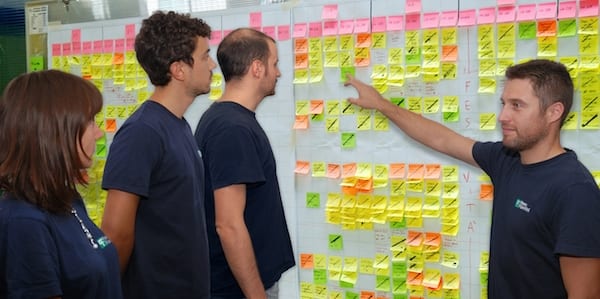
How Pietro Fiorentini became Italy's lean champion
CASE STUDY – A unique approach to lean management and the involvement of CEO Mario Nardi helped Pietro Fiorentini, provider of solutions for natural gas distribution, become a model for lean companies in Italy.
Words: Arnaldo Camuffo, Professor of Business Organization at Bocconi University and President of Istituto Lean Management, Italy
There is an increasing interest among lean practitioners and researchers in how to successfully lead a transformation, which - at a high level - is a comprehensive, large-scale organizational experiment. Given the risks inherent to such ground-shaking changes and the potentially harmful effects of their failure on a variety of internal and external stakeholders, understanding the dynamics of a lean transformation becomes critical.
To this end, the Lean Global Network and its affiliate institutes around the world have adopted a common framework, originally developed by John Shook at the Lean Enterprise Institute. The Lean Transformation Model comprises of five key questions entrepreneurs and managers need to ask themselves and their management teams during a lean transformation.
Answering these five questions, developing metrics to understand if there is progress in the corresponding dimensions, and ensuring consistency and alignment among them is a process that, over time, can lead to a radically transformed organization.
In the video below, John Shook explains the Lean Transformation Model.
In this short article, I am looking at the application of the Model to what is often regarded as the most successful case of lean transformation in Italy, that of Pietro Fiorentini, a provider of technology and services used for the distribution, transport, and utilization of natural gas.
BACKGROUND
Milan-born Mario Nardi is the prototype of how we would like Italian entrepreneurs to be: young, worldly, competent, brave and above all fiercely dedicated to making his business thrive.
He used lean thinking not only to design the company's production system, but also to shape its management style, corporate culture, and - why not – his own life philosophy. The transformation of his family business began in 2000, and since then the company has experienced continuous growth and generated value for shareholders and jobs for Italians.
At the time, Pietro Fiorentini was one of many medium-sized mechanical and engineering companies in the province of Vicenza. Founded by Mario's grandfather in 1938 during Fascism, the organization succeeded thanks to a patent for a somehow curious control valve for LPG cars (during the regime, restrictions often forced vehicles to carry a gas tank on the roof, which required an adjustment in the transmission and distribution of gas from the tank to the engine). It enjoyed the "long wave" of the legendary boom of the Northeast of Italy, but arrived at the end of the 1990s with profitability and growth problems.
Mario and his brothers Cristiano and Paolo took over the reins of the company and changed its course by making lean thinking - accurately re-interpreted - their guiding principle. They originally defined the strategic problem they needed to solve as one of operational efficiency and productivity, but soon realized that this was intimately linked with market positioning and growth opportunities.
WHAT WAS THE PROBLEM THEY WERE TRYING TO SOLVE?
What is unique to Pietro Fiorentini is the company's absolute clarity over the effects of lean thinking not only on its production department but also on its market positioning and on its economic and financial wellbeing.
Mario's interpretation of lean is quite unique: most firms talk about it in terms of "efficiency" (that is, cost reduction) and tend to see it as a quick remedy (sometimes a bitter medicine, perhaps) to solve business problems. If used for the sole purpose of "efficiency," however, lean results in temporary and limited cost reductions, but not in the elimination of problems. But Pietro Fiorentini's approach was to link continuous product and process improvements to market positioning and financial performance: through hoshin kanri, on one hand Mario and his team asked themselves whether the business was on the right track and the business model appropriate; on the other hand, they systematically evaluated the effects of decisions on financial dynamics at corporate level, in order to improve the company's net financial positioning and free up the resources needed for investment and growth.
PROCESS IMPROVEMENT
Pietro Fiorentini's transformation started right on the shop floor, where Mario applied his kaizen-based, restless, and demanding spirit to the performance improvement of a small set of operational processes in the main plant, near the city of Vicenza. At first, he allowed for the achievement of small improvements to build confidence as capability was also developed in the organization; once buy-in was secured, he enlarged the scope of the transformation process.
