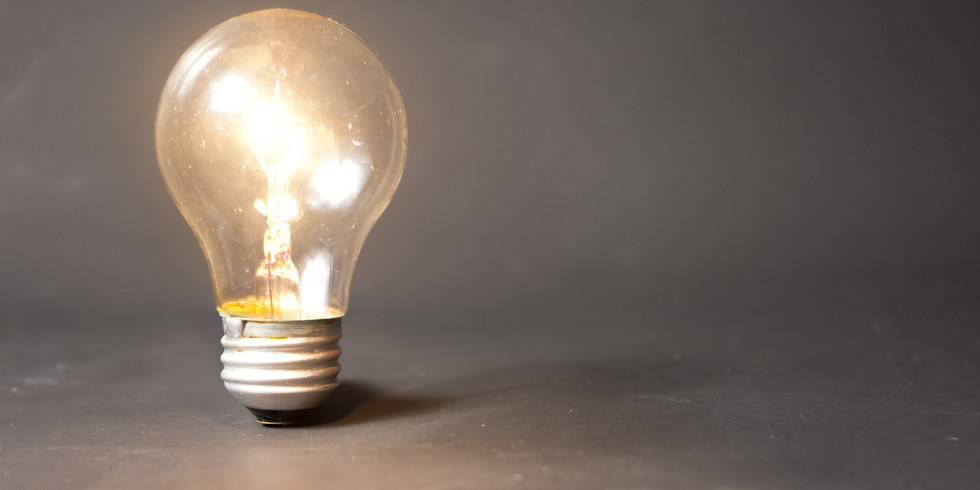
The paradox of learning
FEATURE – In this call to arms, the author encourages us to fight to prove the relevance of Lean Thinking in such difficult times and explains why only mastering it can truly address our problems.
Words: Michael Ballé, lean author, executive coach and co-founder of Institut Lean France
Mastery – in anything – is about lifelong deliberate practice. There is no way around this, whether in cooking, skiing or indeed leadership or Lean Thinking. Deliberate practice means taking one’s mind (and in sports, body) into one’s hand and deliberately practicing something difficult, again and again.
Any field of study is made of troublesome problems, problems which each student has to face and somehow master in a variety of contexts. Every time the problem occurs specifically, whether naturally or via an exercise, is the occasion of practicing learning: activating what one already knows, then elaborating on it to deepen that knowledge. If you’re playing with a band, keeping up your skill level will always be difficult. It drops off as soon as you stop practicing. Or listening to the other players and finding the mood of the song together. No matter how good you get, these problems remain: they are troublesome. You can progress at them, but never entirely solve them.
The learning environment can support this process by providing some situational interest (such as motivation to learn as part of a group) or scaffolding with methods and tutoring with mentors ahead on the learning curve. But ultimately, learning happens on one’s own – away from context, and is self-directed. Learning happens when one chooses to grapple with the problem on one’s own and try a new thought or a new action. Repeatedly trying new ways and practicing the old ones is what creates the learning curves that can be observed from the outside.
The lifelong hours spent deliberately practicing a skill – say, juggling – make you a master of it. Few people become masters, because few people have the patience and persistence to continue to practice. Many feel that once they’ve learned something, that’s good enough, they can move on. In Herbert Simon’s terms, most of us satisfice rather than maximize when it comes to skills.
The paradox is, however, that when one does devote oneself to a skill long enough to become a master at it, society often moves on. Craftsmen are replaced by robots, analysts by AI, and so on. Some skills simply seem to be socially relevant no matter how valuable they still are. Think of selling – the information asymmetry that used to make selling a sport and a joy both for salesperson and customer has turned around, and selling is now mostly a chore that stands between you and what you want. Or is it? There are still many, many complex products where selling is still necessary and would be fun for both if anyone still knew how to do it well. Or, for that matter – teaching.
As our environmental crisis looms larger by the day, lean is increasingly relevant. Lean is a system of troublesome problems:
- How can we satisfy customers more with less wasted resources?
- How can we react more quickly to technical problems?
- How can we reduce lead-times?
- How can we all better master our know-hows?
- How can we involve everyone in improving our ways of working step by step?
- How can we build greater trust between employees and management?
