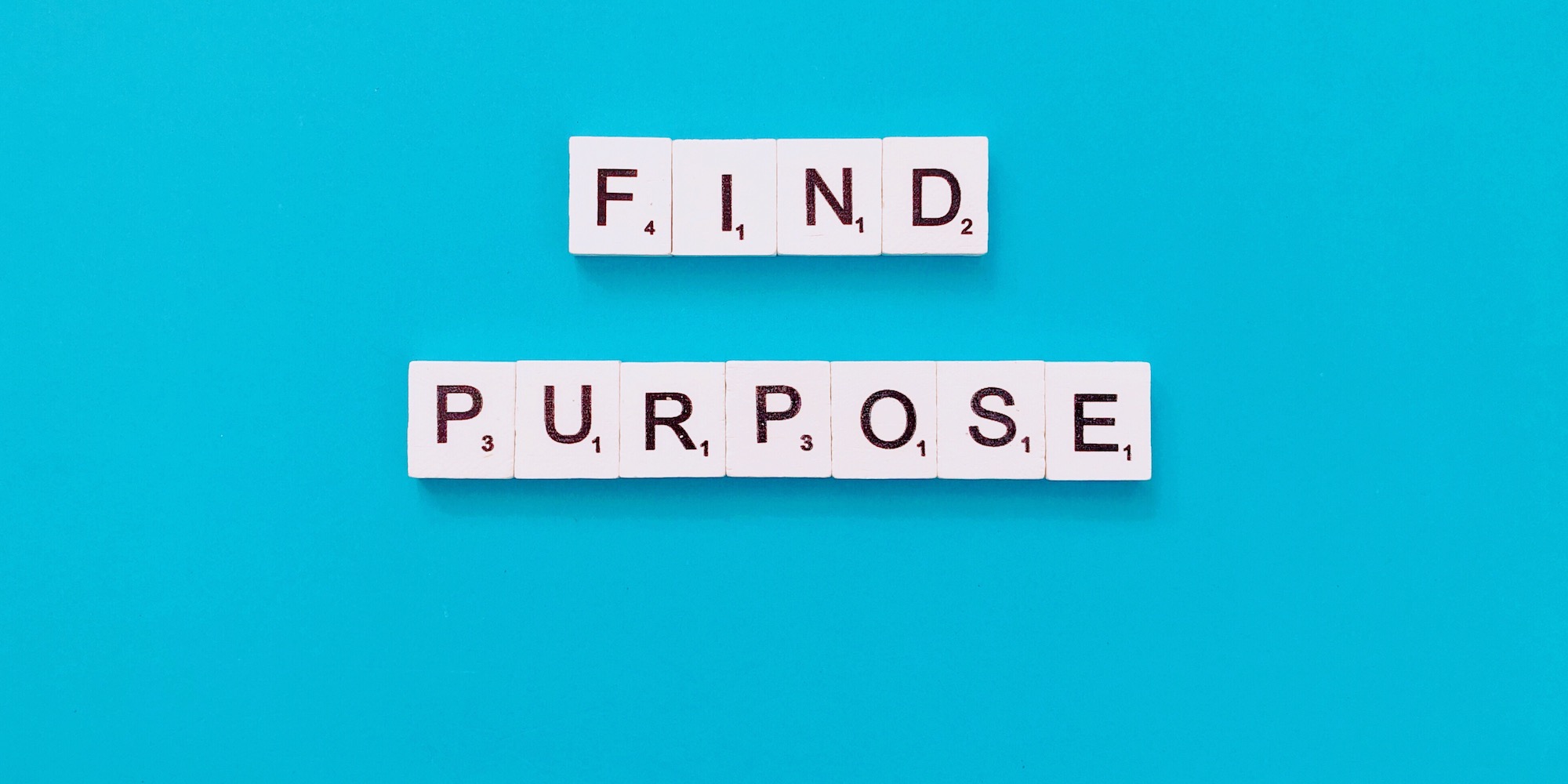
The comfort of purpose
FEATURE – Why is lean change so hard to achieve in times of plenty? And why does it seem to be more attainable when chaos reigns? The author tries to answer these questions.
