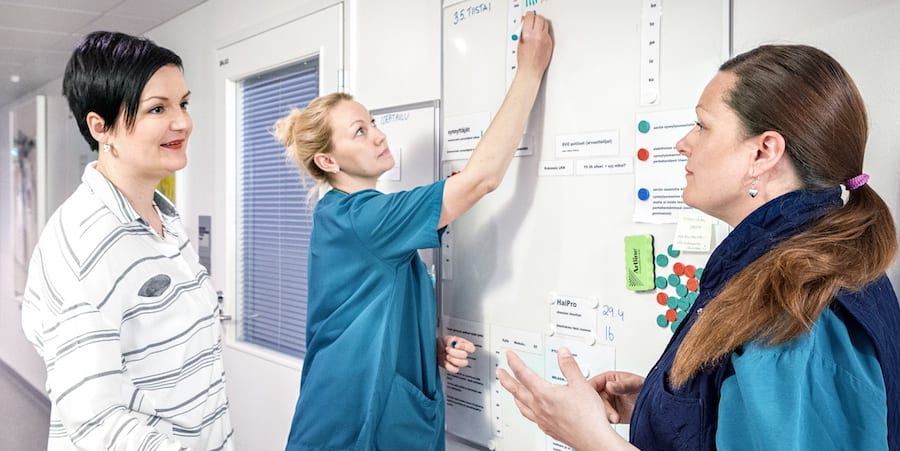
Lean healthcare at a large hospital district in Finland
CASE STUDY – The whole of Helsinki’s hospital district is leaning out, with incredible results. It isn’t every day that we come across – let alone have the opportunity to observe – a lean transformation in such a large healthcare organization.
Words: Markku Mäkijärvi, Chief Medical Officer, and Jyrki Perttunen, Lean Projects Director, Hospital District of Helsinki and Uusimaa
HUS – the Hospital District of Helsinki and Uusimaa – is a group of public healthcare organizations that treat around 500,000 patients every year. Our 22 hospitals provide access to care to 1.6 million people spread across 24 municipalities in and around Finland’s capital city. Part of HUS is also the Helsinki University Central Hospital, which includes 17 facilities in Helsinki, Espoo and Vantaa.
We are a very large organization, with around 23,000 co-workers (of which 3,000 doctors and 12,000 are nurses), and this is perhaps what makes our lean journey so unique: we don’t know of other university hospital settings of our size that are pursuing a real transformation. From a lean standpoint, our size poses great challenges, of course, but we are making progress and in just a few years we have already been able to cover a lot of ground in many of the hospitals that are embracing the methodology.
Our journey began around six years ago. Interestingly, the first experiments didn’t take place in our clinical departments, but in the laboratory and imaging department. The uptake of lean has been gradual at HUS: as pilot projects started to show results, around three years in, the word spread and the clinical side of the organization soon got curious. At the time, there was a lot of public discussion on lean in healthcare and many of us were coming across examples of lean hospitals all around the world (from Virginia Mason to ThedaCare).
The number one challenge we were trying to tackle with lean was, not surprisingly, trying to figure out ways to do more with less and making the most of the resources we had available. As it is the case in most healthcare organizations around the world, our budget was not growing at the same rate as the needs of our patients.
With more divisions beginning to run experiments with lean, we realized we had to organize ourselves better. We therefore made a plan for the lean transformation going forward and presented it to the Board of Trustees in 2013. We were given some resources to get the second phase going.
That’s when we signed a contract with the local university to train lean coaches in 2014 and 2015. We currently have around 100 people in the organization who know enough lean to teach others, but we still need more.
