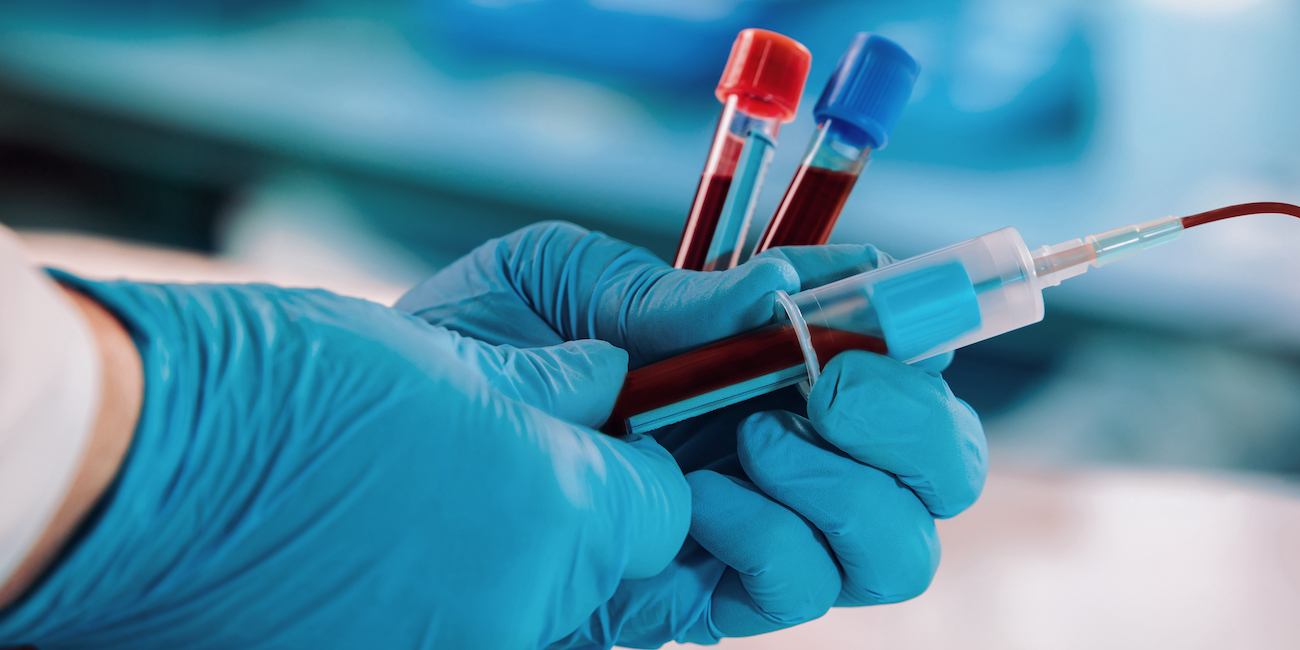
Waste? It makes our blood boil!
FEATURE – Thanks to lean, a primary care unit in Catalonia has streamlined its blood sampling process, improving the patient experience and the life at work for its staff.
Words: Raquel Tena and Anna Vila
The Catalan Healthcare Service – CatSalut – is carrying out an ambitious and pioneering project to improve patient outcomes across its entire network of primary care units (Centros de Atención Primaria – CAP). You can read about it in this Planet Lean article.
Our CAP in Sant Felíu de Guixols, a town on the famous Costa Brava, is also participating in this endeavor. Our lean project focused on streamlining our blood sampling process, which serves around 75 patients each day, Monday to Friday.
Our first step was to observe the process over the course of one week and painstakingly measure times. This helped us clarify our current state. We were aware that problems existed, but before we embraced Lean Thinking we didn’t fully understand their nature and their impact on our work. Writing things down, taking measurements, and deeply analyzing the situation created a sense of urgency in the team and encouraged us to make the necessary changes to the process.
The main problems we identified were that about 80% of those 75 patients showed up at the same time, early in the morning. They often lined up outside, on the street, well before 8 AM, in the hope of being attended earlier than their scheduled appointment. This, coupled with the fact that the workload was not equally balanced between the service’s six nurses and one nursing assistant, made for a huge bottleneck and a very chaotic working environment.