Words: Sharon Visser
I recently came across a photograph of Princess Elizabeth when she was 18. During the war, she trained as a truck driver and mechanic, which made me think a great deal about leadership, where it starts, and what it really is.
The image of the future Queen of England on her knees changing a tire had a huge impact on the British public at the time, mostly because she was showing respect to the people doing the work. In the eyes of the British, she was recognizing the important and honorable work of changing tires. At that moment, she was living her purpose.
I recently participated in the Lean Summit in the UK, where I was lucky enough to listen to a presentation by Serhii Komberianov of Lean Institute Ukraine about lean in a war zone. I was inspired by the sense of peace he conveyed as he spoke, despite the chaos, dangers, and disruptions Ukrainians are now experiencing on a daily basis.
I then realized, what I was seeing was a person who is living his purpose and leading his team through difficult times. His weapon of choice? Removing chaos and creating an oasis of calm where productivity can thrive using Lean Thinking.
If we look at the roots of Lean Thinking, an unexpected and somewhat grim connection with war can be found. Think about TWI, which was devised to boost production to support the war effort during World War 2, or even further back to the 16th-century Arsenal in Venice, where warships were built. This isn’t to say, of course, that lean promotes war. In fact, I believe it is a great advocate for “peace by means of prosperity”. But it is a fact that to achieve a lean turnaround is much harder in times of peace and plenty (which is why we often use the mantra “if you don’t have a crisis, create one”). But what makes lean work so well under war or war-like circumstances?
Is it a survival response? Or is there something much deeper happening?
I believe that during times of war – when Queens become mechanics and mechanics become heroes – there is a great leveling provided by a purpose that people believe in passionately. There is nothing opaque about it and the consequences of not achieving it are as clear as day.
What is the result of this great leveling and connection to purpose?
First of all, when we connect, we can create together, and when we create together with a purpose, very little can get in our way. This connection to purpose makes us more courageous, but also more empathetic, as other team members fill in the gap for us and we fill in the gap for them. We have much to learn about creating at times of peace the same strong connection to purpose that we feel during a war.
Within the Lean Transformation Framework house, the roof is what symbolizes purpose. We learn to make that purpose clear, but seldom mention the consequences of failure. It’s too uncomfortable, too threatening. It’s not like we are in a war, right? Maybe not, but for many front-line workers every day is a battle to make ends meet, feed, clothe and educate their children, or look after elderly parents or family members with serious illnesses and disabilities. If you investigated this within your organization, you’d be amazed at the burdens ordinary people carry bravely and often secretly day after day.
I urge to take another look at your purpose statement, trying to see it with new eyes and understand that if we fail to generate the required revenues and stability within the workplace, people will be impacted. What would a loss of work mean to them? While you are looking, try to see if you can give your brave people better days at work by showing respect for what they do and allowing them to do their work in the best possible conditions.
Each one of us will have a different way of doing this, but in all cases it will require us to follow Princess Elizabeth’s example and be prepared to accept the discomfort of changing a tire or two.
