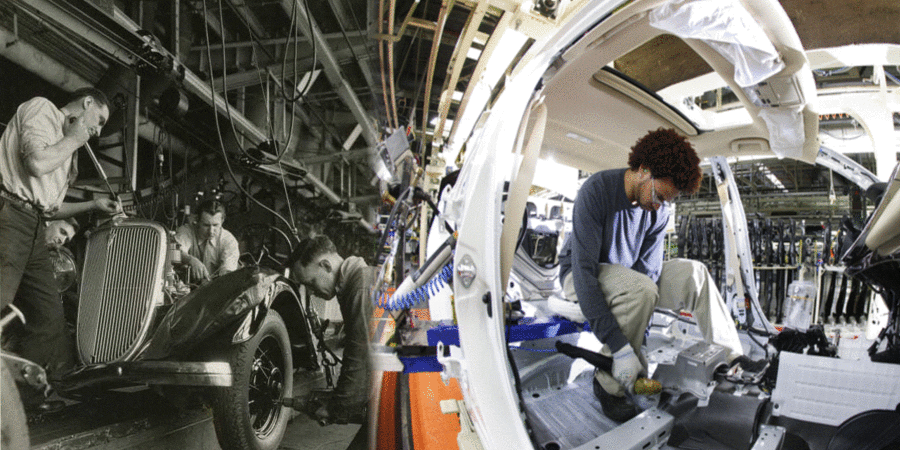
Lean Thinking: ingredients, incubation and diffusion
FEATURE – The author offers an overview of the ingredients that made lean thinking what it is, of the 30 years of incubation it underwent at Toyota, and of its diffusion from 1980 onwards.
Words: John Shook, Executive Chairman, Lean Enterprise Institute and Lean Global Network
Images courtesy of the Collections of The Henry Ford (left) and Toyota (right).
Editor’s Note: As we LGN members got ready for our week-long study mission to Toyota last September, we decided to prepare by conducting a few webinars for ourselves. Jim Morgan led a session about the Toyota New Global Architecture – Jim surely knows that subject matter better than anyone outside the company – since Toyota had promised us a deep-dive into TNGA during our visit. In addition to technical matters such as TNGA, we wanted to deep dive into cultural matters as well. To help us with this, John Shook ran a webinar on the “Toyota double-funnels”. I am excited to share this enlightening reflection with Planet Lean readers in this article. What follows is a transcript – edited lightly for readability – of John’s presentation.
It has long been accepted that lean thinking is not “uniquely Japanese”. For me, that has been a personal mantra since 1984, when I started teaching Toyota’s production and management systems to American employees of General Motors and UAW members.
But what does it really mean to say that lean thinking is not uniquely Japanese? First, it indicates that not all Japanese companies are “lean” – as demonstrated, for example, by the deep trouble in which companies like Sharp or Toshiba find themselves in recent years. Secondly, we have successful examples of lean applications all around the world – not just in Japan (in fact, the belief that lean practice apply everywhere is what holds us together as a Lean Global Network). We know these things to be true.
To say, however, that lean is not uniquely Japanese doesn’t mean that there is nothing Japanese about it. So, let’s explore this second, little explored, idea. And let’s do that in true Toyota style… by asking more questions. One critical question we can ask ourselves is: “Could have TPS emerged anywhere other than Japan?” And finally, “What, if anything, is Japanese about lean thinking?”
My attempt to address these questions – an ever-changing effort as I reflect more and the world around us keeps evolving – has taken the shape of the graph you see below, which illustrates what I call the “Toyota double funnels”. There are three main sections to the graphic:
- The left funnel represents a selection of key ingredients that, combined, have led to the creation of Toyota’s way of working.
- The spiral in the middle of the graphic represents the actual genesis of the Toyota Way, TPS, TPD, TMS and lean thinking, which can be traced back to a 30-year period of incubation, between 1950 and 1980.
- The right funnel represents the diffusion of this body of knowledge around the world, which started around the time of the NUMMI experiment, in 1984.
