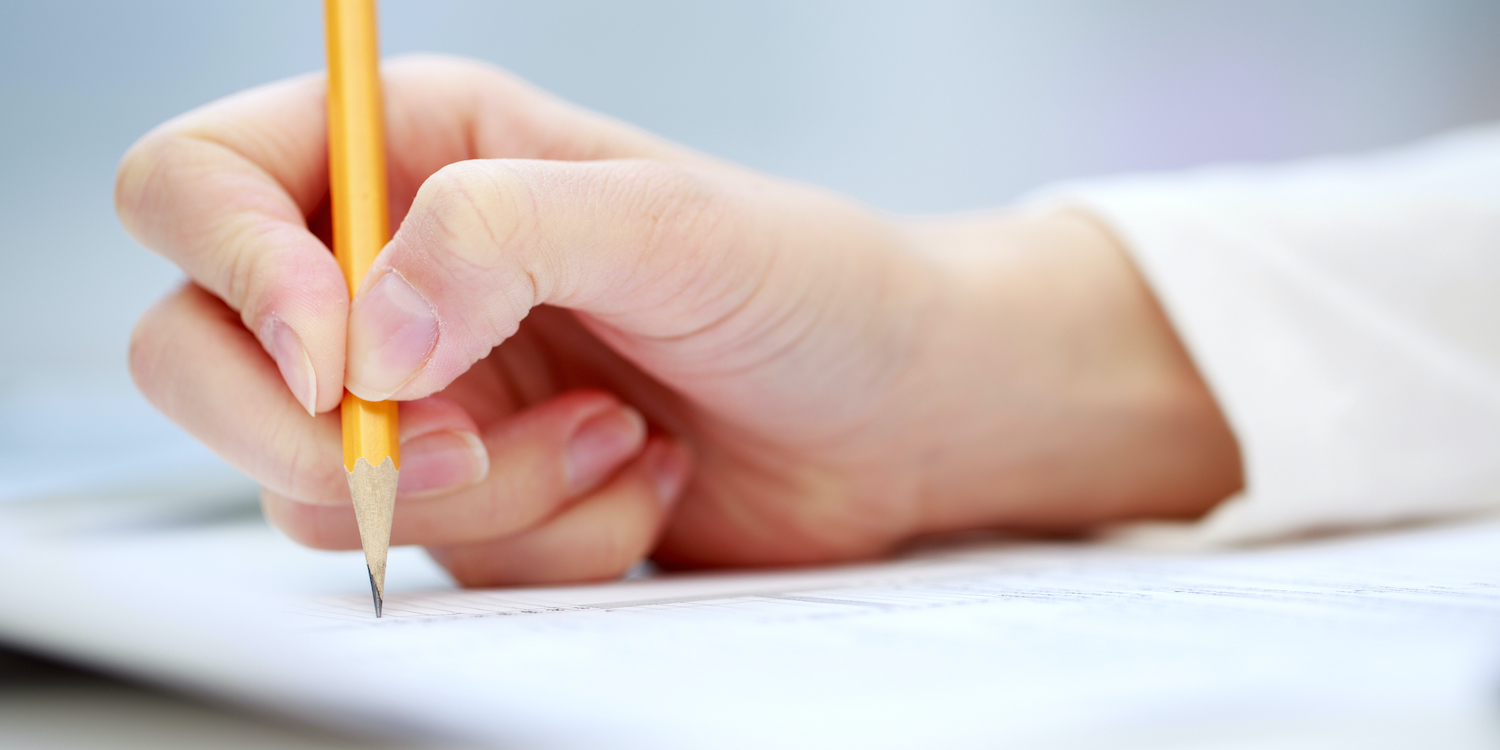
What is A3 Thinking?
ROUNDUP – Our editor discusses A3 Thinking and its various uses, curating a list of the best Planet Lean articles published on this topic over the years.
Words: Roberto Priolo, Managing Editor, Planet Lean
A3 Thinking lies at the heart of lean management. It’s one of its defining and most effective practices. But wait… is it a practice? Is it a way of thinking? Or is it a tool? Actually, it is all of these things, and much more.
In this roundup, I will attempt to shed some light on this fascinating subject pulling together some of the best articles Planet Lean has published on it over the years.
