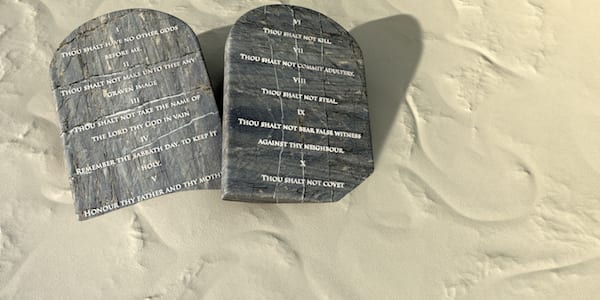
A few tips to make lean training work
FEATURE - One big "introduction to lean" course isn't enough to teach people continuous improvement. Training, and therefore learning, must happen on a daily basis. Here's the Ten Commandments of lean training.
Words: Malgorzata Jakubik and Robert Kagan, Lean Enterprise Institute Polska
“We need to change,” you are thinking. “Do my people have skills to do that? Obviously not… If they did, we would not be in the dire state we are in now. We will have to spend time and money on taking the knowledge and skills of people to the level necessary to achieve the change we want.”
These are some of the thoughts that normally go through the minds of those leaders who want their organizations improved. They realize that training will need to be a big part of the change. What they often don’t understand is that what needs to happen if change is to be sustained is not a single training “event,” but a shift towards make training and learning a daily occurrence. They need to become a natural part of daily work life, so common that they are almost subconsciously applied. After all, the importance that leaders of the organization place on training is one of the things that define lean culture!
Like with everything else, when we train people in lean we are sometimes tempted to go for the “I want results” approach, which inevitably leads us to ignoring the process. Below, we have compiled a list of “sins of the lean training process” – actual points of view and decisions that we have witnessed, argued against, and often changed while working in our lean transformation projects.
Do you recognize any of them as something that might have been said or done in your organization?
Sin #1 – “Manufacturing will decide when and what to train. HR will organize it and keep the records.”
Sounds logical, yet this is a capital sin when trying to develop an effective learning infrastructure in your organization. Since lean training takes place on the shop floor, involves internal trainers and often does not take a whole day, it tends to be completely ignored by the “official” training process. The two departments - manufacturing and HR - look down upon each other. According to manufacturing, HR does not understand and is slow and bureaucratic in the way it reacts. According to HR, manufacturing is smug, doesn’t follow established processes and doesn’t appreciate the department’s efforts to plan and keep record of the training. The result of this is that they work separately, losing that synergy the process would benefit so much from.
We have seen a number of good examples of this: these two functions need to act as partners, with HR treating manufacturing as a customer and manufacturing using HR’s process expertise.
Sin #2 – “Being a trainer is degrading for a manager and a complete waste of time. Trainers do training, not managers.”
This is what a high-level leader told a manager in one of the plants we worked in. The manager looked stunned. He enjoyed explaining lean to his people, who in turn had started to treat him with more respect. He obviously knew what he wanted them to do and was there to help them understand. Now leadership was taking something away from him that was in many ways the true role of a lean leader. This is another sin against building an organization in which everybody learns effectively. It also wastes motivation, creativity and engagement.
Sin #3 – “We cannot waste too much time on training. Let’s hire people as late as possible. It costs money. They will have to train on the go.”
Every time we open a new plant, set up a new line or establish a new process and we have to hire or move people, there is a clash between the need to find the time to train people and the cost we incur for every day people are not working. Well, let us tell you this: training on the go is a sin. It will end up costing you twice as much in the form of safety, quality and rework. It will have the detrimental effect of teaching your people that knowing standards and being able to follow them is not important, and that carrying on as best as they can is sufficient. Once they learn that, it will be very difficult to change their minds and attitudes. Invest in training from the beginning!
Sin #4 – “People have been through training. I have their signatures on the list. If they don’t perform now, it is their fault.”
Having taken part in training means nothing in itself. Instead, being able to perform a task to standard is everything. It is a sin not to work on your training method until it actually brings results.
Sin #5 – “It does not make sense to plan for training. Production needs will always come first. We will train when we have time.”
