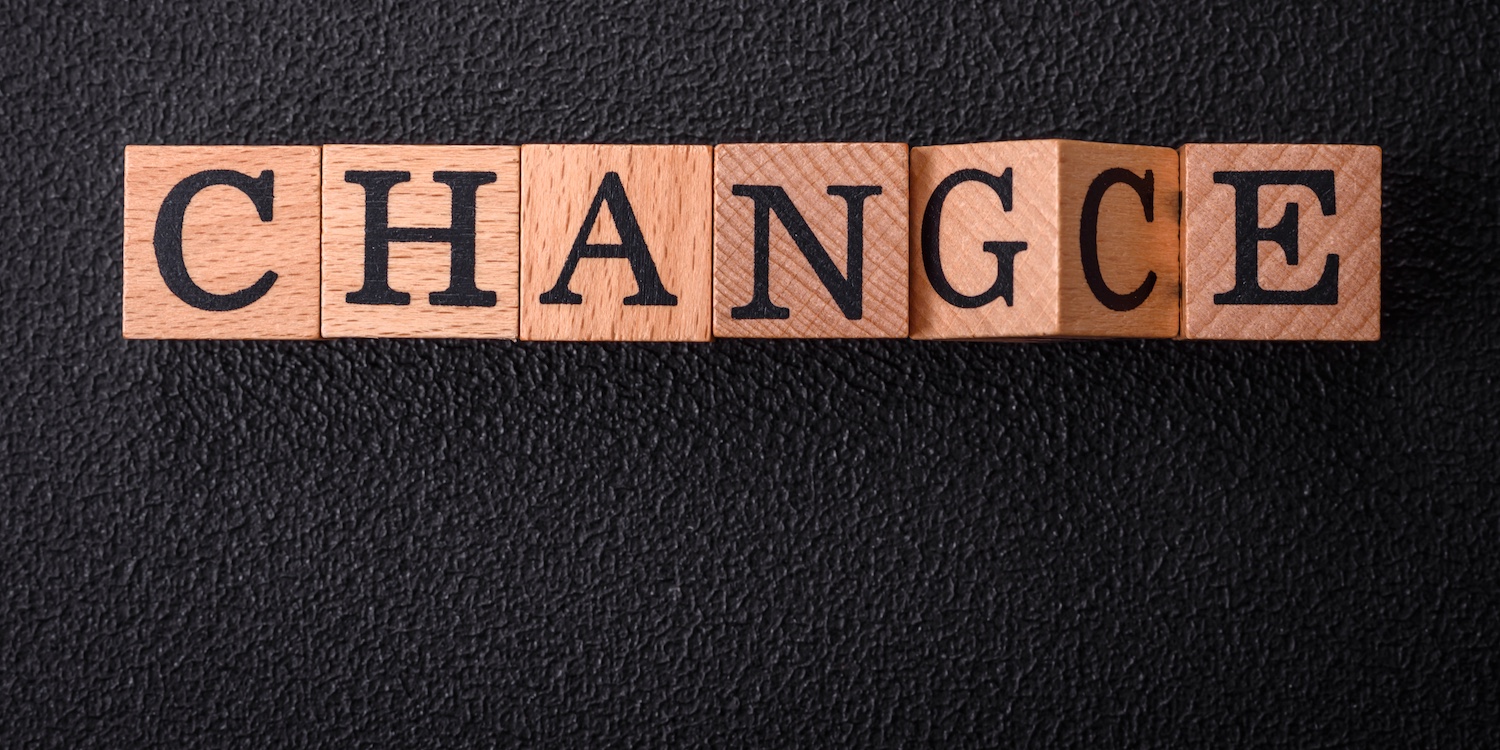
Adapting Lean for a changing world
FEATURE – Ahead of his presentation at next week’s Lean Global Connection, Jim Womack explains why Lean is made for a world in turmoil but urges us to strike a balance between immediate response and thorough understanding of the problem.
