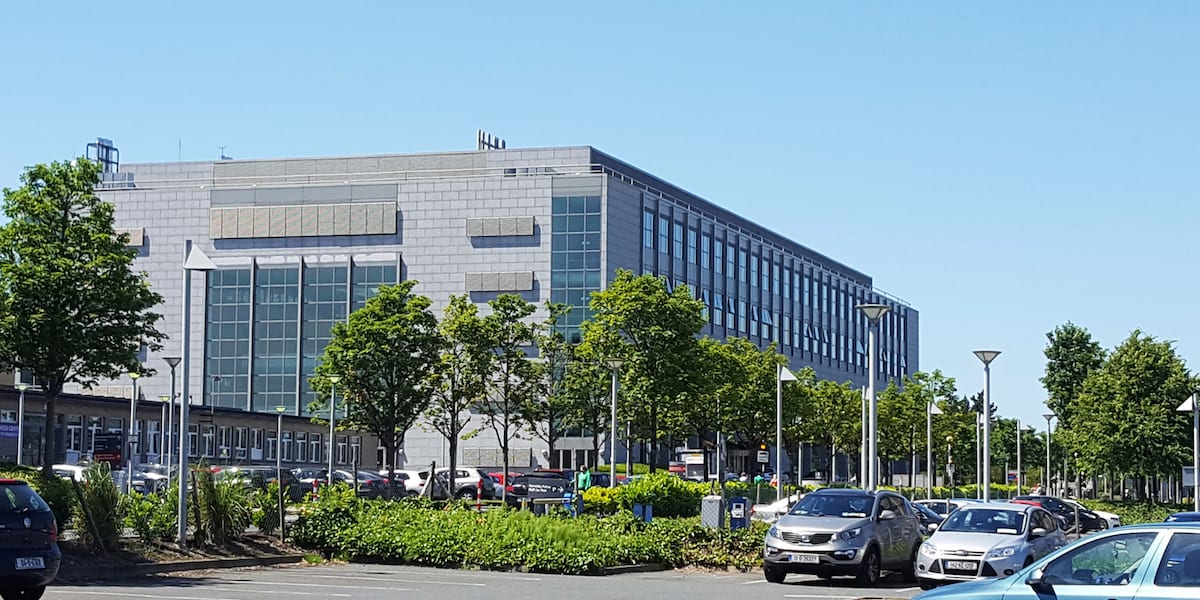
How to transform a large hospital system
CASE STUDY – Hospitals are often part of larger healthcare systems, which makes it critical to learn how to bring lean to such diverse and complex environments. We hear from a large hospital group in Ireland.
Words: Anne-Marie Keown, Director of Lean Transformation and Service Improvement, Ireland East Hospital Group.
Editor's note: PL met Anne-Marie at the recent Lean Healthcare Academic Conference at Stanford. Thank you to the organizers for having us and introducing us to so many wonderful cases.
From small clinics to large hospitals, bringing change to healthcare is hard. Trying to transform a hospital system, however, presents a higher still level of complexity: healthcare groups are made of different hospitals, each with its own culture, level of maturity and problems.
At Ireland East Hospital Group (IEHG) – Ireland’s largest, with 11 facilities and 12,000 workers serving 1.1 million people – we have been on a lean journey for over three years, and I believe that some of the things we have learned to date can be useful to other hospital systems that are thinking about giving lean thinking a try.
We began in 2015, the year Irish hospitals were reorganized in groups and Professor Mary Day became our group CEO. She had previously led a large academic hospital within the group, where she had been very proactive in introducing lean six sigma (they even started a training academy linked with University College Dublin). To mobilize group-wide improvement, she began to network with a number of organizations overseas and quickly saw in the lean methodology – particularly its rapid improvement events – a way of getting the cultural and behavioral improvements we needed to succeed at system level.
Between 2015 and 2016, we organized six Rapid Improvement Events across the group to start to socialize the concept, hoping other hospitals would take it on. These events focused on the discharge process and the front door.
In 2017, we had the opportunity to meet with Denver Health and other healthcare organizations in the US, and we realized we had to use lean not only as an improvement methodology but also as a management system. Critically, we introduced strategy deployment in our work, to really understand how we operationally manage continuous daily improvement and to give staff the tools they need to make that improvement a reality.
