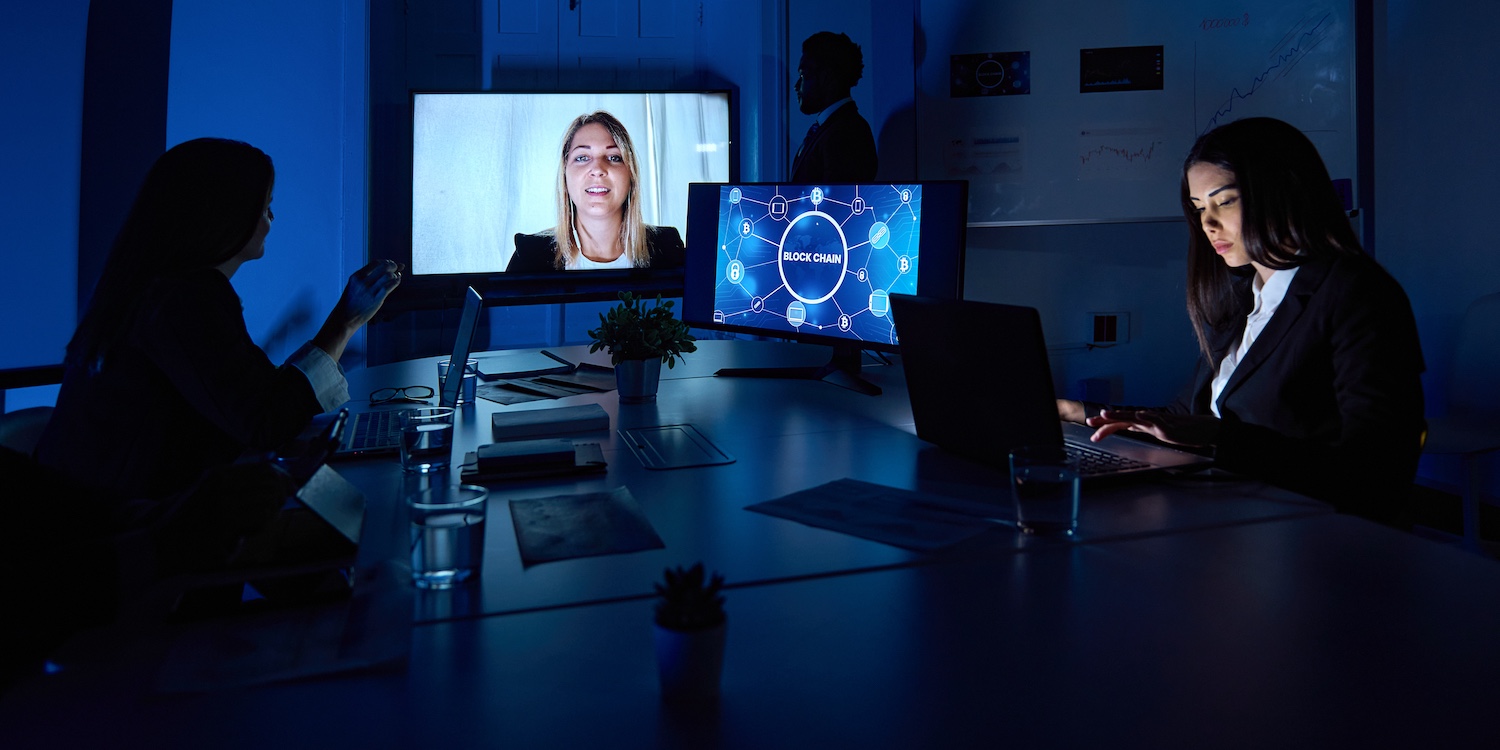
The synergies between digital and lean leadership
FEATURE – This article explores the integration of lean leadership behaviors with digital tools to achieve sustainable performance improvement in modern organizations.
Words: Tony McNaughton
It is now almost 30 years since I stepped out of Toyota, where, as an early adopter in the mid-1990s, I was hungry to explore TPS and Lean Thinking. Since leaving the company, I have helped organizations in many industries throughout the Asia-Pacific region adopt lean principles and practices. While some of them have become globally recognized case studies of successful lean transformations, there have been more than a few failures along the way. I believe it’s worth unpacking this topic to help organizations, and more specifically senior leadership, understand some of the fundamentals that are needed for sustained business improvement – regardless of the industry.
One of the most profound coaching discussions in which I participated in my early years concerned dealing with information in the workplace. My manager, Matt Tajiri, was very sharp in his ability to explain things to me in simple terms. The lessons I learned from his coaching included:
- Having the right organizational structure design to function effectively.
