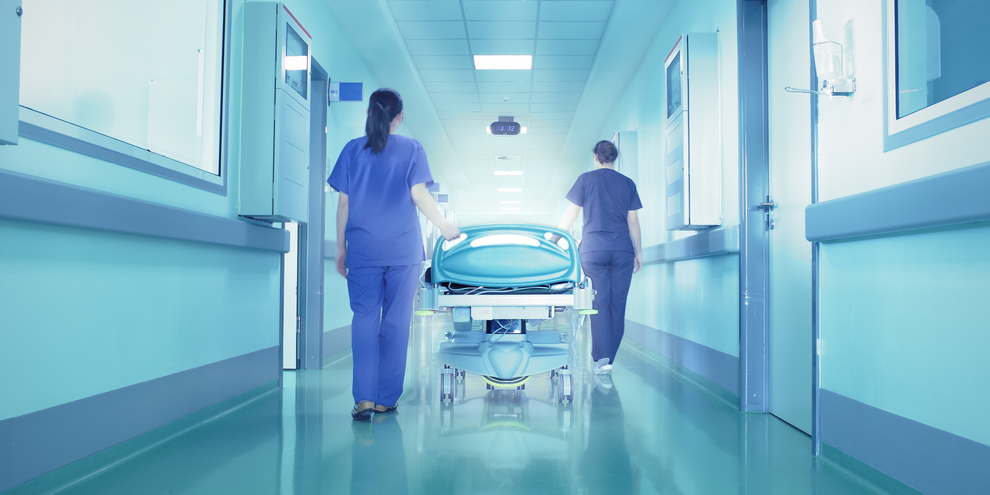
Lean healthcare around the globe
INTERVIEW – With the Lean Global Connection just two weeks away, we learn more about the lean healthcare content available to attendees.
Interviewee: Flávio Battaglia, Director, Lean Institute Brasil and coordinator of the Lean Healthcare Initiative
Planet Lean: What is the Lean Healthcare Initiative and what has its work focused on?
Flávio Battaglia: In 2015, the Lean Global Network create a healthcare initiative, trying to compile our knowledge on lean healthcare and improve the way we supported the industry. We started working together, both remotely and physically, visiting each other’s gemba many times over. We realized that at the current pace transforming the entire healthcare sector would take over a century and started looking for key success factors that could help organizations to speed up and sustain their lean transformations. We studied a number of cases, compared them, and eventually came up with five key elements that we found to be common to all those experiences. With these five guidelines, we believe lean transformations in healthcare can be faster and easier to sustain.
PL: What are the five principles?
FB: The first one – “Don’t wait for the CEO” – relates to the need of not depending on high level leaders to initiate change or keep it moving forward.
The second – “What is your next move, and why?” – is about looking at your next step in the transforming, often addressing a pressing business issue. More generally, the second principle speaks to the need to always have an eye on the future, on what’s the next step in the process? What does the patient need next?
The third principle – “Make it your problem” – encourages areas managers and front-line people to really own the problem they identified and take responsibility for its resolution. Lean is a team sport! Creating a sense of ownership, in other words.
The fourth principle – “The right knowledge for the right people at the right time” – reminds us that blanket training is not a solution to your people-development needs. It’s important we don’t give people so much information that we send them into overload.
The fifth principle – cross-pollination – refers to the all-important idea of yokoten, knowedge sharing, and explains how powerful this can in a lean transformation.
We at LHI have interiorized these principles and are actively using them in our coaching activities. Healthcare organizations are equally enthusiastic about them: every time we have showed them, they have told us they found themselves reflected in them.
PL: What is the contribution of LHI to the upcoming Lean Global Connection?
FB: For our main-stage presentation, we are going to explore each of the five principles in depth. We’ll have our team’s five coaches (myself, Alice Lee, Oriol Cuatrecasas, Denise Bennett, and Vyacheslav Boltrukevich) and five practitioners (Carlos Frederico Pinto, Javier Sala, Olga Farré, David Plunkett, and Kiame Mahaniah), representing six countries. Each principle will be discussed by two practitioners.
We are also organizing a few tracks for the premium stage. We will have Dr Fred discussing the extended value chain for cancer patients with the municipality of Sao Jose dos Campos. A presentation will focus on a national lean program for Brazilian emergency departments, while in another Dr Fred and IHI will share their experience developing a leadership program to reduce infections in the ICUs using TWI. We will also have cases from Argentina, the Netherlands, Turkey, China, and Spain. It’s going to be a great event!
PL: How has being part of the Lean Global Network made you a better lean coach?
