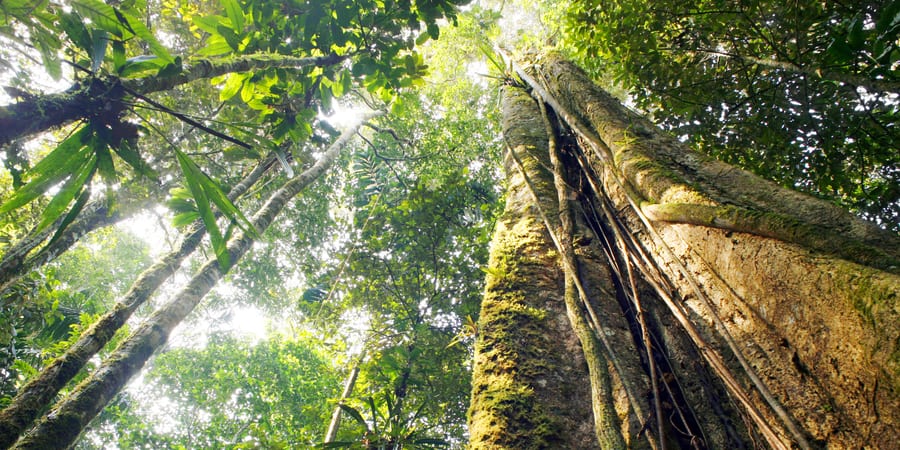
An organic metaphor of the organization to truly grasp lean
FEATURE – We are used to seeing the organization as a mechanical entity, but how can a machine possibly change and improve? We must change our mental model and learn to see the lean enterprise as a growing plant.
Words: Michael Ballé, lean author and executive coach
We are often at pains to explain the meaning of lean thinking: how continuous improvement, supported by a system of lean learning practices such as Just-in-time and Jidoka, can deliver sustainable and profitable growth in saturated markets.
Maybe this is because the lean system doesn’t apply intuitively to our casual metaphor of the organization: a mechanical arrangement of boxes that produce machine-like output, an image clearly born out of the past century.
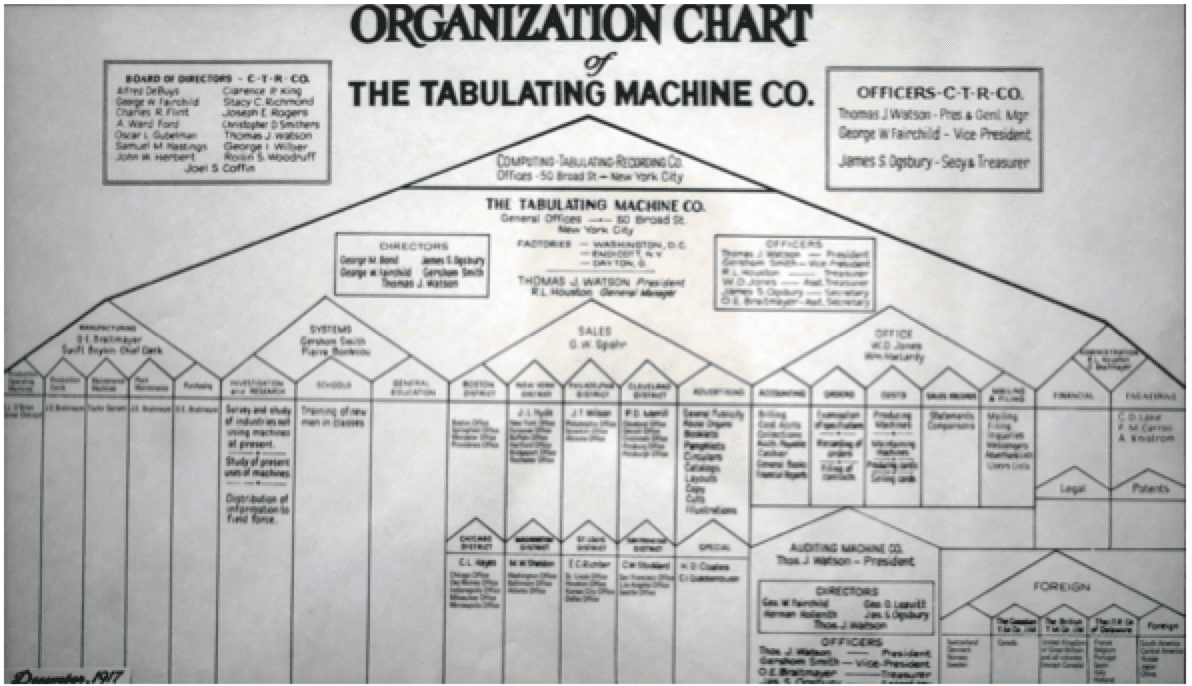
When your main issue is to satisfy demand by ever increasing output, it makes sense to add boxes, grow them and ignore the complexity and coordination costs this creates. After all, sales solve every problem.
