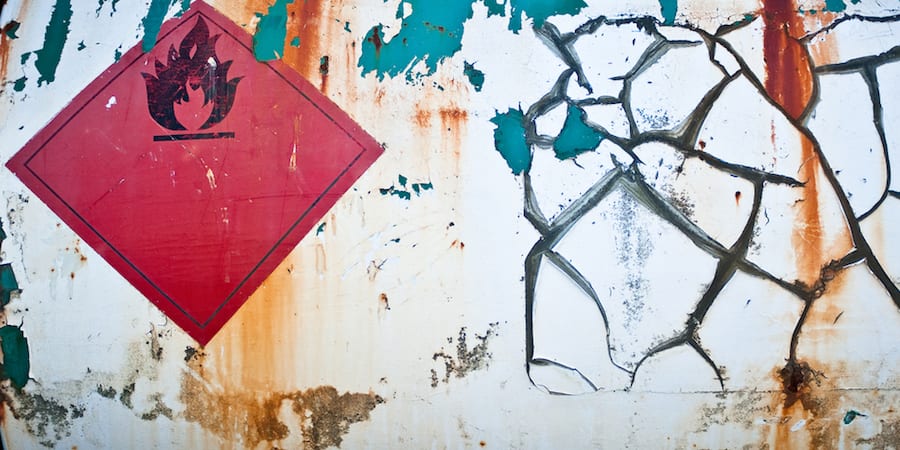
Michael Ballé on the gemba cardinal sins hindering kaizen
FEATURE – What are the immediate signs that tell us that our workplace is not conducive to kaizen? The author draws on his experience as a coach at the gemba to highlight them. Look out for them in your own company!
Words: Michael Ballé
During a recent gemba walk, I was asked, “What are the cardinal sins of the gemba?” The question certainly gave me pause. When asked to clarify, the person explained that they wondered whether some symptoms of a wrong approach to a lean implementation could be spotted at first glace. “What,” they asked, “jumps out at you on the gemba, without looking into the details, that tells you we could be misinterpreting lean principles?”
I’m not sure it’s healthy to comment on a method that is based on experiments in moral terms, without applying the rules, but let’s think about this.
I guess a “cardinal sin” in lean thinking would be creating a workspace environment where there can be no kaizen, or, to be more specific, where kaizen ideas can’t express themselves in any way. And, yes, some of this you can see at first glance, as soon as you step onto the shop floor.
If I were to list them, off the top of my head, I’d say:
- No red bins
- Isolated workstations
- Parts moved in batches
- Powerpoint charts on boards
- No daily plan and comments
- No 5S efforts
- No way for people to call for help
Now, let’s look at these examples one by one.
NO RED BINS
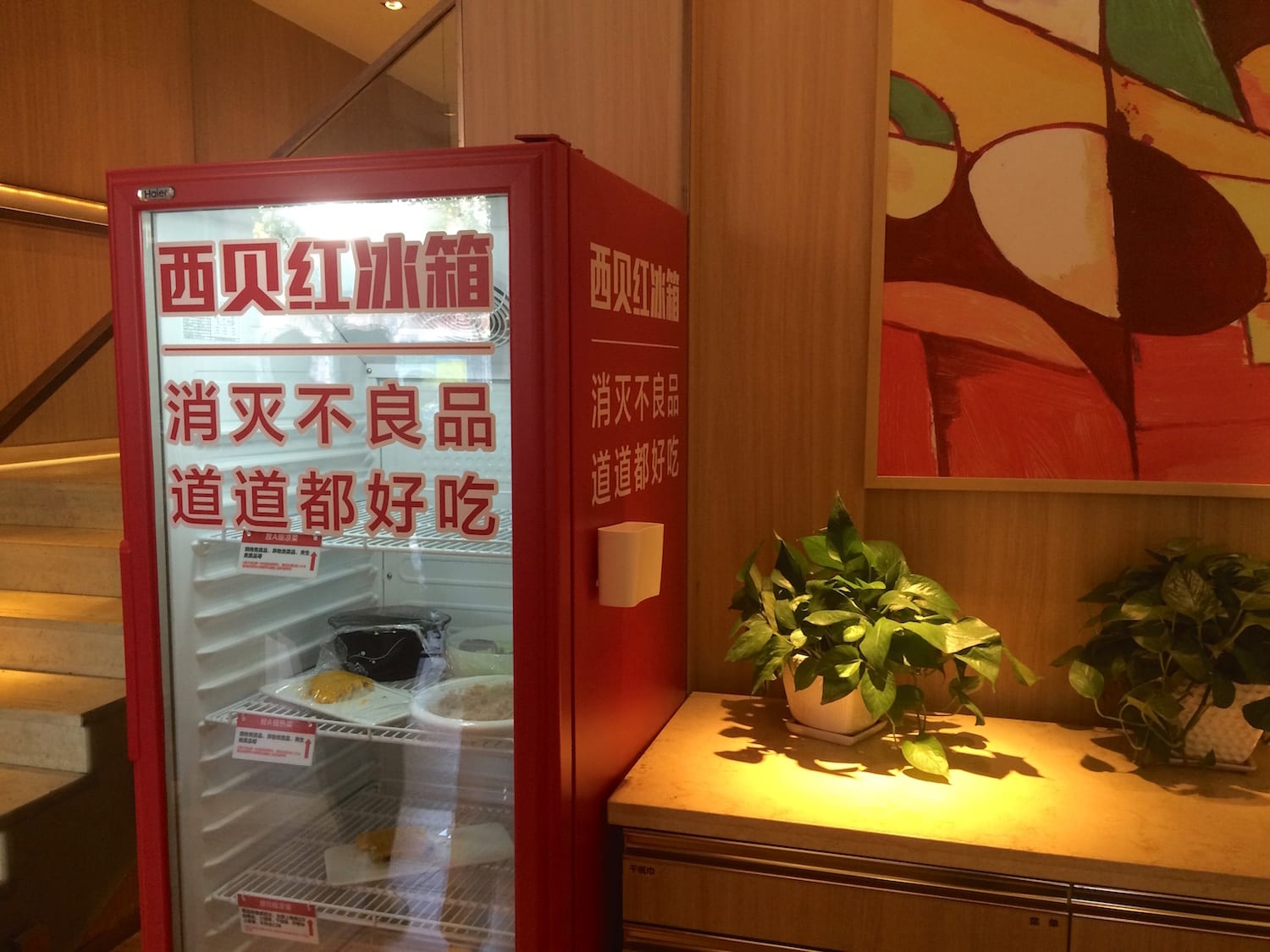
Red bins have to be literally red (red says quality issue), but they don't have to be literally bins (they can be an area - like the red fridge here). Each process should have a clearly identified place to highlight defective – our potentially defective – components of the work. Without this dedicated place, it’s obvious that the focus on quality is not on the shop floor with the employees themselves, but somewhere in the management office. This completely kills the kaizen spirit because it tells people we don’t need them to do quality work, as whatever they do wrong will be fixed somewhere else.
There are two other horrible variants of the “no red bins” sin that you still see on the gemba:
- Reject boxes painted red – nothing but containers where defectives are thrown away without any analysis. Painting them red doesn’t make them red bins. A proper red bin should highlight the defective part and trigger a rapid analysis: what is wrong with this part? What happened in the process?
- Prisons – in some places you see “locked prison cells” containing bad parts waiting to be analyzed by quality. In other words, when a part is potentially defective, it gets locked away and quality comes in its own good time to see what’s wrong with it. This is like batching quality analyses. Obviously, it is terribly wrong to do so, as the message everyone on the shop floor receives is to just carry on working, keep your nose clean, and don’t ask questions – if any problems arise, put them in the prison and the quality folks will eventually deal with it.
ISOLATED WORKSTATIONS
In recent years, many assembly lines have moved East to lower-cost countries, and the processes remaining in the West have become increasingly technical and machine intensive. As a result, we see shop floors with machines spread around and operators isolated behind each machine. This means the death of kaizen because even if an operator finds the cleverest idea to reduce their work content and improve their standard work, they can’t translate it into greater productivity because of how isolated they are. This situation should be avoided at all costs, because it stifles the teamwork and kaizen spirit.
