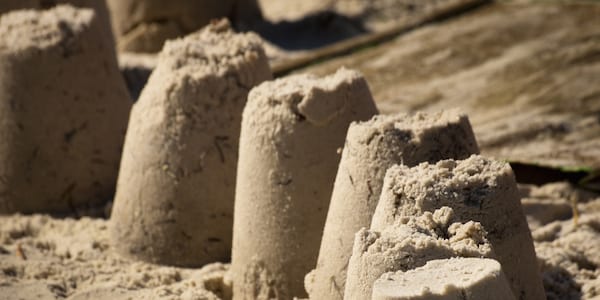
Should you form a central lean team?
FEATURE – In a transformation, should we spread responsibilities across the business or go for a centralized Lean Office? For their second piece, our Polish colleagues look at what they have learned on the field.
Words: Malgorzata Jakubik and Robert Kagan, Lean Enterprise Institute Poland
LEAN IMPLEMENTATION STRUCTURES
- WHO IS GOING TO MAKE LEAN HAPPEN? -
As no true lean person should walk by waste and ignore a chance for improvement, we felt the need to put together our reflections on things big and small that, while working with our customers, we have found to be common “speed bumps” or even show stoppers in a lean implementation. Whether systemic or tool-related, these obstacles have one thing in common: they tell our “war stories,” which we want to share with those on the road to lean, hoping they will warn them against frequent hazards others have struggled with.
Once an organization has realized it seriously needs to change the way it does business and that change will go by the name “lean,” the next big step is to create the structure supporting the continuous improvement transformation process.
We have seen a number of different approaches leaders adopt to go about this, obviously based on their previous experience, beliefs and perception of what is needed in their organization to make lean happen. At this point, leaders have several questions to answer – what are the resources I am going to devote to change? Where shall I find them? What people do I choose to make it work? Where will I find my lean change agents, within my own team or outside?
Sometimes the designed solutions work, sometimes they fail. And when they fail, it is usually because of one of the two misconceptions we illustrate in the examples below, which we have experienced first hand through our work.
Example #1 – No need for central resources, we are all going to do it
The leader of the organization is a passionate student of lean. He has visited lean plants, he has read a lot and discussed lean whenever possible. Now, as his organization is ready to start and he is thinking resources, he believes that the key is to spread the knowledge, the drive and the responsibility across the entire team. He has seen organizations succeed without central lean teams and with responsibility completely delegated to operational units, so he will do the same. Therefore, the plan is communicated, responsibilities are assigned, and the critical problems of the organization are targeted using lean tools.
The outcome? Initially, there is a lot of enthusiasm as tools begin to bring results. Mighty plans on how they will be deployed further and utilized in other parts of the business start popping up. Eventually, however, initiatives get pushed aside as the pressure of running day-to-day business mounts. Where people in units are persistent and passionate enough, processes do develop but they take completely different shapes in different units, best practices are not shared, actions are not coordinated, and the organization breaks up into “islands” – some good, some bad – unable to reap the benefits of team work.
Example #2 – Strong central lean team with a “lean boss”, lean not to “mess up” regular production
In this scenario, the leader understands the magnitude of the change her organization will have to go through. There are many problems and things have to improve quickly. So what does she do? She dedicates specific resources to the lean implementation, creating a large and strong team of full-time people with a charismatic leader. However, she does not want to put too much pressure on the already overburdened operational units, so both the team and the team leader are selected from the support areas.
The result? Again, initially change implementation has a good pace. Plans are well laid out, visualization is superb, and the central lean team is really driving the effort. But in the end, frustration dawns on them as they try very hard but fail to involve people on the shop floor. There are always other priorities, and production has to go on, they are told. There is no time to stop machines, to get people focused on problem solving, or to check whether current work methods can be improved.
Lean becomes the worry of the central team, while the majority of the organization remains exactly where they were, in the vicious cycle of trying to keep the business afloat. Sometimes it gets even worse, and people visibly split in two opposing groups: there is “us,” who run the lines, and there is “them,” with their unreasonable requests to change.
So what is our advice to do this right? The answer has two dimensions.
- The face of the lean transformation has to be the face of the person in charge of the main activity in the organization, be it its general manager, its manufacturing manager or its operations director. Lean needs to mean “our daily business from now on” as opposed to “something we do when daily business is taken care of.”
- Like everything in the real lean world, organizational structures supporting lean implementations need to be dynamic and adaptable to match the current level of lean maturity of the organization. The graph below shows how we see this done best.