- Ensuring sufficient bandwidth to manage one’s zone of responsibility (zone control).
- Collecting and providing the appropriate data for the right levels within the structure.
- Ensuring there is sufficient capability to effectively investigate, analyze, and solve problems.
- Having a robust process to help review, resolve and reflect on the problems with some level of standardization and accountability (KATA).
All of this was underpinned by a phrase Tajiri-san would often repeat – “Information without action is MUDA [waste].” This idea has stuck with me throughout my career and still holds relevance today.
DEVELOPING PEOPLE
Since James Womack and Dan Jones defined the gap between Toyota Motor Corporation and the other global automotive manufacturers four decades ago, lean efforts have been taking place across the world. Over this time, many organizations have realized and sustained significant gains in operational performance. However, many others have failed to fully leverage the potential of Lean Thinking.
Every organization has their fair share of challenges and opportunities for improvement, which are also an opportunity for internal capability development. Every problem, every challenge, every improvement is fertile ground on which to grow the skills, talent, and creativity of people. The caveat is that this is entirely dependent on senior leadership supporting such efforts and taking responsibility for people development as part of their role. At Toyota, hitozukuri (or developing people) is a precondition for monozukuri (making products), which deemed equally, if not more important than the tactical technical improvements achieved in successful organizations.
High-performing, lean organizations understand very well the idea of leaders acting as teachers, something that has become a non-negotiable trait for them. Indeed, it is vital that leaders understand their role and responsibility to fully leverage enterprise-wide performance optimization through the capability development of the people they manage and lead.
Interestingly, however, it seems that this is a very difficult transition for many leaders, no matter how capable. If I am raising this issue is that I have witnessed time and time again how critical it is for leaders to coach their teams and look at this as an intentional, strategic, long-term investment. And with digital technologies taking the world by storm, this is becoming more critical than ever before.
THE OPPORTUNITY OF THE DIGITAL WAVE
As technology becomes more sophisticated and evolves, so does the workplace. Many organizations are investing in digital, as new opportunities to leverage tech to support company processes and optimize appear. And yet, I still see too many companies investing in multi-million dollar “digital” or “Industry 4.0” solutions, only to be left wondering where their ROI is or when it will materialize (if ever). I believe it is essential to develop an understanding of how best to leverage lean fundamentals to tap into the full potential of digital solutions, so they can become true enablers of an improved operational performance.
The first question a company should ask before investing in digital technologies should be, “What problem am I trying to solve, or what opportunity am I providing to my people?” With that clarity in mind, lean organizations can then strive to create stable and optimized processes that support a value stream that allows them to meet, and indeed exceed, customer expectations. This problem-defining question is something every company should answer, no matter what industry they are operating in. In most cases, their answer will focus on improving things like quality, cost, speed (lead-time), flexibility (agility), safety, capability development, capacity, or the company’s impact on the planet.
But problems will surface even with stable processes, and this where today’s digital solutions can provide some great opportunities. In the past, when faced with a problem, a supervisor or manager would struggle to understand the issue and detect its root cause. They were typically forced to carry out their problem-solving efforts after the fact and retrospectively tried to put the pieces of the puzzle together. Often, this would lead them to make assumptions and based their actions on them. The result? They normally missed the mark and failed to solve the problem or prevent it from reoccurring.

But things are different today. We have access to an incredible amount of data and information, allowing us to understand facts and engage in real-time problem solving. We can now detect a failure mode as soon as it occurs and act accordingly in a timely manner, thus achieving a better result. Technology brings problems that were once relegated to the “hidden factory” to the surface and provides the problem solver with the information they need to investigate and take swift action.
Having clarified the role that digitalization can play in a lean transformation, it’s worth giving a more in-depth look at the opportunities afforded to us by an approach to lean leadership that fully leverages the power of digital technologies.
OPPORTUNITY 1: TACKLING COMMON LEADER STANDARD WORK “FAILURE MODES”
The intent of Standard Work for a front-line team member is to define the most efficient and safest repetitive method of work. This is then deemed as the current baseline for further refinement and improvement. In many ways, Leader Standard Work (LSW) is also trying to define the most efficient way of managing within a leader’s zone of accountability or control. (The Lean Enterprise Institute defines LSW as “the repetitive pattern of activities that represent the current least wasteful method of planning and controlling normal business processes”.)
Leader Standard Work is a well-studied practice that constitutes an important part of a lean leader’s journey, but I have observed a few situations that make it difficult to sustain:
- The process is not stable and, therefore, leaders are firefighting throughout the day.
- The span of control (zone control) is too broad.
- The LSW is too tightly packed and there is no room to deep dive or deviate if necessary.
