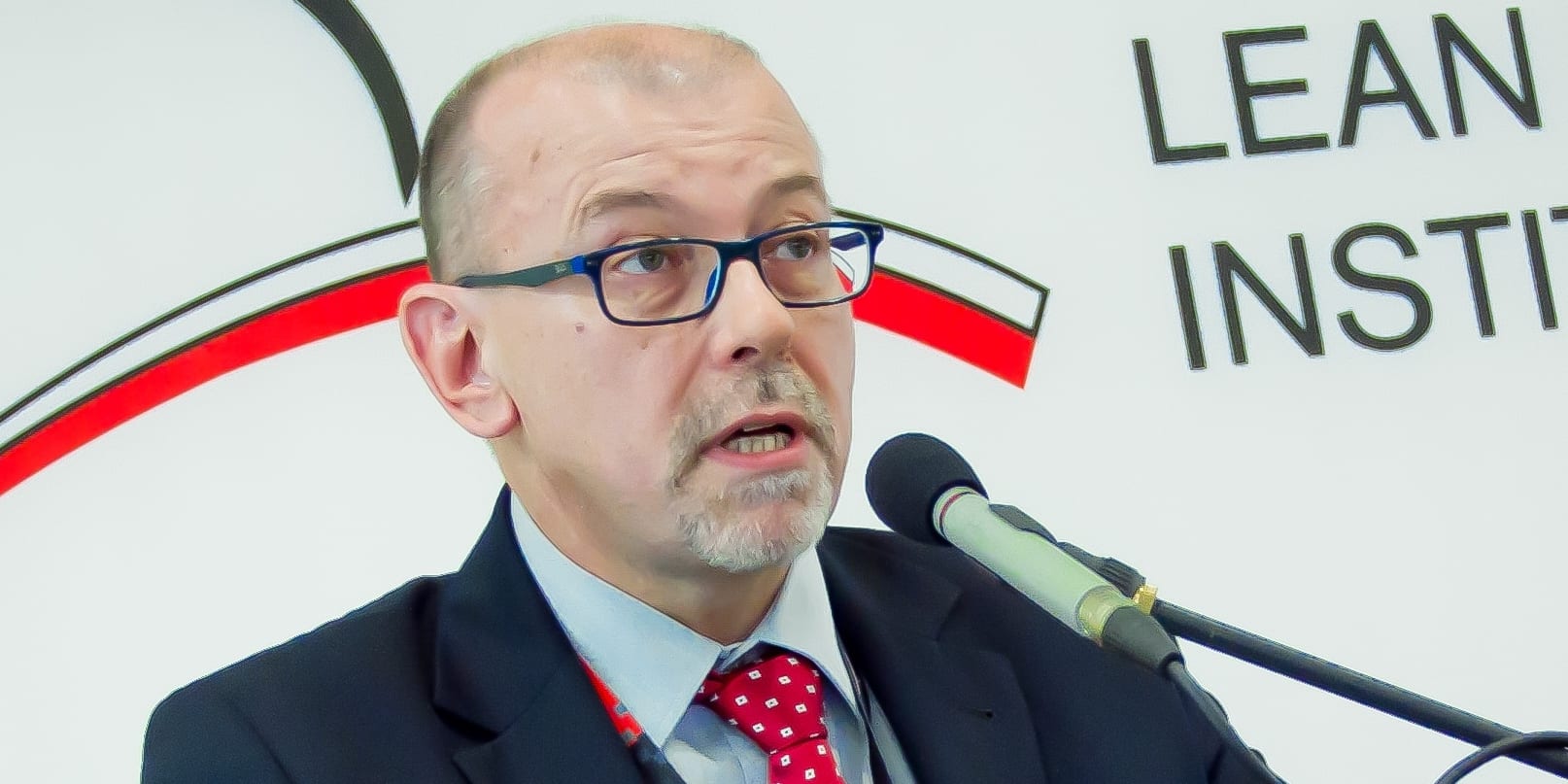
Lean thinking in 'Pole' position
GETTING TO KNOW US – We continue our series of interviews with Lean Global Network directors with a Q&A with another veteran of the global lean movement, Poland’s Tomasz Koch.
Interviewee: Tomasz Koch, President, Lean Enterprise Institute Polska
Interviewer: Roberto Priolo, Managing editor, Planet Lean
Roberto Priolo: When did you first encounter lean thinking?
