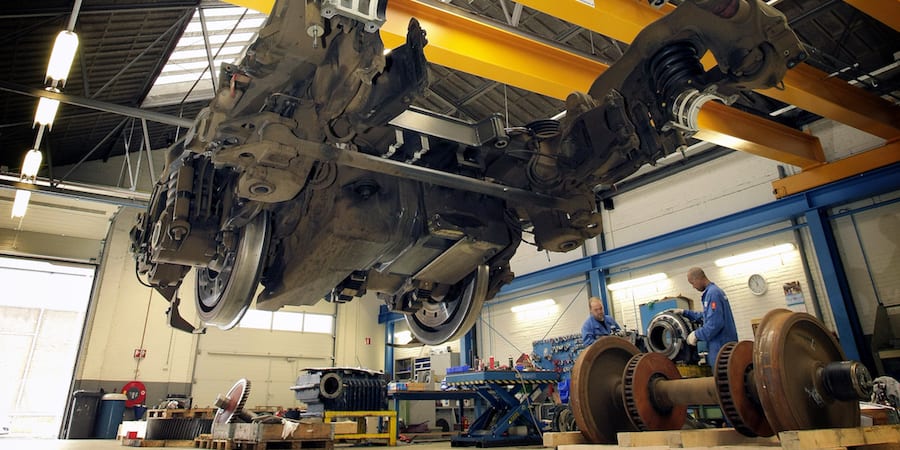
Applying lean thinking to the maintenance of train bogies
FEATURE – A Dutch company that maintains and overhauls train bogies has realized that in order for lean to work, a focus on continuous learning must be established. Here is how they are trying to get there.
Words: Wouter Van Der Helm, Business Unit Manager, and Rianne in ‘t Hout, Quality Assurance Officer, Stork Railways Services; with Wiebe Nijdam, Director, Lean Management Instituut
First, the introductions: Stork’s Railway Services division entered the market in 2005 as an organization that maintains, overhauls and repairs e-machinery, bogies (wheels sets) and gearboxes. After a certain number of kilometers, a train must be checked and maintained, similar to what happens when we take our car in for servicing – even though it takes a bit longer to maintain a train.
A few years ago, in 2012, we won a contract to revise an entire fleet. It was a large project, and at the start it wasn’t as successful as we had hoped. We encountered delivery time and quality issues. We invited a consultancy firm to come in and teach us how to do things differently using lean methods – including the creation of workstations. These efforts allowed us to improve the quality and deliver the project on time.
When another big project came, we felt confident that the lean methods would help us to deliver it on time, within budget and with no issues. However, we encountered similar challenges and after some soul-searching we decided to reach out to the Lean Management Instituut and ask them to help us to improve the situation.
In the first meeting we identified the four biggest bottlenecks in our process to overhaul and fix a bogie:
- Disassembly;
- Blasting and painting;
- Overhauling of the electric motor;
- And mounting of a specific type of bearing.
This allowed us to focus our efforts in the areas that needed it most.
One of the main changes we implemented in disassembly was in the organization of the work. In the original system, a group of two people worked on the same wheel set throughout the process. We changed that, and created specialists for different parts of the process. It’s the same thing that Ford did back in the day.
We encountered some resistance internally as people were used to working to deliver the perfect project – being asked to complete just one step was a big change for them. We quickly found that breaking the work down into chunks that different people with different specializations could deliver led to a much higher quality. Our employees became more aware of the overall quality of the project: having to hand over their part of the work to the next colleague in line helped ensure they did everything properly.
We then moved on to the next bottleneck, realizing we had to find a way to speed up the blasting and painting process without compromising quality. We were experiencing waiting time in our production process, and therefore decided to go to see the supplier responsible for the painting of the trains (as this part of the work is outsourced). The frames and components would reach the supplier and because there was no clear process in place there, they would be painted whenever there was time to do it. If one came in at 3pm, for example, work on it wouldn’t start until the following day – at the earliest. To solve this problem, we established a simple and clear rule: the paint would have to dry at night, and the rest of the process would be built around that. There are now time slots when Stork has to deliver the train to the painter: the new fixed sequence ensures the painting is completed in three days and that we receive the train back early on Monday morning. What this change taught us is that you always need to look at what the process needs, without getting fixated on the way things have always been done.
