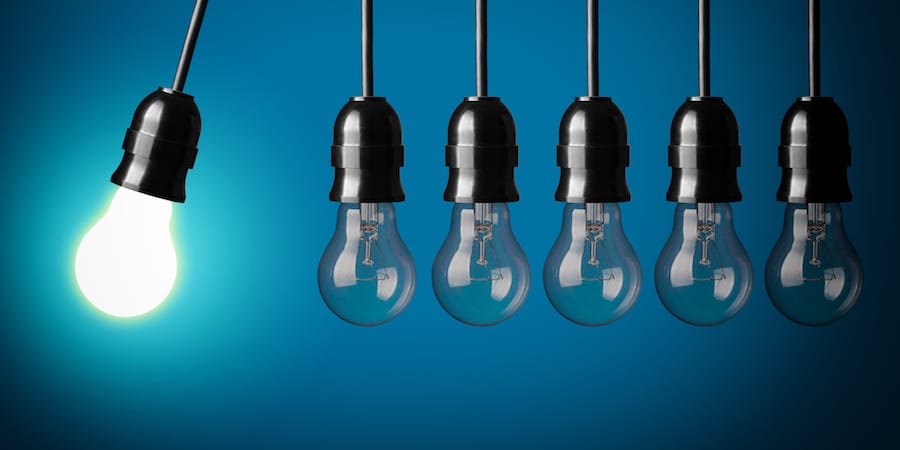
Five lean practitioners answer the same question #7
ONE QUESTION, FIVE ANSWERS – Inspiration can help us solve a problem, get our colleagues interested in lean, or even pick ourselves up after a failure. But where do we get it from? We asked five practitioners.
"Where do you draw your lean inspiration from?"
Margarette Purvis, President and CEO, Food Bank For New York City - New York City, USA
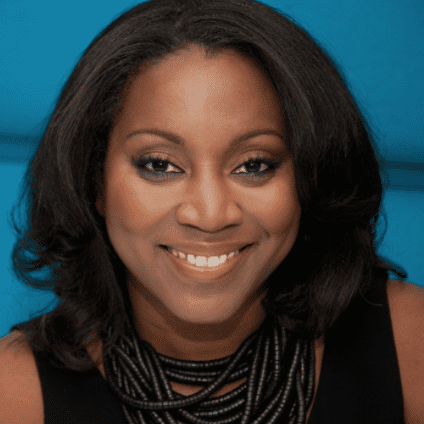
I work in a large charity leading a team of more than 150 employees who focus their many talents on our goal of ending hunger. Planning for and managing our multifaceted programming portfolio means that on any given day various important things will compete for my attention. My lean journey relies on a simple inspiration and it's called "results". No matter how taxing the review of process may be when I look at the benefits to my organization's ability to meet and sometimes exceed our goals, I can't help but feel inspired to soldier on. Improving the process increases the success of the bottom line: more meals and vital services to New Yorkers in need.
For an interview with Margarette on the great work of the food bank, click here
Michael Ballé, lean author and executive coach - Paris, France
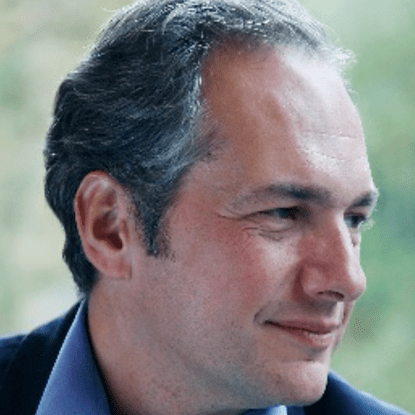
I'm clearly inspired by conversations with sensei on the gemba. Last time this happened, I was visiting a Toyota plant in Taipei with Joe Lee, a TPS veteran of 30 years. We were looking at an inspection station and discussing how the inspector interacted with a digital tablet as opposed to the old paper forms: did that influence how he looked at the car itself?
We discussed the relationship between eye, hand and mind at length – reflecting on how lean tools are often about materializing abstract concepts. Our conversation about the interaction between thinking and doing carried on for a couple of months, and laid the foundations for what is now a book I am working on with Dan Jones, Jacques Chaize and Orry Fiume (you'll see it in the spring of 2017). In it, we talk about lean as a cognitive revolution (not just an organizational one) and TPS as a learning system (not just a management system) – a full strategy. And all of this came from a conversation with a sensei in Taipei.
