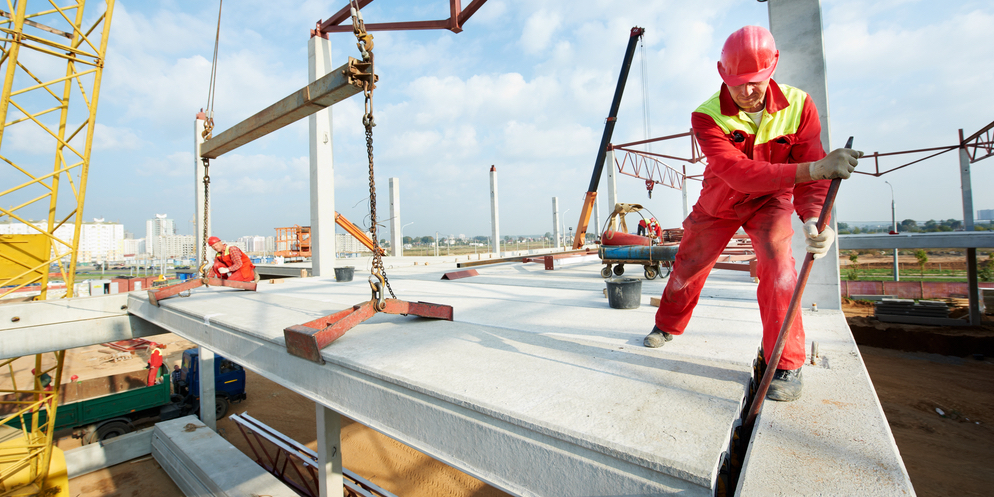
Developing problem solvers to advance lean construction
FEATURE – Construction is rife with waste, and yet lean is not widely adopted in the industry. The authors highlight how lean could benefit the sector, emphasizing the importance of developing problem-solving capabilities.
Words: The LGN Lean Construction Working Group
As far as work goes, it is hard to deny the complexity that construction companies face on a daily basis. In part, this is the result of the diversity in the types of projects that they take on (from infrastructure to residential and mining), but also of the difficulty of coordinating and integrating the work of several players – including owners, designers, suppliers, contractors and subcontractors – throughout the process, from planning to product delivery and aftersales. Quality self-control is all but missing, and incomplete designs often cause errors, delays, cost overruns and rework. Add to the mix a common lack of leadership across the value chain, stressful working conditions at the front line, adversarial relationships in the traditional Design-Bid-Build contracting system and a tendency to not trust that people (at all levels) can really solve problems, and you might be excused for thinking that construction is beyond saving.
And yet, this traditional industry is evolving. As a movement, construction industrialization – inspired by manufacturing techniques – has existed since after World War 2, when the need to rebuild entire countries put pressure on the sector to deliver faster than it ever had. In recent years, we have seen a new wave of industrialization, with innovative offsite techniques like modular construction, jobsite assembly rationalization, and advances in digital technologies (such as BIM, Building Information Modeling, and new planning and management software).
In this new stage in its evolution, construction is also showing an increased interest in Lean Thinking. More companies are realizing that lean can bring a deep transformation to this industry, as it did in almost all economic sectors. With a few notable exceptions, however, construction companies still tend to perceive lean as mere process improvement. What happened with lean in manufacturing 40 years ago, when people thought all there was to it was Kanban and a bunch of other tools, is happening today in construction. What’s worse is that the improvement work is often taking place in isolation – perhaps in one job site – and even when it leads to good results the fact that the rest of the organization has no exposure to lean makes progress limited and hard to sustain.
At the Lean Global Network, we aim to help companies to achieve a sustainable lean transformation by addressing five dimensions of our very own Lean Transformation Framework (LTF): value-driven purpose, improving processes, developing capabilities, changing management systems and leadership behaviors, and transforming mental models. If we look at construction from the perspective of the LTF, one can see that most of the improvement work in this sector is limited to the process pillar of those five dimensions. Even then, it only touches on the planning stage. Indeed, in a project-based industry like construction, planning is fundamental, which makes the commonly used Last Planner System a valuable tool for organizations interested in achieving some basic stability. But there is much more to lean construction that just Last Planner!