We know this leads to better environmental solutions because the whole point of lean is to do the same with better quality and less resources by using brainpower and collaboration to improve delivery systems. The catch, however, is that adopting Lean Thinking means lifelong practicing of the lean system, all the time, everywhere, and engaging others in adopting it as well.
To continue to convince people to engage in lifelong hours of deliberate practice with the lean thinking system we need to convince society that it is relevant, and relevant as an alternative to the mainstream way of doing business. We need to showcase lean successes. We need to show up at conferences and explain lean logic. We need to continue to argue that quality drives sales, lead-time reduction drives cash and technical know-how drives profitability. We need to create a social context that validates the effort in lifelong hours of learning.
We all need successes as much as we need to breathe, eat, and drink. Small daily successes, and large longer-term successes. Success makes us thrive, failure makes us shrink, and moral fiber is found in adversity when we find the energy to look for the success beyond the obstacles. Practice can be satisfying, but it’s also often hard – and few practices feel truly successful. This is why creating a positive context for learning matters, whether with our kids or with people we practice lean with. Without society recognizing its eventual success, practice is that much harder.
To sum up, lean is currently our best lead to reduce the pressure on the environment from industry. To succeed at lean, we need lean masters – people who have devoted enough lifelong hours to practicing with the troublesome problems of the lean system. To do so, we need to convince society that lean is a worldwide endeavor – not in the easy bits and pieces consultants love to sell, not in the “agile is mostly lean” sense, but in a full recognition of the lean system as a complete business system. We need to stand and be counted.
THE AUTHOR
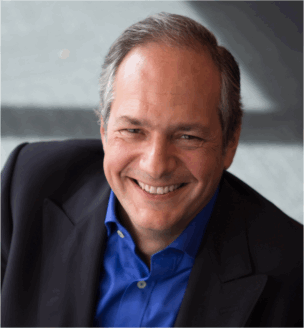
Read more
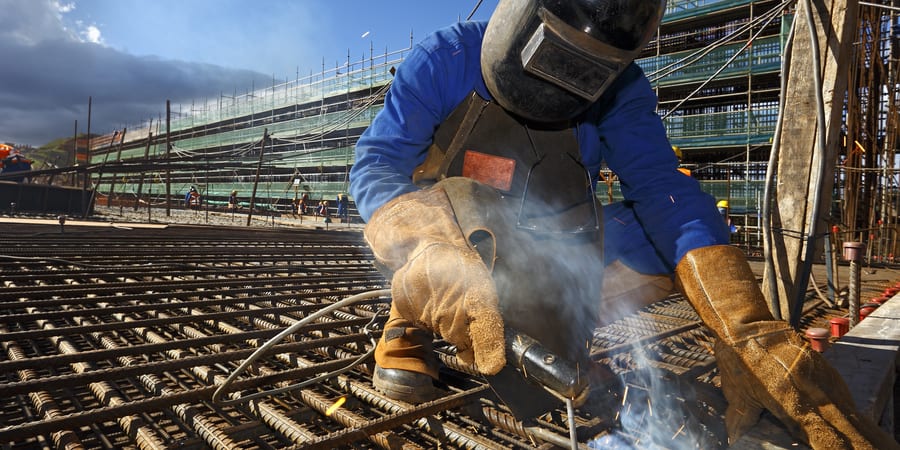
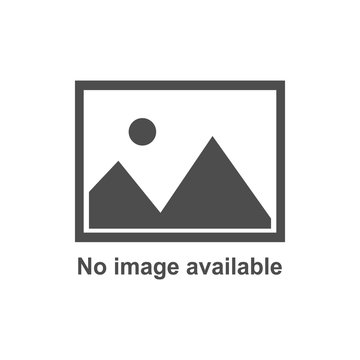
WOMACK’S YOKOTEN – If truly embraced, lean thinking sustains and (in the long run) even creates jobs, but if a transformation is to last these jobs must be “good,” says Jim Womack.