Mirette Kangas, Head of Lean & Agile Development, Finnish Broadcasting Company (YLE) - Helsinki, Finland
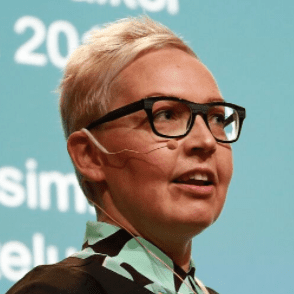
A mission to do good – at work and in life in general – is what guides me, and the inspiration I need in order to do it comes from the talent of other people. My interaction with them stimulates my creativity and energizes me.
In my professional life, this interaction takes place in workshops, at summits and in my daily work at YLE, and I complement it by reading a lot of books and articles about lean, agile, lean startup, leadership and company culture. But what about my personal life? Well, let's say that arts and culture have a special place in my heart. I'm a classical music enthusiast and a violin player with an amateur symphony orchestra full of very talented people from various backgrounds. Music – much like the art of improving – requires a life-long commitment to learning and the harmonious interaction with other players.
Interestingly, in a broad sense, the orchestra and YLE share the same mission: delighting their audiences, with perfection being the end goal (unattainable perhaps, but an end goal nonetheless). There is no doubt that the inspiration needed to fulfil such a noble mission comes from engaging with new and different perspectives all the time.
YLE has used lean to scale up agile. Learn more here
Javier Oliete, General Manager, Neo@Ogilvy - Madrid, Spain
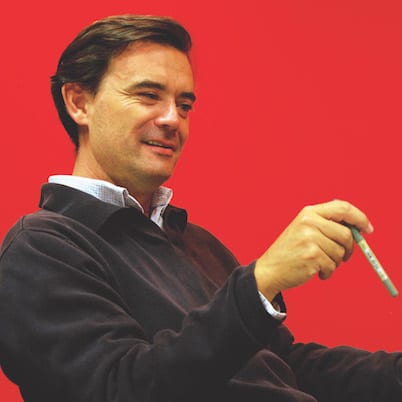
One night a couple of years ago I was out for dinner with some friends, sitting next to a couple, Emilio and Blanca (he is in supply chain, while she works in banking). They were talking about lean with great enthusiasm, explaining how beneficial it had been to their organizations.
To us marketing professionals, lean thinking can initially appear as something rather alien. It feels very far from our skills set and daily scope, and we tend to think the methodology is only for engineers. Indeed, I was very surprised to hear Blanca talking about it in those terms, as I had no idea lean could work in a bank! I was really inspired by the stories of practical improvements that she shared, and a week later I had enrolled into a lean course.
Now that my organization is applying lean too, I realize that what inspires me to take lean forward are the very experiments we carry out at Neo@Ogilvy (just like it was Blanca's stories that had inspired me to take a lean course). I realize that the best ambassadors for lean are those who work with it every day and experience the benefits it can bring.
Javier told us about lean in digital marketing here
Caterina Bianciardi, Lean Manager, Siena University Hospital - Siena, Italy
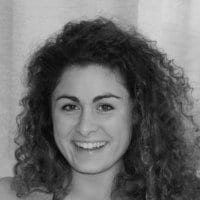
Our improvement projects at Azienda Ospedaliera Universitaria Senese call for the full engagement of our professionals. Whenever we want to solve a problem, the first thing we do is always going to the gemba to understand the situation in which the problem is occurring. And it is exactly from the gemba that ideas come from. Talking to people, listening to what they have to say, and discussing problems with them is where I get my lean inspiration from. Even short conversations can often lead to big breakthroughs.
Another huge source of inspiration is of course observing and benchmarking against other lean organizations. We often bring professionals who are interested in developing an improvement project to visit other organizations, within our hospital or outside, and help them see how similar problems were tackled there. And the inspiration we draw from those experiences is invaluable.
To read about the lean turnaround of Siena University Hospital, click here
Read more
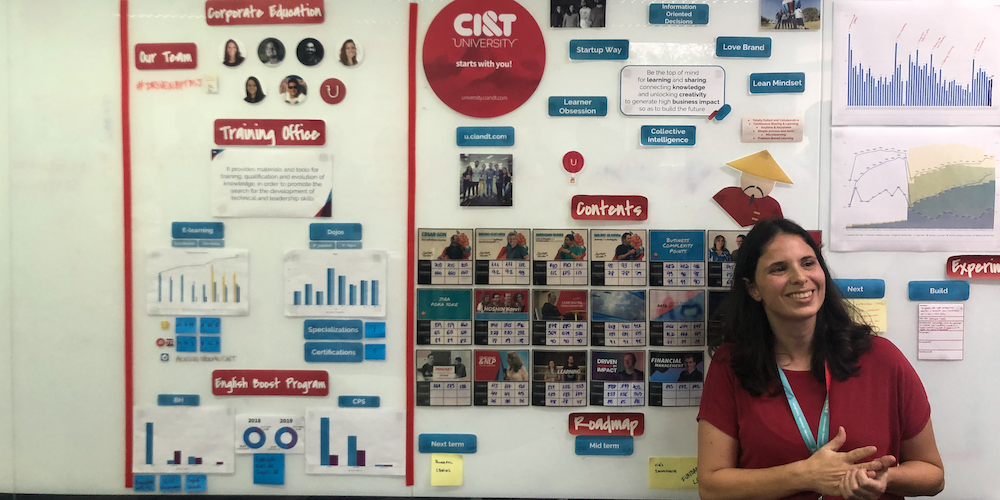
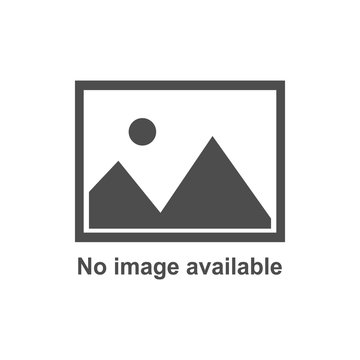
FEATURE – Last month, the Lean Global Network met in Brazil for its annual meeting. As part of it, we visited several amazing gembas. Three of our lean coaches reflect on what we learned.