Isolated workstations scattered around the workplace – or groups in process islands – means no flow; no flow means not looking at products one at a time, and so no opportunity to see the variation between how we make two products; no variation means we don’t see problems and can’t carry out kaizen. In the old days, the first thing we’d do to get lean started was to create flow, sometimes clumsily, in order to create the conditions for kaizen. With isolated workstations, working together in a “relay race” is impossible and not only will kaizen ideas be few, but they will also be hard to implement because of the difficulty to show their practical benefit.
PARTS MOVED IN BATCHES
You can tell right away when parts are moved in batches. There are normally piles of containers on pallets waiting to be shifted by forklifts. Forklifts, as opposed to trains, are typically another good giveaway. If parts are moved by batch at the workstation, chances are they’re being taken to an inventory of work-in-progress of finished goods and that the real manager of the workplace is the MRP. Since the MRP thrives on rescheduling in order to keep people busy and is not very interested in improvement, the odds for kaizen are very low. As with isolated workstations, any place run by a computer is death to kaizen because good ideas can’t be turned into increased performance. IT scheduling systems are not flexible enough to incorporate good ideas.
Some clever people have found ways to move parts that are supposedly more flexible, using devices that look like trains but are still batches (rather than one huge container, you’re still moving three smaller containers at one time). You’ve got to be be moving every part every hour, not fake pull. The question remains the same: if I have an idea that can reduce changeover time and, as a result, reduce batch duration (often calculated at 10 x changeover-time), can I actually benefit from it by rotating parts faster? Without proper pull, I can’t since the pick-up will still be for the full batch.
POWERPOINT CHARTS ON BOARDS
Another clear sign that the company doesn’t get kaizen is large areas with lots of boards full of PowerPoint charts, mostly hiding the shop floor. This is where front-line managers gather for so-called “visual management” or “leader standard work”, but it is actually absolute nonsense. It is nothing but another way to show operators the difference between the people who do the work and those who run the show.
Real visual management is about creating a workplace where the difference between normal and abnormal can be spotted immediately, without having to look it up on a board. Charts are hand written because they’re filled in as the work progresses (as opposed to being printed out of a PC), and they are conducive to kaizen – not the opposite.
On boards, we’re looking for, in particular:
- Photos of defectives: explaining over and over again what can happen at the customer sites if certain criteria are off in making the product. Daily analysis and discussion of customer issues is essential to keeping the kaizen spirit alive.
- Operator tracking, to ensure they take responsibility for their outcomes and always think of better ways of doing the work. Be careful, however, that tracking is in no way linked or perceived to be linked to a performance evaluation. In lean thinking, these tracking charts are about the “Check” part of the PDCA as ways to support the kaizen spirit by having an instantaneous measurement of results.
Management loves talking to itself and filling boards with information it believes operators should pay attention to. This is the very opposite of lean management (talking to operators to resolve their concerns) and a sure sign the workplace is not set up for kaizen.
NO DAILY PLAN AT WORKSTATIONS
The Production Analysis Boards showing hourly targets, realizations and comments are not for control, but to develop team autonomy. Teams are taught to 1) plan the output of the day (like planning your route to visit someone on the weekend), 2) check how the day is going, hour by hour, and 3) write down any obstacles encountered in fulfilling the promise for the day. In a lean environment, it’s these last comments that matter most – the team’s engagement in observing and explaining what is not working as it should.
Comments on the plan, whether an hourly board or actual plan, are essential to getting kaizen going – they are the first step to take responsibility for our own problems and seeking to resolve them. Of course, this only works if management is interested and regularly comes to check the boards to have this conversation. Otherwise, people will quickly drop the demanding practice of stating what, in their opinion, is going wrong with the process.
Unfortunately, many Production Analysis Boards I see are devoid of analysis – management doesn’t care enough about current working conditions to discuss with their teams how to improve them hour after hour. As a result, the “comments” column is often empty, or sometimes altogether missing, which turns the board into yet another control tool to show that output is below what was planned (yes, well, here’s a surprise). Without a visible interest in why the output was not achieved (defective parts? Machine slowdowns? Lack of qualified personnel? Component issues? Hard to keep to target with the current work method?), there is no way of starting kaizen.
NO 5S EFFORTS
I don’t mean that the workspace is messy or dirty – I mean no 5S plan. The point of 5S is people learning, through regular practice of the 5S, to create the kind of work environment where standardized work is easy to follow.