Tomasz Koch: My first meaningful encounter with lean was through the academic world. I have taught at Wroclaw University of Technology for more than 30 years now, but in 1997 I had the opportunity to teach for a semester at Central Connecticut State University as a full-time visiting professor. One day, the then Dean of the School of Technology gave me a copy of Lean Thinking, around one year after the first edition had come out. I was amazed! Reading that book was a a-ha moment for me.
Another milestone came two years later, in 1999, when I visited the Center for Manufacturing at the University of Kentucky’s College of Engineering for one week. A couple of years earlier, they had launched a Lean Manufacturing Program. The proximity of Toyota’s Georgetown plant to the university couldn’t have been more noticeable – I even remember being shown an A3 (not that I knew what an A3 was back then) on how Toyota Motor Manufacturing Kentucky planned to help the University of Kentucky with the lean program they had just launched. That week, I attended a Lean Manufacturing Simulation workshop (based on the assembly of a circuit board) and I immediately knew that’s what I wanted back in Wroclaw. At the time, only a handful of companies were applying lean thinking in Poland (like Polish plants of Pratt & Whitney, Delphi and General Motors), and there was a huge potential in the country that I wanted to tap into. [Check out this paper that Tomasz and his coworkers wrote about the evolution of the lean movement in Poland over the years.]
When I first started to discuss the idea of bringing some elements of the Kentucky Lean Manufacturing Program to Wroclaw, my colleagues at the university didn’t think I was serious. But I was, and with my team we soon succeeded in this endeavor. We are still using that very simulation as part of one of our workshops!
RP: You played a very important role in introducing lean in Poland. How did you manage that?
TK: I was so passionate about it that I organized Poland’s first lean conference on June 6, 2000, hosted by the university. I invited people from a couple of companies in Poland to present their early lean experiences: Delphi, Pratt & Whitney, Stanley Fastening Systems, Magneti Marelli and Sauer-Danfoss. Representative of University of Kentucky’s Lean Manufacturing Program Dave MacDuffee was also speaker at that event. From that moment onwards, things started to happen very fast.
A few months later, my contacts at the University of Kentucky told me about a tool that I should learn about – value stream mapping. One of University of Kentucky Lean Program team members came to Wroclaw to teach us how to use it on the premises of Sauer-Danfoss plant, and I quickly realized we had to translate Learning to See into Polish so that more people could also learn to use this powerful method. So, I contacted John Shook and that’s how I learned about the Lean Enterprise Institute.
It was vitally important for my future lean journey that I had infected a few of my coworkers – Remigiusz Horbal, Robert Kagan and Tomasz Sobczyk – with the lean bug. Together, we are still running the Polish lean institute.
In 2002, LEI sent José Ferro (at the time, Lean Global Network didn’t exist and José was LEI’s international ambassador) to attend our second lean conference. We went to visit companies together and José concluded that there was a strong enough base in Poland to start an affiliate institute. That’s when the idea of creating Lean Enterprise Institute Polska first appeared (we eventually opened it in 2006). We published the Polish edition of Learning to See at the Wroclaw University of Technology in 2003 and, that same year, Jim Womack and Dan Jones joined our third lean summit.
Jim put me in contact with Marek Piatkowski, a former manager at Toyota Motor Manufacturing Canada, who visited us on a monthly basis and became our sensei for a couple of years – this was a period of crucial and very rapid development for our team, as we assisted several lean transformations in Poland together with Marek.
By this time, it was impossible to stop the spread of lean in Poland.
