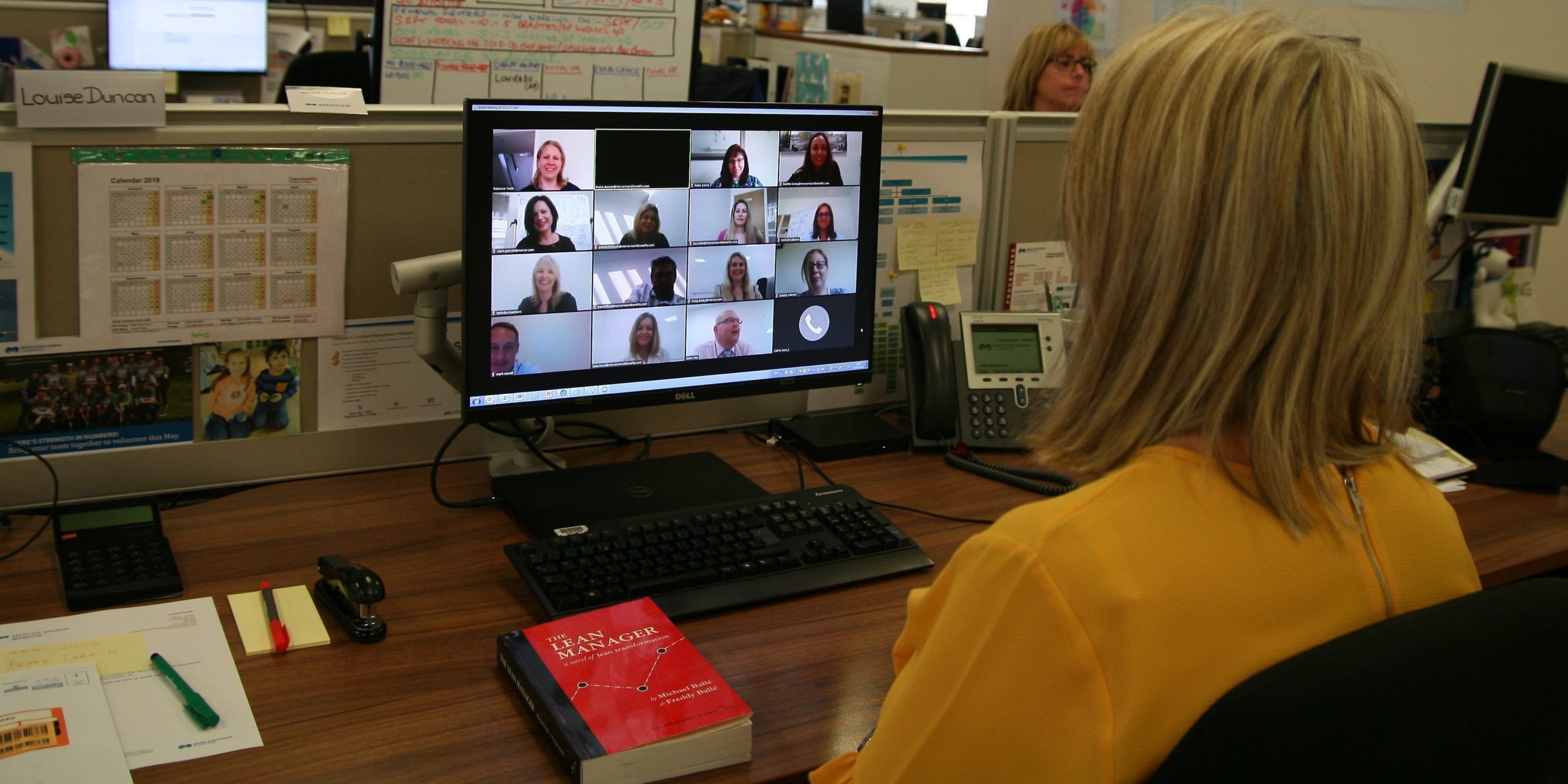
A virtual book club got us started on our lean journey
FEATURE – A UK-based team of client services managers working for HR consultancy Mercer is using a virtual book club to take their first steps into the world of lean thinking.