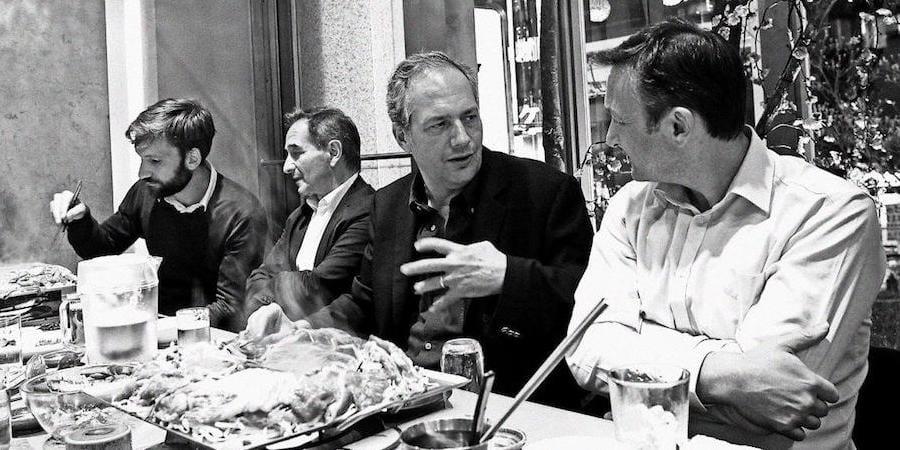
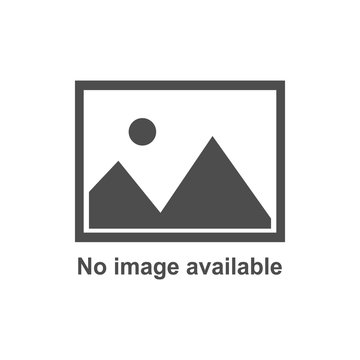
FEATURE – Following a visit to a Toyota supplier in Japan, the authors reflect on the nature of kaizen and explain why we might be looking for it in the wrong place.
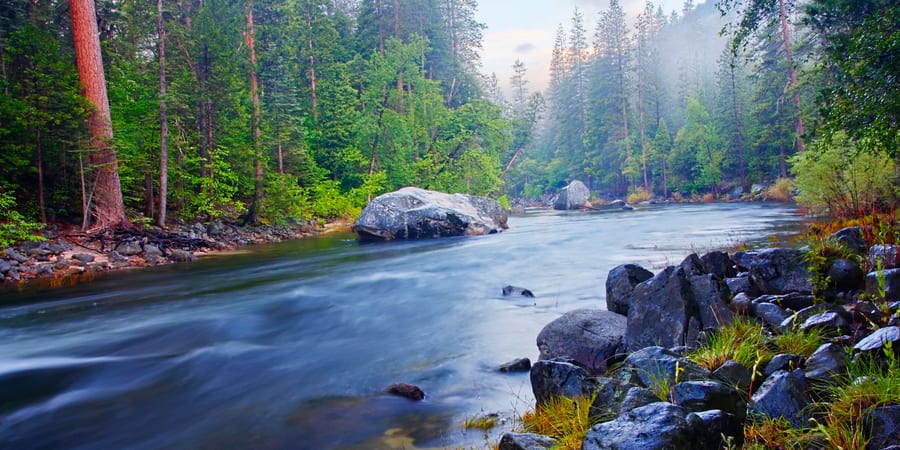
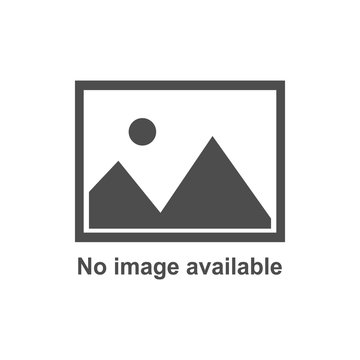
OPINION – Look at today's disruptive companies and you'll see how all of them have understood that real innovation calls for close proximity to the customer, rather than for stubbornly taking cover in the comfort of the upstream.
