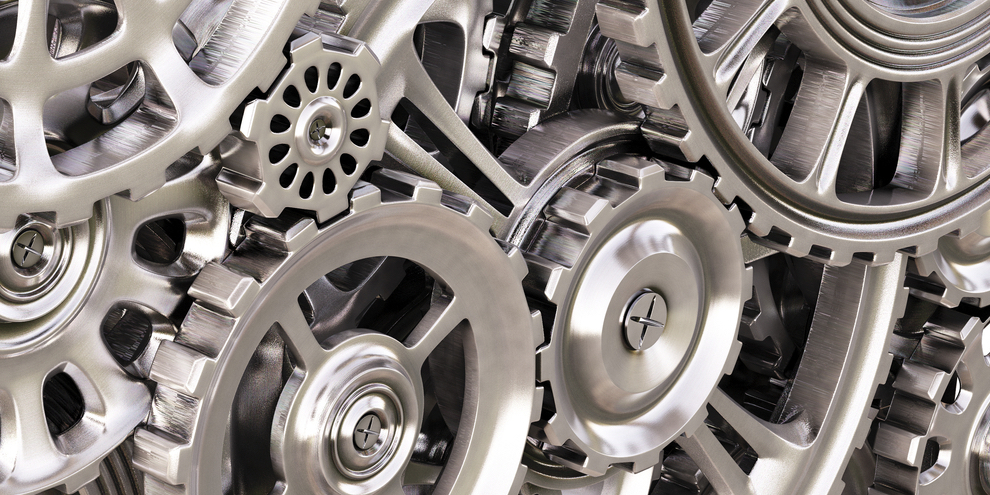
7 tools to establish pull production
FEATURE – Kanban is the best-known method to establish pull production, but it is not the only one. Here’s a few other ways you can create a pull system.
Words: Christoph Roser
There are many misconceptions on what a pull system is. In my experience, there are three requirements for a pull system to exist:
- An explicit target limit on your inventory or workload.
- A signal must be released when an item or batch of items leaves the system. For batches of material, the signal can be with either the first or the last item in a batch.
- This signal must start replenishment for make-to-stock items or release the next job for make-to-order items. The replenishment or release must be the same quantity or the same workload as the items that left the system.
Miss any one of these requirements, and you’ll find yourself with a push system on your hands. (See also my post The (True) Difference Between Push and Pull).
In this article, I’d like to introduce you to the many different ways to establish pull systems.
Almost Pull: FIFO

This one may surprise you, but First-In-First-Out (FIFO) is not only an excellent tool for material flow, but also a rudimentary pull system. There is an upper limit on the inventory. When a part leaves, a space opens up, which is the signal for the preceding process to fill up this space. The only thing missing from FIFO is that while an empty slot signals the preceding process to produce, it does not signal what to produce.
Hence, if you use only FIFO, you will need additional information on what to produce. In reality, FIFO is typically part of a larger production system, and the information on what to produce is provided, often even through a pull system.
Kanban
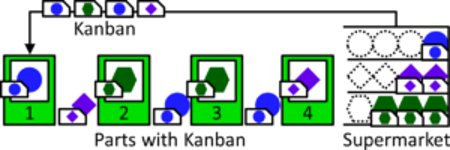
This is the best-known way to establish pull production. The inventory is limited by the number of kanbans. If a part leaves the system, the kanban returns to the beginning of the loop and reinitiates production. Effectively, the kanban is the signal. This is one of the easiest ways to implement pull, and there are even different types of kanban systems.
Production kanban and transport kanban work very in a very similar way, except that the former reproduces and the latter redelivers. If you have only two kanban for one part type, it is often called a two-bin kanban system: one box of parts is used, while another one is replenished. A triangle kanban has only one kanban per part type, which reduces ordering effort at the cost of a slightly higher inventory.
CONWIP
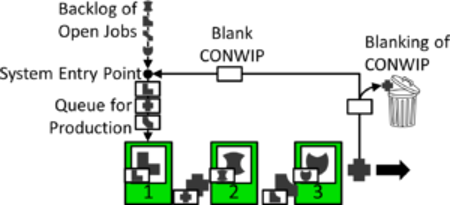
Kanban and its variations are excellent tools to establish pull production. Unfortunately, these work only for make-to-stock production. So, what to do when we are operating in a make-to-order setting? We can use what’s generally called CONWIP – or Constant Work in Progress (at Toyota it’s called Type B Kanban). Many companies use this system without ever giving it a name.
