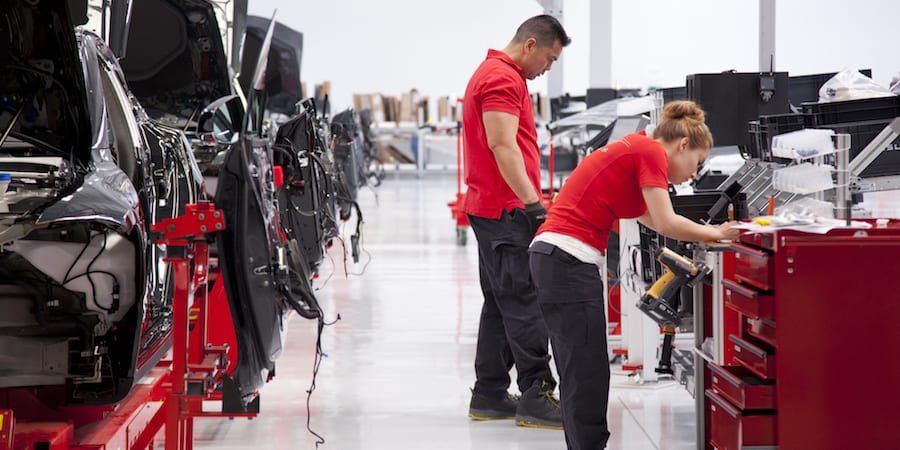
Lean has changed the production line forever
WOMACK’S YOKOTEN – This month, the author looks at the production line, a century-old idea that still fascinates us, reflecting on how lean thinking has changed it.
Words: Jim Womack, Co-Founder and Senior Advisor, Lean Enterprise Institute
This month I’m doing something I never do: taking a vacation, in a remote area of New Zealand no less. This leaves me short on the gemba experience I need for my column. So I was delighted – on my PC in my country cottage – to come across YouTube clips of a brand-new moving assembly line for railway locomotives that General Electric has just launched at its factory in Contagem, Brazil, and other clips of Tesla’s production line in California as it looks prior to the promised leap to worker-free assembly. They caused me to think anew about an old idea – the assembly line.
The idea of moving products past a line of workers and production stations (hence, “the line”) has been one of the iconic images of industrial, business and social history in the 104 years since Henry Ford lined-off the first Model T at Highland Park, Michigan. Over that time, the alleged “monotonous tyranny” of the line has often been attacked (Charlie Chaplin in the 1930s, “blue collar blues” in the 1960s). But the loss (of the very same) “high-paying, blue-collar” jobs on the line has often been mourned – in every recession, and in the US and Europe even in boom times since the 1990s. And automated lines that eliminate all “touch labor” have often been forecast, with excitement about productivity gains and anxiety about job losses (beginning in the US in 1958 with the introduction of the first robot at General Motors). Yet, the idea of the production line, with or without humans, keeps popping up after more than a century, today as a low-speed, low-volume, high-product-mix diesel locomotive line and as a prospective no-labor (indeed, “autonomous”) ultra-high-speed line for the Model 3 (with a vehicle lined-off every 20 seconds versus the usual 60.)
As lean thinkers, what do we make of this icon today and moving forward?
The first point is that many folks have been “working on the line” for a long time, both front-line workers to assemble the product and manufacturing or industrial engineers working to discover ways to make the line more productive with higher quality and (sometimes) more humane. Henry’s line, while seemingly a mature idea at birth, was only the start, due to the lack of feedback loops for quality and improvement of the work, the obsession with the uptime and speed of the line (leading managers everywhere to “line-off” defective products to keep the line running steadily and make their KPI), and the inability to assemble a wide mix of products to customer demand.
When I started observing assembly lines around 1980, more than 60 years after Henry’s breakthrough, most were still managed with the objective of output first with quality added in stationary rework areas at the end of the line. All improvement was done by staffs of industrial and manufacturing engineers, often long after the need for improvement was discovered. And most could only handle one product type at a time, in long batches.