He soon realized that lean thinking was not just a set of practices aimed at improving operational performance (namely reducing costs), but a management system applicable to all business processes (including management processes) for the sustainable generation of value. The first example of this newly acquired conception of lean was the extensive use of the scientific method in strategic planning.
Pietro Fiorentini operates through a complex process of strategy deployment, structured as a portfolio of improvement projects (A3) and involving the entire organizational structure. This corporate planning and control process, which was perfected over the years, effectively replaces the budgeting process, eliminating its typical pitfalls and internal politics, aligning decisions to company goals, and improving the internal allocation of financial and organizational resources.
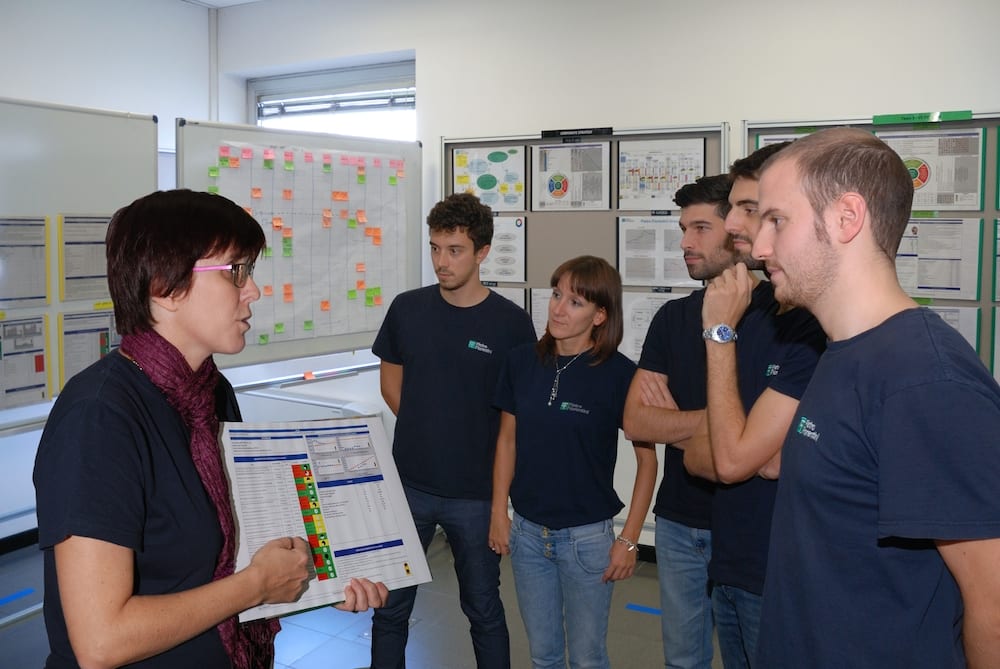
HOW ARE THEY BUILDING CAPABILITY?
Despite being a medium sized business, Pietro Fiorentini extensively and consistently invested significant amounts of money in lean knowledge. This resulted, first and foremost, in many resources being put towards training production staff and young people (especially engineers selected with great rigor from the best Italian universities, including Padua University, Polytechnic of Milan, and Bocconi University) and external training courses (often with Istituto Lean Management of Italy and other LGN affiliates), alternated with internal training activities and experimentations on the field - in factories, technical departments, and more generally in offices.
This mix of activities has allowed for the systematic dissemination of lean knowledge at all levels of the company. Ten years worth of this type of training investments resulted in the establishment of a team of highly skilled and motivated managers, engineers and workers, perhaps unseen anywhere else in Italy, whose energy and enthusiasm in applying lean thinking are immediately evident upon going on a gemba walk at the organization.
The massive and ongoing investment in knowledge also translated into the acquisition of the best international expertise in the field.
In the first place, Pietro Fiorentini gradually formed an internal unit of specialists, and in doing so it did not scrimp and save on resources (neither in terms of quantity not in terms of quality), to the point of even hiring at one point in time a specialist from Boeing as head of the Kaizen Promotion Office. In the 1990s, this man was at the core of a monumentally innovative lean transformation.
The establishment of this office was accompanied by a detailed and judicious use of consultancies. With regards to this, two elements of the experience of Pietro Fiorentini are particularly striking: the first is the use of a number of different consultants, each in their own specialization area, according to specific business needs; the second is the exclusive use of national and international excellence with a proven track record of supporting successful transformations. Thus, in Pietro Fiorentini factories one can encounter the best lean application skills available internationally, running into Chihiro Nakao, a student of Taiichi Ohno and founder of Shingjiutsu, or into John Black, who implemented the lean transformation at Boeing (which led to the famous B737 moving assembly line) with Carolyn Corvi. They might meet Mike Rona, former President of the Virginia Mason Medical Centre, or Tom Jackson, one of the world's leading experts on hoshin kanri.
