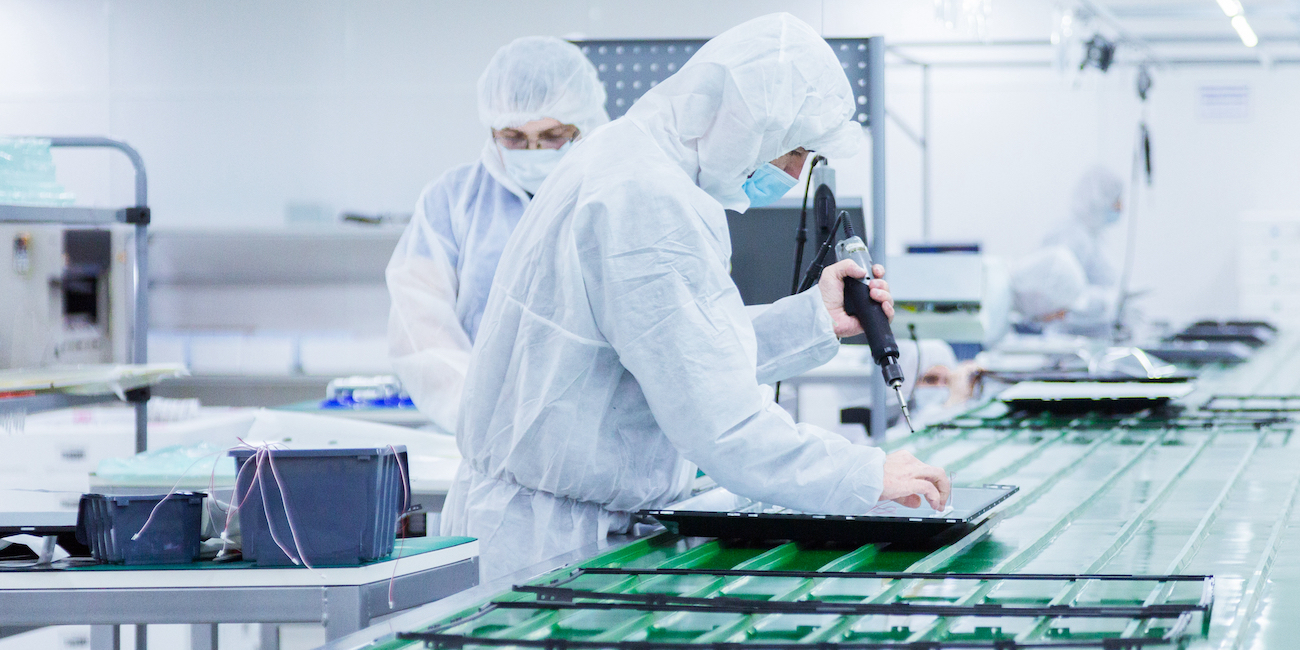
The synchronization of material flow with demand
FEATURE – Aligning supply flows with demand is crucial to success, but it can be complicated. Lean Thinking can help us identify the strategy and sequence of activities that we need to make it a reality.
Words: Adionil Jose Fumagali Junior, Lean Institute Brasil
Supply flows are often handled directly by the operators, but in most cases the sourcing of the materials and tools they need doesn’t occur in an organized manner. Operators working in the different flows often have to go up and down the plant to find the components they need, which can easily result in a higher lead-time and bad performance in deliveries to the customer.
When we look at the detail, these problems become ever more complex. A lack of aisles and means of transportation for the organized and standardized movement of materials are usually the first problems we observe. Other issues that typically catch the leadership team’s attention and impact the company’s results include missing parts, difficulty in finding all components, delays in production, problems with documentation, controls, quality and product disposal due to inadequate material handling.
In such a situation, it is important to understand and analyze the current process the company has in place for solving problems. There is great value in having a safe and proven method, like Lean Thinking, to help with the creation of a structured plan to resolve issues and remedy all losses. Such a strategy will highlight the problems having the most significant impact on the process, so that we know what we need to tackle first.
At Lean Institute Brasil, we have recently come across the case of a medium-sized company operating in the hydraulic pump sector. The business was in the process of tripling their production volume from approximately 30,000 to 90,000 products per year. Their operations were already marred by serious storage problems and the inadequate movement of materials. The immediate problem to address was related to organization, as it was impacting quality and making it difficult to control inventory. The company found that using KLT boxes was an excellent solution: they come in different sizes and heights, which allows you to identify the best packaging solution and to guarantee the best quantity for each of the flows and internal products (depending on their dimensions, type, and level of demand) using takt time. In order to measure the quantity of those boxes, all of the company’s products had to be analyzed in terms of purchase volume variations.
It is also important to establish ways of identifying and moving materials. For products that may have quality problems due to collision during handling and transportation, for example, trays can be created to better separate materials and mitigate risk. The gains from this alone can have a huge impact, standardizing the quantity per package and facilitating inventory controls. As a result, the volume for each box is defined clearly, significantly reducing deviation and improving inventory control in production processes, in addition to helping to mitigate quality losses.