As you explore this graphic, keep in mind that the individual items are less important than the three phases. I have had to make choices, and my selection is essentially subjective. More importantly, it keeps changing! For example, in the ingredients funnel, I included John Dewey but not Max Weber. Elton Mayo but not Mary Jo Follet. I chose Galileo, but could have as easily chosen other similar early experimental scientist-craftsmen. Dan Heller, professor of operations management at University of Yokohama, noted that I had originally left out Peter Drucker. My intent is to be concise in the interest of fitting “everything” into one graphic illustration. I’ll defend the choices I made, though this would be best done over drinks at a bar. The important thing to take away from the left funnel is that Toyota’s system didn’t appear out of nowhere; rather, it was a synthesis of many influences (not just Ford, not just TWI, and not just Japanese culture). As I hope the graphic will show you, every piece of the Toyota puzzle has antecedents aplenty.
Probably more so than the items in the ingredients funnel, the items I’ve chosen to include (so far) in the diffusion funnel are going to be controversial. I routinely get asked why I didn’t include this or that. The graphic is also pretty USA-centric (sorry about that, although, in my defense, it is the Japan-US relationship that has dominated developments in Japan for most of the past century and a half, and that extends to business matters in general and Toyota in particular). A lot has happened in the years since Toyota’s way of working encountered the world, with small adaptations occurring every day and major mutations taking place each decade or so. In the graphic, I talk about diffusion, but also wonder whether we might not be facing the dilution of Toyota’s core message. Are the several schools of thought and interpretations of Toyota’s way and lean thinking positive system evolutions or aberrations? Is lean startup lean? It isn’t what Toyota does, but does the fact that Toyota operates differently