I typically start these roundups with a Lean Lexicon definition. In this case, the Lexicon explains what an A3 report is: “A Toyota-pioneered practice of getting the problem, the analysis, the corrective actions, and the action plan down on a single sheet of large (A3) paper, often with the use of graphics.”
As an approach, the A3 report has the scientific method at its base: fundamentally, it helps you to gather and use data to truly understand the problem you want to solve and identify the best countermeasures you can implement in order to reach your target condition. In the words of the authors of this article, it is “an antidote to jumping to solutions”.
An A3 report has the PDCA cycle built in it, in that there is an expectation that it will reviewed and updated several times until the problem has been solved: it is through these incremental improvements and adjustments that you get closer and closer to your target. (This is also why you should always use a pencil to work on your A3… you will need to erase and rewrite several times.)
In the left side of the A3, we find four sections (and a title) – Background, Current Condition, Goal/Target, and Analysis. This is where the problem and context in which it exists are studied to reach the root cause. On the right side, we have three sections – Proposed Countermeasures, Plan and Follow-up. This is where possible solutions are identified, and a plan of action is prepared.
MULTIPLE PURPOSES
As mentioned, however, problem solving is only one of the uses we can make of an A3. In its definition, the Lexicon itself explains: “At Toyota, A3 reports have evolved into a standard method for summarizing problem-solving exercises, status reports, and planning exercises like value-stream mapping.” But there is more still!
In the introduction to Managing to Learn (the seminal book on A3 Thinking, which he wrote), John Shook, Chairman of the Lean Global Network, says: “Many people familiar with A3 reports see them primarily as a simple communication tool or problem-solving technique. It’s understandable that they focus on this immediate, though limited, application. A3s are, indeed, powerful tools that lead to effective countermeasures based on facts. As a result, companies that successfully implement them for decision-making, planning, proposals, and problem-solving can realize instant gains. But [A3 is also] a management process. The widespread adoption of the A3 process standardizes a methodology for innovating, planning, problem-solving, and building foundational structures for sharing a broader and deeper form of thinking. This produces organizational learning that is deeply rooted in the work itself – operational learning.”
It’s worth remembering these words every time you are tempted to treat A3s as simple problem-solving tools (while you are at it, and if you haven’t yet, you should read Managing to Learn – it is essential lean reading).
But what is the role of A3 Thinking in a lean organization? According to Jim Womack, one of the founding fathers of the lean movement, it is one of the three founding elements of a lean management system, together with hoshin planning and daily management. This case study on hoshin kanri at Itaú Bank is useful to understand how many different uses there are of A3s. In the Brazilian bank, it was used to “deploy the strategy, empower people, and stimulate teamwork.”
Let’s now take a look at some of the most important benefits of A3 Thinking:
- Problem-solving. As mentioned above, this is the main purpose of A3s.
- Planning. As a framework, A3s help us to structure our thoughts and organize them in a logical way, which makes them a great tool to strategize.
- People development. This is perhaps the greatest benefit of an A3: by using it, people learn to develop their critical thinking and to base their actions and problem solving on data. That’s why A3 Thinking is also a coaching tool: by asking the coachee to explain and then review her A3, the coach is really asking her to explain her thought process. With her assumptions and conclusions challenged, the coachee will be encouraged to dig even deeper into the problem in a quest to reach a new level of improvement. We see examples of A3 Thinking being used to development the capabilities of people every day, even in leadership teams: Ohio State University uses it to teach scientific problem solving to principals in Ohio, whereas construction company Turner has adopted it to develop many of its leaders.
- Teaching. Dr Jack Billi, a dedicated lean leader with the University of Michigan Health System, teaches A3 skills to his medical students. Laura O’Donohue, one of Dr Billi’s students, said: “The biggest benefit of the A3 model is that it encouraged me to go see: shadowing on rounds allowed me to talk to people at all levels, something I wouldn’t have done as thoroughly and extensively without the guidance of the model.” Read her full story here.
- Capture knowledge. Recording knowledge to make it reusable is fundamental in a learning organization, because it enables innovation and progress. Capturing improvements in A3s means that people will always be able to refer to them and the incredible amount of data they typically carry. This Dutch university has replaced theses with A3s altogether!