Words: Jim Womack, Senior Advisor, Lean Enterprise Institute
The world is clearly changing, and lean thinkers are sensibly asking how Lean will need to adapt. The good news – which I will explain in my presentation to start this year’s Lean Global Connection – is that we don’t need any fundamental invention. Our key ideas and methods are adequate to the situation. We do need to change our orientation, from a stable world where we showed organizations how to continuously improve to a chaotic world where kaikaku (dramatic change through hoshin deployment), kaizen (through A3 analysis), and, yes, daily management (to prevent deterioration of processes that still meet the needs of the moment) are all deployed in order for lean organizations to survive and flourish.
Let me unpack this. Lean organizations have always focused on change because improvement (which requires change) is always necessary and possible. These organizations are inherently adaptive. The issue now is adapting to what. We are in an environment where the rules of economic competition are changing as the geopolitical system is changing as fundamental technologies are changing as the climate is changing. Wow. That requires a lot of adaptation.
We are used to thinking of hoshin kanri as a leisurely process on an annual cycle aiming for a North Star three or even five years ahead. But in a time of dramatic change, we can and must speed up the clock. Similarly, problem solving for existing processes is well suited to A3 analyses extending for a considerable period. But in a time when new problems can emerge suddenly and dramatically, we again must speed up the clock.
What’s needed is a balance between immediate response and the need to truly understand the problem. And this needs to be struck by a chief engineer responsible for each opportunity and/or problem, who knows that heroic leaps to solutions – no matter how satisfying in a crisis – are inferior to pursuing a portfolio of countermeasures through rapid prototyping and experimentation. Toyota’s recent experience in developing no/low-carbon vehicles is instructive. While the entire global auto industry was leaping wheels first to pure battery electric vehicles, Toyota continued to focus on developing many alternatives – BEVs, plug-in hybrids, hybrids, hydrogen fueled internal combustion vehicles, and hydrogen fuel cell vehicles. And now the whole industry is in retreat, without much experience with alternatives to draw on, as pure EVs with proven battery technologies prove too expensive to sell in mass markets.