Our nursing assistant had to welcome each and every patient, collect non-blood samples (like urine or feces), and direct them to the waiting room where they waited to be called in for their blood sample to be taken. Her workload was too high, and she simply didn’t have enough time to do everything. Because of the bottleneck at the entry point, while the nursing assistant struggled to do it all, our nurses often found themselves slowed down in their work and waiting for patients in the exam rooms. We had to find a better way.
From a patient’s perspective, there was a sense of confusion. People came in and didn’t know what to do and where to sit. The nursing assistant couldn’t help them all at once, of course. To make matters worse, patients were coming in from both our entrances. It wasn’t until we did a spaghetti diagram that we realized how intricate the patient journey could be within our primary care unit.
The result of this needlessly complex process was that patients waited at least 30 minutes to have their blood sample taken – much longer for those who had showed up before opening time to line outside.
HOW WE CHANGED THE WORK
Our observation and the Value Stream Map we drew had highlighted the pain points in the process and the main problems we had to tackle. It was clear we had to balance the workload of our staff and simplify the patient journey within the CAP and make our own work manageable. Here’s what we did.
We reorganized the space and redistributed staff, dividing the waiting room into four areas corresponding to the three time blocks (of 15 patients each) we began to use in our scheduling, plus the block dedicated to urgent blood work. We also started insisting that they showed up at that time rather than early in the morning.
Additionally, we put up a notice on one of the two entrances to the unit to communicate to blood-sample patients that they had to come in from one entrance. This brought consistency to the patient pathway and made it easier for people to navigate the space and the process.
The other big change we made addressed the workload problem. The role of the nursing assistant is now to manage the flow of patients, ensuring the room and work is organized and the situation under control. Now it is up to nurses in the exam room to collect non-blood samples when the patient comes into the exam room for the blood sample collection. One immediate sign that this has dramatically improved the work is that now the area is incredibly quiet, whereas before, from within the exam rooms, nurses could hear a lot of noise from people moving around and asking questions. Sometimes, it feels like there is no one outside!
WHAT WE ACCOMPLISHED
The line of people waiting outside when the service opens at 8 AM is gone. Now, we only have 25-30% of our daily patients showing up at their time – those who have an appointment between 8:00 and 8:15. On average, once inside, they wait 10 to 15 minutes, instead of the 30 minutes they did before (and with their privacy safeguarded, since we no longer call their names out in a room full of people). The patient experience has improved significantly.
Now that we removed the bottleneck, we no longer finish the blood sample service late. These days, by 9:30, we are always done with the blood samples and nurses can move on their other duties. In fact, most days, the waiting room is empty by 8:30 and people simply drop in at the allotted time for their blood sampling. Amazingly, what we previously struggled to do with six nurses can now be done in less time by five. What’s also important is that the workload of the nursing assistant has been reduced and that she is now under less pressure.
We have also seen benefits in the handling of urgent blood samples, which we can now schedule more of in the early morning time slot. As we study the new process, however, we realize that this means the 8:00-8:15 slot is still the busiest of the day and that perhaps we could think about moving urgent blood sampling to a quieter time later in the morning. This is the sort of potential improvement we would have never been able to see if we had not initiated our lean journey.
WHAT WE LEARNED
When we proposed the new system, we were met with a “no”. We didn’t know anything about lean at the beginning, and this made people reluctant to take it in their stride. Slowly, however, they saw that this was a better way of working that would benefit everyone and they eventually embraced it. Change is always hard, and the hardest part is probably to get started.
We are all used to seeing problems every day, but often don’t know how to approach them. Lean shed a light on our situation and helped us to make decisions on what actions we needed to take. We are proud of the results we have achieved, which tell us we are clearly on the right track.
Since this system has worked so well here in Sant Felíu, we are going to bring the same model to another primary care unit nearby, the CAP in Platja d’Aro. This is the idea behind this CatSalut project, after all: discovering better ways of working and spreading them across the organization to provide ever better care to Catalans.
