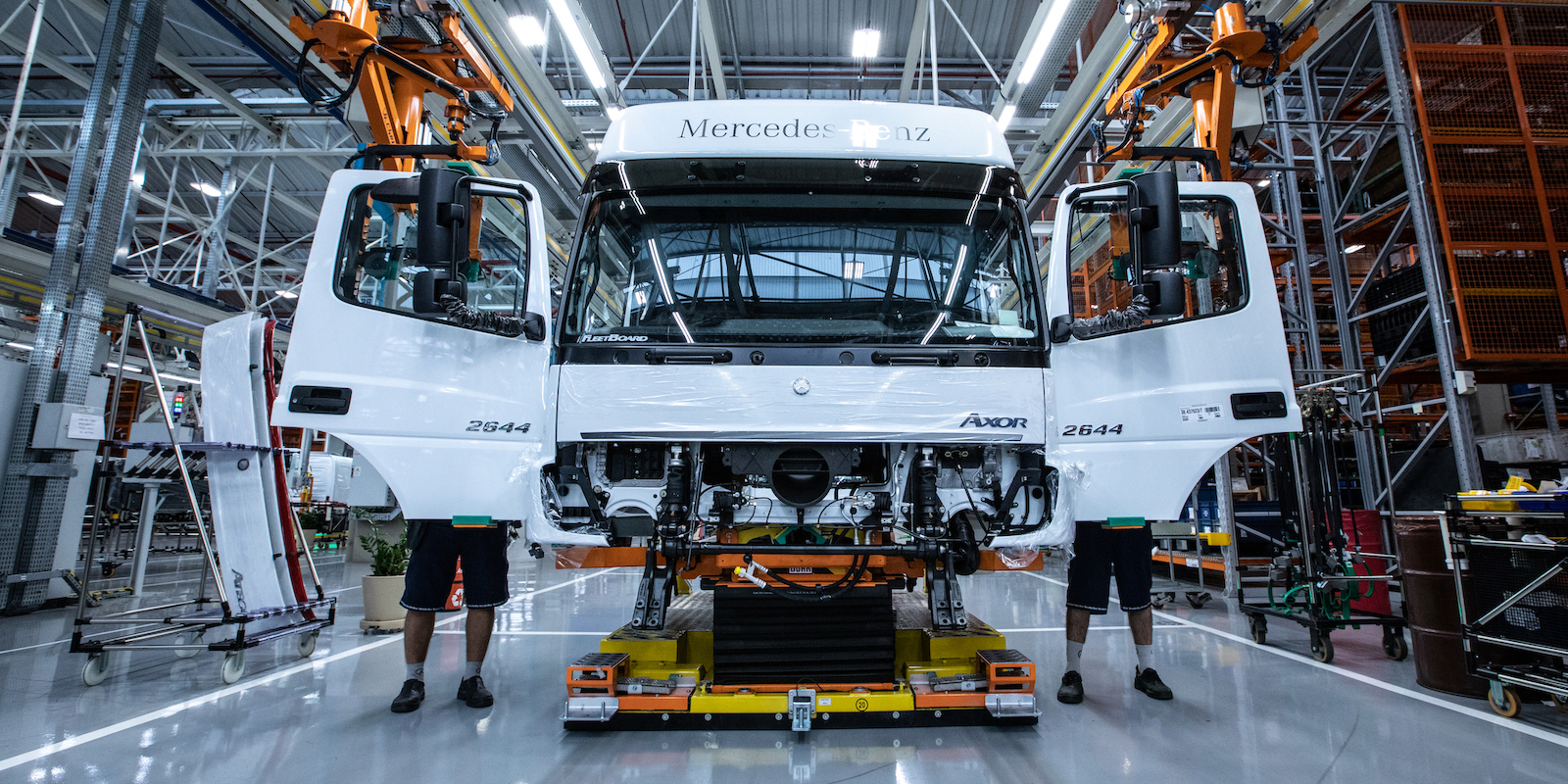
Bringing lean to the people
CASE STUDY – This article briefly outlines the different stages of the lean transformation at Mercedes Benz Brazil, as the company looked for the best approach to engage everyone in continuous improvement.