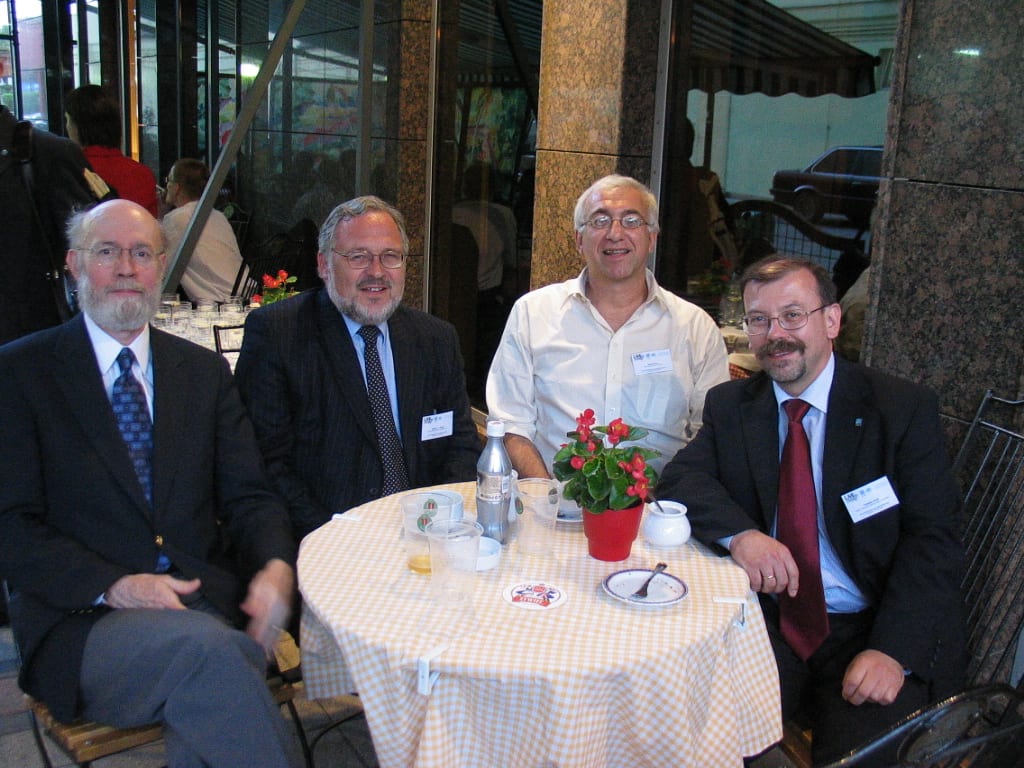
RP: You have witnessed the entire evolution of the Lean Global Network. How have you seen it change?
TK: LGN was founded in 2007, a couple of months after LEI Polska opened its doors. Jim Womack and Dan Jones’s idea had become a reality and, over the years, the network grew to include more and more institutes.
I have been serving in the Lean Global Network Executive Committee since 2014, directly supporting our Chairman John Shook and assisting with the development of the network. I think that the biggest change for the Lean Global Network came in 2015 (during our global meeting, which we hosted in our very own Wroclaw that year), when our regional strategies were launched as a way to try and spread lean thinking and practice around the world more effectively. Shortly thereafter, we introduced the current tier structure, which allows for more flexibility in the way we get more affiliates. We can now join forces with companies, individuals, universities, and other likeminded organizations. You no longer have to start an institute to be a part of LGN, and that is really what is fueling our growth currently – today, we are present in 31 countries.
We should be really proud of the difference we make in the world. Many of our institutes have projects with organizations, coaching them in their lean transformations, and are making great progress with them. We constantly generate new learning, a lot of which you can see published here on Planet Lean.
We are currently looking for new and better ways to support organizations. (We have had interesting conversations about this last month at our annual Board Meeting.) It is clear to us that it all starts with awareness, and that is why our focus on delivering public workshops, publishing books and organizing lean summits is still strong. However, we also realized that we can more directly contribute to bringing lean change about by assisting companies and individuals on their transformations. At LGN, we do so using the Lean Transformation Framework as a reference, because we believe that effective and sustainable change can only come from tackling each of its five dimensions.
RP: What are the benefits of being part of the Lean Global Network?
TK: Being a part of LGN is very important for us in Poland, for several reasons. The most important is the fact that we can learn from others. Seeing how our peers organize training, approach coaching companies or start to introduce lean to new areas is a big advantage for us.
As a network, we have a clear idea of where we are with lean in every corner of the world. Belonging to an international not-for-profit organization whose aim is to spread lean thinking and practice around the world makes us unique – and therefore stronger – in the Polish market. Belonging to the Lean Global Network has helped us to make a substantial contribution to the spread of lean in our country (through conferences, gemba-based workshops, books, articles and case studies, and of course assisting companies in their lean journeys). When I first started, our lean conference was the only one in the country, whereas there are now over 30 lean-related events each year!