Words: Rebecca Veale, Team Leader, Mercer – United Kingdom
Lean was new to us, a journey just beginning and full of unfamiliar words and concepts to be explored. Our journey began with a one-day Lean Leadership workshop. Prior to this we were provided with the first chapter of Freddy and Michael Ballé’s The Lean Manager to read and then share our thoughts on during the workshop.
As a team of client services managers at Mercer, we had many questions: What was this all about? How could we make this work for us? How could we translate these concepts to our workplace, which to us seemed so different from the car manufacturing industry? Our business is about driving sales and revenue, and this is achieved through us providing a high-quality consultancy and administration service to our clients. We needed to go and see, to delve into the concepts and immerse ourselves in lean thinking. We spent the day discussing the first chapter of the book, learning about lean and walking the gemba of some of our teams. We talked about quality, timely delivery, processes, problem solving, and we asked why a lot.
Following the workshop, we needed a way to keep our lean momentum going and share the ideas with our teams. Some in the office were skeptical about lean, and there were challenges to overcome with managers feeling that its introduction was another thing to do that was going to take up valuable time. It was therefore important to show the benefits of adopting lean thinking and practices.
The idea of a The Lean Manager book club was to give us a chance to come together for a focused half-hour session every couple of weeks to discuss a specific chapter. The primary focus was on how the concepts covered in the book could directly translate to us and to the teams we manage.
We are all based in different parts of the UK, so we had to come together virtually. As a tool to run our sessions and capture our thoughts, we used a virtual reflection board. This enabled us to focus on a few points from each chapter, record our thoughts and identify ways to bring lean to our teams. We were sometimes joined by our manager and by our Continuous Improvement Leader and Operations Leader – they were going and seeing. We knew that lean is not just something to be discussed manager to manager and that we had to engage our teams, but the book club provided us with initial focus that could then be driven forward.
There were already many lean projects going on at a higher level, but the concepts had yet to filter down to the people doing the work at the front line – our teams often thought that it was not worth making suggestions for process improvements because nothing would change. This is something we have looked to turn around following one of our discussions in the book club calls, and we did it by deploying visual management boards for each team and starting to go on gemba walks regularly. The aim of our lean journey became to drive up quality, to eliminate waste from our processes, and to work together as a team to solve problems.
Our Operations Manager recently went on a gemba walk, and we shared the success of this on one of our calls. She said: “I needed to go and see. How could I ask my leaders if I wasn’t prepared to do this myself? I spent time with an experienced member of the team to go through the steps of one of their end-to-end processes. Initially, I was worried about asking too many questions, but that initial fear wore off very quickly. By listening and watching, it was evident that the team spent a lot of time copying and pasting from Excel into Word and manually calculating figures over and over again throughout the day. When I asked why that was, the team member just told me, ‘That’s how we do it.’ I am sure this is a common occurrence at the beginning of any lean journey. The 5 Why’s technique soon highlighted opportunities to enhance a tool used by the team every day, and this improvement has led to reduction in time and potential errors. However, more than that, it has shown the individuals that they can be part of making a change and have the power to take their ideas from concept to implementation.”
Having seen the success of our virtual reflection board, we have now discussed using a virtual kanban board to consolidate all the work we are doing around lean. Items to do, in progress, done, on hold or in need of urgent attention will all be easy to see.
In just a few months, we’ve embraced lean and are growing as a team and trying to transmit this alternative way of thinking to our teams. The book club has been instrumental in focusing our thoughts and planning a way forward. We have shared the success of our book club with other parts of the business, encouraging them to run a similar session. We also have plans to run a second book club using another book in the Freddy and Michael Ballé series: Lead with Respect. The journey continues!