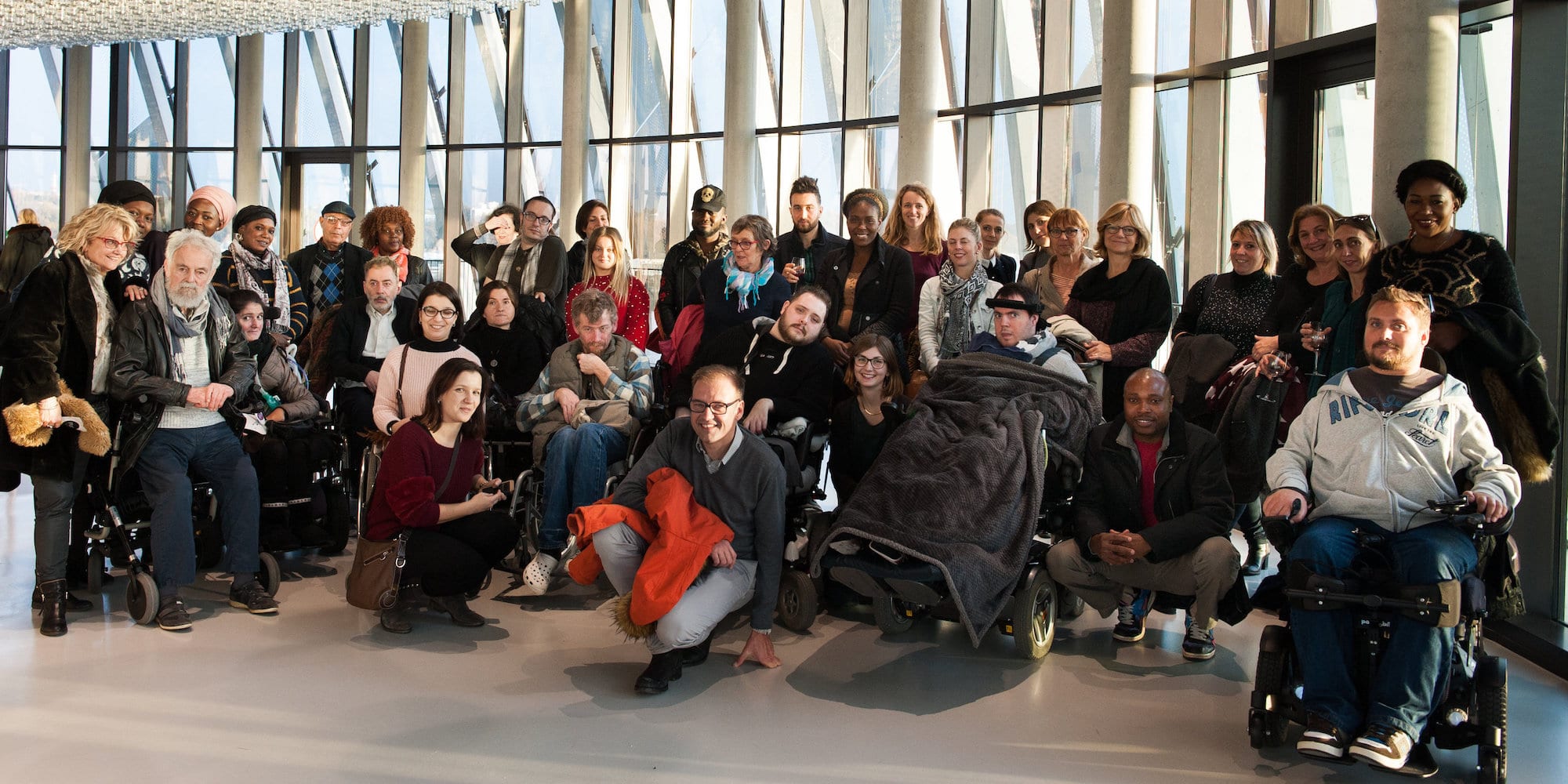
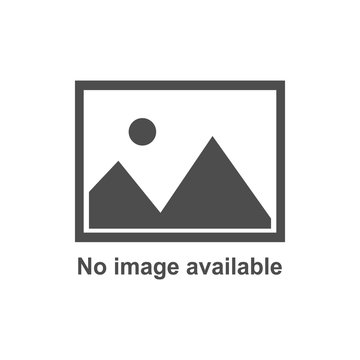
NOTES FROM THE GEMBA – This French company provides support to the severely disabled, and is currently using lean thinking to limit employee turnover and recruit faster.