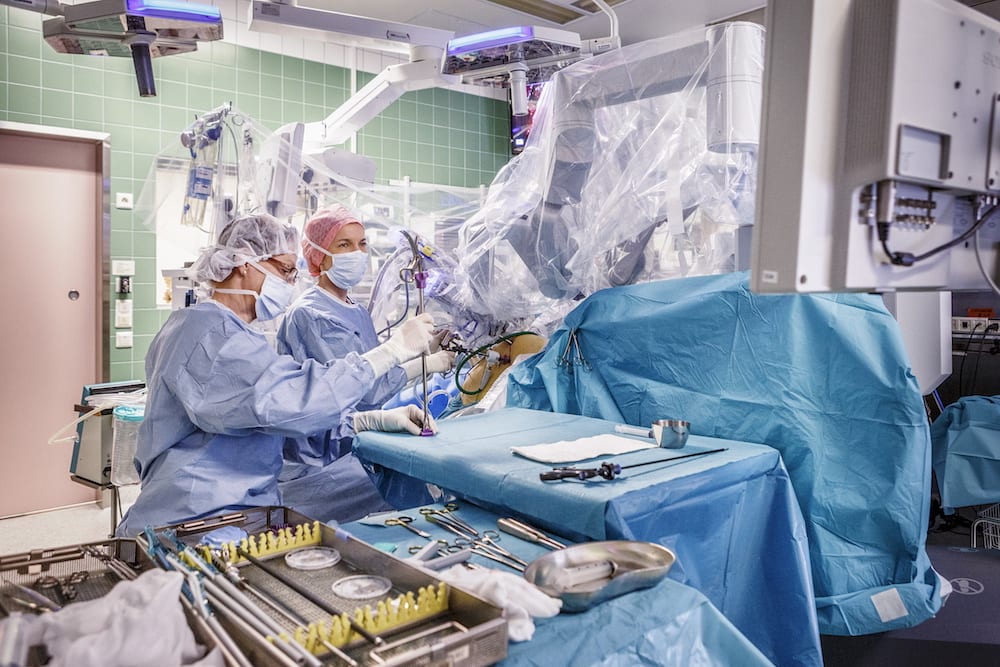
Identifying and developing our lean coaches was a rigorous process, and we are very happy with the people we have. The majority of them are doctors and nurses, with most other functions also represented: we believe that the more cross-functional the pool of coaches is, the better for the organization. When they go back to their units, the coaches initiate projects there – the multi-professional nature of the group greatly helps us to spread the lean culture and practices across HUS. (Of course, this has to be coupled with active support from area management teams.)
Our strategy to develop people doesn’t stop with the coaches, however. We regularly organize wider training for managers – a one-day course that has already been attended by 700 people. We have also started our own Lean Academy, which is our way to execute our plan for development. We believe in a mix of classroom and on-the-job training (with a slightly bigger focus on the latter, the ratio being around 30/70).
Another step forward in our lean journey was made in November 2015, when the Executive Board set the goal for 2016 of introducing daily management in at least half of our units. Even though we are already implementing techniques like A3 thinking and 5S – even hoshin kanri in one department – the main focus at the moment is on building a working lean management system, because we see this as the only way to improve communication across different management levels, a necessary step towards improving the care we offer.
LEAN AT DIFFERENT STAGES
If you look at the different specialties and functions within HUS, you will see that some are proceeding very fast down the lean path, while others are a bit slower. This is completely normal, and we are working hard to spread knowledge and best practice to help the areas that are already doing well to do better and those that are struggling to catch up.
Among the “success stories” we have our internationally renowned Comprehensive Cancer Center, for example, but also our Anesthesiology Department, our Children’s Hospital and our Women’s Hospital. The reasons behind the success or struggle of each of the organizations making up HUS of course vary hugely: for instance, the Cancer Center already had a solid quality system in place and the standard work is now clearly defined, while at the Children’s Hospital there is a major focus on becoming the best children’s hospital in the world. What we see, however, is that wherever leadership is supportive and progressive, things seem to proceed faster.
It is leadership that makes the difference. Where things are going well, they have set very clear improvement targets, explaining what the organization needs and translating those goals into actions individual roles can perform. That’s the power of a lean management system: a clear commitment to improving communication across organizational levels, which results in a better working environment and a faster transformation.
In several departments, leadership has created “lean taskforce groups” that are asked to follow the progress of lean projects on a regular basis. Despite the commitment showed by many top leaders to support the work of these groups, we would like to see them more present at the gemba – whenever a senior leader takes part in a morning huddle or in any other lean activity, we receive a lot of positive feedback. As management starts to go to the gemba more, our transformation will receive a further boost.