Five 5 is really about 3S, then a fourth and a fifth S:
- Sort and eliminate: look around and chuck anything that isn’t going to be useful in the near future (or file it away);
- Straighten: each item in regular use should have a dedicated location, in a way that is easy to access when needed, according to frequency or urgency of use. Sorting is not just about “a place for each thing and everything in its place,” but actually thinking out where things should be given their use.
- Shine: making sure everything is clean and working after use – so that the next cycle occurs without any surprises. Clean after using, change the batteries, put fuel in the pool car after driving. Shining is really about taking responsibility for the workplace and making sure the next user can do their work confidently.
- Standardize: what is the 5S plan to have 5S occur regularly? This is where the team takes responsibility for itself and decides a standard way to conduct its 5S. (After every job? Five minutes at the end of the day? A weekly clean-up?). This is when 5S starts happening for real as teams begin to kaizen their environment according to what they find during their regular 3S exercises.
- Sustain: how can management support the fourth S’s plan? By both auditing and helping to improve the work environment. The fifth S is about engaging teams in their own workplace and recognizing their work by giving them concrete help with issues that are outside of their control (such as IT problems, renewing dodgy equipment, etc.
Without 5S, it’s unlikely that kaizen will ever get off the ground because people won’t try to own their workspace or try to make it better. Improving 3S is the smallest kaizen one can do and a great place to start. By introducing 5S mindfully (which doesn’t mean saying, “clean your room!”) management can support and sustain very concrete kaizen and then move on to actual work methods.
NO WAY TO CALL FOR HELP
Last, but not least – maybe this should even be at the top of the list – is wondering how, on any workstation, people can deal with a difficulty. In many, many cases, managers explain than when something appears off, employees simply have to stop their work and go and find their manager who, by the way, has an open door policy and will certainly help them out. Sure, let’s picture the person stopping their work (and therefore impacting output) and, cap in hand, interrupting their manager in whatever they’re doing. No doubt the manager will immediately put down their own work and come to the rescue, right? How likely is this to happen?
The point of an andon system is to create an embedded learning system. At every doubt, an employee can flag a problem, receive support within the minute by his or her team leader who will then check standards and give a hand to correct the situation. This is like having an onsite tutor whose job is to help you learn and keep standards as you work. The relationship this close contact builds is essential to kaizen, which will spontaneously appear when people hit the same difficulty time and time again and start wondering about changing how things are done to eliminate a problem.
Setting up a pull system with andon is not the end point of lean, but it is the starting point of kaizen. As Jim Womack and Dan Jones saw years ago, the entry fee of lean is to focus on value, distinguish value streams, improve flow and go to pull in order to, then, relentlessly seek perfection through kaizen. Kaizen means forming a better process with the people doing the work themselves and taking your workplace to a superior state of performance, not by having all the answers and implementing them but by exploring problems with people and accelerating the flow of ideas up the management line and across departments.
Beyond these obvious "sins" that jump out at you as you set your first step on the gemba, is a deep problem that needs a second look to ferret out: are people working as teams, and do teams have a team leader? Teams are the locus for kaizen. As long as employees are considered as isolated human resources, no kaizen is really possible - and indeed, this worldview explains how the gemba is set up around the previous "7 sins."
One of the first questions my father, Freddy Ballé, asks on the shop floor (after asking about quality performance) is: how are people organized? Management often pulls out organizational charts to show how authority flows from the CEO down to each department head and worker. "No, no," he explains, pointing at a value-adding employee, "how is this person organized? Which team are they part of? Who is their team leader?" One of Toyota’s leading – and revolutionary – ideas is to redefine jobs as JOB = WORK + KAIZEN, and not just work. Kaizen happens in a team when the team 1) owns its own work procedures and improves by discovering new, better ways, and 2) individuals come up with new insights and suggestions. Neither will happen on their own unless a team leader leads this process, with the support of his or her own front-line manager. The lack of teams or team leaders is probably the biggest sign on the shop floor that the company, regardless of all the lean bureaucracy it has put in place, is not serious in developing the kaizen spirit in each person.