Because we went for some high-level value streams – frailty being a case in point – that cross the organization both vertically and horizontally, we were able to leverage the rapid improvements events to understand our current state and challenges and to bring different stakeholders together who ordinarily wouldn’t have had the opportunity to be in the same room. Building this community of practice is giving our people a safe space to discuss problems, ask for help, and access data. The power of building those relationships and using lean as a way of integrating services and people is starting to resonate across the system. At the same, the leadership team is starting to talk about the impact the lean work is having – it’s great to see.
THE RIGHT WAY OF SHARING KNOWLEDGE
The challenges the various hospitals in the group are facing are fundamentally the same, which makes knowledge-sharing a particularly fruitful activity for us. At Ireland East, we have been bringing together staff working on specific value streams on a regular basis: the purpose of these meetings is to have them share their learnings and experience.
We also organize masterclasses to show what good looks like (outside and inside the organization): we want our people to talk about their work and challenges and to have the opportunity to network. We are using different tools – besides the masterclasses, for instance, we have webinars and our group newsletter – as we search for the most effective way to communicate and share.
We have put a lot of emphasis on developing our people through an accredited training program teaching them lean tools: we are progressively training cohorts of front-line staff in each of the hospitals to what we call Bronze level. The first few cohorts were made up of people we had identified; now we have a waiting list.
One of the most powerful approaches we have used, however, is having teams who are further along on their journeys visit teams who have just started: nothing beats that face-to-face interaction (like doctors reassuring other doctors that lean is a worthwhile pursuit, and that it has improved patient outcomes elsewhere in the group). What’s important to note is that we have gone where the pull is: there is no point in imposing lean on people, if you want them to truly embrace it.
I think we are succeeding at spreading lean thinking across our hospitals because we have something for everybody: if you just want an introduction, you take an introductory course; if you want a masterclass, you can take a masterclass; if you want to try out some of the tools, you can get involved in a rapid improvement event; and so on.
There is often a temptation to go to one site and turn it around completely so that you can use it as a model for others to replicate, but I don’t think that works. Instead, our approach has been to share success stories, build credibility and make sure improvements are sustained. It was good for us to go after a variety of value streams (as opposed to a focused piece of work), because it gives people choice and shows them that lean applies across the board.
Facilitating our lean work is the Improvement Team, with four Service Improvement Leads working in and out of all our hospitals. We are finding that having different people support different pathways and value streams – and often helping each other facilitating improvement events – is extremely effective. As a “Lean Team”, our objective is to build the internal capability in each hospital to do daily improvement.
Our role has changed a lot over time: at first, we were mostly facilitating improvement events, whereas now we are spending more and more time coaching our senior managers to help them understand their role in supporting daily management. Encouraging senior leaders to go to the gemba, take the time to talk to people, coach them to solve problems, and more in general turn the hierarchical structure of the group on its head is our main remit at the moment. We have built a lot of improvement so far, and now we are trying to build the leadership that will make that improvement sustainable. It won’t happen overnight, but we will get the right culture.
OVERCOMING RESISTANCE
Like most organization, at times we struggle with some of the bad press that lean has gotten over the years – you mention it, and there are still those who think you are talking about cutting resources. We constantly reiterate that our lean transformation is actually about valuing our patients’ time and ensuring that every decision we make has patients and staff at its center.
We are seeing that the more events we deliver, the more opportunities to celebrate success we offer and the more masterclass we organize, the more trust we can build in the lean process. Additionally, it is clear that asking staff to share their personal experiences with the improvement work is much more effective in getting people on board than anything we can say or do as facilitators or leaders.
More importantly, we have realized that the best thing we can do is to let the improvement speak for itself. The incredible work we have done to improve the care we offer to frail older people has changed hearts and minds across Ireland East Hospital Group. When people saw the results (for instance, the number of elderly patients went to nursing homes or long-term care being reduced from 26% to 8%), they realized the impact that lean can have on the work they do: more, better service with the same resources and in the face of increasing external pressure. The same is happening in Emergency Care, a traditionally harder environment to change: even though we are still holding performance there, the work and improvement are becoming visible… and that’s invaluable in winning people over.