We also started working more closely with the department that overhauls the electric motors (using value stream mapping with them), and created a customized tool to disassemble the bearing that was causing us problems and mount it back on, which had a huge impact.
Overall, we decided to start structuring our work around eight-hour blocks. On Monday we do one part, on Tuesday we do another, and so on. Leveling the workload like this gives you a smaller part of process to manage at any given time – the most meaningful result in our performance was that the time it takes us to fully overhaul a wheel set has gone down from 7.1 weeks to 3.5 weeks.
Today we have a more stable process in place and we can manage demand more easily, which helps us to provide a better and more reliable service to our customers.
CHANGING A CULTURE, AND STILL STRUGGLING AT TIMES
Our lean journey has been a tremendous learning process. For example, we realized that in the past we have focused too much on the execution of what we had learned, rather than on the preparation needed to ensure it would work. While we have worked hard on process improvement, we still need to focus more on capability development, a necessary step to move forward. Now we get it, and we feel we have a more complete approach to our lean transformation: we have developed a common language, and vision of what our future should look like – and this is what sets the course for our lean work going forward.
All key people within Stork’s Railway Services have attended the Lean Practitioner Course, after which they have started to work on projects in different parts of the business.
While on the actual job we are encouraging people to take on one step of the process (depending on their specialty), we are also helping them to get a better understanding of the big picture and of how their part of the process fits into the overall work that needs to be done. We