So, the world still needs us. And we have the ideas and methods organizations will need to survive and even flourish in rapidly changing conditions. But we must, as always, make our case to the world with compelling examples of success. Let’s get going, using the Lean Global Network and the Lean Global Connection as our megaphones!
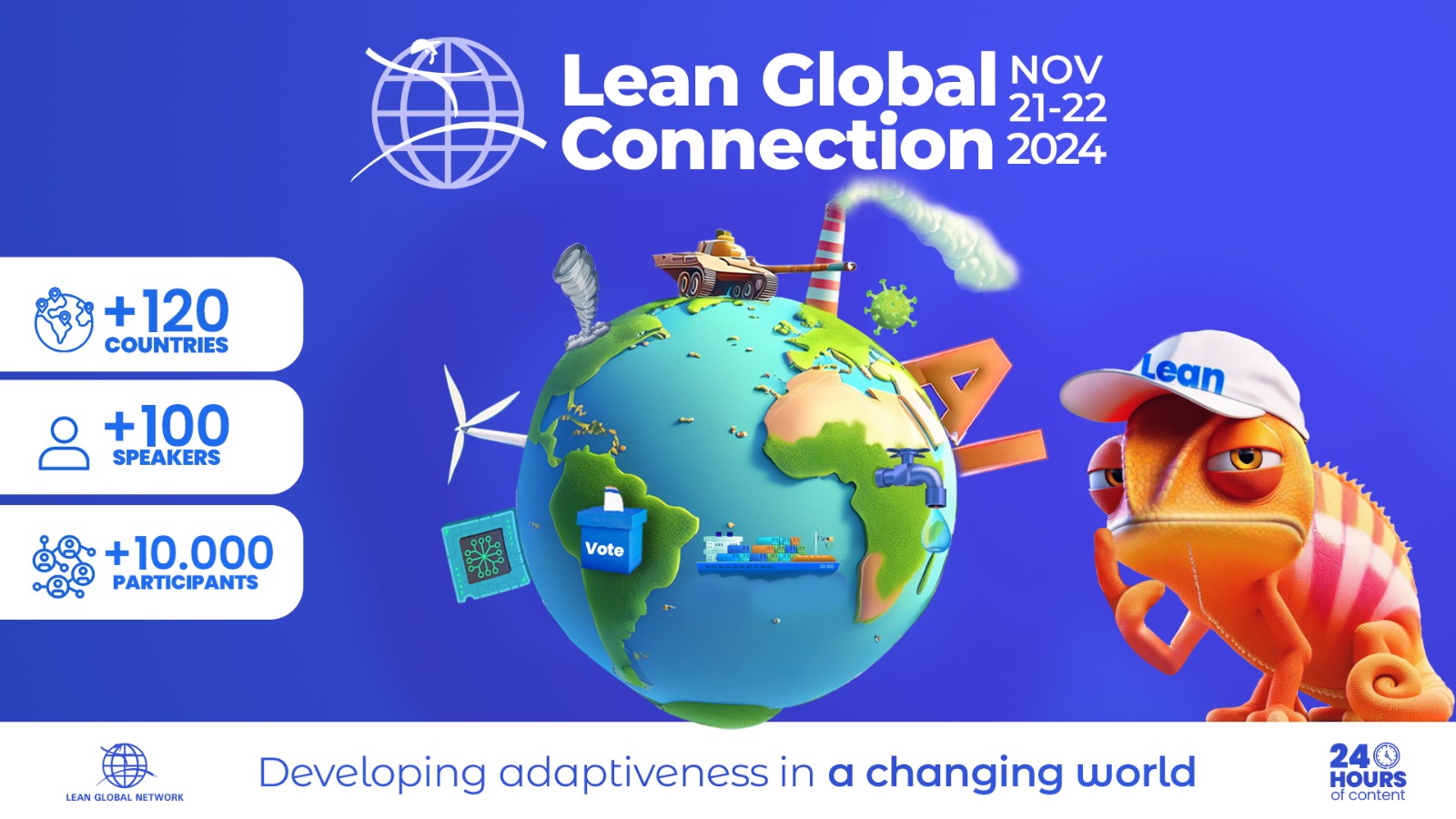
THE AUTHOR
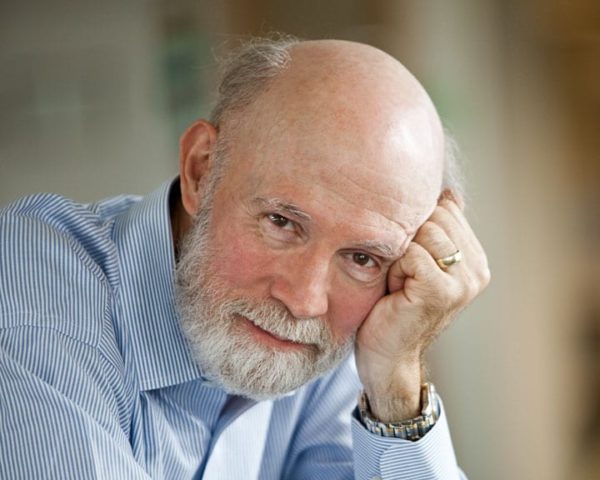
Read more
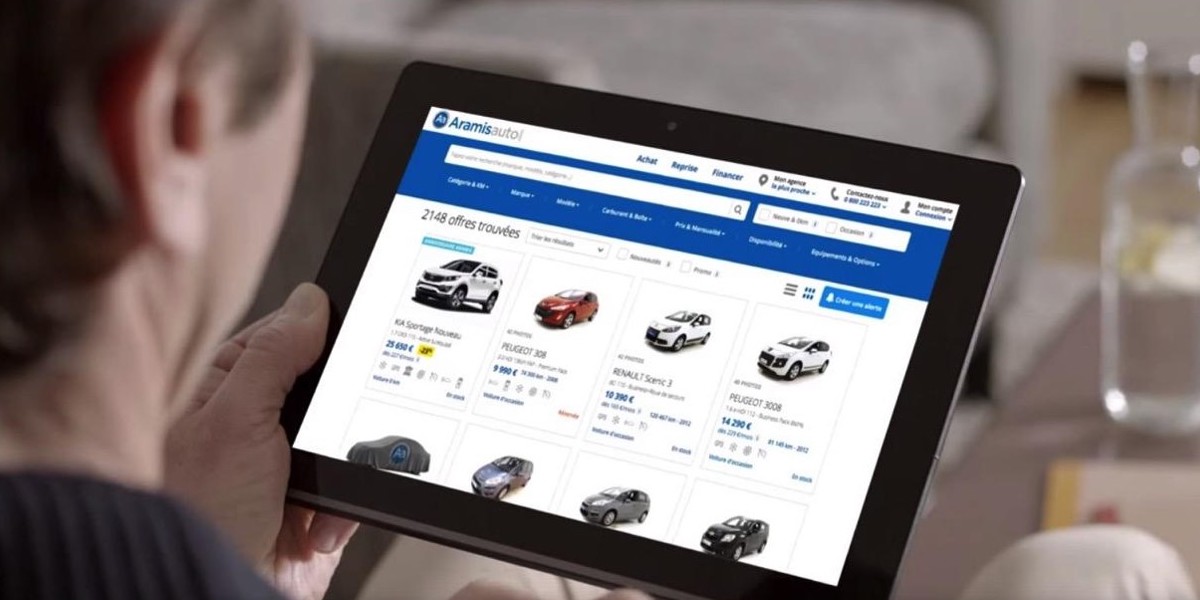
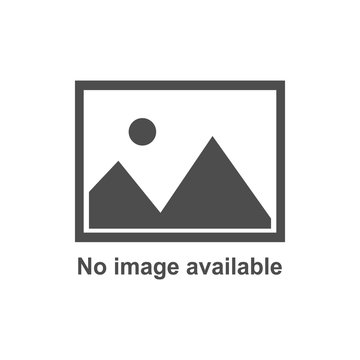
NOTES FROM THE (VIRTUAL) GEMBA – Throughout the lockdown, this car-selling business has never lost its focus on people development. The author learns how this approach is helping the firm make the most of the crisis.
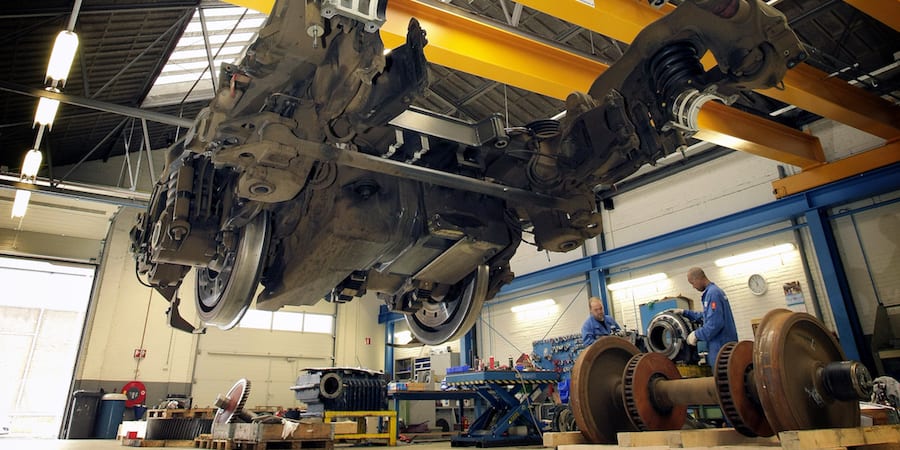
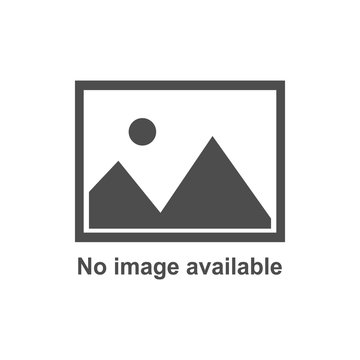
FEATURE – A Dutch company that maintains and overhauls train bogies has realized that in order for lean to work, a focus on continuous learning must be established. Here is how they are trying to get there.
