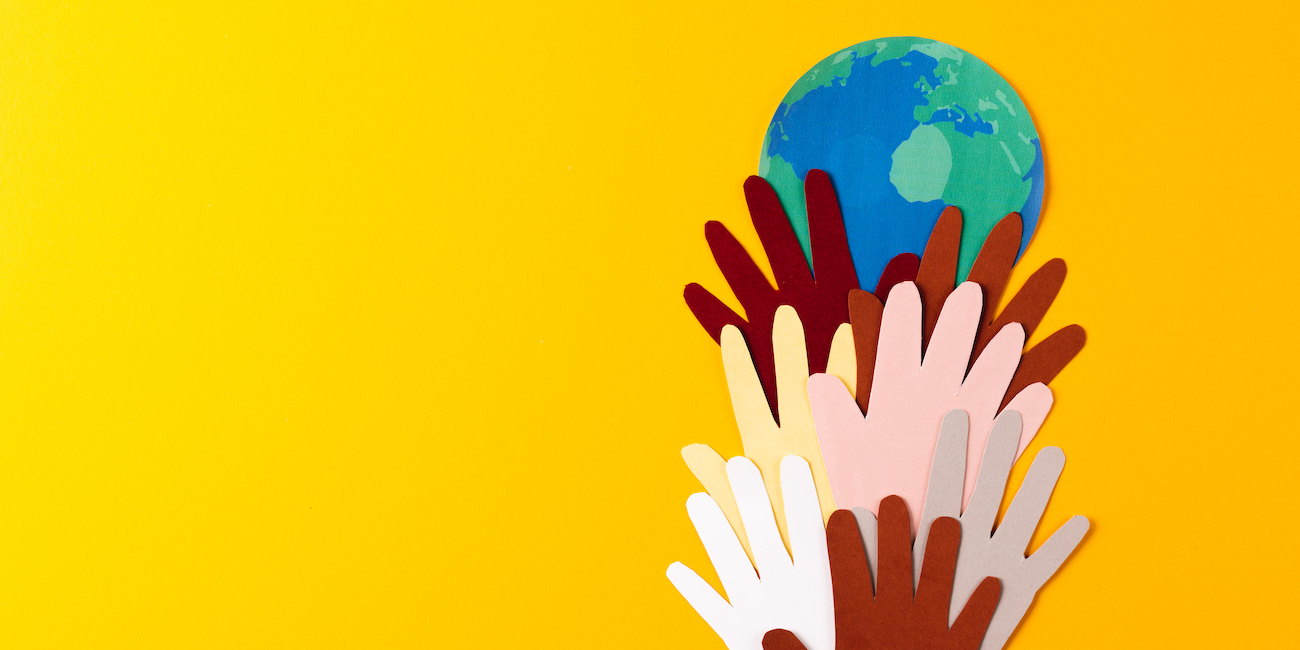
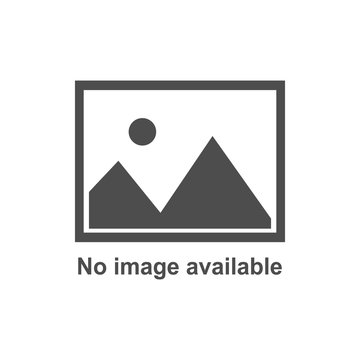
INTERVIEW - In this interview, Lynne Smith discusses the potential and difficulties of applying Lean Thinking to NGOs and looks back at the lean transformation at the Gates Foundation.