The LTF teaches us there is much more to explore here. What can we say about people development in construction? Can construction companies define value for customers well enough? How often do managers in construction go to the gemba to see the work with their own eyes, listen and provide support to people as they try to solve problems? Does the management team understand the value stream in detail, from start to finish, and work with the team on the ground to improve it as a whole?
In the construction industry, lean is still not seen as a strategic asset that can transform the entire organization – and its culture – by turning front-line workers into autonomous problem solvers so that more value can be provided to the end customer. We believe that it is about time that changed. A broader adoption of Lean Thinking as a socio-technical management system is fundamental to help the industry to overcome its most pressing issues, like safety, cost overruns, low productivity (according to OECD data, productivity in construction hasn’t changed in 20 years), quality problems, and chronic delays.
DEVELOPING PROBLEM SOLVERS IN CONSTRUCTION
To solve the problems highlighted above, however, we need to primarily focus our efforts on developing the problem-solving skills of everyone, from top executives to foremen, from tradesmen on site to employees working in supporting functions. But what does it take to create an army of problem solvers in the construction sector? In our mind, it requires us to provide people with the ability to raise problems, the tools and knowledge to solve them, and the support to make problem-solving a part of their every-day work.
Critically, we also need to make sure that the right people are addressing the right problems. For this, Art Smalley’s 4 Types of Problems framework is particularly useful. Before we delve deeper into problem solving, let’s see how the framework can apply to construction.
First of all, as a precondition for any sustainable improvement to happen, we need to create basic stability in the process. This can be achieved by fixing Type-1 (Troubleshooting) and Type-2 (Gap from standard) reactive problems right at the front line. Unfortunately, in construction, there are usually few standards in the work, which makes problem-solving difficult. How can you address a gap from standard if you don’t know what the standard is? Before any improvement can be made, therefore, it’s necessary to establish clear work standard.
Once basic stability is achieved, the company can start paying attention to more high-level, strategic issues that concern the entire value flow – Type-3 (Target condition) and Type-4 (Open ended Innovation). To solve these problems requires management to get involved, together with all business functions – from supply chain to design. At this stage, an organization can begin innovating on a regular basis. By achieving basic stability and establishing a structured approach to problem solving, Lean Thinking can give innovation in construction a clear purpose.
Let’s now look more specifically at how we can turn our job site workers into skilled and autonomous problem solvers.
To develop problem-solving skills at the gemba, we first need to take fear out of the workplace and replacing it with trust. This can cause a huge shift in the mindset of an organization and encourage people to raise their hands whenever a problem occurs. To have this in place, we need to change behaviors and to build a system in which visual management allows for problems to be tracked and people across the business to be aware of them and know what to do about them. This is a particularly big problem in construction because of the project-based nature of the work, with different companies and teams acting in each job site. That is why a lean implementation should be seen as a company-wide transformation rather than an initiative taking place in one site or project.
Communicating to everyone what should be done, by who and how is hard on a construction site, where thousands of people might work at any one time and deadlines are often tight. The foreman typically makes the decisions on what work to do and when, but the focus is typically on production rather than productivity. With this approach, as soon as a problem occurs the answer is normally to throw more resources at it (in the form of people or overtime, for example). Alas, that’s often not enough to avoid compromising safety and quality. Conversely, standardization breaks the work down into smaller tasks, clearly defines roles and responsibilities and, more importantly, makes it easier to recognize deviations before they become problems that are too big to manage. (More on this in the next article from our working group.)
Once problems are seen as opportunities for improvement and a system is put in place to identify them and tackle them swiftly and effectively, it’s important for a company to focus on providing everyone contributing to the creation of value with the tools they need to become problem solvers. When they hear training, people normally think about classroom training, but in the lean world capability development happens at the gemba, on the job. Simply put, there is no other way of developing problem solvers than having them solve problems!
But how can we solve process problems without mentors helping people through it? As ever, the role of leadership here is absolutely critical, as the following examples show.
Turner Construction Company (one of the largest construction companies in the USA and a co-learning partner of the Lean Enterprise Institute) has been on a lean journey for the past six years, with a strong focus on developing the problem-solving skills of senior leaders through LEI’s Lean Leader Program (LLP). We all know how important coaching is, but if you want leaders to be coaches, they need to first become problem solvers themselves (“We need to model the behaviors we want to see in our people,” a senior exec from Turner recently said). Following several “lean field trips” at the gemba, senior leaders clearly appreciated that to truly engage their people they had to ensure the improvement work focused on their problems. They committed to understanding the work from the perspective of the workers, and to making things easier for them. This transformed attitude, fueled by an extensive use of A3 Thinking, has become a powerful catalyst for change at the North America-based construction company.