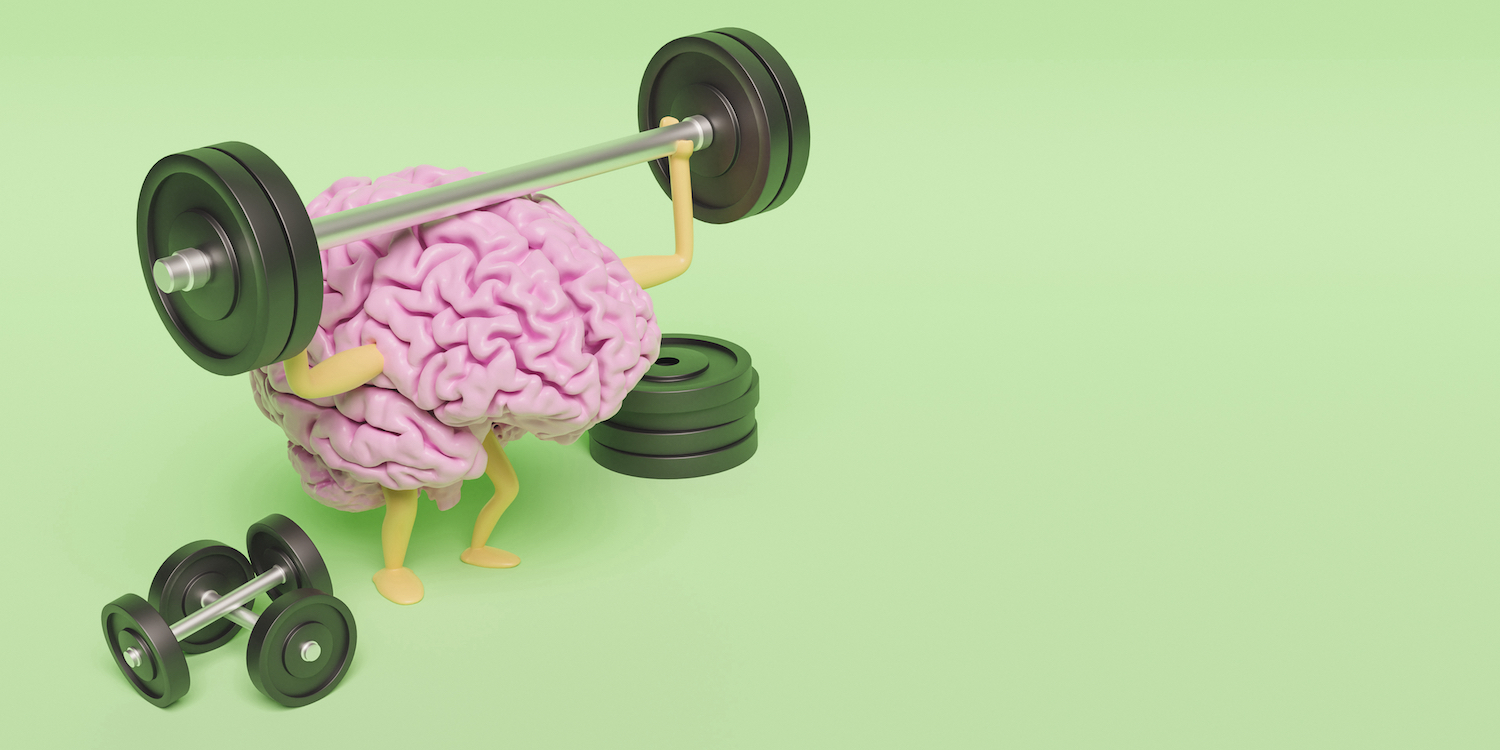
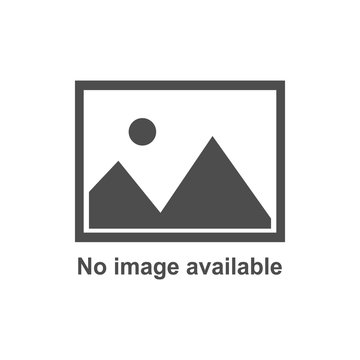
FEATURE – In this interesting piece, the author explains how lean provided everyone, everywhere with a framework to work their intuition muscle and develop insights.