A FEW TIPS
If I look back at what we have done so far (including what we have done wrong) and think about our plans for the future, there are a number of elements that I think are helping us to successfully make our lean transformation group-wide. Let me share them with you:
- It’s important that to brand the transformation, that people understand what the vision is and what the objectives are. Everybody at the front line should be able to tell you what the lean work is trying to achieve.
- In our experience, you need an upfront investment. Understanding what that investment looks like and how you are going to get your return on that investment entails involving the finance team from the very beginning. They, too, need to start thinking differently, in order to get the most value out of the improvement work.
- Building a community of practice is fundamental, and that’s hard to do without face-to-face interactions. Find a way of bringing your people together: as long as they feel safe and they are surrounded by others on the same journey, they will be open to hear you out and try new things.
- You must have data capability and give your front-line staff access to information, or you won’t be able to manage for daily improvement.
- Presenting the improvement is also critical: think long and hard about how you are communicating your achievements and mission, and get your communications team involved as early as you can.
- Take every hospital’s uniqueness into account. At Ireland East Hospital Group, we allow the different organization to brand their work for a particular pathway: in one of our hospitals, anything that has to do with frailty is pink; at Wexford General Hospital they refer to it Wexfit; in Kilkenny, they call it GEMS, Geriatric Emergency Medicine Service. The work might be the same, but people have to be able to see themselves in it.
