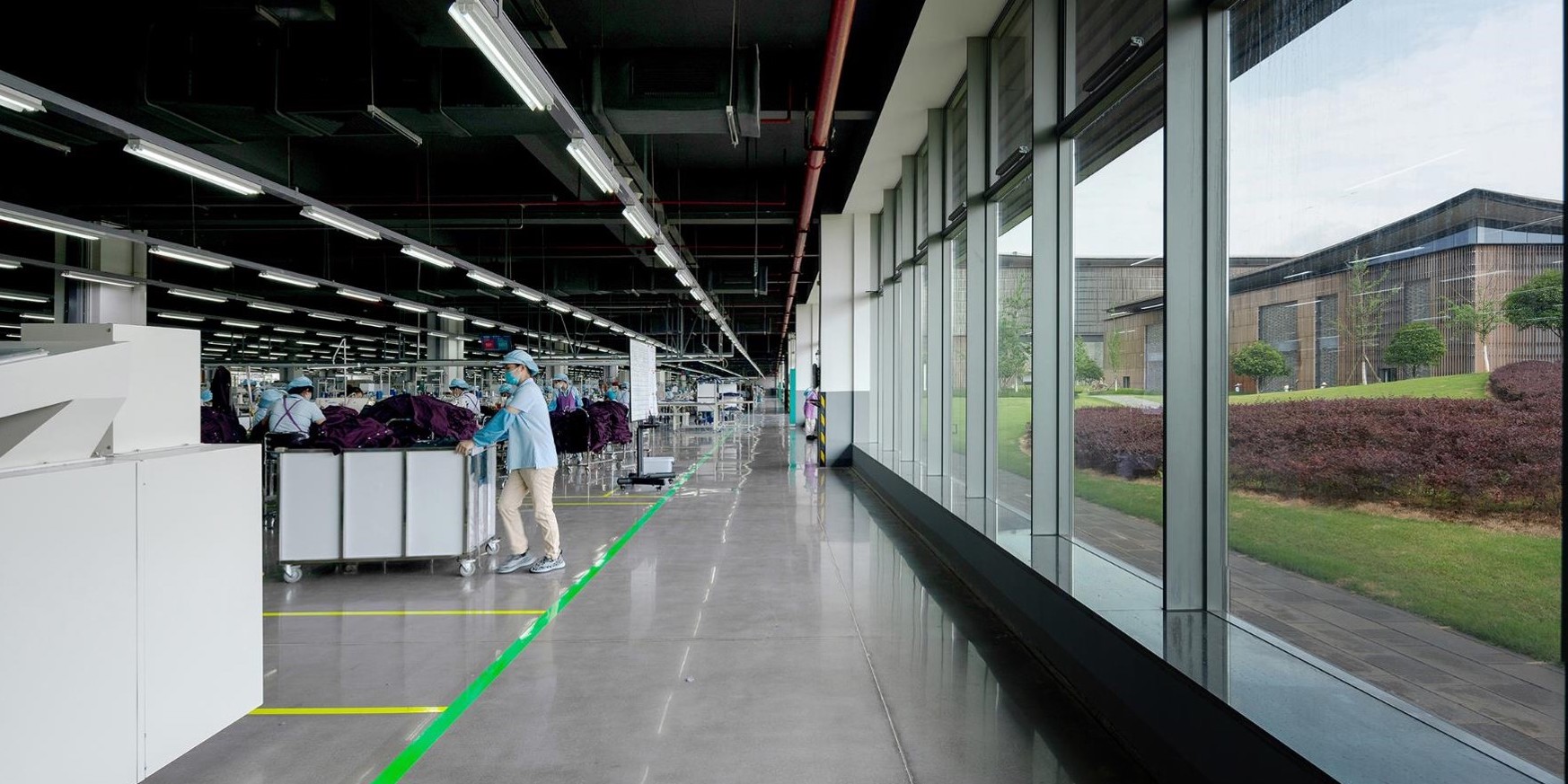
Smooth as silk
CASE STUDY – An Esquel factory in GuiLin, China injected lean principles and practices into its processes to become more efficient and environmentally-friendly.
Words: Marcus Chao, President, Lean Enterprise China
The textile industry has undergone deep scrutiny and several changes in recent years. The pressure to reduce costs has been relentless, global competition is growing fiercer by the day, and charges of labor exploitation and unfair practices are rampant. As new revolutionary strategies of retailers such as Sara or Fast Retailing continue to disrupt the market, garment suppliers globally have also struggled to keep up.
Global textile and apparel manufacturer Esquel is one garment producer that has risen to these many challenges by embracing lean principles and practices in an exemplary fashion (pun intended). The company, headquartered in Hong Kong, has an integrated operation from cotton to yarn and supplied over 100 million shirts to global brands in 2019.