FB: What put us together as LGN is our common sense of purpose, both as individuals and institutes. It’s our DNA. Events like LGC help us to get to know each other better. Over the years, we have found it incredibly useful to learn from each other and have grown so much by analyzing our different perspectives. Even though we often have different ways of working, in LGN we are more similar than we think. It’s our sense of purpose that brings us together. The mission to spread lean thinking and practice is in our DNA.
Join us at the Lean Global Connection to enjoy this (and much more) content for FREE. Register here.

THE INTERVIEWEE
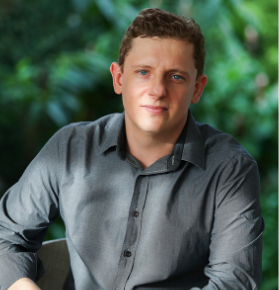
Read more
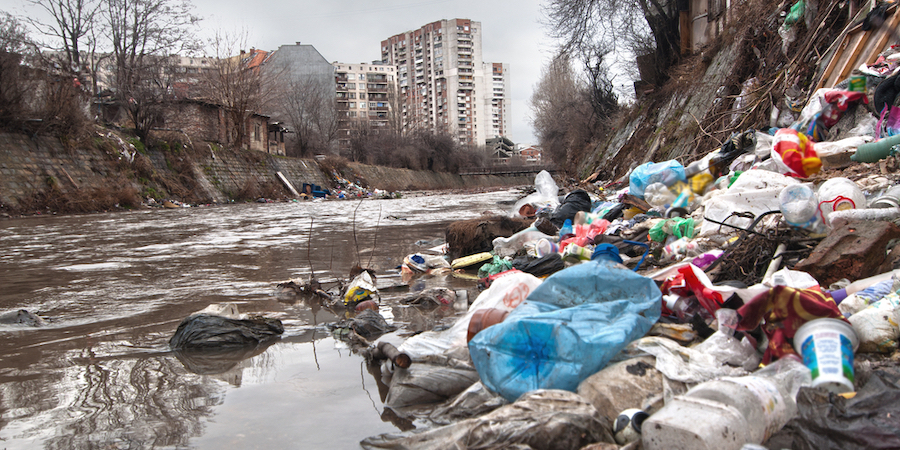
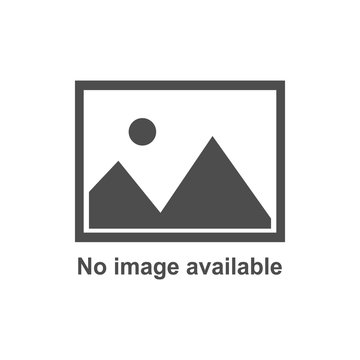
FEATURE – The transformational power of Lean Thinking allows us to see it as a way to solve some of the world’s biggest problems. Dan Jones explains why it can represent an alternative to our exploitation-based system.
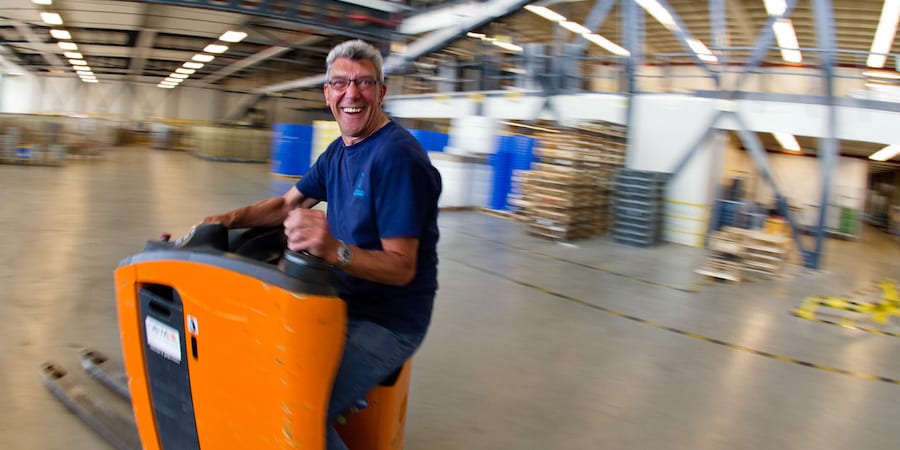
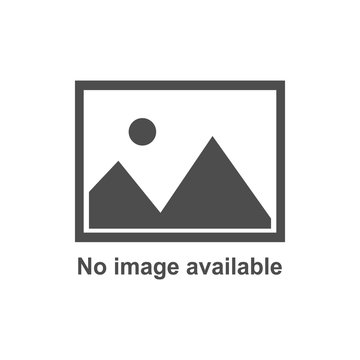
FEATURE – The warehousing department of a Dutch hospital has been implementing lean for a few years. Its Head of Logistics believes in an approach to change based on respect for people and on making small but steady steps.
