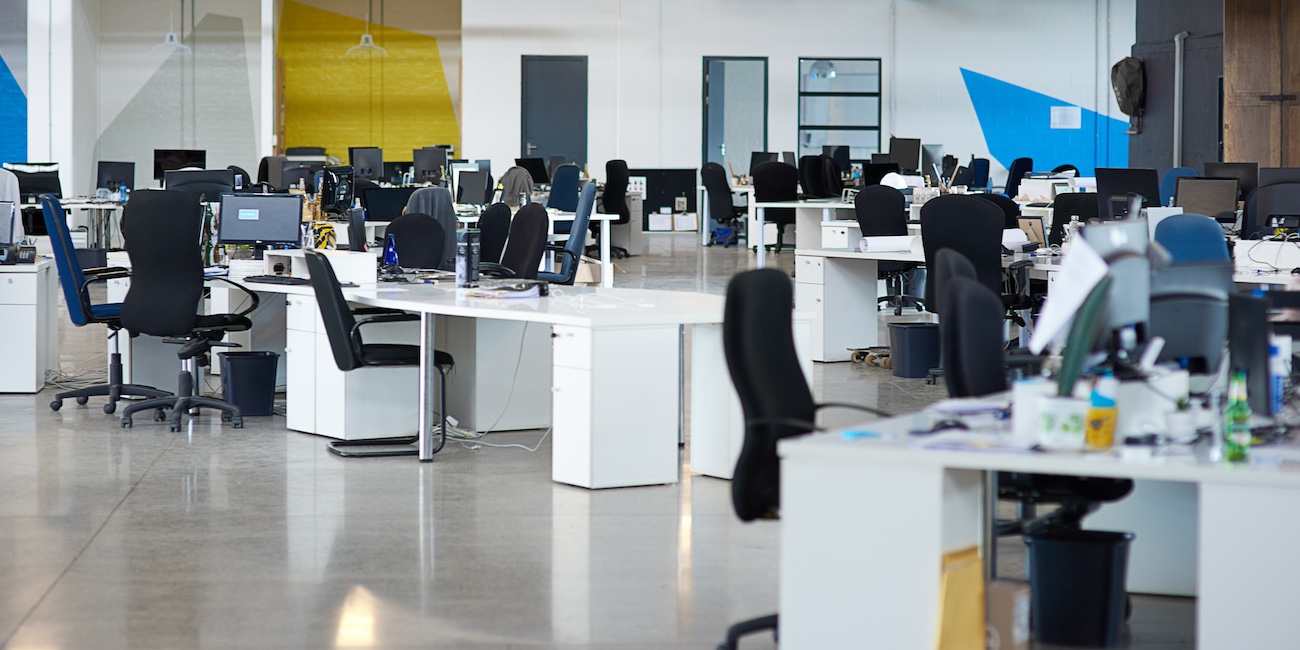
Lean Management against labor shortages
FEATURE – Attracting, developing and retaining talent has become a pressing issue in the corporate world, as new generations show skepticism towards traditional management. Lean is the answer, say the authors.
Words: Flávio Battaglia and Luciana Gomes
Companies have rarely encountered a challenge as acute as the growing shortage of qualified workers across various sectors, coupled with the difficulty of retaining talent after hiring. This phenomenon – which is occurring all over the world – threatens to undermine competitiveness, innovation, and sustainability.
Globally, 77% of companies struggle to find professionals, the highest percentage in 17 years, according to ManpowerGroup's Global Talent Shortage 2023. By 2030, there is already a projected deficit of 85 million specialists in data science, cybersecurity, and artificial intelligence. This could lead to annual losses of up to $8.5 trillion, according to the World Economic Forum.
Some of the causes behind this phenomenon are well-known. For example, the rise of informal work, digital entrepreneurship, and certain types of gig work (like app-based delivery drivers and riders) have drawn workers away from more traditional industries. The challenge becomes even more complex with the arrival of Generation Z in the workforce. These "digital natives," born between the mid-1990s and early 2010s, also known as Zoomers or Centennials, have distinctive characteristics that are both interesting and challenging. They are hyper-connected, creative, and authentic. They easily adapt to multitasking and lean towards entrepreneurship. They place high value on autonomy, diversity, mobility, and social inclusion. However, they are also part of the "anxious generation," influenced by social media and favoring hybrid and remote work environments, and struggle with building workplace connections. These factors remain significant obstacles for more traditional companies.