THE AUTHOR
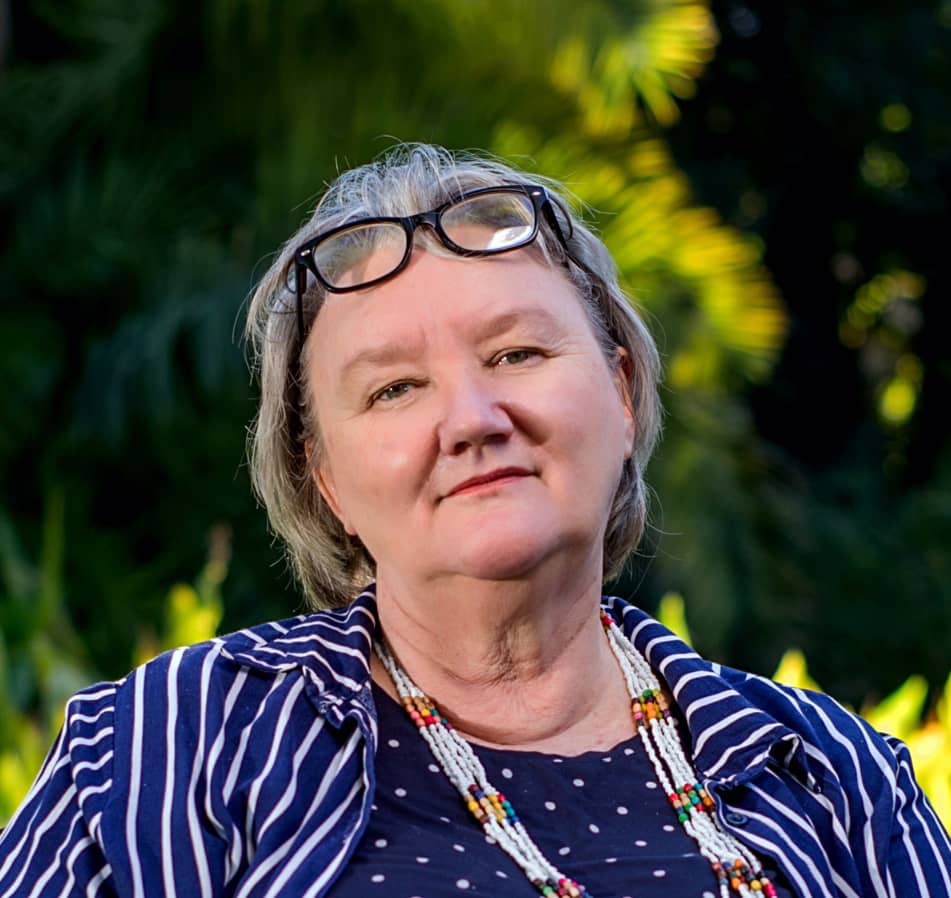
Read more
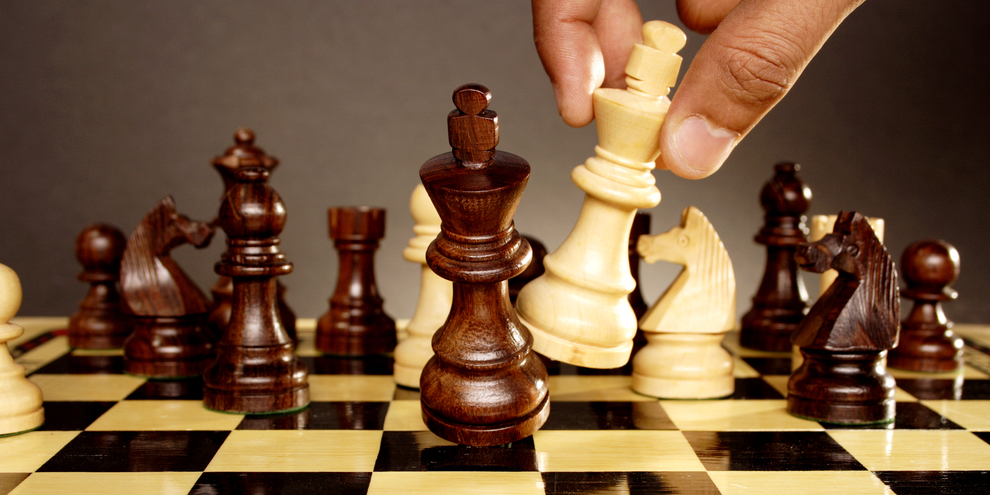
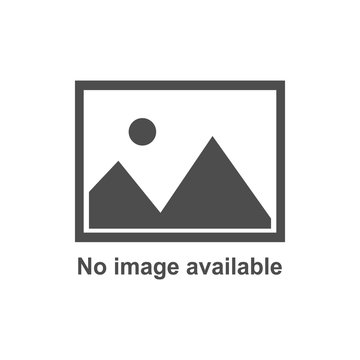
ROUNDUP – In the last roundup on lean tools and concepts of the year, our editor collects and curates the best articles on strategy deployment (hoshin kanri).