Every time we hear that training is impossible to plan, we know there is something that is generally wrong with the way the organization is managed. Training is in fact one big PDCA exercise that can be planned easily. Processes vary and there might be different levels of variation in them, but if you know your processes you need to find the training method that matches them. It is a sin not to plan for training. You do not need to plan the exact days when training will be happening, but you need to determine what skills need to be taught, to whom and in what timeframe. Dividing training into standard modules and using internal trainers will make training possible even in fast-changing, high-pressure environments.
Sin #6 – “You’ve been to a kanban training. Now go and implement. We better have a working process within three months.”
Lean training is about building internal knowledge and capability within your organization. The key here is the word “building.” It is a sin to expect inexperienced people to perform without being given any support and time to experiment and develop. A kanban training is nothing but a trigger for an implementation process. People who are tasked with making lean tools work desperately need to know where to look for advice and who is there to help them and answer their questions when they struggle.
These were just a few very common sins against lean training. But no discussion on sins would be complete without a few pointers on how to stay away from them. That’s why we recommend you study and apply our 10 Commandments of lean training:
- Build training capability within your organization. Outsiders should only be used to start the process.
- Make sure that all leadership levels in your organization are teaching.
- If your training efforts have not resulted in practical applications of the process or tool taught, you have failed. Make sure practice is a vital part of every training event.