THE COACHES COMMENT
By Lalis Fontcuberta
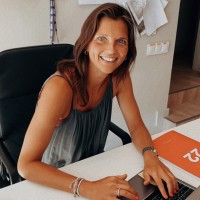
In a very few training sessions with us, the team in Sant Felíu was able to interiorize lean tools and principles, translating complex concepts into something that everyone in the CAP could understand. While the initial focus was on reducing variability, introducing a lean way of thinking in the organization meant they know started to see other opportunities for improvement (for example, the possibility of moving urgent blood work to a quieter time slot). This is a reminder of the power of cultural change.
THE AUTHORS
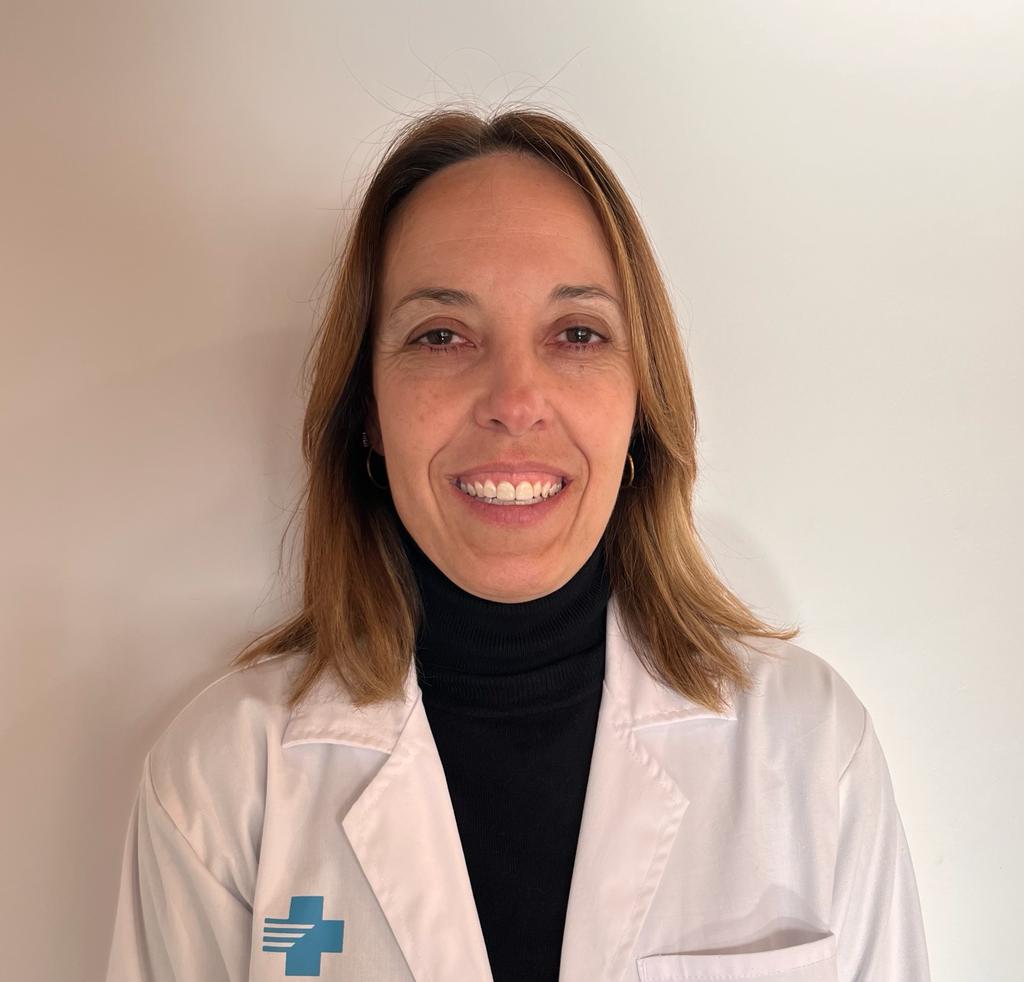

Read more
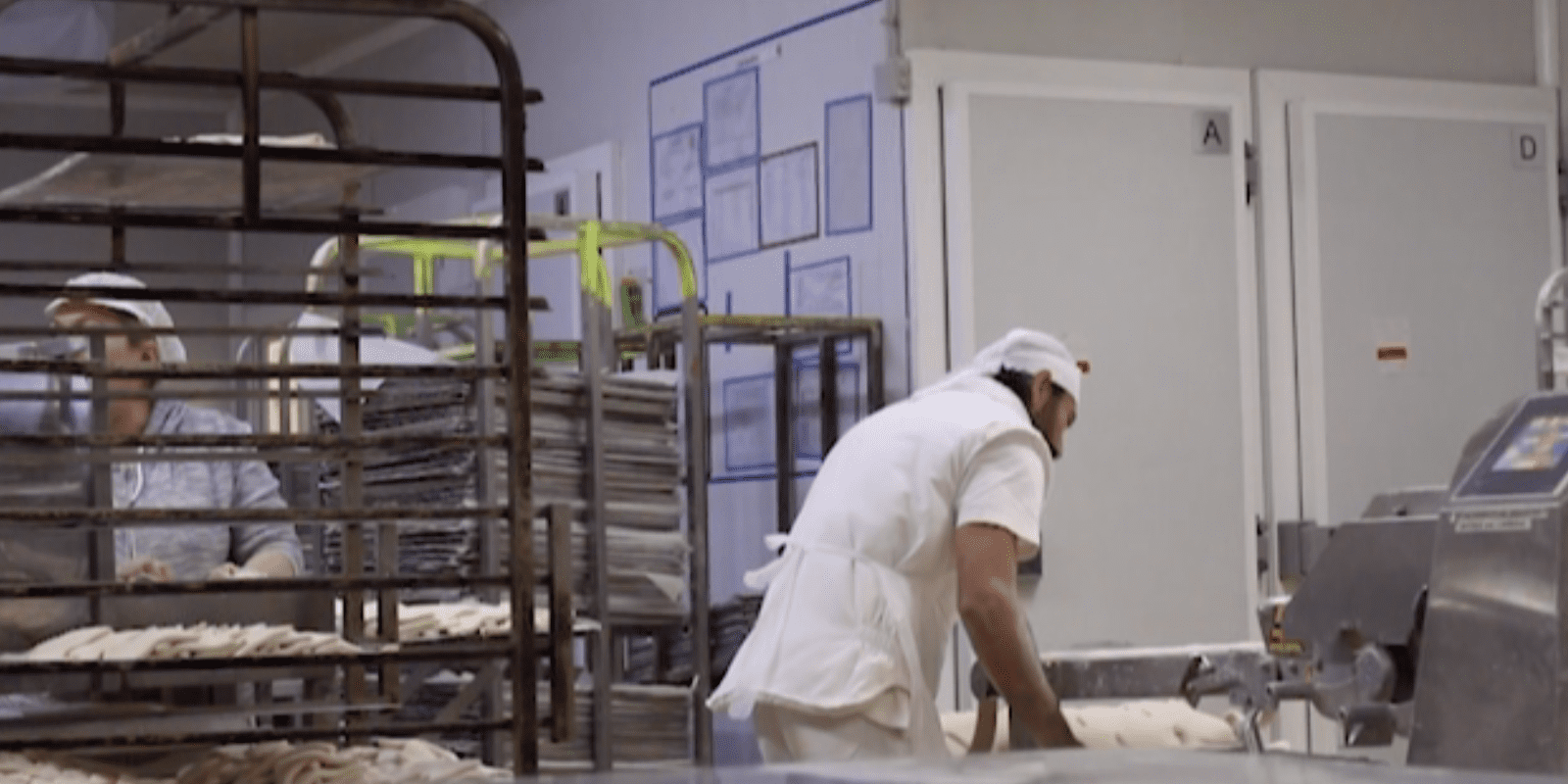
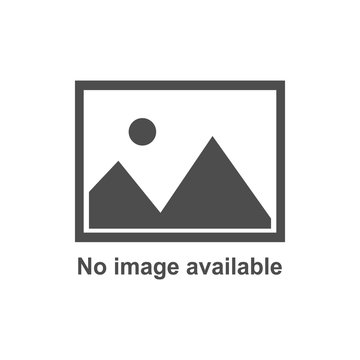
THE LEAN BAKERY – In the fourth episode in our video series, the CEO of 365 explains how lean showed him that his business could grow (exponentially) without using any extra resources.