TO CONCLUDE
I’m not sure “cardinal sins” is quite the right term. The definition of “sin” is wrongdoing in the eyes of God – which does seem a bit over the top in the context of lean thinking – while another more casual meaning is simply “missing the mark.” In this simpler sense, it is indeed easy to miss the mark in a lean implementation. The point of lean tools and processes is kaizen – improving customer satisfaction by engaging all employees in small-step changes for the better, one after the other. Too often, managers will “implement” lean to fix the process and simply replace, say, an ERP system with kanban cards, still without kaizen.
Kanban, for instance, should be a tool for kaizen (constantly reducing cards) and not the other way around – doing kaizen to install kanban. The mark is 1) improvement suggestions from every one, all the time, 2) problem avoidance and eradicating the cause of problems on a daily basis, and 3) teams taking responsibility for their own work methods and improving them regularly, one topic after the other.
Certain workspace conditions, such as flow and pull, will support kaizen; others will inhibit it. In this sense, yes, one can see at a glance how certain characteristics in the layout of a shop floor can make it difficult for kaizen to thrive. Learning to see them right away and to understand the various ways in which they will hinder your ability to improve is a key part of learning to think lean.
THE AUTHOR
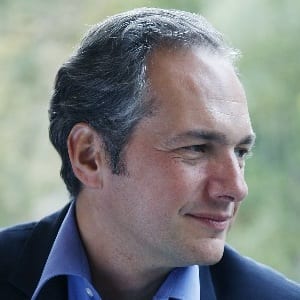
Read more
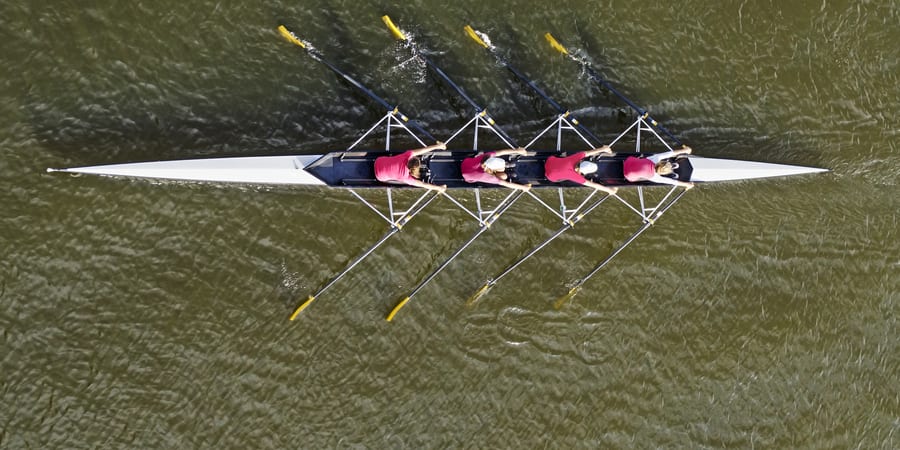
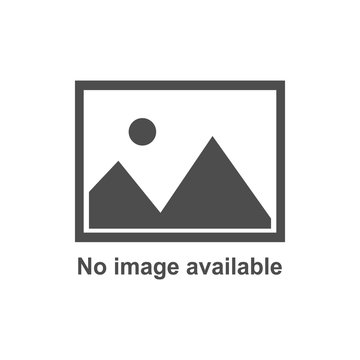
FEATURE – We all want to create a lean culture in our organizations, but what makes cultural change possible? And, more importantly, what are the leadership behaviors that enable a new culture to take root?