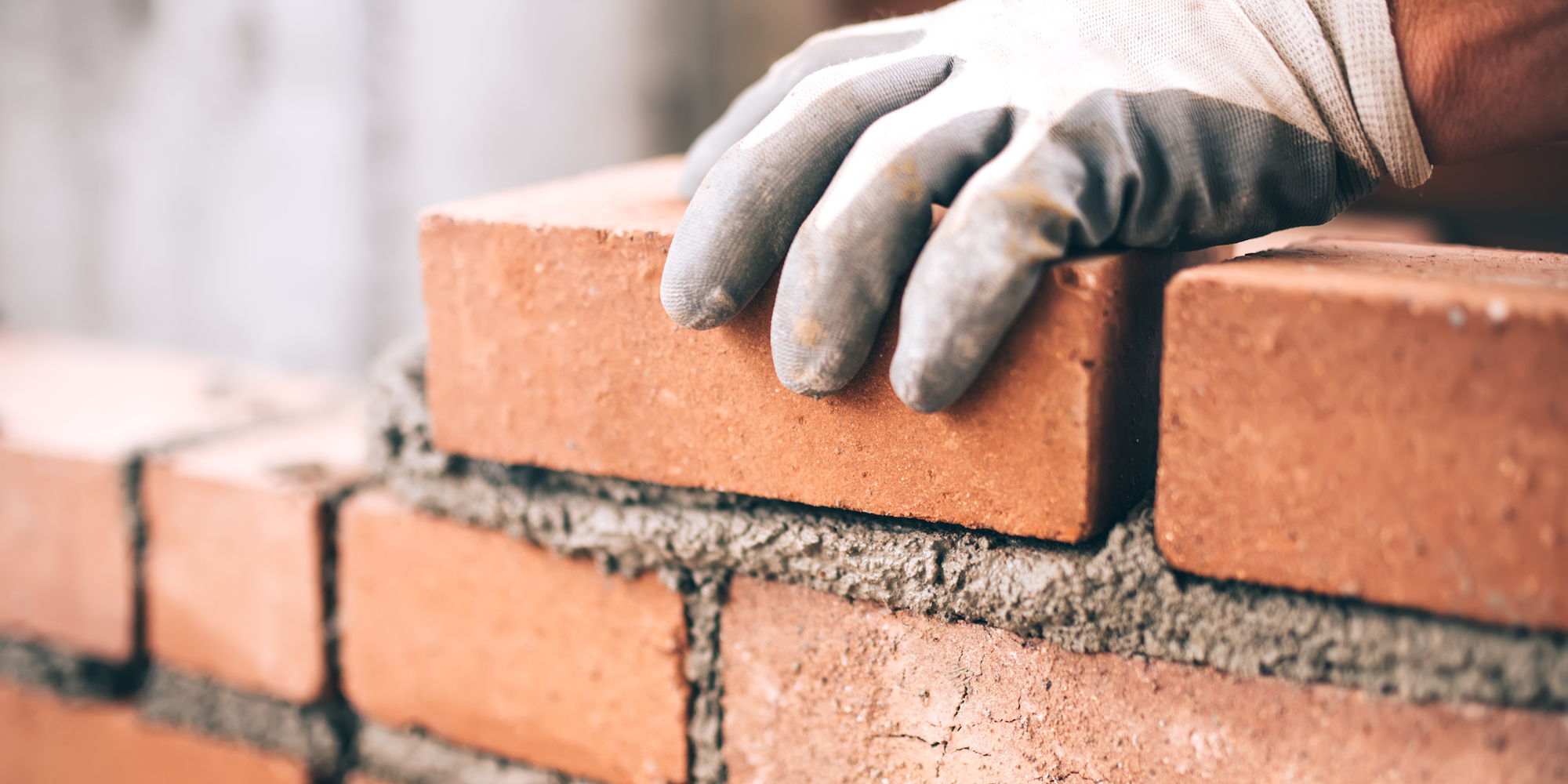
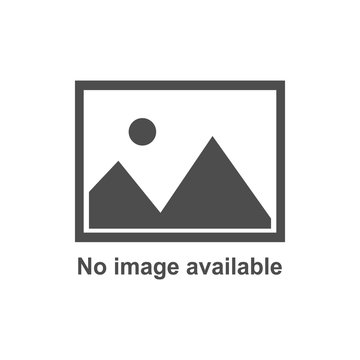
INTERVIEW – The editors of Planet Lean and Lean Post recently met with a senior executive of Turner Construction in New York City. Together, they discussed leadership development, respect for people, and the future of the industry.