The method is very similar to Kanban, except for the fact that a Kanban card is permanently assigned to a certain part type (we have therefore different kanban for different part types). CONWIP is for make-to-order production, and its cards are blanked whenever a finished job leaves the system. A returning blank CONWIP card signals that the next job can start. To know which job to start, you need a (prioritized) backlog of open jobs. A returning blank CONWIP card gets attached to the next available job in the backlog – a process known as “system entry”.
Overall, CONWIP limits the number of jobs in the system. Whenever a job leaves, a signal is given to start the next one. This approach, best suited for make-to-order, can be easily combined with Kanban.
POLCA
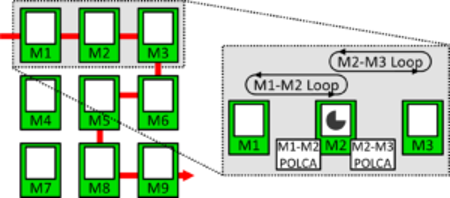
POLCA stands for “paired-cell overlapping loops of cards with authorization” and was developed by Rajan Suri around 1990. It is designed for low-volume-high-mix production and intended for job shops. It is an alternative to CONWIP. While both can be used on job shops, POLCA is slightly better at controlling the inventory – even though it is more cumbersome to implement and maintain. POLCA is also not designed for flow lines, but for job shops and networks of cells.
Reorder Point
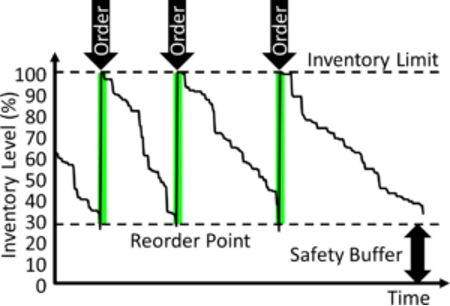
Reorder point and the closely related reorder period method for managing inventory is also a pull system. You have your target inventory and a reorder point. Whenever the inventory reaches the reorder point, you order enough material to re-fill the inventory to the target.
Reorder point is most-commonly found in purchasing, but sometimes it is deployed in production too (always in make-to-stock or purchase-to-stock situations, however). Its function is very similar to that of the triangle Kanban.
Drum-Buffer-Rope
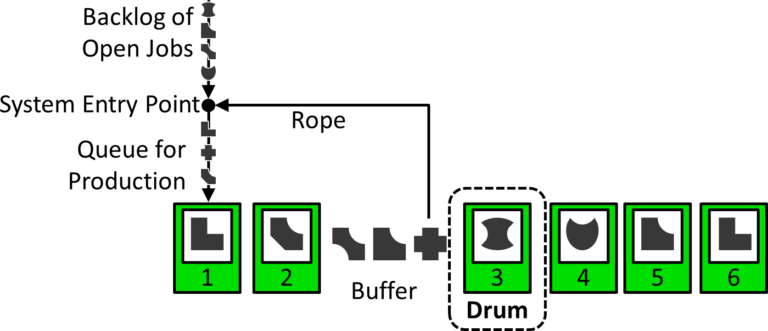
Drum-Buffer-Rope (DBR) originated with Goldratt and his Theory of Constraints. It is similar to Kanban or CONWIP, but with a few key differences. Drum-Buffer-Rope usually measures not the quantity of parts, but the level of workload in the system. This sort of workload control is very accurate but requires a lot of effort. Therefore, I’d avoid workload control unless my parts have enormously different workloads, and even then I may just stick to Kanban or CONWIP. Besides, you can also adjust CONWIP to use workload control, resulting in a system similar to Drum-Buffer-Rope, but much better.
The reason CONWIP is better is that Drum-Buffer-Rope has the limitation that the pull loop ends at the bottleneck (or the customer). It only has a single loop, which may not even cover the entire value stream. It also assumes that the bottleneck is fixed, which it rarely is. Unless you are a lover of Drum-Buffer-Rope, stay away from this.