Through this approach, the organization has avoided the common pitfall of exclusively relying on consultancies for the launch and implementation of lean, with the dual negative result of becoming dependent on external resources for continuous improvement and of achieving only sporadic, short-term improvements.
Pietro Fiorentini has instead become a place of experimentation, in which the knowledge, approaches and methodologies of the best consulting firms are compared and combined with internal knowledge and with the enthusiasm and energy of the company's people. Indeed, it is a unique production and management model.
WHAT LEADERSHIP BEHAVIORS AND MANAGEMENT SYSTEMS SUPPORT THIS NEW WAY OF WORKING?
Not only did Mario support and sponsor the transformation, but he also was the true creator and "engine" of the application of lean at Pietro Fiorentini. The support he provided was not limited to leadership promoting "a lean project," as it is often the case in the average organizational change initiative. Instead, it meant that he was fully involved in the lean journey, becoming its initiator and driver. He led the transformation firsthand, for example by taking part in every activity of the process, from the redesigning of the layout to the creation of manufacturing cells and the launch of kaizen weeks.
This was only possible because of Mario's profound understanding of the principles and techniques of lean thinking, which comes from direct experience gained through years of studying (his lean library is quite impressive), through his relationship with academics and national and international thought leaders (from Jim Womack to Chihiro Nakao and George Koenigsaecker, just to mention three senseis), and through his discussions at gembas around the world (not only in Toyota factories).
Simply put, Mario has been the leader and sensei of the transformation of Pietro Fiorentini. Humble and committed, he often questioned himself and hugely invested in his own capabilities and understanding, deciding to learn the theory and practice of lean and putting himself in the shoes of the deshi (student).
The secret to the success of "Super (Lean) Mario" also lies in his leadership style, a blend of humility, rigor and determination. Above all, he believes in the power of relying on facts and empirical evidence as the basis for any decision-making and on human intelligence as a weapon to solve problems.
WHAT BASIC THINKING UNDERLIE THE EXISTING CULTURE?
Five traits permeate Pietro Fiorentini's organizational culture, which are very evident immediately after stepping into the company's gemba:
- The primacy of action, the number and frequency of experiments (conducted by everybody at all levels), and the reliance on empirical evidence to make decisions about alternative courses of action;
- The role of management in creating commitment to a common purpose that overcomes internal boundaries, establishing cross-functional processes and structures and promoting collaboration among departments;
- The constant sustainment of lean operational practices guaranteeing that they become organizational routines and that the improved processes become new standards;
- Performance measurements based on process measures (and not only on outcome measures);
- The belief that people can learn and improve and that it is necessary to create an open and collaborative context promoting a continuous improvement culture.
In a way, this lean transformation is an archetype, a textbook example. It's no surprise that today Pietro Fiorentini is one of the most visited lean companies in Italy, a destination of "pilgrimages" for entrepreneurs and managers who are searching for a role model for the adoption of lean management principles and aspire to learn from Mario Nardi's experience.
