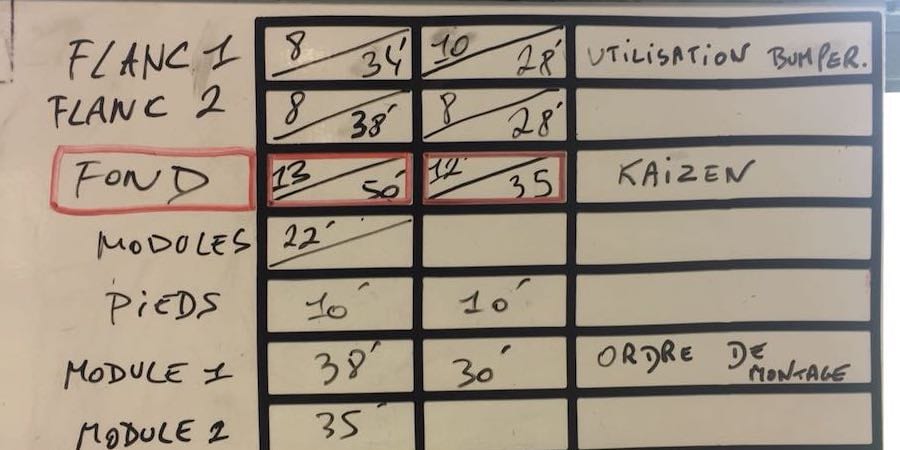
Michael Ballé on how a yamazumi chart enables standard work
THE TOOLS CORNER – Standardizing the work is one of the fundamentals of lean thinking, but without a yamazumi chart visualizing it (and helping us to streamline it) this is impossible.
Words: Michael Ballé, lean author, executive coach and co-founder of Lean Institut France
WHAT IT IS
A yamazumi chart is a stack up of specific tasks that compose a job at takt time.
Many lean professionals in the Western world are obsessed with work standards (more rarely, with standardized work). This reveals the depth of our taylorist conditioning: we want to organize people to make them perform better. More exactly, we want to figure out what is the best method, and then apply it to front-line staff to make them perform.
Clearly, work content is the key to productivity. Continuously analyzing work content – the actual content of work to perform an operation properly, taking out the causes of variation and the muda – is, no debate there, the secret to massive productivity gains. Done consistently over time, it can yield spectacular results as it did for Porsche in the 1990s.
The work content is the total amount of work needed to make a product – it is the sum of all team member cycles.
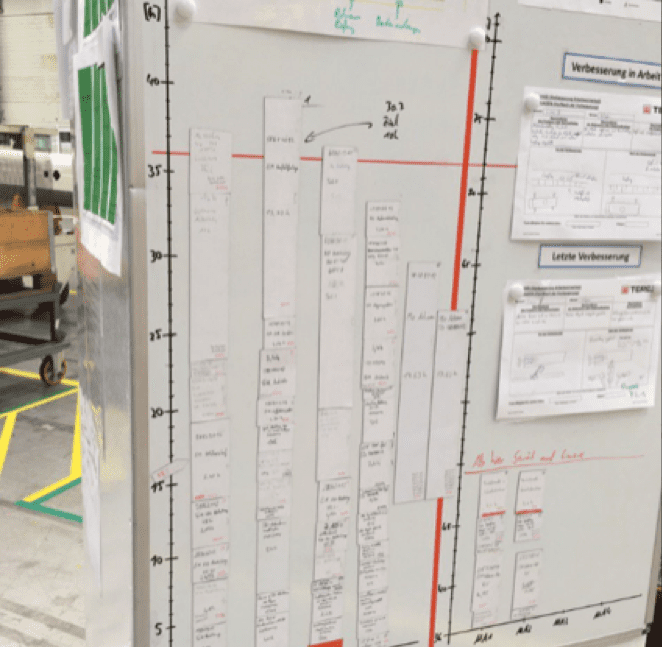
Optimizing work content means reducing each operator cycle, and if the work can be rebalanced between operators, it leads to productivity by eliminating positions: the same work can be done with less people (for instance, imagine the impact of both hands adding value as opposed to one hand at a time). Below is an illustration from The Gold Mine.