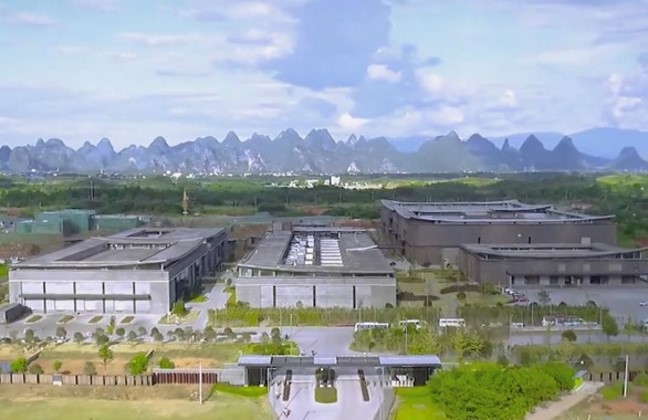
To learn how Esquel is faring, last year John Shook and I visited its Integral Center in GuiLin, China.
The company’s owner, Margie Yang, has long pursued her dream to turn the traditional garment industry into a lean manufacturing system in order to relieve workers from daily low value-added work and make Esquel an environmentally-friendly operation moving ever closer to zero emission. This is a noble cause that every lean practitioner should support wholeheartedly, which why Lean Enterprise China (LEC) is committed to support Esquel’s transformation.
With the objective of bringing together lean and green, LEC asked our lean sensei Joe Lee – a Toyota Taiwan veteran with 25 years of hands-on experience, to guide the Esquel team in GuiLin in its transformation from a traditional garment operation to a lean one. Joe’s approach is to take local management teams to gemba and ask them questions encouraging them to think in terms of flow and pull.
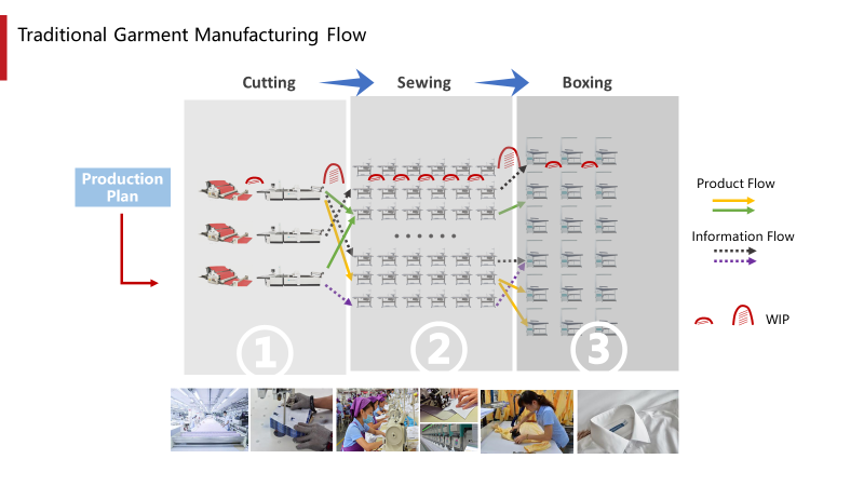
Traditionally, textile operations are composed of three main steps: cutting, sewing, and boxing. The old GuiLin garment factory was designed in process villages (island layout) with all cutting equipment and operations concentrated in one area. The same was true for sewing and boxing areas. These siloes caused the well-known problems of stagnation in the “cut to box” flow, high defect rates, long lead-times, and high WIP inventory.
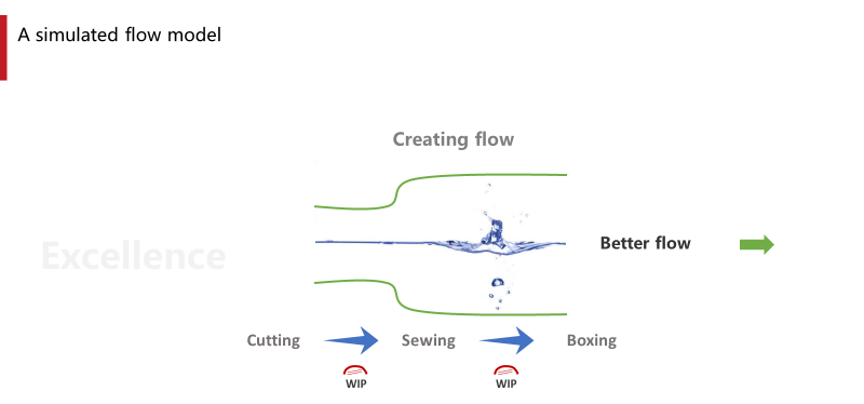
With the old GuiLin factory targeted for closure in April 2019, the team had a mere nine months to prepare for the move to the new Integral Center. With the encouragement of Joe Lee, the local team set the goal of leaving old operation issues behind and starting from scratch in the new factory with a flow and pull process in place. Therefore, they decided to implement flow in the boxing area and then pull from sewing and cutting, step by step.