Toyota started to change this thinking in the 1950s and 1960s with the small team and the team leader (rather than the foreman with a 20 or 30 person span on control), “quality first” with line stops as needed, the mixed-model line to assemble a variety of product on the same line at the same time, and kaizen to deal with impediments to productivity and to alleviate worker “struggles” in doing good work in a humane way.
Equally interesting and important, Toyota was also the leader in the 1960s in applying the idea of the continuous flow assembly line to components manufacturing processes that had previously been conducted in process villages with many transfers of material and large losses of time between steps. In spurring this transition in its supplier firms, Toyota urged starting with a “model line” (even though there was no traditional assembly line on a track) for a single product family with the concept of “single-piece-flow” to takt time as the substitute for the pacing function of the traditional line. And, in many cases, Toyota advisors urged suppliers to altogether eliminate assembly lines for components. Instead, they incorporated the final assembly steps for each product family in a “cell” (which is really a u-shaped line) where the fabrication of parts was also occurring in single-piece flow. Thus “model lines” were often cells that eliminated traditional assembly lines.
In the past 20 years, the big contribution of the Lean Community has been to apply the concept of the moving line and the single-piece-flow cell to practically any value-creating process, many a world away from the auto industry factory: patient flow in healthcare, document processing in a financial services, software writing for Apps, etc.
The sum-up is that the current-day best-practice line is the culmination of more than a century of thinking and experimentation. Both innovation and spread (yokoten) have been a lengthy process.
The second key point about the line is that it continues to be a powerful business idea because it focuses our minds on speed, which gives us shortened lead-times that in turn can mean a dramatic reduction in costly inventories that tie up cash. But for a line to actually achieve these business objectives men (or better, people), methods, machines, and materials (the 4Ms) must be tightly synchronized. A line is a technical achievement, but it is also a socio-technical phenomenon. And this is true whether it is largely manual or even totally automated.
This means that work must be standardized and precisely repeatable within takt time, that the people must be engaged in continuous improvement (touch labor, front-line managers, and engineers) to keep performance from deteriorating, that equipment must work correctly on every cycle (because lines by design require everything to work or nothing progresses), and that good materials must arrive from suppliers at the line every time at the right time in the right amount. If these conditions aren’t met, the high-speed, high-quality, high-throughput, low-cost line of theory becomes the jerky, quality-by-rework, lower throughput, high-cost line of practice. In the 1980s at NUMMI, GM managers and then Toyota managers operated assembly lines doing exactly the same things. But, due to superiority on every one of the 4Ms and a constant focus on the social aspects of production, the Toyota-managed line had much higher quality at much lower cost with much shorter lead-times than the previous GM line doing the same basic work in the same facility.
In essence, only paying attention to the technical aspects of the line usually results in disappointment or even business failures.
A third point, looking forward, is that higher levels of automation actually require higher levels of social collaboration by managers and engineers, often working in different firms. The idea in every era seems to be that automation eliminates the need for transparency and collaboration among old-fashioned objects called human beings. The result is that things mysteriously don’t work and enormous amounts of rework of line designs, hardware and software are required to get them to work, until the business need changes and the cycle starts again.
Finally, looking further ahead, the line as a concept and as an actuality is not going to go away. The current techno-fantasy of additive (3-D) manufacturing is that whole products can be printed from the ground up at one work station rather then moving products down lines for sequential build-up of component parts. This sounds nice and is organizationally simple, but think about an additive manufacturing process that could build a car, for example, from the ground up in one place by etching chips, molding tires, laying up glass, etc. This may happen somehow someday but not on our watch, even for the teenage reader!
This said, I have no romance about the line. The manned lines of current best practice with supportive work teams, job rotation, periodic opportunities for point kaizen to make work easier, and career progressions for front-line workers into team leadership and supervision are a dramatic advance beyond Henry’s keep-your-head-down-and-keep-working line of 1914. They are not a bad thing, but they aren’t an ideal state either. In the long run, humans can do better things than put nuts on bolts and I look forward to the touch-labor free line, so long as it is done the right way for the right purpose.