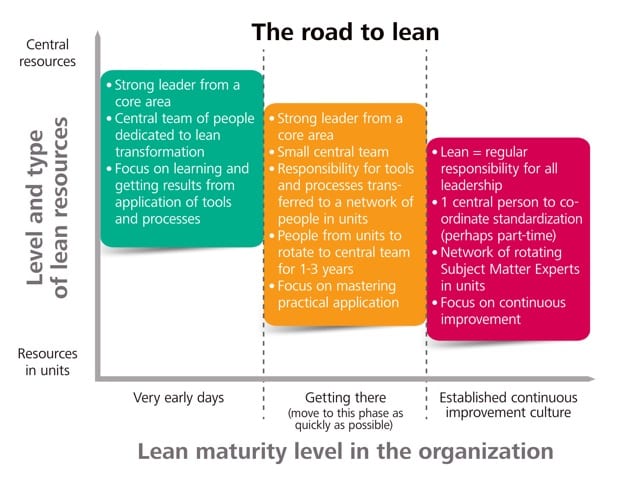
The only answer to the question “Who is going to make lean happen?” is simple: the whole organization. The important thing is to gradually make lean everybody’s responsibility, and to learn to be flexible in how the transformation is organized. If you don’t do this, the question you might soon find yourself having to answer will be: “Who caused our lean transformation to fail?”
THE AUTHORS
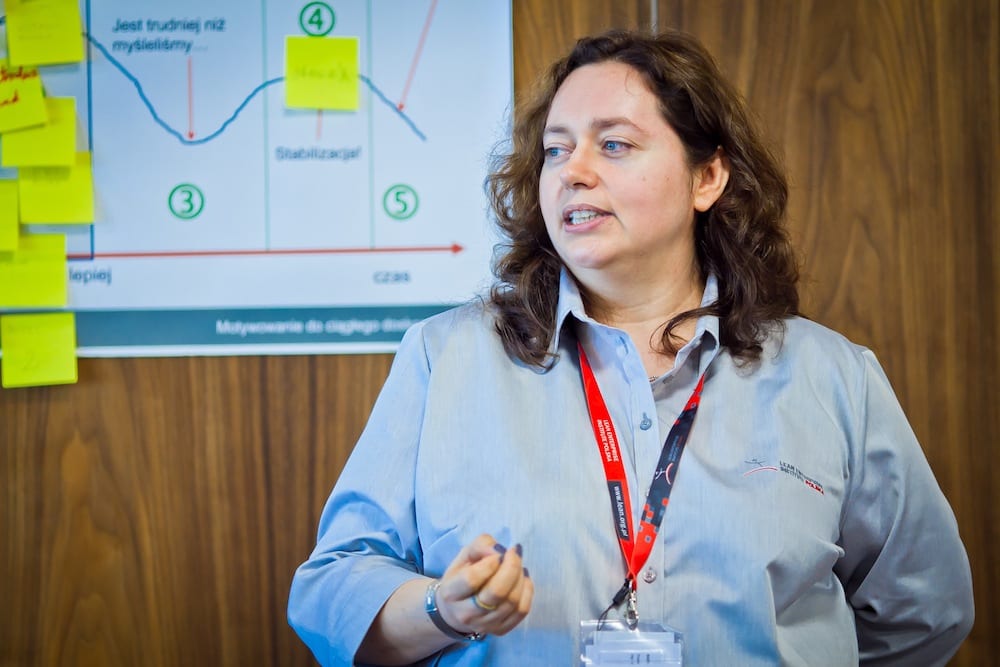
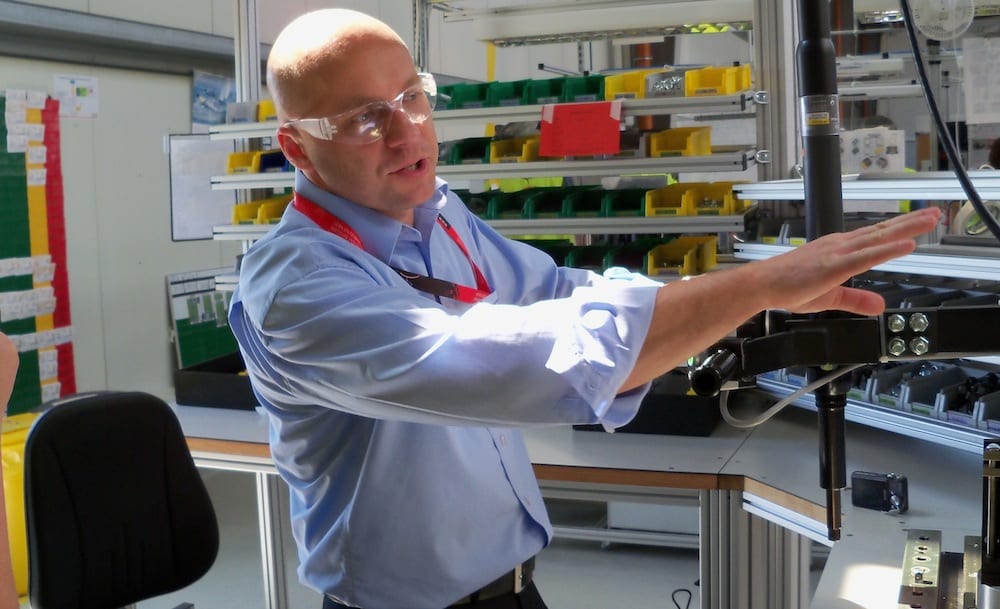