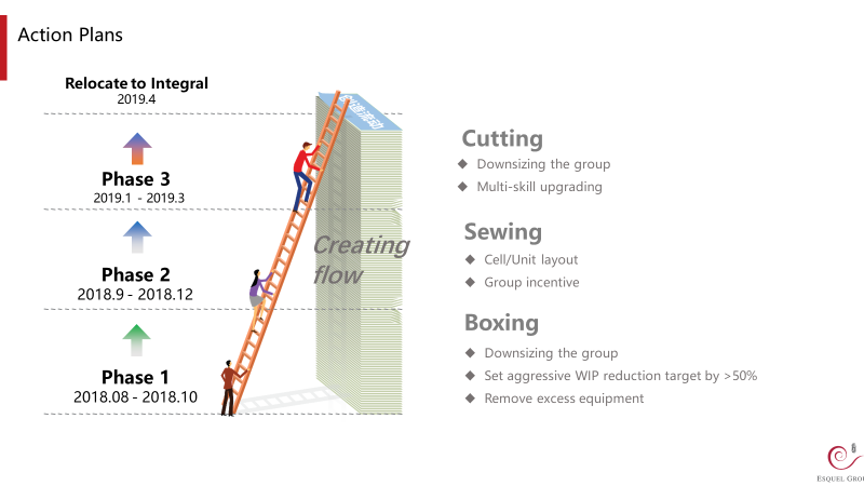
In the first phase of the project, the team streamlined the boxing processes and made an experiment to reorganize a 25-strong team into three smaller groups of seven people each to ensure better communication and work coordination. The team was challenged and empowered to remove excess equipment and change the layout of the working area to improve the flow and, within just eight weeks, they achieved a 50% reduction in WIP. Not only did this improve performance dramatically, but it also boosted the team’s confidence. So, they decided to implement similar changes across the boxing area to align every line with the sewing area.
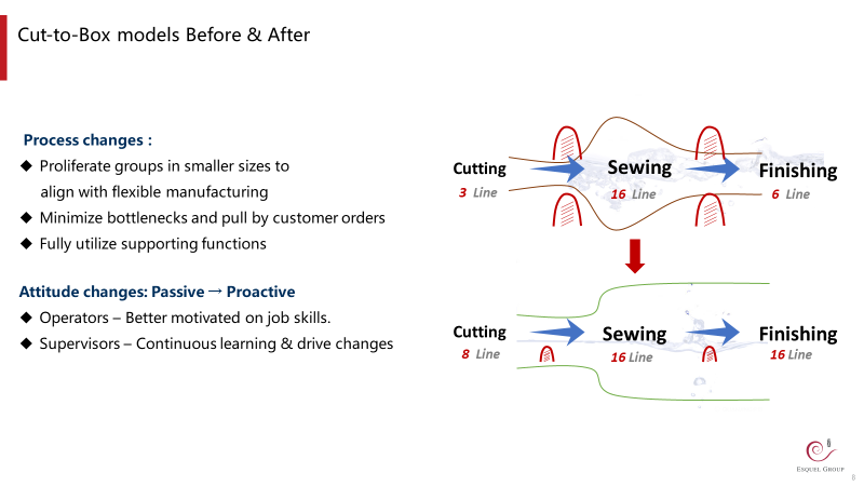
In the second phase, the team implemented a U-shaped layout in the sewing area and, to shorten the assembly line, rearranged the seating layout from one side to back-to-back. They consolidated quality, process and maintenance engineers into one core support team to respond to any andon calls coming from assembly workers and set up production visual analysis boards to manage current performance against hourly targets. The team also redesigned the “piece-rate pay system” and made it a combination of team performance and salary system to better compensate people for their work.
