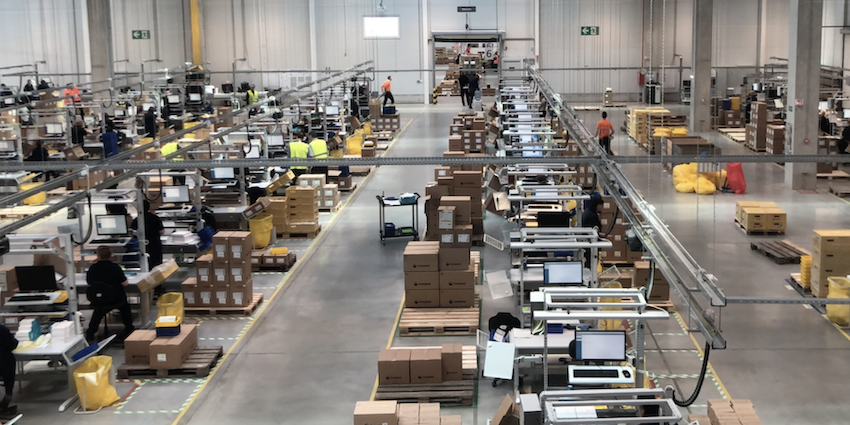
Jishuken at a Coloplast distribution center
VIDEO - In February, a group of Lean Global Network coaches visited Coloplast's Postponement and Distribution Center in Hungary to help the local team improve the internal lead-time across the facility.
Video by: Roberto Priolo, Managing Editor, Planet Lean
The Coloplast Parts Distribution Center (PDC) in Tatabanya, Hungary was experiencing long lead-times in its internal processes. At busy times, orders picked in the warehouse tended to accumulate in the Preparation area, creating a bottleneck that made the work difficult to handle for the workers in Packing area and caused delays.
With the help of an international group of coaches from the Lean Global Network (coming from Hungary, Ukraine, the US, Lithuania, Canada, Brazil and Turkey), the Coloplast team was able to quickly identify a number of issues in the three areas of the PDC and initiate rapid experimentation to try and tackle them. Jishuken is more than just kaizen: it is an activity with a strong focus on learning and capability development.
In this video, you will understand the problems facing the facility, the focus of this Jishuken activity and the impact it had on the way people at the PDC work and think.
Jishuken Lean Global Network team: Csaba Bereczki (Hungary), Csaba Szalay (Hungary), Beáta Bartha (Hungary), Mark Reich (USA), Cevdet Özdogan (Turkey), Hüsrev Yaman (Turkey), Laura Mottola (Canada), Augusto Fonseca (Brazil), Serhii Komberianov (Ukraine), Andriy Dmitriev (Ukraine), Tadas Puksta (Lithuania) and Donatas Kaminskas (Lithuania).
Read more
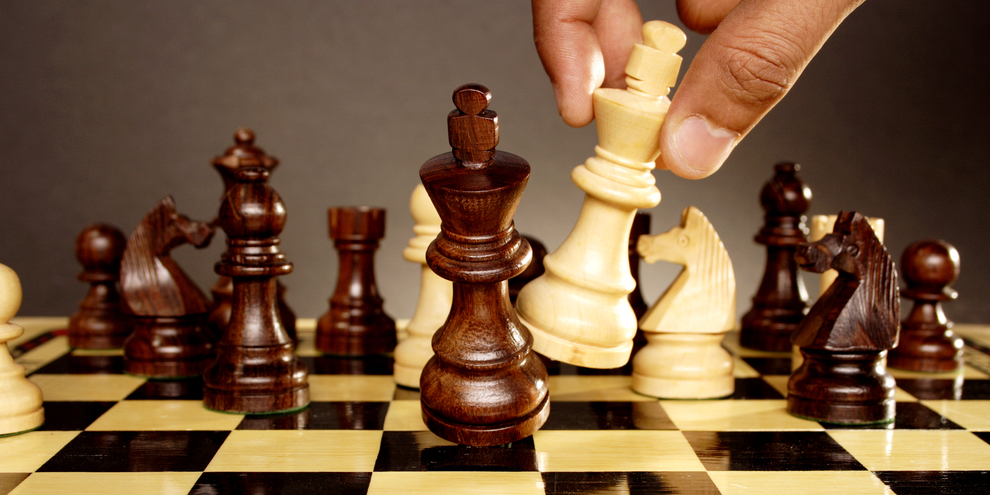
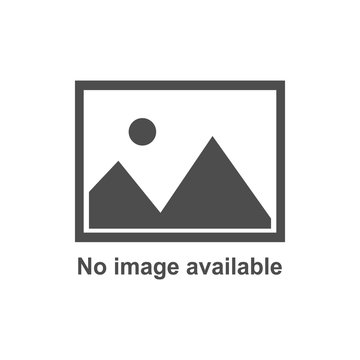
ROUNDUP – In the last roundup on lean tools and concepts of the year, our editor collects and curates the best articles on strategy deployment (hoshin kanri).