But in highly competitive markets where every new sale has to be taken away from a competitor and every customer has to be convinced of the superiority of our offer in smart usage, service and technology, the complexity and coordination costs of the old built-it-and-manage-by-numbers approach become crippling. This is where lean thinking came in: Toyota invented a different way to approach markets, designed around quality and flexibility rather than output and unit cost.
This approach, however, is difficult to explain. If one looks at the previous chart, it’s easy to grasp that if we increase the output of each of the segments and lower their costs, one should end up ahead. Of course, we now know that this is an illusion born out of the chart itself, because markets change every day, output doesn’t mean outcome and the interrelationships between work, say, engineering and production are where quality and flexibility are found. In lean thinking, for instance, one should design a new product to be produced on an existing line to increase flexibility and lower total cost.
The difficulty with seeing any mental bias is that we use our own minds to think and see – so it’s very hard to see the bias in the very tool we try to use to see it, which is why truly new ideas are few and hard to come by (usually invented by crazy people).
Let’s change the metaphor of the organization, then, and try to adopt an organic one. What better than a tree?
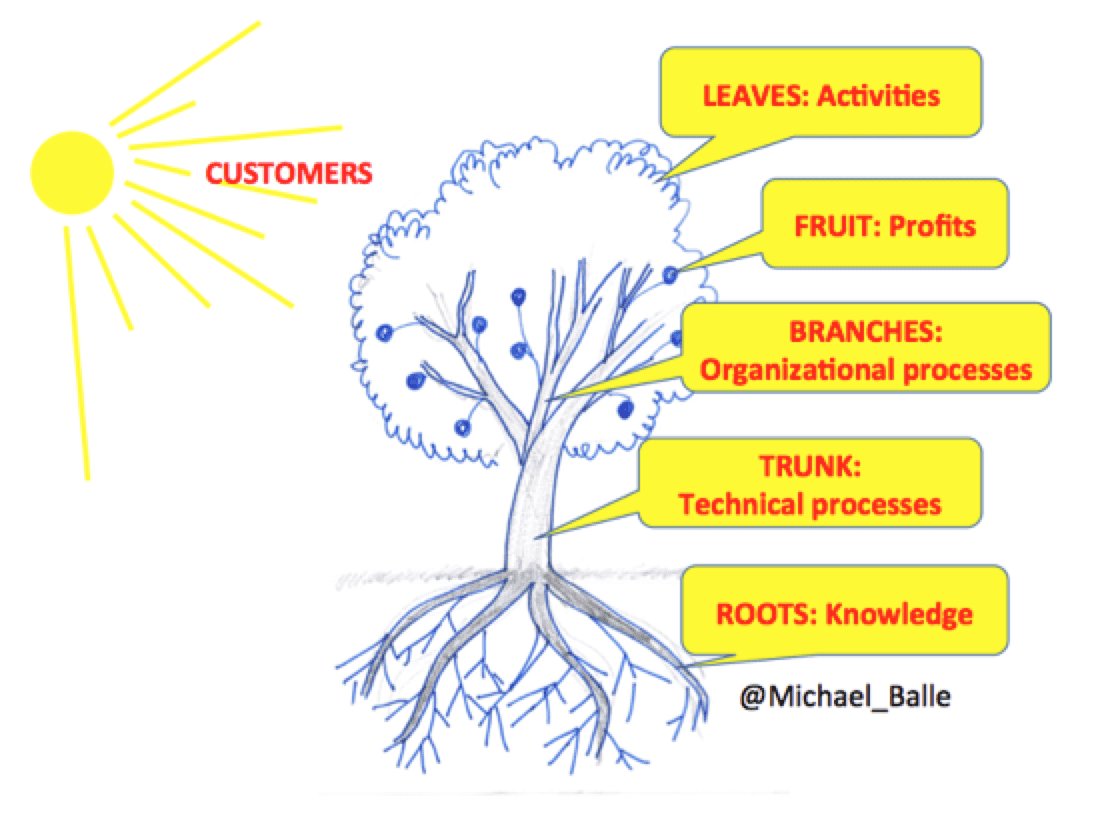
- Leaves are the daily activities that stretch to capture the sunrays of customer satisfaction.
