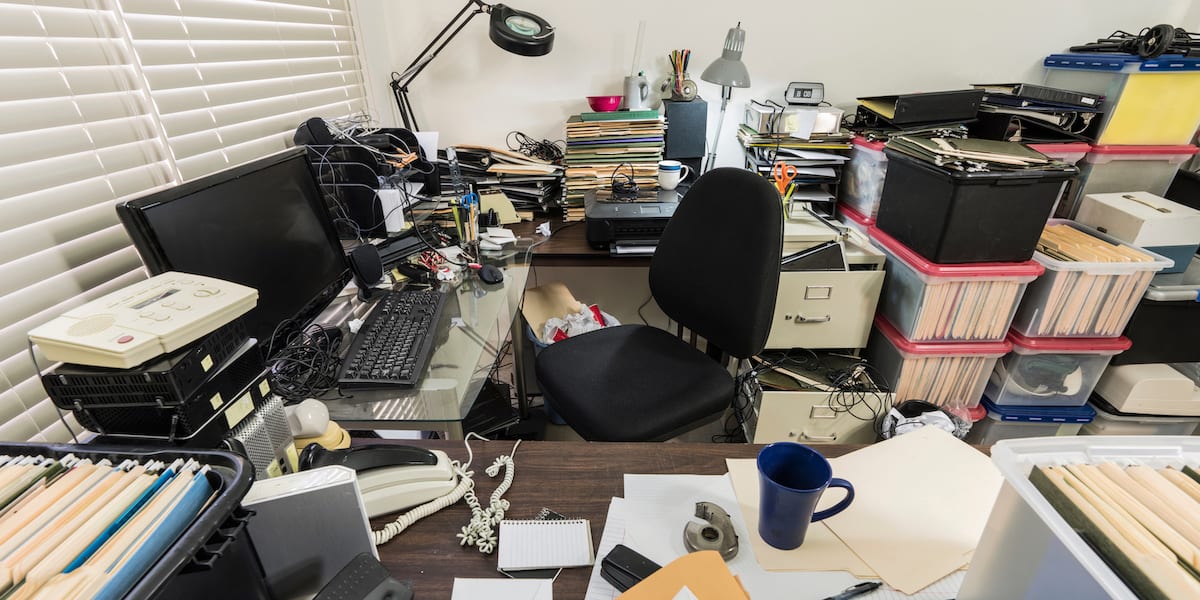
What is 5S?
FEATURE – In this roundup, we look at one of the most important lean tools and how it is deployed in organizations by bringing together PL articles on the subject.
Words: Roberto Priolo, Managing Editor, Planet Lean
According to the Lean Lexicon, the 5Ss are “five related terms, beginning with an S sound, describing workplace practices conducive to visual control and lean production.”
In Japanese, these five words are:
- Seiri: Separate necessary from unnecessary items – whether it is tools, parts, materials or paperwork – and discard the unnecessary.
- Seiton: Neatly arrange what is left – finding a place for everything and putting everything in its place.
- Seiso: Clean and wash the work area, equipment and tools.
- Seiketsu: Cleanliness resulting from regular performance of the first three Ss.
- Shitsuke: Discipline to perform the first four Ss.
These five concepts are typically translated into English as Sort, Straighten, Shine, Standardize, and Sustain. (Some add a sixth S for Safety.)
Interestingly, Toyota traditionally refers to just four Ss, because the idea of shitsuke is made redundant by the company’s system of daily, weekly, and monthly audits to check standardized work.
The Lexicon also reminds us this: “Whether four, five, or six Ss are used, the key point to remember is that the effort is systematic and organic to lean production, not a ‘bolt-on’ stand-alone program.”
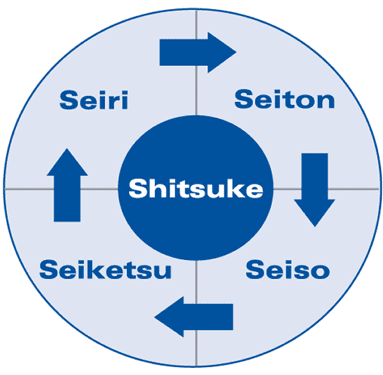
BEGIN WITH 5S
The application of 5S is often the first step in a lean transformation. This is because the idea behind it is simple to understand and its application brings immediately visible results. By helping people begin the transformation of their way of thinking and empowering them to organize their workplace (and therefore their work) in a different way, 5S can be a powerful catalyst in a lean journey.