HOW TO USE IT
First, chart each operator cycle by measuring 10 to 20 cycles and writing down minimum and maximum times:
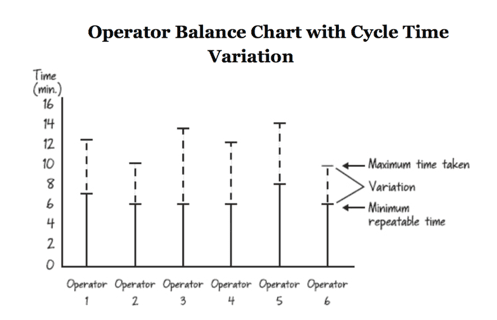
Then draw the takt time on the chart.
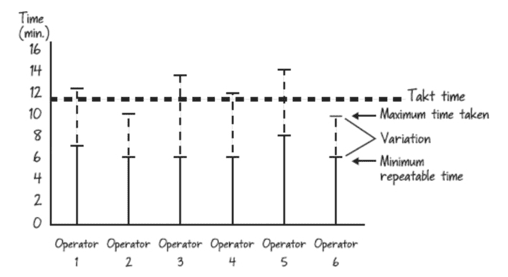
Work with the operators on eliminating variation and then rebalancing the line:
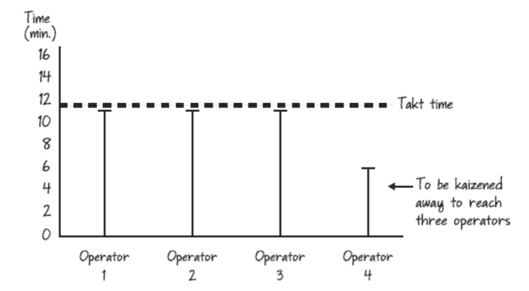
In lean thinking, you start with takt time, which is your operating time divided by average customer demand. Then you graph team members’ total cycle time, from fixed point to fixed point, against takt time.
Then you can stack the work within each bar to visualize what the total cycle is made of.
Obviously, you can do this to people, with experts and what not. But the purpose of lean tools is to develop people first, to give them the orientation they need to improve their own jobs.
So, really, yamazumi is about getting team members to be aware of takt time (as opposed to cycle time), to draw their own work stack-up charts, to identify which of the blocks has the greatest variation. And then to kaizen.
Here, at AIO, a company that helps industrials with karakuri and kaizen, team members design and assemble equipment that is produced in short runs of small volumes. The team members plan their day and track their progress, noting problems they encounter on the way:
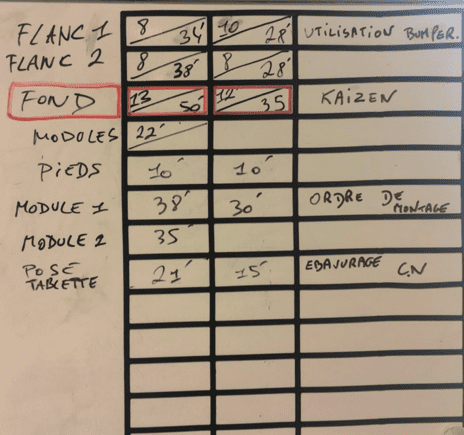
Kaizen means moving value closer to the customer, pushing blocks of stable work up the line to fill up takt time, which becomes possible if causes of variation are eliminated and if, as a result, work is simplified.
The team members plot their own yamazumi chart with magnets, identify the job with the greatest variation and work on before and after, with some kaizen at every production run:
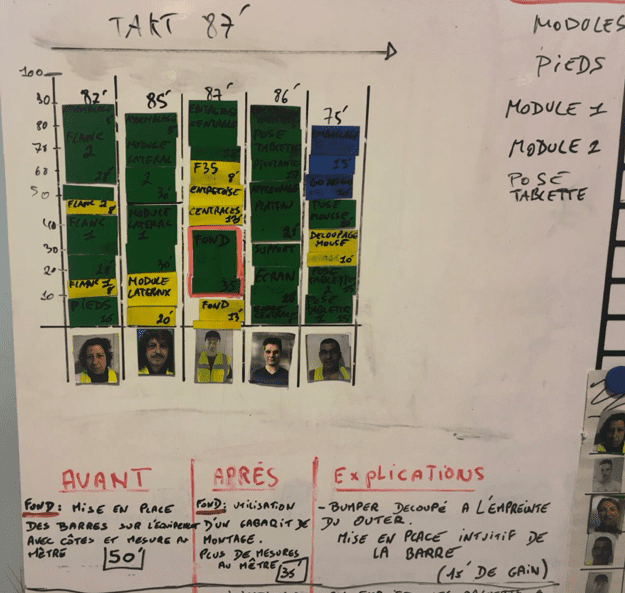
The ultimate aim of kaizen is to reduce work content and rebalance the line in order to eliminate a position – in stable production conditions – or, as here, to turn around the order faster.
