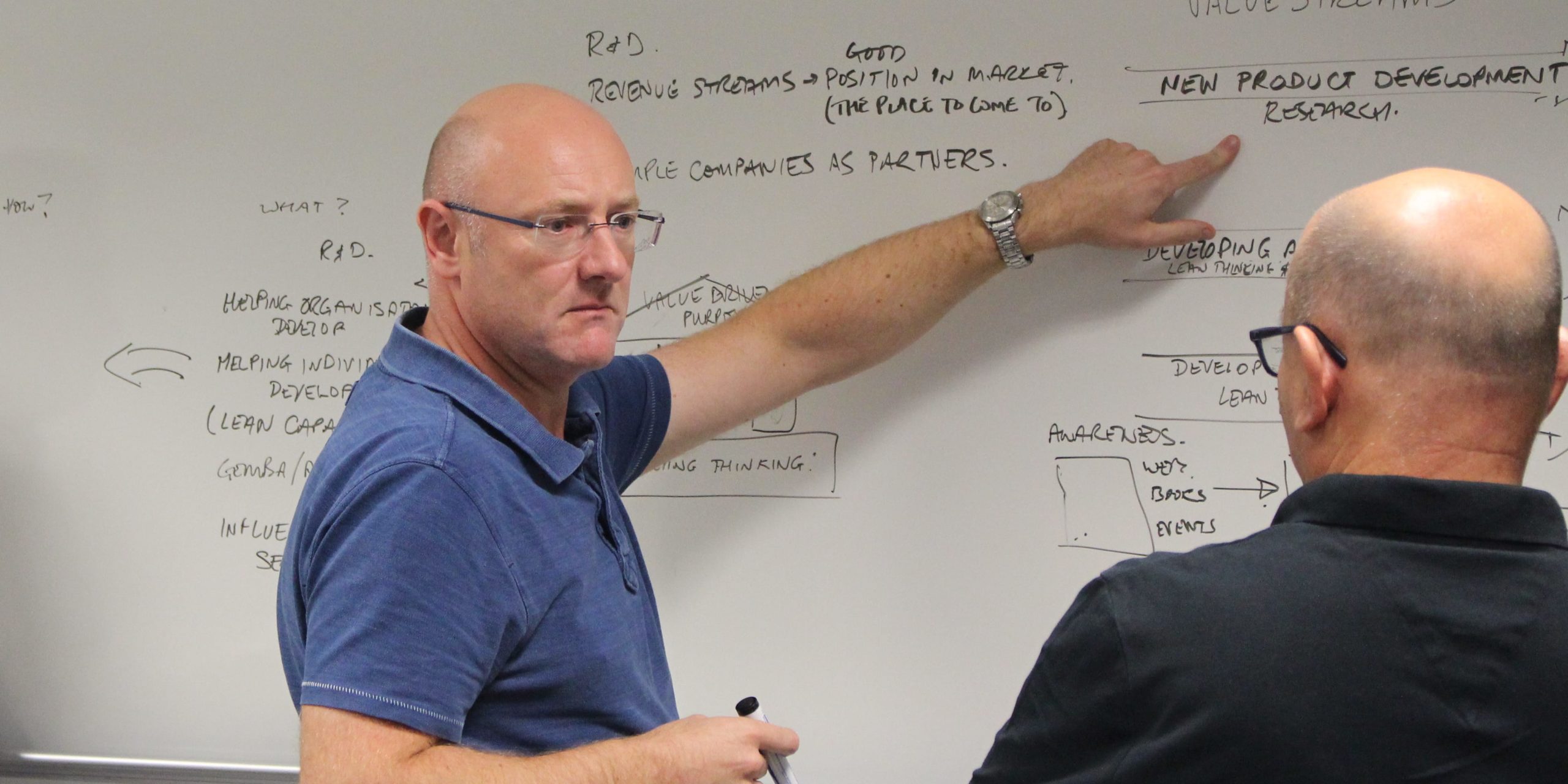
Living and breathing the original lean mission
GETTING TO KNOW US – It’s easy to over-complicate lean thinking. This month’s Lean Global Network interviewee tells us why we should always start with the work and the people doing it.
Interviewee: Dave Brunt, CEO, Lean Enterprise Academy – United Kingdom.
Roberto Priolo: How did you learn about lean in first place?