COBACABANA (Theoretical Only)
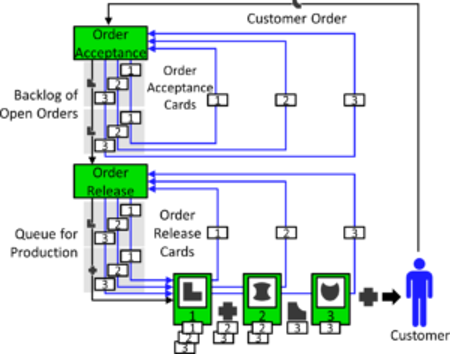
COBACABANA, is a pull method developed by Martin Land and improved by Matthias Thürer. It is entirely paper based, but rather complicated, requiring several cards for each job. In theory, it is a complicated but solid system.
Unfortunately, to my knowledge, there is no real-world application of this method yet. Unless you love to try out new and untested methods, I would advise against using it.
SUMMARY
Chances are you already knew Kanban and perhaps a couple more of these tools, but I’d be surprised if you knew all of them (unless they have already read my book, that is). This wide array of tools gives you different options to establish pull. Which one is right for you? For the answer to this question, you’ll have to wait for my next post.
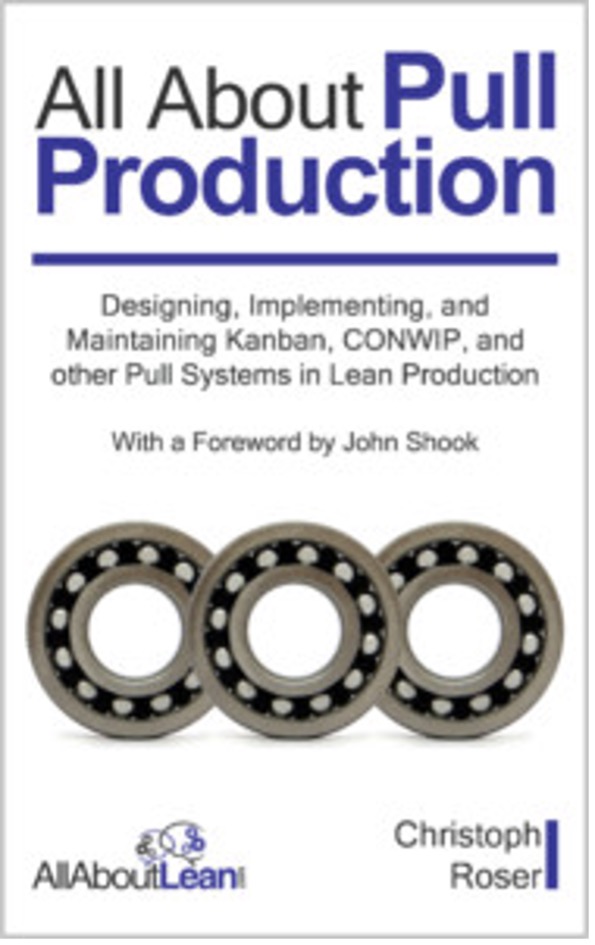
This article, originally published on All About Lean, is loosely based on Christoph's new book All About Pull Production: Designing, Implementing, and Maintaining Kanban, CONWIP, and other Pull Systems in Lean Production, a practical guide for anyone looking to implement pull systems.
THE AUTHOR
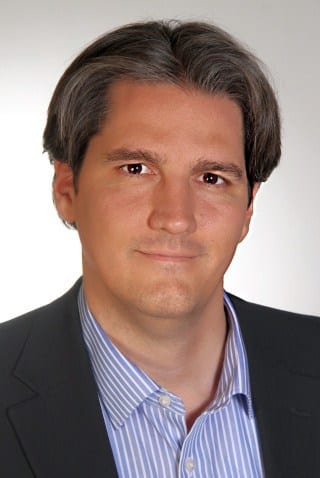
Christoph Roser is Professor of Production Management at the Karlsruhe University of Applied Sciences. He writes based on decades of experience in implementing, researching, and teaching lean manufacturing, including five years working at and researching for Toyota in Japan.