Words: Vagner Agostinho Junior, Operational Excellence Manager and Lean Coach, Mercedes Benz do Brasil
The manufacture of trucks and buses has been at the heart of our work at Mercedes Benz Brazil since the company opened its first factory in the country – in São Bernardo do Campo, near São Paulo – in 1956. Over time, as our brand gained greater recognition in Brazil and in the rest of the world, we increased our portfolio of products and services.
Today, Mercedes Benz Brazil has four factories across the country (São Bernardo do Campo, Juiz de Fora, Campinas, and Iracemapolis), producing trucks, bus chassis, powerpack and premium cars and employing over 10,000 people.
Trucks and buses represent most of our business, and these segments are very dependent on Brazil's overall economic situation. Because of the recession that the country has experienced in the past few years, we had to seek cost savings in our operations. To do that, we decided to embrace lean thinking.
Lean thinking has been around at our company since the early 1990s, when we hired outside consultants and introduced the practice of production kaizens. After that, a central Lean Department was created (today it’s called Continuous Improvement Office). In those early years, however, it focused too much on lean compliance audits, which eventually caused lean to lose credibility.
A first turning point came in 2011, when headquarters introduced in Brazil an international program for developing Lean Consultants. For those, like me, who participated in it, the qualification program was a fantastic learning opportunity. I was a warehouse supervisor when I started, but as I worked on improvement projects in machining, assembly, logistics, maintenance, etc, I learned a lot more about the company. I eventually became a manager and, around three years ago, I joined the CI Office team. Although it was a high-quality training program, the potential for transformation and results was limited, because the lean knowledge was restricted to only a few highly qualified individuals.
Having learned from our experience, in 2017 we developed and introduced the Continuous Improvement Framework (CI Framework) to represent and coordinate the many activities we had already put in place. This was the second, and most important turning point in our lean transformation. The Framework has a clear strategy: business excellence (“why”), achieved through process improvement (“what”) which is done through the development of people (“how”). It’s our own version of the TPS house, and it has lean thinking as its base.
Better structuring our improvement work showed us where the blind spots were. For example, we learned that the qualification program was too big to “go viral” in the organization and that it was not engaging everyone in continuous improvement. We realized we had to find a way to make our improvement work more inclusive, to make it everybody’s responsibility. To do so, we created the figure of the Lean Specialist, the Kaizen Driver and we introduced the Ideas Factory (I will explain them shortly).
The goal of the CI Framework is to develop a large number of people in the techniques and mindset of continuous improvement to solve various types of problems (from simple to complicated) at all levels of the organization. This is done through training programs tailored to all audiences, from the operational level to the leadership, in both production and administrative areas.