Dave Brunt: I was a graduate trainee (purchasing) at Rolls-Royce Motor Cars. We were supported by a group of consultants and I was seconded to a part-time team to look at purchasing. One of the consultants gave me The Machine that Changed the World. I read it and thought it was brilliant. It so succinctly described the issues required to be a lean enterprise and the gaps we had at the time. We started to learn about kaizen and I got to do some work with our suppliers. I realized the power of looking at the work and engaging the people who did it and I wanted to learn more.
I found out that Dan Jones was a professor at Cardiff Business School and that they had set up an MBA specializing in lean. I managed to get company sponsorship for the course. The rest, as they say, is history!
RP: How did your career change after that?
DB: The course at Cardiff taught me how important cross-functional management is and so I decided to get exposure in different areas of Rolls-Royce Motor Cars, rather than stay in purchasing. I worked for the quality director and then in customer service in Mulliner Park Ward, which made bespoke cars. When Rolls-Royce and Bentley were being sold to BMW and VW respectively, I decided to move on and went to work for Dan at the Lean Enterprise Research Centre (LERC) in Cardiff Business School. It was 1997, and I’ve worked for Dan ever since – even when I was asked to work as the Porsche Verbessurungs Process Manager at Porsche Cars Great Britain (which I did 3 days per week in the early 2000s).
Dan had a clear vision of what lean thinking could do for individuals, organizations and society at large, and needed people who were keen to engage others and conducts experiments in lots of different environments. At LERC, I was a researcher (I still think of myself as a researcher). We had a lot of fun! I’d report back on my findings and Dan (and sometimes Jim Womack) would write them up. During that time, I learnt an awful lot about what works and what doesn’t, and I can apply that learning in my current role.
When we set up LEA, I just carried on running experiments – applying lean thinking to different settings. We needed to differentiate ourselves from the consultants doing lean in order to stay independent and continue to research as opposed to help implement lean programs. That’s what I still do today: helping firms that really want to apply lean for the benefit of their customers, employees, shareholders and society at large.
RP: When LEA's Office Manager resigned last year, you were faced with a difficult situation that you were able to turn into an opportunity to streamline your internal processes. Can you tell us about it?
DB: Hannah was a fantastic office manager. When she decided she wanted a new challenge, I decided to try some experiments. As lean folks we tend to stick to visual whiteboards and manual processes (or cumbersome electronic processes at best), but technology has truly changed work and I decided to explore some of those opportunities.
Around the same time, we had started to experiment with online databases to compress the information flow into the physical flow at the Halfway Group in Africa. Could the same idea apply to our book fulfilment process and other key processes at LEA? There is no doubt that using Apps together with lean principles can greatly improve lead-times and transform the work required to support value-creating activities. We have learned a lot from this experiment, but two things struck me more than others. First of all, becoming proficient at something new is incredibly time consuming. Being a citizen developer (the manager who learns to understand the work and then develops Apps to eliminate waste from the work) is easier than ever, but finding the time is still difficult. Nonetheless, it’s the right thing to do and it is much more effective than using off-the-shelf solutions that don’t quite work or getting someone else to design something for you (that you then can’t change/apply kaizen to). Secondly, I was reminded of the importance of standardized work. If you don’t use it or you don’t document it during the App development process, there’s no foundation, no gap to close, and no learning. The fundamentals are still the fundamentals!
I’d encourage everyone to start to investigate these technologies. Very soon, they will be as ubiquitous as the spreadsheet.
RP: What are the most interesting activities LEA is carrying out right now?
DB: We are incredibly busy with a variety of projects in manufacturing, supply chain, lean product and process development and with organizations at the interface with end users. It is perhaps no coincidence that these were the four areas highlighted at the enterprise level in The Machine that Changed the World all those years ago.
Of course, my passion is the motor industry. There’s unprecedented change in the sector at the moment, as manufacturers seek to think through what it means to provide mobility. (This is what we mean by value when we buy a car – Dan and Jim wrote about this way back in 2005 in Lean Solutions and folks are finally realizing what they meant!) LEA is doing action research in this area, with a global network of Toyota dealers that are conducting experiments with us. We are learning so much from this, and a lot of it has been published here on Planet Lean. There’s much more to come, no doubt. Unfortunately, we haven’t found a Toyota dealer in the UK yet, so I have to keep travelling to keep learning.
We have also volunteered our time to support the The Learning Trust in Chester and we will organize an event with them next year to share and inspire others with an interest in lean education and learning. This is very exciting work. I believe that the level of lean education currently available is generally pretty poor, with much of it revolving around accreditations and certifications rather than capability. I hope the experiments at Christleton articulate a much higher purpose that goes beyond education to thinking more in terms of life-long learning.