- Fruit are the resulting profits.
- Branches are the organizational processes that support these daily activities.
- The trunk is made of the technical know-how of each team, which enables the delivery of products and services through the organizational (technical) processes.
- The roots are made of the deeper knowledge embedded in each person making up the organization and the mutual trust and spirit of teamwork that makes this knowledge add up in collective understanding.
This is an organic, dynamic vision of the organization that either grows in a balanced way by seeking the warmth of the sun – customers – or withers and dies. In this vision the sap is the flow of ideas that runs through the organization, from each person through to each team and process and delivers more value at the level of each activity.
With this image in mind, we can now perfectly see how lean thinking applies:
- Value analysis (improving current contracts) and value engineering (improving future offers) are the key efforts to develop activities to continuously explore and learn how to better satisfy customers.
- The tension between Just-in-time (reduce the lead-time of all your activities) and Jidoka (stop at every defect and solve problems as they appear) is what makes processes grow healthily and not become bureaucratic dead wood.
- The daily effort to train people by problem-based teaching to better own their work standards and improve these standards through team kaizen is how the trunk of the tree grows by developing the base of team technical processes which deliver value every day.
- The search for deeper thinking and greater mutual trust by stability of the teams and constant seeking of deeper thinking and greater understanding of the theory and practice of what we do, strengthen the deep roots of knowledge and permit a growth of activity (leaves) without taking the risk of uprooting the full tree by not growing its roots as well.
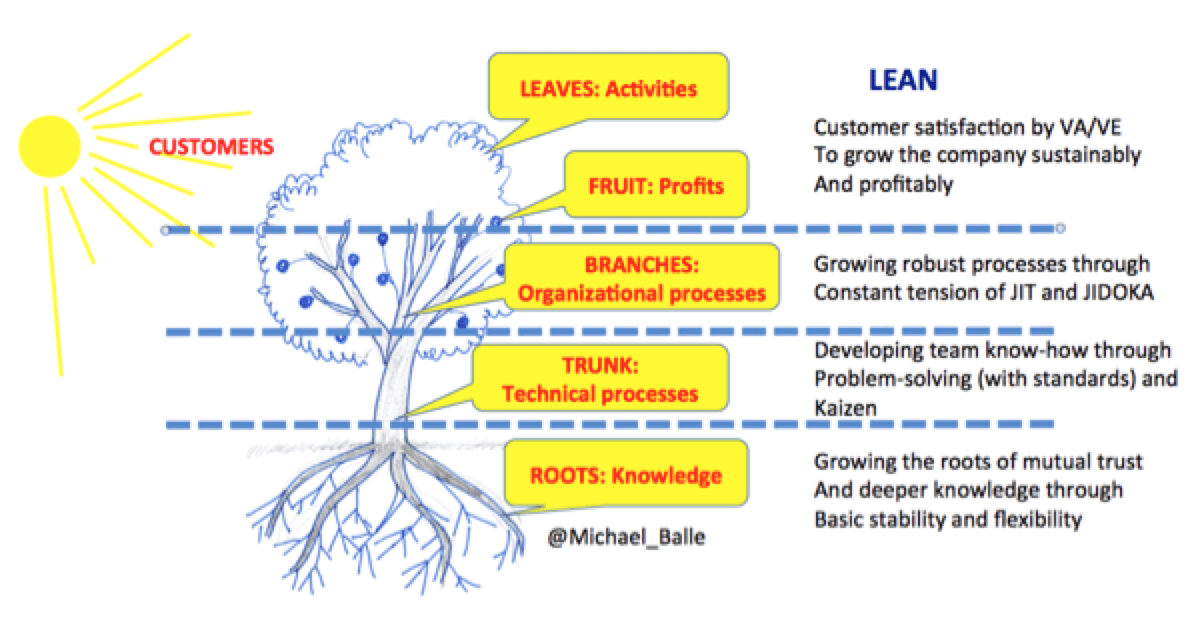
Many companies these days have been misled by the mechanical vision of their organizations. They have tried to constantly increase their activities whilst cutting costs where it matters most: in the deep technical knowledge. As a result, their efforts continuously fail and customers turn to safer competitors, ones that know what they are doing.