RP: You have been running summits for nearly two decades. Does the old formula still work?
TK: We are having intense discussions about this in our institute, and we have reached the conclusion that we need to discover the next paradigm for lean summits. The old formula (a lot of case studies, foreign speakers, practitioners and authors) still works, but I don’t think it will for long. We need to think about how to deliver the content in a different way.
Another problem we will need to tackle is that, as much as we have tried to explain that’s not the way to go about creating change, people still expect to come to a summit and get the silver-bullet solution that will magically solve all their problems. It doesn’t work like that, of course, but that poses interesting questions on what sort of content we should look for and how we should share it at summits.
RP: What’s the state of lean in Poland at the moment?
TK: In manufacturing, lean is wide-spread. In fact, at our summit, the majority of participants are still from manufacturing companies, which surely has to do with the fact that Poland is still heavy on manufacturing compared to Western Europe. What’s certain is that we are getting more and more Polish-owned companies knocking on our door, whereas in the early years it was usually only plants belonging to international corporations. That’s great to see.
In non-manufacturing sectors, lean isn’t developing as fast. Part of the reason for this is that there are many improvement methodologies available to them. Many of these firms started with six sigma years ago, for example, and have more recently turned to approaches like agile, scrum, BPMN. I am confident they will soon realize why they need lean thinking in order to move forward.