The key strategic element of this new approach is the decentralization of lean knowledge: the small team at the CI Office (five coaches and consultants) only coordinates the program strategy and people development, but it comes down to each and every person at Mercedes Benz Brazil to spread the lean culture across the business and make improvements. The CI Framework is what truly brought lean thinking to our people!
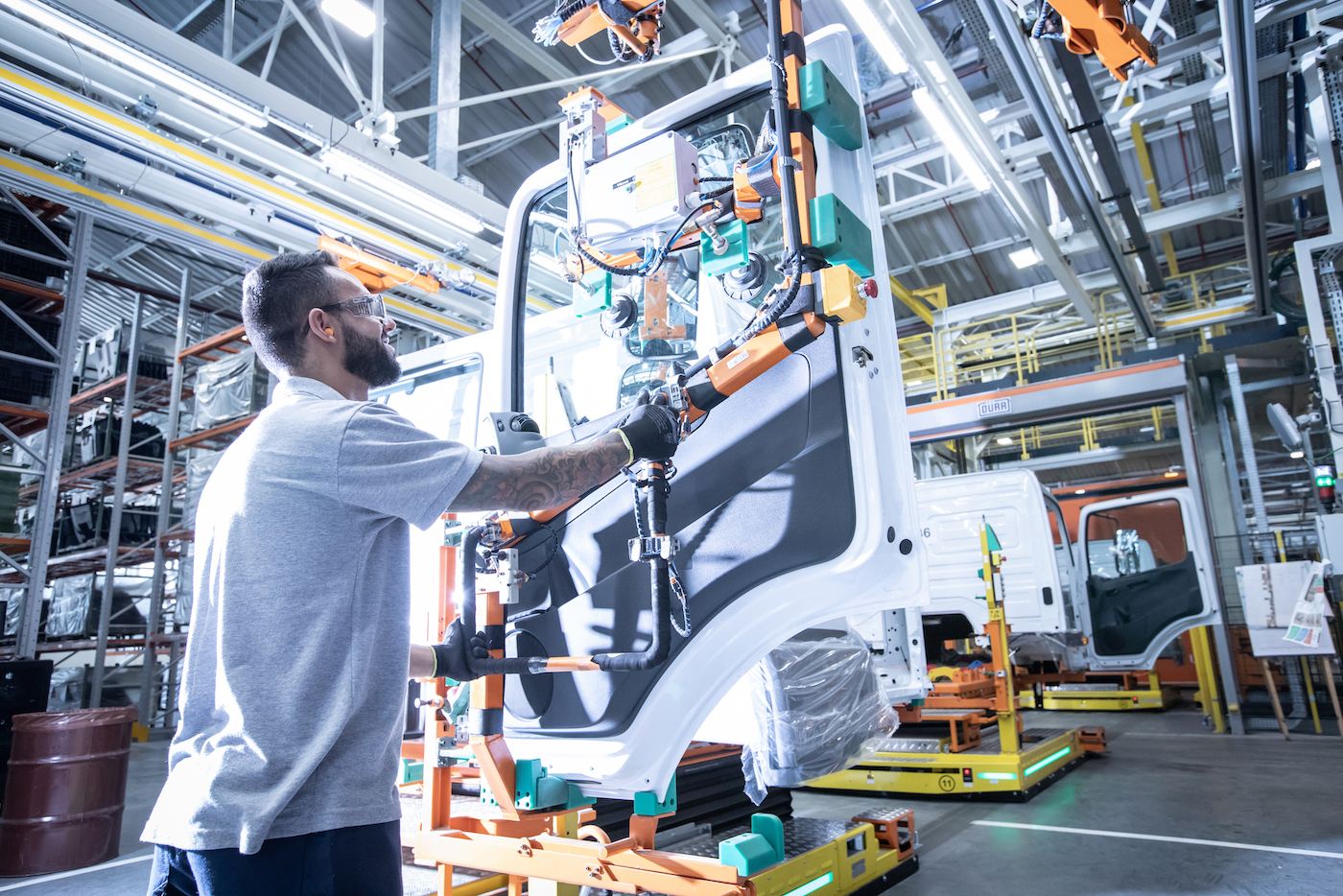
WHAT WE DID, AND HOW
As mentioned, the CI Framework is represented as a house, whose pillars (the What and How) are people development and process improvement:
- Capability development at Mercedes Benz Brazil is brought to life by Lean Career, a five-level development program. Each level has its own target audience and focuses on solving a specific type of problem. To take part in the program, trainees leave their role for a time. In true lean tradition, the training program consists of 10-15% theoretical content and 85-90% practical. Once the training is completed, the person returns to his or her original role as a lean transformation agent in his or her department. They will eventually be invited to undertake projects in other departments, which is how we ensure cross-fertilization. Career Lean has five levels of development: a) Lean Basics (4-8h), theoretical content on lean concepts available to all employees; b) Kaizen Driver (2 weeks), theory as well as the completion of one kaizen; c) Lean Specialist with focus on production and administrative areas (6-12 weeks), consisting of theory as well as the completion of three kaizens in different areas or around different problems; d) Lean Consultant with a focus on production and administrative areas and on project management (12 months), consisting of theory as well as the completion of four three-month projects; and e) Lean Coach, an advanced training program of up to 24 months that adds to the consultants some behavioral people management and coaching skills, allowing them to train all other training levels. Lean Career is coordinated by the CI Office, which works in partnership with all business areas. We have offered 25,000 hours of lean training yearly, for the past two years.
- To improve our processes, we follow different approaches based on the type of problem we need to solve. The Ideas Factory, for example, is a corporate program for the implementation of ideas by the employees themselves that aims to foster participation and engagement, discover talent and develop people’s capabilities. Kaizens are projects that last from one to three weeks, conducted by Kaizen drivers or Specialists. They rely on the PDCA methodology to solve simple and moderate problems. Finally, Lean Projects, with a duration of one to three months, are managed by our Lean Consultants and are suitable for medium- and high-complexity problems. Kaizens and Lean Projects are the CI activities that generate savings for Mercedes-Benz Brazil, but we also rely on them to develop our teams. Every year, we create a roadmap of initiatives. These are then evaluated and prioritized (we look at complexity, necessary and available resources, and earning potential) to allocate lean professionals to each project.