We are still trying to figure out how to track progress and assess the level of lean adoption in different parts of the organization. The lean taskforce groups measure the outcome of different projects, but we are still working on a wider, all-encompassing plan to gauge where we are on the journey.
This will prove very helpful, as different divisions and departments across HUS are at very different stages in the journey: in some, the focus is still on localized lean projects, while others are already well on their way towards a lean transformation. To ensure good ideas and best practices spread across the hospitals system, we have the lean coaches participate in a quarterly meeting in the Lean Academy to share what they have learned, and we also ask them to regularly attend huddles in other units to see what’s new out there.
It is good to see our hospitals progress at a steady rate (albeit at different levels) and we find it incredibly rewarding to watch lean blossom into a culture at HUS. The change we are experiencing is particularly evident when we look at the ever-increasing levels of cross-functional collaboration: doctors, nurses and support staff are really working together to drive change and improve the care we offer to our patients. The huddles are proof of the fact that the old model – which saw each profession, from doctors to nurses, meet separately – is gradually disappearing.
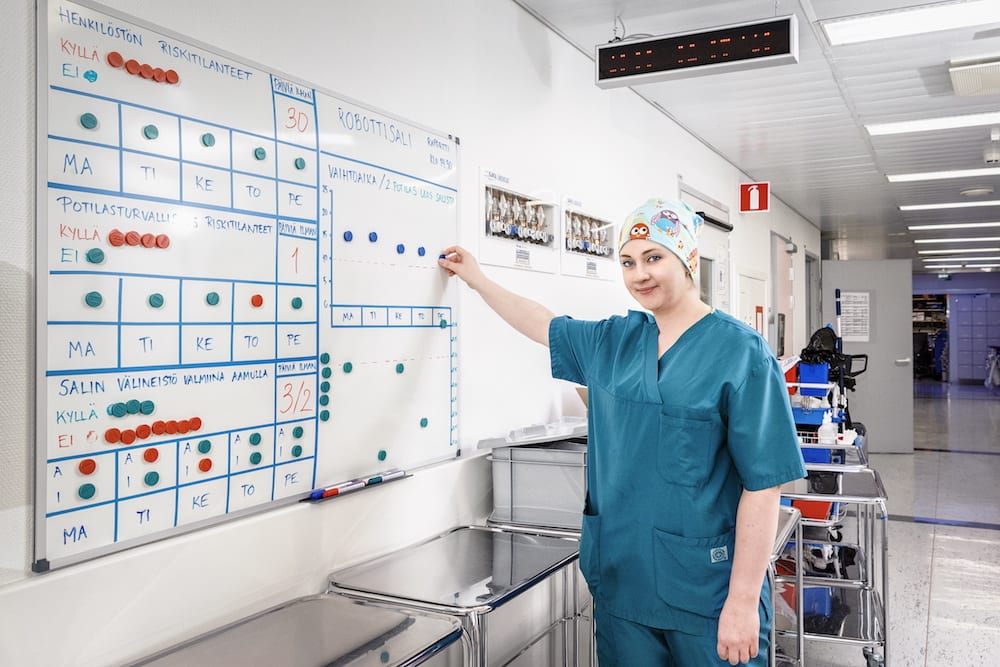
THINGS ARE CHANGING
Every day more good examples of lean improvements pop up somewhere in the organization, and the ever-increasing pace of change can only be a result of a shift in culture.
The most successful improvements have taken place in the hospitals that use daily management, in which work transfers have been reduced by over 40% – a result they have been able to maintain – and nearly all morning delays in the operating rooms have been eliminated. A number of wards have also managed to significantly increase the number of patients who are discharged before 1pm, from 10% to 50%.
Now that our transformation is picking up pace, we are finding that our approach is paying off: while we have borrowed ideas from other lean healthcare organizations, we have always been careful not to simply copy and paste them into our processes. Instead, we have customized ideas and techniques to our own circumstances, to ensure they really helped our people and our patients. There is not one way of doing lean, and every organization has to find theirs. This is hard at first, but there will be more (and more sustainable) benefits to be reaped in the medium to long term.