automatically mean a practice is not lean? I don’t think so. The more relevant question to ask here is whether the practice (lean startup, TOC, scrum…) hold critical views that are incompatible with foundational Toyota views – also remembering that you don't know whether a mutation of any organic system is good or bad until later. I believe the spread of lean has been both a matter of diffusion and of dilution. I would add that, along with the dilution, there’s been more than a little delusion, aided by consultants selling things under the name of “lean” that are far from the original intent of the thinking, system and application (solving specific, fundamental business problems) that were developed in Toyota City during the 1950-1980 incubation period.
And as for the spiral of incubation itself, it would be easy enough to add more to it. The key message of this section is, in my mind, that Toyota got off to a good start in 1950, with a good foundation that had already been laid (in the 1980s, I benefited from countless hours of discussion with many of the old guys of Toyota, who would never fail to recall 1950 as the pivotal time of the company becoming what it became), but then worked it and worked it – kaizen and failures and problem solving and innovation and hard work – until it all gelled into something unique and powerful. Toyota’s system was pretty mature by the mid- to late 1970s (some say mid-1960s, but to say that requires defining many critical pieces far too narrowly). You could say that the 30-year incubation period is something of a microcosm of Japan’s 300 years of isolation from the rest of the world, when so many aspects of Japanese culture were born – with numerous influences imported from the outside – and refined.
THE AUTHOR
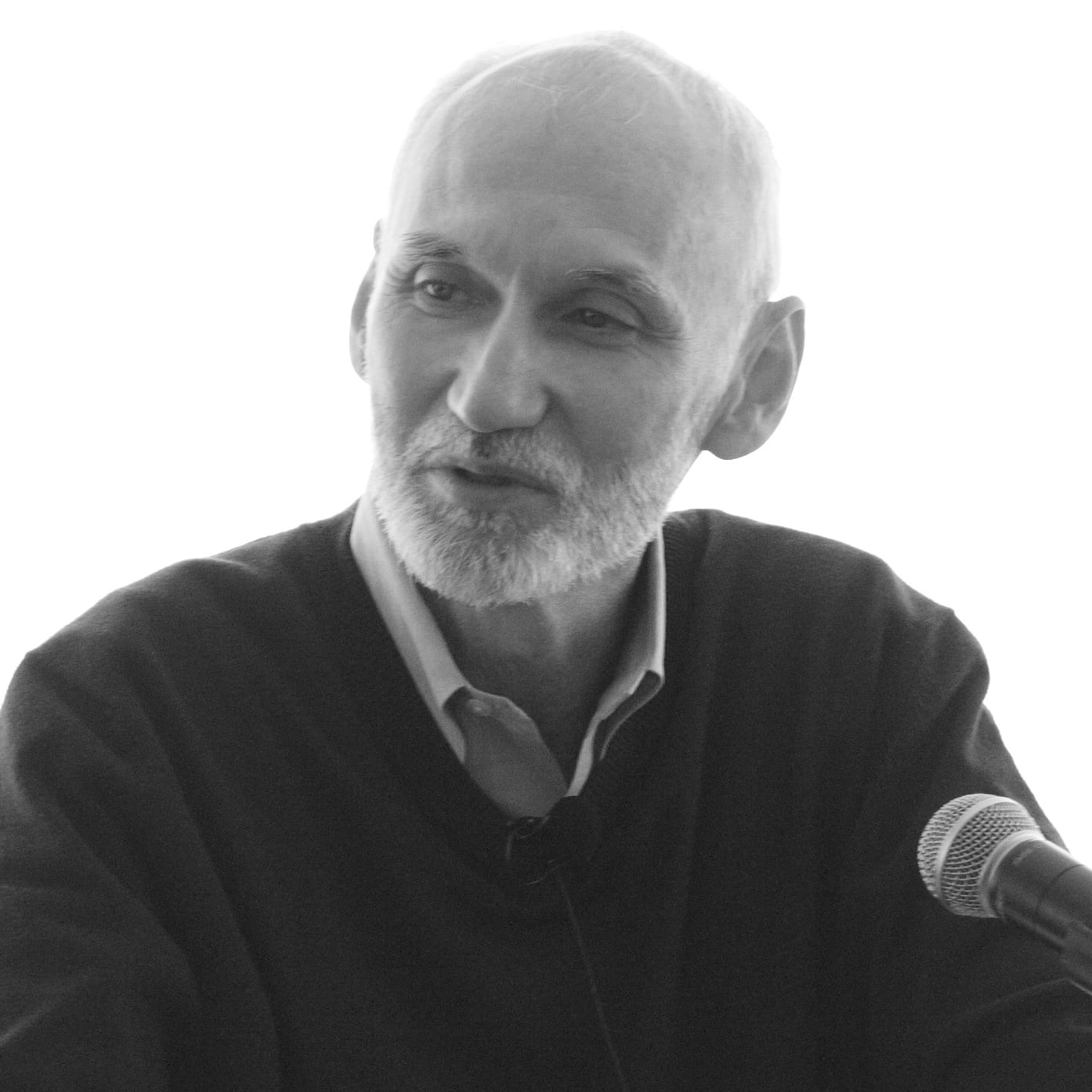
Read more
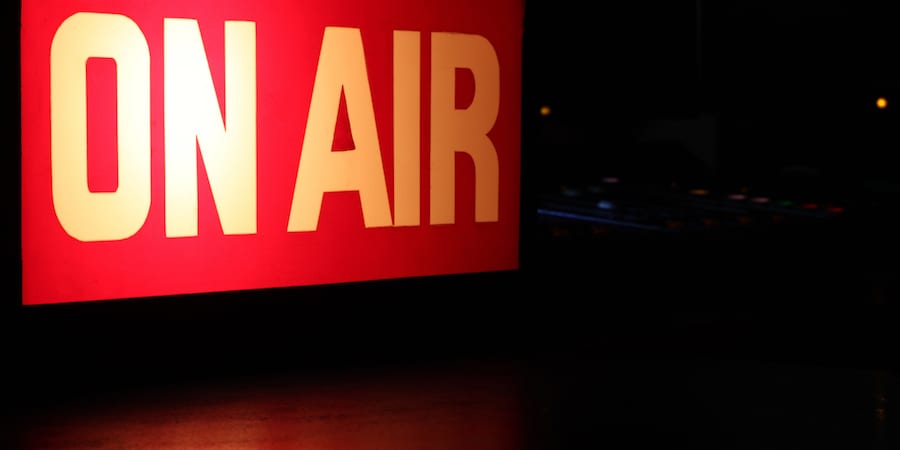
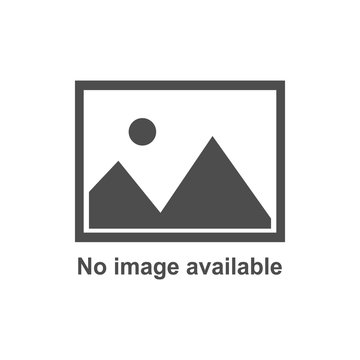
CASE STUDY – The Finnish Broadcasting Company has been leveraging lean thinking to scale up its agile work. In the process, it has developed a greater understanding of customer value.