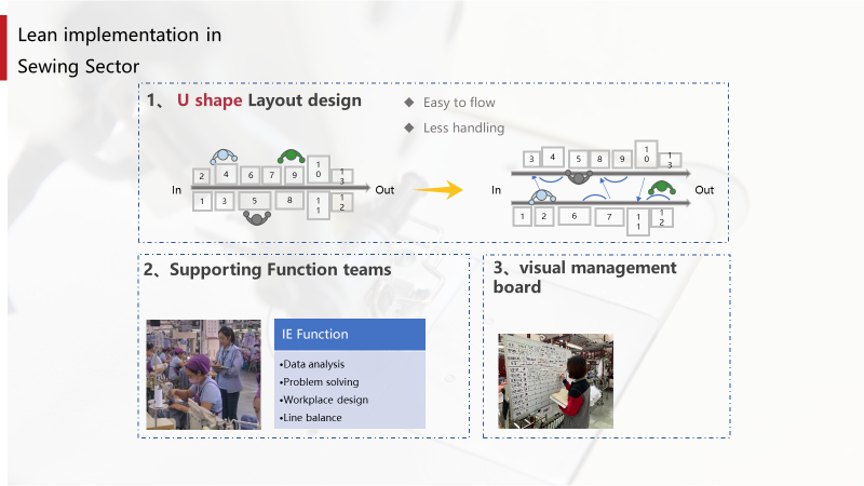
Previously, the cutting area would cut materials based on its own determinations, which resulted in a large amount of work-in-progress accumulating right before the sewing area. Previous efforts to change the system had failed. Following the lean improvement, the sewing area is pulling materials from the cutting operation based on what is needed exactly in its high-mix low-volume production schedule. Similarly, the large team was broken down into smaller groups to better align with the requirements of the sewing area. Since cutting is mostly performed by automated machines, team members are now expected to learn multiple skills so that they are able to cover for one another, which has improved both performance and motivation.
The local management team also added the flexible manufacturing concept to the new factory layout, by setting up eight mini factories instead of one. Each unit features its own cut, sew and box operations enabling them to take on low-volume high-mix orders from customers. All three phases were successfully carried out before the move. Lean coach Joe Lee was happy to see the team accomplish even more than they had committed to.
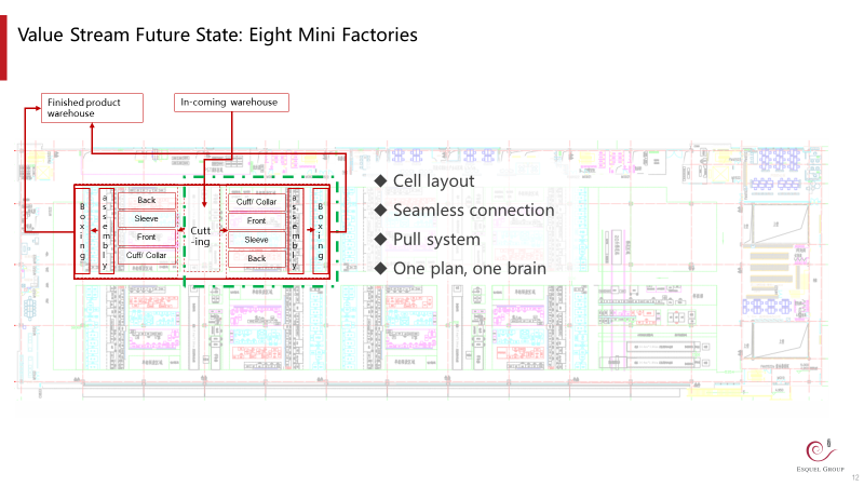
In describing the changes in the factory, Joe Lee told me that, in the beginning, as he walked around the factory he could see WIP but no workers or table tops, whereas now he can see both. It is important to observe the worker’s face and the top of the table: the former gives you a sense of employee satisfaction, the latter reveals any problems in the process. Such a simple way to take the pulse of the flow and pull operation!
As far as performance improvements go, the team achieved four major objectives:
- WIP was reduced by 60%;
- Lead-time was reduced from 15 days to 5 days;
- The average employee income increased by 19%;
- Annual cost saving: RMB 3 million ($430k)
Making employees more conscious of the importance of high quality led to several intangible but important results, including a more cohesive team spirit as well as stronger skillset within the teams (which enhances the company’s overall competitiveness).
Despite these impressive improvements, this is only the beginning of the Esquel Integral Center’s lean journey. The team has recently built a daily Walk Around Review (WAR) – or gemba walk system – to identify issues and to take quick corrective actions. As continuous improvement is being pursued at all times by team members, people are happy to embrace their leader’s dream to transform the traditional garment manufacturing environment into a vibrant lean system.
In terms of environmental sustainability, Esquel has decided to prioritize the reduction of its energy and water consumption – something it’s been focusing on for well over a decade now. The company wants to influence employees, surrounding communities, suppliers, and customers and helped them to see that green is the way forward. They started by asking employees to save water and energy in their daily work (for instance, by immediately reporting any faucets leaking or closing windows when the AC is on), which went a long way towards showing that every single individual contributes to the group’s collective destiny. This effort has contributed to the company achieving its goal of a 48% energy consumption saving and 66% water usage reduction over the past 14 years. More importantly, the over 40,000 Esquel employees are now taking the green message to their families and communities (to make the world a better place, we all have our role to play).
Esquel is committed to applying innovation to effectively minimize dye consumption and to use alternative energy to reduce its footprint. Its goal is to become a zero-emission business.