RP: What is the state of lean in the United Kingdom at the moment?
DB: Take a look at LinkedIn and you’ll see there are lots of experts in the UK. My remarks here come with a health warning: there’s always more improvement to be had and more to do.
There is no doubt that we (and others) have successfully spread the “lean word”, which means that lots of people have heard about it and claim to be embracing it. That said, I am not so sure how successful these firms are actually being at developing their lean thinking. I say this because of the UK’s stagnating top-line productivity figures. Are we getting the dramatic productivity improvement that we know lean thinking can help us achieve? The figures suggest not.
I often hear lean being associated with job losses and restructuring, but this isn’t lean thinking at all. The same is true for outsiders asked to assist an organization and only grabbing at low-hanging fruit, who conveniently borrow some of the tools and techniques and use them to eliminate waste as a one-off. This can’t be considered lean thinking.
I’m also concerned that lean has become a profession. Lean is not a project or a program, and it needs to be embedded into line management activities. It can’t be reduced to the work of a few experts, but unfortunately that’s how it is increasingly being portrayed.
On a more positive note, it is good to see examples of lean being introduced in product and process development, supply chain and customer interface – and not just operations – across the United Kingdom. There are big opportunities to do this in technology (with the App-style work discussed above) and with SMEs, which I think the UK is well positioned to support.
RP: Has your attitude towards lean changed over time?
DB: I’m still as enthusiastic about the opportunities that lean thinking can bring as I’ve always been. But I’ve certainly mellowed! I’ve learned to be a lot more patient about progress and I’ve realized that there are only certain things that folks on the outside of an organization can do. I am also disappointed when people make lean complicated. I think it’s really quite simple, if difficult to do at times. What’s also changed is that I pick and choose what I want to work on. For example, I am really interested in working with firms over a long period of time: this narrow and deep work holds a lot of learning opportunities and reflection on such activity is difficult for many in the lean community.
RP: What's next for LEA?
DB: The needs of our customers have changed dramatically since we started LEA, and we need to recognize this and adapt. We have a lot of ideas and we are going to test some hypotheses around what we have heard from customers, to see how we can provide them with better value. We will run these experiments under the radar (as we do with all our research) until we are ready to broadcast them.
I think you will see us integrating the things we do for customers – from books to information on the web, from events to education, from our research to our co-learning projects – instead of treating them as discrete offerings: we want these to be items the community can “pull” as part of their life-long journey of lean learning. To do this, we will continue to collaborate with our partners in the UK and overseas – starting with other members of the Lean Global Network, of course.
RP: Speaking of LGN, what’s its current state and how can we move to our ideal state?
DB: When Dan and Jim set up LGN, I am sure they didn’t realize what they were taking on. The network is developing into an amazing organization. It really is like the United Nations of Lean! LGN gives everyone in it (and to those engaging with it) the opportunity to learn and share. It’s a hotbed of ideas and experiences - and that’s why it’s so important to be part of it and to contribute to it.
As ever, there are opportunities to do more and better. The key to the network improving is practicing what we preach: conducting systematic PDCA on our activities and continuing to refine our purpose to improve the work. Practically speaking, this means developing standardized work inside and across institutes and constantly reflecting upon our efforts.