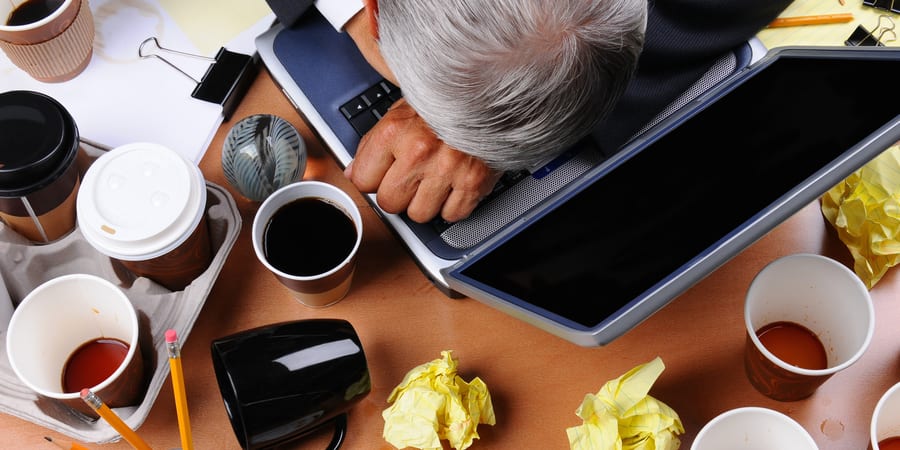
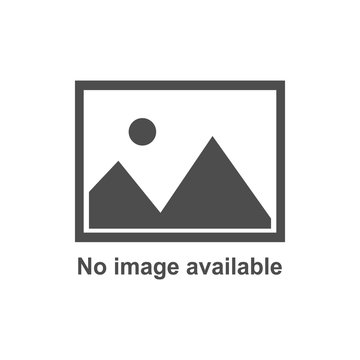
FEATURE ARTICLE - With 2015 drawing to an end, it's time to look back at the year that was and at the articles that our readers have enjoyed reading the most. So here is the Top 10 most read articles of 2015 on Planet Lean.
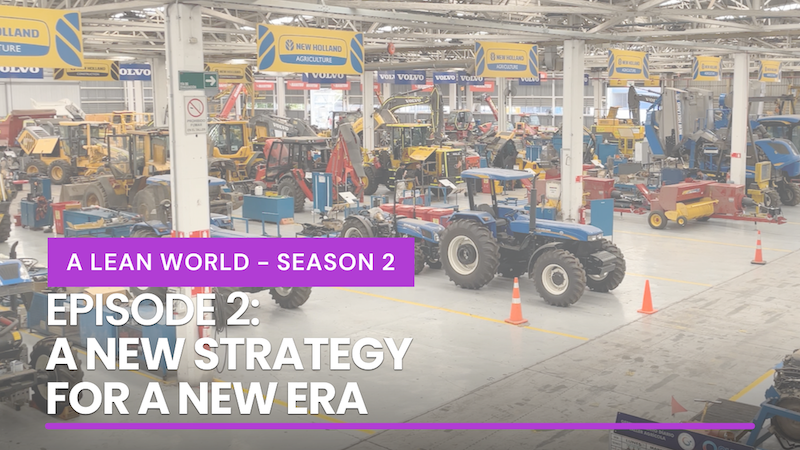
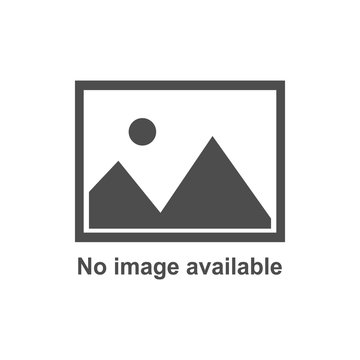
WEB SERIES – In the second episode of our docuseries on lean in Chile, we learn how, with a clear purpose and strong commitment from leadership, SKC is transforming its processes and mindset and building a competitive advantage.
