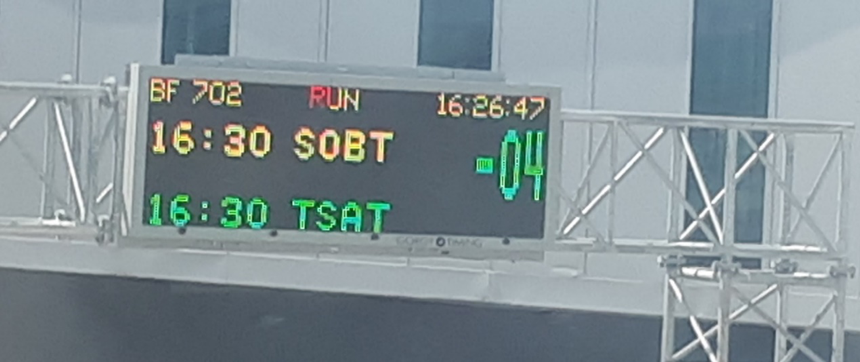
If no delay is requested, the gate planning will be affected and incoming flights or next departures will wait instead of being reassigned to other available gates.
We suddenly see a change on the control panel: a 15-minute delay is requested by the flight coordinator and lights up on the panel (TOBT – Targeted Off Block Time). It is soon accepted by the team in charge of the airport gate allocation as a TSAT time lights up (Target Startup Approval Time). The flight will now depart at 16:45.
At 16:31, the fuelling is still going on. Hand luggage not accepted in the cabin is still waiting in the gangways to be collected and loaded in the hold of the aircraft.
16:41 – We see the flight coordinator running up and down the two gangways, handing over the remaining hand luggage, checking a few technical aspects on the ground. Fuelling is now complete and the Economy Class gangway is pulled away. Will the 16-minute punctuality be achieved? Unlikely, as some luggage is still on the ground and the push is still not connected to the plane to initiate the departure from the block.
16:43 – Another 10-minute delay is requested and accepted.
16:45 – It turns out a passenger is not feeling well and medical aid is being provided inside the plane. Should the passenger be disembarked or not? At 16:52, the passenger is escorted out of the plane, the precautionary principle prevailing. The 16-minute punctuality will not be met.
16:54 – The luggage loading ramp is taken away but the push is still not connected to the plane, revealing a new problem.
17:03 – A new delay is requested and accepted. The push moves towards the plane.
17:14 – The plane pulls off 44 minutes later than scheduled, and Agnès sighs.
This is when we have the opportunity to catch up with the flight coordinator to try and understand what happened (he has already debriefed on the phone with the French Bee Operations Director, with whom the punctuality project has been conducted).
It turns out that in addition to the late arrival of the plane at the gate and the sick passenger, the pilot decided to take 78 tons of fuel instead of the expected 73 tons (this is the pilot’s decision to make, as he examines the load and flight conditions along the route). This forced the flight coordinator to unload a freight pallet to keep the weight of the plane on target. But of course, the selected pallet was not easy to reach and it took some shuffling and sorting before this could be done.
SOLVE PROBLEMS ONE BY ONE
Each flight will have similar small issues to tackle. Overall, the 16-minute punctuality of French Bee on the route Paris – Réunion has already improved from 18% in early 2018 to 78% in March 2019. But to move further would require a systematic analysis of the real causes at each flight delay. Causes for delay are tracked on flight reports but they are often debated (“Don’t put the blame on me”). Other times, the reports only shows the last apparent cause (in our case, the time to unload a freight pallet). Unless a debrief immediately takes place (Jidoka), it is very difficult to investigate root causes based only on the information provided in official reports and to act on them (in our case, an interesting improvement track would be to reduce the uncertainty on weight and at least anticipate the need to adjust it at the last minute).
So Agnès is now thinking of the next step.
Should they continue to promote improvement carried out by a project team? As such, they can only handle recurrent transverse issues. But, because of the other challenging priorities at the airport mentioned above and the organizational changes, it is hard work to bring together all the functions on a regular basis.