Obviously, if the person whose position is eliminated is downsized, your kaizen efforts are going to die very quickly of their natural death. The person whose position is eliminated must know exactly where she’s going next, and if at all possible, get promoted to either team leader or a technical function (or she gets another position and someone gets promoted).
SO WHAT?
Work content reduction for overall, repeatable productivity is one of the ultimate aims of lean, one we should always keep in mind. Yes, it is achieved through standardized work, and the tool to progressively move from work as it is to standardized work is the yamazumi chart.
This goes beyond production. In his recent speech presenting Toyota’s 2017 result, Akio Toyoda, the president of TMC, showed a slide about his intention to “introduce the TPS principles of standardized work on the development side to determine the necessary time and cost per unit of output to shorten lead-times.” Yamazumi is the key tool to visualize work at takt time, narrow down on waste, and eliminate it in everything we do.
THE AUTHOR
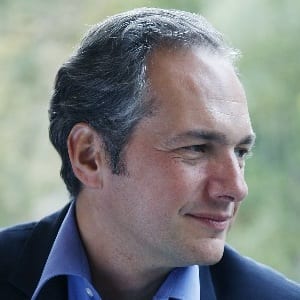
Read more
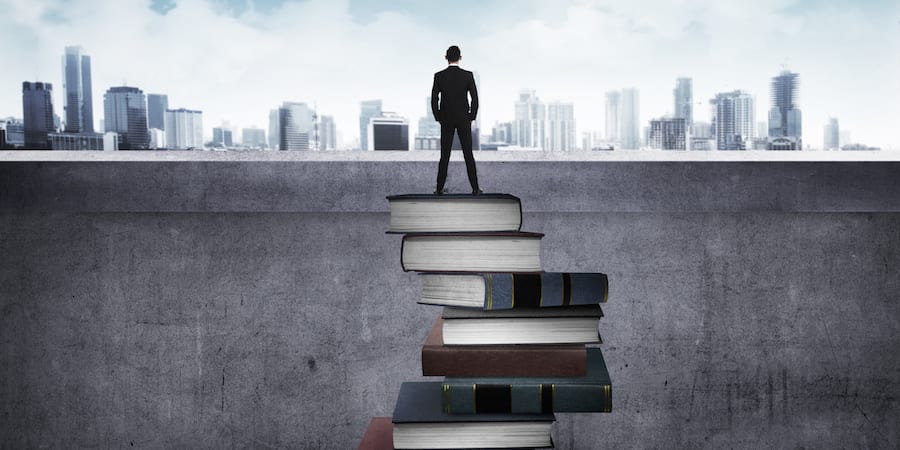
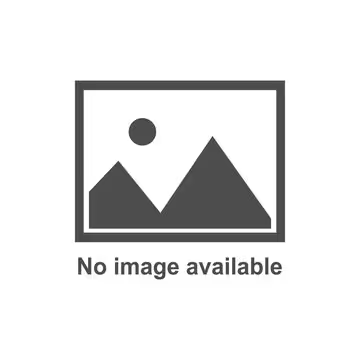
INTERVIEW – At the recent LPPDE event in England, Planet Lean editor Roberto Priolo sat with Takao Sakai to understand how Toyota approaches product and process development and how the Chief Engineer system works.