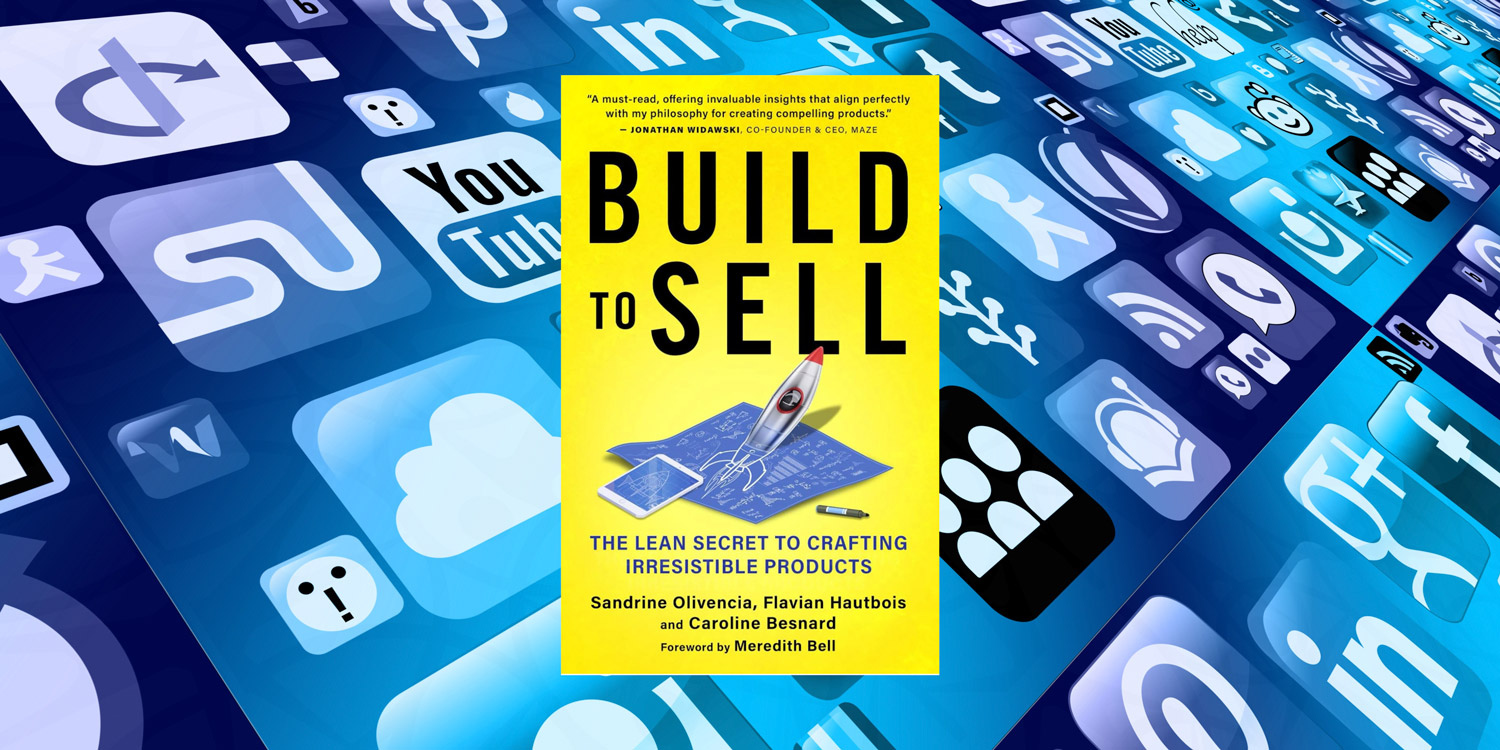
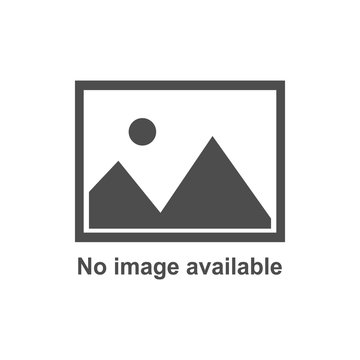
FEATURE - Presenting the key concepts in her latest book, the author tells us how to escape the feature frenzy trap and build products customers love.