RP: What is the Polish institute currently working on?
TK: We are currently helping several Polish companies to solve their business problems using lean thinking. We train hundreds of people each month on various lean methods and tools showing them best practices during visits to some 30 companies. We are currently busy designing our public lean workshop program for next year, knowing how important it is to keep up with the market and to adapt to changing customer needs.
Our R&D team has been working on connections between environmental and business aspects of the production process within the Maestri project co-funded by the EU. Here are two videos about two of the tools developed within the scope of this project: Eco Lean Management Board and Eco Orbit View. We are also developing lean Apps – a brand-new R&D project for us, which we consider crucial for our future success.
We are striving to publish more books in Polish. Our current goal is to release four titles a year! One of the most recent books we translated and published was The Work of Management by Jim Lancaster. Tracey and Ernie Richardson’s The Toyota Engagement Equation is coming out this week, and the next in the pipeline is Art Smalley’s book on Four Types of Problems. Since we breathed new air into the publishing value stream, we have experienced a dramatic increase in sales – which is very promising.
THE INTERVIEWEE
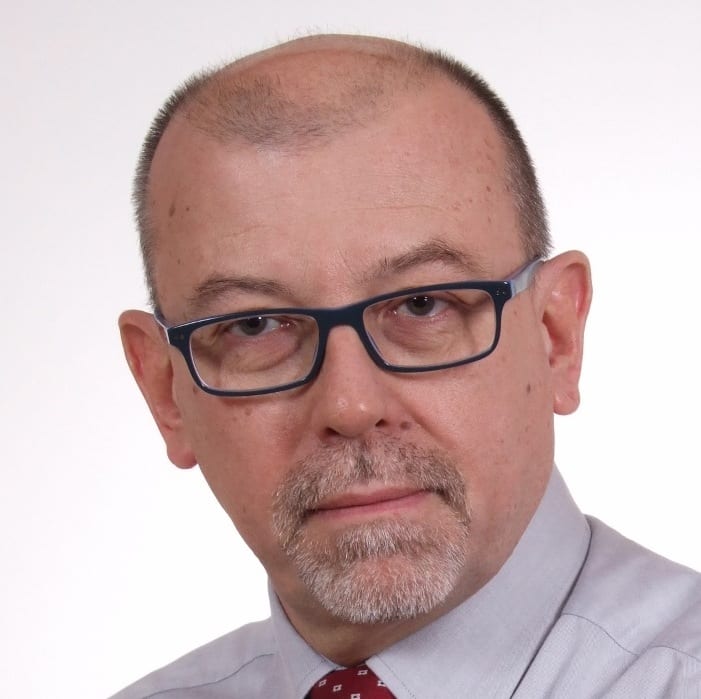
Read more
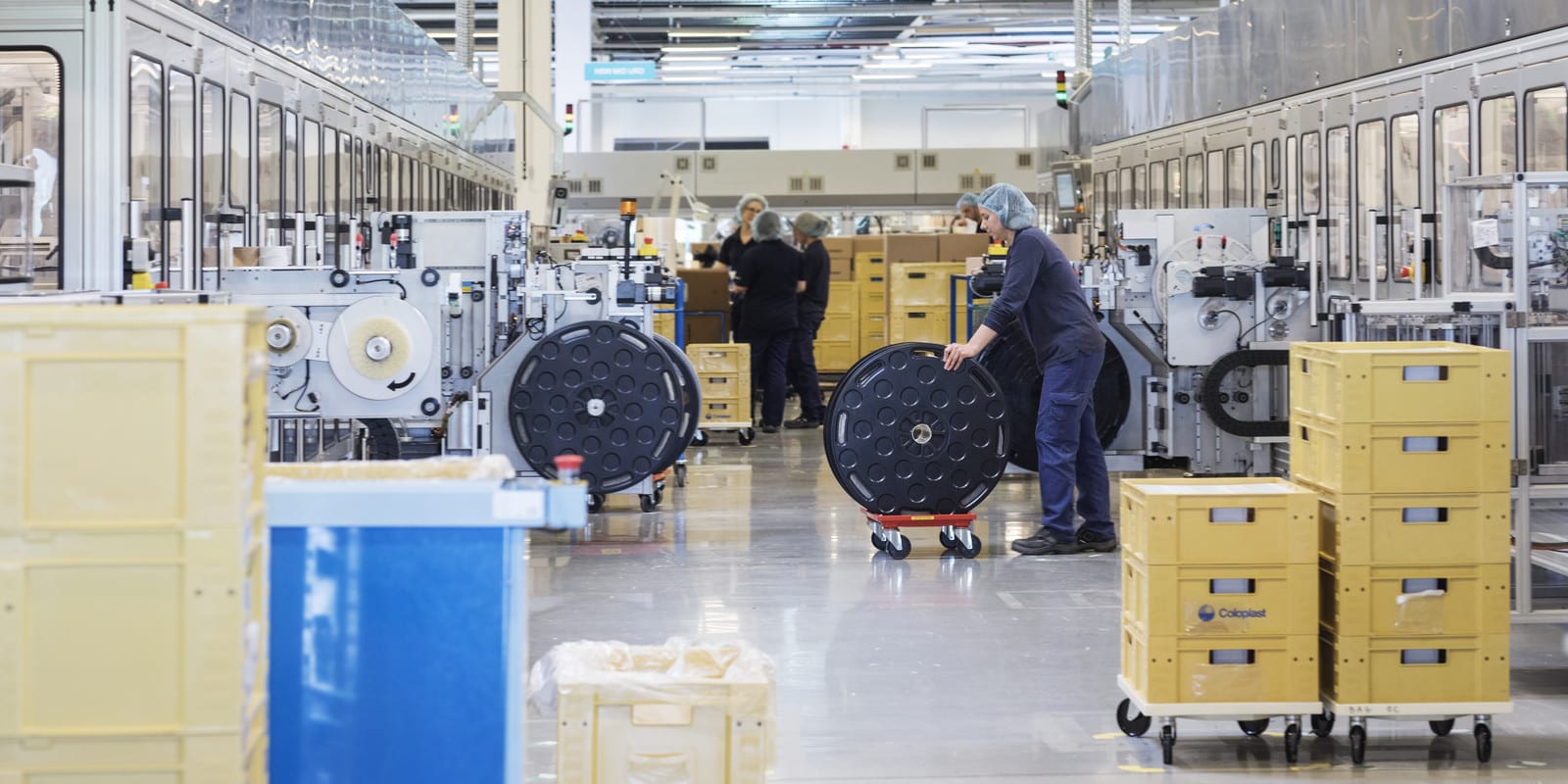
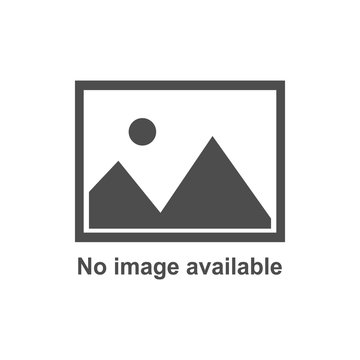
CASE STUDY – The author looks back at the impressive lean transformation of the Hungarian plant of Coloplast, a Danish company offering medical devices and services.