When the most serious problems are solved, the new challenge becomes to expand the planning of movement and control of materials in a structured way for the entire plant. But how can we do this taking into account the different product families of the company, which have various volumes and sizes? The first step is to define a plan and its steps with the objective of making a structured change oriented towards continuous improvement, using Lean Thinking to synchronize the flows and connect production with the logistics processes. The main steps are:
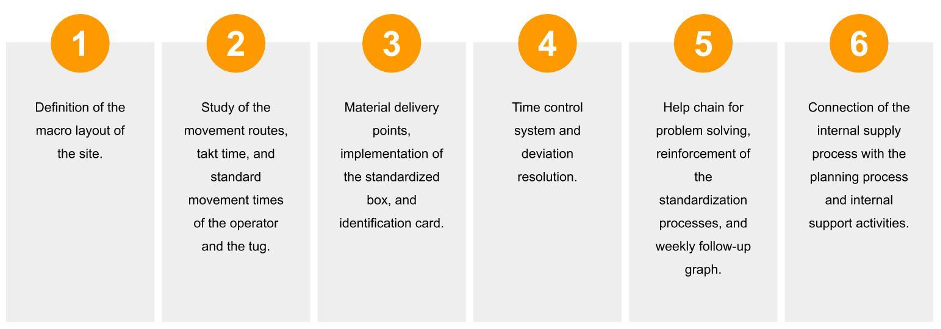
1. Definition of the macro layout of the site
In this initial step, the team must analyze the layout options, considering the pros and cons of each based on the materials and the variation of the production volume of the site. They should also consider the best position for the receiving and shipping processes, the sizes and flows of the input and output processes, the process of separating and allocating the materials received for production processes, the departure of processed products from the production areas, the aisles of the site as well as strategic areas for expansion as new business appears.
A sticky point in this analysis is figuring out how to make a layout that supports changes in demand over time (for example, if the company is dealing with an increase in volume or a reduction in demand). The important thing is to be able to synchronize the workflow with the demand. To this end, model and modular cells (each designed to obtain maximum productivity with the lowest use of resources and costs) are extremely effective. It’s also useful to define an area for potential growth (as shown below), allowing for potential expansions beyond those initially planned.
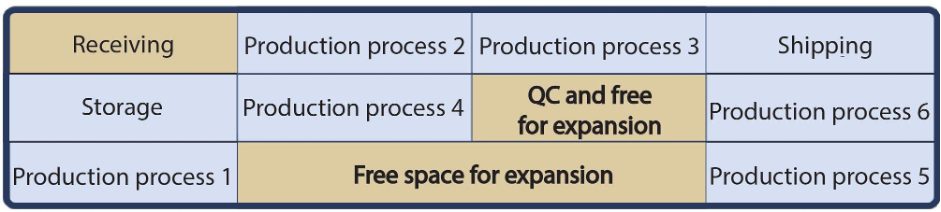
Image 1: Top macro view of the company's layout
2. Study of the routes, takt time, and standard movement times of the operator and the tug cart.
This step seeks to analyze in detail the flow of the tug cart and its speed, as well as the number of operators and equipment needed. This will allow us to make the best use of resources based on our capacity, handling times, and supply frequency. The 2004 book Making Materials Flow offers information on how this analysis can be carried out in a simple way. It also details the calculations in the process, such as timing and analyzing the process with the takt time to understand the resources needed.
At this point, the speed of the tug should also be calculated, as well as the movement of the operators on their respective routes. This will allow us to find out the best frequency of sup ply for the different processes and reduce the storage area for materials in production as they are transferred from the receiving area. In production areas, we seek to achieve maximum productivity per square meter. This stage of the work provides a series of information to detail the layouts of each area.
In processes with higher demand, the flows must be supplied in a shorter time interval, while in processes with lower demand, they can be supplied in a longer interval, which impacts the material handling area in production. Before considering an investment in equipment, it’s worth considering increasing the frequency of supply by streamlining internal routes to account for the volume variation.
In the image below, you can see a sheet with the operator’s standard working time, carrying an example of material handling in logistics. In each line of the form, the work performed by the operator is recorded – with each movement of the operators timed as they supply, deliver, and collect packages at each delivery point in production – to cover the whole process.
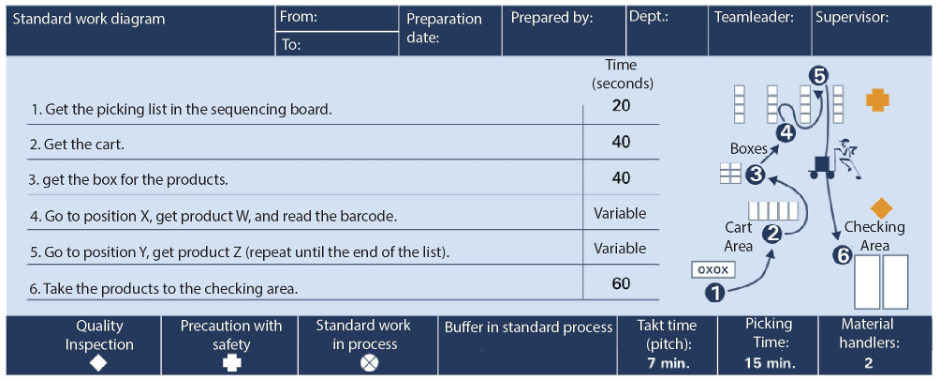
Image 2: Example of standardized work of picking
3) Material delivery points, implementation of the standardized box, and identification card.