What about handing over the punctuality improvement to those who see an on-time departure as a key measure of success, in this case French Bee? Kaizen by project is rarely sustainable: the only way to continuous improvement is to engage everyone in the daily improvement of the delivery, supported by Jidoka and short PDCA cycles. And, by the way, how would Jidoka work in the case described above? Certainly not with airline supervisors summoning, at the top of the crisis, their outsourced resources (like the very busy flight coordinator) to understand what’s going on. But rather by observing on the gemba and debriefing after the fact, so that support standards of who does what in which scenario, as those are progressively unveiled, are designed in order to save each flight departure. And, since the various steps of the flight preparation from H-4 onwards are now well known, pulled flows and Kanban cards providing clear signals on upcoming or missed steps could also be the way to improve the visual management of the delivery. This is certainly not easy to implement along halls and gangways (digital tools could help here), but a sure way to on-time delivery and, beyond that, to agreeing on which problem to solve next.
Another idea would be launching a community of practice, to get a group of flight coordinators and check-in / boarding staff share their experiences to learn from each other and build up competence.
As we walk towards the exit, Agnès tells me the story of one European airport that has made on-time departure an overall company challenge. Their rating shot up and their ranking in the ACI surveys considerably improved. She firmly believes Orly can do the same.
THE AUTHOR
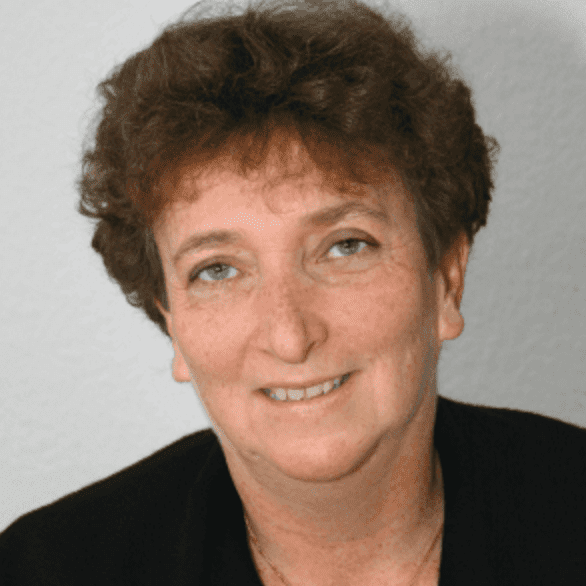
Read more
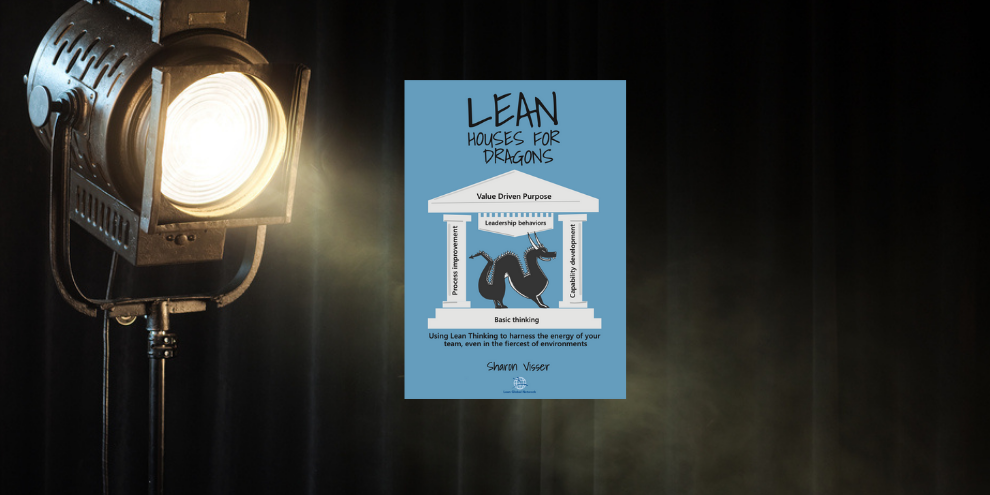
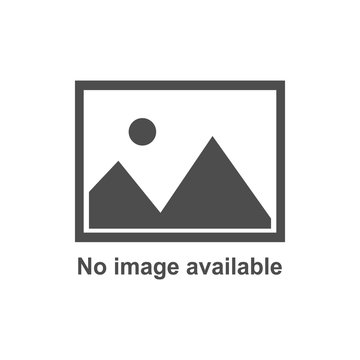
FEATURE – As her new book comes out, the author discusses how it is people who breathe life into an organization and how much a leader’s behavior can influence them.