- Cross-fertilization. In Barcelona, where I am based, the local LGN institute periodically brings together people from the different lean hospitals in the region for a day of sharing and “cross-fertilization” – in which the A3 is typically the main vehicle of communication. The institute has also introduced this idea in many of the organizations he coaches: at Dreamplace Hotels in Tenerife, for instance, middle management from the different hotels in the chain regularly meets and shares A3. The benefits of such meeting is that they facilitate the spread of Lean Thinking across the organization, stimulate learning and create an environment of friendly competition.
With this in mind, it’s easy to see why John Shook called A3 Thinking a “management process”: successfully embedding it in an organization will give people across the business a common language and a go-to way of tackling issues. In a lean environment, the first reaction people will have when faced with a problem typically is: “Let’s open an A3!” Everyone can (and should) use A3s in their daily work, from front-line workers to senior leaders: so versatile is this framework that it can be used for anything from organizing and facilitating a kaizen on an operational problem (like a machine breakdown) to establishing the strategic goals of the whole enterprise. At IOV, a cancer treatment center in Brazil, a few years ago the CEO has introduced “kaizen shifts”, time of the week during which everyone in the organization is expected to work on their A3s. Dr Fred himself takes the time to coach at least one person on an A3 every week. Talk about leading by example!
A3s can exist at different levels of a lean organization: there are strategic A3s, value stream A3s, and operational A3s. Like branches in a tree, A3s have a way of generating more A3s (just like unearthing one problem usually alerts us of the existence of many others). Leaders will work on A3s that aim to help them face organizational challenges and reach organizational goals; the achievement of those goals, however, will depend on what happens at department (or value stream) level, which will warrant the creation of several A3s at that level too. One layer down, the same thing happens: the performance of the department depends on the performance of the front-line. A3s help us to solve problems at all levels of the business and, in doing that, create a thread connecting different levels of management ensuring there is alignment from the top all the way to the bottom. That’s why A3s are a fundamental element of strategy deployment.
I hope this roundup has given you a bit more clarity on this elusive, yet critical practice, which can represent great support for a lean transformation.
THE AUTHOR
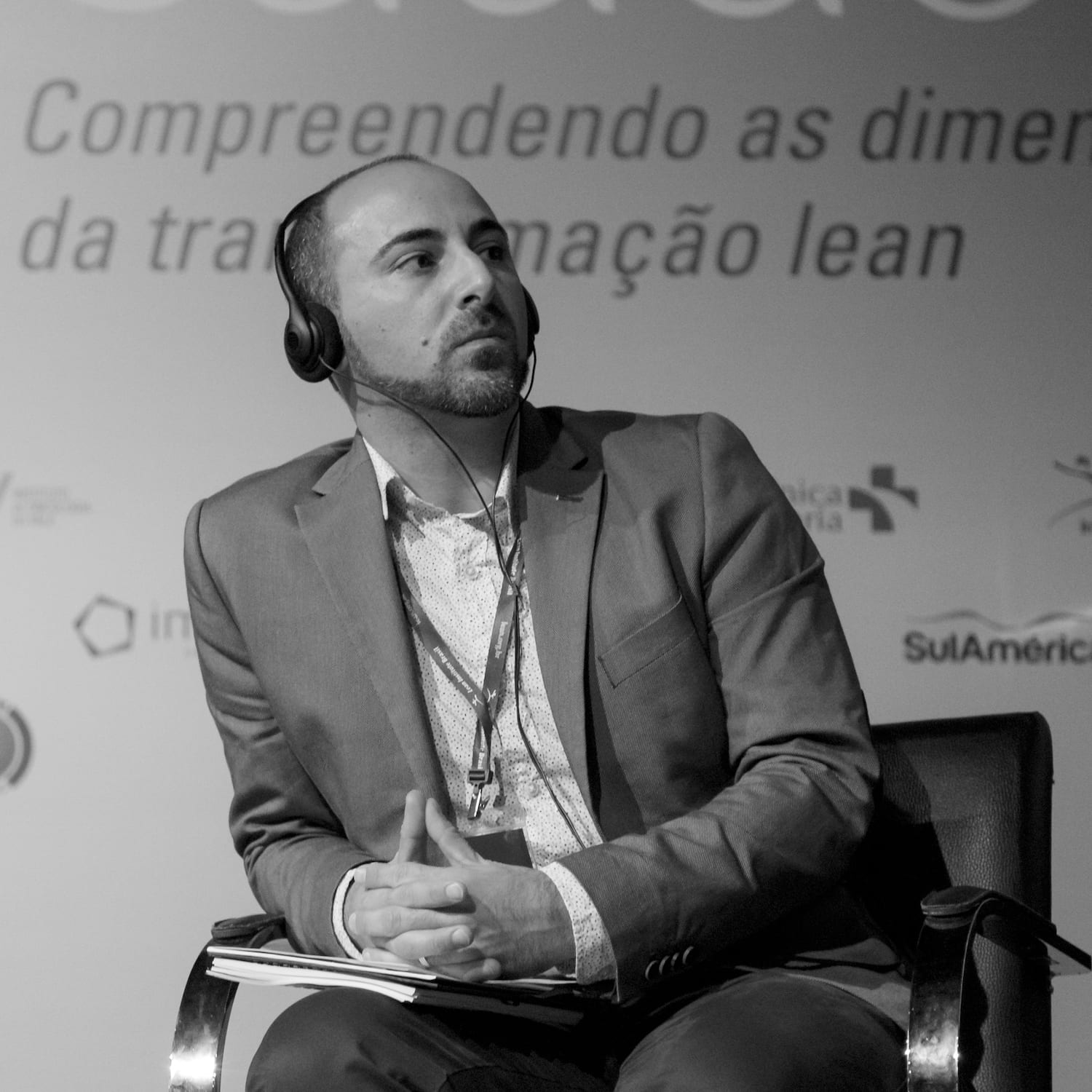
Read more
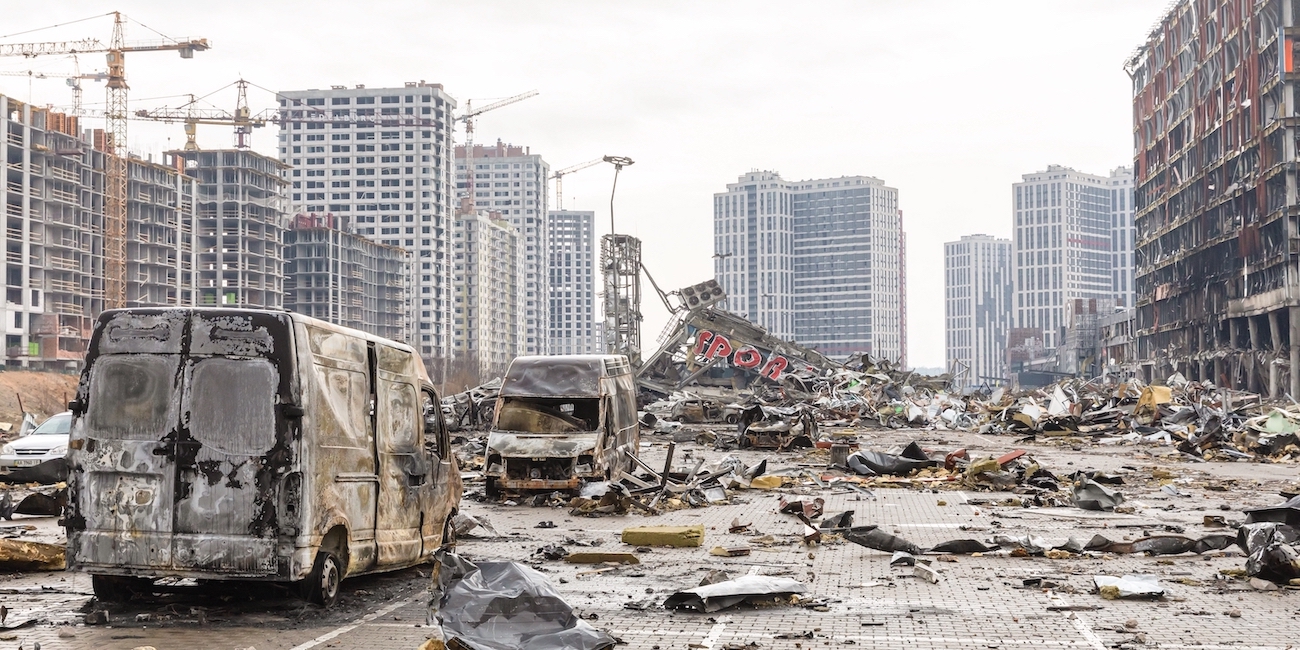
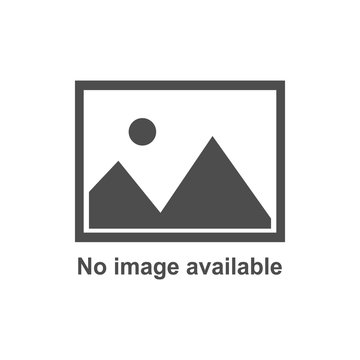
FEATURE – Ahead of their exclusive webinar next week, the authors outline some of the problems Ukrainian companies are facing as the Russian invasion continues.
