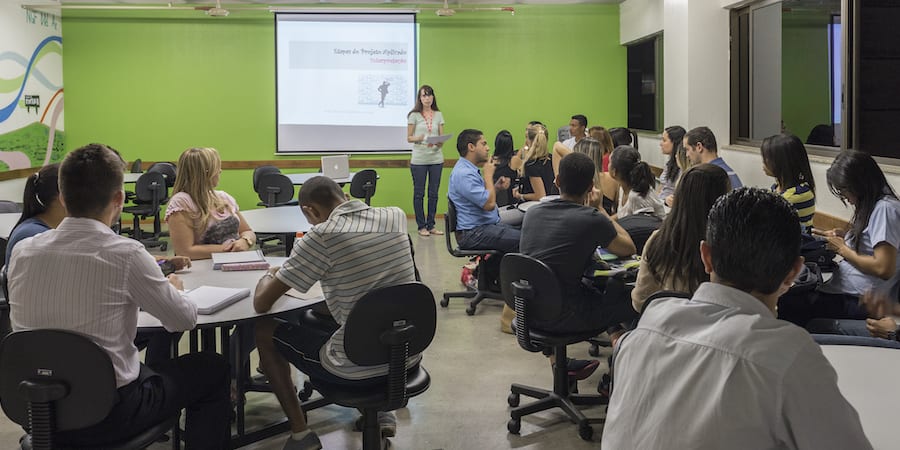
A pioneer in applying lean to the education sector in Brazil
INTERVIEW – Grupo Anima, a Brazilian private education organization with almost 100,000 high-school students enrolled, has revolutionized its culture since introducing lean. But it all started with one project…
Interviewee: Ana Carolina Sarmento, Director of Student Affairs, Anima Educação
Interviewer: Robson Gouveia, Project Manager, Lean Institute Brasil
Robson Gouveia: What is your role at Anima?
Ana Carolina Sarmento: I am Director of Student Affairs, a role that was created specifically to streamline and bring consistency to the provision of student services across different parts of the Grupo Anima.
RG: Anima is a pioneer in implementing lean thinking in education in Brazil. How did its transformation begin?
ACS: One of our directors was introduced to lean at a Shared Service Center meeting. He immediately saw it as a great opportunity for Anima, specifically for the area that at the moment needed improvement most urgently: student affairs. We started in October 2015 with a small project that aimed to eliminate some of the problems students were flagging up. It wasn’t until January 2016 that we started to really study lean thinking and eventually initiate a more comprehensive transformation – we call it STAR – that built on the lessons we had learned during the first project. Initially, I was supposed to be something of a bridge between the 2015 project and STAR, but I ended up remaining involved after the first results appeared. I had become (and still am) so enthusiastic about lean and its transformative potential.
RG: Who championed the first experiments you ran at Anima?
ACS: The interesting thing about how we started is that the project was not top down. It wasn’t initiated by top management. Instead, it was a group of enthusiastic people who set things in motion and, as results started to appear, manage to get more and more people engaged, until they eventually reached most of the organization. Lean has radically changed the culture at Anima, and we are definitely a different organization today.
RG: What are the most important changes that lean has brought about?
ACS: One of the most visible changes has certainly been in leadership behavior. Since embracing lean thinking, our leaders have become very much involved in the many activities we carry out at Anima. They now go to the gemba on a regular basis, and are committed to developing people. The strong support they receive from their leaders has, in turn, helped our employees realize they are capable of improving and transforming themselves and their work. We also see our leaders constantly monitor what’s happening in the organization and collect data.
More importantly, lean has taught us to listen to our students to really understand the process they go through in order to receive the service they require from us. Following the customer journey has revealed how critical it is for us to plan and think through everything we do. It’s also showed us that problems don’t disappear unless you understand and tackle their root cause once and for all. With this in mind, we have started to involve everyone at Anima in the planning process, to broaden their view of the overall process and increase their understanding of how their work impacts the final outcome. This makes them feel more valued.
Another fundamental piece of the puzzle is our daily management system, through which we have been able to get the team to interact and find solutions that we never thought we could get to.
RG: You talked about the changes in leadership. As a director, what would you say the role of leadership is in a lean transformation?
ACS: It's fundamental, there is no doubt about that. At first, people were reluctant to even consider change. They just stared at me, probably wondering what I would suggest next. While some of them bought into lean from the beginning, most had doubts and tended to simply reject the project. It was the fact that, as leaders, we persevered and always showed people we were by their side that made the difference. Leading by examples and actively participating in the work is the only way for leaders to achieve employee buy-in, in my experience. Without people, all you have is tools!
RG: The organization started its lean journey in the administrative area of student affairs. What’s next?
ACS: Our next goal is to build on what we have achieved so far and bring lean to the commercial area. At the same time, we want to continue our work in the student affairs department – it’s important to extend our reach without compromising what’s been achieved so far. Another area we are targeting – a great challenge for us – is the academic one, specifically the evaluation process. Planning has already begun.