To summarize, we are going to be working on the line as front-line workers, team leaders, managers, and engineers for a long time to come. Our work as a Lean Community is far from finished. The challenge now is to raise all lines to the level of current best practice and to apply the idea in every type of value-creating activity where it might be useful, even as we search for further improvements to best-practice lines through experimentation.
THE AUTHOR
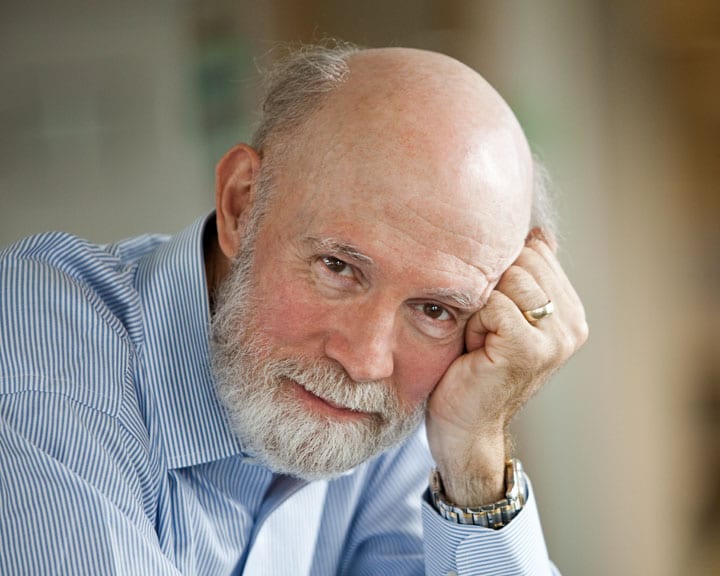
Read more
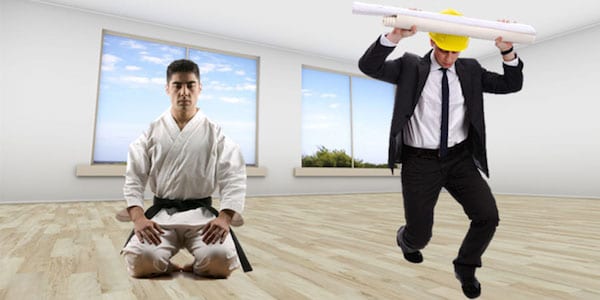
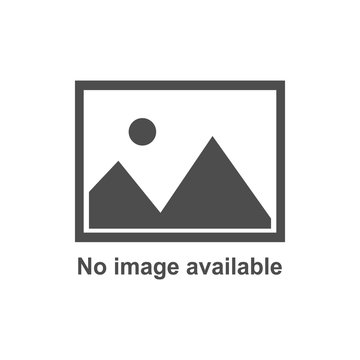
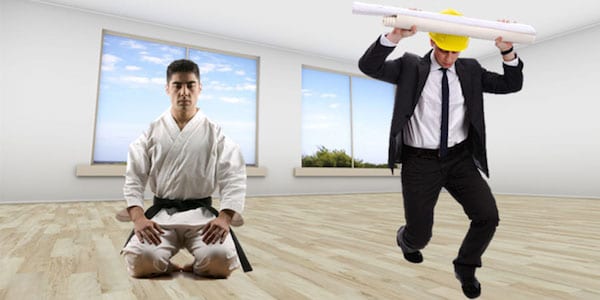
ARTICLE – In her second piece for PL, Frances Steinberg returns to the topic of working more effectively with people and the importance of going beyond the structured approach of kata familiar to so many of us.