Reporting from a lean conference in Tunisia, Norman Faull from Lean Institute Africa recently told us how 5S has been used by many companies on the continent to introduce a kaizen culture. A powerful reminder of the importance of sticking to the basics.
A great example of how 5S can be used to give that first push towards a lean transformation comes from this Italian hospital, where nurses initiated change in a department by bringing the 5S technique to the warehouses, nursing station and medical trolleys. Read about their work with 5S and the results it achieved here.
Lean farmer Ben Hartman also started his lean journey at its Indiana farm by applying 5S. Ben turned his warehouse overflowing with equipment into a handful of tools he can now load in the back of his truck. He explains how he did it in this interview.
The fact that 5S is a good first step in your journey doesn’t mean it’s an easy one or that you can simply forget about it after the first implementation. Like everything in lean, sustaining your 5S efforts is tough. In an important Yokoten column, Jim Womack writes: “Let’s suppose an organization is implementing 5S for the right reasons and in the right ways to improve the work. It seems like this should be easy once the work is correctly specified. Just sort, straighten, shine, standardize and sustain the process! But the sustain part is actually very hard. In my experience, as an inadvertent industrial and organizational archeologist, I have often observed the remains of 5S implementations (e.g., the tattered blue tape around the empty space where tools or supplies should be and probably once were). […] In practice, I observe that 5S has a different curve, with benefits often disappearing altogether in two short half-lives, one a steep decent and the second a nose dive.” Check out the column for a few great tips on how to ensure our 5S practices stick around.
5S IN LEAN
The importance of 5S in a lean transformation can’t be stressed enough. In fact, in this compelling article, Michael Ballé went as far as listing the lack of 5S efforts as one of the cardinal sins hindering our ability to kaizen at the gemba. In this piece, Michael writes: “The point of 5S is people learning, through the regular practice of the five Ss, to create the kind of work environment where standardized work is easy to follow. […] Without 5S, it’s unlikely that kaizen will get off the ground because people won’t try to own their workspace or try to make it better.”
It is interesting to see how, like for other lean tools, 5S is more important for the underlying principles it embodies than for the practice of keeping the workplace clean and tidy it teaches us. In this sense, 5S facilitates standardization and empowers people to own the resolution of the problems at the workstations.
Thinking that 5S is just about cleaning up and organizing a few shelves is very limiting. In the same way, don’t make the mistake of overdoing it with 5S – sticking tape around every single item in an office, for example (from chairs to water dispensers).
In this article sharing the account of a gemba walk at Tokheim Italia, Michael Ballé provides us with another important reminder: lean tools often mean different things to different people, and 5S is no exception. This is why it’s critical to ensure that the application of 5S truly benefits the operator. Michael writes: “How does 5S work out for the technicians, then? At the maintenance center, 5S is about helping operators restock their vans with the least waste and frustration possible.”
The benefits of 5S are several, but they aren’t always obvious (lean is a holistic system, and its positive effects are typically felt across the enterprise): Tokheim itself, for example, teaches us how practicing 5S had a positive impact on the company’s environmental record. Director Mauro Cartello says: “Waste generates waste. The better we become at eliminating waste and identifying things of real value, the smaller our impact on nature and use of natural resources, and the greater our business success.” Read the article to learn about 5S supporting Tokheim’s green performance.