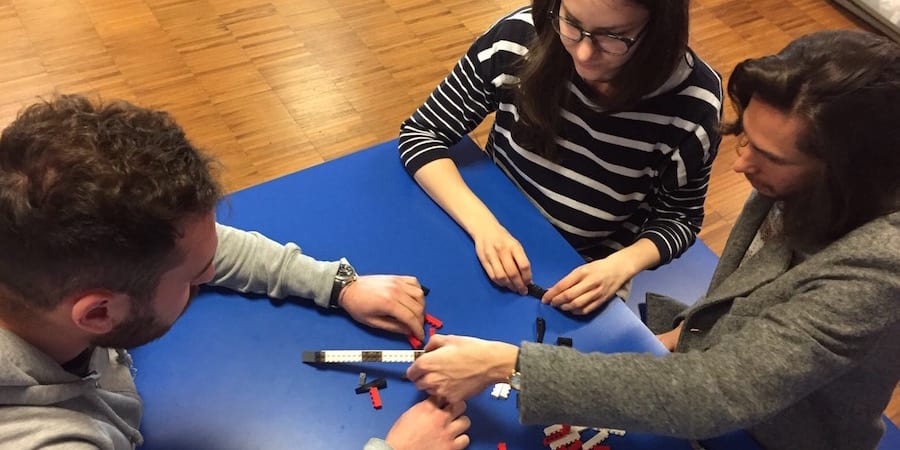
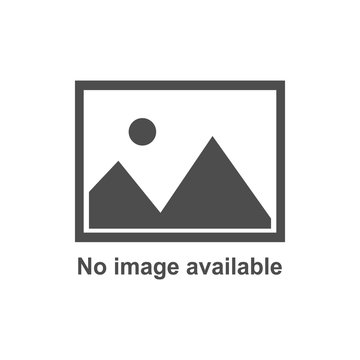
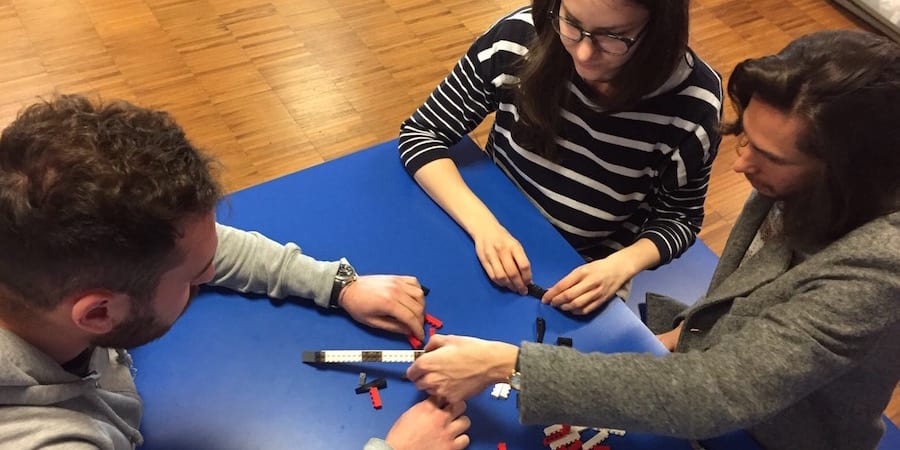
FEATURE – In a world of disruptive innovation, being faster and smarter at developing new products has become critical. The authors explain why set-based concurrent engineering is the answer, and why a game is the best way to learn it.
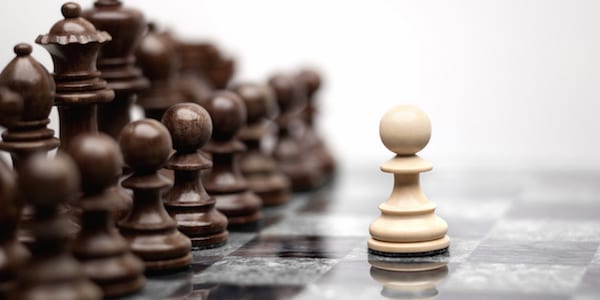
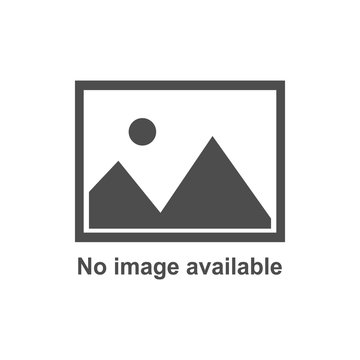
INTERVIEW – During a chat with Planet Lean, Darril Wilburn explains why courage and humility are necessary elements to establish a culture based on continuous improvement.