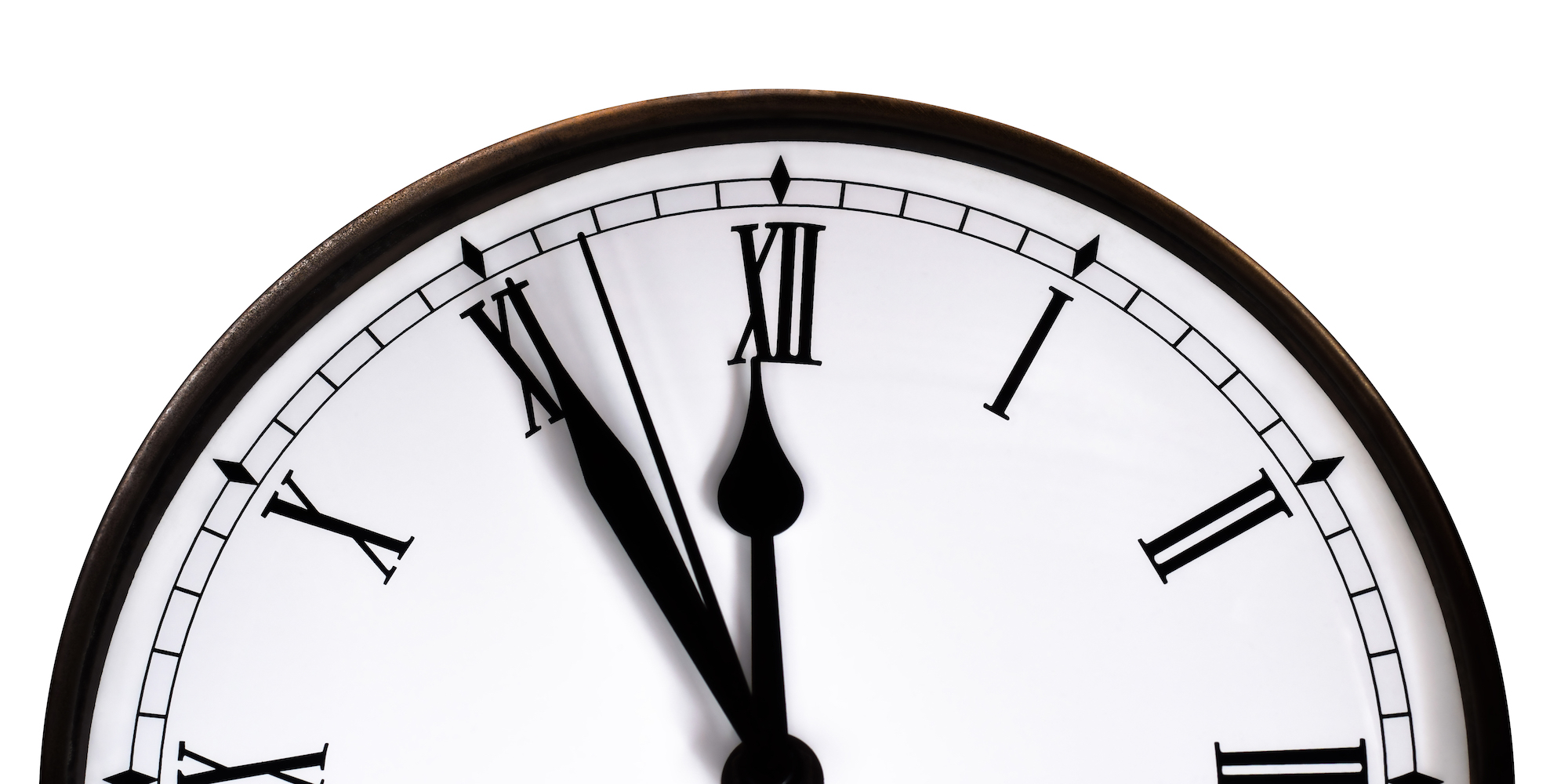
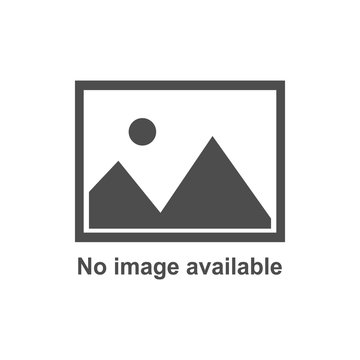
FEATURE – Freeing up beds is an age-old problem for hospitals. The medical area of this Catalan hospital group has found in lean a creative way to solve it.
