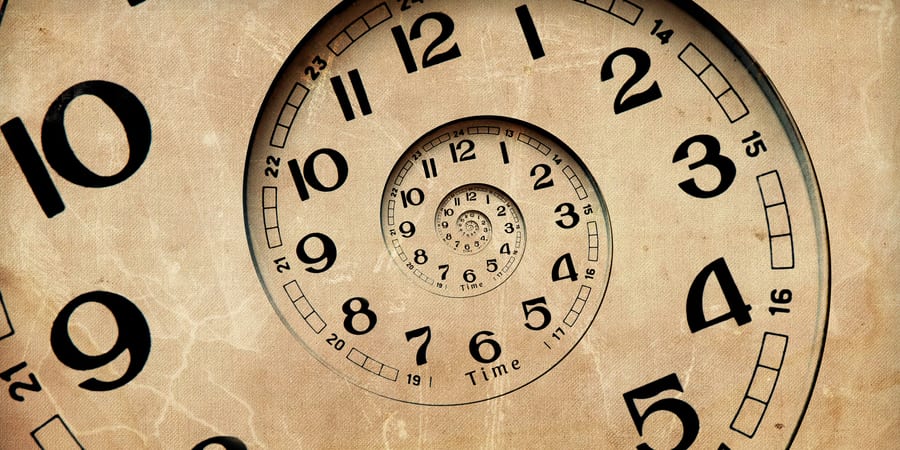
To initiate levelled production you need to run to time
FEATURE – What if we ran our production schedule to time instead of quantity? While creating overproduction, running to time is a temporary first step to establish levelled production with fixed repetitive cycles.
Words: Ian Glenday, lean coach and author
The first article in this series on levelled production showed how ERP planning, based on economic order quantities (EOQs), is guaranteed to create instability through plan changes that have nothing to do with actual customer demand. The second article described how Toyota created stability as a foundation for sustainable continuous improvement and application of standards through a fixed repetitive plan over 6 to 8 cycles for the “greens”.
With ERP planning not only is the plan constantly changing but output rates also tend to be quite variable. Of course, there is a demonstrated output rate that is used in planning, but this is an average figure. Actual outputs are in reality higher or lower than this, meaning that planned production can take longer or shorter than expected. This is yet another form of variability that challenges both having an effective supply chain and achieving sustainable continuous improvement.
It certainly presents a big challenge when first attempting to implement a fixed levelled production cycles – especially regarding major changeovers. These are usually a big opportunity for improvement, as often the amount of time lost in both the changeover and, crucially, the ramp up following the changeover can be significant. Variable outputs means that a major changeover in reality can happen at any time, and almost certainly not at the time it was planned to take place! Not a good a situation when trying to sustain changeover improvements through activities such as SMED.
But what if we ran the green fixed cycle to time instead of quantity? This entails calculating the quantity needed using demonstrated average output rates, and converting this into a fixed start and stop time. The neat bit is to then get the start and stop times to be at the best possible times for the changeovers to happen (this may involve a bit of manipulation on the overall quantities) – the best time being when the right resources are available with help from technical experts to improve the changeover and reduce the ramp-up losses.
It’s a simple idea, which met a lot of opposition at first. “What if we don’t produce enough?” was the typical first response I got, quickly followed by “But we can just stop – what do we do with what product is left over?” With levelled production there is a buffer tank of inventory that absorbs fluctuations in outputs – and empirical evidence shows it is more common to over-produce than under-produce when running to time.
Why? There are several reasons. Changeovers at the same and best time happen faster and with less ramp-up issues, which results in more outputs. It’s the idea of the economies of repetition: by doing the same thing at same time each week teams get better, they follow standard setting more and – here is an interesting phenomenon – they try to beat each other on the quantity made in the same time. It creates positive competition. This was nicely illustrated at a biscuit factory I worked with, where the Site Director told me he had tried for years to get operators to accurately monitor changeover times but never succeeded – until he started to “run to time”. “Now,” he told me, “they measure changeovers to the second just to show they beat the time set the previous week. The time lost graph just keeps going down. It’s great and outputs keep going up.”