THE INTERVIEWEE
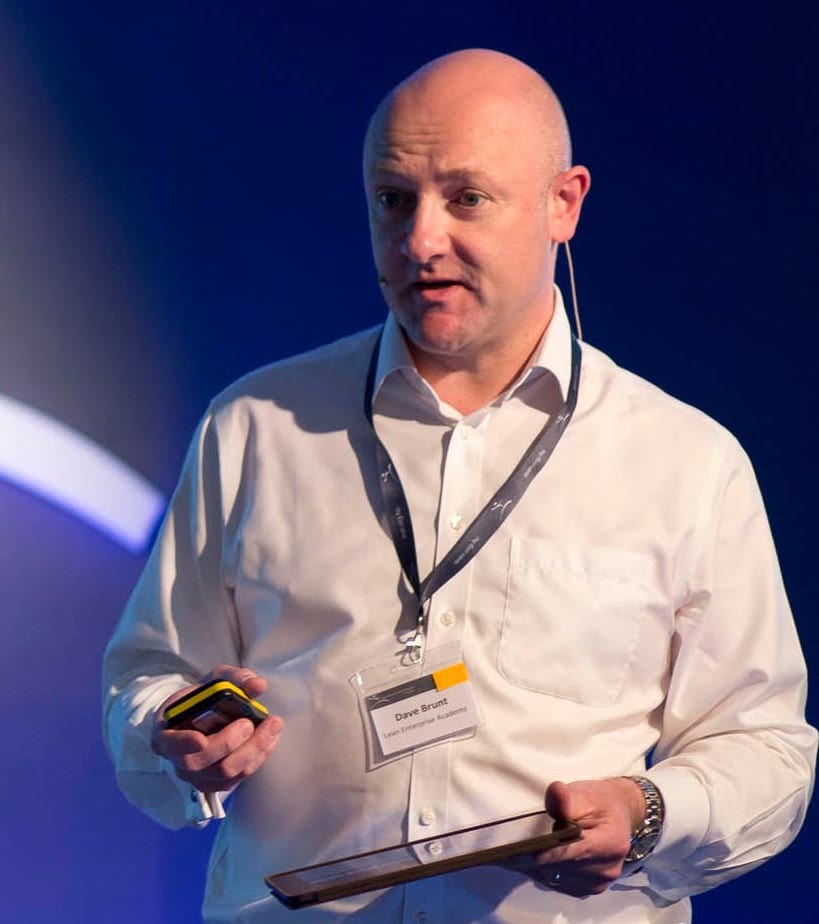
Read more
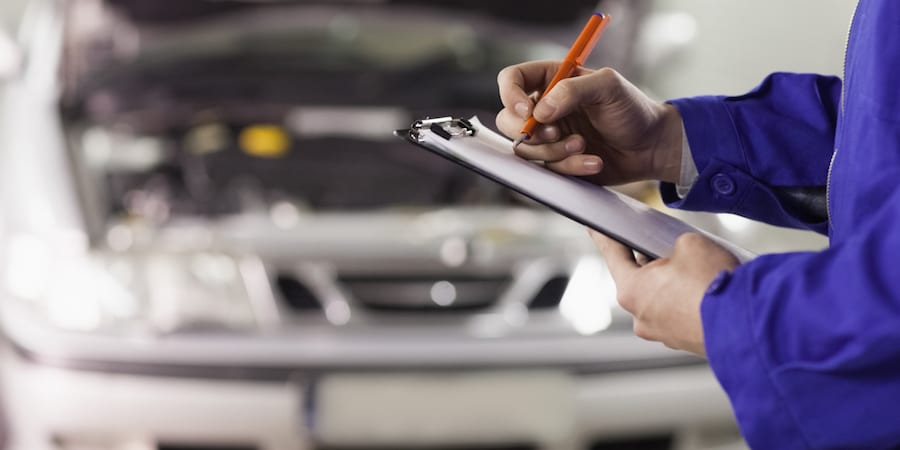
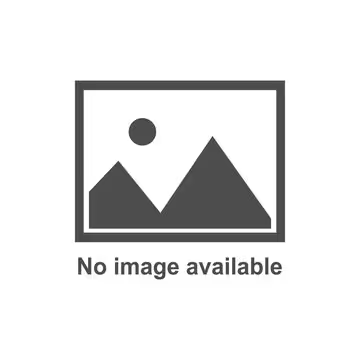
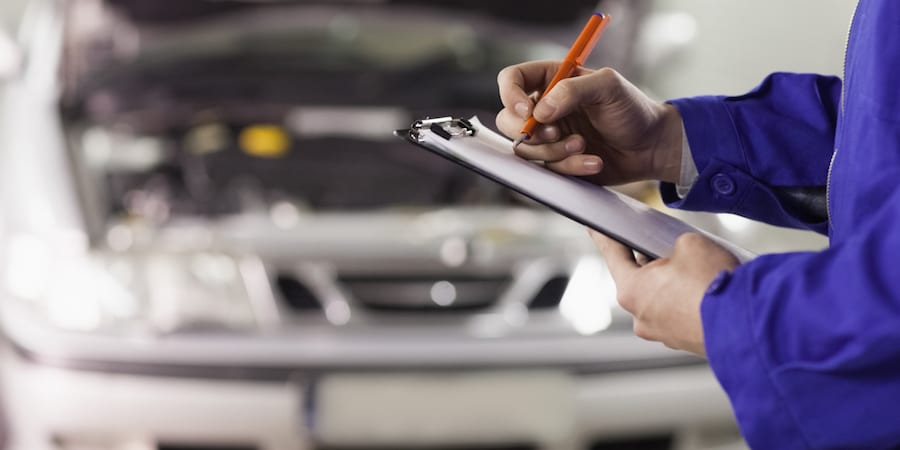
WOMACK'S YOKOTEN – In our lean journeys we spend so much time on improvement (kaizen) and innovation (kaikaku) that we often forget to address the issue of how to maintain our gains. Do you know iji? Perhaps you should.