The interesting mental experiment – disconcerting, I’ll concede – to think differently about organizations is that in this organic metaphor, lean thinking makes intuitive sense: how to leverage the talent and passion of people and take it all the way to customer facing activities.
According to Prof. Takeuchi, Toyota sees itself as a green tomato: always growing, never ripe. This means accepting that there is no finished mechanical state, that we’re forever unfinished and incomplete. But this is also a hopeful vision of continuous growth through continuous engagement of everyone in their own personal development. Such vision brings meaning to the work and commitment of every person, just as every cell of an organism matters to the whole, and vice-versa.
To a large degree, our mental models define our reality and certainly influence how we think, act and react. To change the world, first we need to change our minds. To change our minds, we need to explore new avenues of thought to loosen the grip of our existing models on our own patterns of behavior. Even if we decide this can’t be right in the end, conducting such mental experiments in seeing things differently are the key to new insights and, occasionally, new mental models. Organizations are teams of people working together: neither a mechanical assortment of boxes, neither growing trees. Yet, thinking about them in different ways is precisely the key to learning to see beyond frameworks and worldviews, and progressively grasp things as they really are so that we can act the right way. Inventing new metaphors for what we do is, in fact, purely rational. The firm is a growing plant, and lean is the art of gardening.
THE AUTHOR
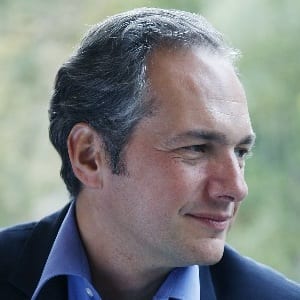
Read more
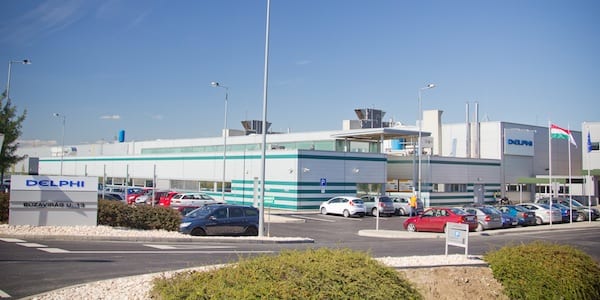
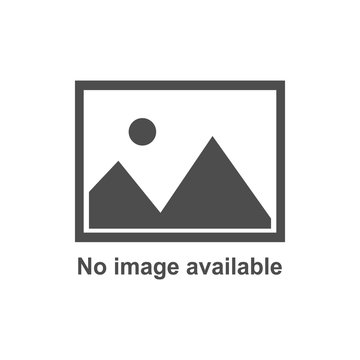
INTERVIEW - The General Manager of a Delphi plant in Hungary talks about the lean transformation the site went through and the challenges automotive suppliers face in this day and age.