Read more
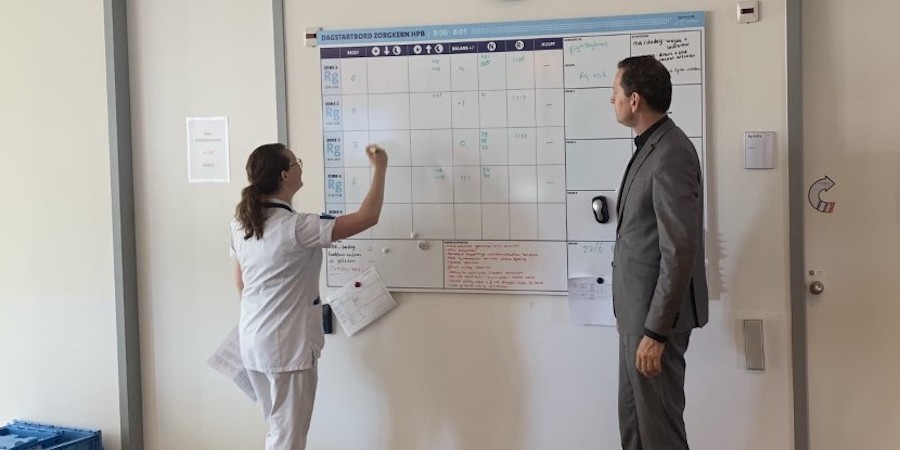
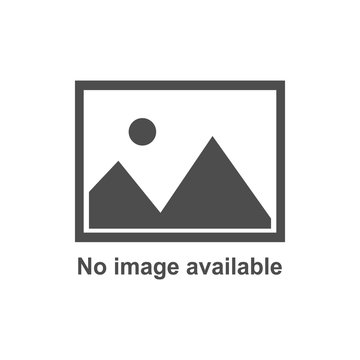
FEATURE – Our editor recently caught up with the director of the largest hospital in the Netherlands and asked him about the lean transformation he’s leading there.
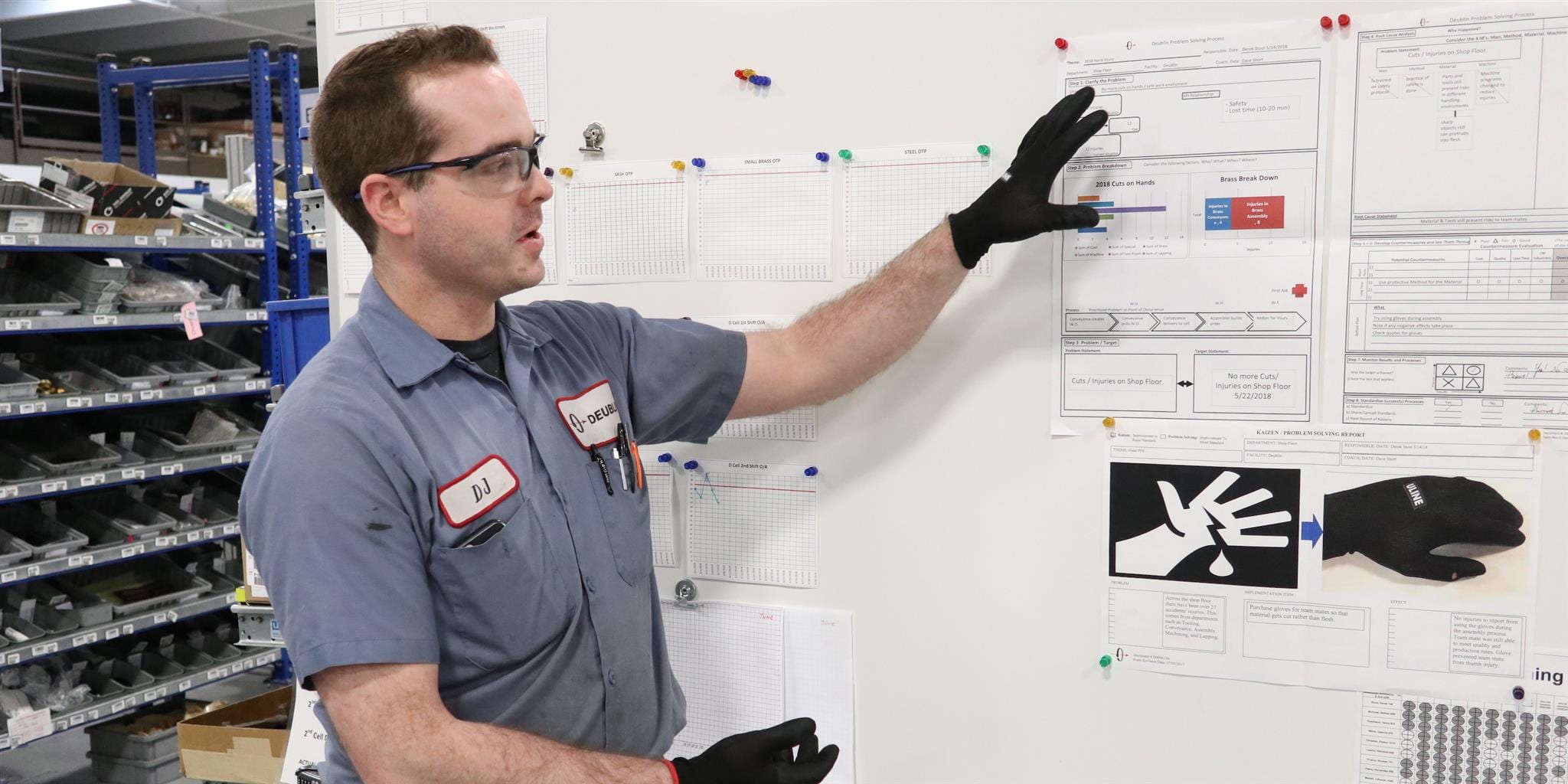
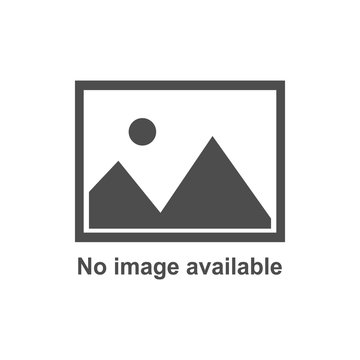