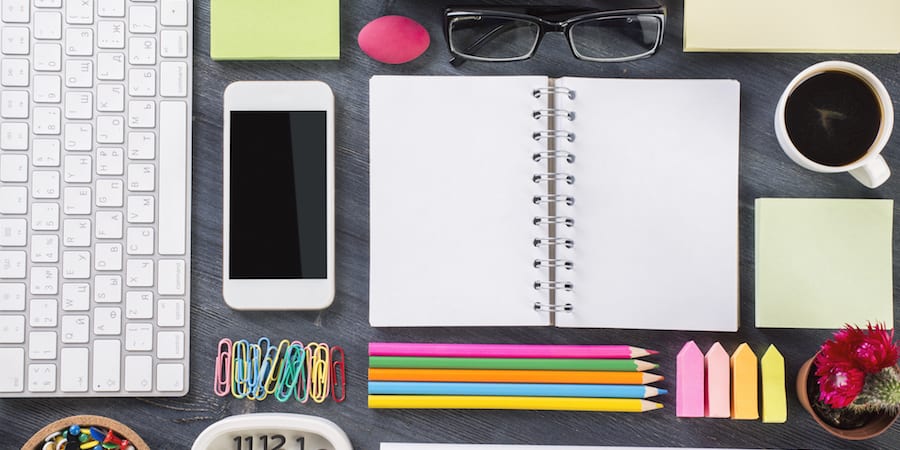
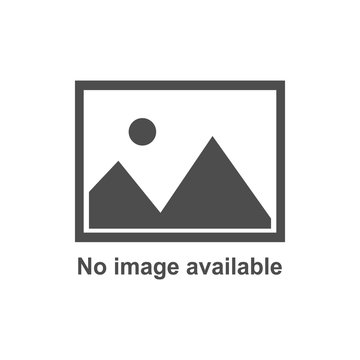
WOMACK’S YOKOTEN – 5S seems to mean different things to different people. What’s common, however, is the difficulty to sustain it. The author offers a few tips.
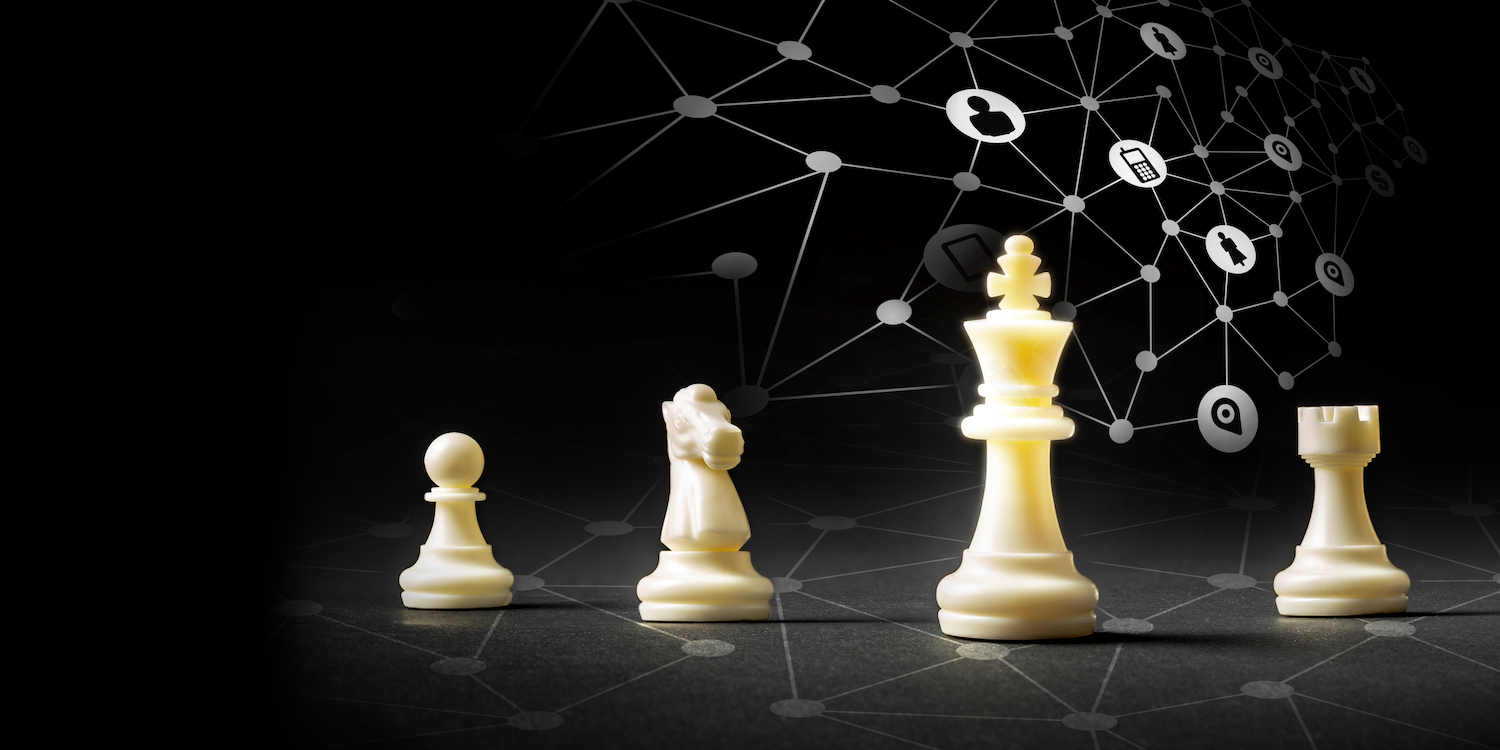
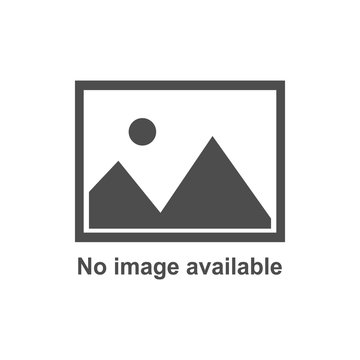