- The capability of front-line leaders is insufficient to drive effective improvement.
- The support infrastructure lacks the “leader as a teacher” mode.
Takeaway 1: Challenge your organization’s current state against these five “failure modes”.
OPPORTUNITY 2: ENABLING LSW BY LEVERAGING REAL-TIME DATA TO RESPOND TO PROBLEMS
Digitalization enables a new way of working for leaders and allows them to redefine their Leader Standard Work (although it’s important to remember that addressing previously hidden problems requires sufficient bandwidth in their LSW).
Let’s take two of the failure modes outlined above as examples to better illustrate this second opportunity. Imagine a manufacturing workplace that is not stable. The LSW is well defined for each level within the organization, but each day the leaders are overwhelmed with unplanned issues that continuously surface. Things like unplanned equipment downtime, high absenteeism, material shortages, or quality issues make it unrealistic for them to focus on their LSW, as most of their time is consumed by firefighting. The result is a LSW that is not sustainable and that ultimately fails.
In an office environment in which the front-line supervisor’s or group leader’s span of control is too broad, we’ll encounter similar difficulties, resulting in the ability to get the right things done in each cycle (hourly or daily). At the first unplanned issue, the leader will simply run out of bandwidth to respond and provide support. Again, a failure of the management system will ensue.
Now, let’s look at a situation in which LSW and digital technology can work together. In this case, the LSW is well defined for each level of the organization and designed in a way that allows for some freedom to deviate when unplanned issues surface, and the organizational structure ensures the leader has the sufficient bandwidth to manage their zone effectively. Additionally, leaders are trained to unpack issues as they appear and to solve both short-term and long-term problems. With well-defined and standardized processes, an investment in digital enablers that can capture real-time quality performance data in each critical process will pay dividends. This digital information is available to the leaders throughout the day. The system has inbuilt “andon” features that send an alert signal whenever more than three non-conforming items are produced over a one-hour period. This allows the leader to break from their LSW and go to the “hotspot” for investigation and support, unlocking their ability to see the problem at the source in real time and better understand the failure mode and its causes. As a result, the company can achieve early intervention and minimize the overall performance erosion that was so prevalent in the past.
Takeaway 2: Leverage data to develop the real-time problem solving and escalation/accountability muscle
OPPORTUNITY 3: DIGITAL “BIG DATA”
Having a system that is rolling up performance data is the other big unlock that companies are now leveraging. While real-time data and response is fundamental for performance optimization, getting an overall picture of the situation is also extremely valuable.
Here’s an example. An organization receives news that there are quality issues with their product in the market. In some cases, this can be up to six months after the actual product was manufactured. The consumer demands action to prevent recurrence. Rather than taking some loose best-guess actions, the company decides to connect the field failure to the actual critical process manufacturing data sets. This allows them to identify any correlations with the failure or prove that the problem is not a result of the manufacturing process (perhaps it was a design fault or a case of misuse by the consumer).
Big data is big picture. While organizations are focused on the short-term to drive optimal performance, big data provides a higher-level perspective that can bring to light other important aspects of the business. Thank to it, trends, hotspots, and previously undetected opportunities can be surfaced. Once again, this will then require the right skill sets and leadership behaviors as previously mentioned to address appropriately.
Takeaway 3: Repetitive cycles of real-time response, analysis and problem solving will no doubt drive better performance in the organization. This should be reflected in internal metrics as well as external indicators. However, the big data can uncover patterns, trends and associations that may not be visible in the daily activities and processes.
TO CONCLUDE
Investing in digital solutions can become very costly. I believe that now, more than ever, lean leadership fundamentals and behavior accountability (not the tools) are vitally important for organizations eager to maximize their performance as they embrace their digital future.
THE AUTHOR

Read more

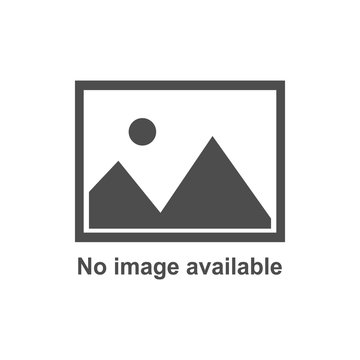
FEATURE – The future has never looked more uncertain for restaurants and cafes. The authors share a set of practical lean tips that can guide these organizations navigate the storm.

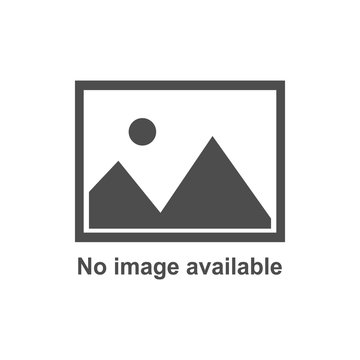
FEATURE – The author discusses the practices that can help us make the most of the traditional mantra “go see, ask why, and show respect”.