As far as we at LEC are concerned, we know that lean applies to any sort of human endeavor (not just manufacturing) and I must say that we are deeply honored to work with Esquel on their pursuit of sustainability model rooted in Lean Thinking. As Esquel’s Vice Chairwoman Teresa Yang said: “At Esquel we not only make shirts, we make a difference!”
A COMMENT BY JOHN SHOOK
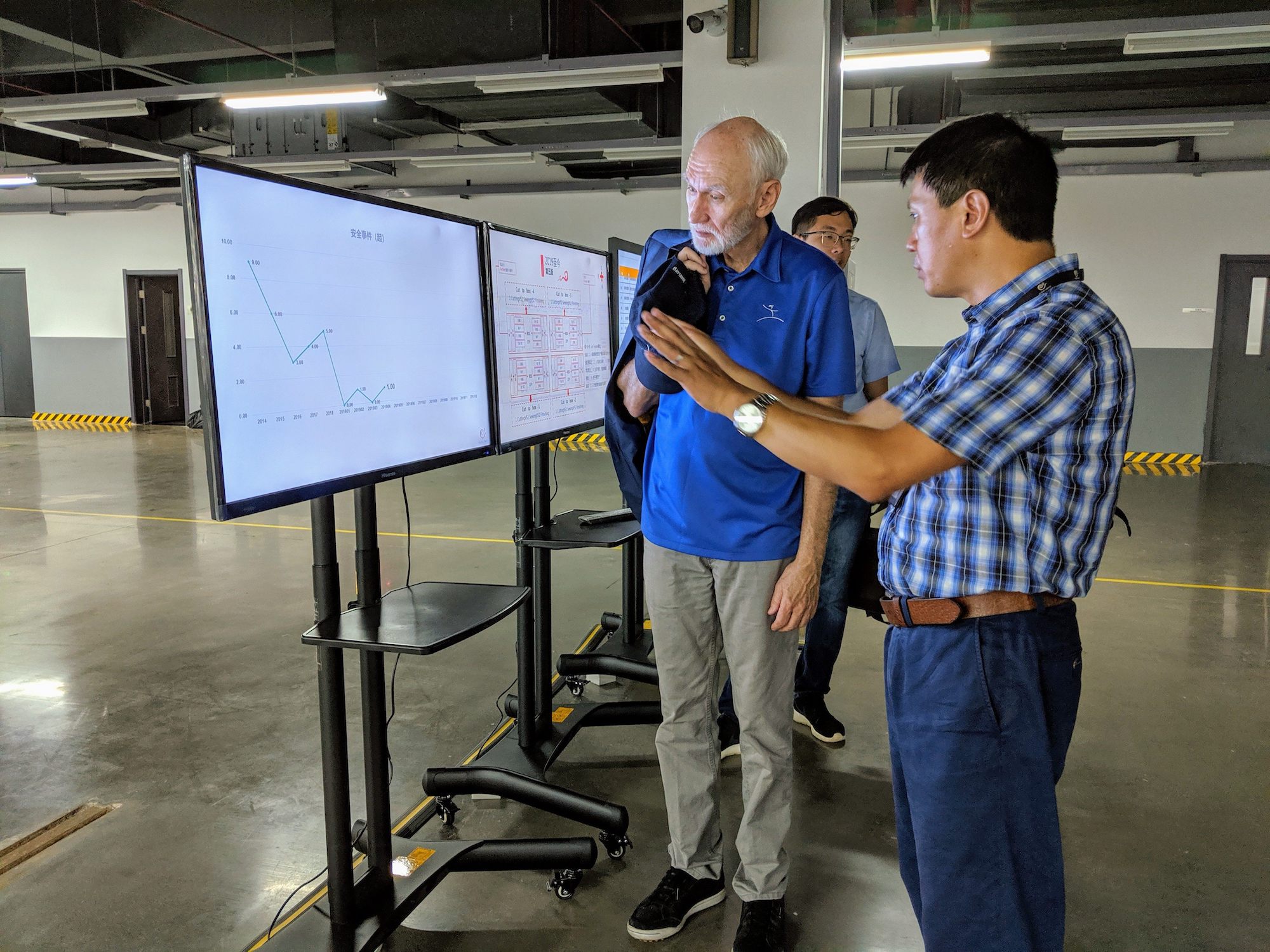
As Marcus reports, our observations at Esquel Guilin revealed sustained efforts and results to transform the company’s manufacturing operations but to also create an admirable enterprise in all respects. We were impressed with the efforts to provide safe and inviting working conditions within a site design that was highly conscious of environmental impact and a commendable effort to blend well with the local natural environment resulting in a design that reflected the natural beauty the GuiLin region is known around the world for. GuiLin is a natural wonderland with its ubiquitous misty mountains made famous through countless Chinese paintings and ink drawings. If you ever wondered why Chinese landscape paintings look like that, it is because the landscape actually looks like this. And it is just a few kilometers from the Esquel site.