Read more
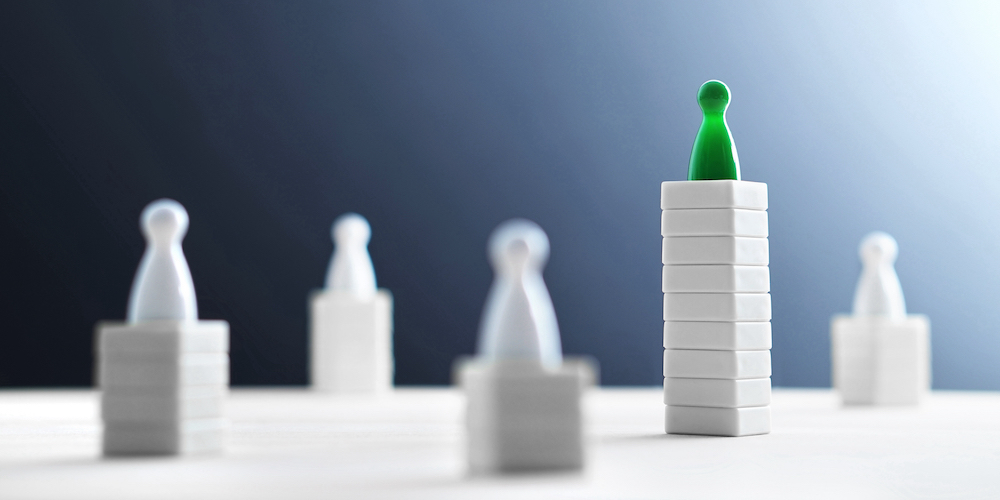
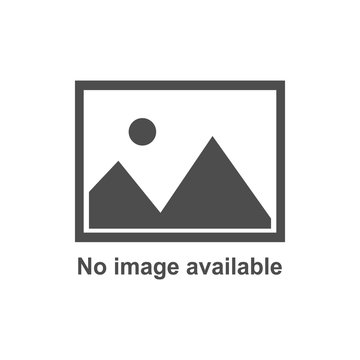
FEATURE – Lean represents a strategy to understand what needs to be improved, the critical skills that must be developed to solve a specific problem – whether it’s a quality defect or a pandemic.
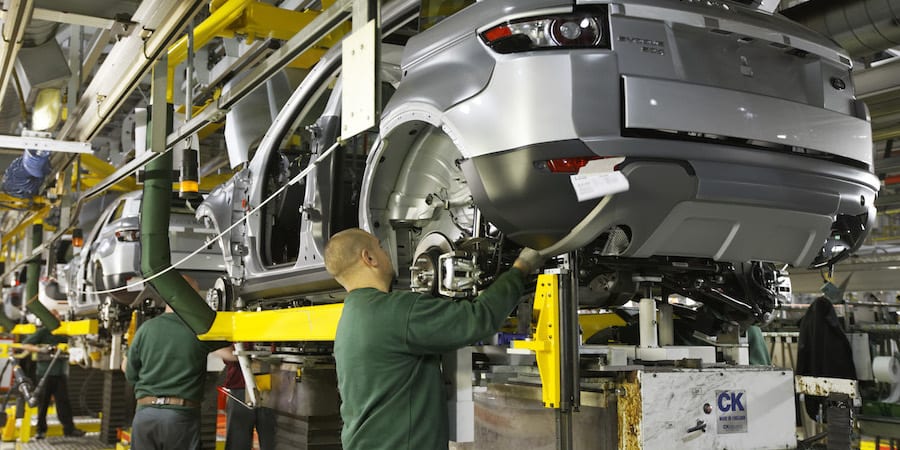
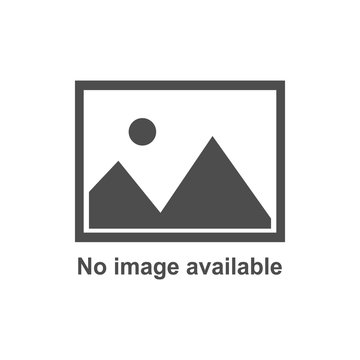
INTERVIEW – Following two successful experiments with kanban boards, Jaguar Land Rover decided to extend the reach of its lean product development activities to include all new vehicle programs. Here’s how the story unfolded.