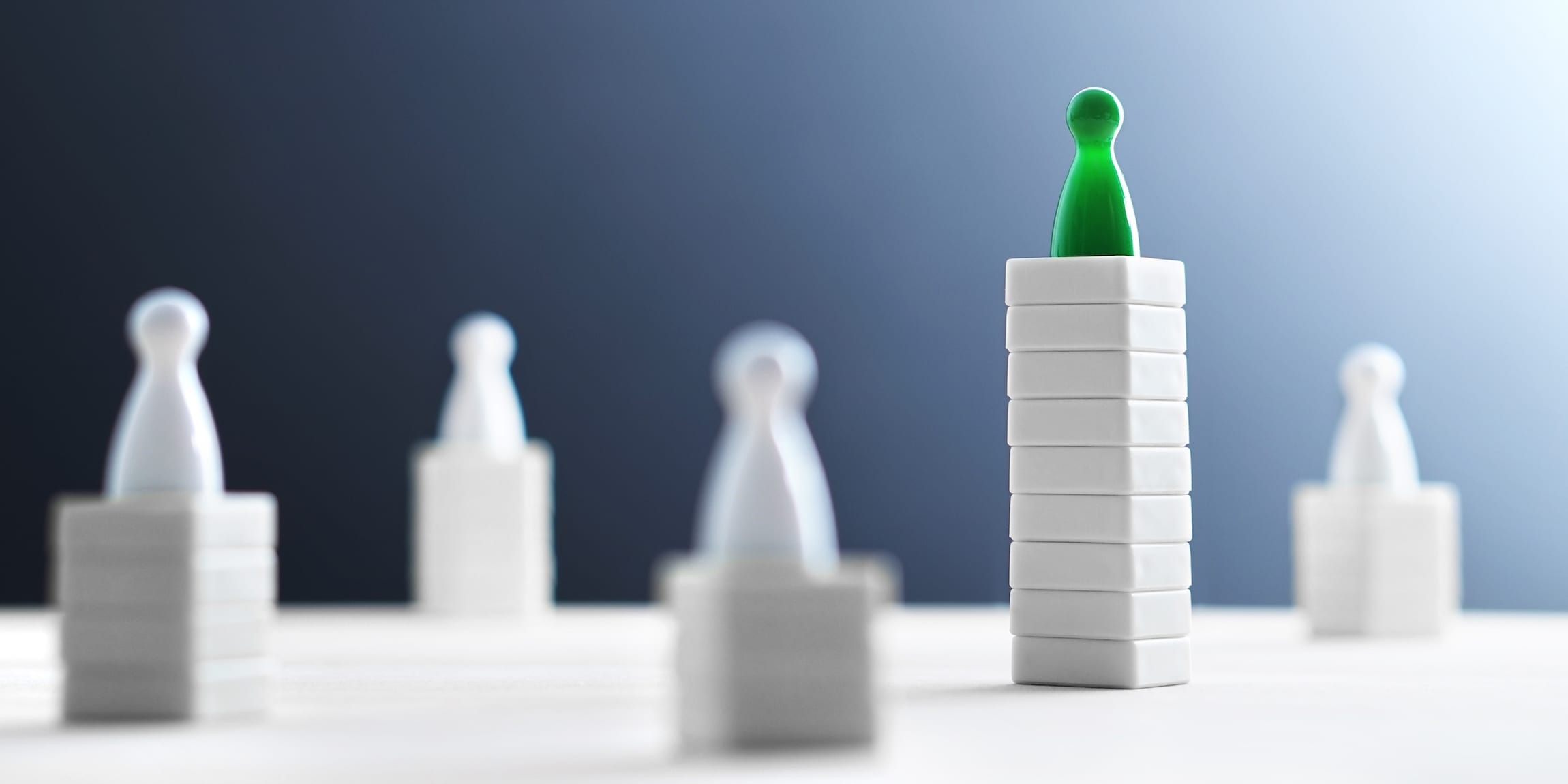
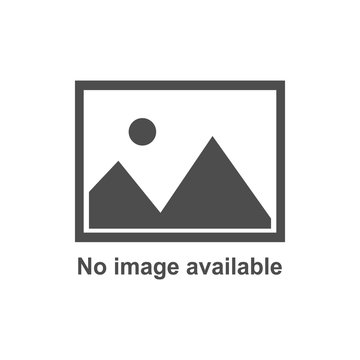
FEATURE – To really embrace lean thinking means to ensure the bureaucratic structures in our organizations enable our people to excel, rather than constrain their creativity.