A3 Thinking was also a fundamental tool at Socovesa, a Chilean construction company that has been on a lean journey for four years. LGN affiliate Lean Institute Chile has helped Socovesa to understand this important problem-solving framework. Their first step was to stabilize and standardize the planning process for all projects – no matter how different. This helped to generate a common language and create an opportunity for weekly interaction. The initial experiments with problem solving, which concentrated on one specific project and three teams, led to exceptional results. According to the project manager, however, the best outcome was the fact that the area supervisors began to develop the capabilities of their team members and that everyone started to learn to solve problems.
A similar approach is being followed at Battistella Spa, a small construction firm in northern Italy, which recently started its own lean journey, with Italy’s Istituto Lean Management’s help. After receiving some basic lean training, the management team started focusing on real business problems (using the Lean Transformation Framework as a reference) while A3 Thinking at the front line led to a number of quick results in process efficiency. This is gradually creating awareness across Battistella that change is possible and that processes can be improved continuously.
Indeed, the most effective way to engage people in problem solving is showing results, especially those that most directly impact their work. Leadership should get involved in small cycles of PDCA, while at the same time showing workers how their problem-solving efforts are making the work safer and the company more productive.
This strategy worked for conglomerate Andrade Gutierrez, a major Brazilian infrastructure company that operates in several countries, which Lean Institute Brasil (another affiliate of the Lean Global Network) helped to create a different culture by supporting the development of an initial group of lean facilitators. LIB provided them with the lean knowledge they would need to effect change across the group. This clearly paid off, since over the years Andrade Gutierrez has developed four generations of facilitators, who have progressively been able to introduce Lean Thinking in all job sites and business areas.
A MORE HOLISTIC APPLICATION OF LEAN
Lean Thinking is more than just transforming operations. If looked at as an all-encompassing framework, lean can cause a shift in the company’s overall mindset, in its leadership, and in its strategy. When it is applied to the entire value-creating process (as it should), it can lead an organization to a complete turnaround. We already know how impactful Lean Thinking has been in industries like manufacturing or healthcare, and there is no reason to believe it shouldn’t bring just as many benefits to construction.
As briefly mentioned above, the construction process is very atomized and the supply chain supporting it incredibly fragmented. It is normal, therefore, that investors and construction companies interact with one another through lawsuits, that designers and builders have to deal with constant project changes, that material suppliers deliver late, that invoices are routinely disputed at the end of each month, that aftersales service is slow, and so on. Additionally, and more dangerously, the culture that permeates the industry discourages people from highlighting problems. Ultimately, all of this impacts the real customer, be it the owner of a house or an operator in a hydroelectric plant.
Thanks to the holistic, “big picture” view it affords, lean can help the industry to overcome these obstacles, thus becoming a powerful differentiator for the businesses that decide to take the lean leap. In particular, we believe it can be extremely beneficial in addressing issues like culture, supply chain, and the industrialization of the construction process.
Transforming the culture that prevails in the industry, which is notoriously tough and based on a command-and-control approach to leadership, is perhaps the most fundamental outcome that lean can achieve. In an environment in which trust is lacking, people tend to hide problems rather to flag them up, compounding an already difficult situation. In such a scenario, problems only appear at the end, when the project is handed over to the customer. Lean teaches leaders to respect people, to lead by example, which is key to the creation of a working environment where problems are welcomed.
Lean Thinking can also contribute to the effectiveness of the construction supply chain, by boosting collaboration among owners, designers, suppliers, contractors and subcontractors and moving past the toxic relationships that so often exist between them. Much like with culture, this is a matter of injecting trust in the communication and interaction among different players, for example by running experiments like relational contracts and Integrated Project Delivery (IPD). The increasing use of BIM (Building Information Modeling) is another enabler of supply chain integration, and combined with lean concepts it can represent a powerful catalyst for change.
Finally, lean can help this sector to fully leverage the opportunities provided by new technologies to achieve a full industrialization of the construction process. For this to happen, the industry will need to incorporate the principles brought forward by Lean Product and Process Development, which emphasize the importance of bringing design and production (in this case, construction) together from the very beginning.