THE AUTHOR
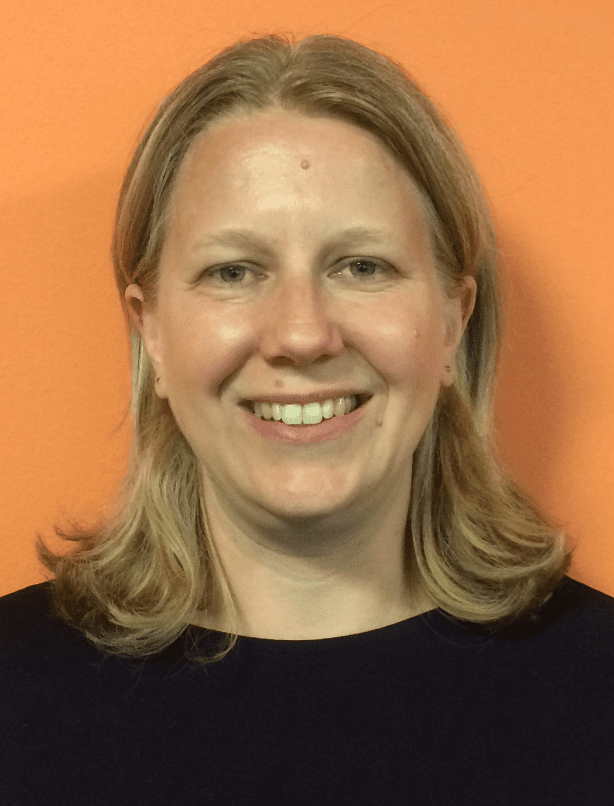
Read more
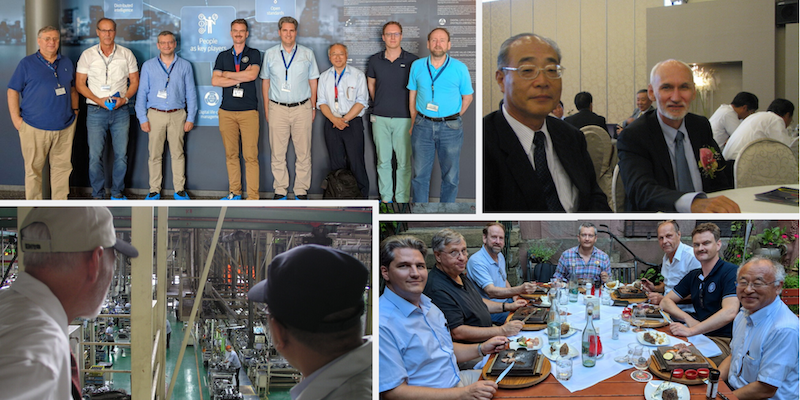
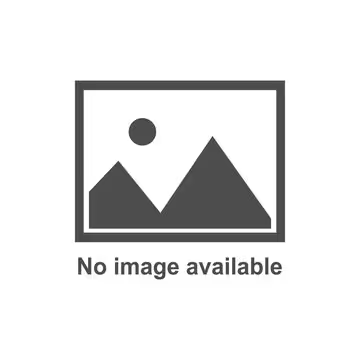
FEATURE – 2019 was another momentous year for the Lean Community. John Shook reflects on what we lost and what we gained in the last year of the decade.