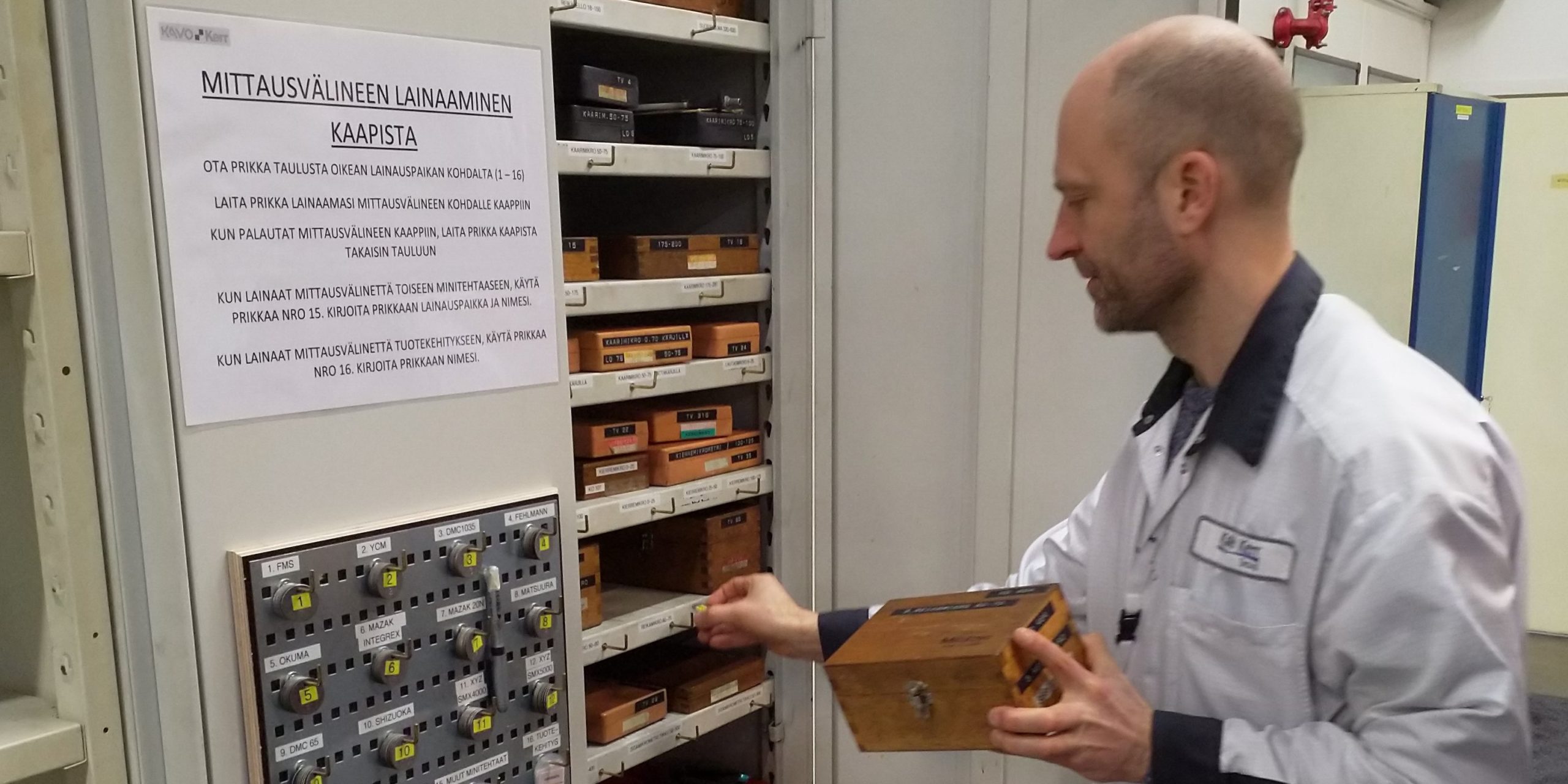
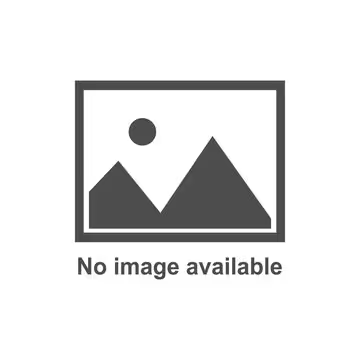
FEATURE – When people become enthusiastic about improvement work, there's no limit to what can be achieved. Join the author on a visit to a Finland-based manufacturer, whose lean efforts range from production to customer service.