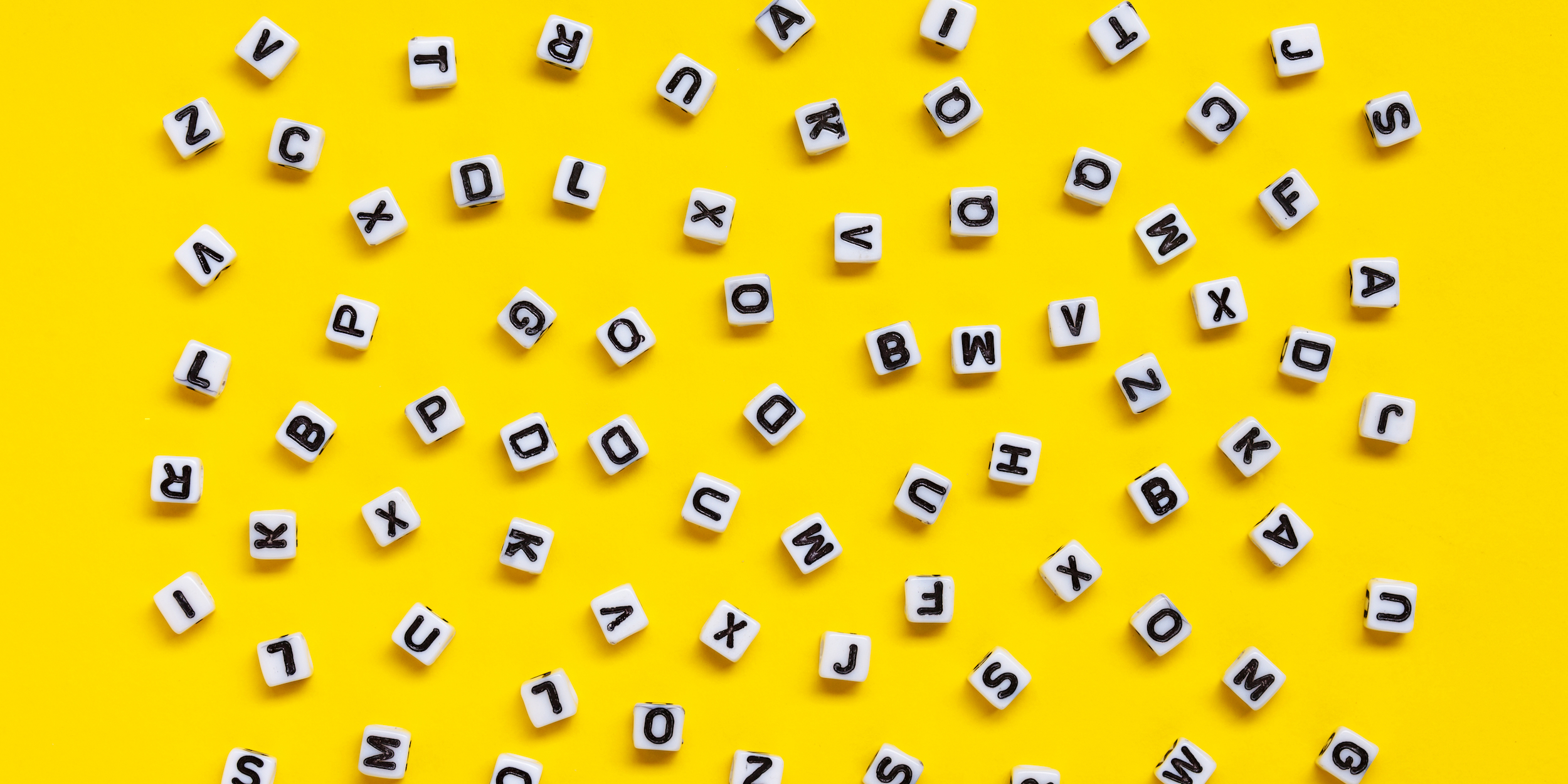
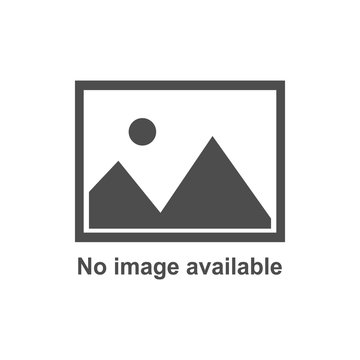
FEATURE – In the lean world, we are used to acronyms and abbreviations. But what’s the value of words if their meaning is lost and fails to reach those we are communicating with?