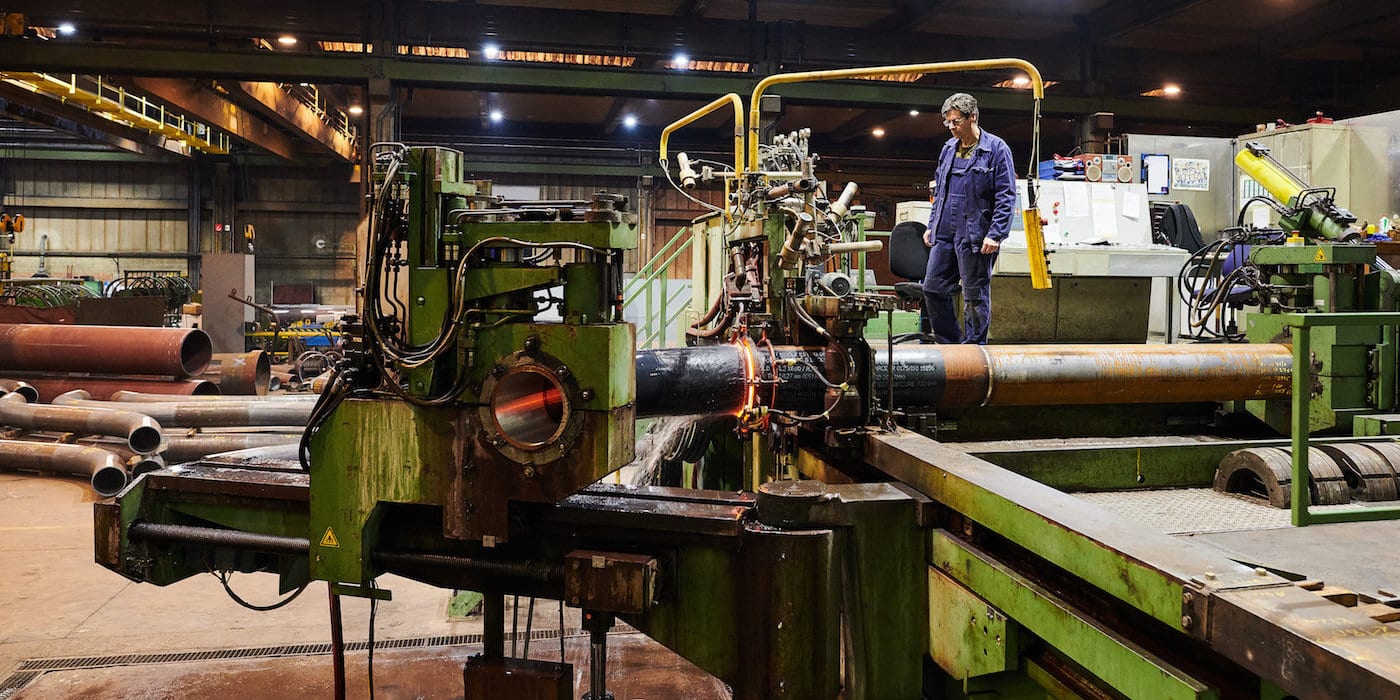
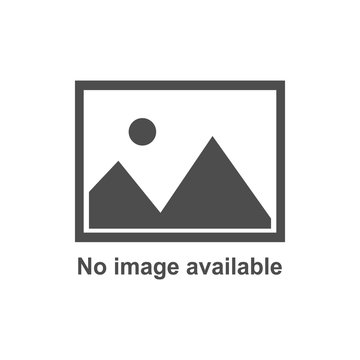
FEATURE – This Dutch company decided to start its lean journey by involving its suppliers in the improvement work. We hear from both customer and supplier.