are also working hard to strike a balance between pushing lean improvements and asking people to take the initiative. This sounds good, but is a difficult thing to do.
The most critical lesson for us is that lean cannot be delegated, and that it is necessary to always work as a team towards a common goal: continuous learning.
THE AUTHORS
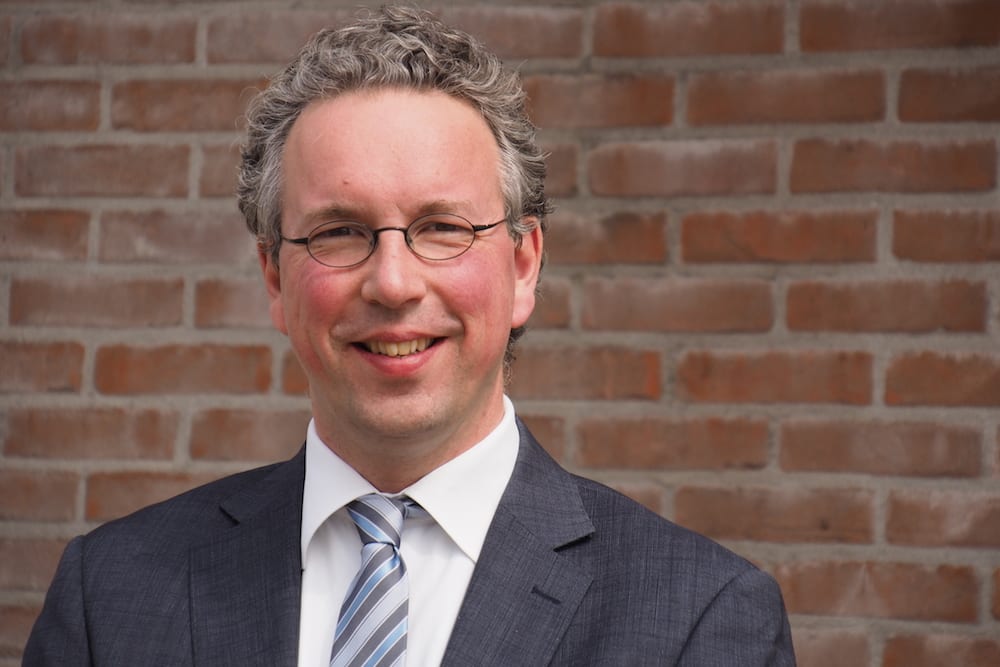
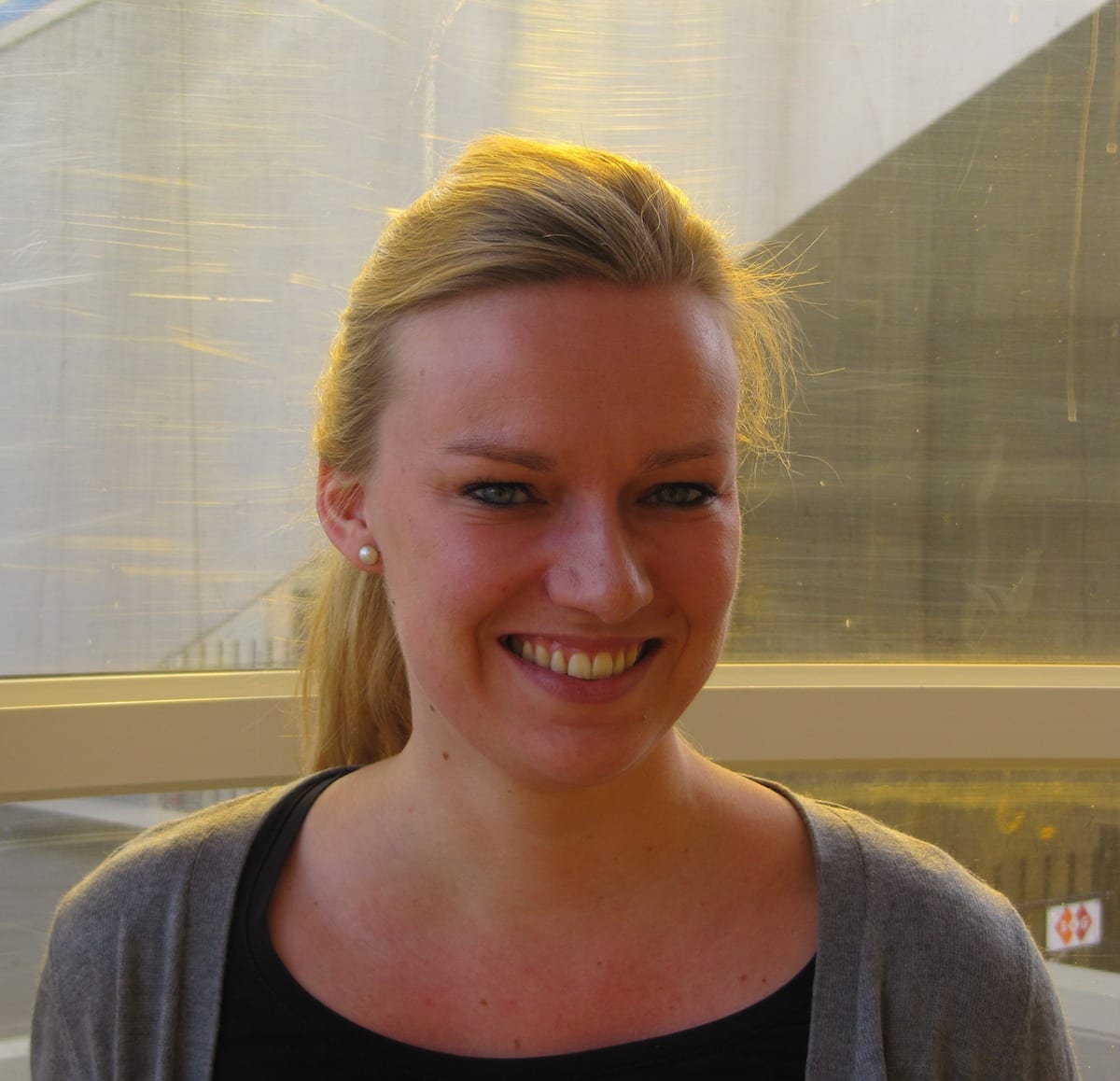
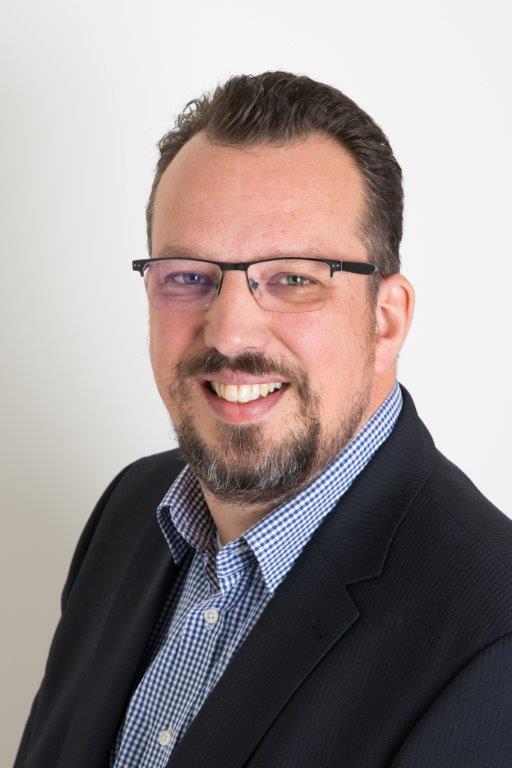
Read more
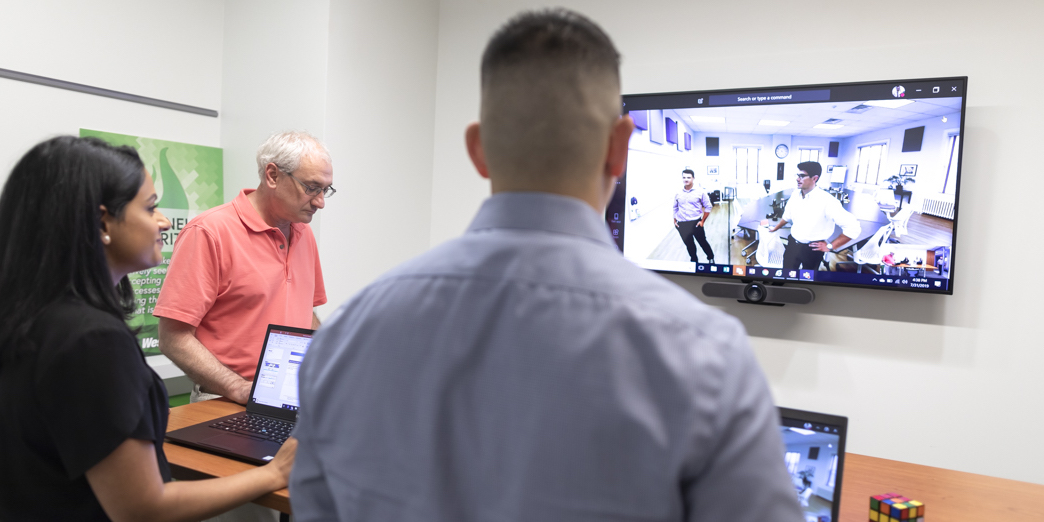
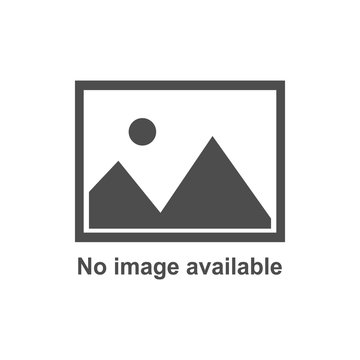
FEATURE – This global designer and manufacturer has leveraged a remote kaizen initiative to keep the flame of continuous improvement burning during the Covid-19 pandemic.

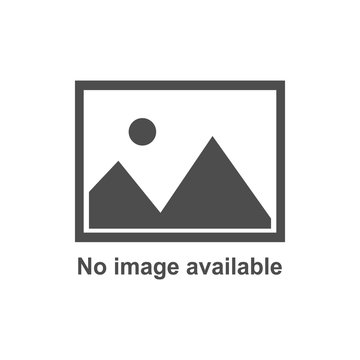
INTERVIEW – At last month’s International Lean Summit in Hungary, our editor sat down with the manager of a CooperVision site that is gradually converting its operations to make them leaner.