Read more
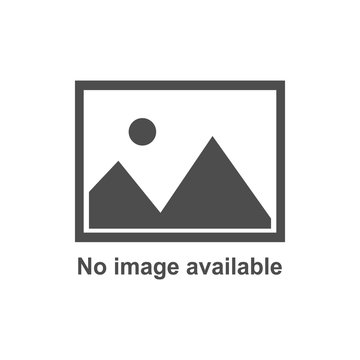
INTERVIEW – The UK Lean Summit 2024 is coming up in April. We speak to Dave Brunt to hear about the event and what we can expect from the presentations.
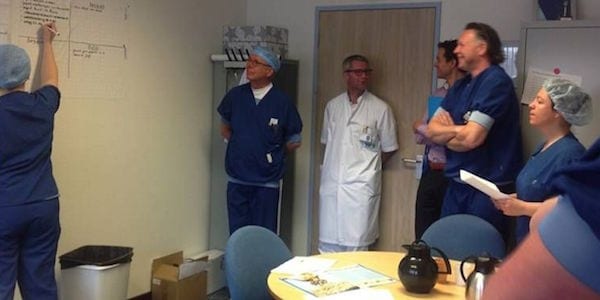
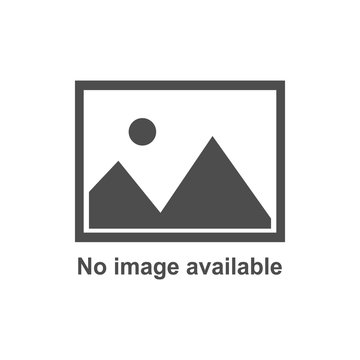
INTERVIEW – PL sits down with a consultant and a manager from the St Elisabeth hospital in the Netherlands to talk about the organization’s “loving care” approach to treating patients.
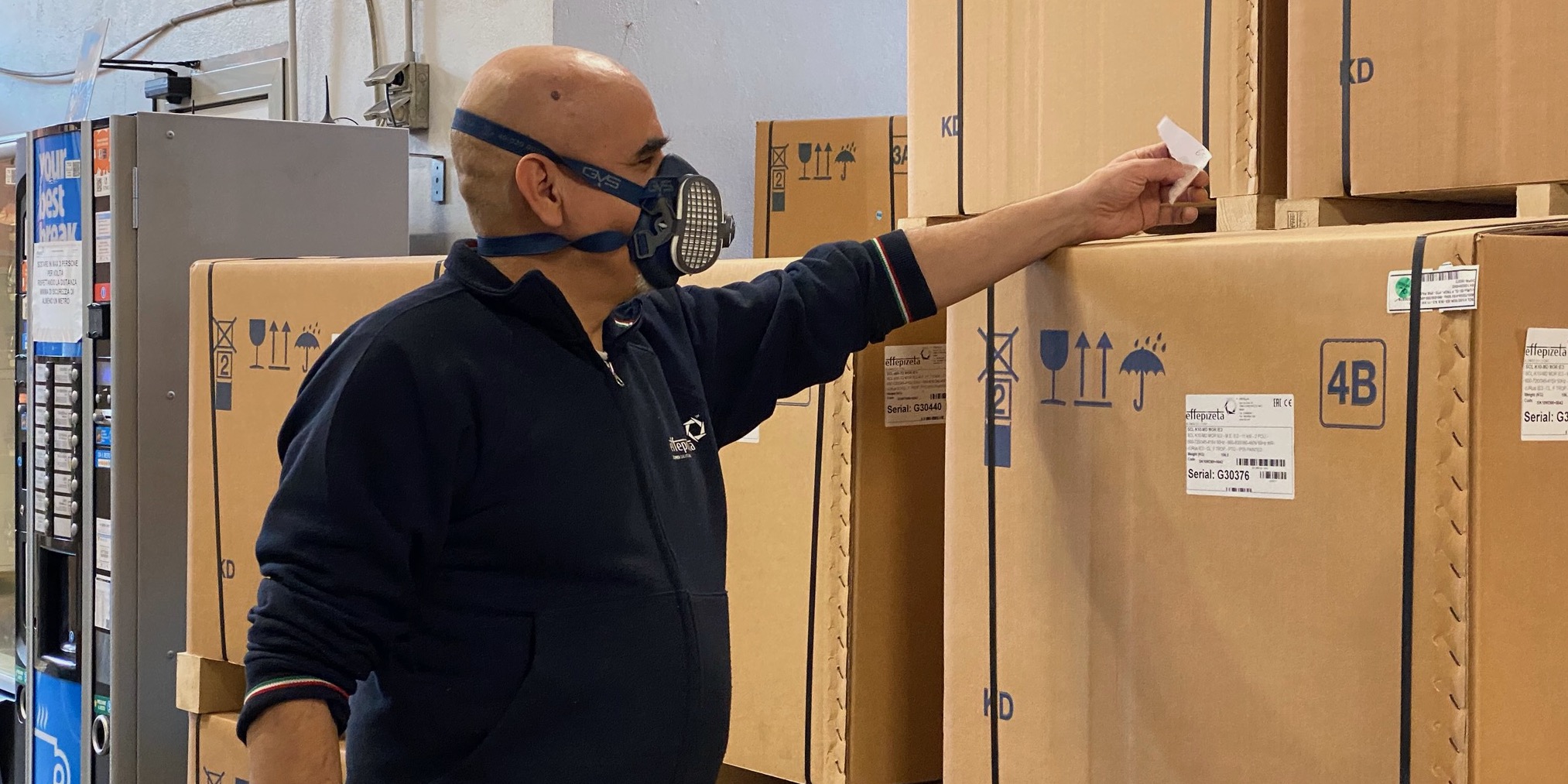