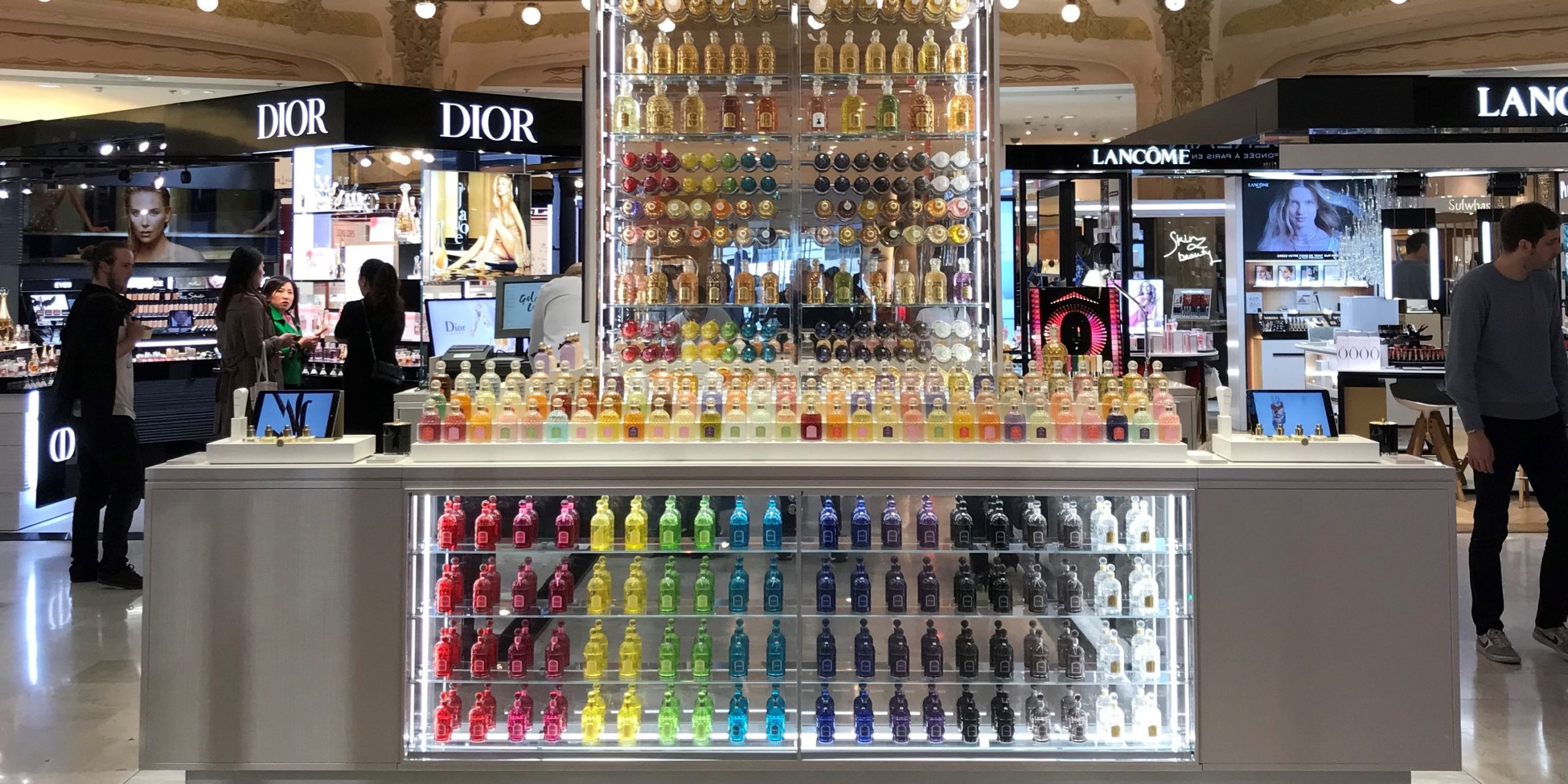
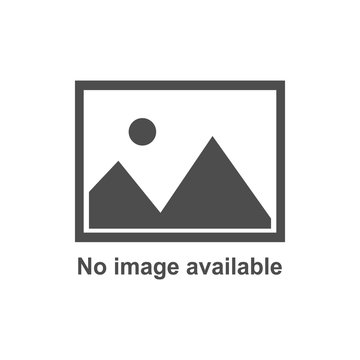
NOTES FROM THE GEMBA – How do you kick off a lean journey? This French company has chosen to begin by analyzing and tackling each customer complaint.