RG: Education, in Brazil like in many other countries around the world, needs to change quickly if we are to develop citizens who can think critically. How can lean help with this?
ACS: There's a lot of potential here, and we need to figure out the best way to tap into it. First of all, we should make lean a part of higher-education curricula. The methodology has the power to change the old-fashioned methods we still have in place in our schools and universities, bringing practice to the classroom. It gives us an opportunity to educate students with a different mindset – and that’s an important step to create better-informed citizens that are capable of thinking critically.
RG: What does the future of lean look like, both at Anima and in Brazil in general?
ACS: There are many things at Anima that indicate that we are on the right path. What stands out the most is perhaps the engagement our employees are showing: each time we go on a gemba walk, for instance, we see more and more A3s pop up spontaneously all over the place. Areas we haven’t reached yet have started lean experiments without us, and this can only be a resulted of a culture that has shifted. It’s great to see people buying into lean.
I hope our example can inspire more educational organizations to embrace lean thinking. Nothing would make us prouder, especially because we still don’t know much about lean in education – at least here in Brazil. We are just at the beginning of our journey and we certainly have a long way to go, but I feel we might just be witnessing the beginning of revolution. We are very excited to be a part of it and, perhaps, to even inspire it.
THE INTERVIEWEE
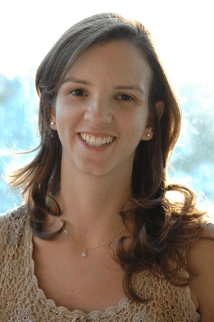
Read more
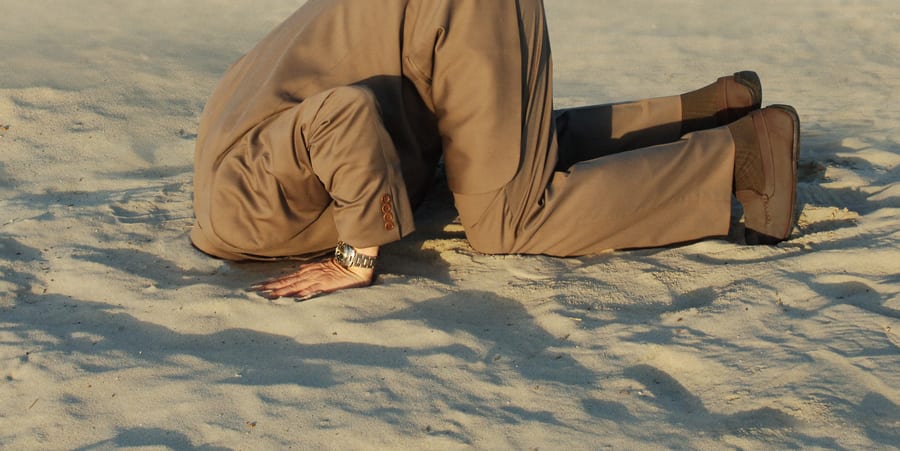
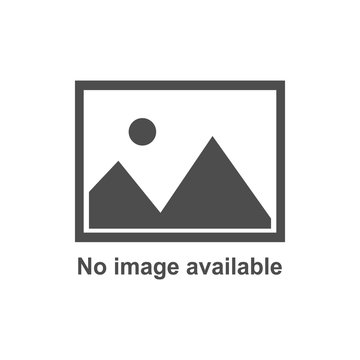
FEATURE – There are five dimensions to a lean transformation – purpose, process, people, management behaviors, and mental models – and it is the role of leadership to adjust its stance to each of them.
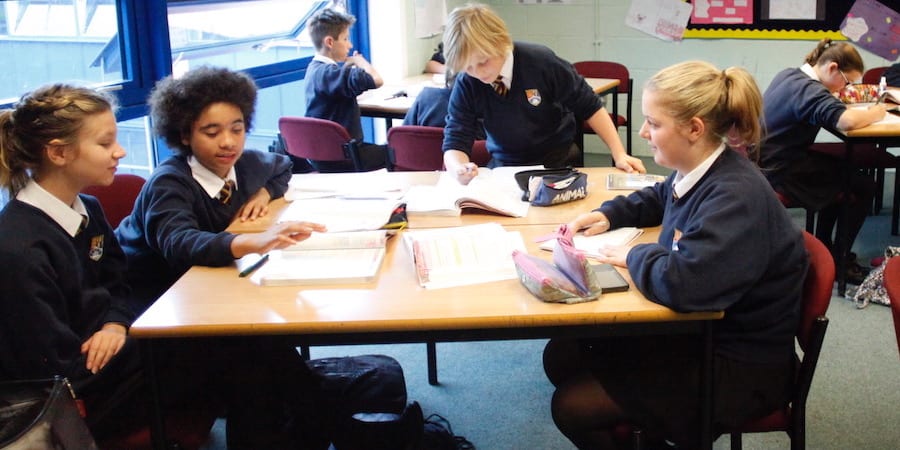
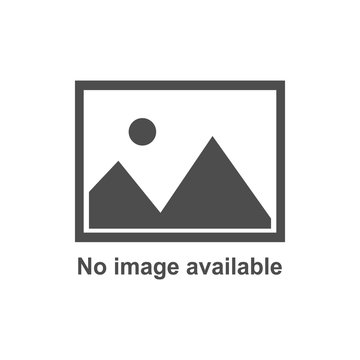
INTERVIEW – Christleton Learning Trust in the UK is running several lean experiments across its three schools. We spoke with its CEO, who told us how coaching is supporting the transformation.