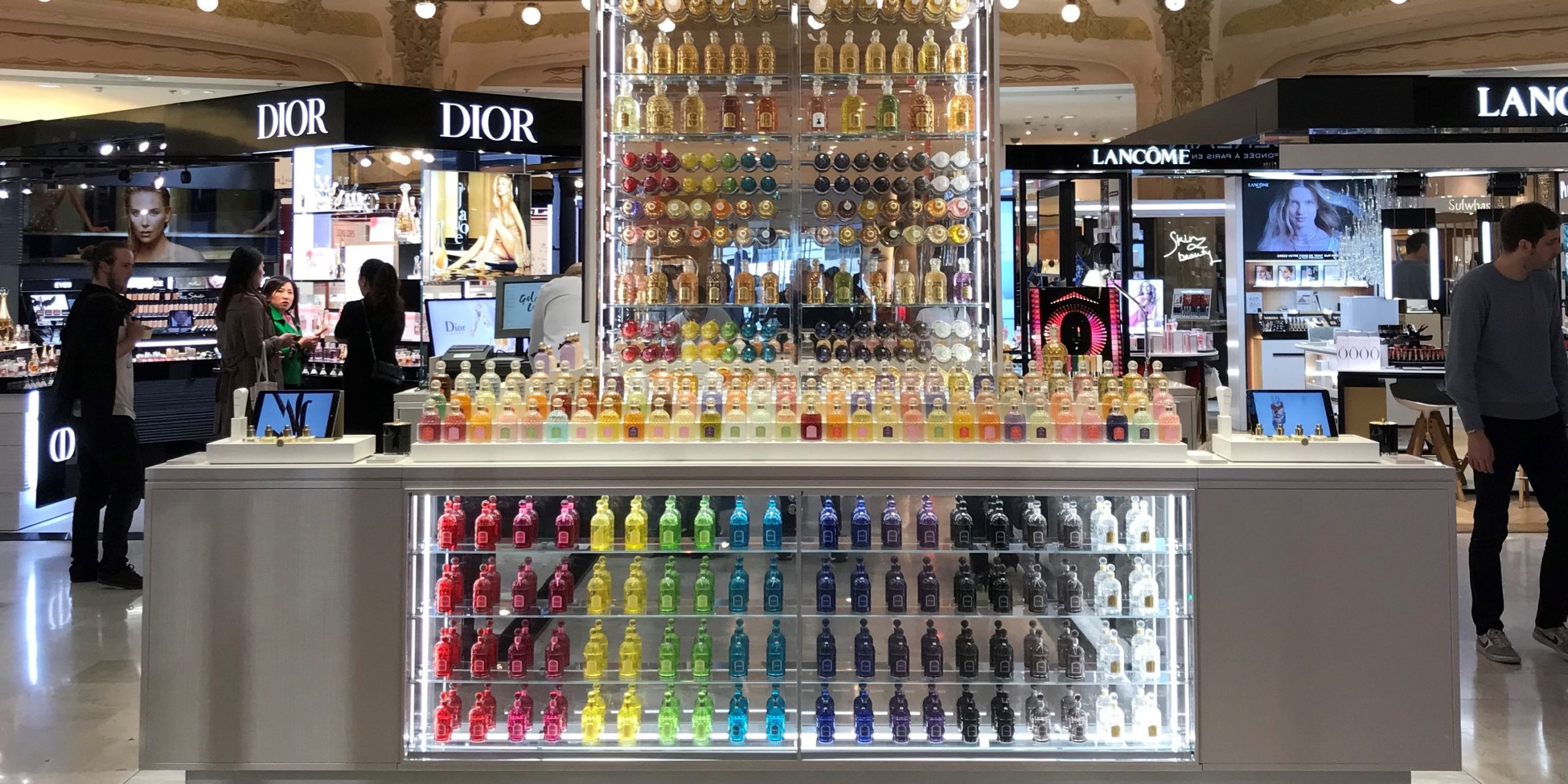
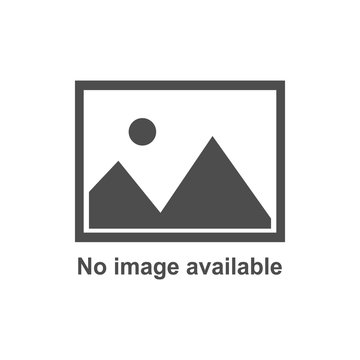
NOTES FROM THE GEMBA – How do you kick off a lean journey? This French company has chosen to begin by analyzing and tackling each customer complaint.