THE AUTHOR
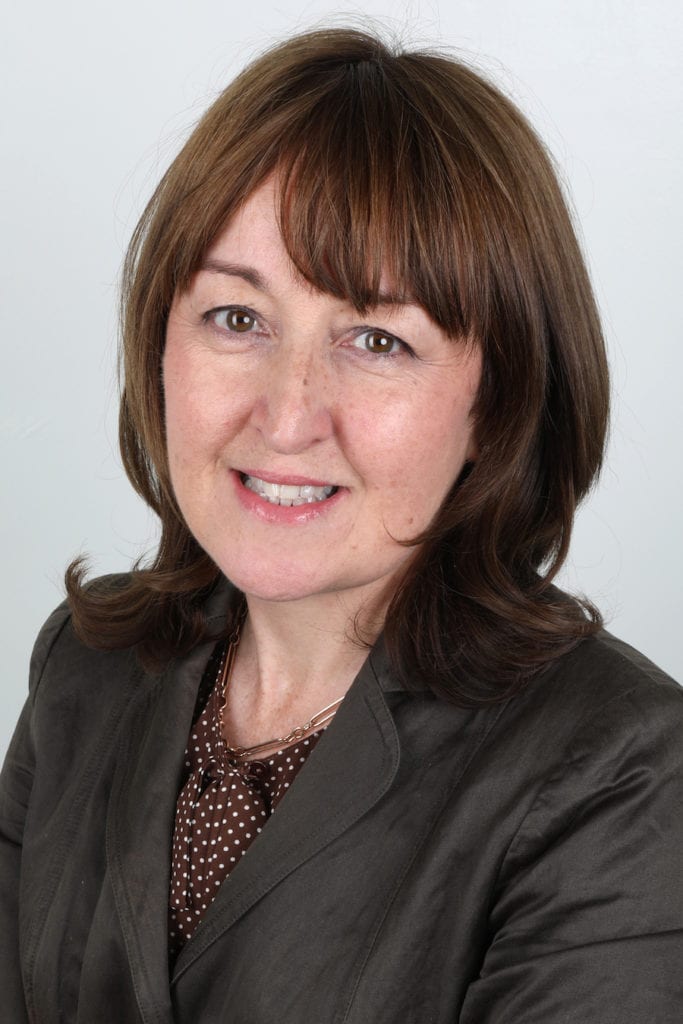
Read more
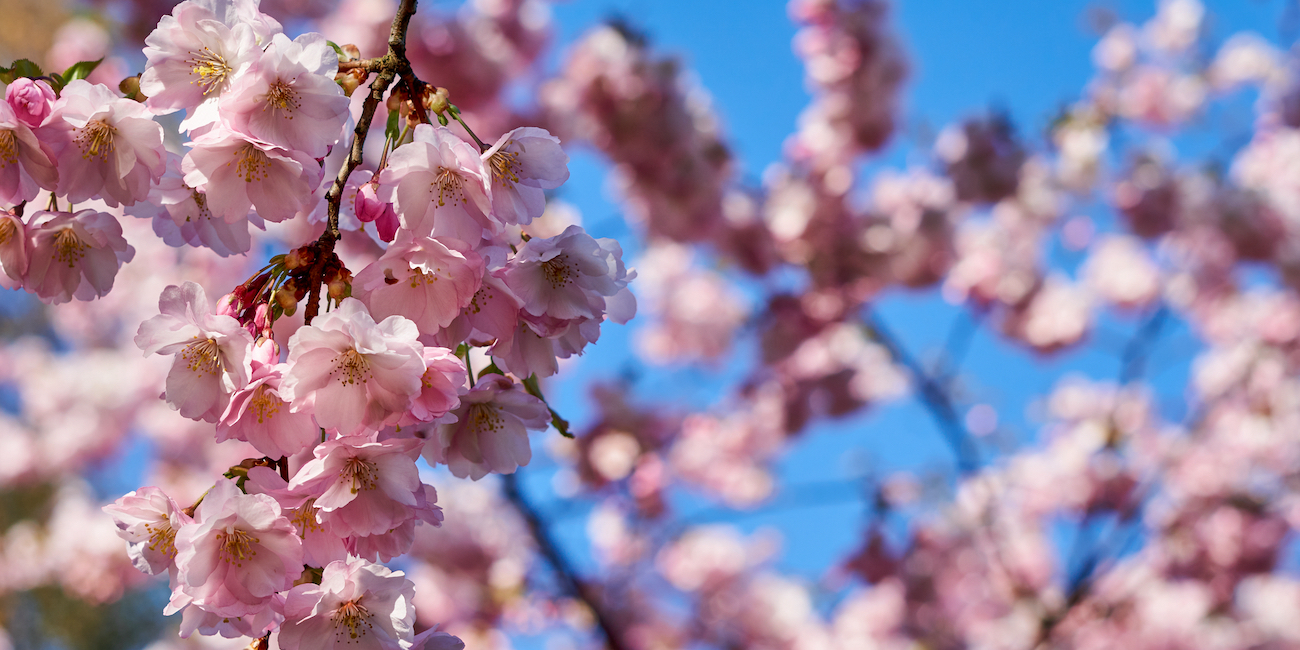
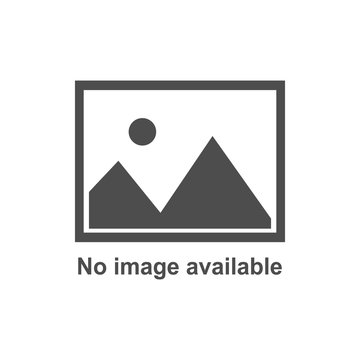
FEATURE – Visuals are a natural way in which human beings learn and teach. The author discusses why visual thinking is part of our DNA and the implications this has on our lives at work.
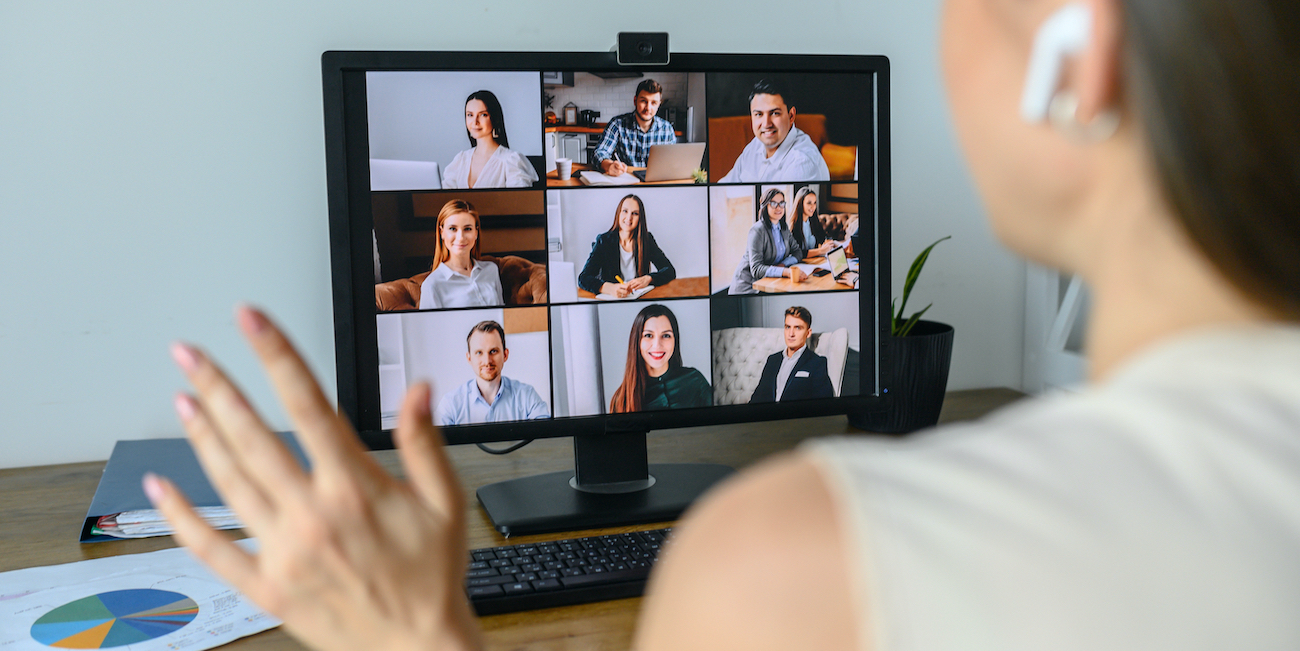
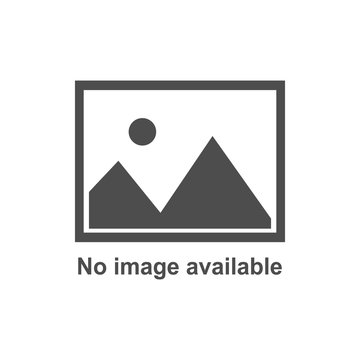
FEATURE – The Covid-19 pandemic has reminded us all that the nature of the work has changed forever. The author discusses remote work and how Lean Thinking can help you make the most of it.
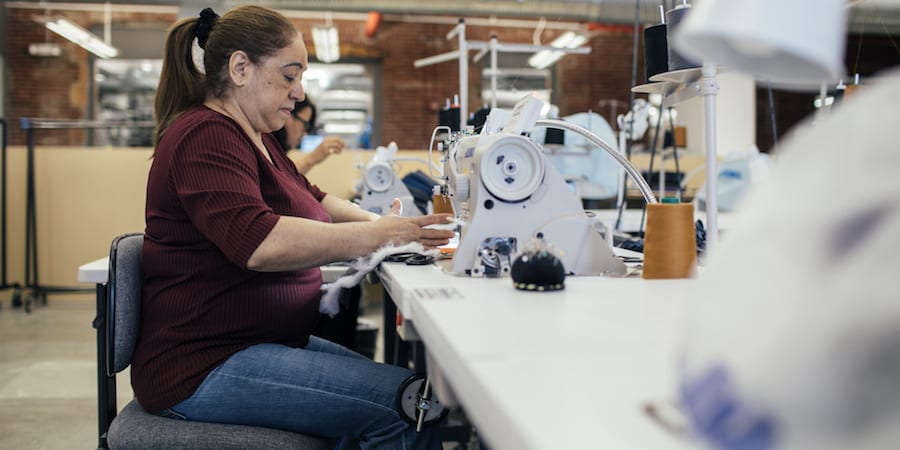
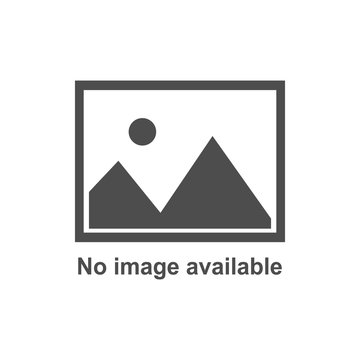
FEATURE – Designing beautiful work helps design beautiful clothes. Here’s the story of how women’s clothing brand Eileen Fisher found in lean a way to support its environmental sustainability strategy.