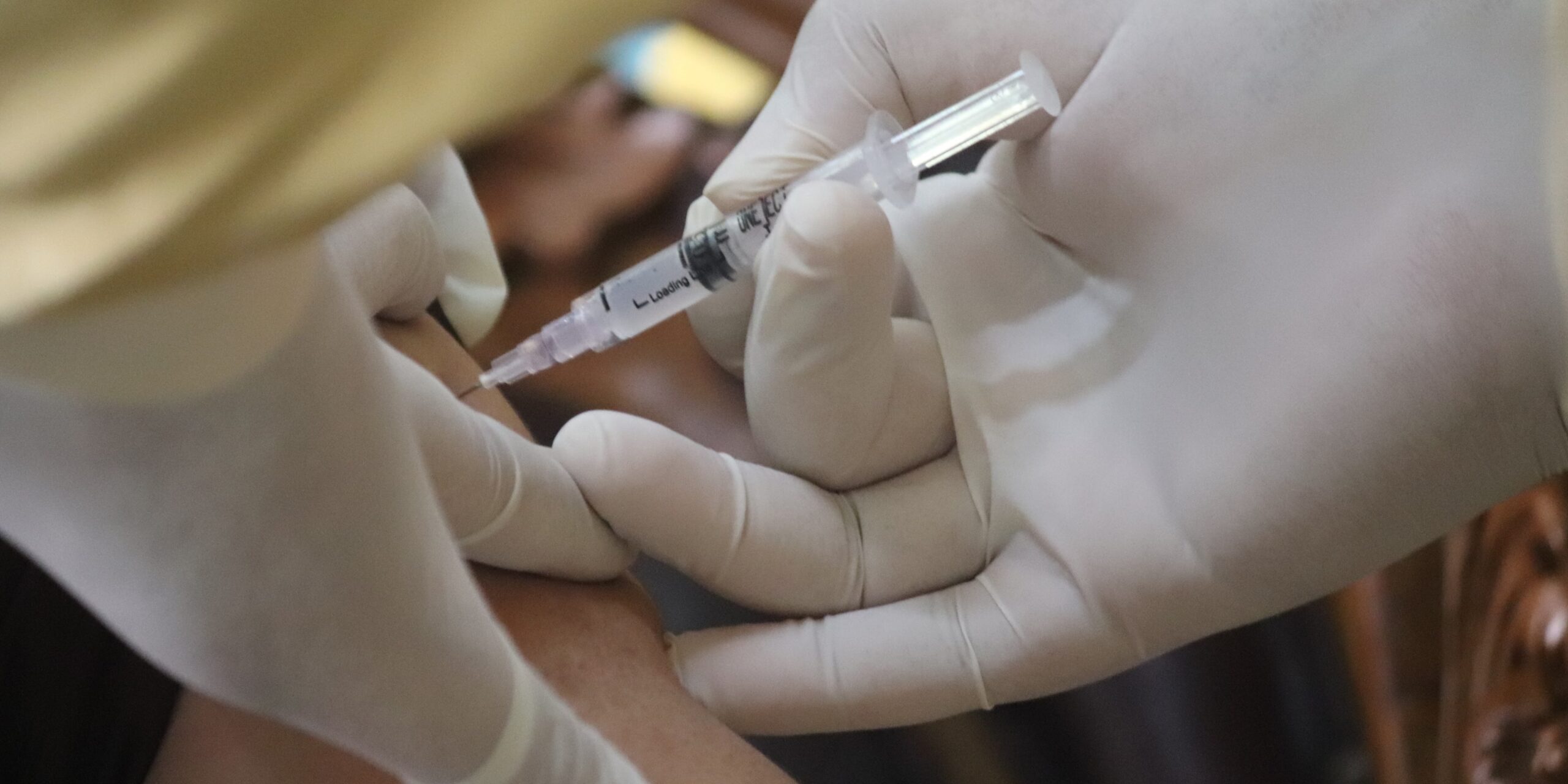
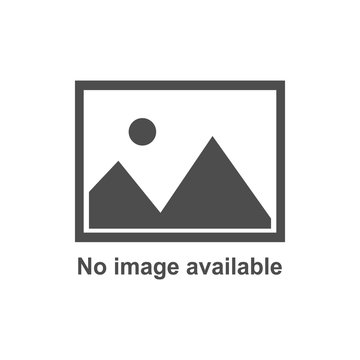
FEATURE – In his first gemba walk in months, the author observes the Covid-19 vaccination process in a physician’s practice in Wales and reflects on how lean it is.