Read more
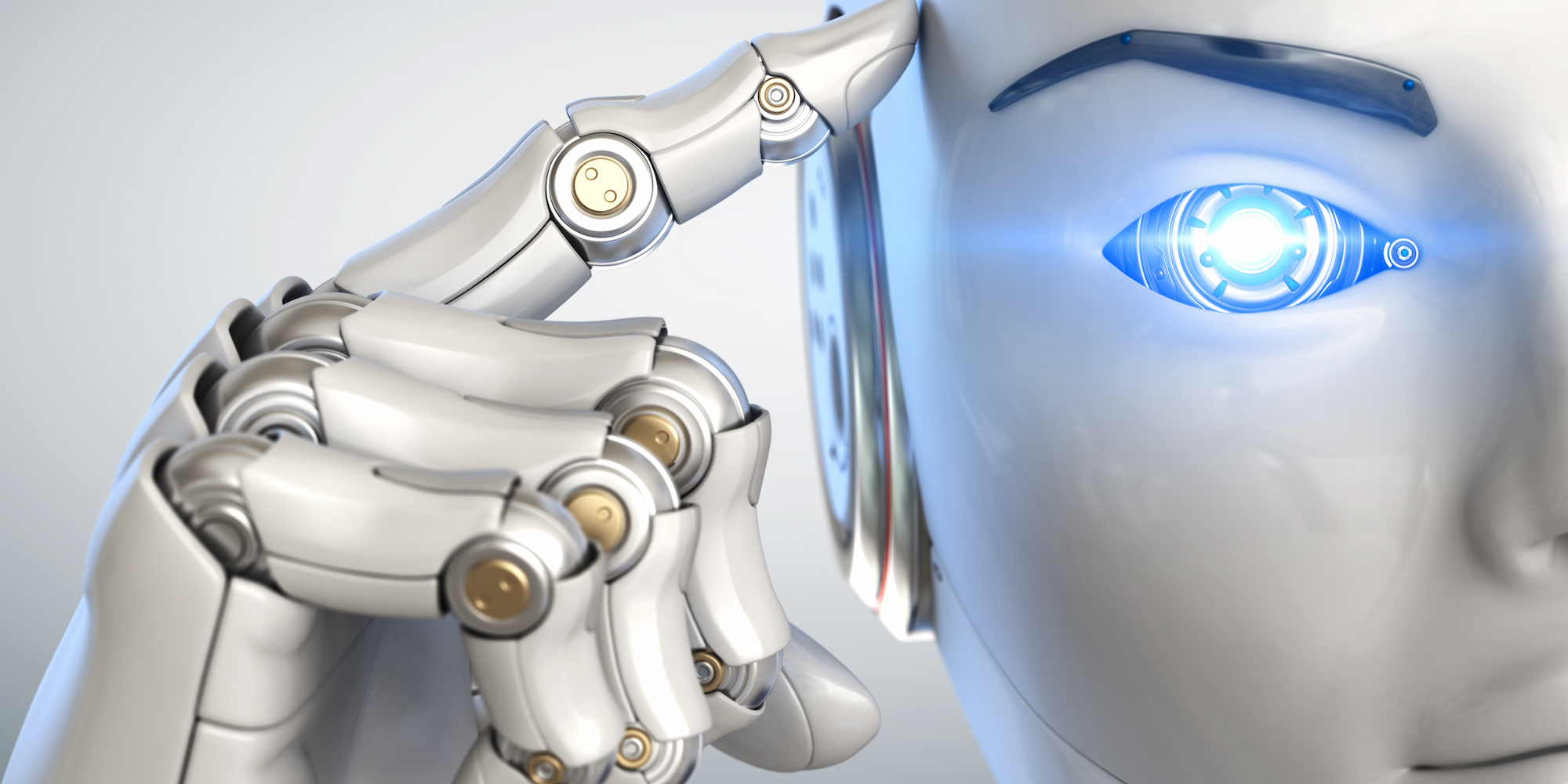
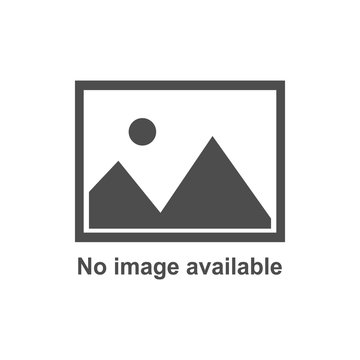
FEATURE – This year, PL will try to understand what the future of work looks like in a world with AI. To kick us off and make us think, we publish an article that is the result of a one-hour conversation between a human and a machine.