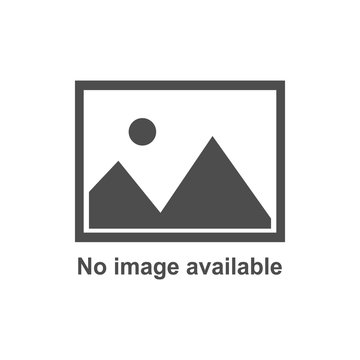
CASE STUDY – This Italian manufacturer has found in lean a way to ensure business continuity and provide support to a distraught workforce in the midst of the coronavirus outbreak.
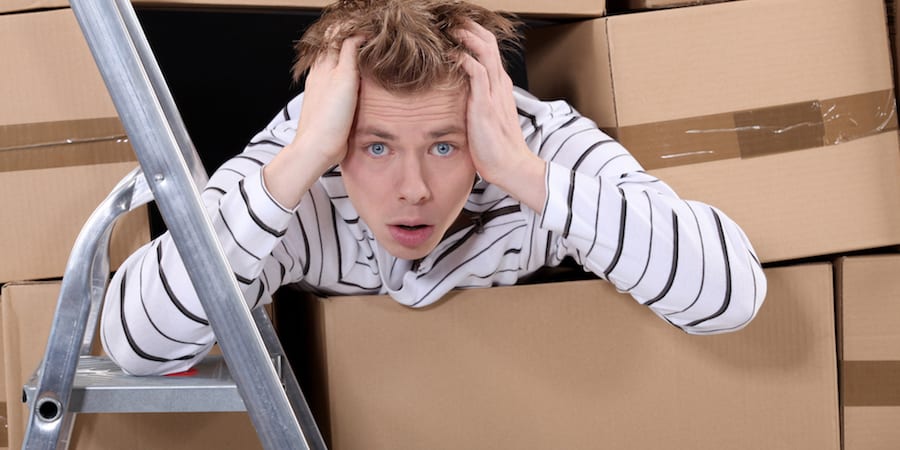
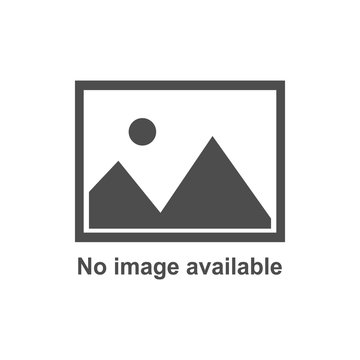
FEATURE – Inventory reduction is critical to waste elimination. Yet, many are reluctant to do it, fearing demand variability and production instability will neutralize their efforts. Grupo Sabó's story proves otherwise.