At this stage, we start to work on the entry and exit points for materials. The identification of the components by box and the standardization of the identification card across all processes makes it easier to complete the different stages of the process. At the beginning, this process of material handling can be carried out manually, but over time small automations and controls in the process can be implemented to save time and avoid typing errors, allowing for greater control of the process and easier tracking of each product.
Below, we can see a revised list of materials, with the definition of the supply point, place of origin and destination, the type (whether it is coming in or out), description of the type of material, means of transport, triggers, and quantity of supply locations. This activity aims to reduce the area needed and lower the volume of materials present in the production areas – in addition to delivering the materials as close as possible to the point of use, maximizing the productivity of the operation.
List of materials
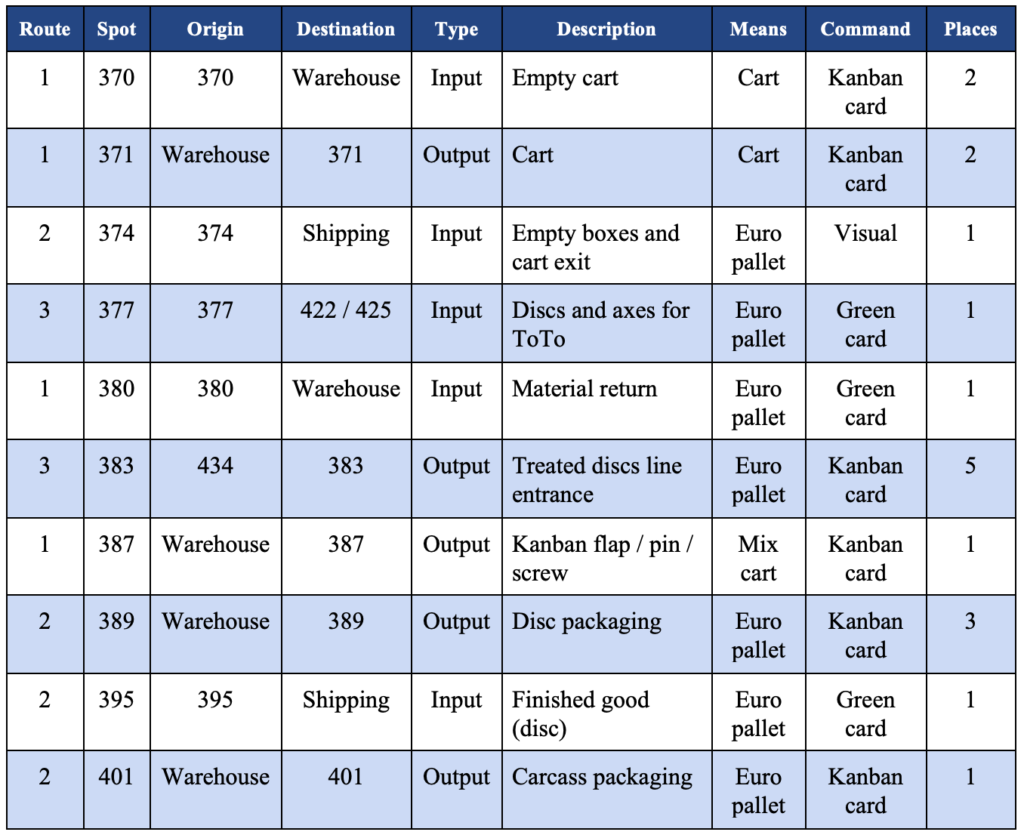
Table 1: List of materials by supply point
4) Time control system and deviation resolution.
This step focuses on the observation of any stoppages on the line due to the lack of components, encouraging an investigation process to analyze deviations. For this, there are a number of useful strategies, such as standardizing the times and controls in the processes and defining the exact stopping point of the tug in the production process to make it easier to reduce the variation in the time spent by the operator when walking through the operation.
Milk Run - Stop point
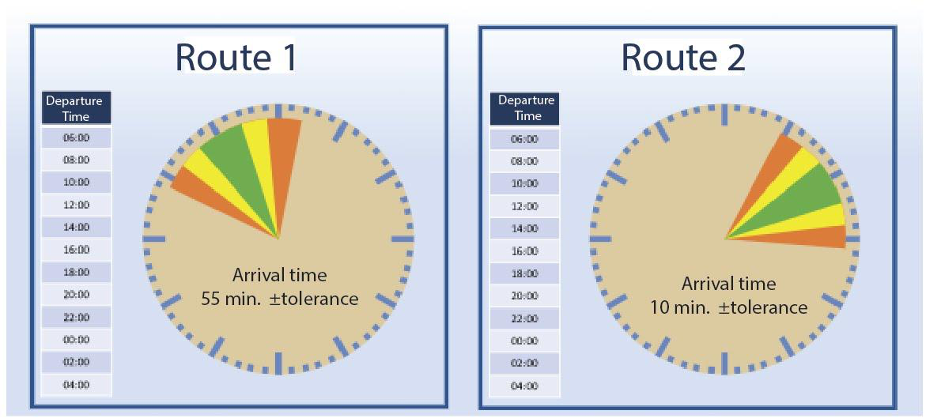
Image 3: Visual management of the stop point of the material supply route
It is also worth reviewing the speed of the tug cart and defining a maximum and safe speed to avoid variation in the displacement between supply points, reducing safety risks for operators and the quality of the materials handled. It is possible to define the exact moment of collection and delivery of the materials at each point. In case of any deviations or delays (which can be seen on the example below) – that is, if the supply time on the line is outside this range – a person is assigned to the resolution of this problem and given the authority to contact the person in charge to analyze the situation and make adjustments or deal with deviations so that the route can be completed within the allowed range.