Running to time has both positive and negative implications on material supplies. Fixing the time means that ensuring materials are available at the right time becomes easier, but at the same time production may make more in the same time, meaning that extra materials need to be available. Making more output in the same time makes the operators feel good – and management likes it too as they see efficiency and fixed costs improve – but in lean theory overproduction is bad. Running to time is a first-stage process, in order to get fixed cycles running and economies of repetition occurring so that improvements in outputs and efficiencies can happen. However, once output rates go up and the variability in outputs is reduced – the hour-by-hour rates stabilize albeit at a higher level than they were previously – it is time to move to a second, more advanced stage of fixed cycles, where the order quantity is fixed. Now, as output rates are more stable, changeovers will happen at more or less the same time each cycle. It is also possible to achieve just-in-time (JIT) for materials and reduction of inventories in raw, packing and finished goods.
Run to time is not strictly lean, but I have found it is a useful first step to help implement levelled production with fixed repetitive cycles – which are the foundation of the Toyota Production System. It also helps improve and stabilize output rates, and that is certainly an objective of lean.
THE AUTHOR
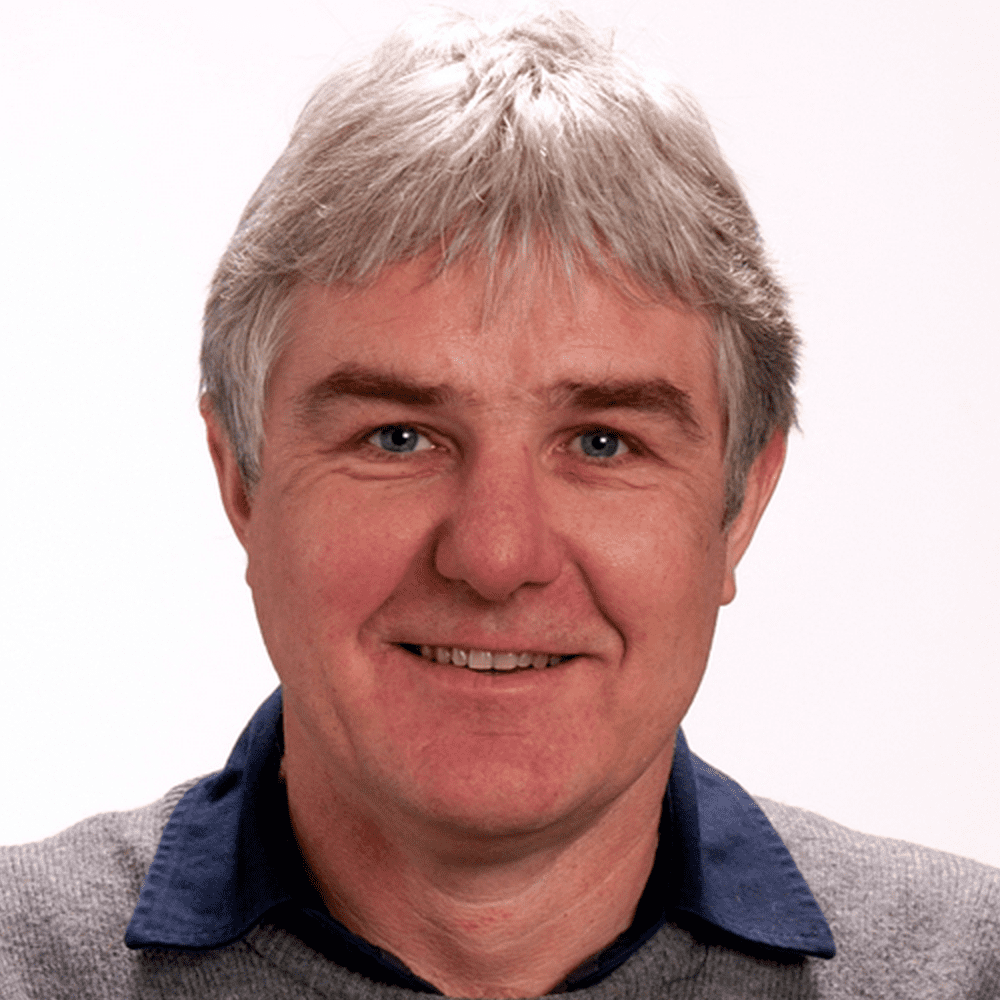
Read more
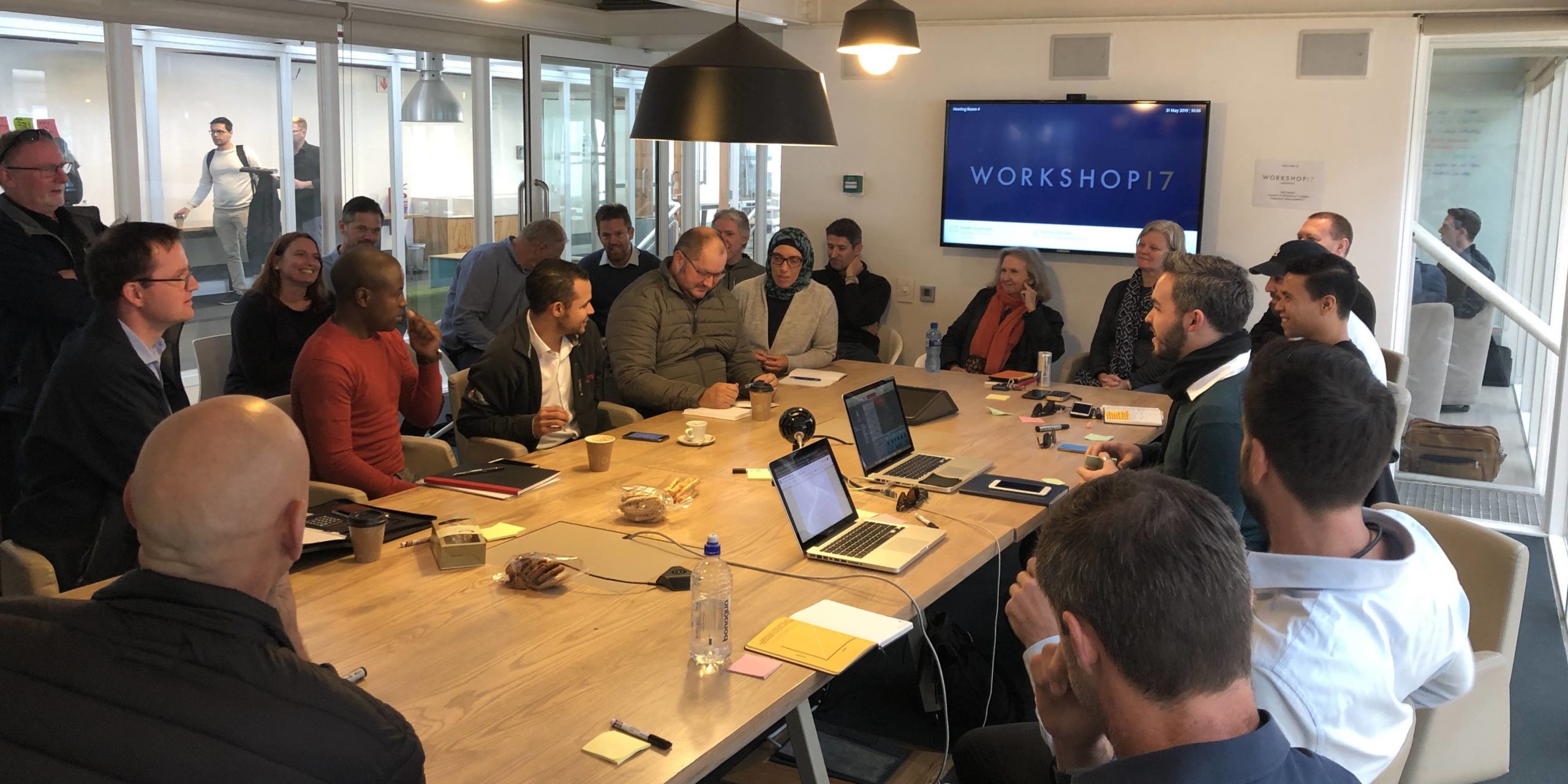
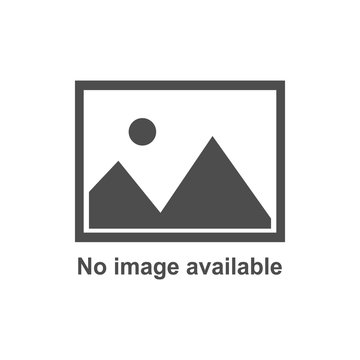
FEATURE – What started as the idea of two friends to meet up and discuss their lean journeys turned into a regular get-together of lean practitioners in the Cape Town area. Another example of the importance of sharing.