THE AUTHOR
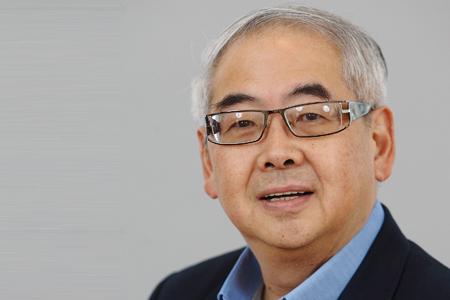
Read more
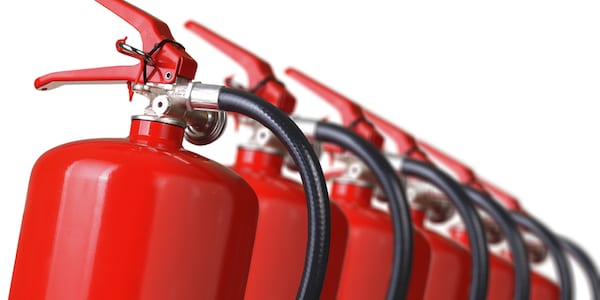
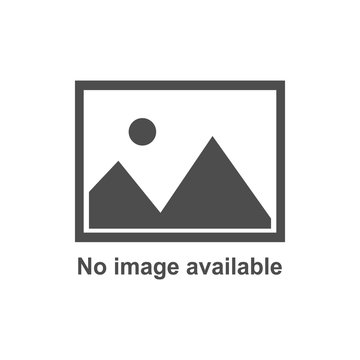
INTERVIEW - Eric Ethington shares what he has learned about lean thinking implementations during his 30-year career holding positions at General Motors, Delphi and Textron.
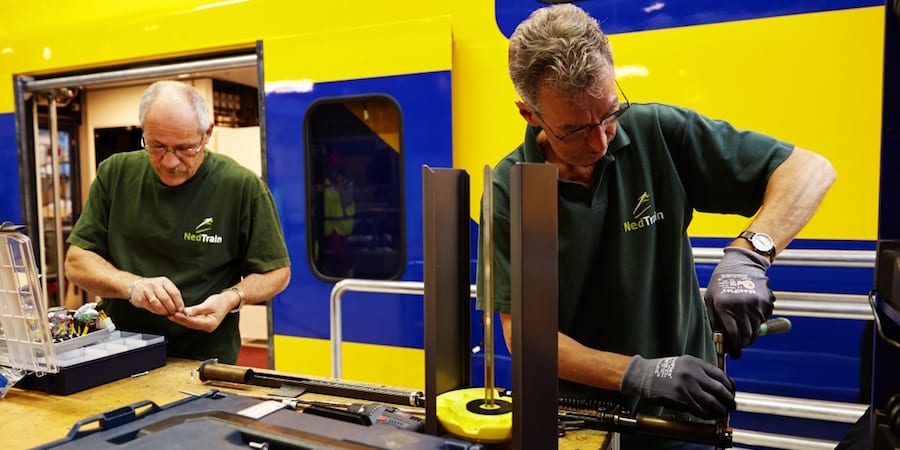
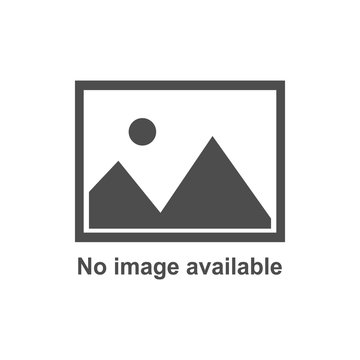
FEATURE – Faced with long lead-times to hire new people and with tens of millions paid in sick leave every year, the HR department of Dutch railway operator NS has turned to lean thinking to set them on the right track for the future.