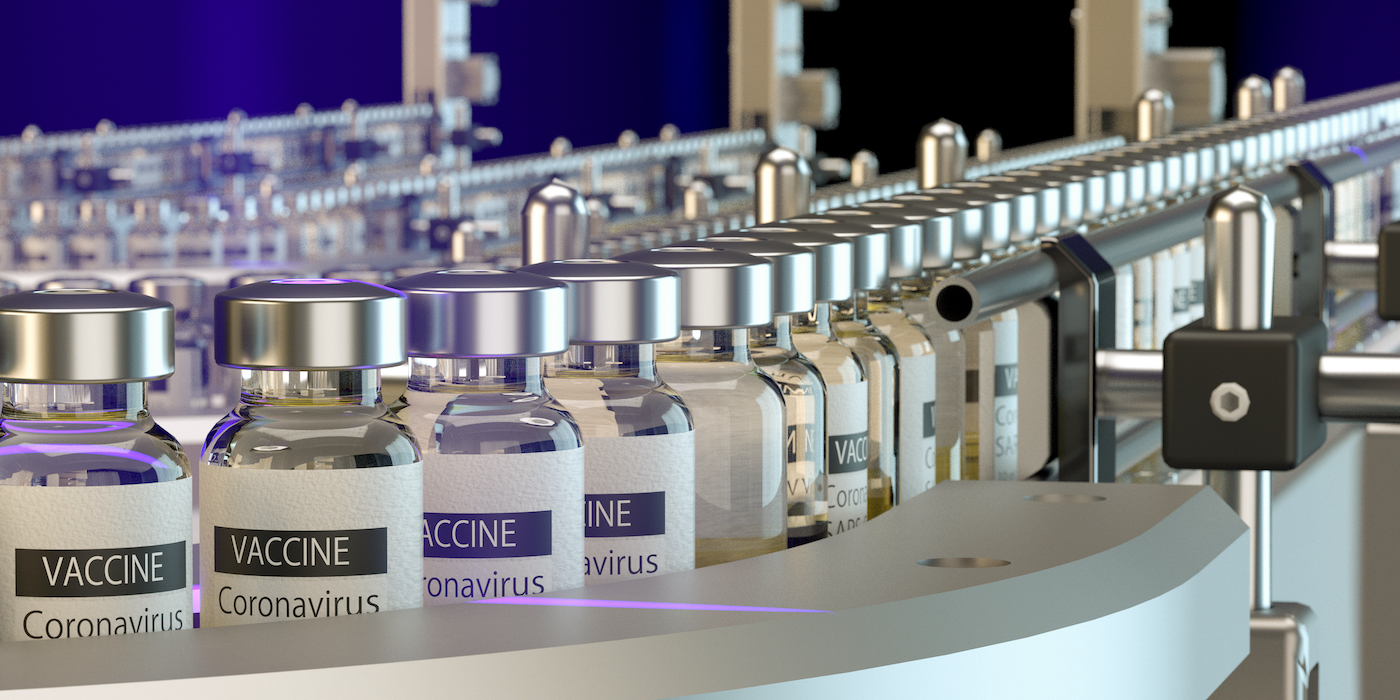
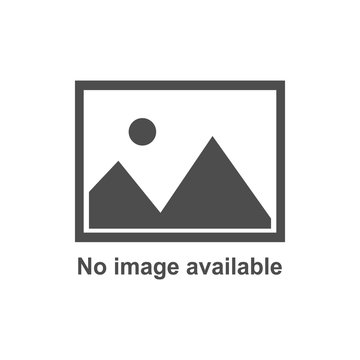
FEATURE – What does it take to meet the historic challenge of rapidly increasing the annual global vaccine capacity from 5 billion to 19 billion doses? And how could Lean Thinking help?