Read more
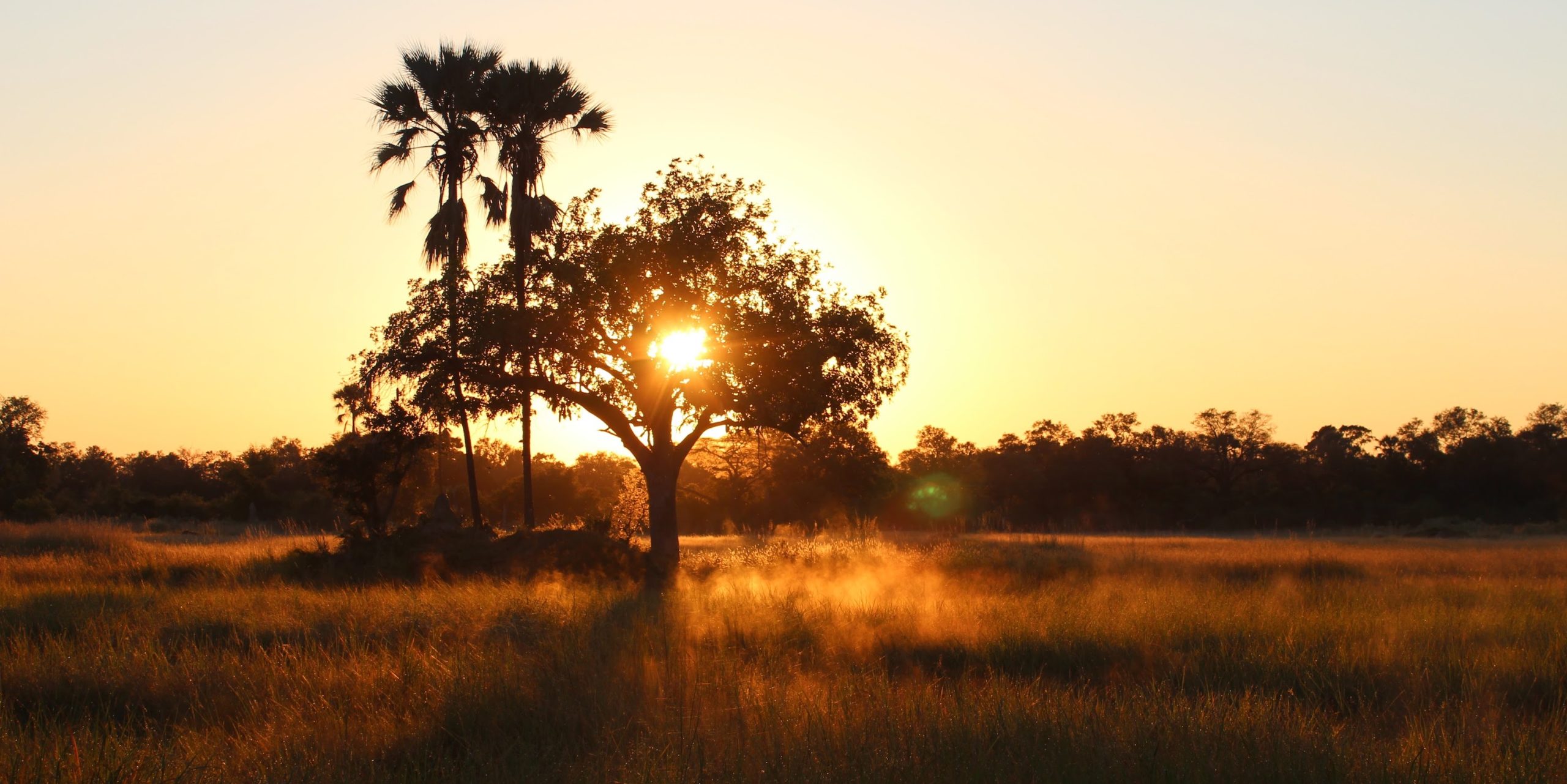
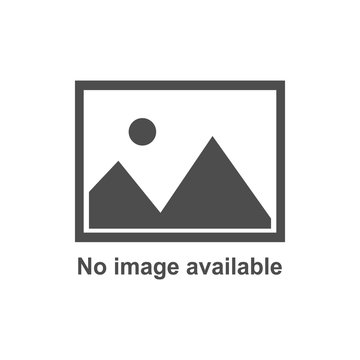
FEATURE – This time of crisis is a perfect opportunity to use Lean Thinking to review processes, improve standards and prepare ourselves for the “reconstruction”, says Sharon Visser.