We believe that these two pillars underpin a continuous cycle of improvement and people development, whose aim is to spread lean thinking throughout the organization. To keep supporting this, we have set an ambitious goal for ourselves to greatly increase the number of professionals trained in continuous improvement by the year 2022 (in some cases, like our Lean Specialists, more than doubling their number.)
The results we have achieved in the past two years thanks to the CI Framework are proof that this is the right approach for us when it comes to our lean transformation. Not only have we been able to achieve a 10% to 20% reduction in HPU (Hour per Unit) in manufacturing, but it is also clear that our people have really bought into lean thinking. They have completed 300 kaizens a year on average, 20 six- to twelve-week projects a year, and brought forward 12,000 self-implemented ideas. We have also seen a 300% increase in the deployment of Karakuri devices in our industrial processes.
Finally, we have had the recognition from the rest of the Daimler Truck group. Despite representing only 10% of the group in terms of headcount and revenue, Mercedes Benz Brazil was the biggest winner in the CI Cup global competition, promoted by the head office to award group best practices, for the past two years. In 2019, in particular, we scooped up 70% of the awards. In 2018, the CI Framework was awarded as the best lean culture program across the Daimler Trucks group.
For more articles on lean in Brazil, click here.
THE AUTHOR
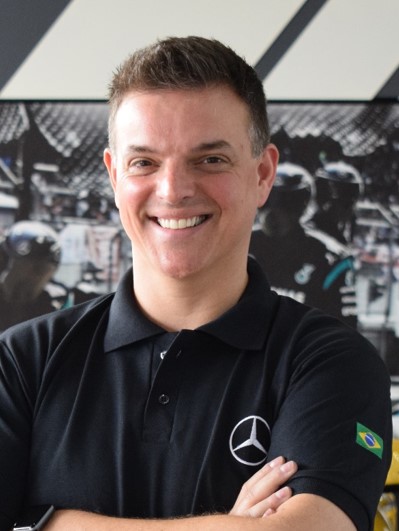
Read more
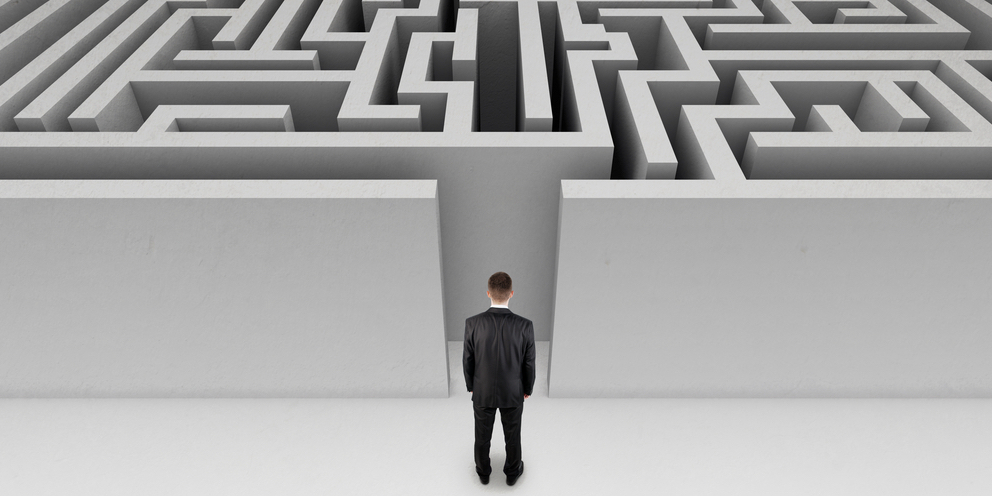
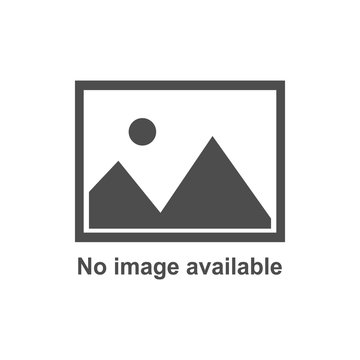
FEATURE – For many organizations, devising effective strategies remains a gap to fill and that’s something lean can help with. Michael Ballé discusses strategic thinking with our editor.