5S METHODOLOGY VIDEO
THE AUTHOR
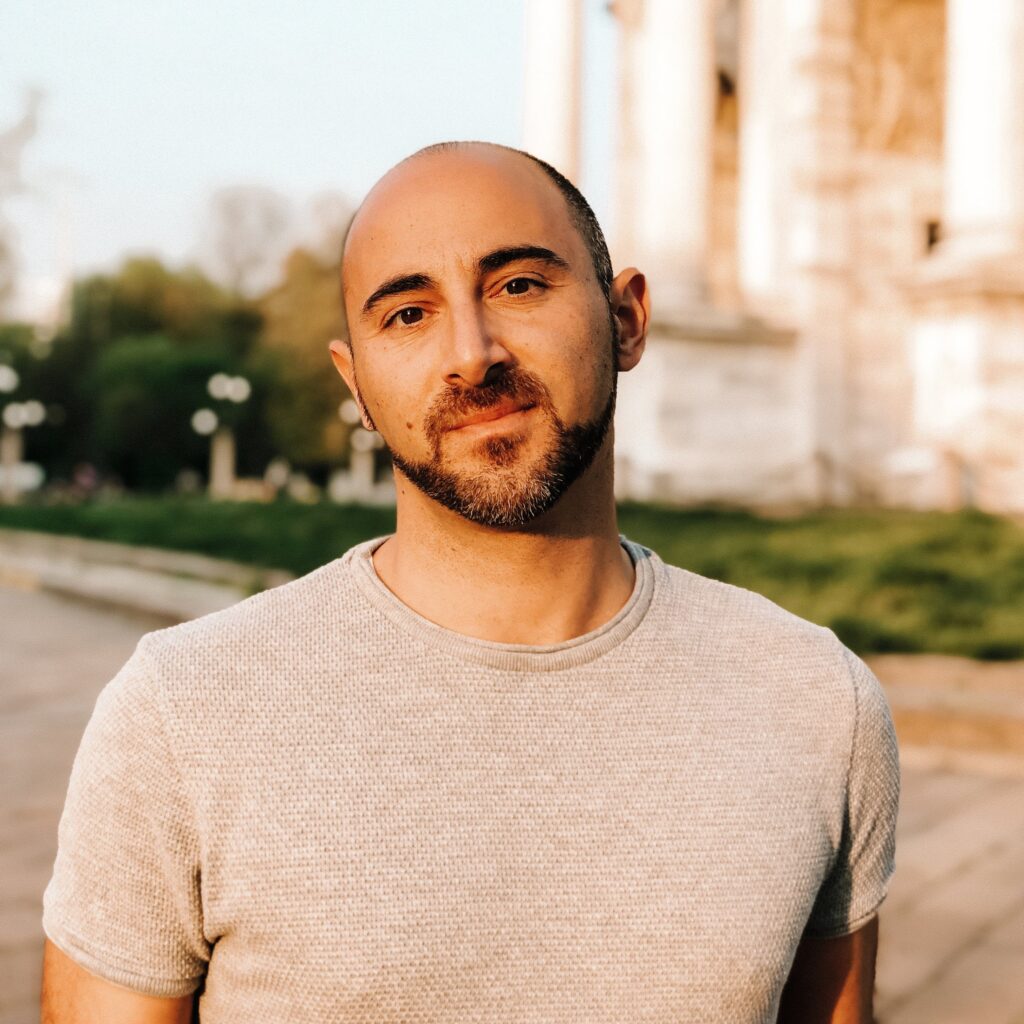
Read more
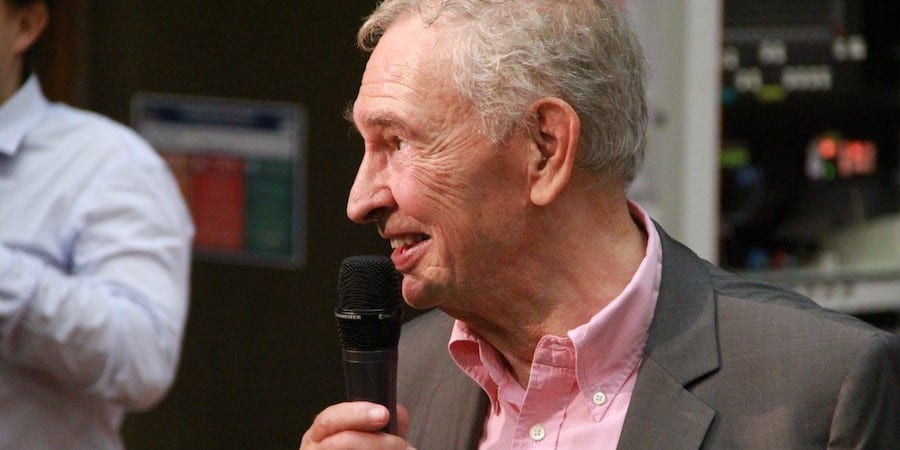
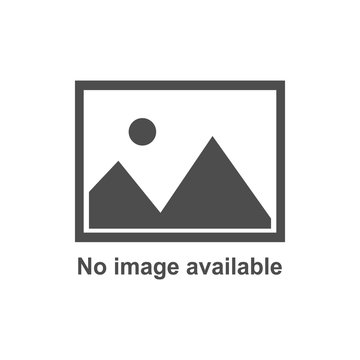
INTERVIEW – Having started to explore TPS in the mid-1970s, Freddy Ballé is one of the great pioneers of our movement. Here, he shares what he learned about Toyota over the past 40 years.