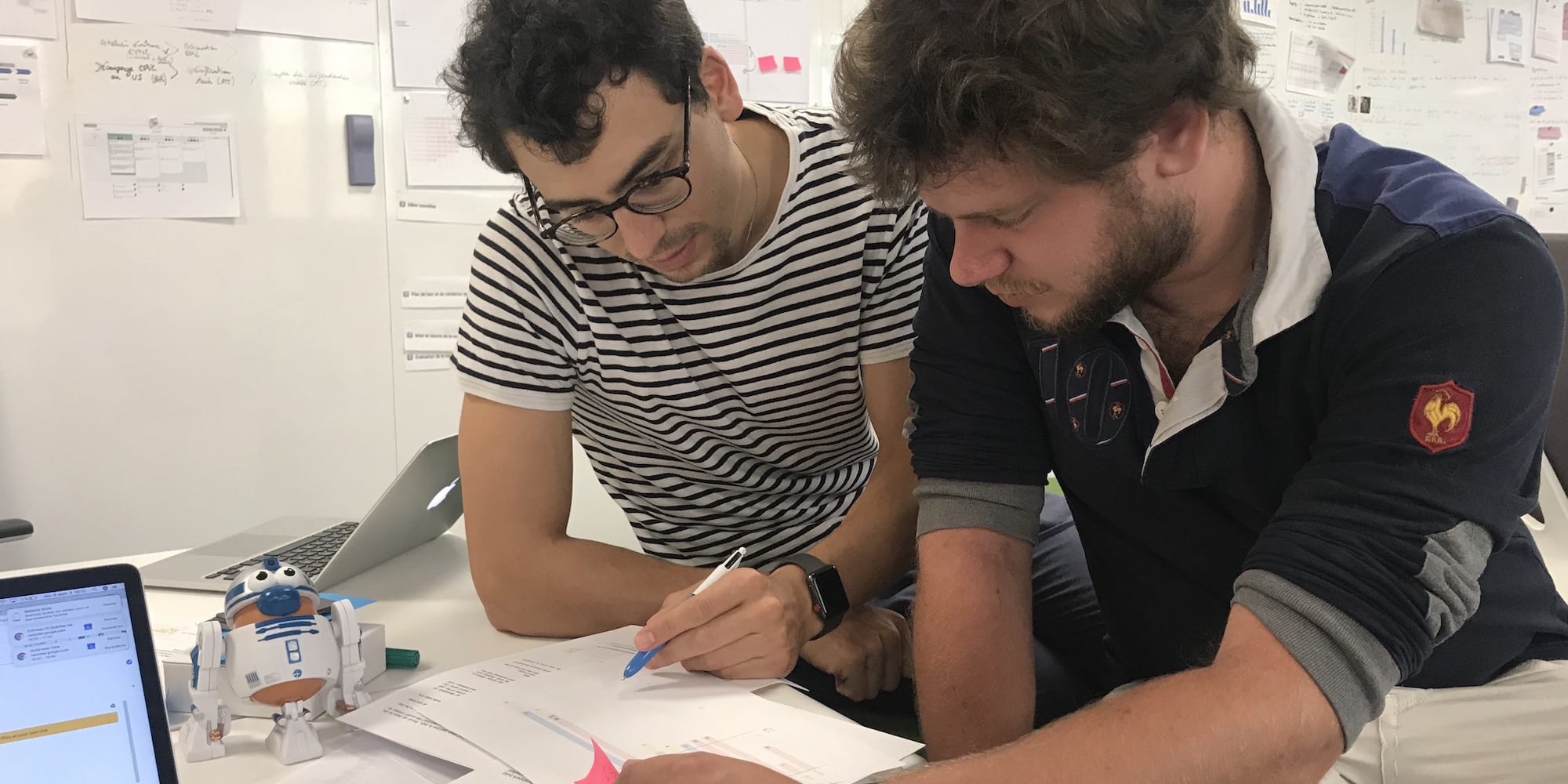
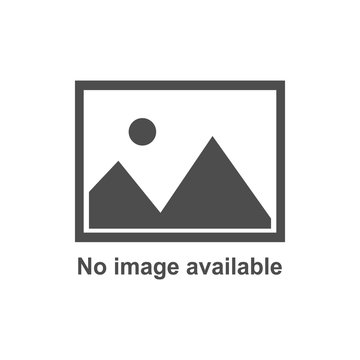
BUILDING BRIDGES – In another article for their series, lean digital company Theodo tells us about their efforts to measure and reduce its lead-time to deliver product features.