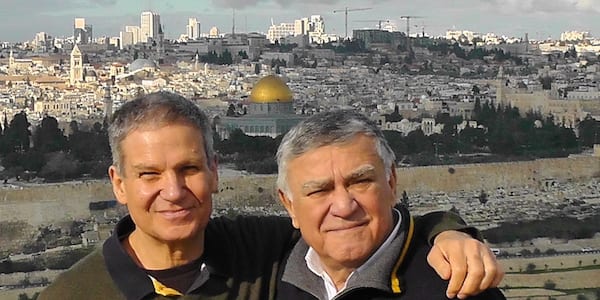
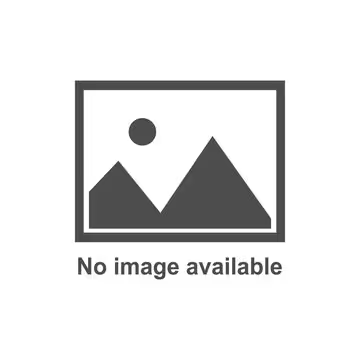
NEWS - Our institutes in Turkey and Israel have collaborated closely for years. A few weeks ago, the President of Lean Institute Turkey flew to Tel Aviv to learn about Israeli agriculture.
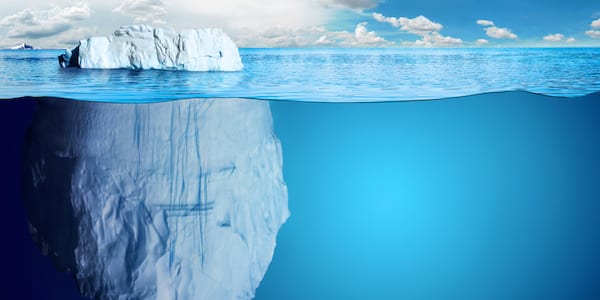
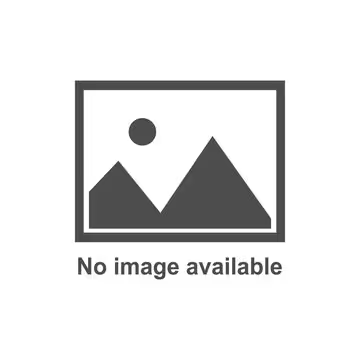
ARTICLE - What is lean? We all like to think that we know. This personal story reminds us all of how elusive the methodology can be, and how determined a practitioner has to be to fully grasp it.
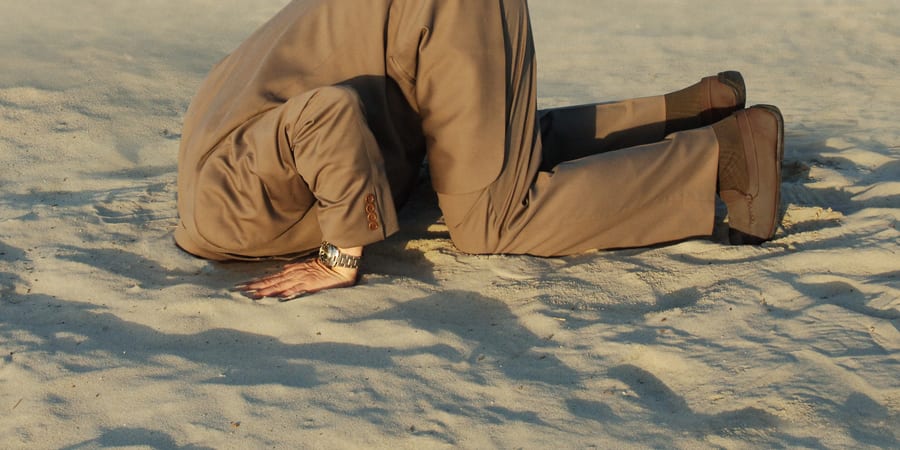
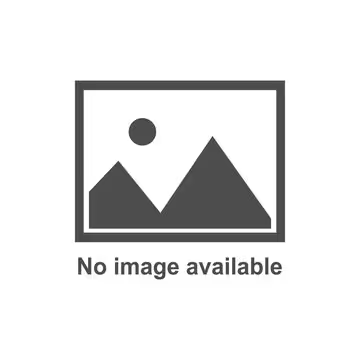
FEATURE – CEOs need to see people as assets and transform their companies’ product development systems if they are to tap into the full potential of a lean strategy.