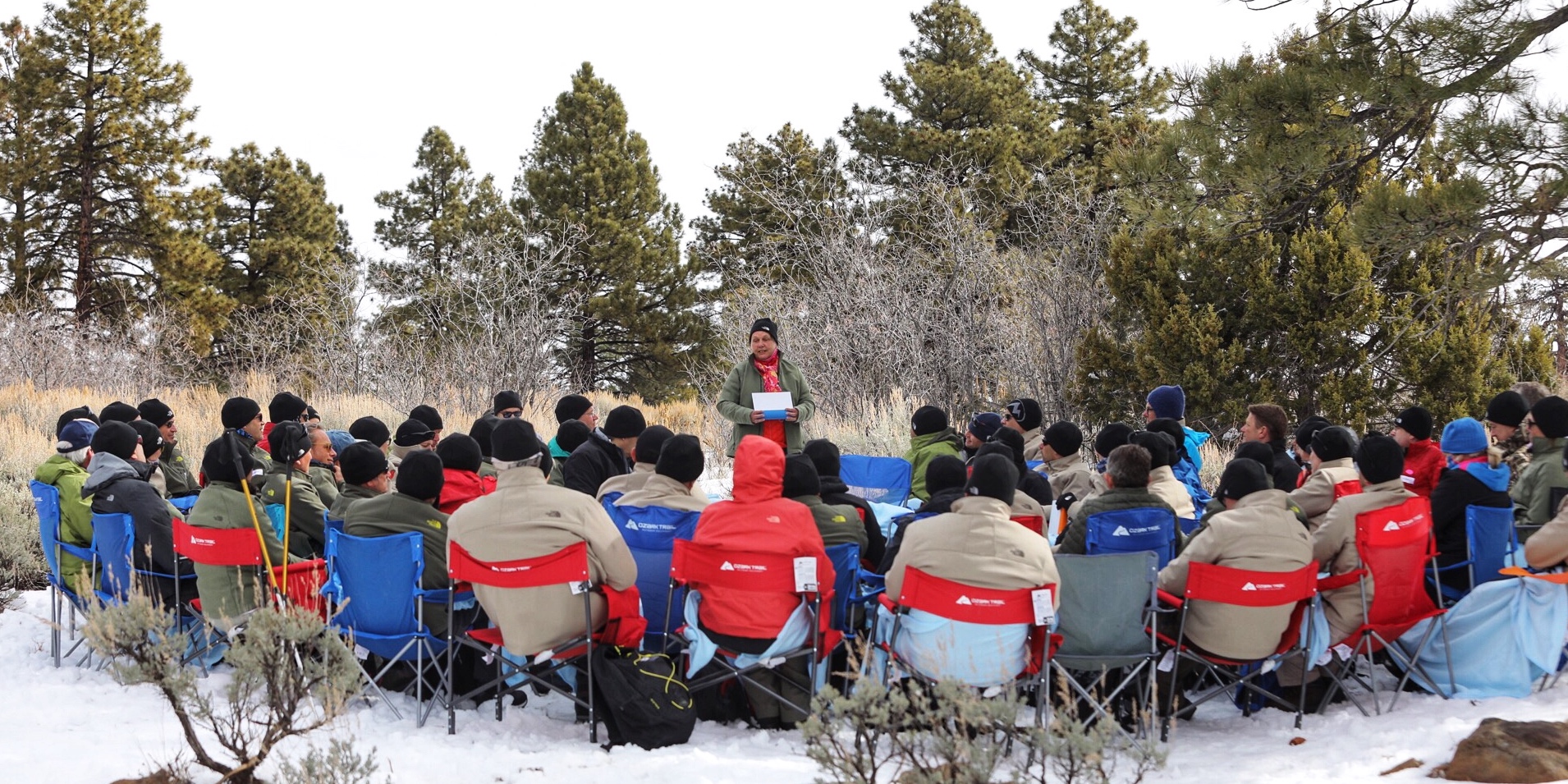
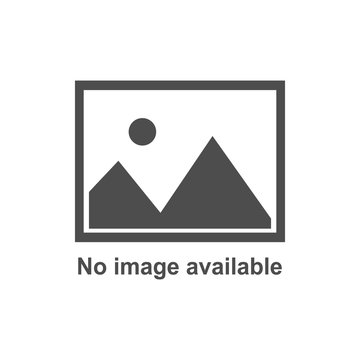
FEATURE – A few weeks ago, we learned how Philips is leading their lean transformation. In this follow-up article, the authors provide some great tips based on the company’s experience.