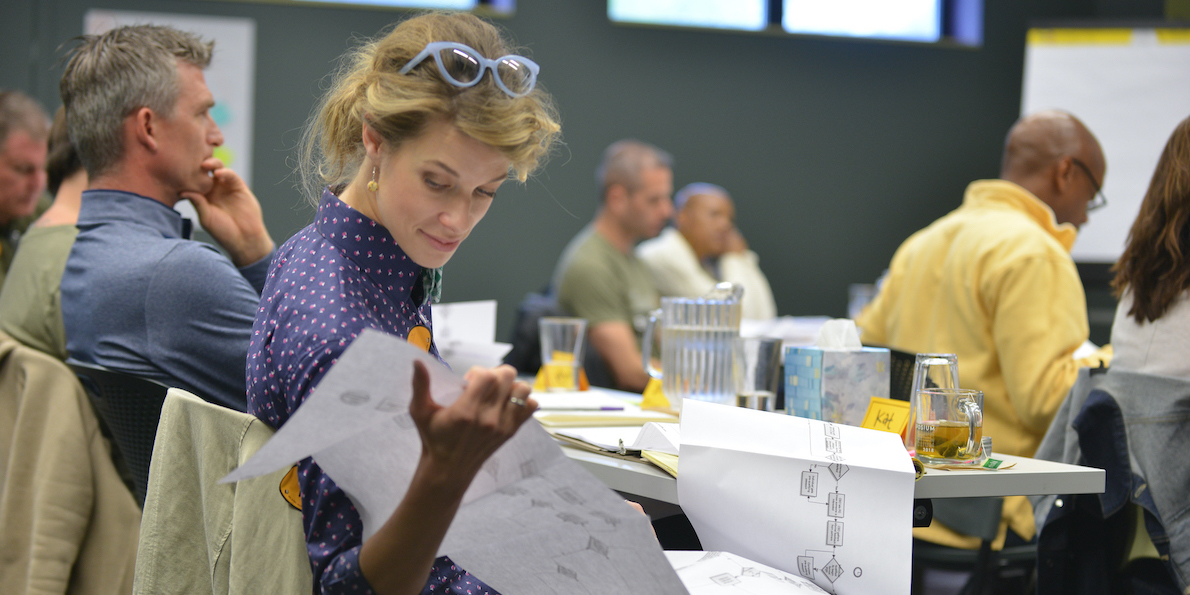
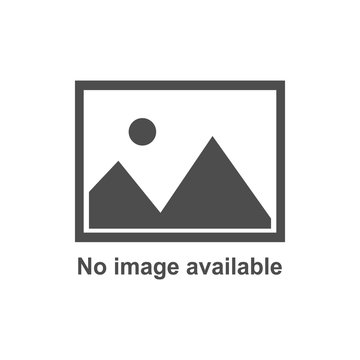
FEATURE – To lean out a training organization means to both transform its internal processes and integrate Lean Thinking in its educational offering: the story of ZingTrain.
