
A lean take on trade
WOMACK’S YOKOTEN – As tariffs spread, the author explains why forcing production to move overnight is wasteful, particularly for lean producers.
Words: Jim Womack, Founder and Senior Advisor, Lean Enterprise Institute
What is “trade”? It’s a curious concept in public consciousness. Making Teslas in San Francisco and selling them in Michigan is not trade in terms of today’s debates, even if some auto workers in Michigan lose their jobs in the process. But making Mercedes in Stuttgart and selling them in Michigan is trade in public discussions, even if the number of Mercedes exported from the US to Europe and China from a plant in Alabama largely offsets them. So “trade” in current usage means moving physical objects across national boundaries for sale with potential consequences for jobs.
Trade in services often seems to be viewed in different way. A vehicle manufactured in Country A and sold in Country A may well have been designed on the opposite side of the world. Isn’t that a cross-border trade in a “service” rather than a “good”? But because this movement isn’t visible as a separate product, it escapes notice. It isn’t “trade” at all as perceived by politicians and the public. Thus trade debates are usually about the location of factories rather than the location of product development and engineering.
Today the world is abuzz with dizzying developments affecting trade. The Americans threaten immediate 20 percent tariffs on autos coming from Europe but may not impose them if the Europeans buy enough American soybeans. The Chinese reduce tariffs on autos from any country from 25 to 15 percent and then, when the American put tariffs on a range of Chinese products, add an immediate 25 percent tariff (on top of the 15%) on American-made vehicles (including more than 100,000 BMW and Mercedes vehicles assembled in the US). Good grief!
Why is trade and the desire to manage it so important to politicians? Because many, along with their constituents, presume that trade into a country (imports) reduces jobs in that country while trade out of a country (exports) increases jobs. And many manufacturing jobs are believed to be “good, high-paying jobs”. So trade in manufactured goods is inherently prone to debates between countries about how much will be imported and how much will be exported. The emerging trade “war” could lead to substantial movements of production systems from one country to another, as happened, for example, in the early 1980s when Japanese automotive production systems were moved to the US and Europe in response to American and European trade barriers.
All very interesting, but what’s the lean angle?
Let’s begin by asking what trade flows would look like in a world of lean producers, open borders, a single currency, and equal pay for equal work. My belief is that there would be a lot less trade between countries and, in particular, over the long distances between regions (North America, East Asia, Europe, South America). This is because lean producers want to be as close to customers as possible to avoid the waste of unnecessary transportation and long lead-times that require the waste of unnecessary inventories. And lean producers work tirelessly to reduce the need for scale economies by cost-effectively building a high mix of products in the same value streams in the same production facilities in response to changing customer demand within local markets. Therefore, lengthy product journeys would likely decline within large countries and regions as well.
I think this is the world we should all be working toward. It can reduce wastes of many sorts. And I hope it is achieved before too many decades pass. But it won’t be soon. So how do lean thinkers engage with a world of unequal wages, imbalanced trade, gyrating currencies, and – quite possibly – borders with higher tariff walls?
I have some ideas but first a couple of features of lean production:
Lean production is sticky wherever it exists. It wants to stay where it is. This is for two reasons. First, a lean production system is designed to continuously improve. So for extended periods it may be possible to reduce costs at production complexes in Country A in order to overcome tariffs or unfavorable exchange rates in Country B. Second, any employer creating a truly lean production system will do this by engaging employees, training them in the daily practice of problem solving and improvement, and promising to protect their jobs. So relocating production to a foreign market at the first sign of trouble wastes hard-won human capital and is a contradiction of the social contract as well.
These attributes of lean production explain why Toyota has kept more of its production in its home country than most companies in the auto industry: Its lean systems continually improve to lower costs in the case of tariffs abroad or a strong yen at home and abandoning highly-skilled workers in Japan to create jobs in other countries violates common sense and goes against obligational norms as well. Since the 1980s, the company has increased foreign production at the same rate as foreign sales but has not reduced production in Japan, meaning a continuing automotive trade surplus with the world and a risk of trade barriers.
Lean production can only be transferred slowly and with difficulty from one country to another. The history of the past 40 years shows this to be true. Despite our best efforts in the Lean Community, it simply takes time to create a lean production system, aided by adjacent lean product and process development and lean supply systems, in a new country. We at LEI have been involved for the past five years with GE Appliances which has re-shored and, I’m happy to say, largely lean-shored its appliance production (and design as well) for the American market from Mexico and China to Louisville, KY, creating 5,000 jobs in the process. But it has been a difficult journey, which is not yet completed.