Once again, management approaches play a critical role. Organizations must be prepared to train, develop, attract, and retain professionals effectively. In this context, Lean Thinking stands out. Its socio-technical approach emphasizes communication and human relationships. When implemented well, it can break down barriers, bring people together, and foster a favorable environment to attract and retain talent.
INSPIRING PURPOSES
The first step towards securing the right talent is simple but essential: defining a clear purpose centered on creating and delivering value to customers in all company actions. More than that, such purpose must be implemented, communicated, and broken down so that everyone understands how their efforts contribute to generating benefits for the customer and society at large, rather than just to making the company money. People need to feel that their jobs have a real impact.
Aligned with this, management must empower individuals to take a critical look at their daily tasks and continuously improve them. Employees need to feel they are not wasting time and energy on unnecessary activities and that they are increasingly productive. This enhances job satisfaction, pride, and self-esteem.
Management should also foster an environment of psychological safety where individuals truly feel included. This means they shouldn't fear punishment, retaliation, or harassment. They need the freedom to responsibly and purposefully ask questions, seek answers, learn, and teach. They should feel safe to make mistakes and challenge established norms – always in the spirit of learning collectively, solving problems collaboratively, fostering innovation, and creating value.
“Z” LEADERSHIP
To achieve this, forming well-prepared and complete leaders is essential. Leaders must be partners, motivators, and always present in the gemba (where work happens), actively listening, challenging, and providing support. Like their team members, leaders should teach and learn continuously, encouraging autonomous teamwork. They must create the conditions for success, helping individuals reach their full potential.
A structured approach toward leveraging the technical aspects of a lean system can also help develop and retain talent: for instance, mapping value streams to identify and eliminate bottlenecks and rework, or establishing clear and widely shared standards and routines. Encouraging the use of the scientific method to uncover and solve problems, such as A3 and PDCA, is equally critical. Daily Management (DM) also strengthens teamwork and a commitment to continuous improvement.
These social and technical dimensions of a lean system undoubtedly make people more empathetic, build solid bonds, and foster long-lasting relationships. They can trigger virtuous cycles of improved communication and reduced anxiety, enhancing workers' experiences. This engagement discourages employees from seeking other opportunities and instead motivates them to grow within and alongside the company. This, in turn, strengthens organizations across various fronts, such as environmental protection, deeper solutions to social challenges, and improved corporate governance.
Labor shortages are becoming an increasingly pressing challenge in the corporate landscape. While solving this issue requires structural changes in areas like politics, economics, and education, companies have the opportunity to make a difference by revisiting their management assumptions and practices. By becoming more attractive and welcoming to prospective workers, they can create an environment conducive to professional fulfillment and the development of new generations, contributing to long-term sustainability and competitiveness.
THE AUTHORS
.jpeg)
.jpeg)
Read more
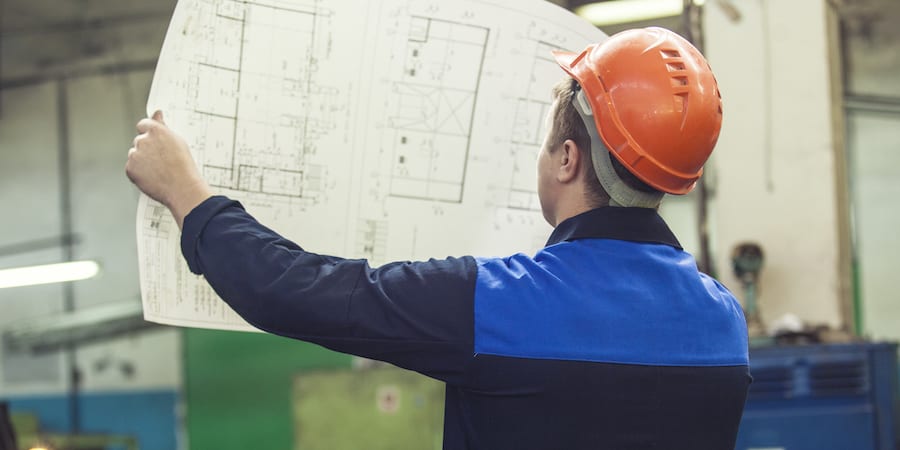
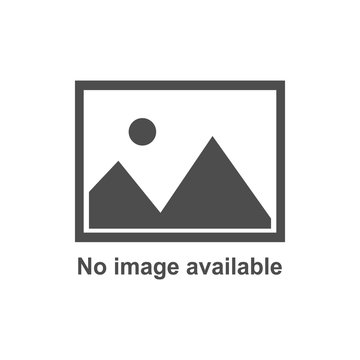
WOMACK'S YOKOTEN - Kaizen or kaikaku? This is the problem. When it comes to the pace of change, should we carry on with small, incremental improvements or aim at more revolutionary changes instead?