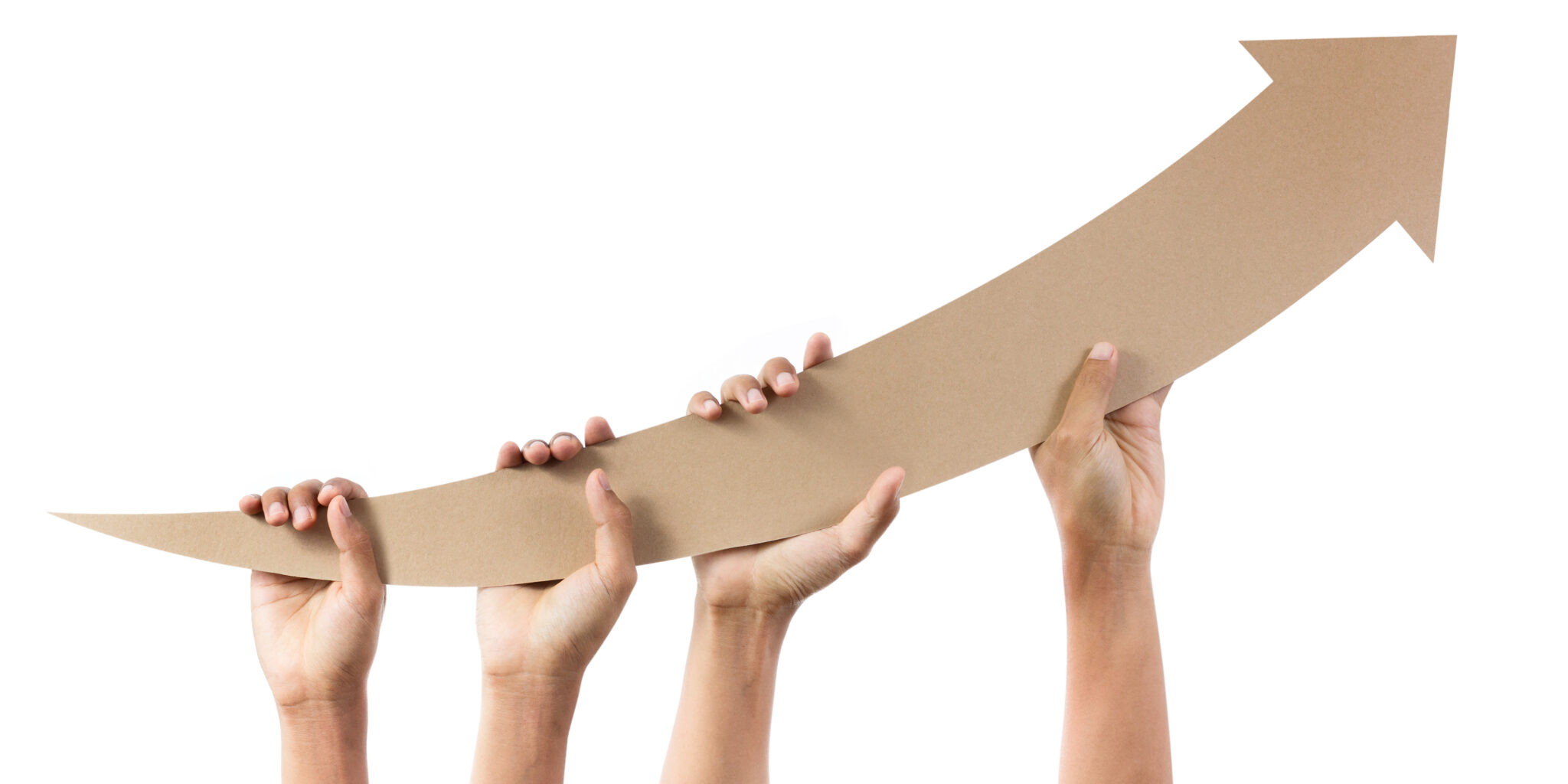
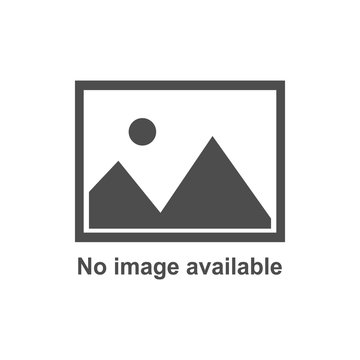
FEATURE – Today we repurpose a great article published in 2016 on Japanese industry magazine Kojo Kanri that focuses on radical quality improvement at Toyota Industries Corporation.
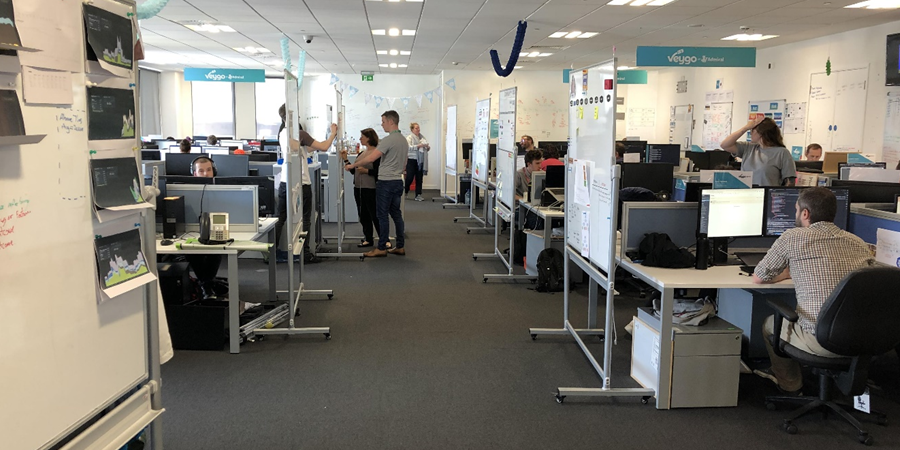
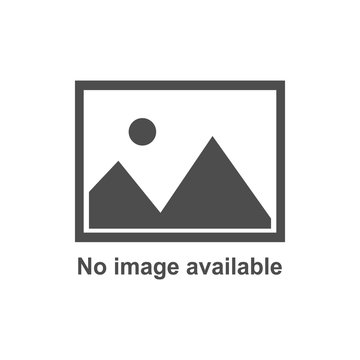
NOTES FROM THE (VIRTUAL) GEMBA – This week, the author chats with an innovative insurance company as it relies on its lean learnings to ensure business continuity and switch to remote working during the Covid-19 crisis.