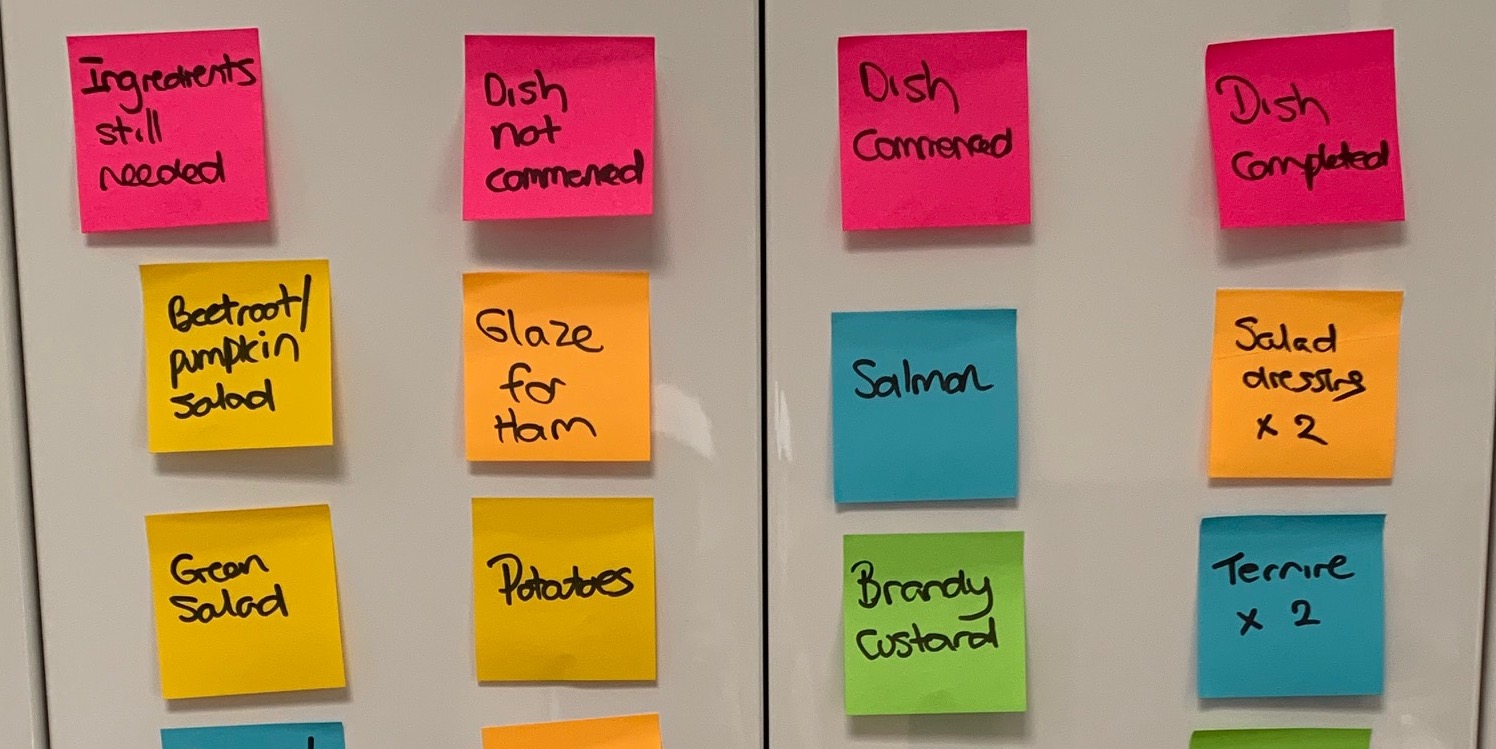
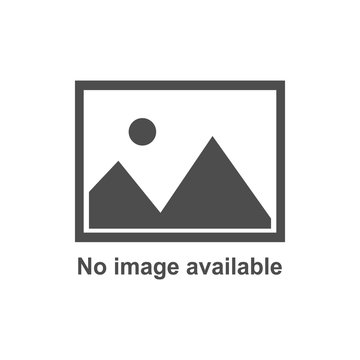
FEATURE – The holidays are a time for reflection. The author shares some her reflections on her experience with lean thinking and the role of leadership in a lean transformation.