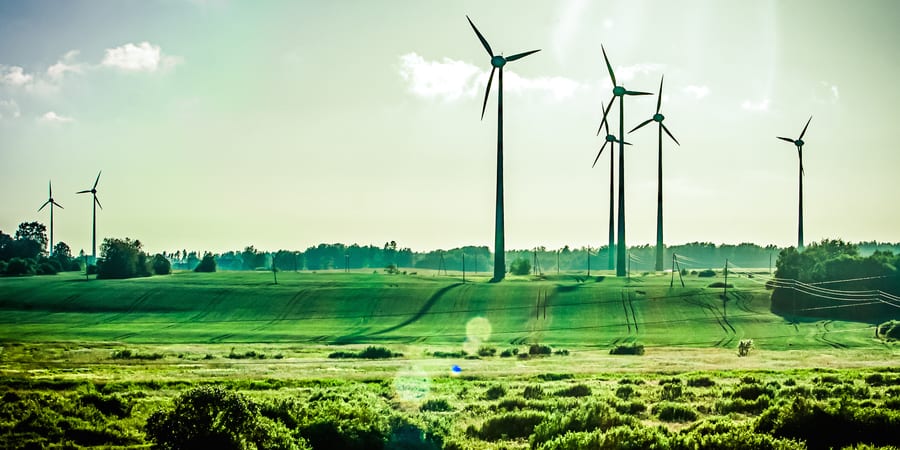
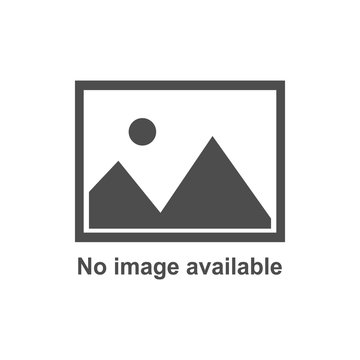

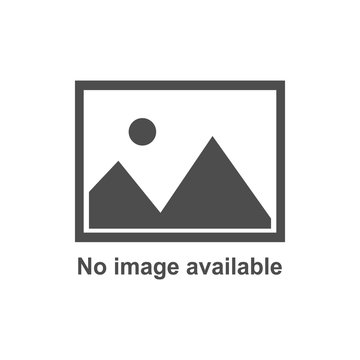
FEATURE – The author shares his thoughts about the thinking that informs Uri Levine’s book and explains why this is perfectly align with a lean mindset.
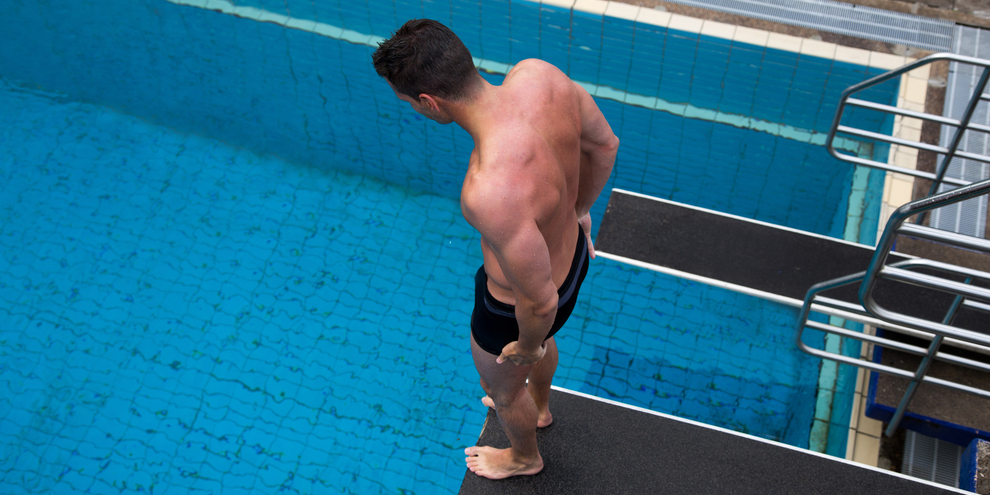
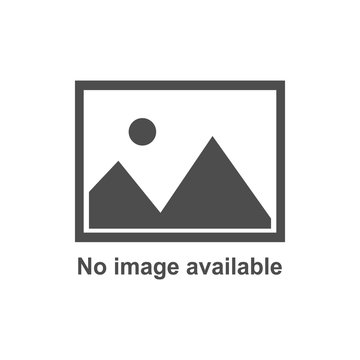
FEATURE – To wholeheartedly embrace lean means to accept changes in our hearts and minds. Understanding this means to finally grasp the reason why lean is only truly taken up by few.