THE AUTHOR
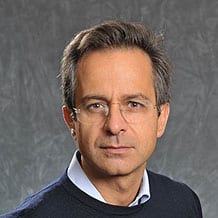
Read more
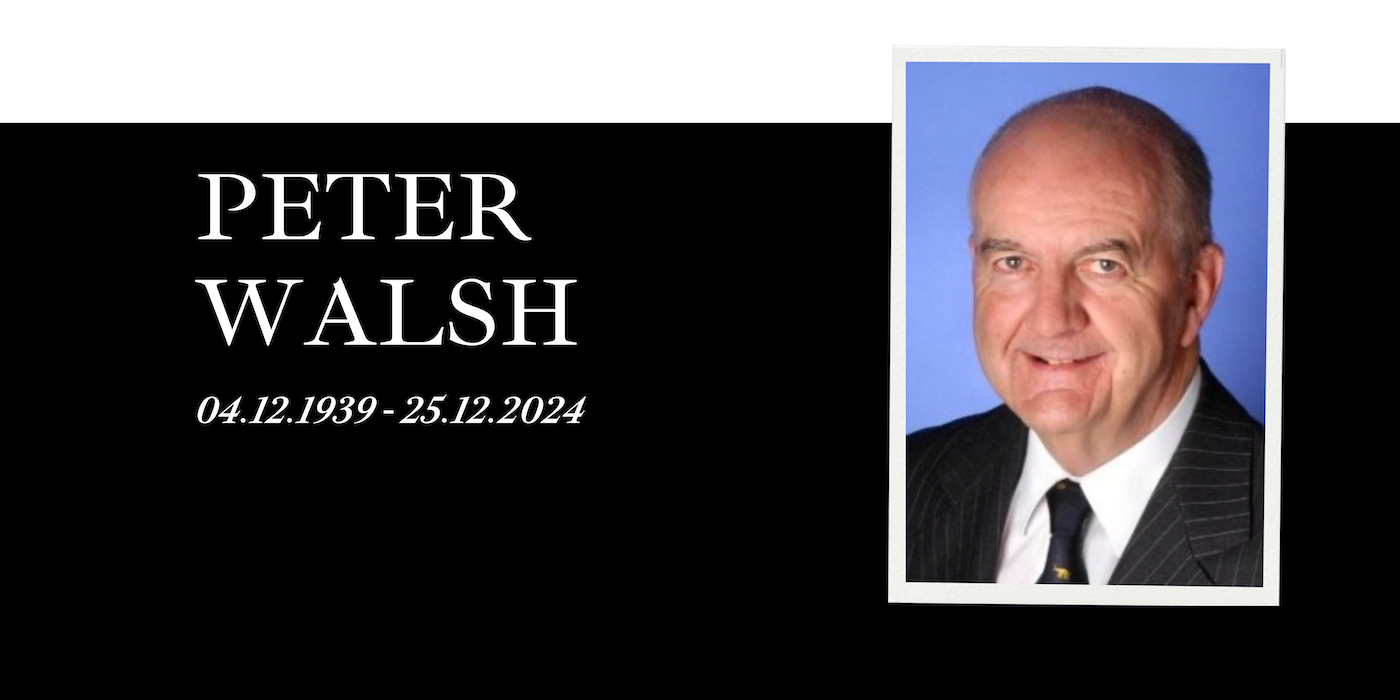
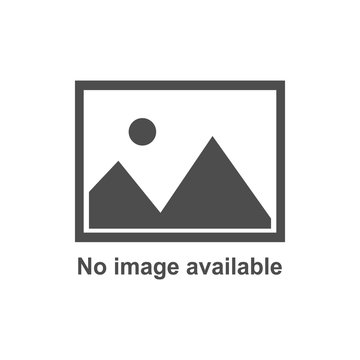
FEATURE - With heavy hearts, we share the news of the passing of Peter Walsh, a pioneer of the Lean Community. Peter's work was instrumental in allowing Lean Thinking to take root in Australia, as some of those who knew him tell us here.
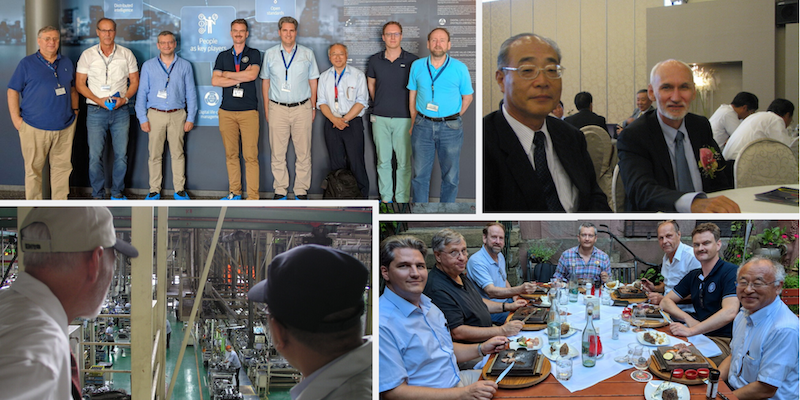
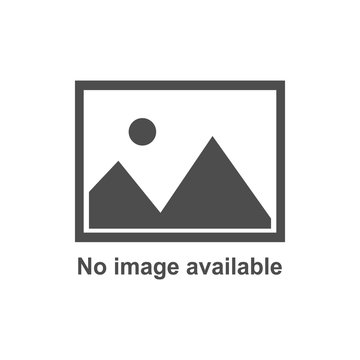
FEATURE – 2019 was another momentous year for the Lean Community. John Shook reflects on what we lost and what we gained in the last year of the decade.