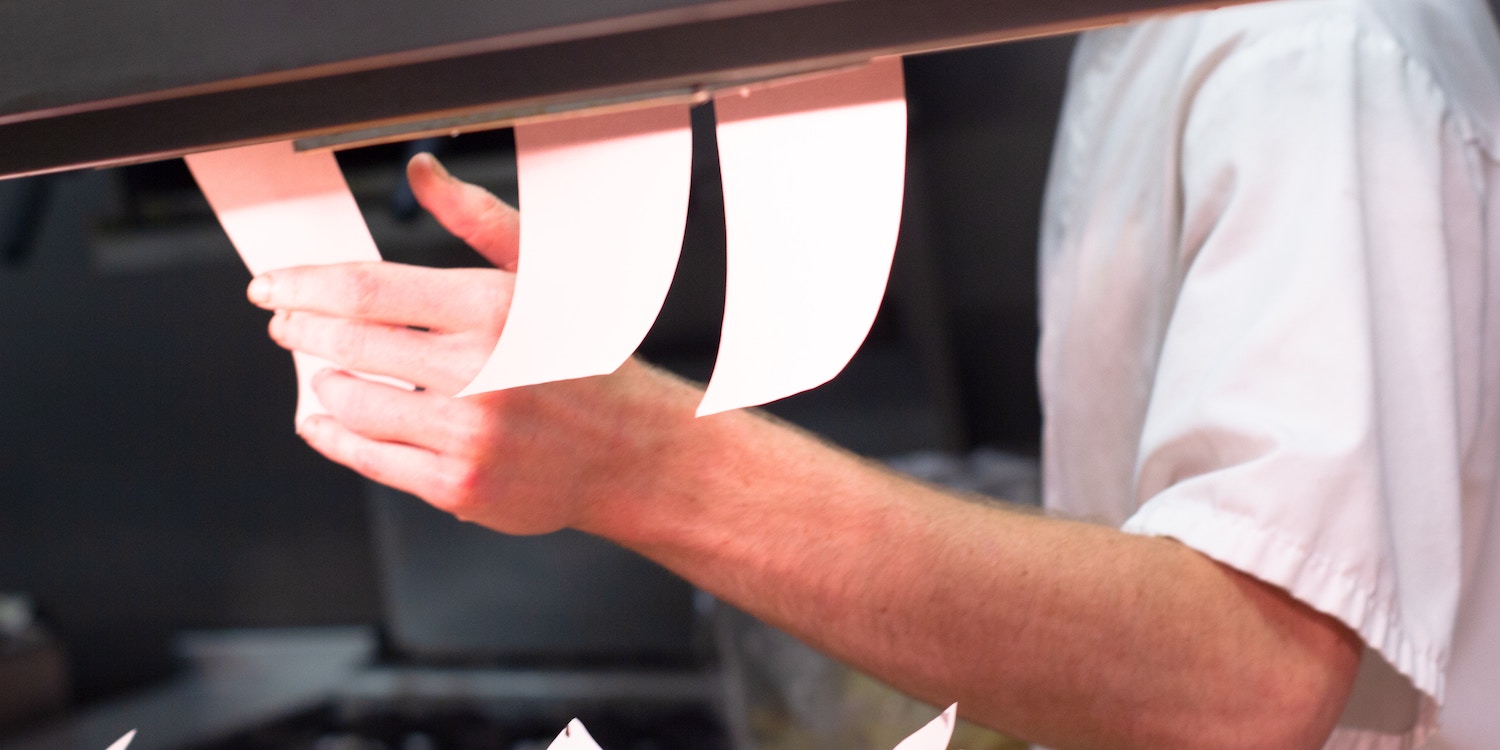
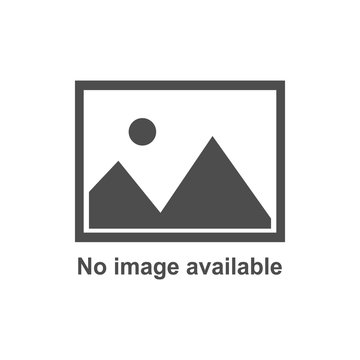
FEATURE – The author explores the relationship between kanban and improvement and discusses how using it can impact our lean transformation.