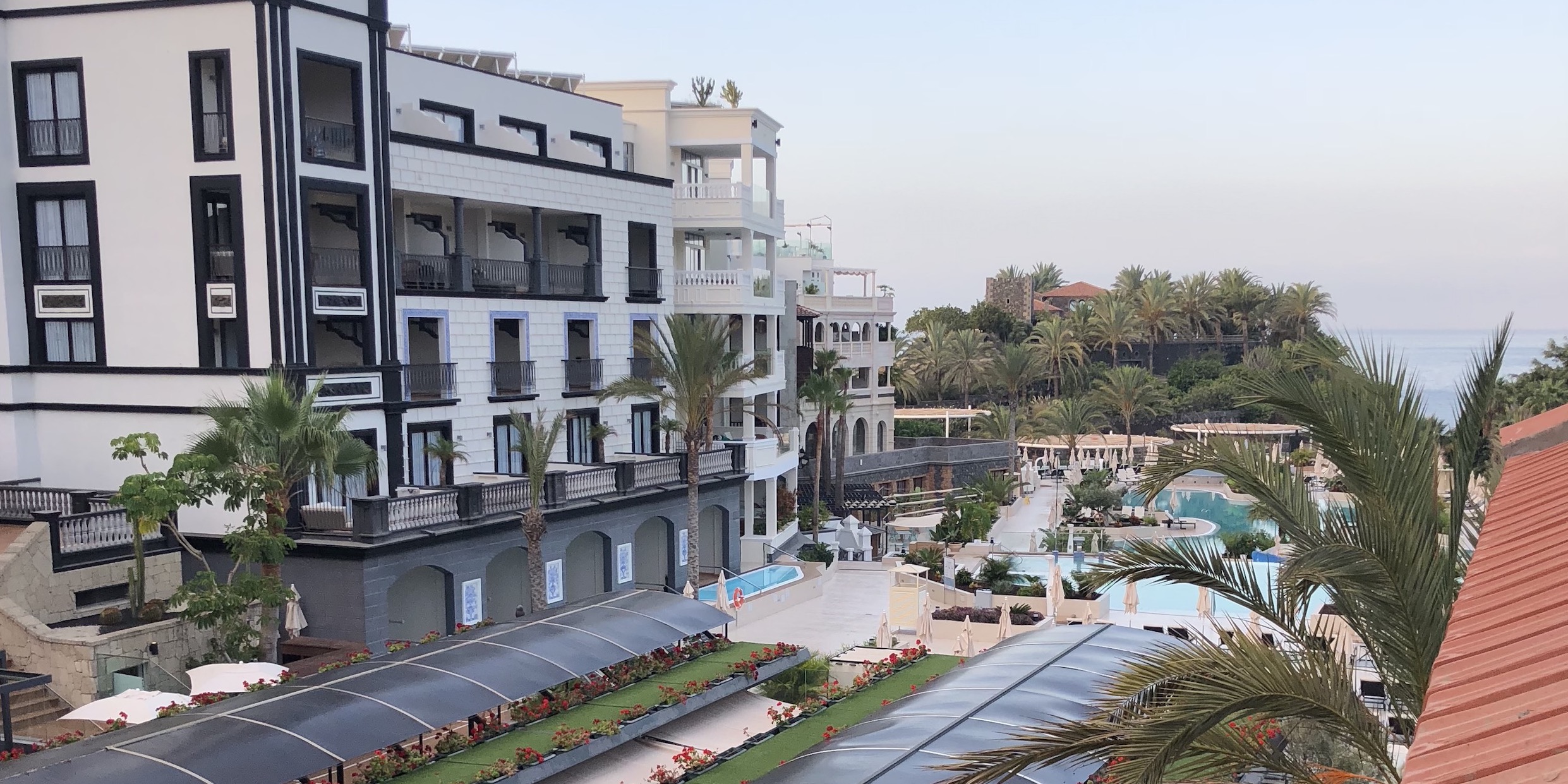
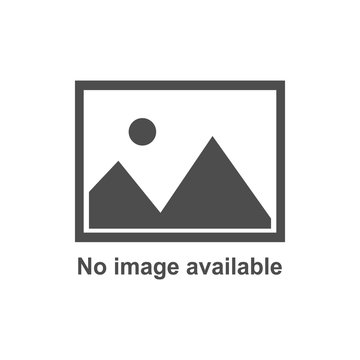
FEATURE – Dreamplace Hotels in Tenerife have been on an improvement journey for several years, but only recently did they find a way to truly become a learning organization: lean thinking.