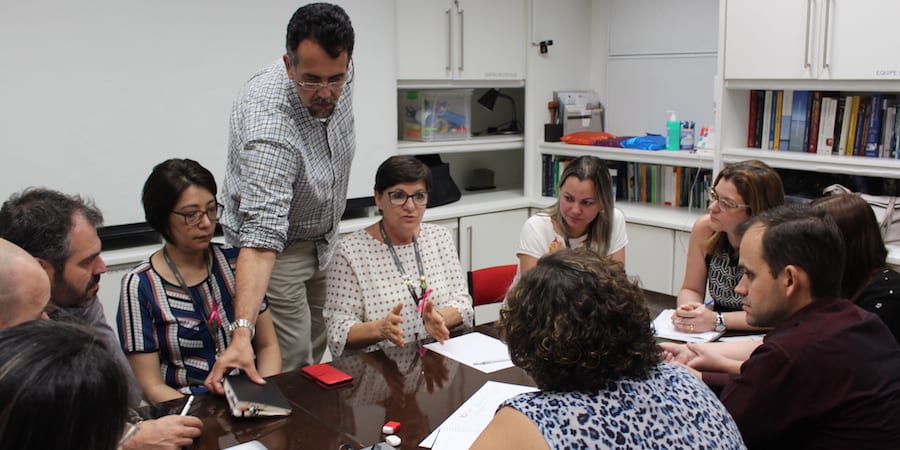
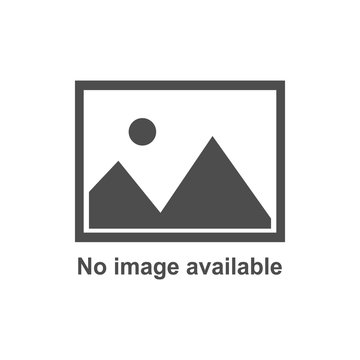
VIDEO - The CEO of a cancer center in Brazil gives us a tour of the their obeya room, taking us through their strategy deployment and explaining how it supports their mission of reducing the burden of cancer.
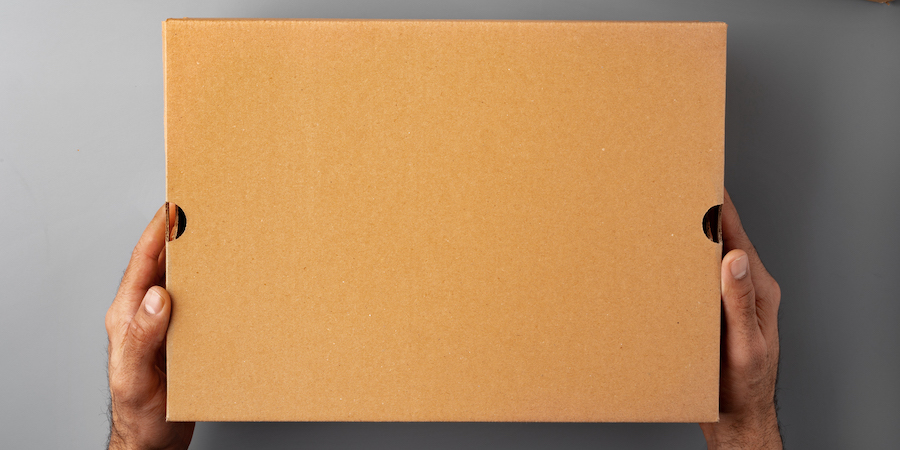
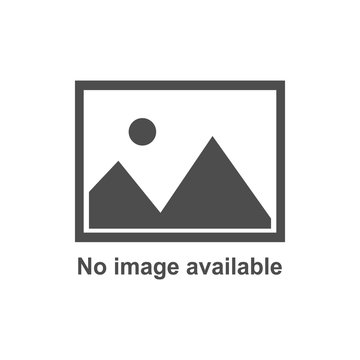
FEATURE – The author shares a story from a training session at the gemba, which contains a couple of important lessons on the Training Within Industry method.