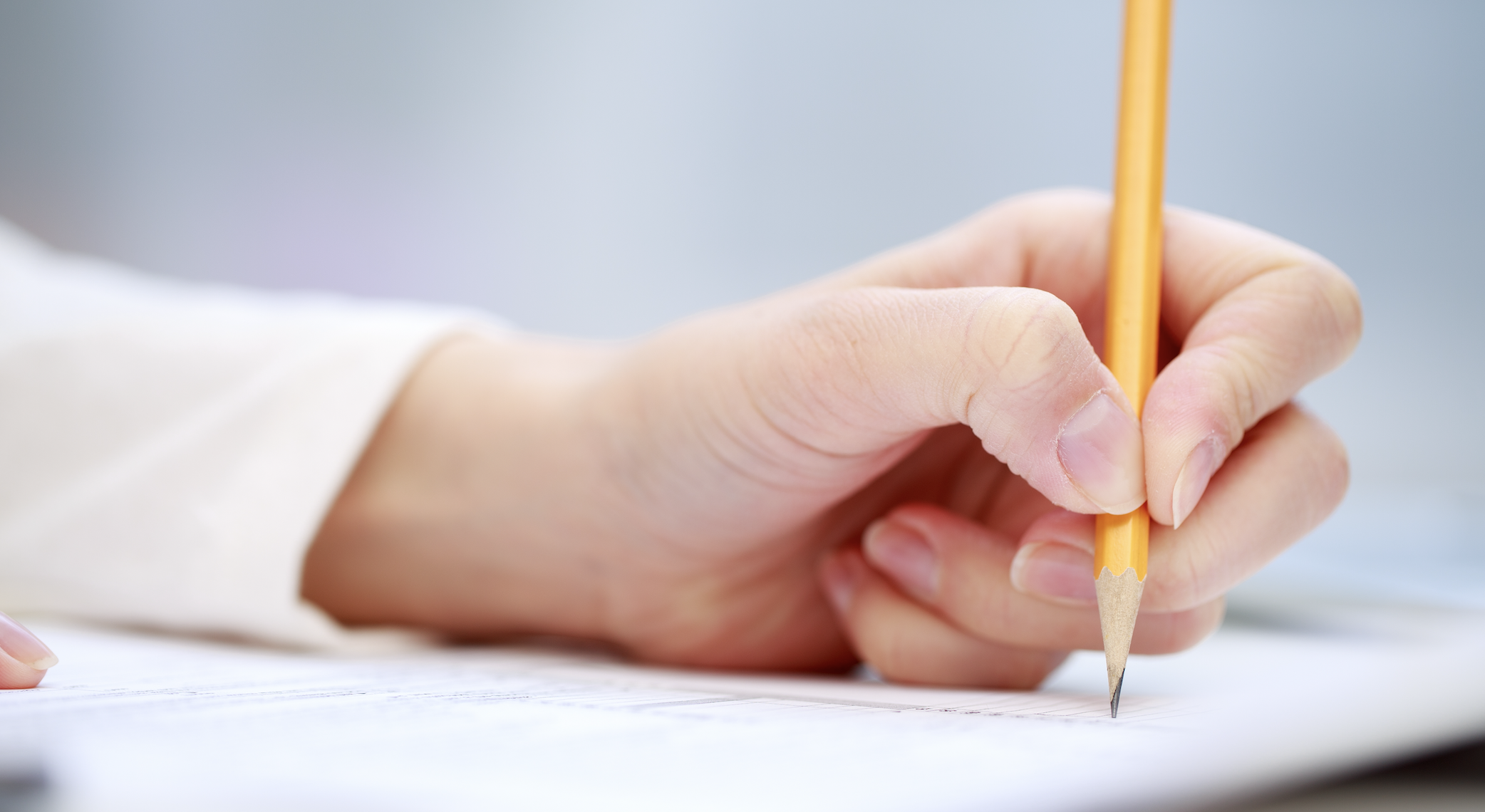
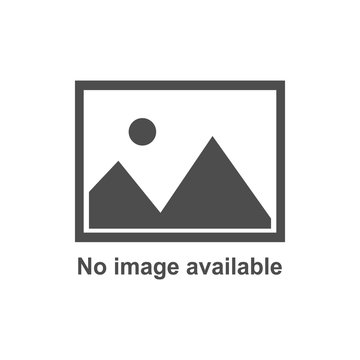
FEATURE – Using her distinctive narrative style, the author breaks down the A3 process to help you understand how it works and how you can tap into its potential.