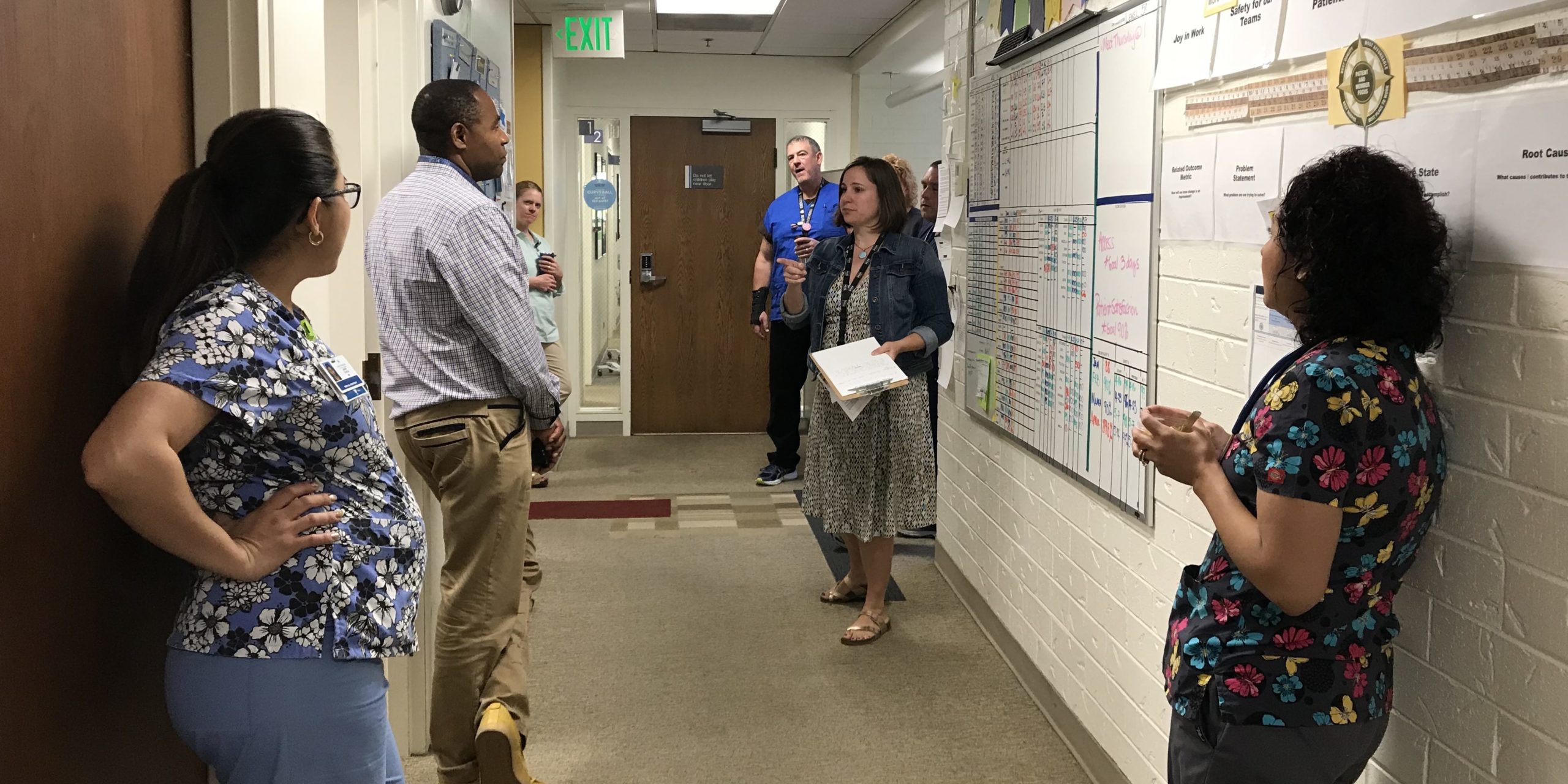
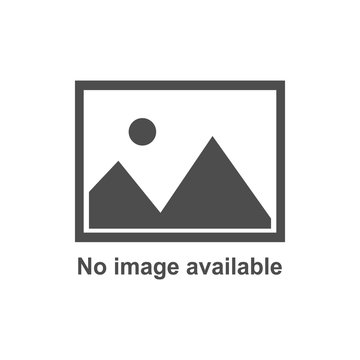
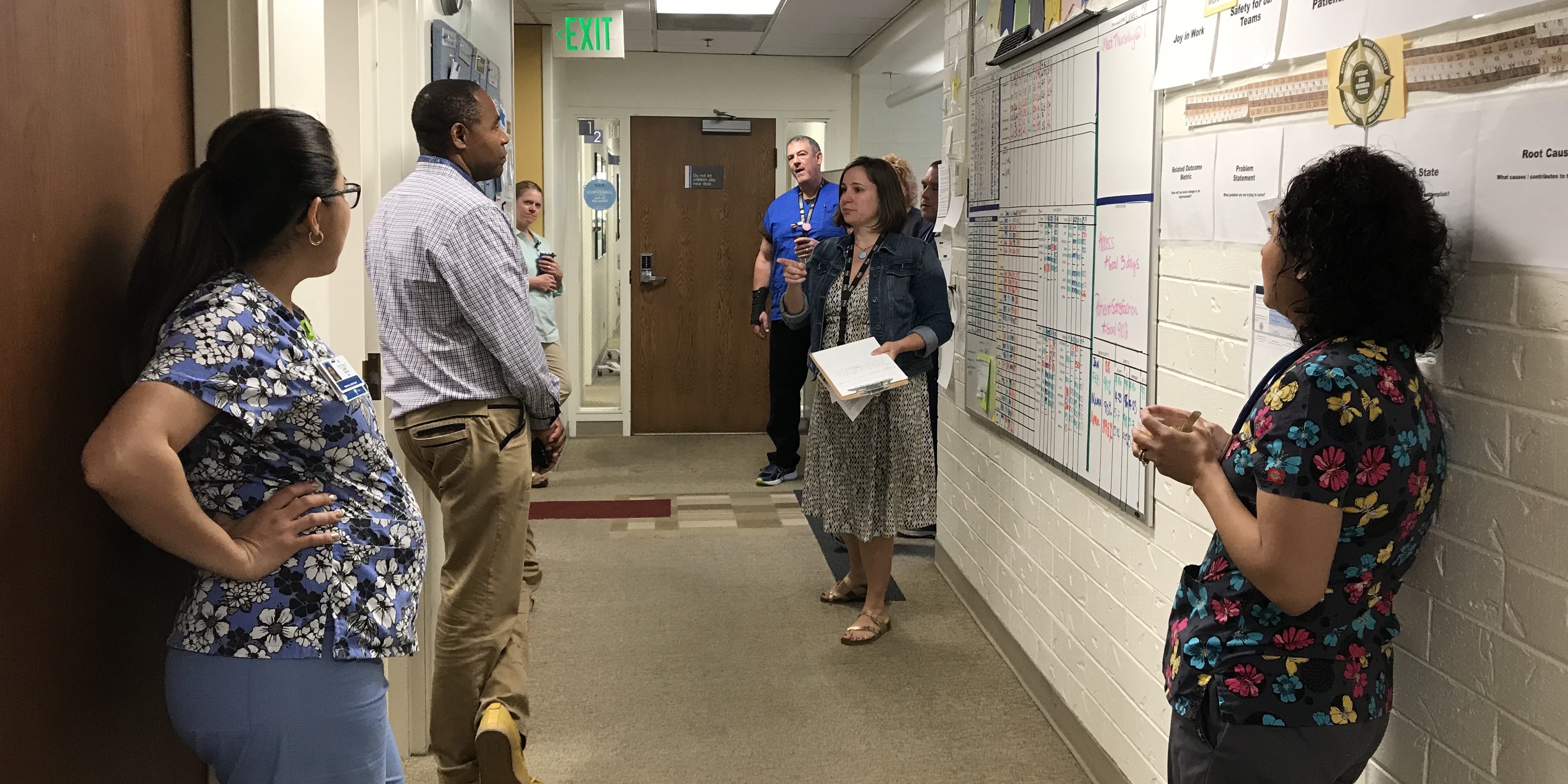
CASE STUDY – A physician tells PL the story of how the East Denver Medical Office became a catalyst for the lean transformation at Colorado Permanente Medical Group.