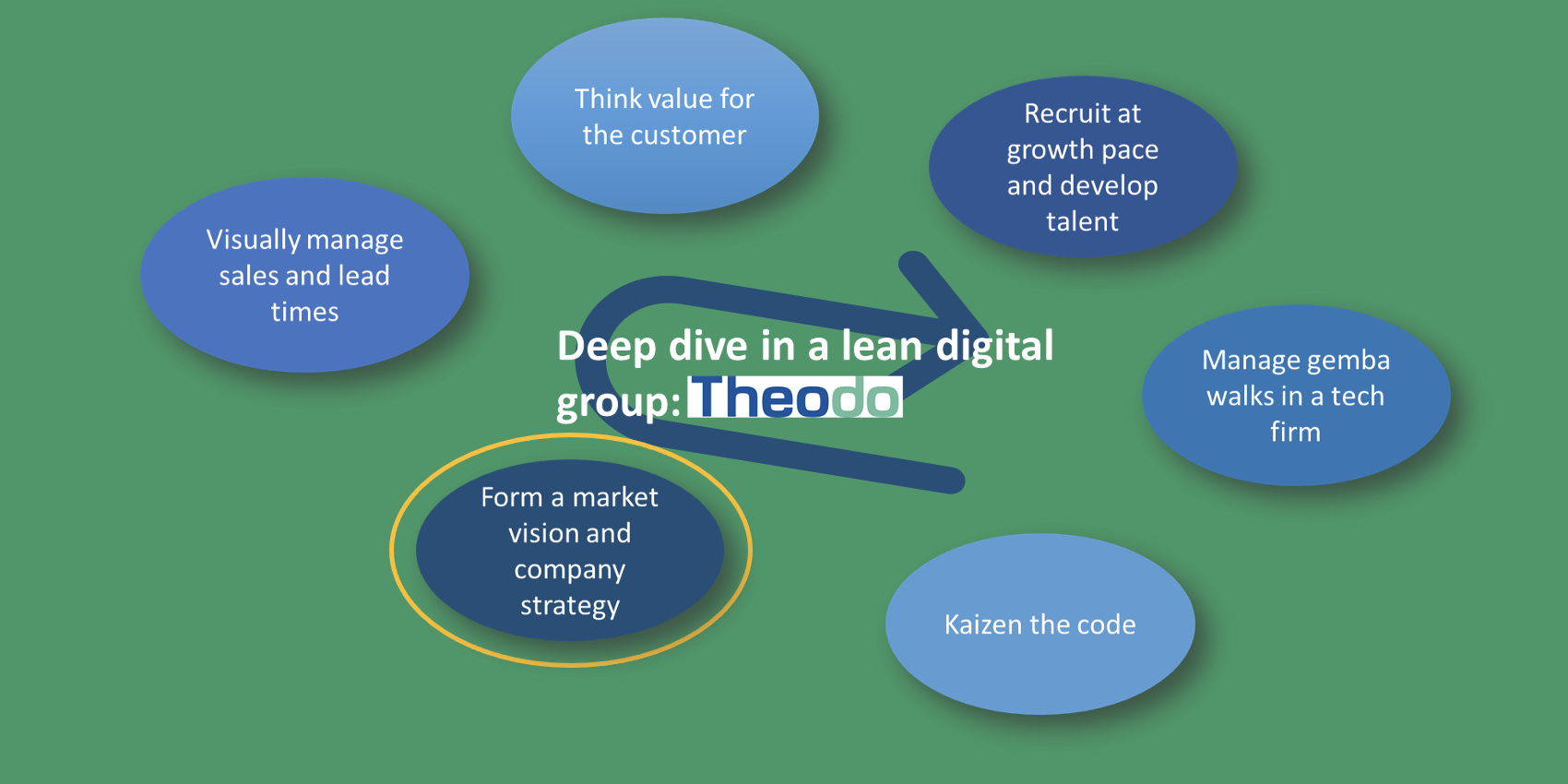
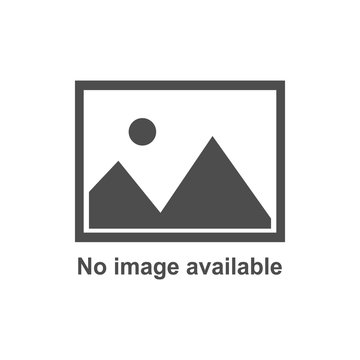
FEATURE – In the final article of her series, the author spends a day with Theodo’s CEO and co-founder to learn how lean informs its strategy and vision.
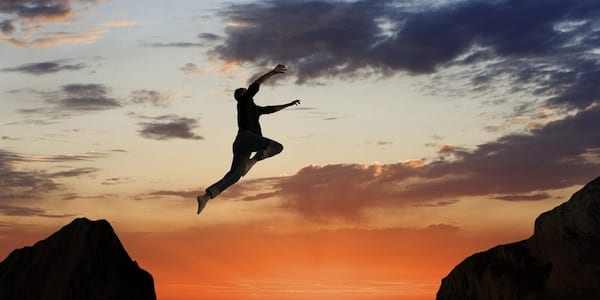
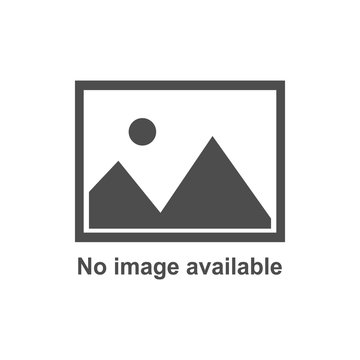
INTERVIEW - What does "leading through incompetence" mean? Peter Willats discusses the role of leadership in a lean management system and the evolution of lean thinking.