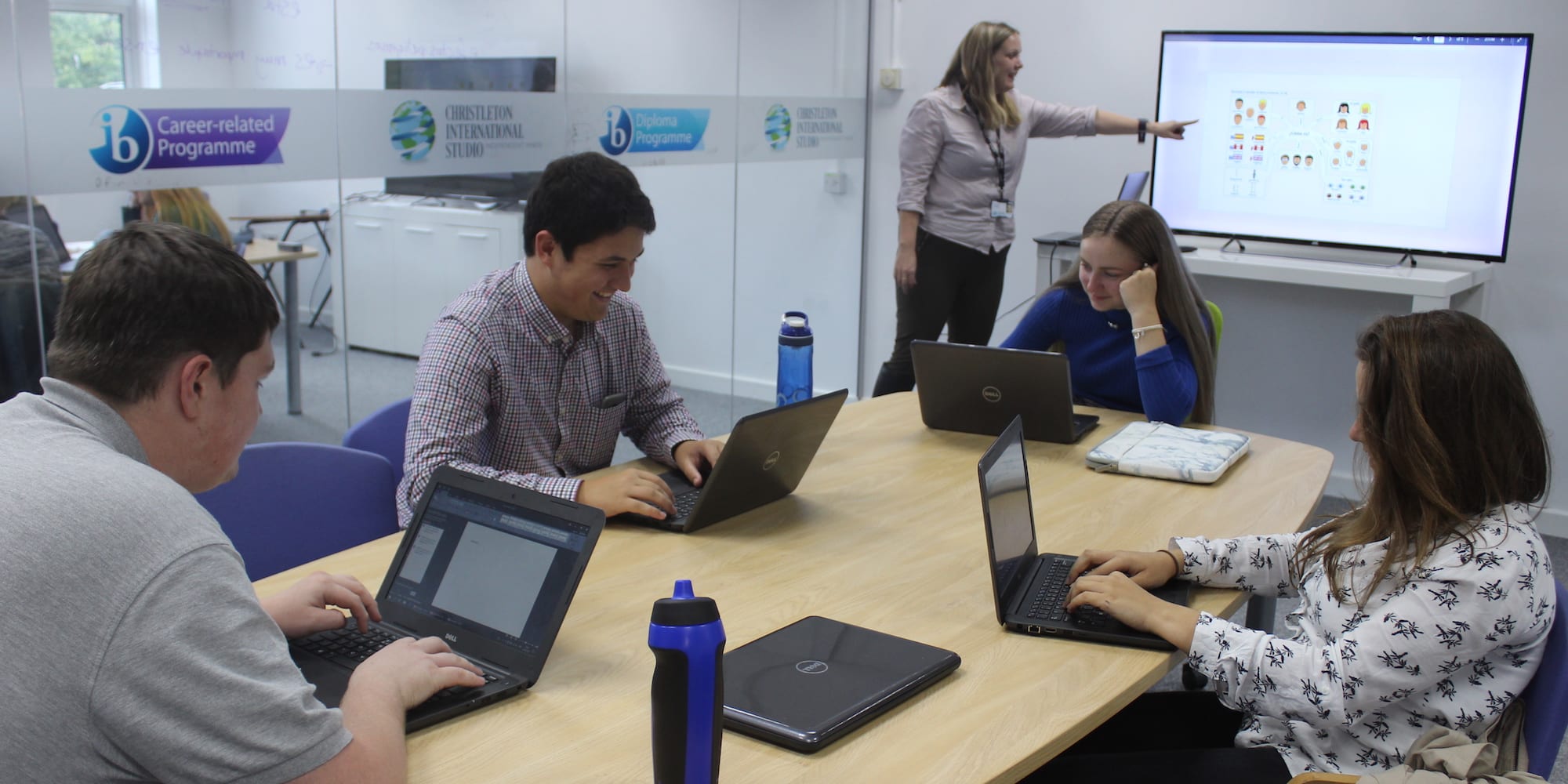
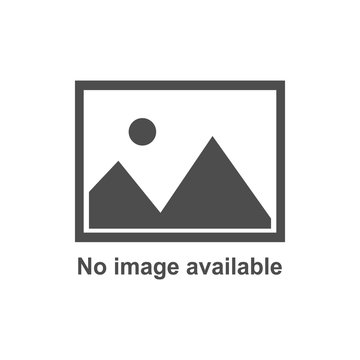
FEATURE – The application of lean management to education is not new, but we all know how hard changing legacy systems is. This greenfield lean school aims higher, trying to rethink learning altogether.