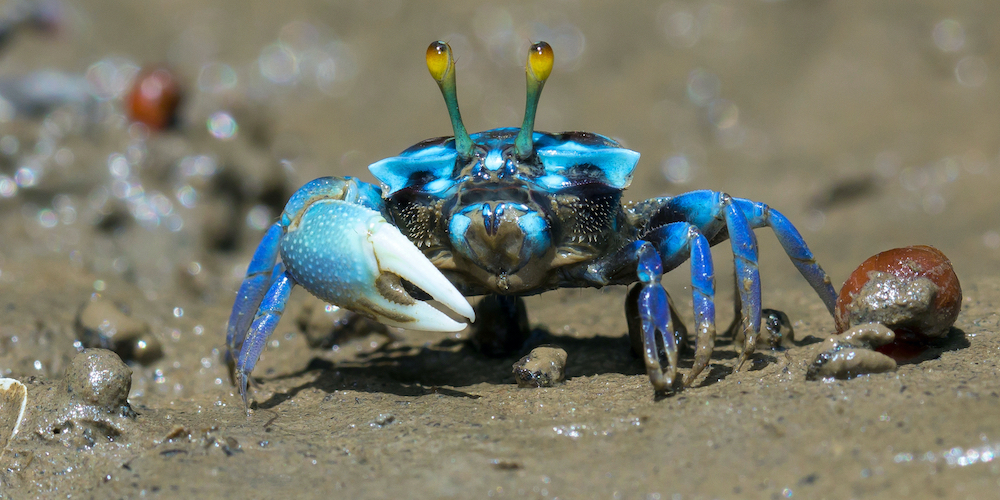
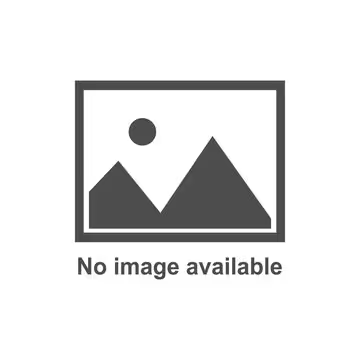
FEATURE – We hear it time and time again: in a lean transformation, middle management is the biggest hindrance to change. The author explains his strategy to win them over.
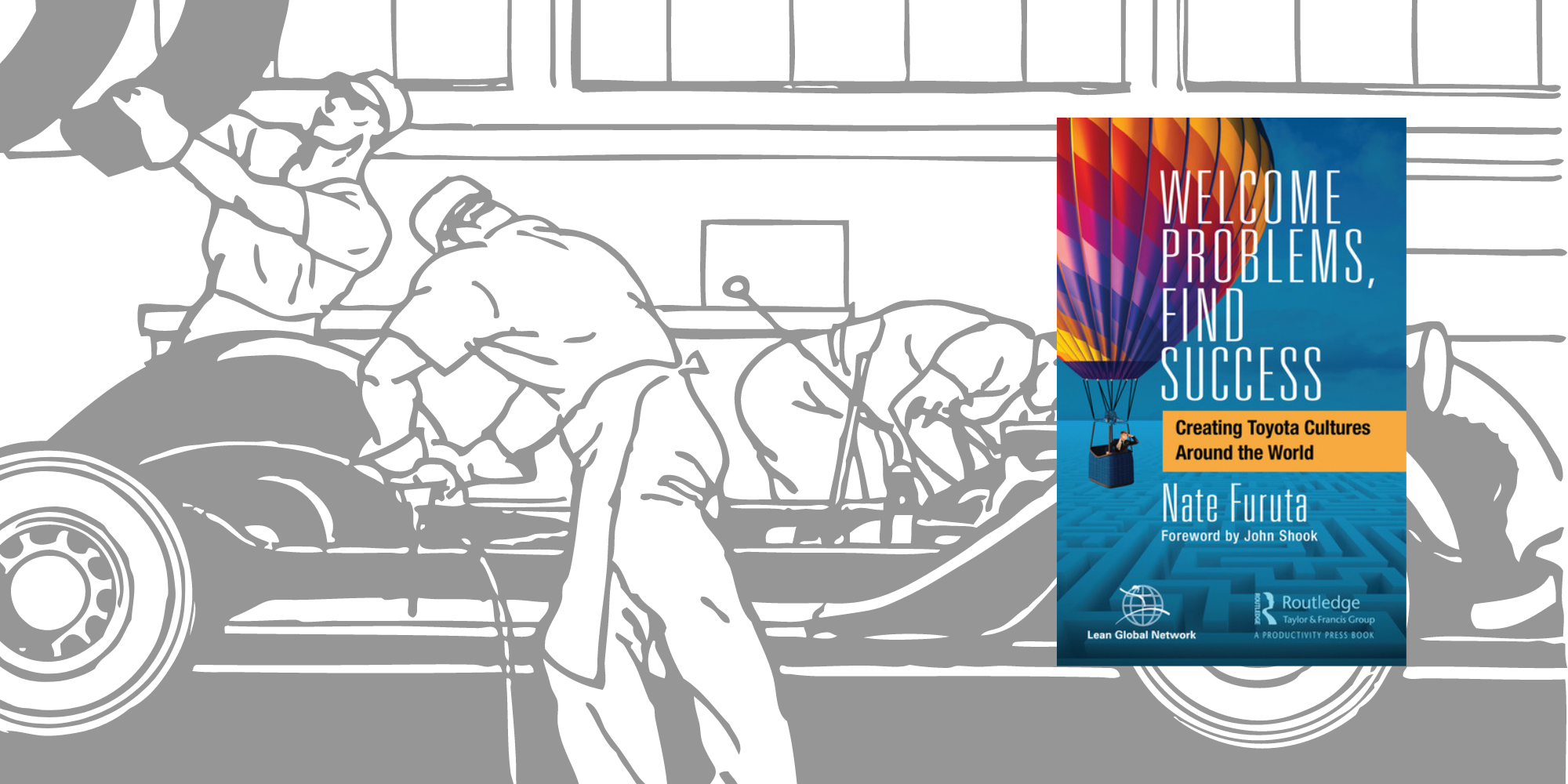
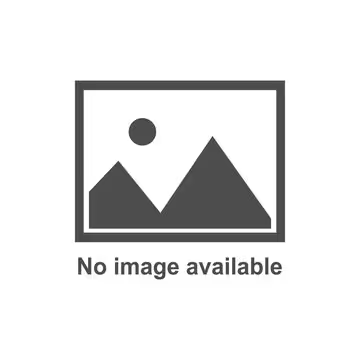