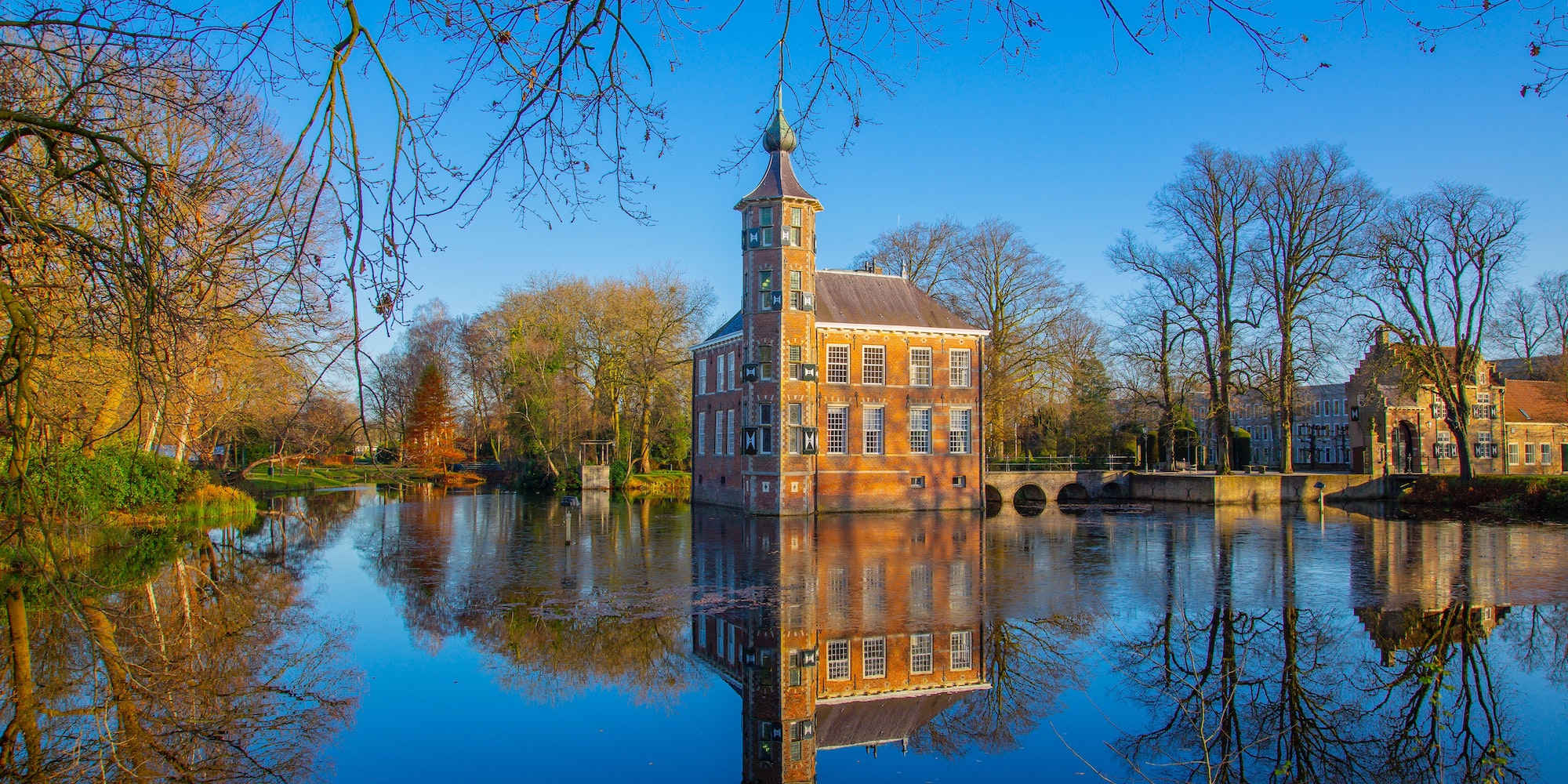
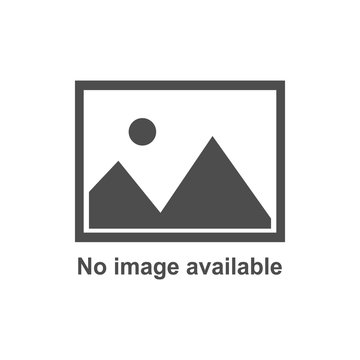
BOOK EXCERPT – The city of Breda in the Netherlands has been on a lean journey for the past six years. Today we share an excerpt from the book The Lean Government, which sets the scene for the transformation.