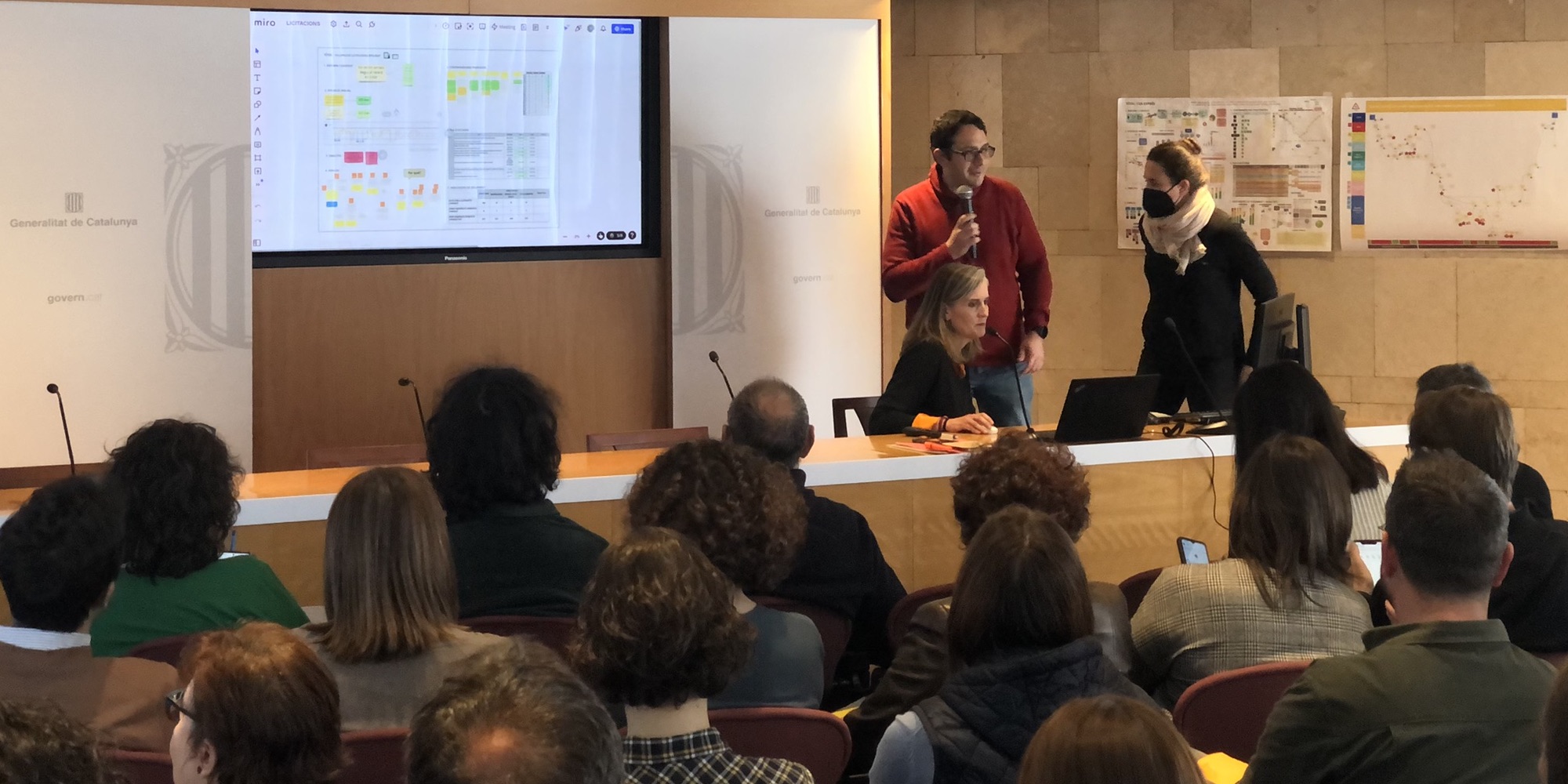
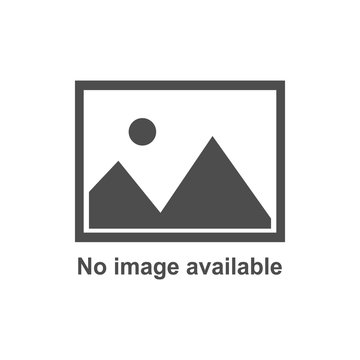
FEATURE – At a recent Lean Day, our editor was reminded of the immense potential of Lean Thinking applied to government. After a few sleepy years, is lean in the public administration having a comeback?