In conclusion, applying lean to construction can lead to:
- Greater safety in the work.
- Higher quality in the delivery to customers.
- Shorter delivery times.
- Increased productivity.
- Reduction of materials wasted.
- A working environment conducive to continuous learning and collaboration.
- The ability to anticipate problems and better manage risk.
- More integration between subcontractors and project owners.
To make the most of these benefits and sustain them, the construction industry needs to engage in a broader and more strategic application of lean management. A shift from tools to problem solving can help it to improve considerably and support its evolution into a real 21st-century industry.
The Lean Global Network’s Lean Construction Working Group aims to contribute to the development of the industry. We have witnessed and supported several experiments in lean construction and believe that our global and multi-industry experience might contribute ideas and concepts that until now have not received the attention they deserved.
THE AUTHORS
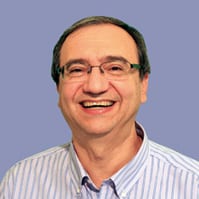
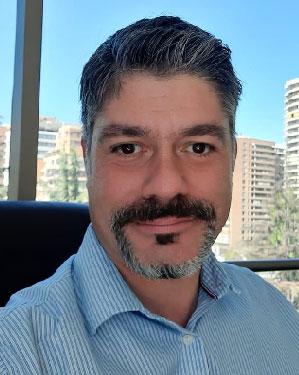
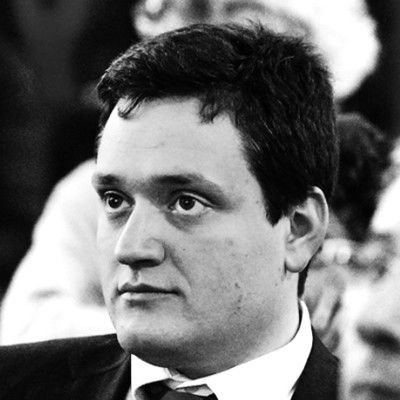
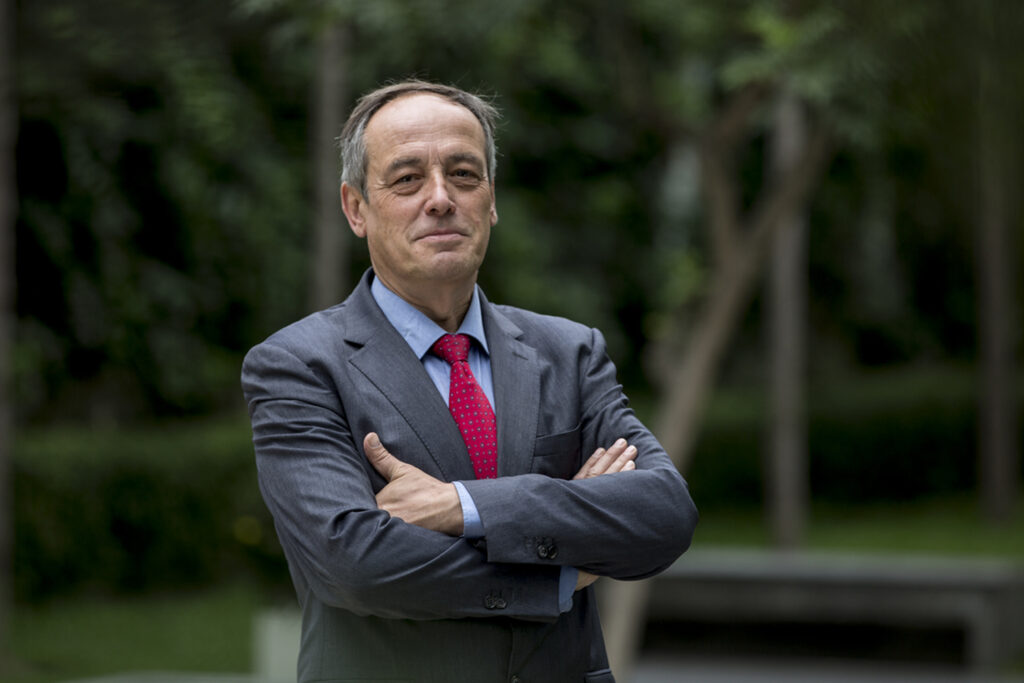
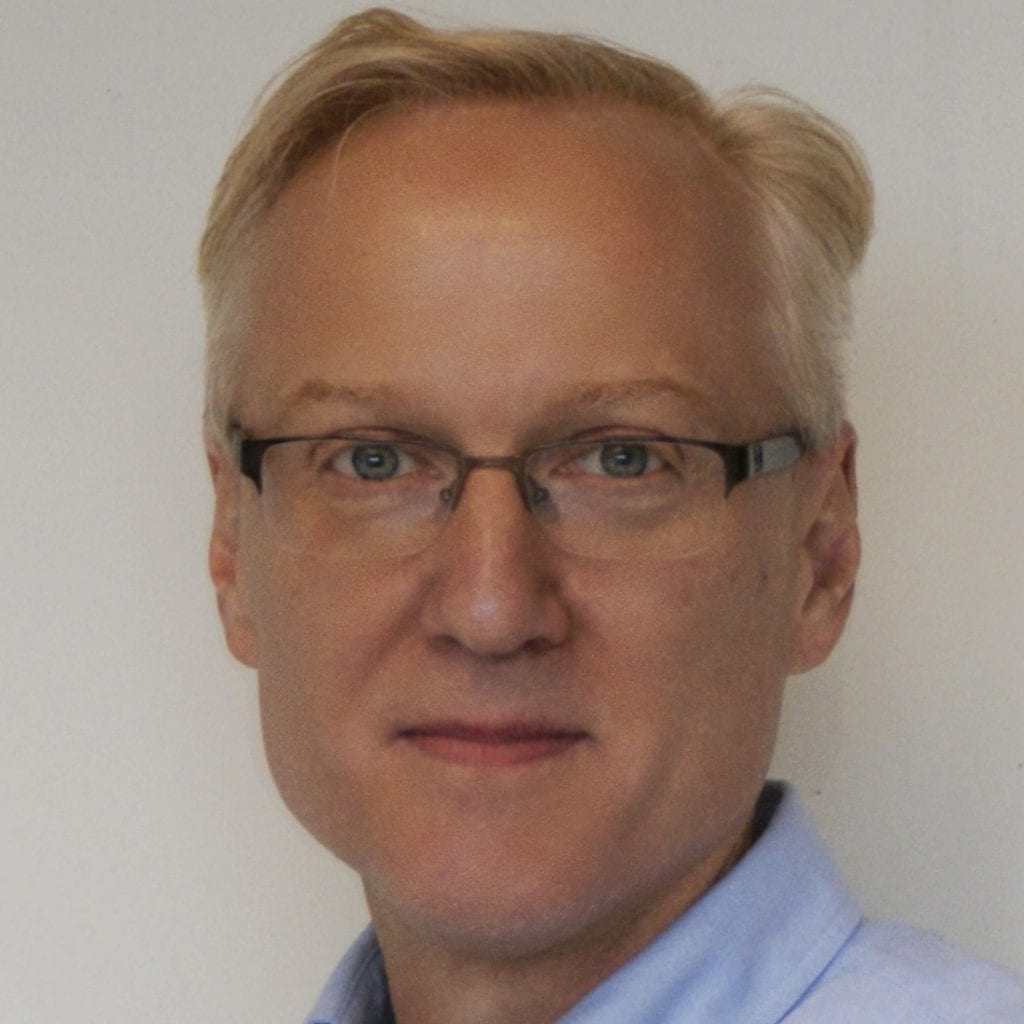
Read more
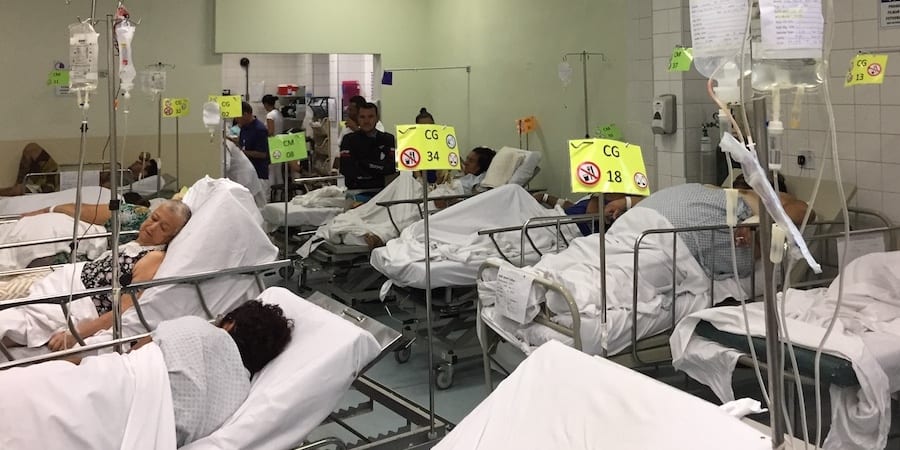
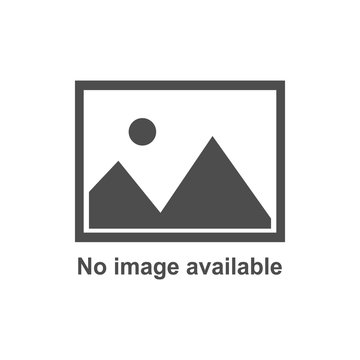
FEATURE – The importance of leveraging early successes to drive engagement to lean is often talked about. The story of this Brazilian hospital confirms this is the way to go.
