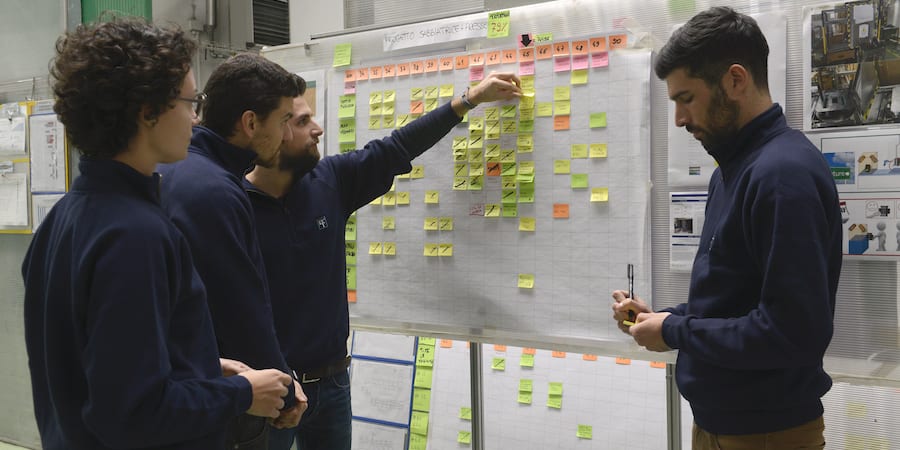
How we pioneered lean in Italy and are still leading the way
INTERVIEW – At the European Lean Summit in Venice, our editor sat down with Italy’s lean CEO extraordinaire. His company, which serves the natural gas industry, has been on the journey for almost two decades.
Interviewee: Mario Nardi, CEO, Pietro Fiorentini
Roberto Priolo: Piero Fiorentini has been on its lean journey for a long time – 17 years to be exact. What led you to embrace the methodology in the first place?
Mario Nardi: Our margins were not satisfying and the climate in the organization was not ideal. Pietro Fiorentini wasn’t doing poorly, but it wasn’t performing as well as we knew it could. We started our journey full of hopes, and lean didn’t disappoint us. At the time, lean was mostly uncharted territory. There wasn’t a ton of literature like there is now, which meant that ours was more a leap of faith than anything else. We relied on what we saw as common sense.
RP: How did you get started?
MN: Thanks to our late friend Alberto Galgano, a pioneer of the Italian lean movement, who one evening had John Black as a guest at an event (he famously implemented lean at Boeing and studied TPS with Chihiro Nakao). We ran our very first kaizen event with him, a very disruptive experience with a lot of symbolic moments: at Pietro Fiorentini, we all remember when John asked me to demolish a 30-meter wall in our manufacturing site… by the following morning. This was a way to gauge our commitment and demonstrate that anything is possible, but there was also a very practical reason for wanting the wall gone: it prevented two batching processes to be put in a continuous flow. That first momentous experience marked the beginning of our journey, which progressed with more kaizen events and the gradual development of internal lean capabilities across the business.
RP: What’s the most important lesson you have learned over the course of such a long journey?
MN: More than anything, I have learned how much an organization can benefit from investing on its human capital, particularly young, motivated people who are eager to take on new challenges. This is very much our biggest focus: we wanted to find people with the right attitude and skills that we can turn into our managers of the future. The commitment they give us and the effort they put into helping Pietro Fiorentini succeed is something I am extremely proud of.
RP: What makes Pietro Fiorentini’s journey unique, in your opinion?
MN: Our determination and the intensity of our effort. We never stopped at the quick wins, knowing that the further we go, the less we know. Working towards gradually mastering our ability to identify and remove waste from our processes is a challenging and enriching endeavour.
RP: How have you changed as a leader over the course of the lean transformation?