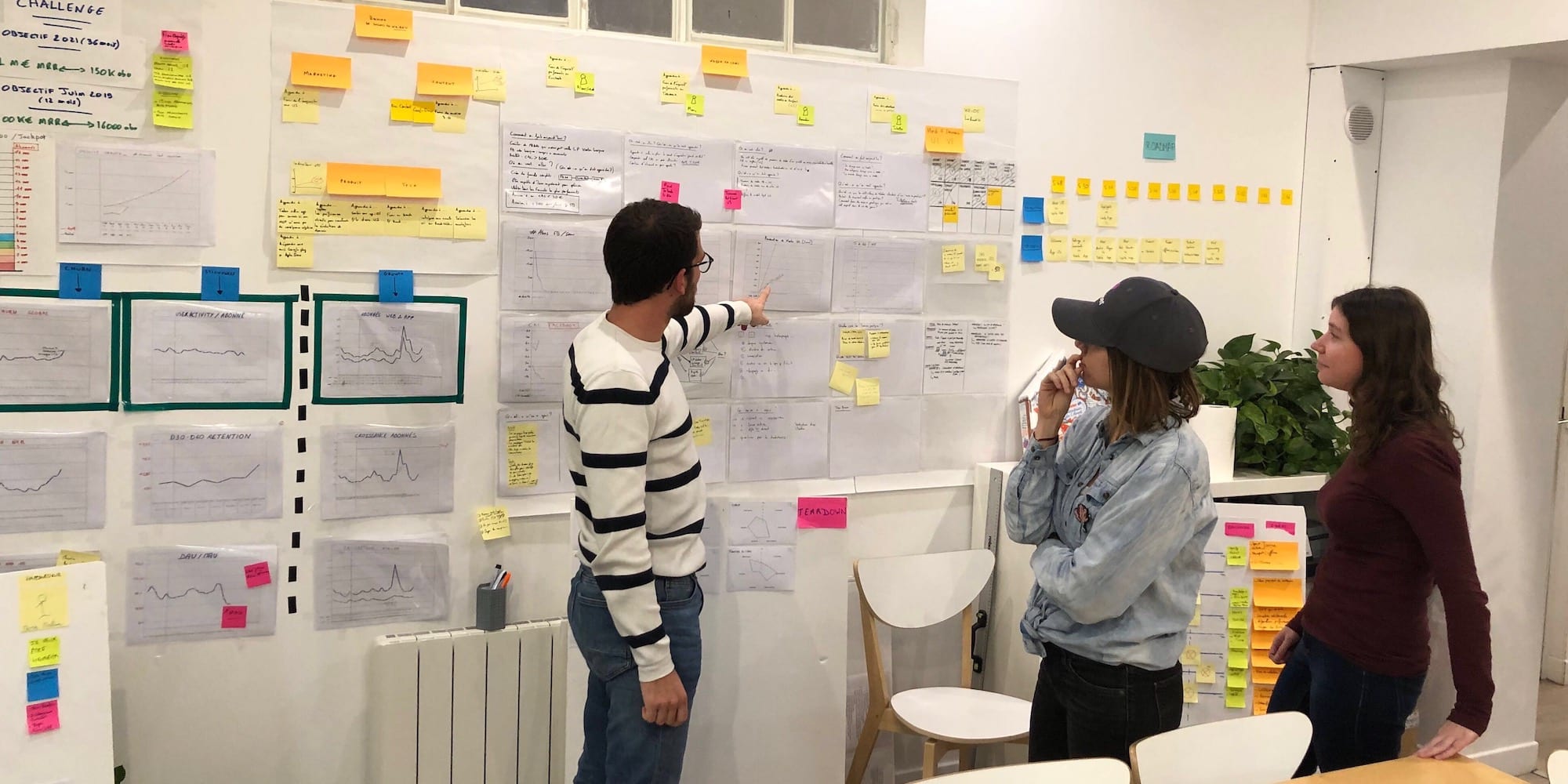
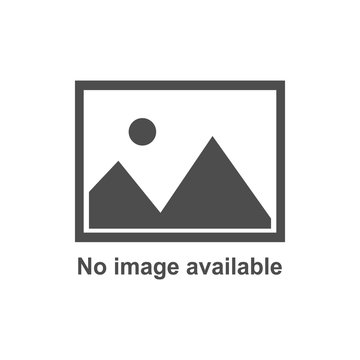
FEATURE – The obeya room limits the number of unknowns before we start developing a product. In this sense, it’s a tool for discovery more than it is for delivery.