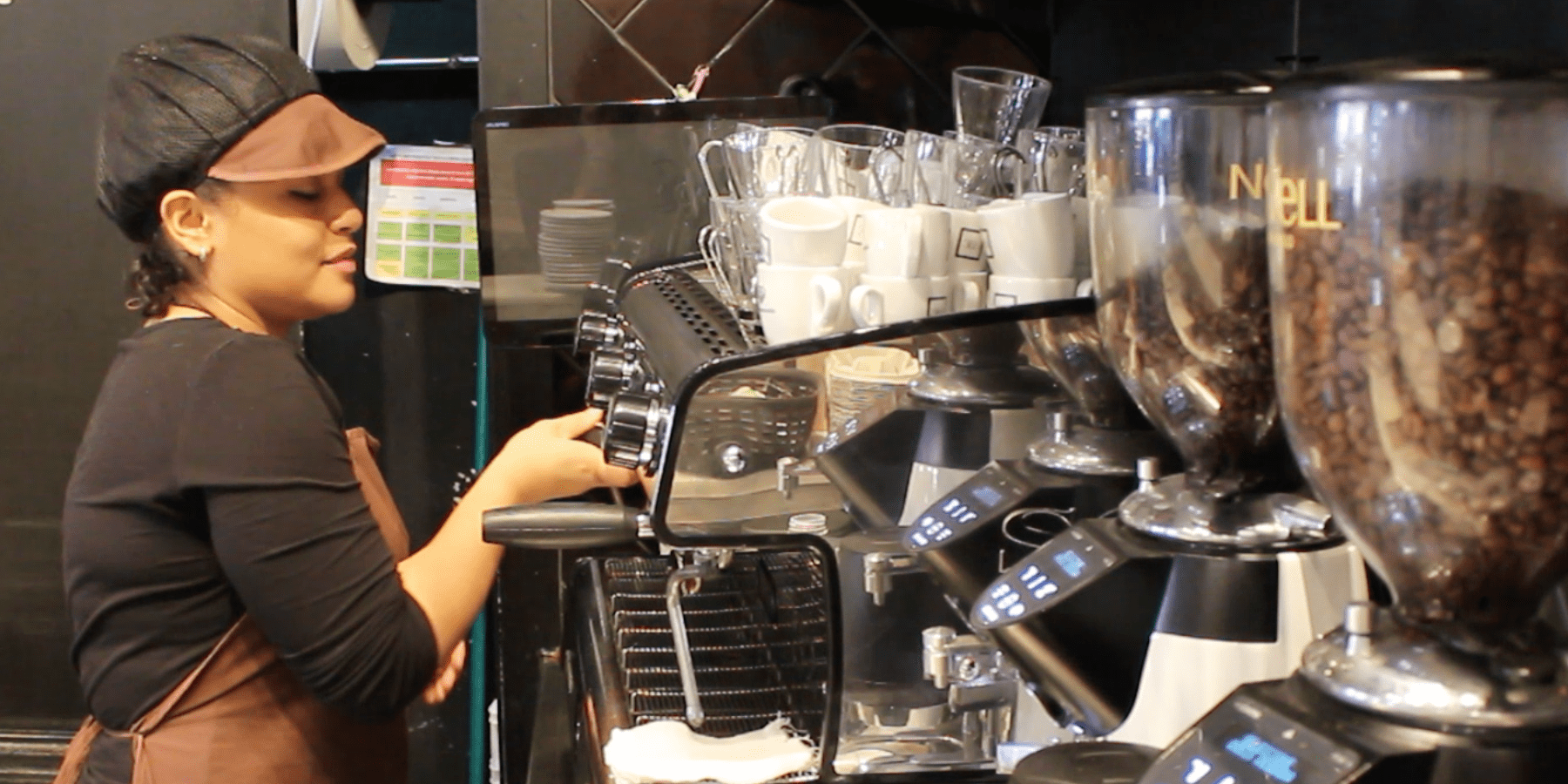
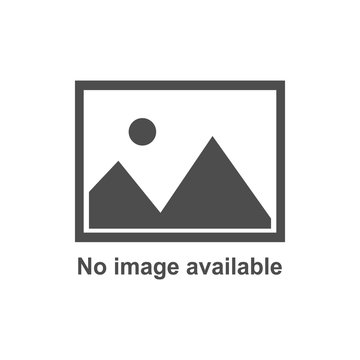
THE LEAN BAKERY – In this video, a shop coordinator explains how the 365 bakeries were able to speed up service to customers and ensure product quality by reorganizing work and responsibilities.