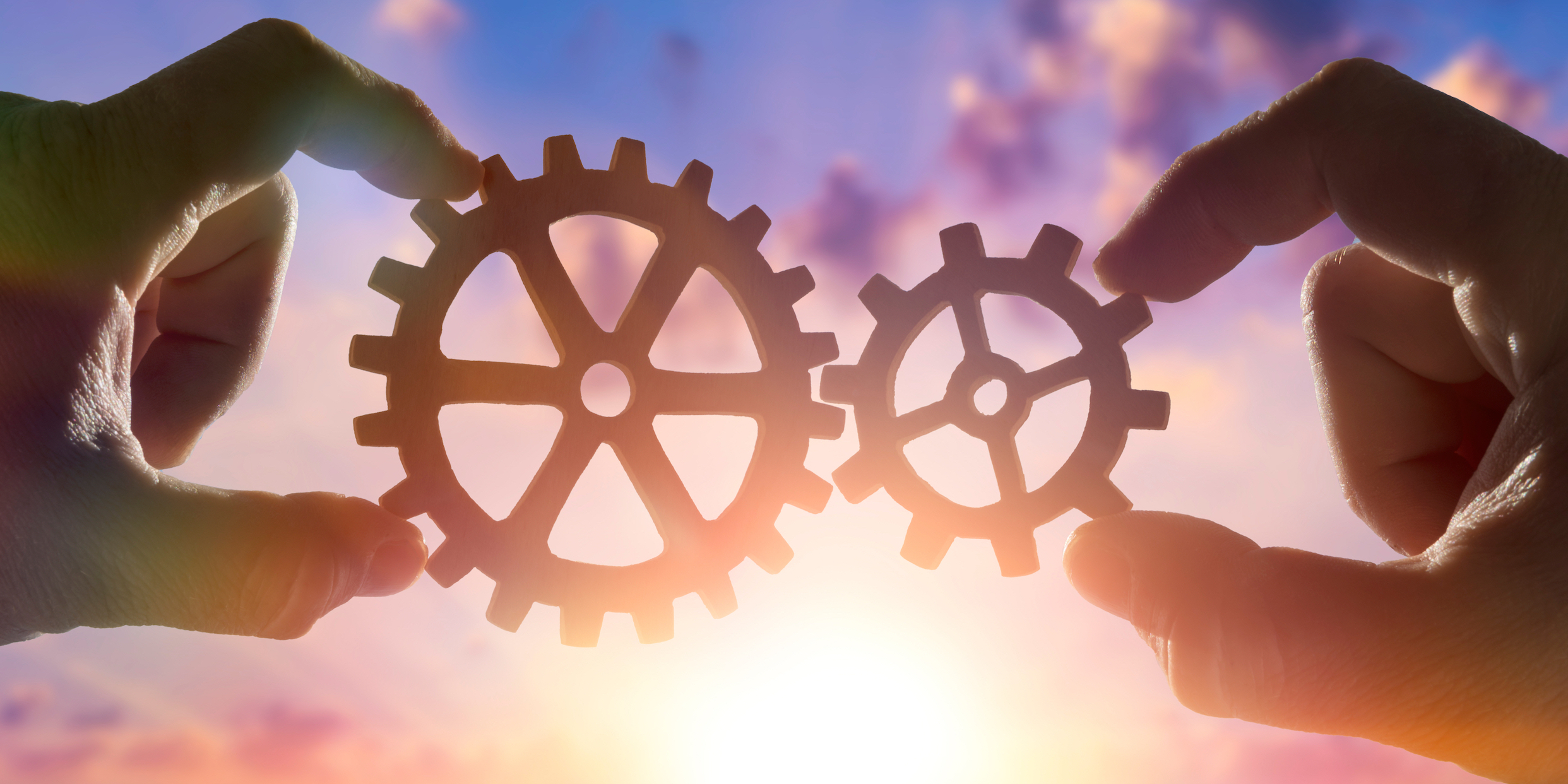
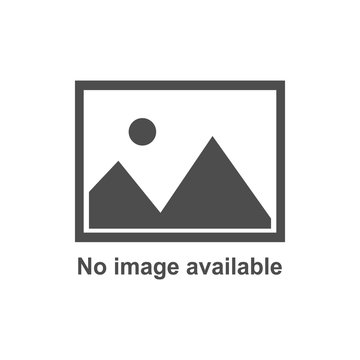
FEATURE – One of the things making lean thinking so hard to explain in general terms is its dual nature as both an organizational and managerial approach. The authors explain how to handle this tension.