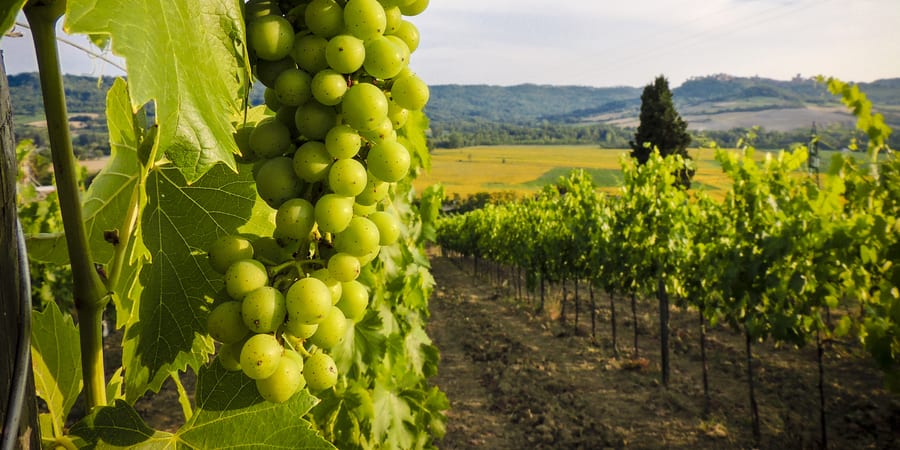
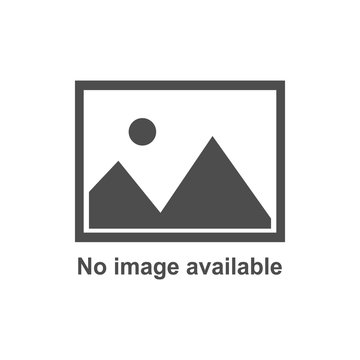
WOMACK'S YOKOTEN – Lean in agriculture might still be in its infancy, but there is a small farm in Indiana that is already proving how valuable lean principles and techniques can be to this industry.
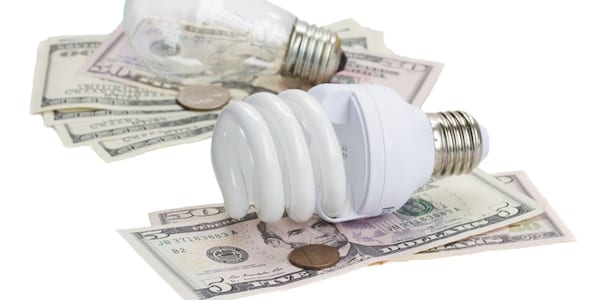
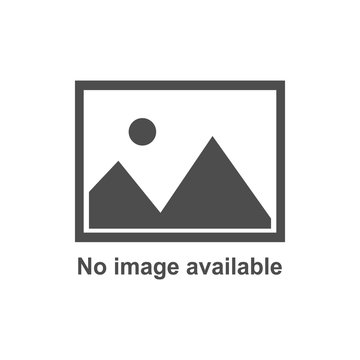
FEATURE - What is the relationship between lean thinking and cost-cutting? Here's why you should focus on improvements as opposed to slashing a budget.