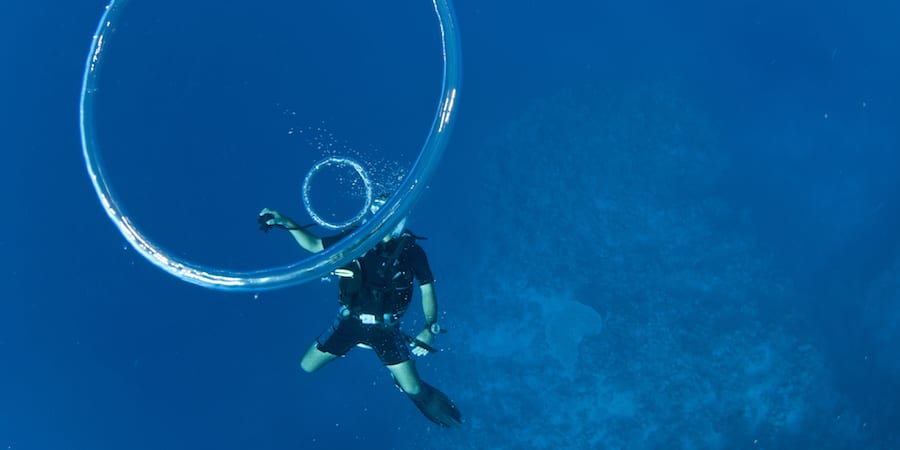
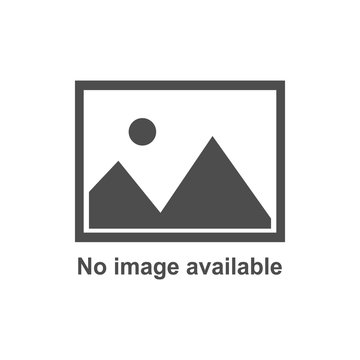
FEATURE – In lean, we talk about PDCA all the time… but do we actually practice it as we should? The authors discuss what makes for successful continuous improvement.
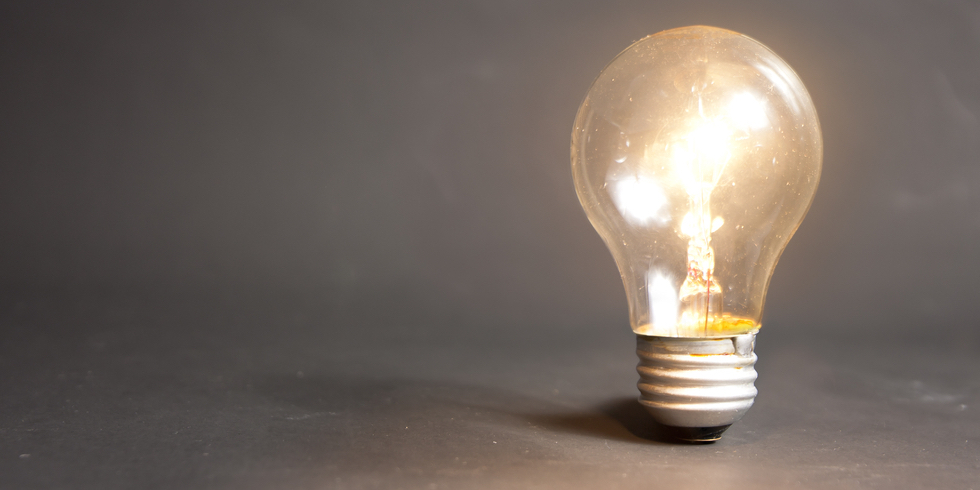
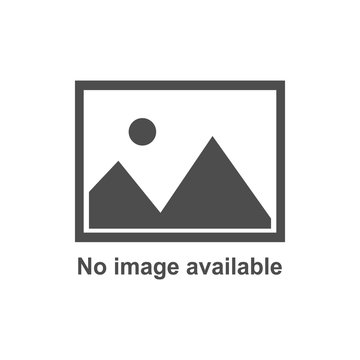
FEATURE – Tools and framework help us to bring lean principles to life and act on our strategies. The author introduces the Lean Marketing Canvas.