FEATURE – The Lean Global Network just published a new book by Kiyoshi “Nate” Furuta sharing compelling examples of how Toyota principles and culture can be effectively spread to new environments.
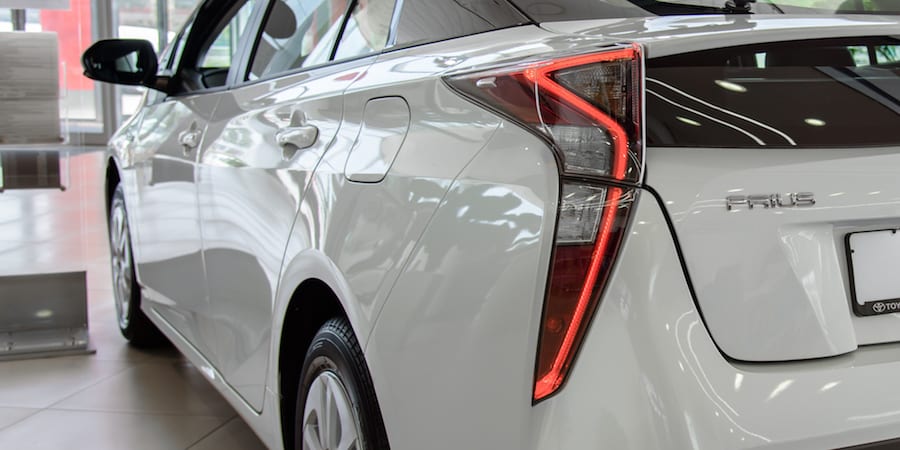
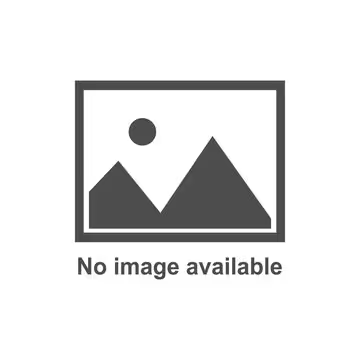
FEATURE – Following a webinar with product development expert Jim Morgan, the author reflects on what the Toyota New Global Architecture and Chief Engineer system can teach us.