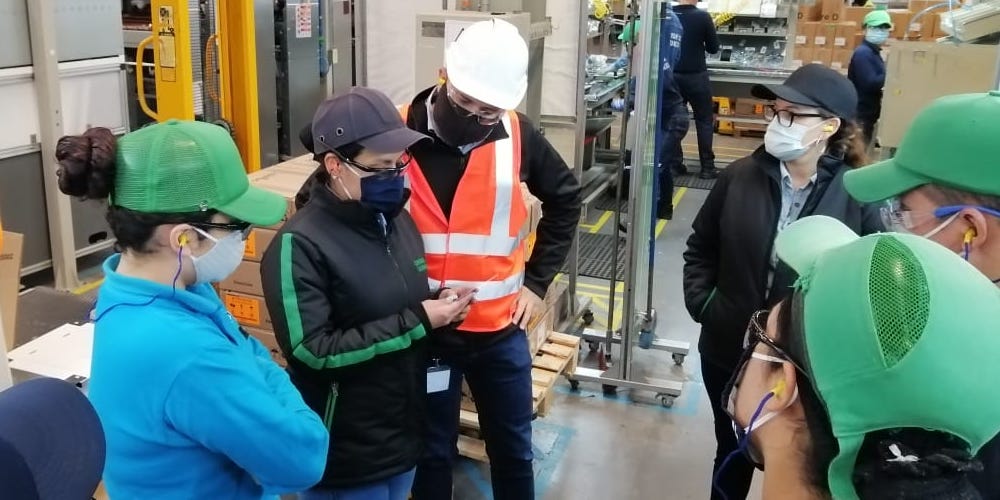
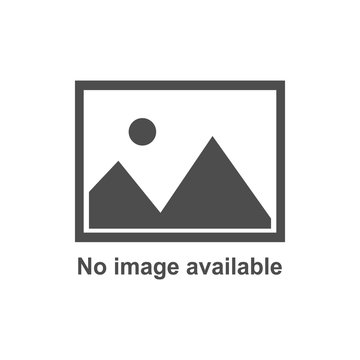
FEATURE – How do kamishibai boards work and what sort of benefits can they bring to a lean transformation? The author discusses what he saw on a recent gemba walk.
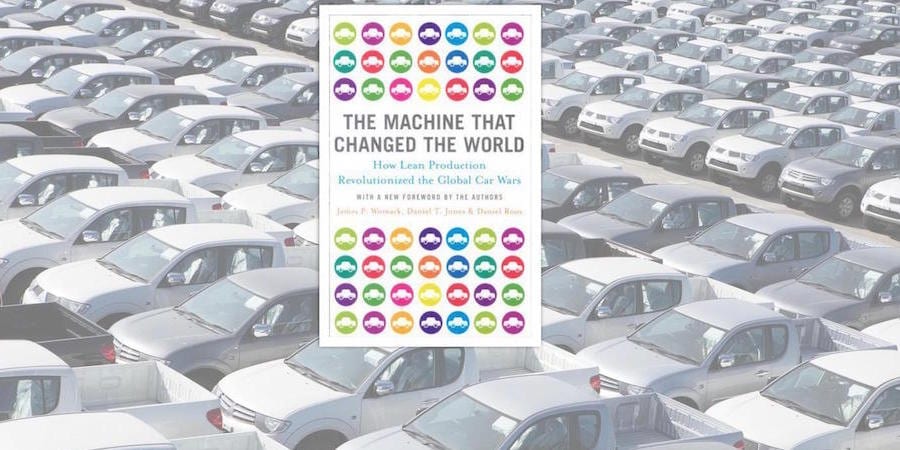
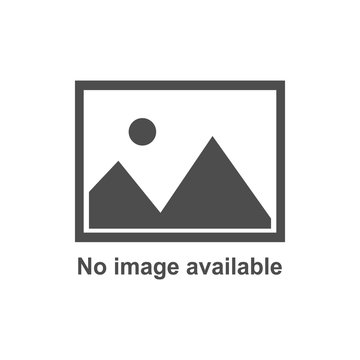
WOMACK’S YOKOTEN – On October 10, 1990 the book that introduced lean thinking to the world was published. Twenty-five years after Machine, one of the authors reflects on what the lean movement has achieved and on what is slowing it down.