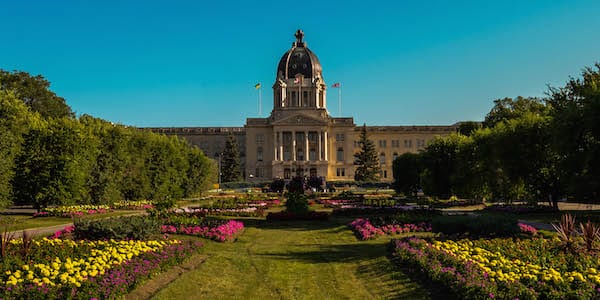
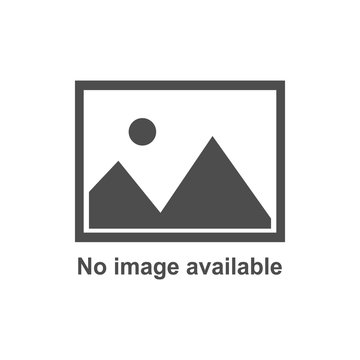
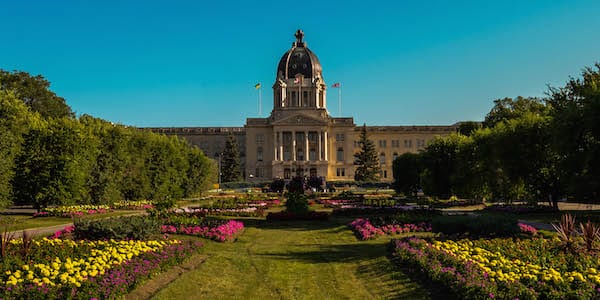
CASE STUDY – The Canadian province of Saskatchewan is running a bold experiment: applying lean management across all government. The driving force? A “compelling vision.”
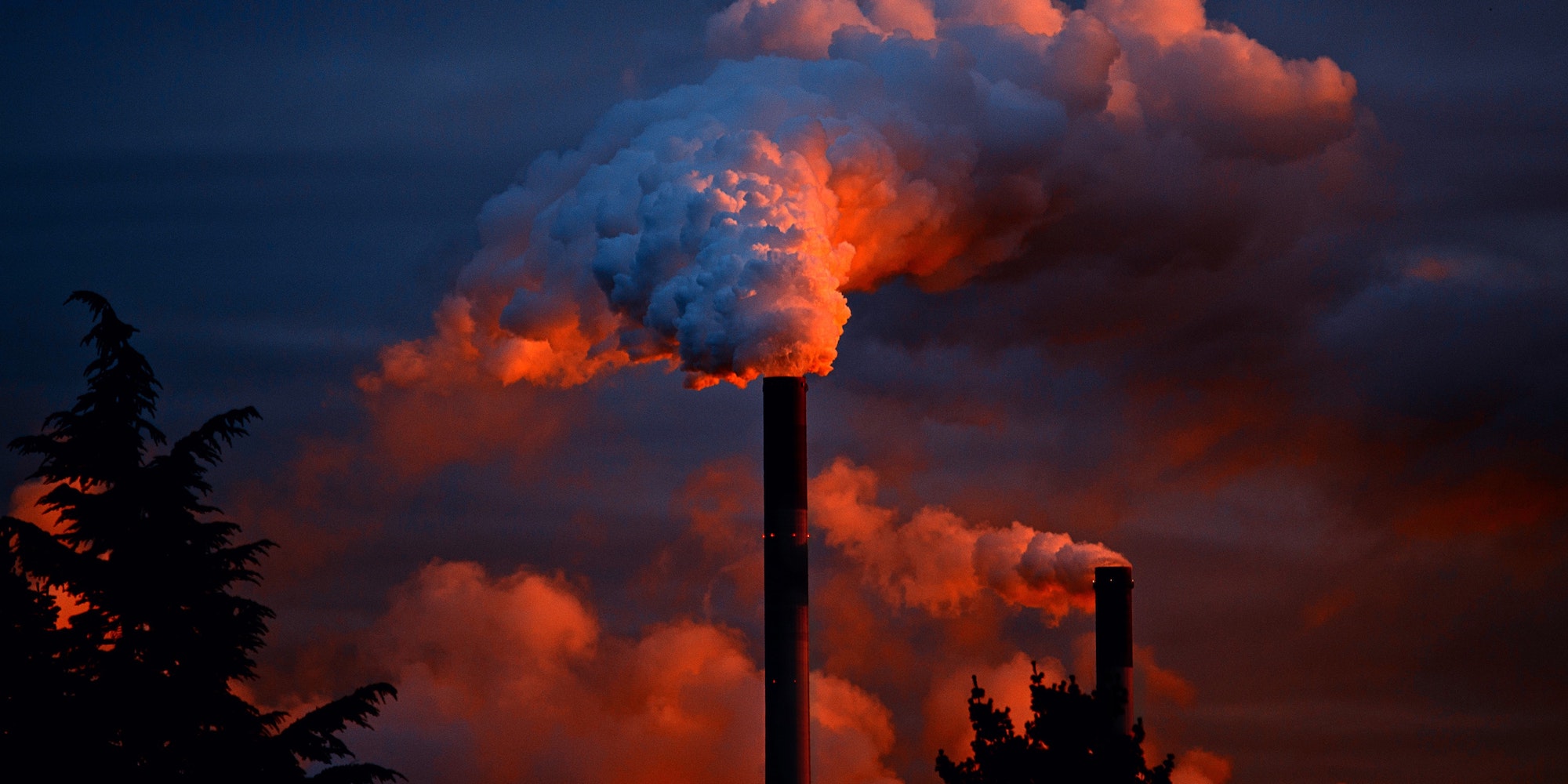
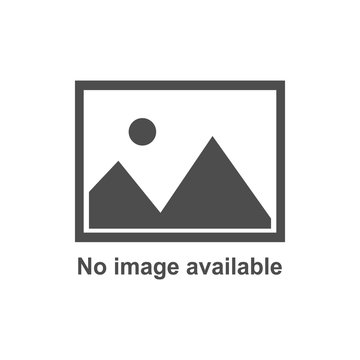