In our minds, customizing also means driving the transformation internally, because we know that consultants might be able to help you on specific tasks, but that they can’t – and shouldn’t – be those driving your turnaround. Instead of relying on someone external to bring the change to us, we work hard to improve ourselves, with the help of a couple of coaches (like Kim Barnas and Dan Jones).
We know that in an organization the size of HUS, with so many different functions, departments and hospitals, it takes years to fully introduce a lean culture, but we are happy with how things are going and confident that our approach and culture will continue to drive the transformation of HUS forward, building on what we have already achieved. In particular, we are planning to get top management and department heads more involved, as we are aware that the real transformation has to happen in their minds.
For this to happen, we need them to understand lean fully and really start living up to its teachings. We might have a trick up our sleeve that might help us to get there. We Finns are known for being extremely jealous: so, what if we offered top management to participate in training that is so good that every senior leader in HUS will want to take part in it just to make sure they don’t miss out? Or maybe we could just leverage the fact that other hospitals in Finland have started to embrace lean management and that if we want to be top of the industry, we have to go that extra mile. We are committed to see things through, whatever it takes.
THE AUTHORS
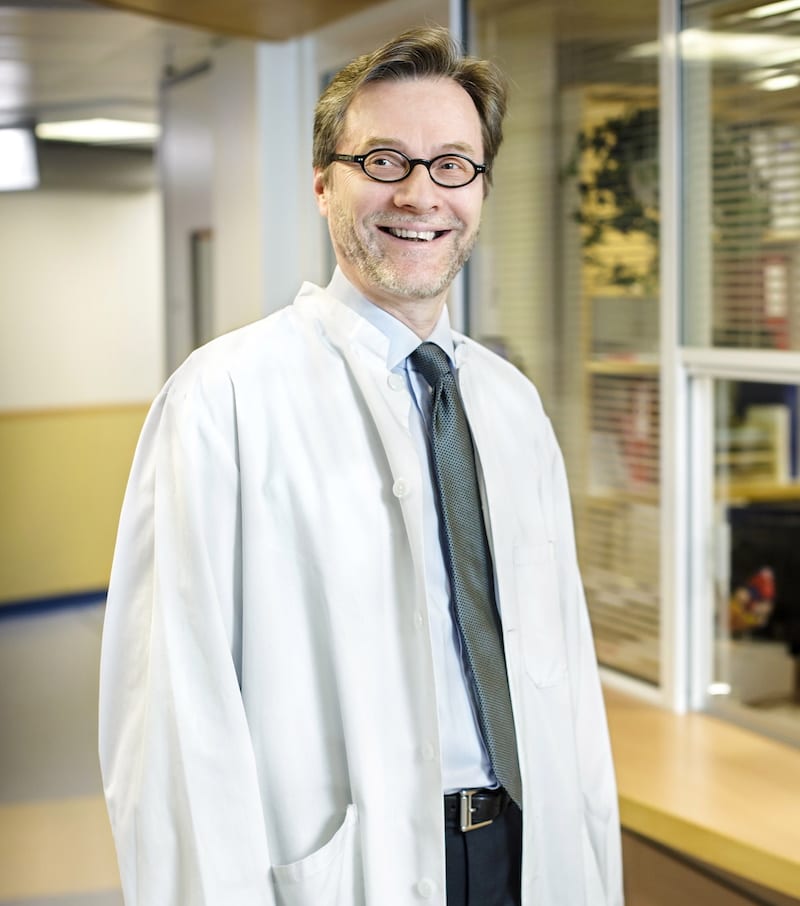

Read more
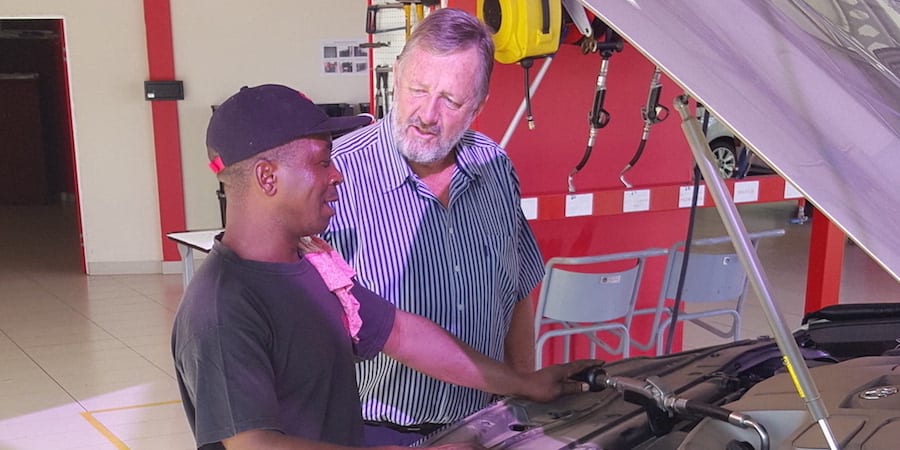
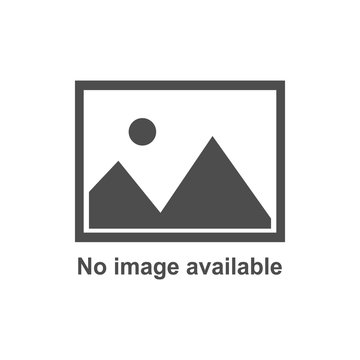
PROFILE - Three decades in Toyota South Africa and an ability to see the value stream as a whole are helping Terry O'Donoghue, COO of Halfway Toyota, to bring lean thinking to a chain of car dealerships.
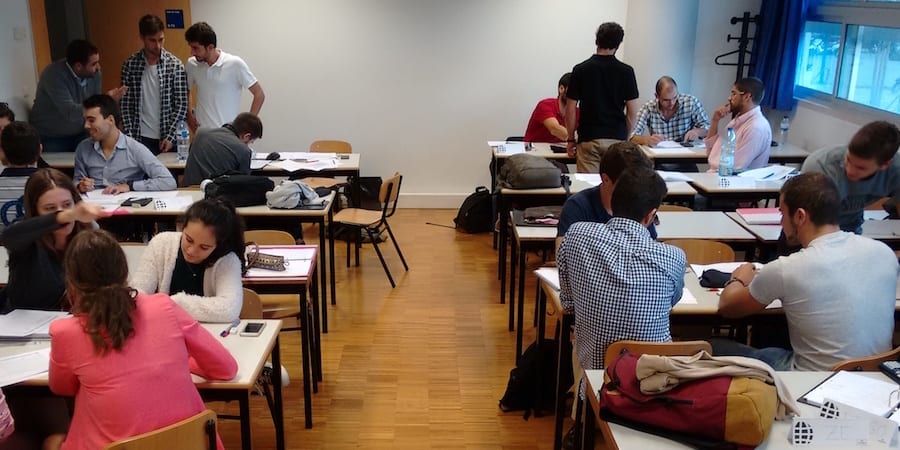
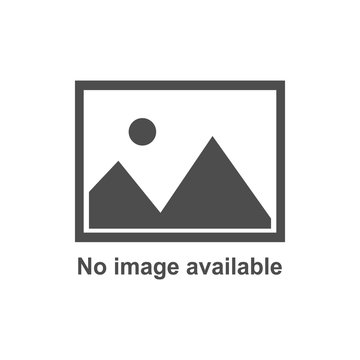
CALL TO ARMS – Despite the spread of lean principles across the world, only a handful of universities have included the methodology in their programs. This article is a call-to-arms telling us why we have an obligation towards future generations.