In the auto industry, Tesla not withstanding to the contrary, it takes four years even in the same country to build a new production facility and bring it to full production with a workforce that can employ lean practices daily with consistent results. In other industries, like raw materials (e.g., steel and aluminum), it may take even longer. And that is not likely to change.
This situation is perplexing: Lean is sticky and moves to new locations slowly while the political world may demand rapid relocation that may be physically impossible, and which is likely – after a time lag – to create new mass-production facilities inside protected markets. These facilities may be no better than the mass production facilities in the same markets that proved uncompetitive and were moved offshore. Thus the likely consequence of undue haste is mostly inflation as offshore producers raise prices to cover their costs of tariffs and domestic producers price up to nearly match them. (See my essay, “Move Your Operations Back from China? Consider Leanshoring Instead” from the Second Edition of my book Gemba Walks.)
So, the idea of bringing production closer to customers, as tariffs and other trade barriers seek to do, is not inconsistent with lean thinking over the long term and is the result that lean thinking will eventually produce on its own. But the idea of mandating production closer to customers overnight by means of tariffs from out of the blue is a nightmare. I imagine that we in the lean movement have hardly any influence on politics, but we can at least say that a long-term goal cannot be accomplished through the application of muri (overburden) to complex systems.
If politicians decide that they must create barriers to trade, they should follow the example of recent regulation of consumer and industrial products: clear performance goals to be reached steadily over long periods of time. The CAFÉ fuel economy regulations in the USA, for example, were set in 1975 at 27.5 miles per gallon for cars and SUVs, with a timetable extending to 1985 for full compliance. Let’s not add mura (unnecessary variation) and muri (over burden from trying to do too much too fast) to the muda inherent in abandoning existing production systems and reestablishing them on the other side of national boundaries.
Setting long-term goals for trade balances might give politicians the short-term victories they crave while leaving time for adjustment. And there may be new politicians with different priorities as time goes on in any case.
A final point: If facilities really are to be moved to accommodate new trade barriers, I hope the Lean Community will be deeply involved in making sure that new trade-compliant production systems are as lean as possible. Getting production and design close to the customer, building lean socio-technical systems methodically and deeply, and defending them once in place is the best lean stance on trade over the long term – whatever the politicians may do.
THE AUTHOR
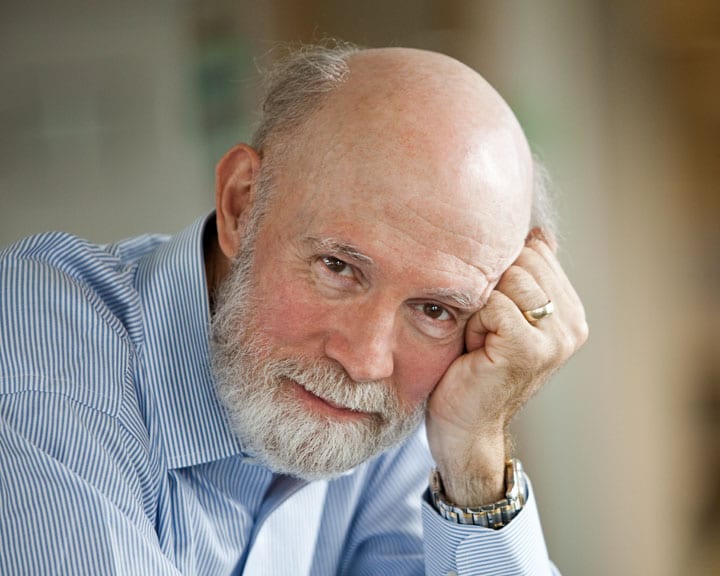
Management expert James P. Womack, is the founder and senior advisor to the Lean Enterprise Institute. The intellectual basis for the Cambridge, MA-based Institute is described in a series of books and articles co-authored by Jim himself and Daniel Jones over the past 25 years. During the period 1975-1991, he was a full-time research scientist at MIT directing a series of comparative studies of world manufacturing practices. As research director of MIT’s International Motor Vehicle Program, Jim led the research team that coined the term “lean production” to describe Toyota’s business system. He served as LEI’s chairman and CEO from 1997 until 2010 when he was succeeded by John Shook.