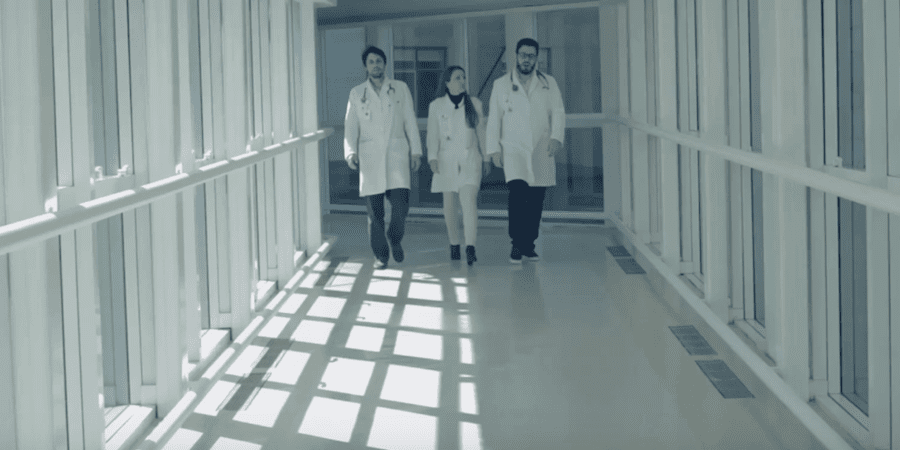
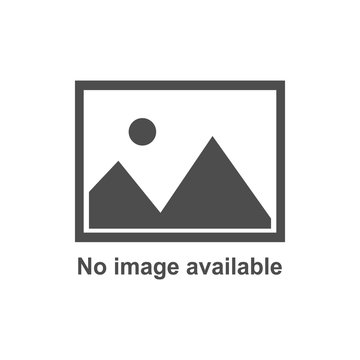
INTERVIEW – By making lean its way of thinking and acting, a hospital in Porto Alegre, Brazil was able to dramatically improve patient flow and transform its culture.