Image 3 shows an example of this control system based on a real-life case and historical times at each point.
5) Help chain for problem solving, reinforcement of the standardization processes, and weekly follow-up graph.
The previous information should always be improved to seek continuous improvement in the process and, as we know, the way to do that is through standardization.
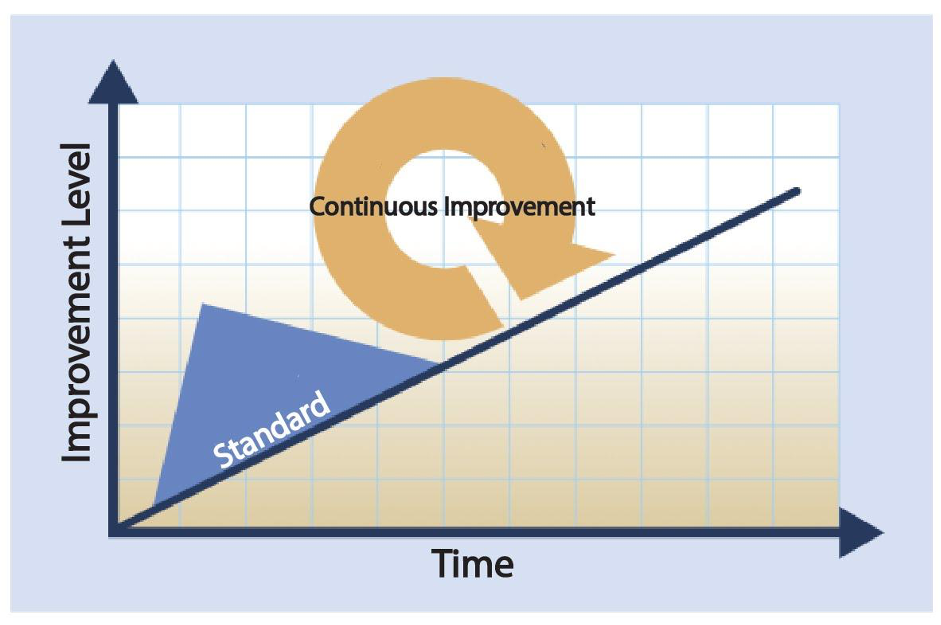
Image 4: Role of the standard in continuous improvement and relationship between the degree of improvement over time
As shown in Graph 1, if the process does not have a standard, over time the improvement will follow the trend of the black line. With the standardization, we will follow the red line trend, which represents a significant change and a positive impact on the rate of improvement.
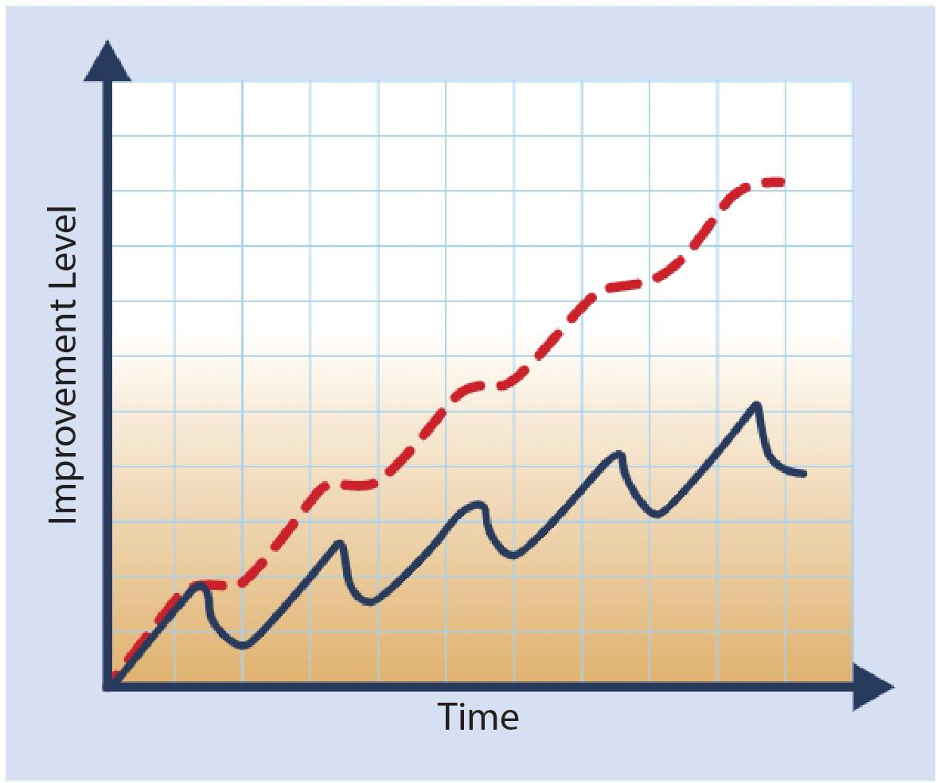
Graph 1: Comparison of the degree of improvement with and without the existence of a standard
To ensure that the process is standardized, all the questions below need to be answered with a YES.