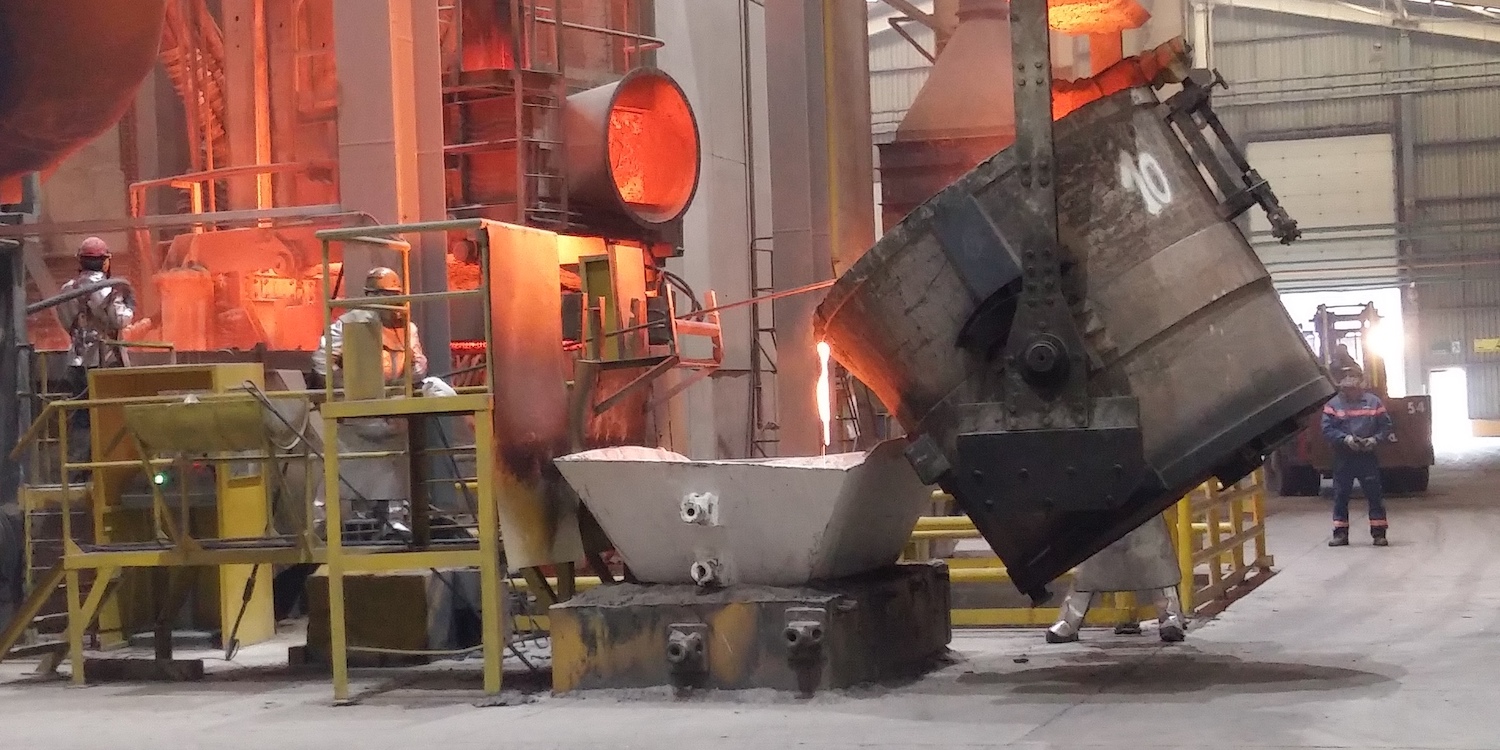
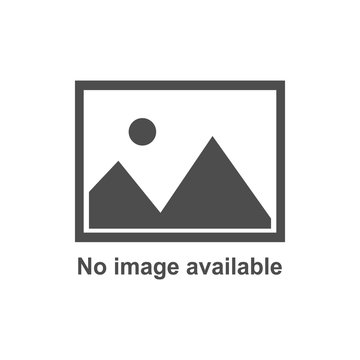
CASE STUDY – This 104-year-old Chilean provider of integral solutions for the mining industry has turned to hoshin kanri to effectively connect everyone’s work with the overall business strategy.