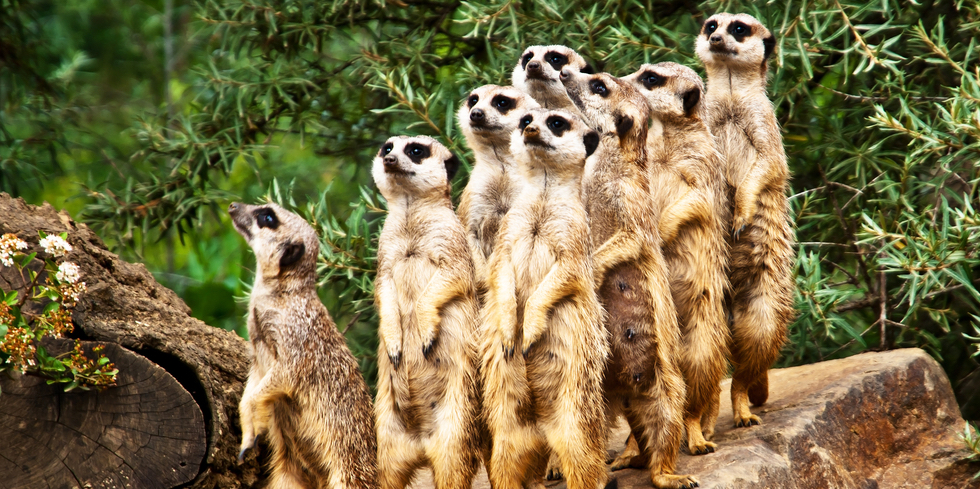
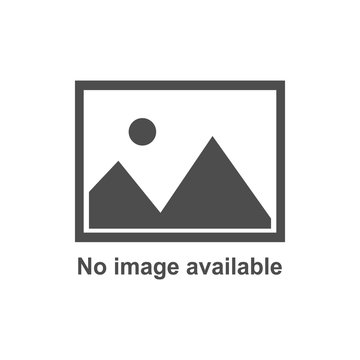
FEATURE – The author discusses two ways in which people can work together in a group – a team or a gang – and explains why you will need both at one time or another in your lean transformation.