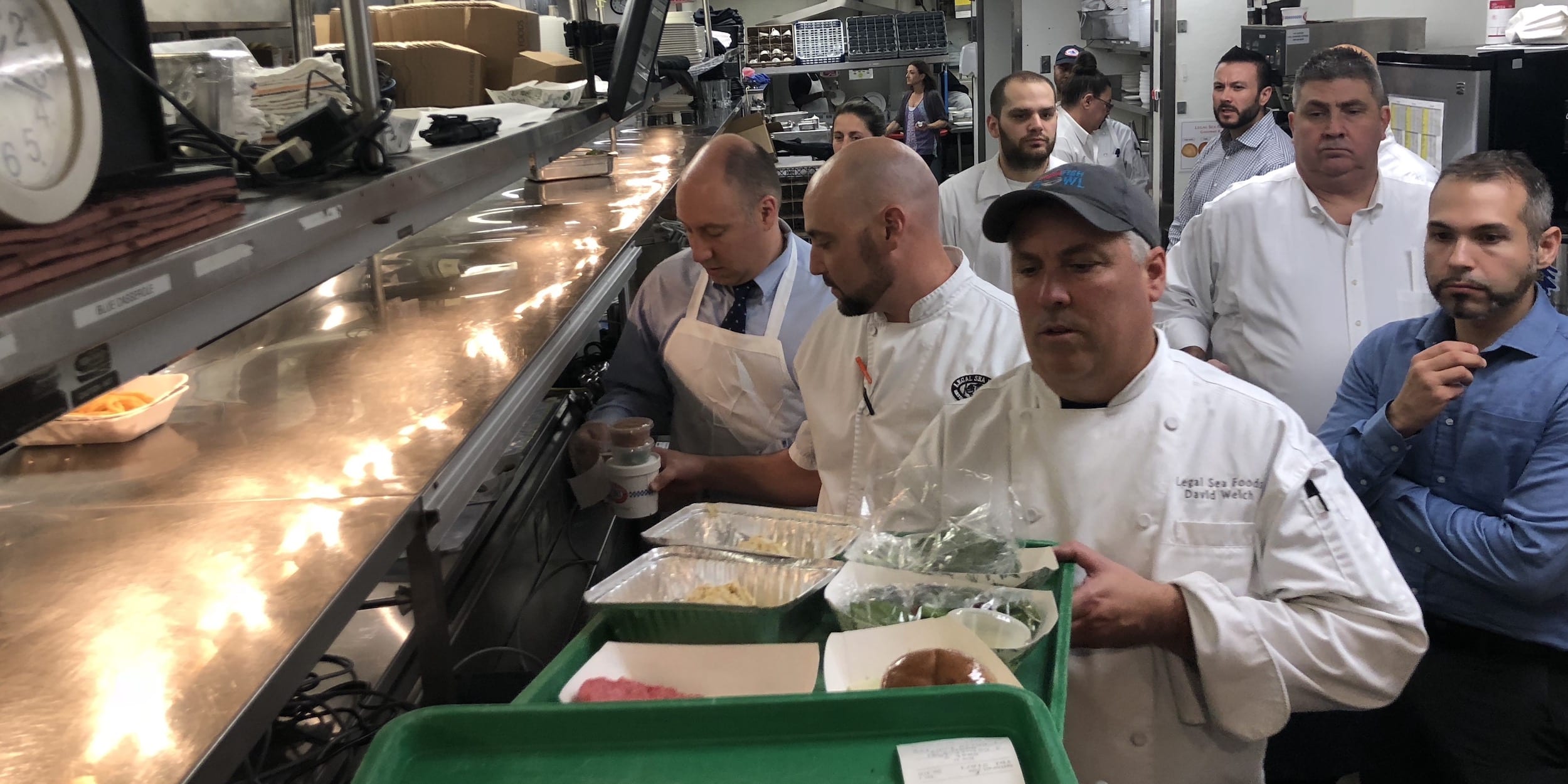
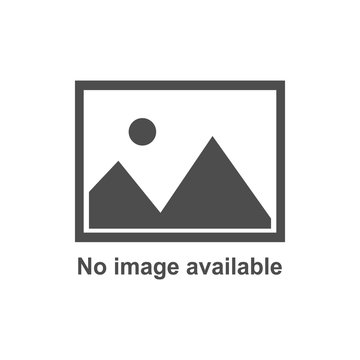
FEATURE – The lean mindset Legal Sea Foods has developed is allowing the company to run bold, aggressive experiments that might some day reinvent the way their restaurant kitchens work.