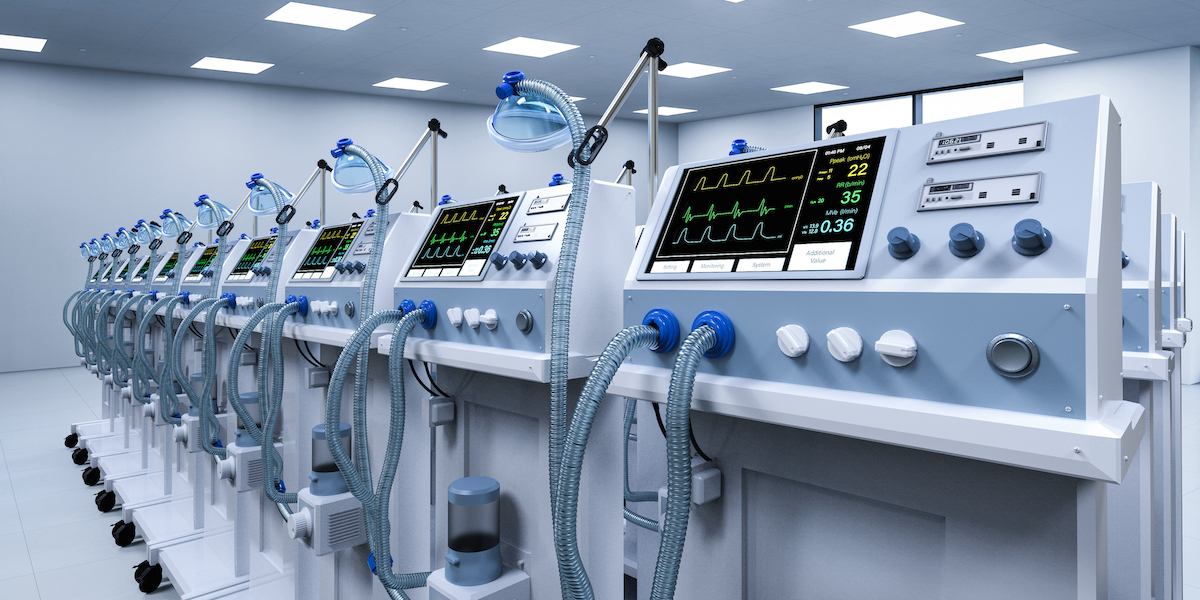
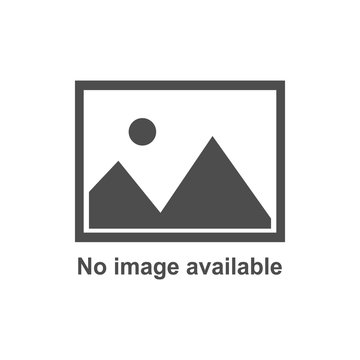
FEATURE – Back on the road after two years, the author reflects on how lean organizations have performed during the pandemic and addresses age-old misunderstandings about Just-in-Time.
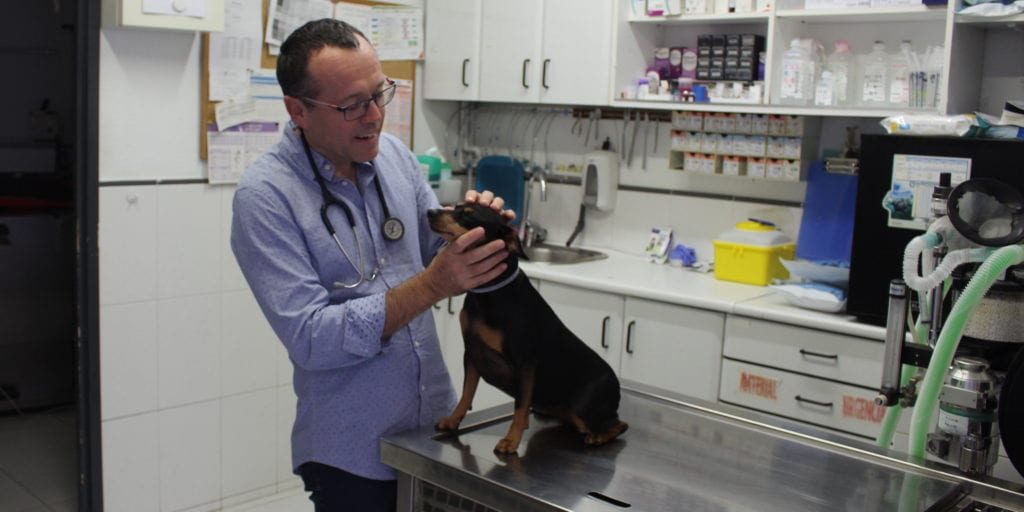
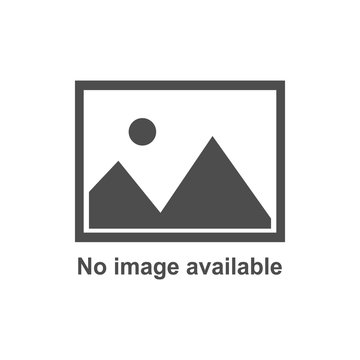
INTERVIEW – A 22-people veterinarian hospital in Barcelona has recently turned to lean thinking. We caught up with the owner to learn how things have changed six months into the journey.