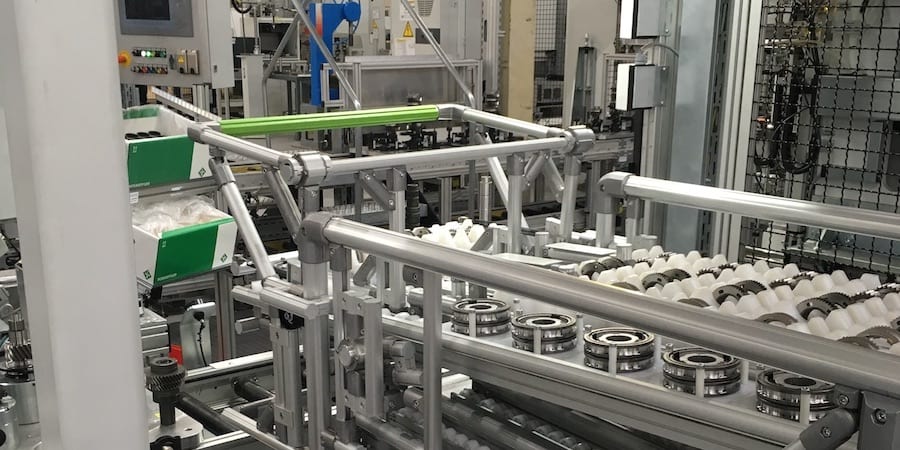
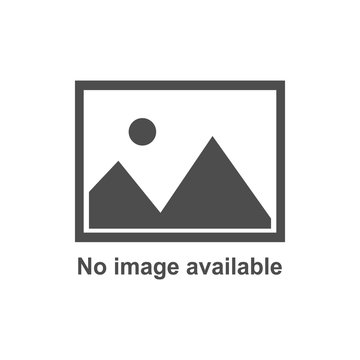
NOTES FROM THE GEMBA – If you need proof that kaizen leads to real innovation, look no further than AIO. This French Tech company that reinvented itself as a karakuri kaizen coach.
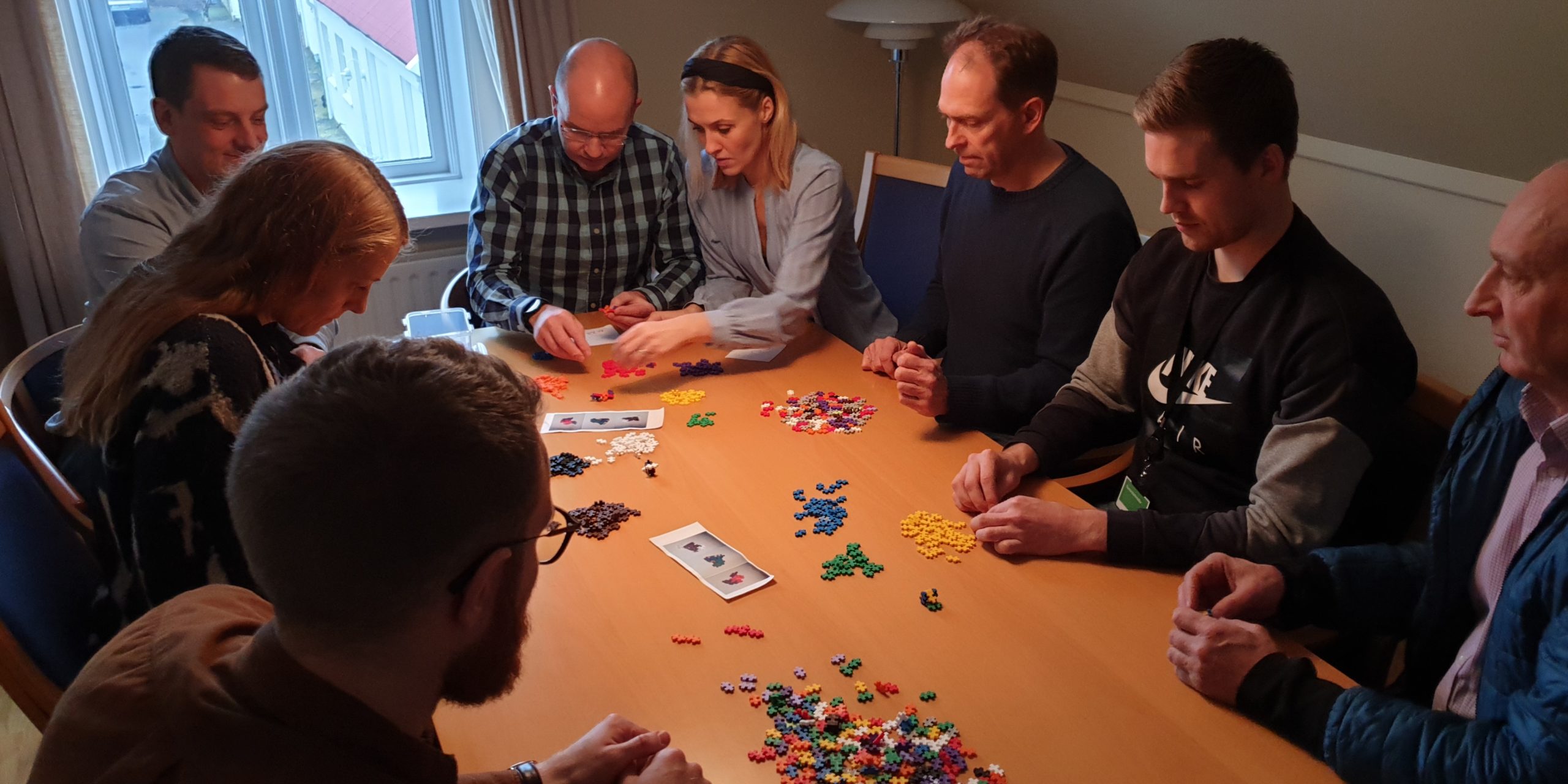
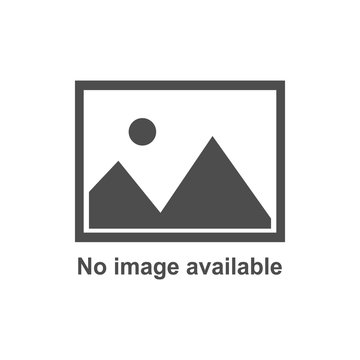