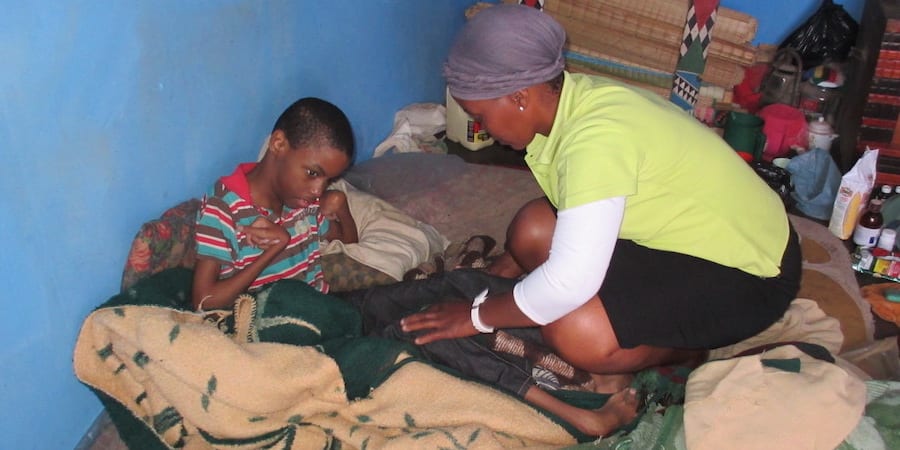
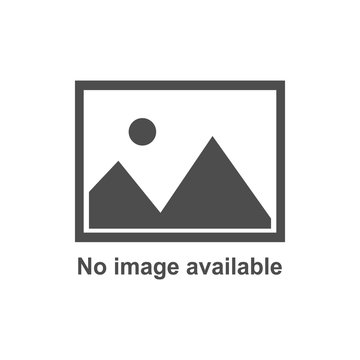
FEATURE – At Malamulele Onward in Johannesburg, a do-it-yourself lean transformation is increasing the impact the nonprofit organization is having on South African children living with cerebral palsy.