FEATURE - Imagine targeting a quarter of the world’s greenhouse gas emissions by setting our lean minds to it? The authors discuss building better, circular supply chains and designing sustainable products.
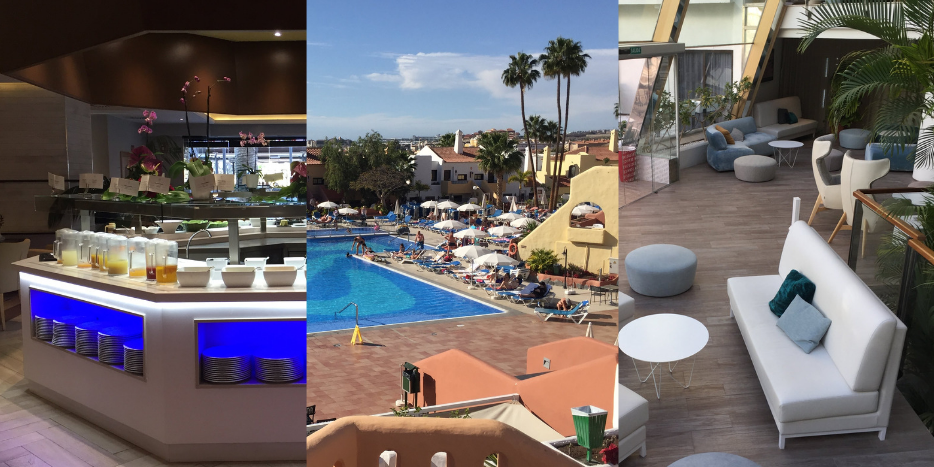
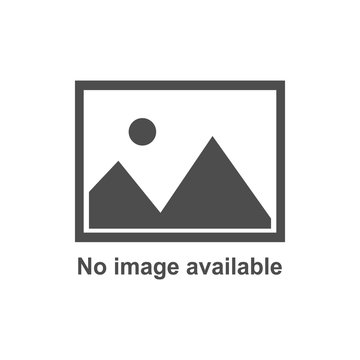
INTERVIEW – Three hotel directors from the same chain in the Canary Islands give us the lowdown on the company’s strategy to facilitate the transfer of lean knowledge from one location to another.