- Is there a standard?
- Is the standard up to date?
- Do employees know the standard?
- Does the work follow the standard?
Below you will see an example of a table for the definition of the standards necessary to monitor and improve the material supply process in production, which was created considering the delivery interval times per day on each shift. With this system, it is possible to track the process on a single sheet every week, as the information is consolidated into a weekly metric at the bottom.
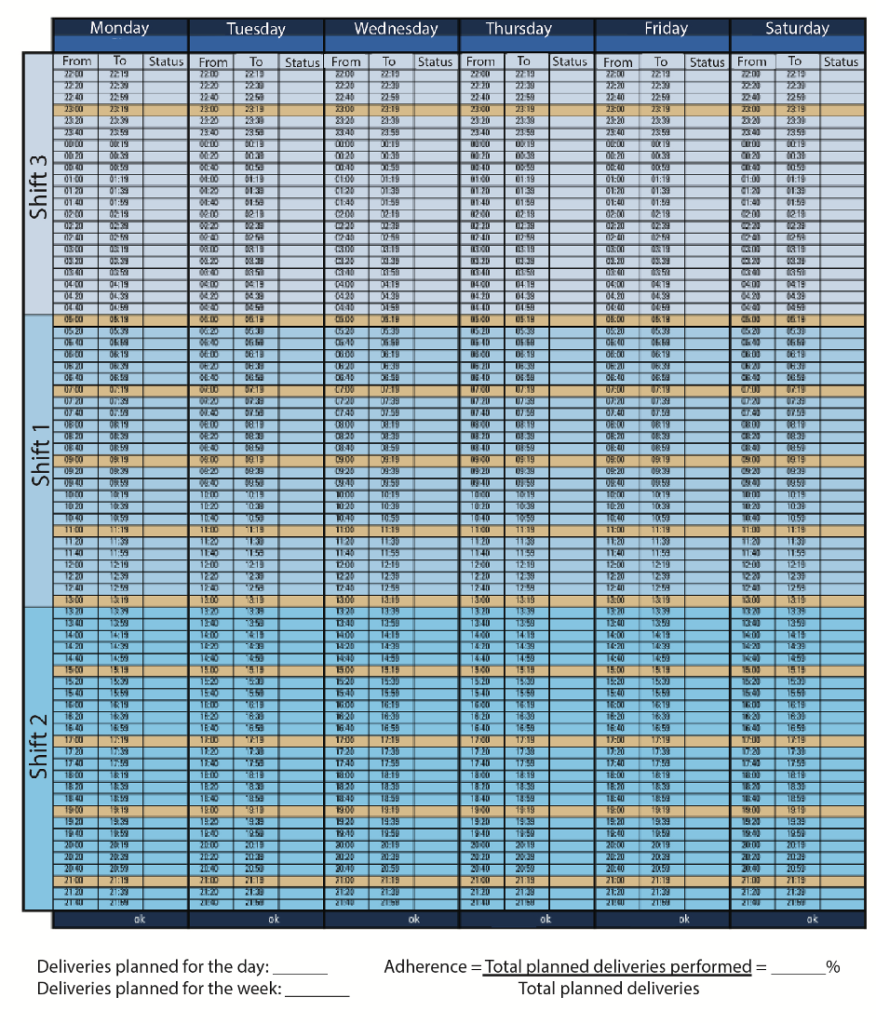
Table 3: Monitoring of material supply
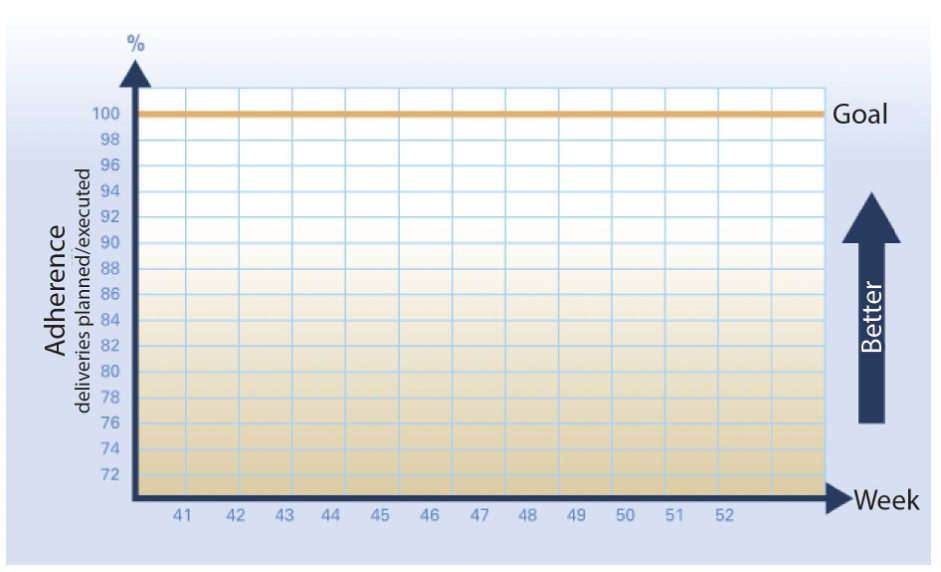
Graph 2: Adherence to Route schedules
Based on the table above, the information is analyzed through metrics and follow-up, as shown visually in Graph 2, representing the adherence to route times.