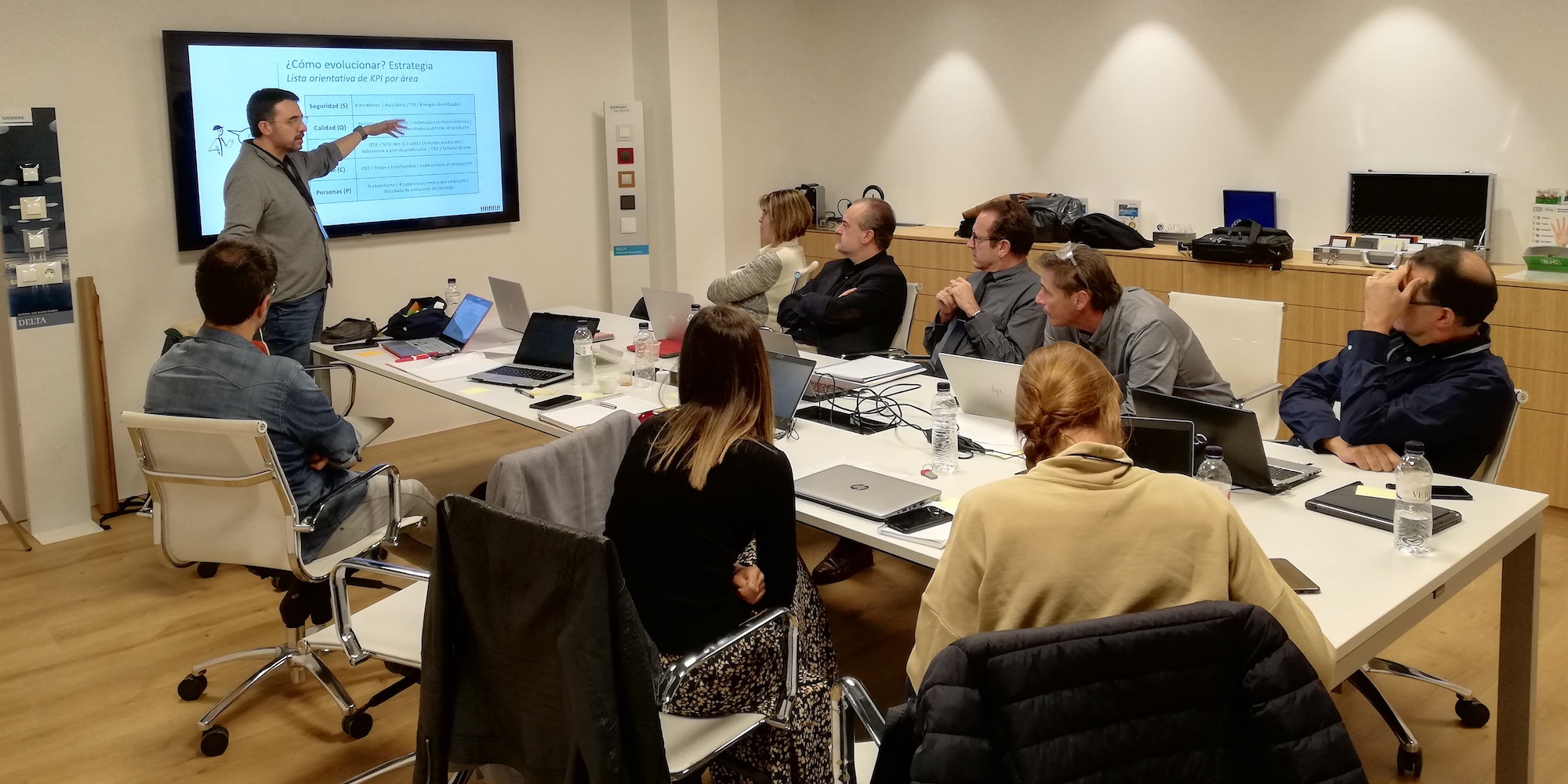
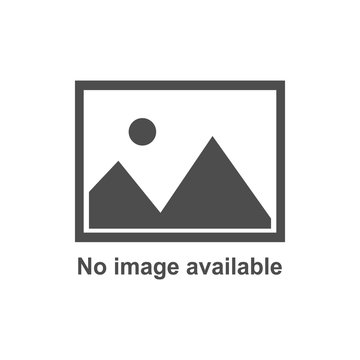
FEATURE – This Siemens Group-owned medium-sized manufacturer of electrical low-voltage devices has been experimenting with hoshin kanri. In this article, they share their experience and lessons learned.