WOMACK’S YOKOTEN – The author visits a company that has sustained lean for a decade. In trying to understand how they did it, he finds how fundamentally the management system has changed.
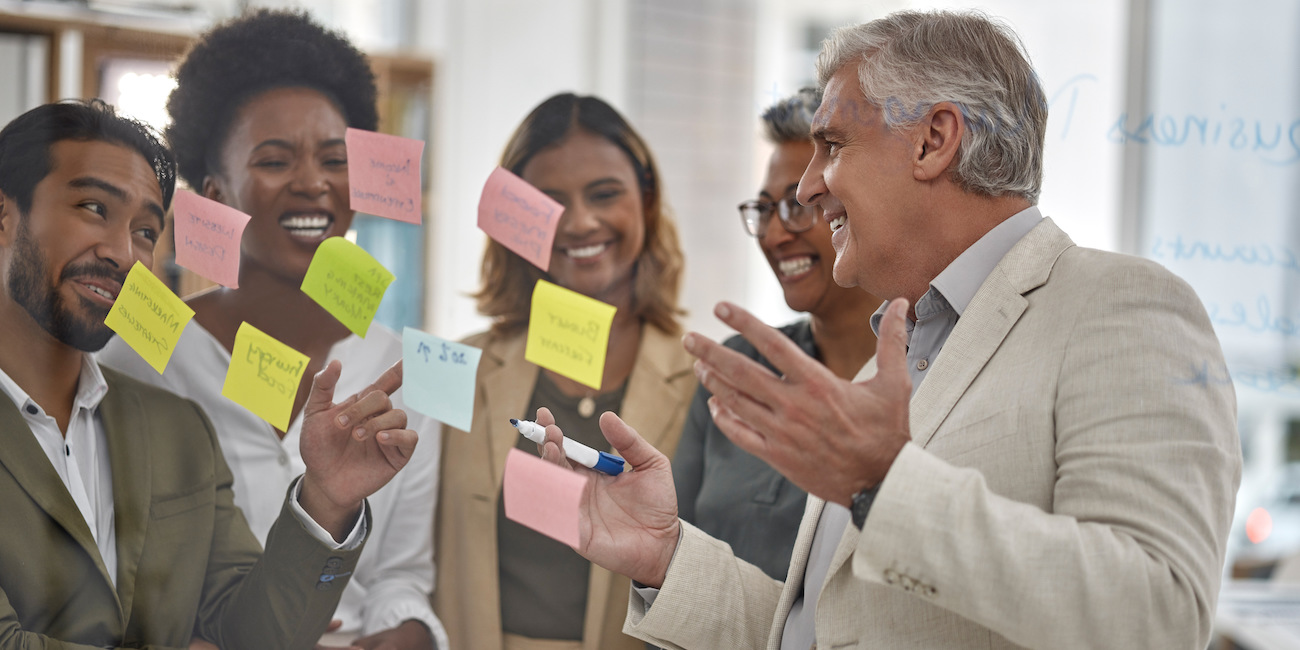
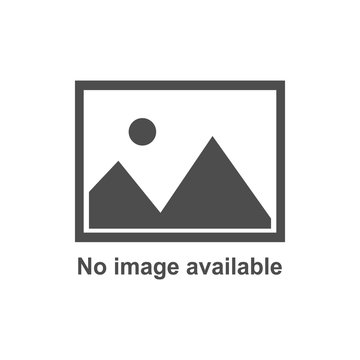
FEATURE – The author highlights the critical “power skills” leaders need to provide the right support to the transformations they lead.