MN: My approach to leadership has shifted completely. At first my leadership style was directive, becoming more and more participative along the journey. At the same time, I have made sure that people at the front line are empowered and given responsibility to drive change themselves. I have found this is a virtuous cycle, where the change in leadership starts to enable teamwork and the two mutually reinforce each other going forward. At Pietro Fiorentini we follow an inverted pyramid structure: top leaders are at the service of the people, to remove all the obstacles that prevent them from doing their job. This is a fundamentally different way of perceiving your role as a manager.
RP: In your experience, what are the pre-conditions for lean success?
MN: In my experience, a good lean journey fundamentally requires three things: commitment; external support (simply because one doesn't necessarily know the subject at first, or because understanding is not always easy); and young, dynamic people who possess those soft skills we can leverage to transform them into leaders. Commitment should be guaranteed over time, but this often doesn’t happen because leadership at the top changes frequently or because, unfortunately, CEOs tend to be more interested in their careers than in the success of the business. That is a massive limitation.
RP: Like any other country, Italy could benefit from more lean. How can we ensure the use of this philosophy becomes more prevalent?
MN: First of all, we need to provide more structured lean education in high schools, universities, business associations, and so on. I can tell you that, at least in the case if Italy, we should perhaps talk not only about Industry 4.0 but also about lean management.
THE INTERVIEWEE
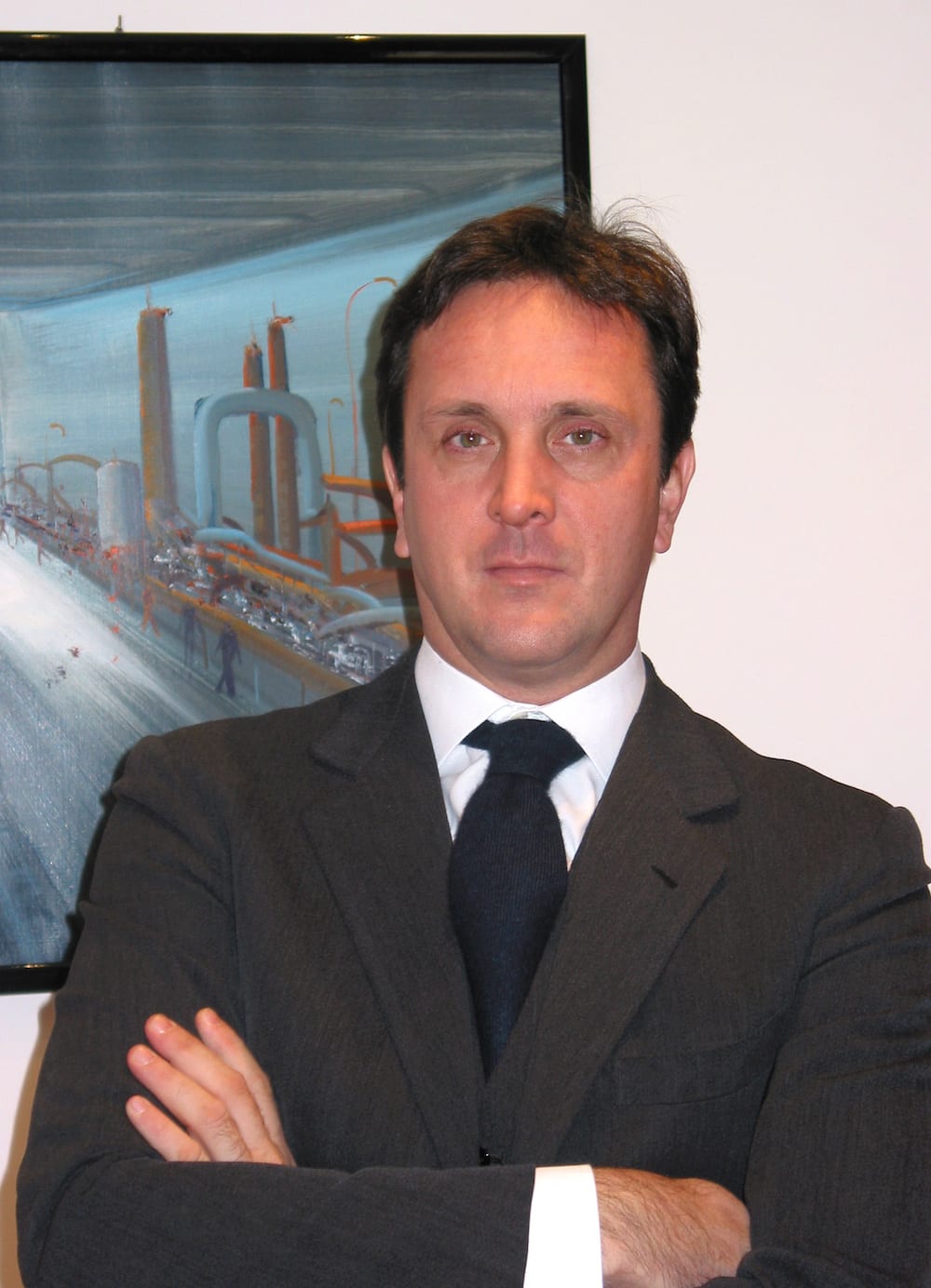
Read more
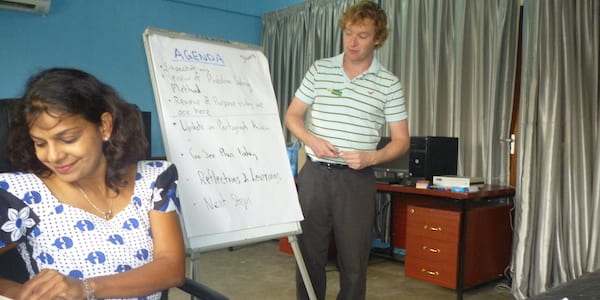
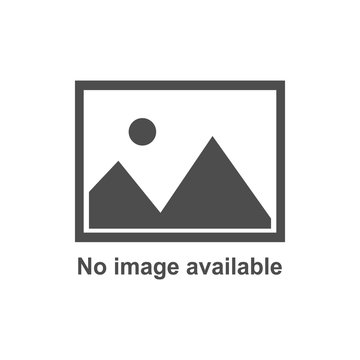
FEATURE – What makes a mentor-mentee relationship successful? This intimate account comes all of the way from a Tanzania healthcare organization, and proves how lean is fundamentally about “caring for people.”
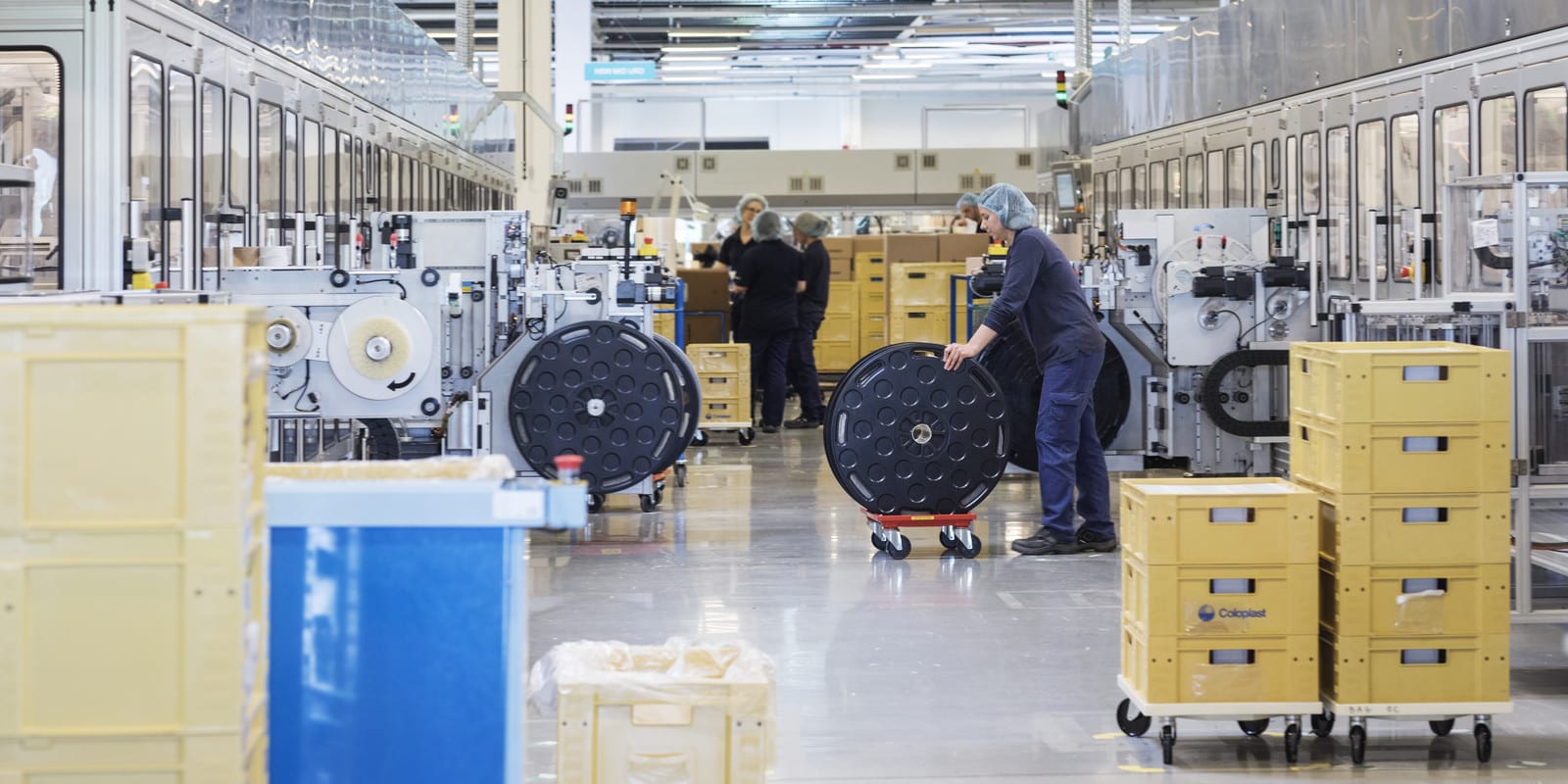
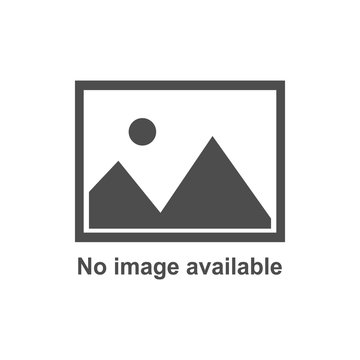
CASE STUDY – The author looks back at the impressive lean transformation of the Hungarian plant of Coloplast, a Danish company offering medical devices and services.