INTERVIEW – Today’s story takes us to Iceland, where a senior leader in a utility company introduced cellular thinking to her team in a bid to improve flexibility and better working conditions.
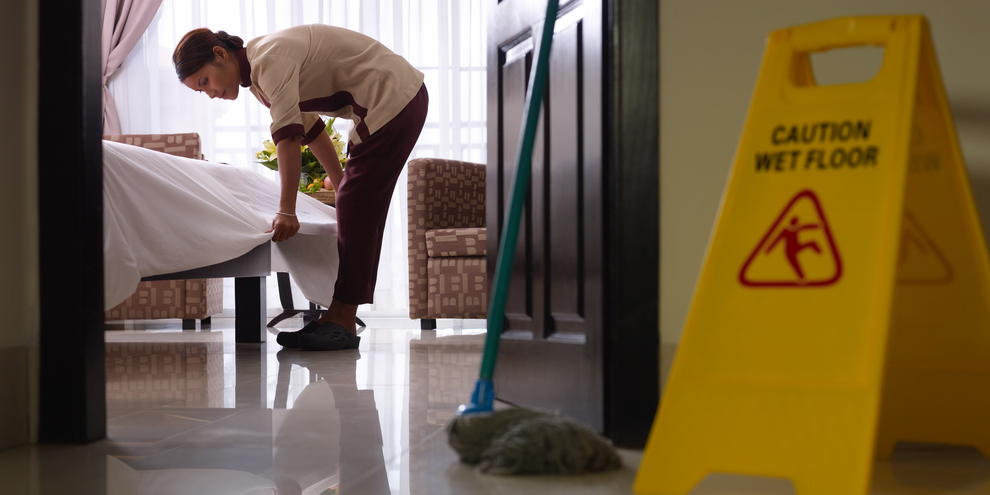
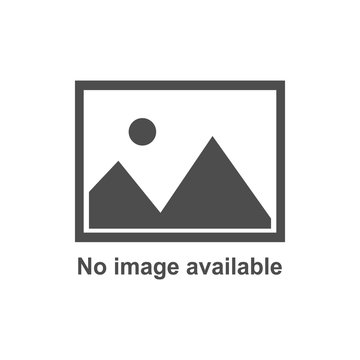
CASE STUDY – Hotels of the Palladium Group are implementing Lean Thinking in their housekeeping departments to improve efficiency and service quality.