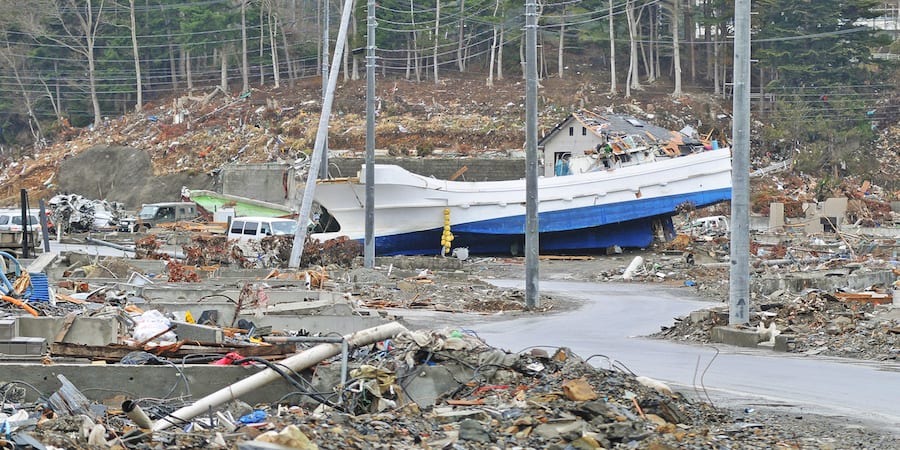
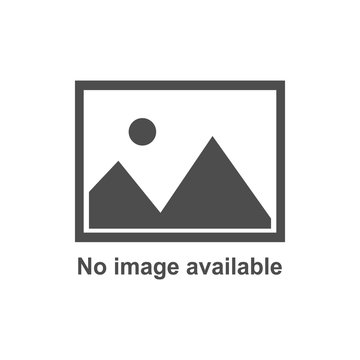
FEATURE – Much has been said and written about Toyota’s ability to recover from disasters. What many don’t realize, however, is that the company’s recovery strategy is informed by its underlying values – not just its tools.