FEATURE – In many organizations, strategy is often lacking from the digital transformation agenda. The authors provide insights into how value chains and Wardley Maps can assist.
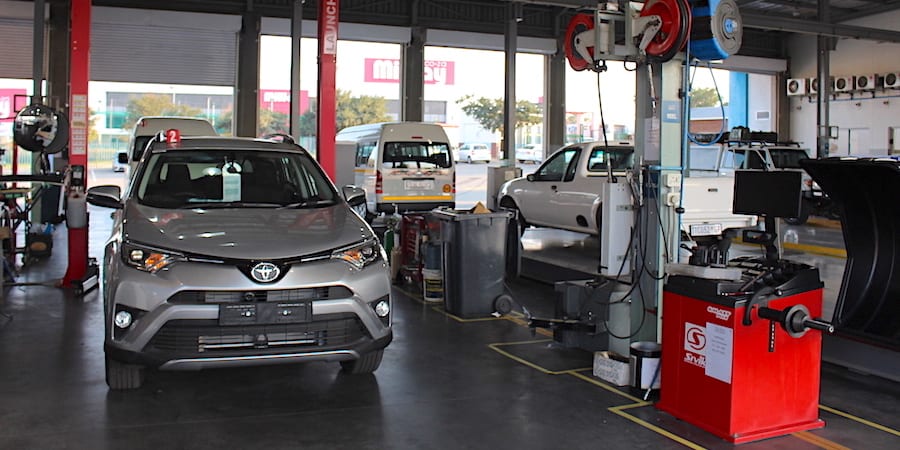
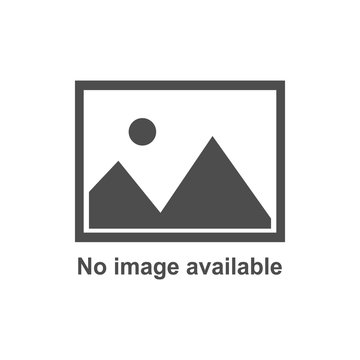
CASE STUDY – One-piece flow and a focus on lean leadership and kaizen have allowed the Halfway Production Centre in Johannesburg to turn itself around in just 14 months.