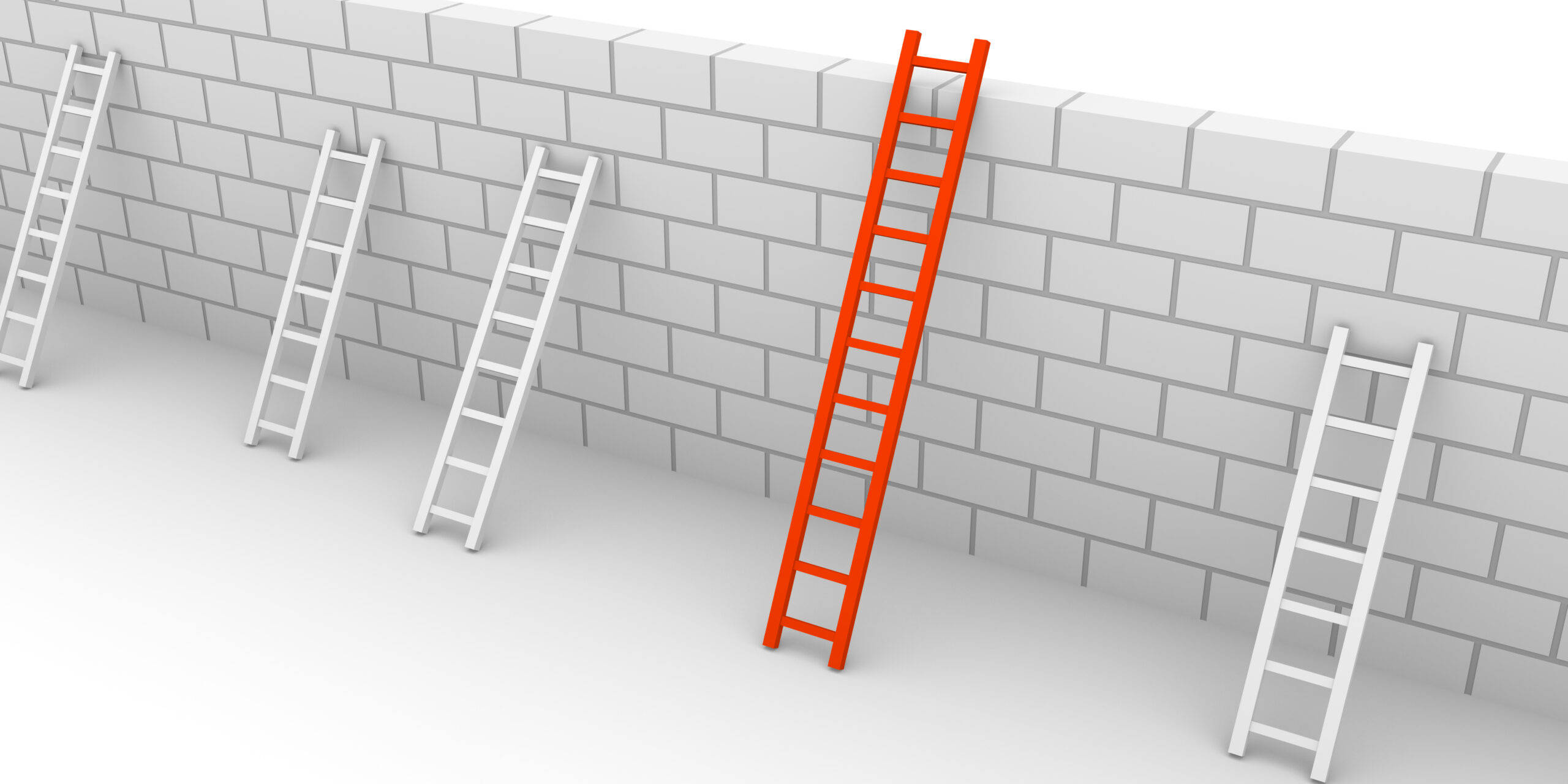
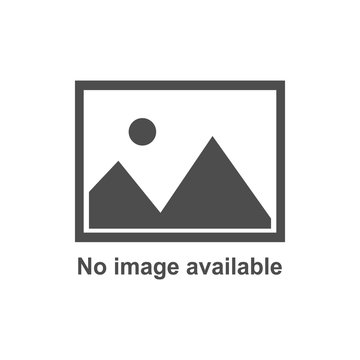
FEATURE – Leading by solving problems is a key trait of any lean leader, but it is important to understand that not all problems are their prerogative.