Read more
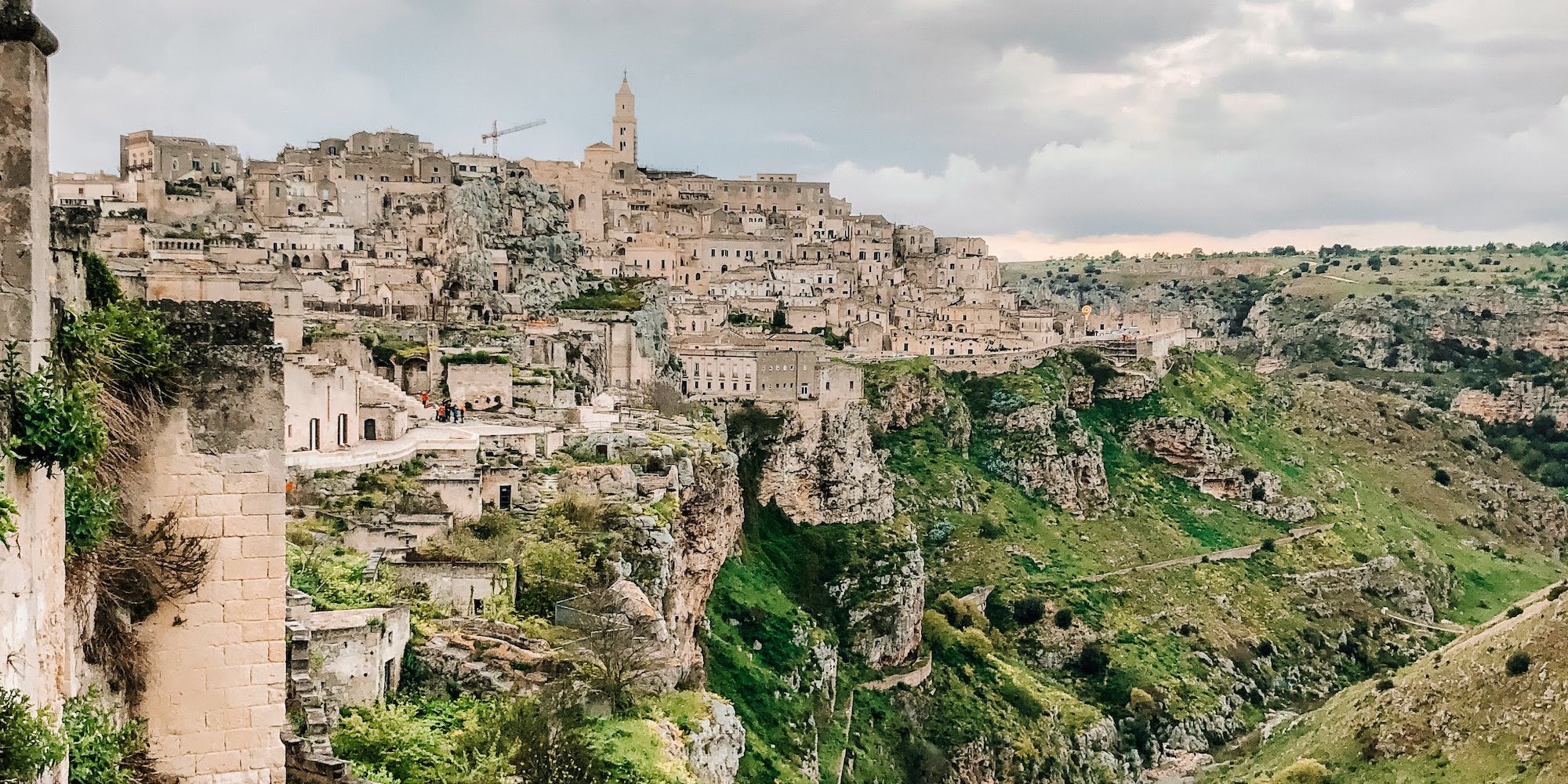
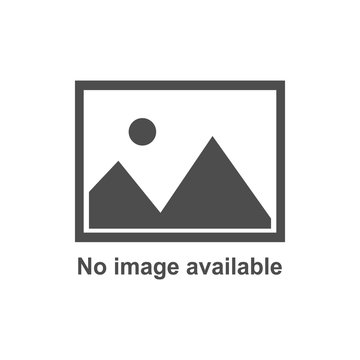
FEATURE – Using lean marketing principles, an entrepreneur in southern Italy was able to pivot from a potentially bad investment and create a unique customer experience instead.