Read more
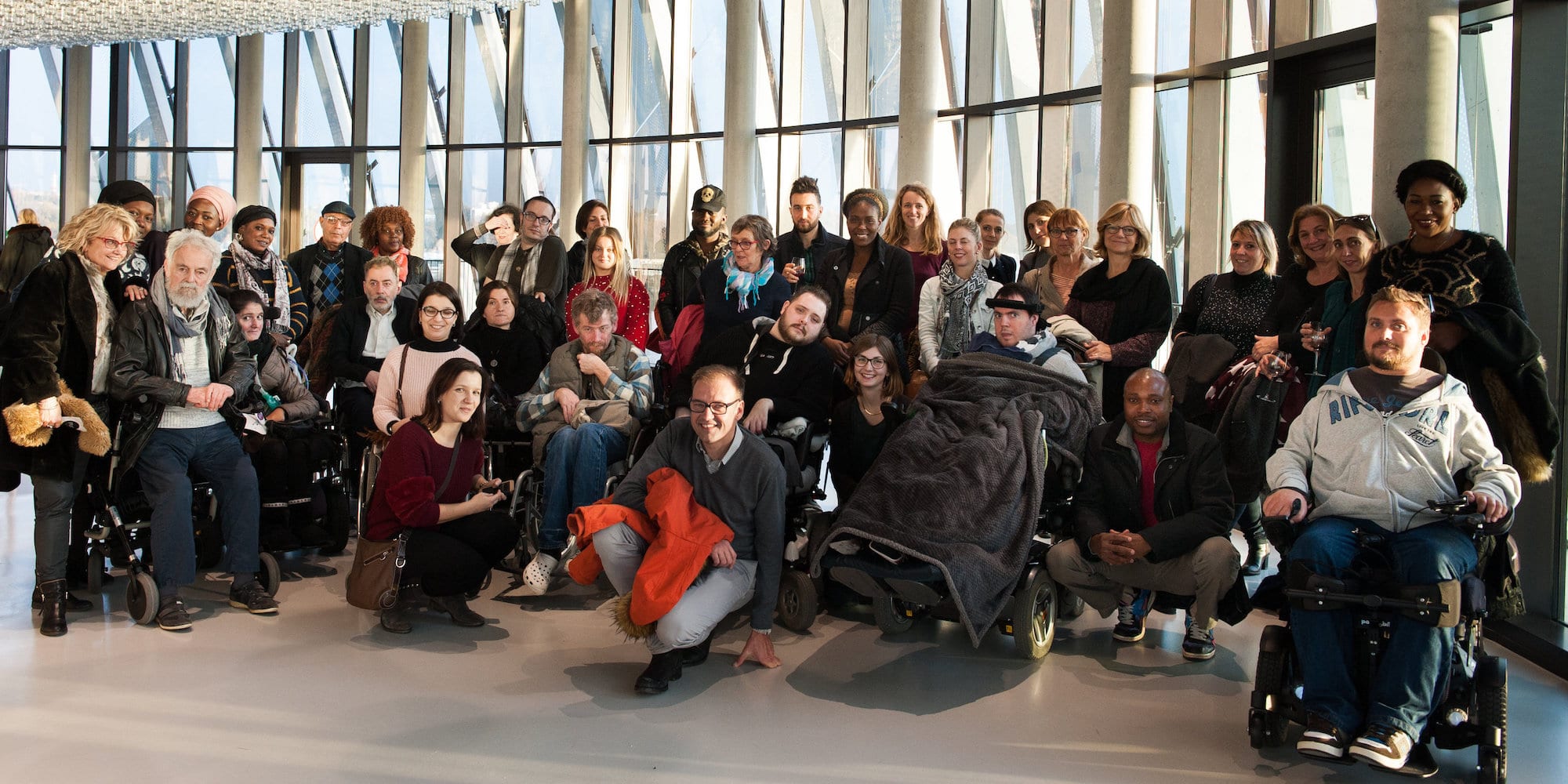
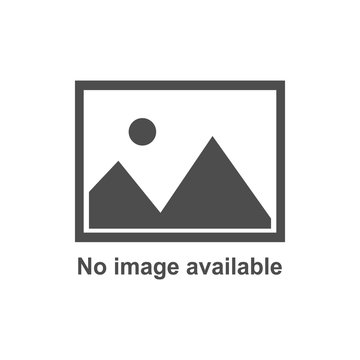
NOTES FROM THE GEMBA – This French company provides support to the severely disabled, and is currently using lean thinking to limit employee turnover and recruit faster.