- Whatever the training method, make sure you use a standard process and check its effectiveness.
- Use a drip-feed approach to training – teach in small amounts, but regularly.
- Go back and review the foundational elements of lean. Make sure you are creative in how you teach them.
- Use a standard training process for new trainers so you are really sure they are capable and comfortable carrying out their training tasks.
- Regularly audit your training process like you would any other. Judge by results: if people fail to perform standardized work after the training, revise how they have been trained even though the training package seems fine!
- Plan training properly. Consult with all groups of users (participants, their bosses and the leaders of the organization), listen to their needs and respond quickly.
- Plan attitude and culture shaping training. Make leaders coaches as well as trainers.
In tune with the religious tone of this article, stay away from sin and follow the commandments. You will see your training efforts result in the development of a dynamic learning organization! So help you God!
This article is also available in Polish here
THE AUTHORS
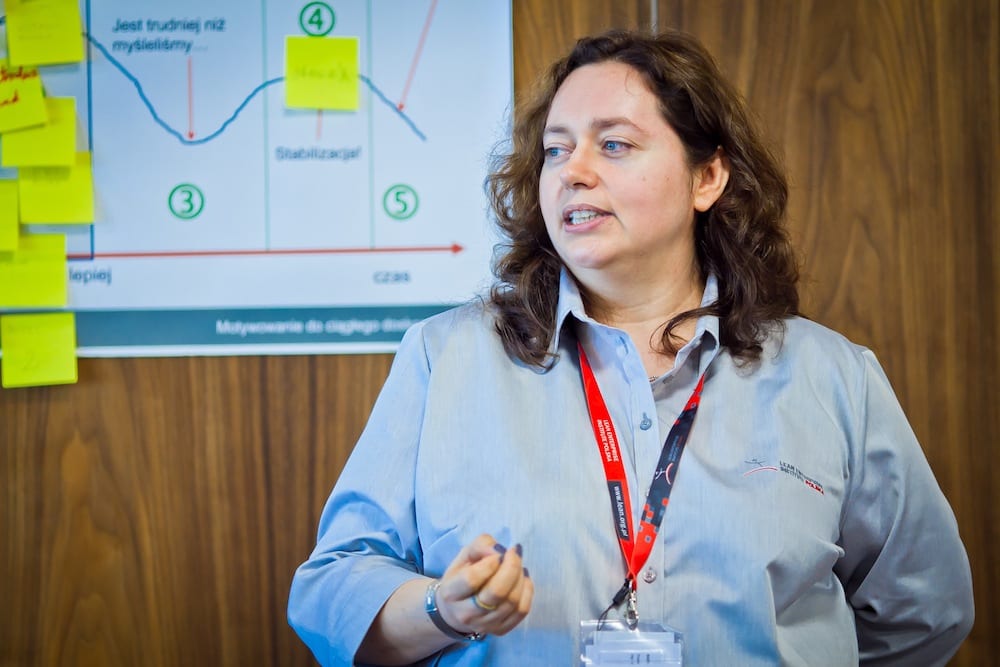
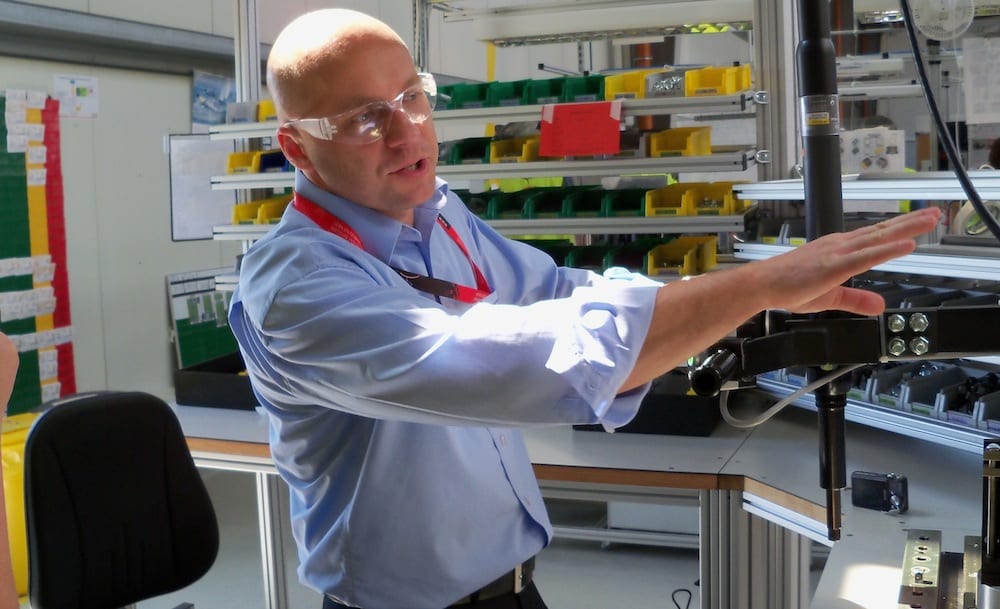
Read more
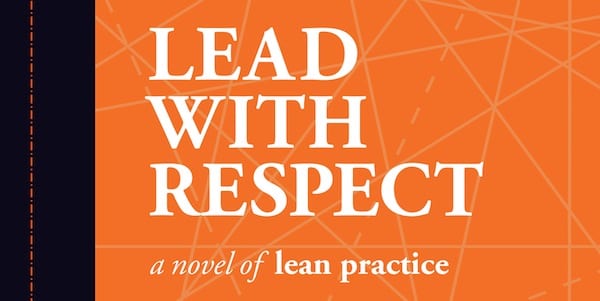
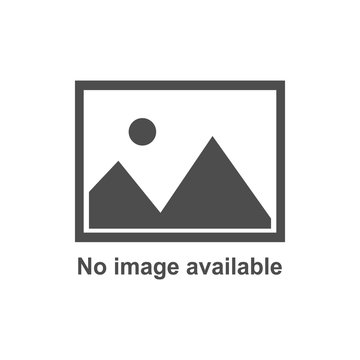
REVIEW - Michael and Freddy Ballé’s new novel, which came out this week, will help readers to understand what it really means to be a lean leader and respect people.
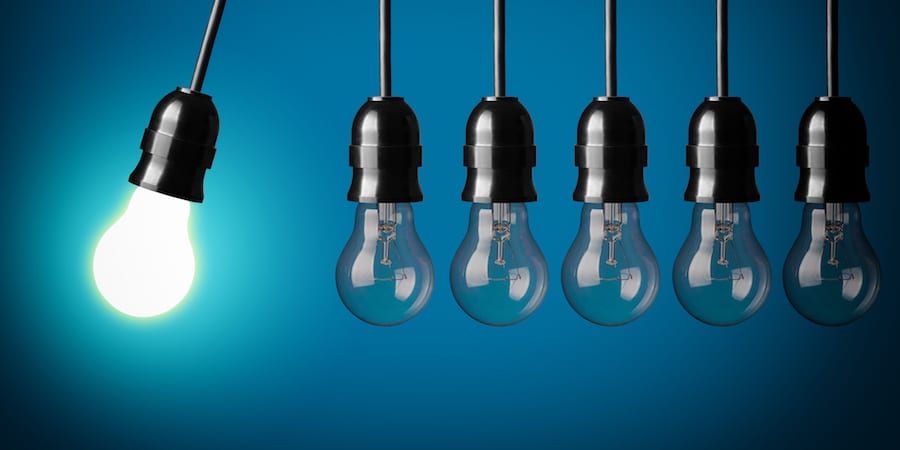
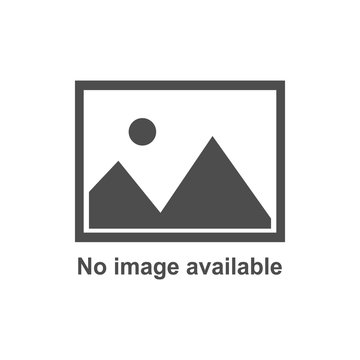
ONE QUESTION, FIVE ANSWERS – Change might be scary but, when things do work out, it also brings us incredible pride and sense of accomplishment. We asked five practitioners to tell us what the most satisfying moment in their lean journey was.