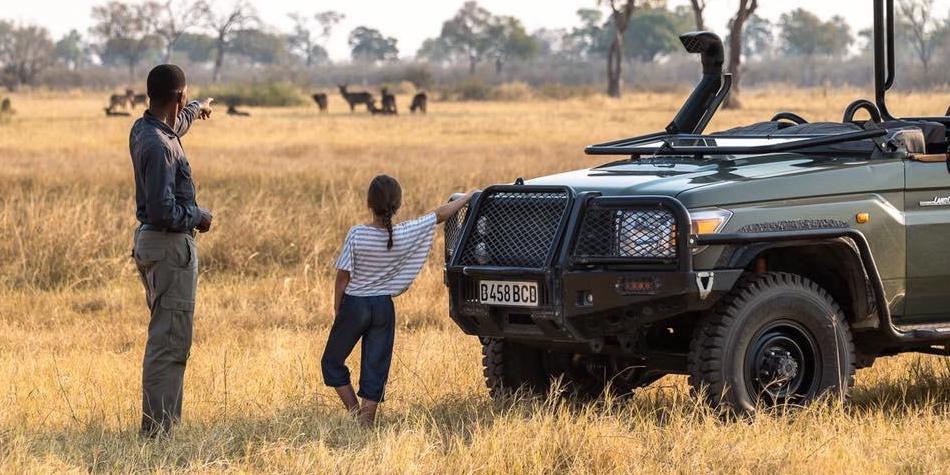
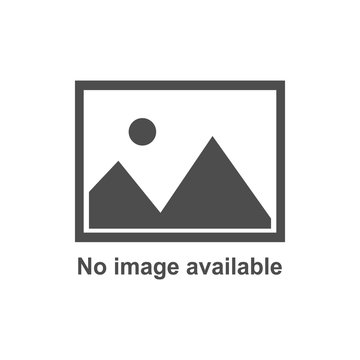
CASE STUDY – This company in Botswana has embraced lean thinking passionately to build the capacity and ability to deal with higher demand for its converted vehicles. The author tells us about their journey.
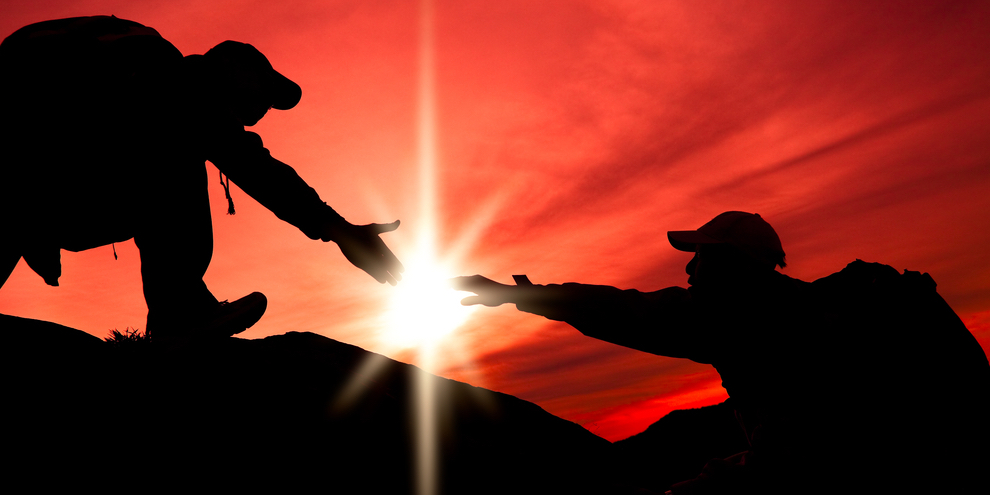
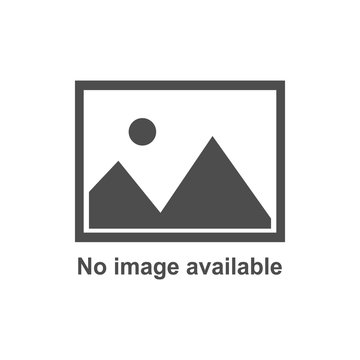
FEATURE – What does it mean to be a lean leader? Our editor tries to answer this question by searching the Planet Lean archives for the best nuggets of wisdom from our authors.