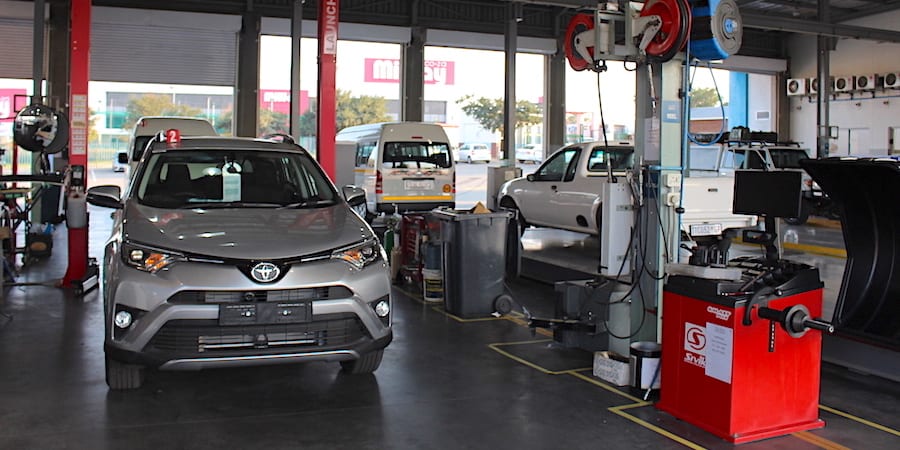
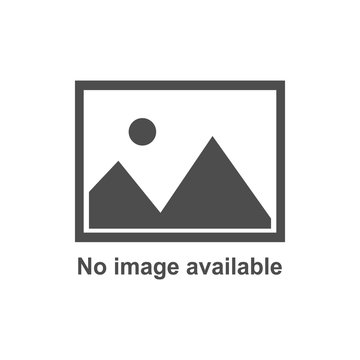
CASE STUDY – One-piece flow and a focus on lean leadership and kaizen have allowed the Halfway Production Centre in Johannesburg to turn itself around in just 14 months.
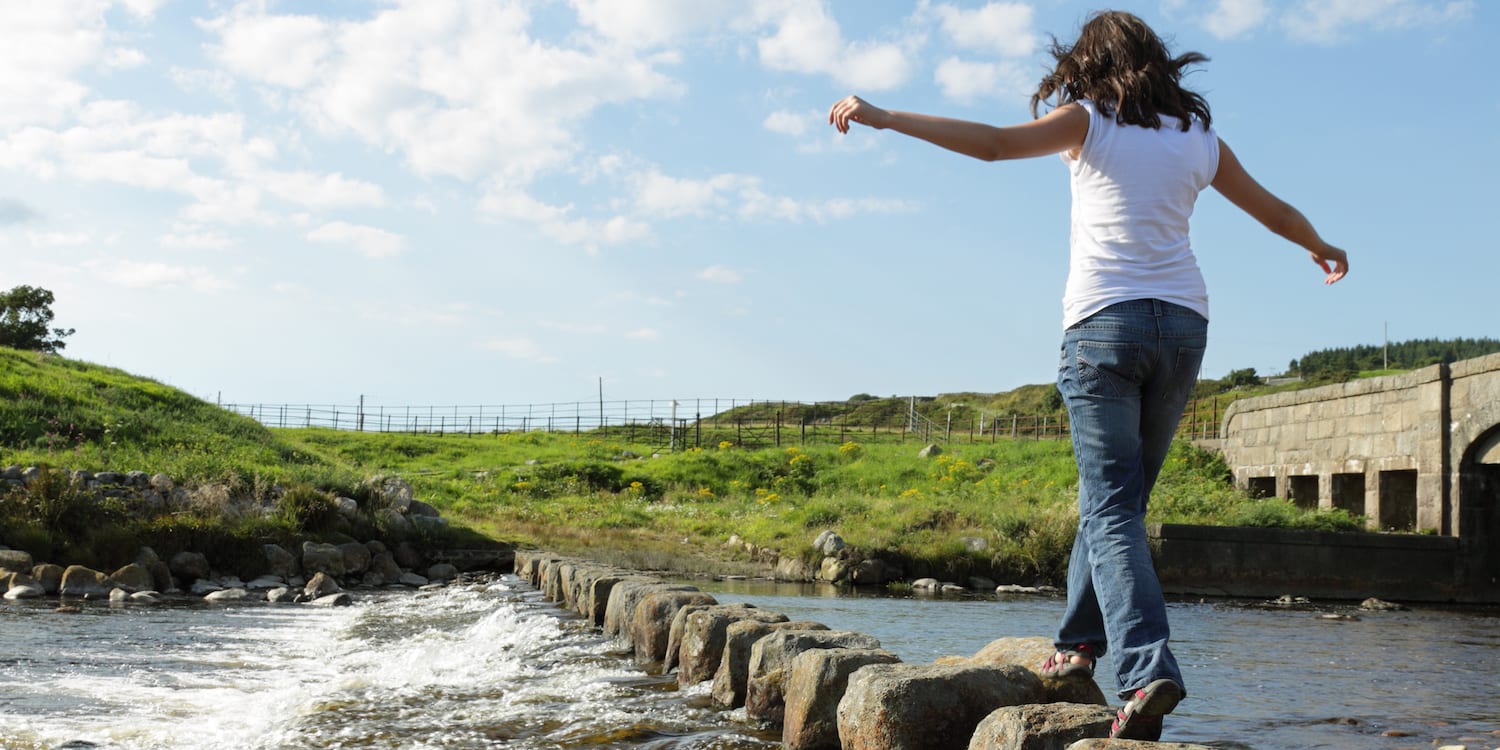
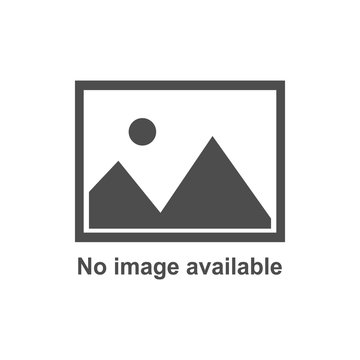