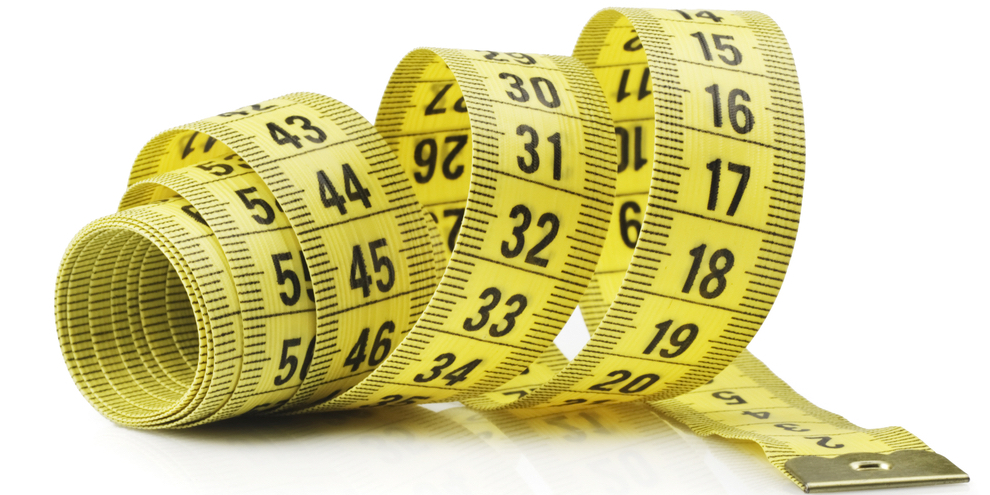
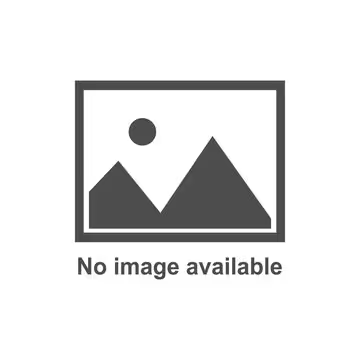
FEATURE – Pure and simple management by indicators can be a trap leading us to make decisions that are inconsistent with the real needs of a company. The balance between facts and data is key.
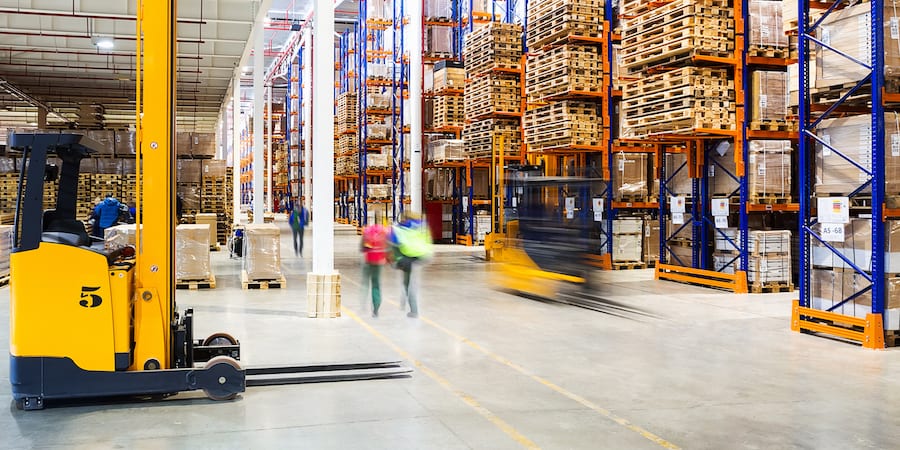
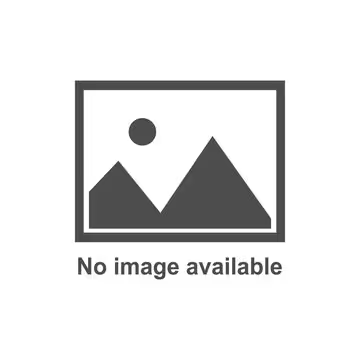
COLUMN – Want to grasp the current situation? Then you must go to the gemba, but it would be a mistake to think that alone is enough to change your business… you also have to ask why and show respect.