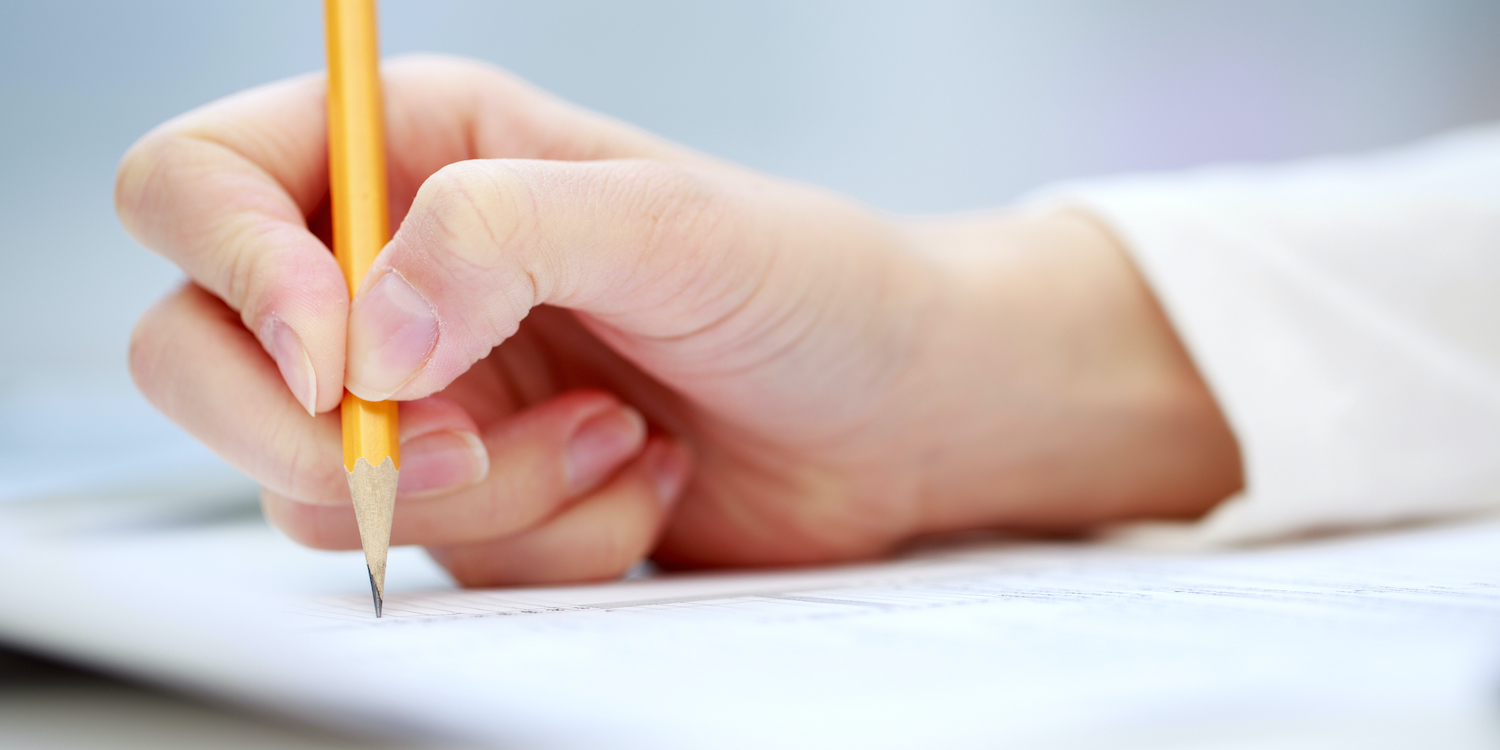
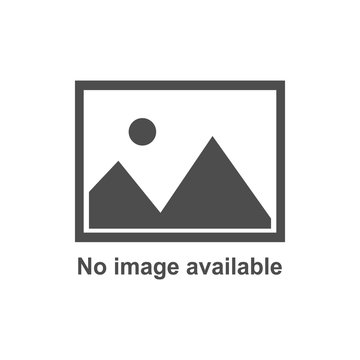
ROUNDUP – Our editor discusses A3 Thinking and its various uses, curating a list of the best Planet Lean articles published on this topic over the years.