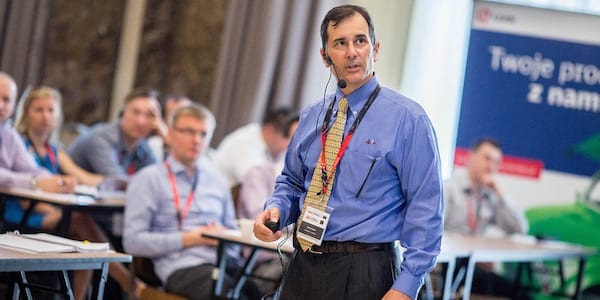
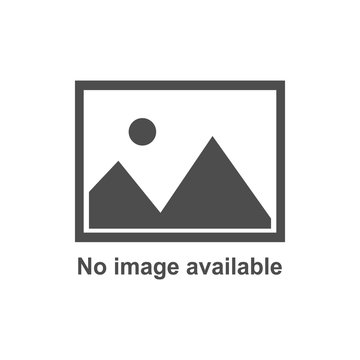
INTERVIEW - What lies at the core of kaizen activity? How has the concept of kaizen evolved over time? Planet Lean’s editor Roberto Priolo discusses these and other topics with kaizen expert Mark Hamel.
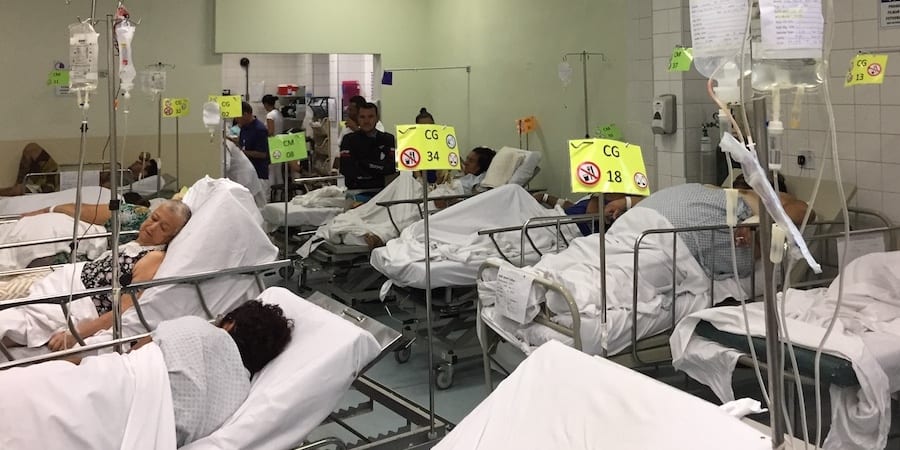
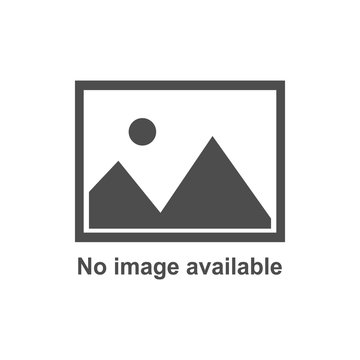
FEATURE – The importance of leveraging early successes to drive engagement to lean is often talked about. The story of this Brazilian hospital confirms this is the way to go.