FEATURE – The continuous flow of developing people’s capabilities throughout their studies and careers is lacking, to say the least. It’s time we saw this as one big value chain.
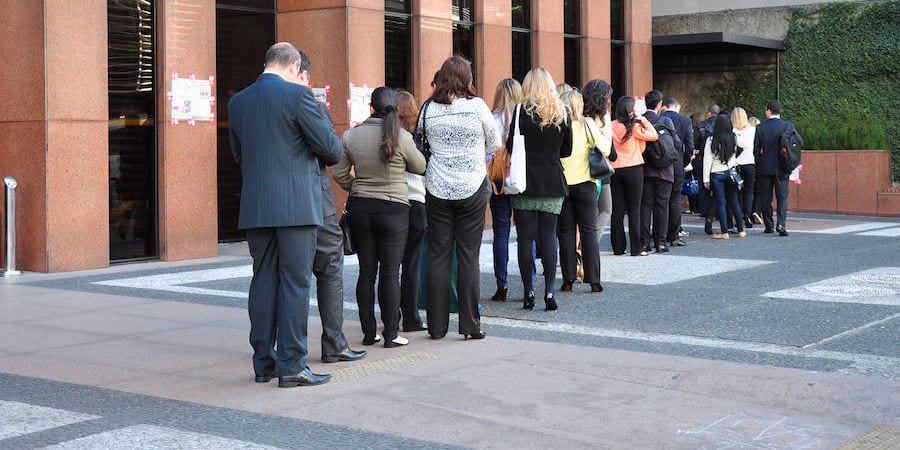
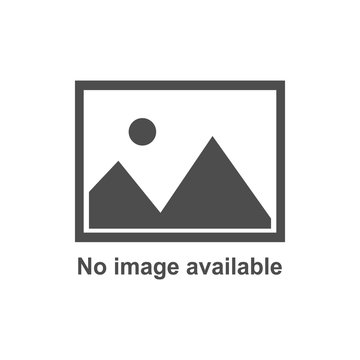
WOMACK’S YOKOTEN – What does a lean employer look like? In this month’s column, the author reflects on the long-term commitment to employees a company engaged in lean thinking should make.