The management process is greatly improved this way, and it becomes possible to detect new opportunities and connect the entire system to the supplier’s process and the internal timetable of quality approvals.
6) Connection of the internal supply process with the planning process and internal support activities.
The last step entails creating visual boards and supporting the handling of materials when the request for material takes place during the approval or handling process itself (or if the material has not yet arrived at the company); the pending material card can be placed in a deviation management board. Thus, the scheduling plan or help chain begins, triggering people to work on the analysis and replacement of the material (even changing the production sequence if necessary) to avoid interrupting the work of the operators on the line.
It is also recommended to hold daily meetings with the leadership team to assess deviations and make the necessary decisions to improve supply. If necessary, it is also recommended to review the processes and procedures to improve the company’s overall performance and results. This will also help us to start focusing on the stability in the supply of materials. This information can help us to avoid small deviations, eliminate shortages or excess materials. For each pending product (one that has not been approved or separated or that hasn’t arrived yet), an action plan must be defined for the replacement of the component, following up with those responsible on the dates established.
With the evolution of technology, some companies have adopted AGVs (Autonomously Guided Vehicles) to move materials between processes, and this can be your next improvement if there is a need and you can afford it. However, don’t try to do this if you haven’t achieved basic stability first.
***
With the changes outlined in this article, several companies have already noticed significant productivity improvements in the areas of manufacturing and logistics, as the line operator is no longer involved in the search for materials and always has all the necessary components available at the point of use, which leads to better control of inventory throughout the factory and reduces deviation.
In conclusion, Lean Thinking enables the synchronization between supply, operations and demand, increasing productivity by ensuring more frequent and standardized supply runs, helping to gradually make changes, and obtaining the best productivity of the processes involved. This article presented in a practical way all the steps that need to be carried out to make this change in a structured way and obtain the best results for the company. Do you have the opportunity to synchronize the logistics process with the customer’s demand? How will you address this gap and improve your internal processes?