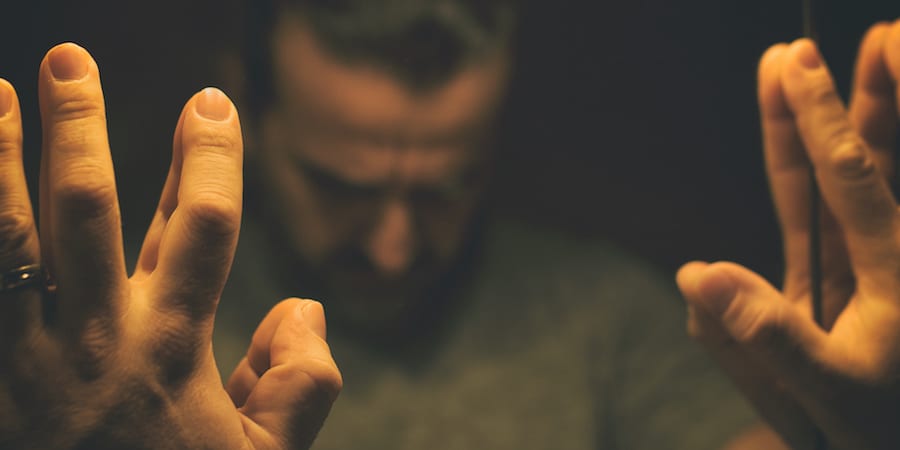
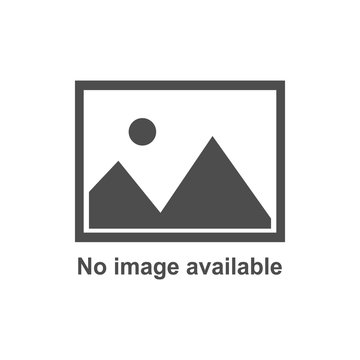
FEATURE – The role of experts in lean thinking is often the subject of heated discussions. Here, Michael Ballé tells us about the common mistakes lean experts make, and explains why – before helping others – they should help themselves.
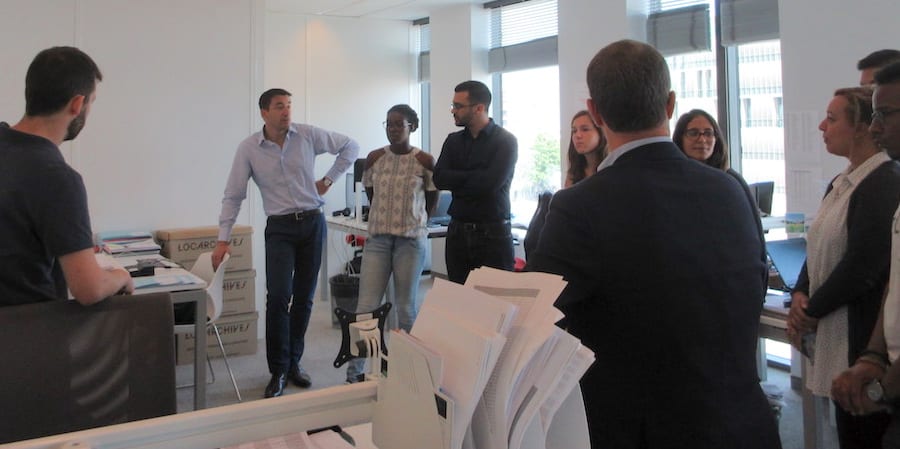
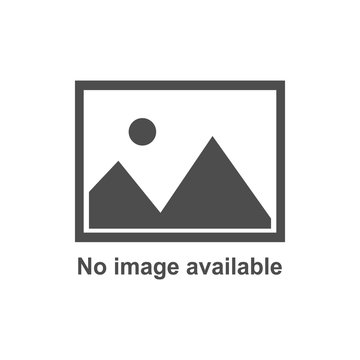
NOTES FROM THE GEMBA – Catherine’s gemba walks are back after the summer break. This month, she visits a start-up that is using lean to manage its growth, and learns about its management’s extraordinary turnaround.