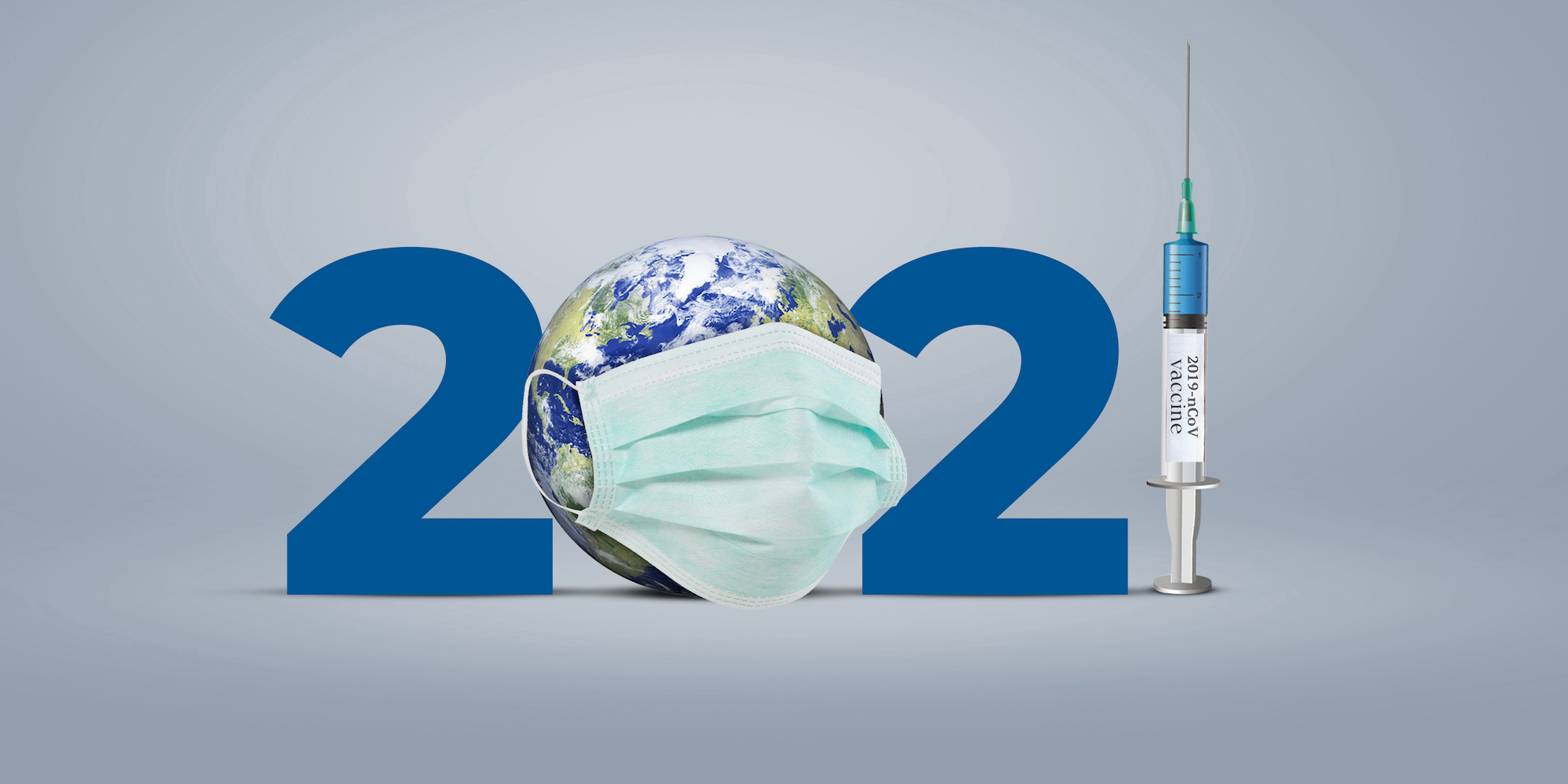
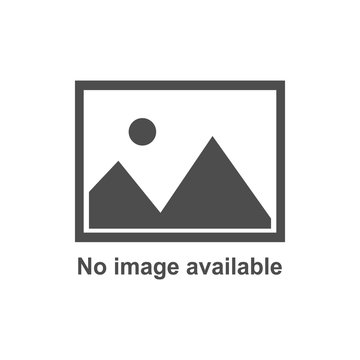
FEATURE – As 2020 finally draws to an end, our editor reflects on the year that was and discusses why the Lean Community is a such an important source of inspiration and hope.