Source: Lean Institute Brasil
THE AUTHOR
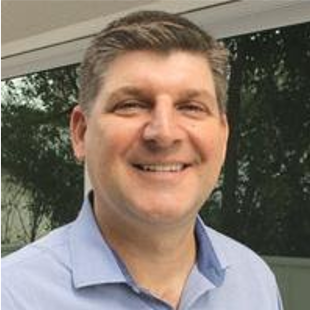
Read more
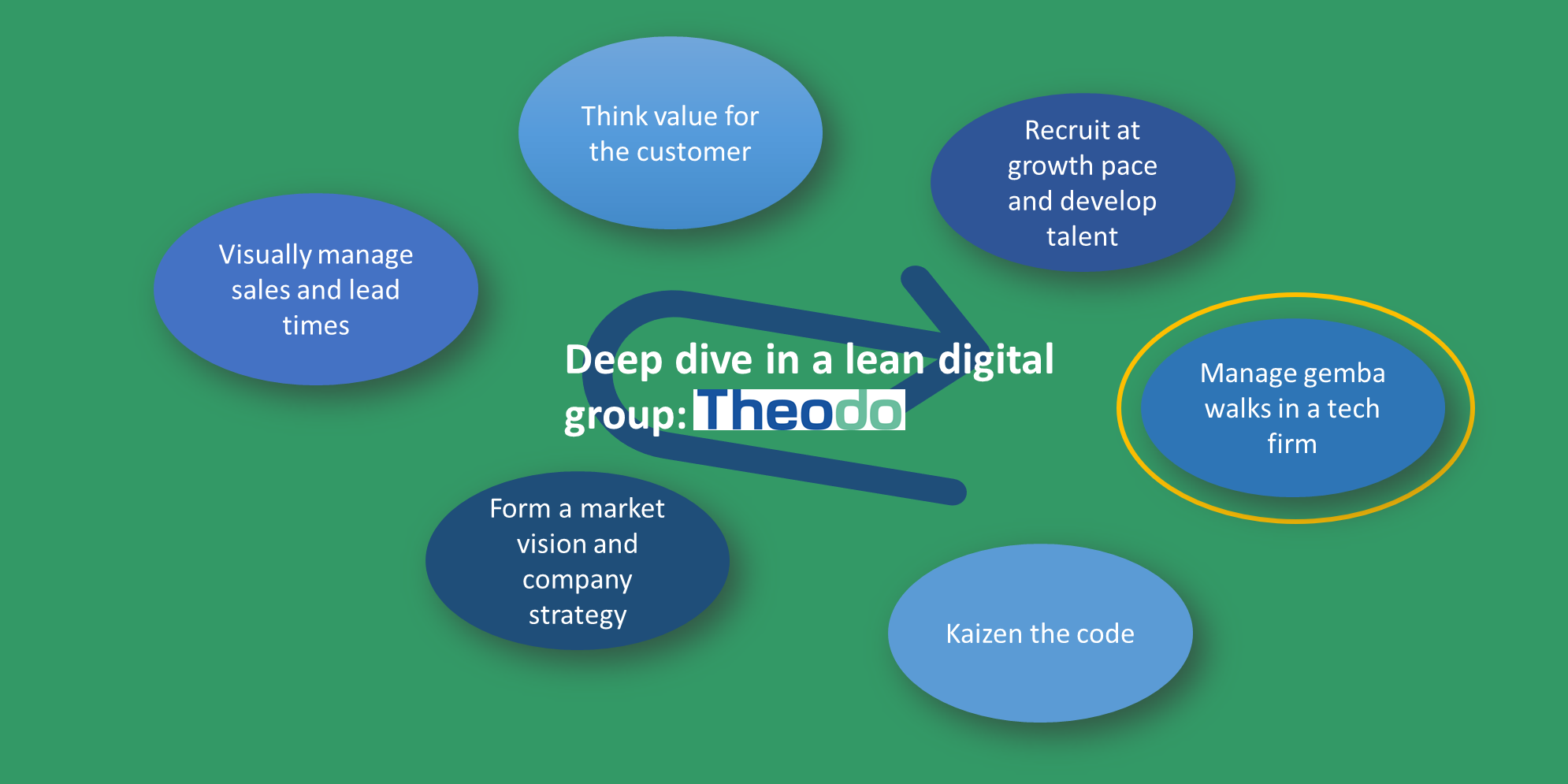
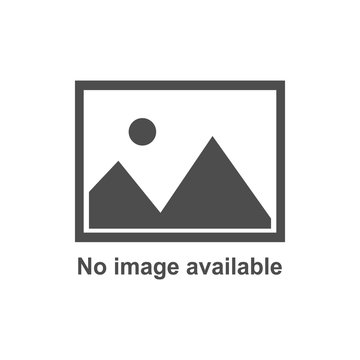
FEATURE – This month, the author learns how gemba walks happen in a digital environment, where the work and information are typically hidden in computers.
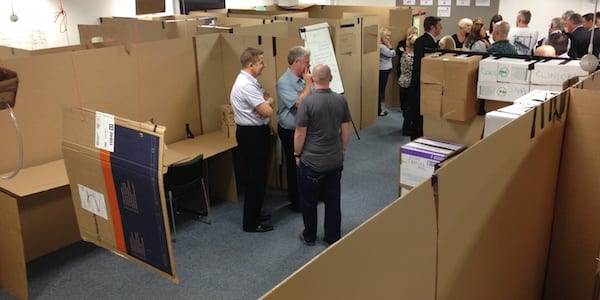
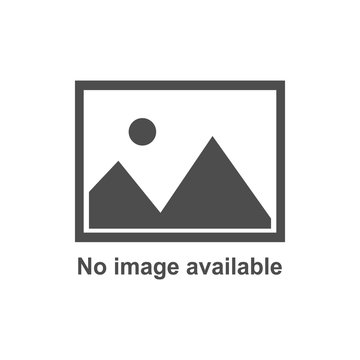
ARTICLE - Improving healthcare architecture means truly meeting patient requirements. This article reflects on the power of 3P design and looks at an implementation in the North East of England.
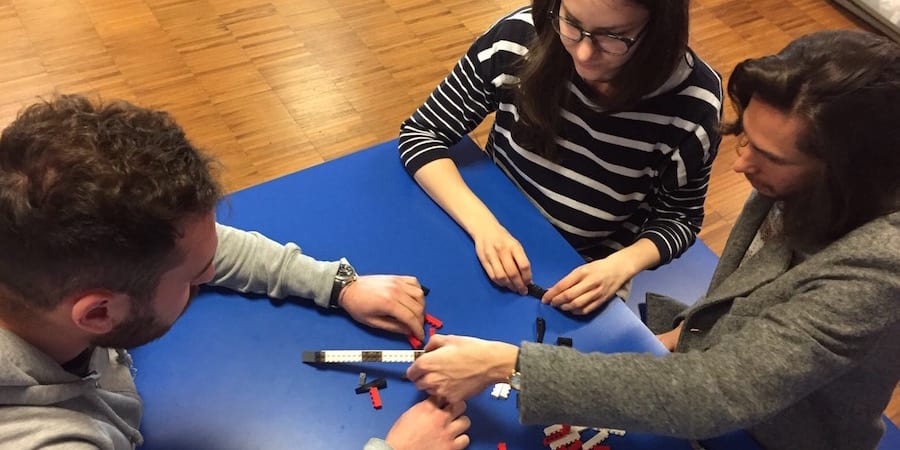
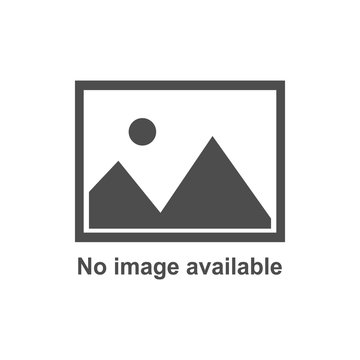
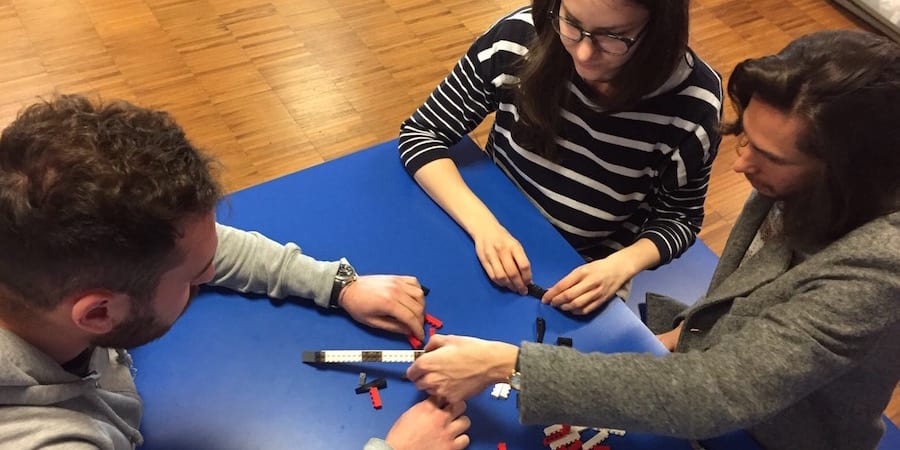
FEATURE – In a world of disruptive innovation, being faster and smarter at developing new products has become critical. The authors explain why set-based concurrent engineering is the answer, and why a game is the best way to learn it.
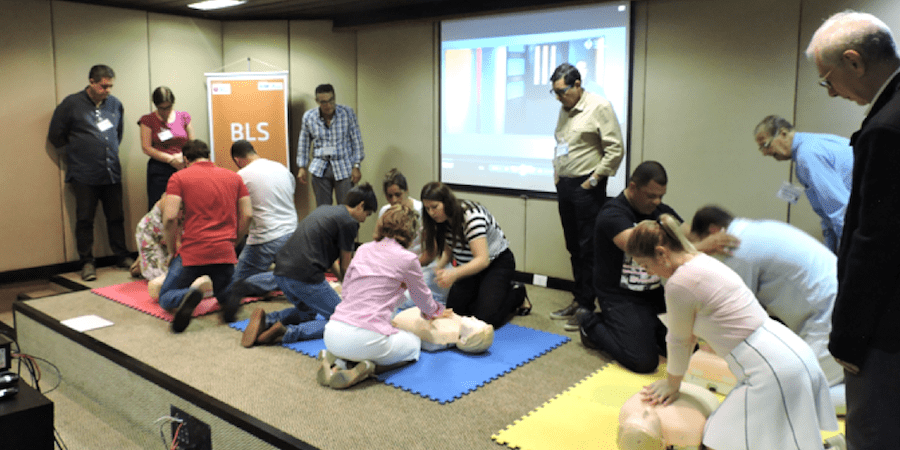
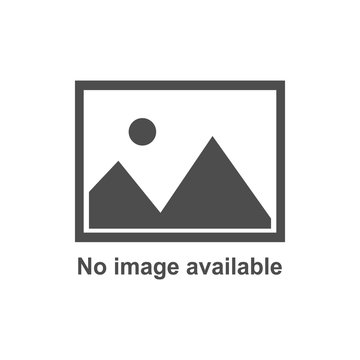
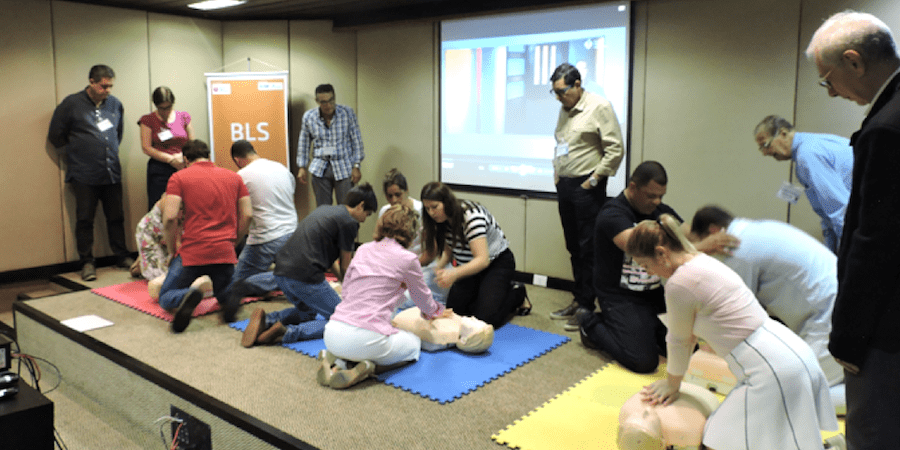
INTERVIEW – A cardiologist from a hospital in Salvador de Bahia explains how his department was completely transformed following the introduction of a dedicated pathway for heart patients.