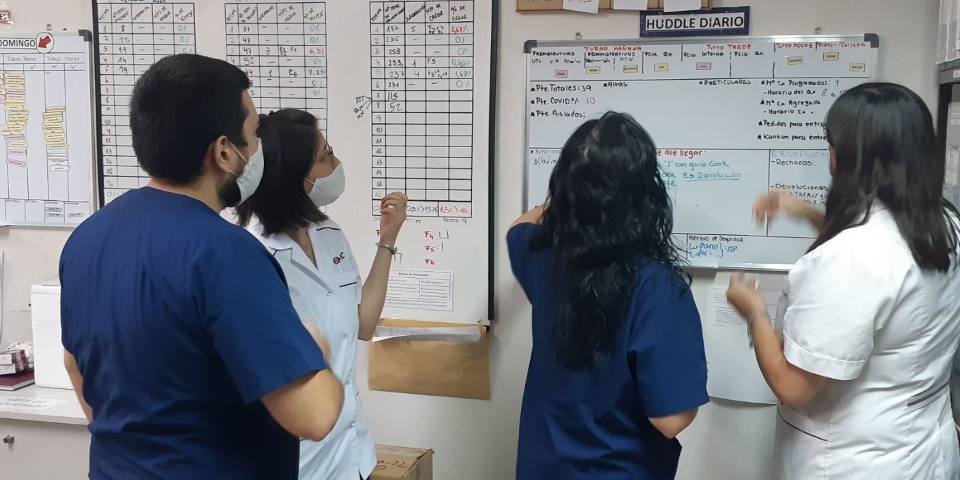
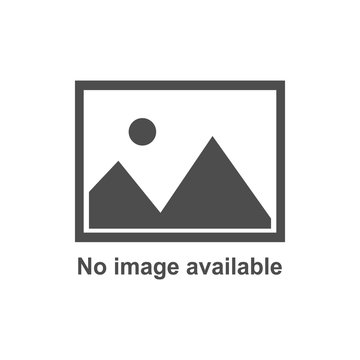
CASE STUDY – This hospital in Argentina has leveraged the power of Lean Thinking to greatly enhance patient care, even in the pandemic, and receive internationally renowned accreditations.
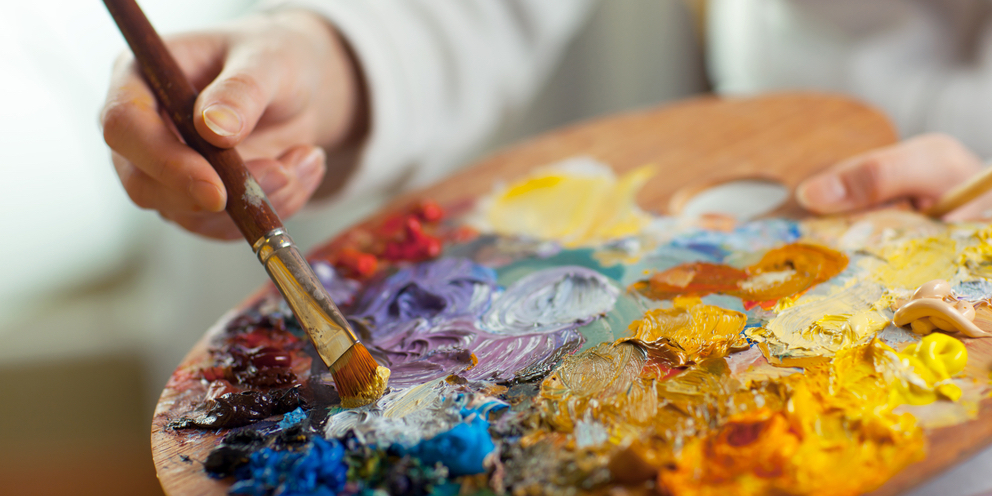
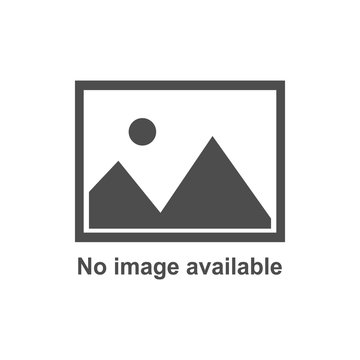
FEATURE – In this personal account, the author explains how Lean Thinking inspires her painting process, debunking the myth that the methodology stifles creativity.