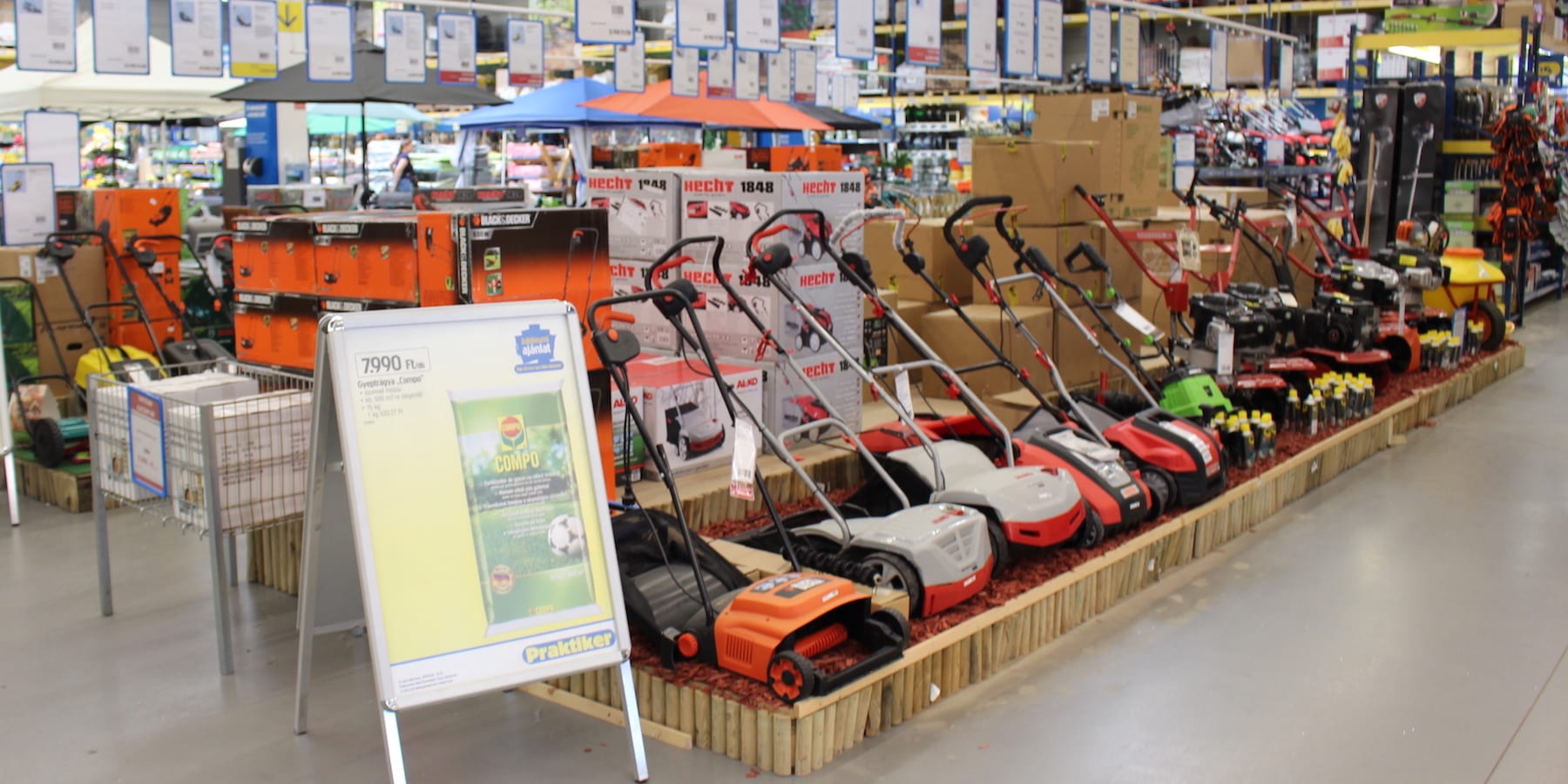
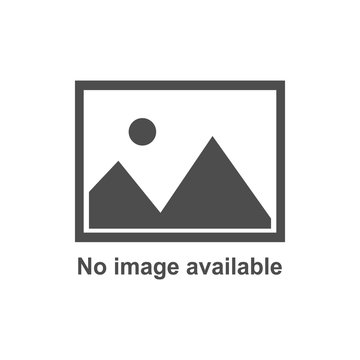
FEATURE – When Praktiker decided to turn to lean thinking, they were faced with the challenge of rolling out its principles and practices to 20 DIY stores. Here’s how they are trying to make it work.