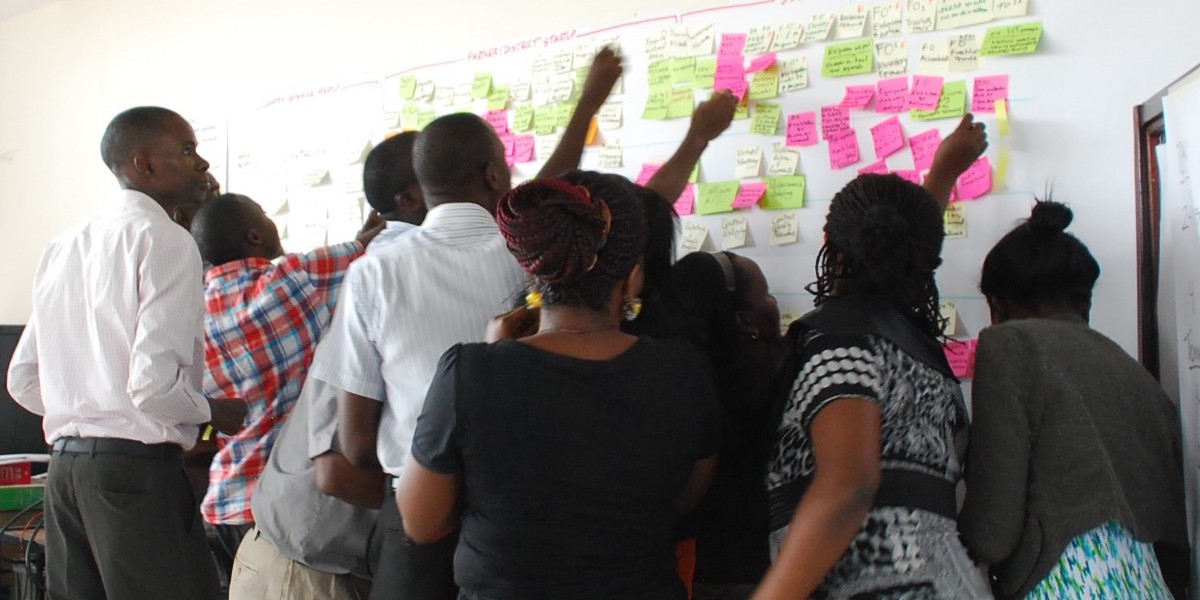
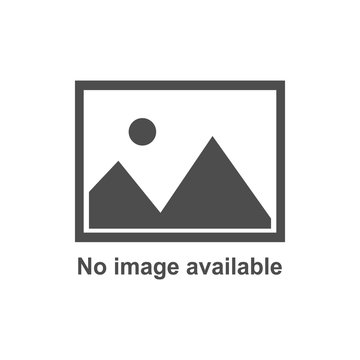
CASE STUDY – The story of this NGO shows how visualizing the work enables improvement and removes barriers among teams. It is a first, fundamental step towards a lean transformation.
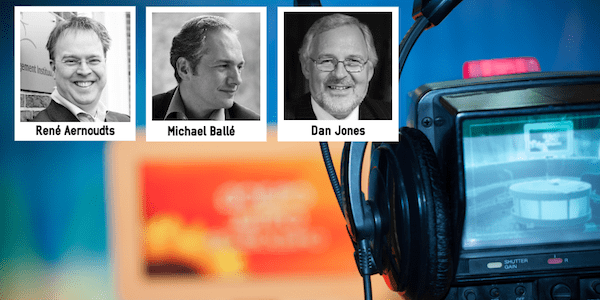
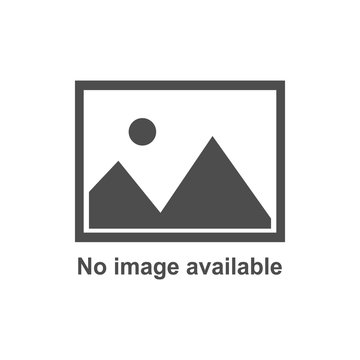
INTERVIEW - In this video interview, René Aernoudts, Michael Ballé and Dan Jones answer a few key questions on what's next for the lean movement.