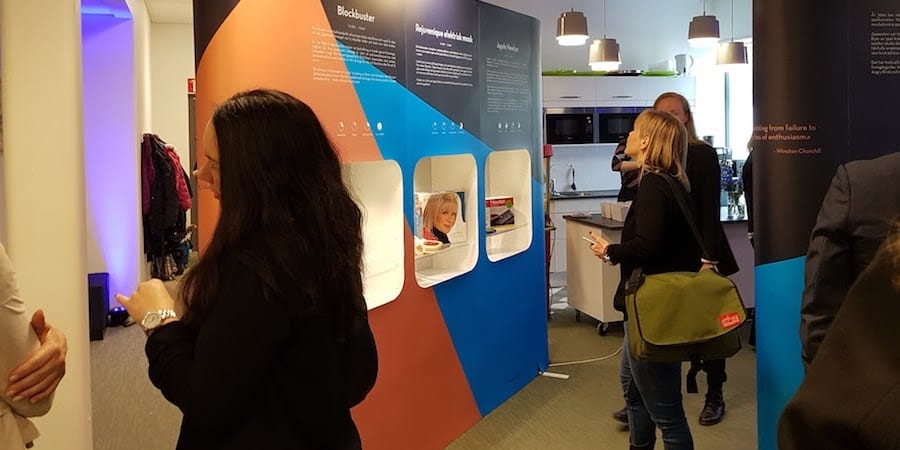
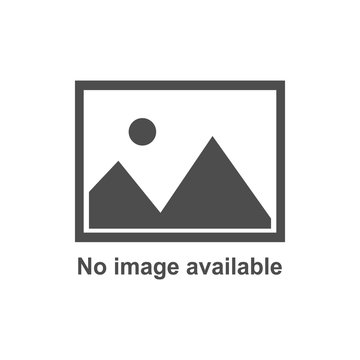
INTERVIEW – Last month the Museum of Failure opened in Sweden. We caught up with the curator, who tells us what the museum is all about and why failure is now “cool”.
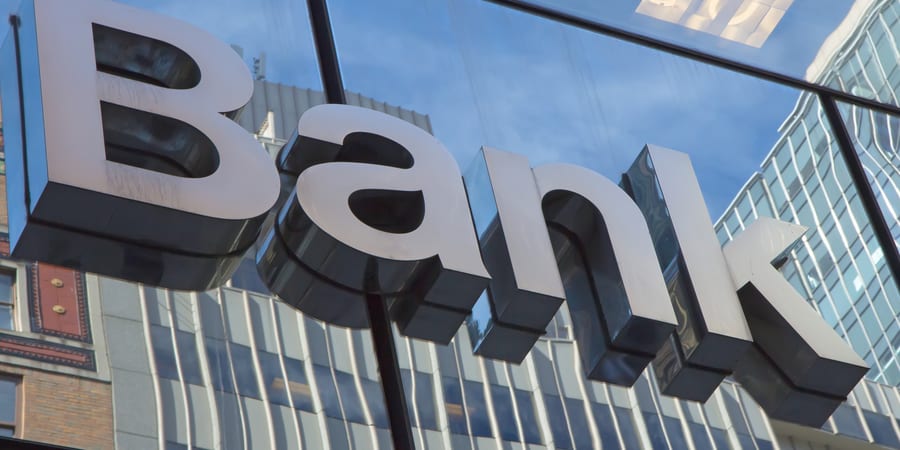
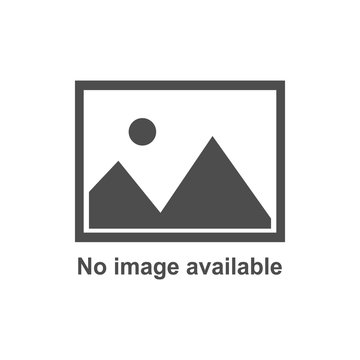
INTERVIEW – Planet Lean interviews Silvia Cespa of Italy’s Banca Nazionale del Lavoro, a bank that boasts one of the most advanced IT departments in Europe. How did it get there? Through a six-year transformation towards lean banking.