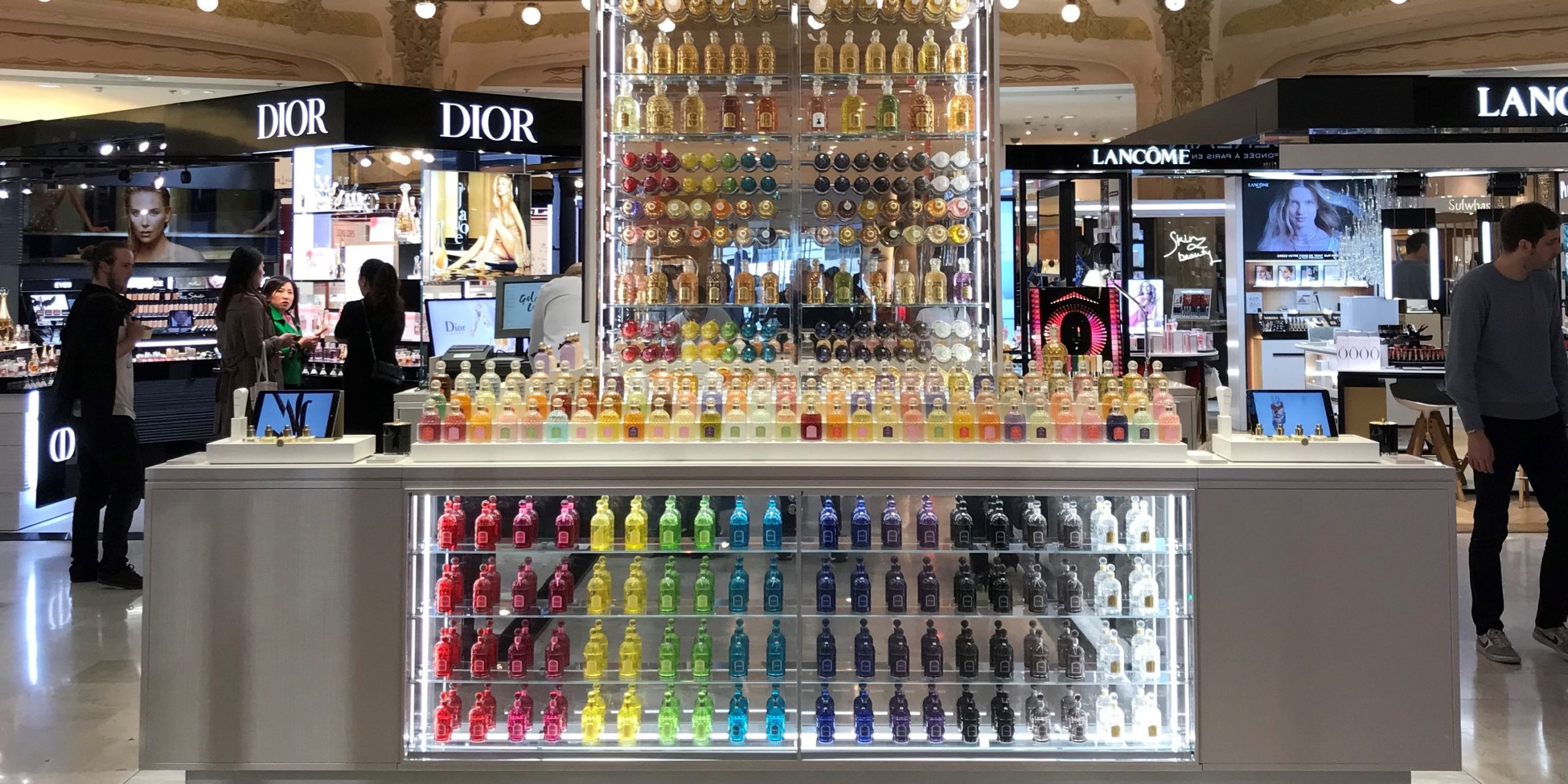
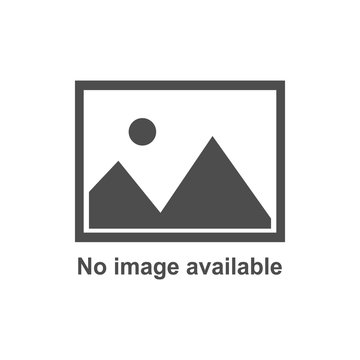
NOTES FROM THE GEMBA – How do you kick off a lean journey? This French company has chosen to begin by analyzing and tackling each customer complaint.