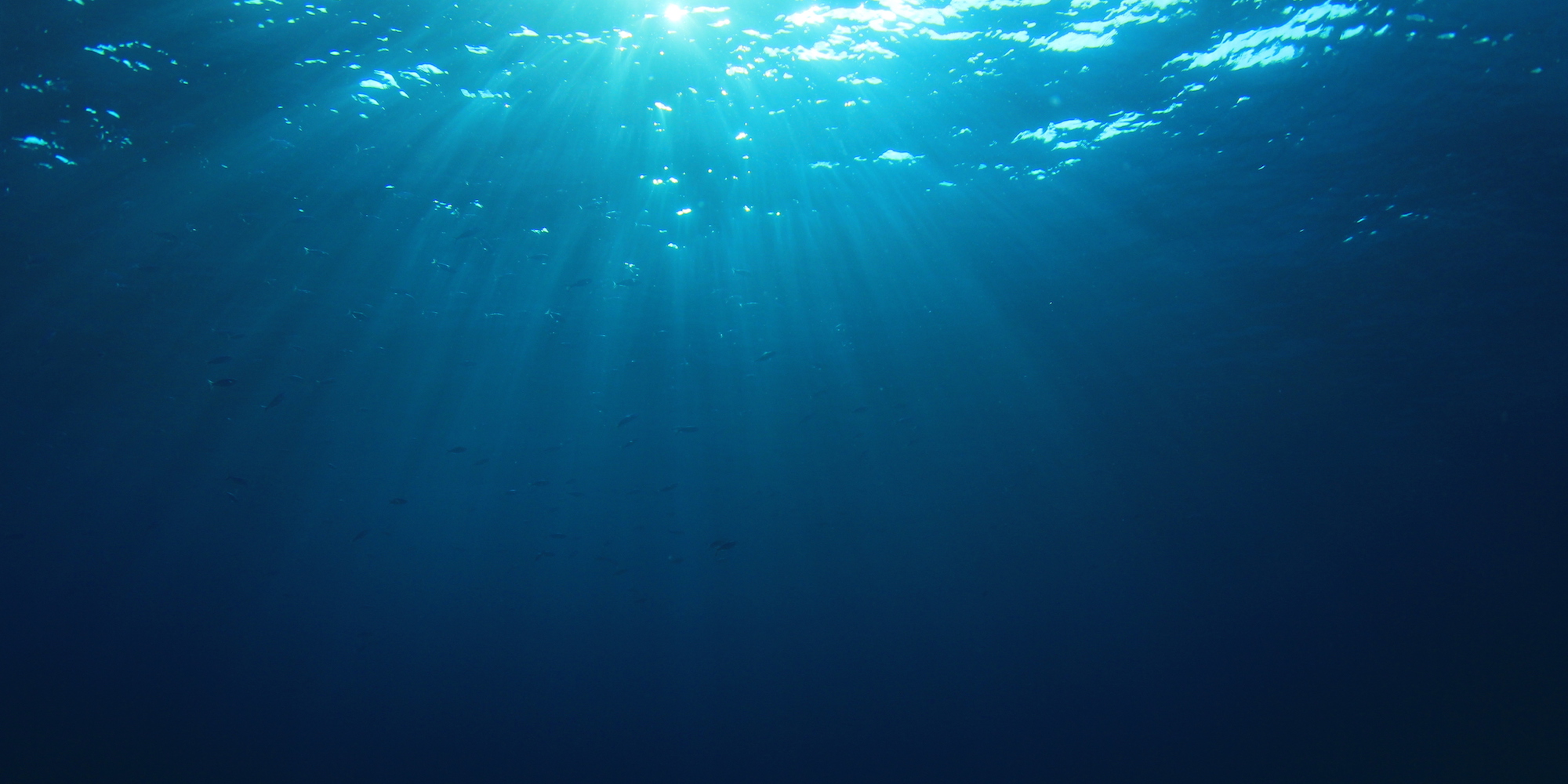
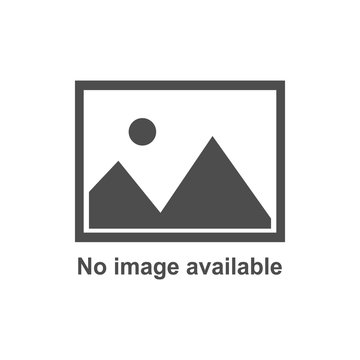
CASE STUDY – Designing good products is challenging in itself, but doing so in harsh, impenetrable environments like the seafloor presents even bigger problems. The answer? Lean product development.