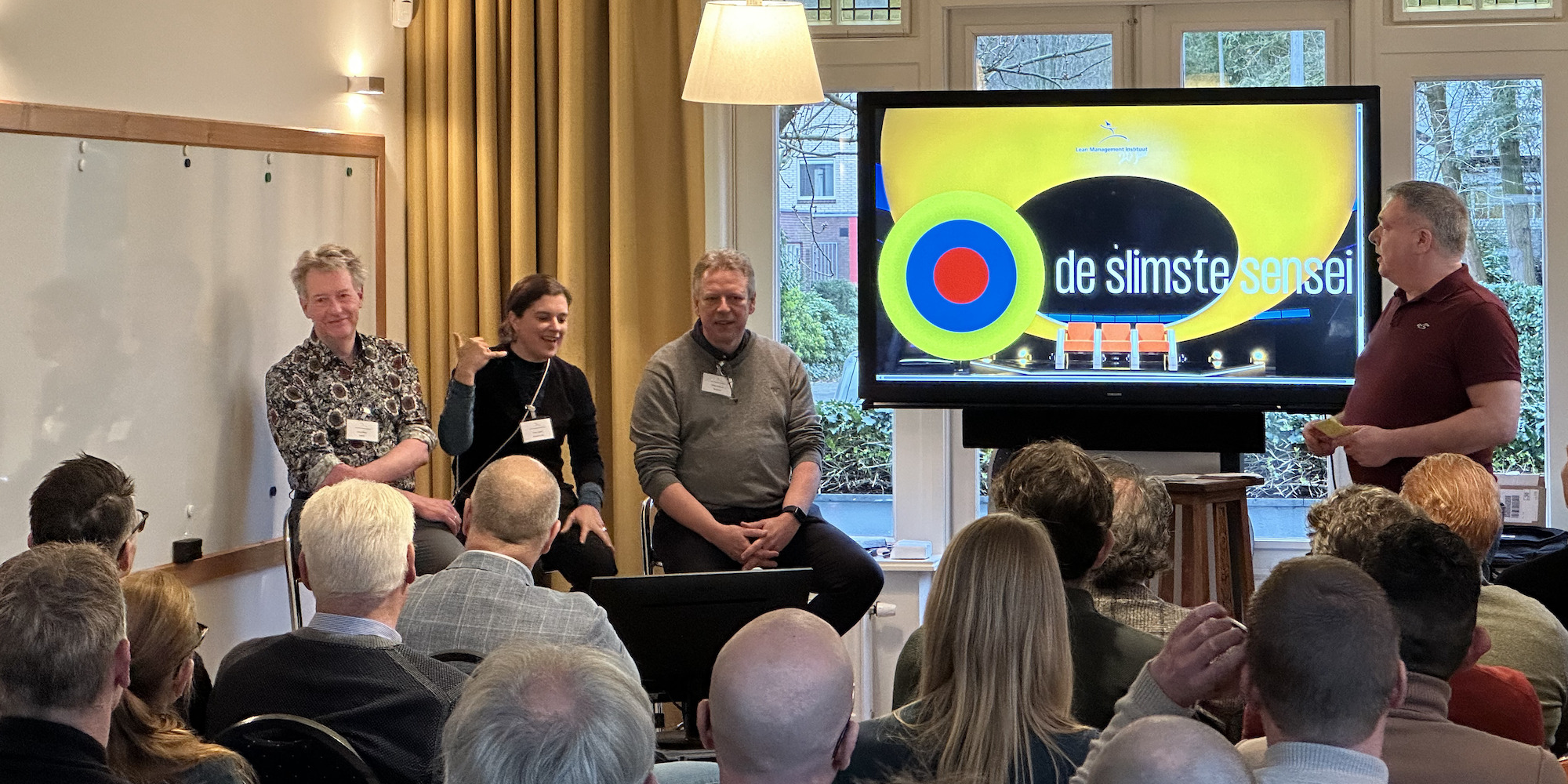
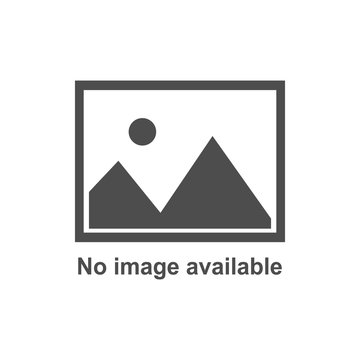
FEATURE – In February, our affiliate in the Netherlands turned 20. The President of Lean Management Instituut reflects on this achievement and looks back at these two decades.
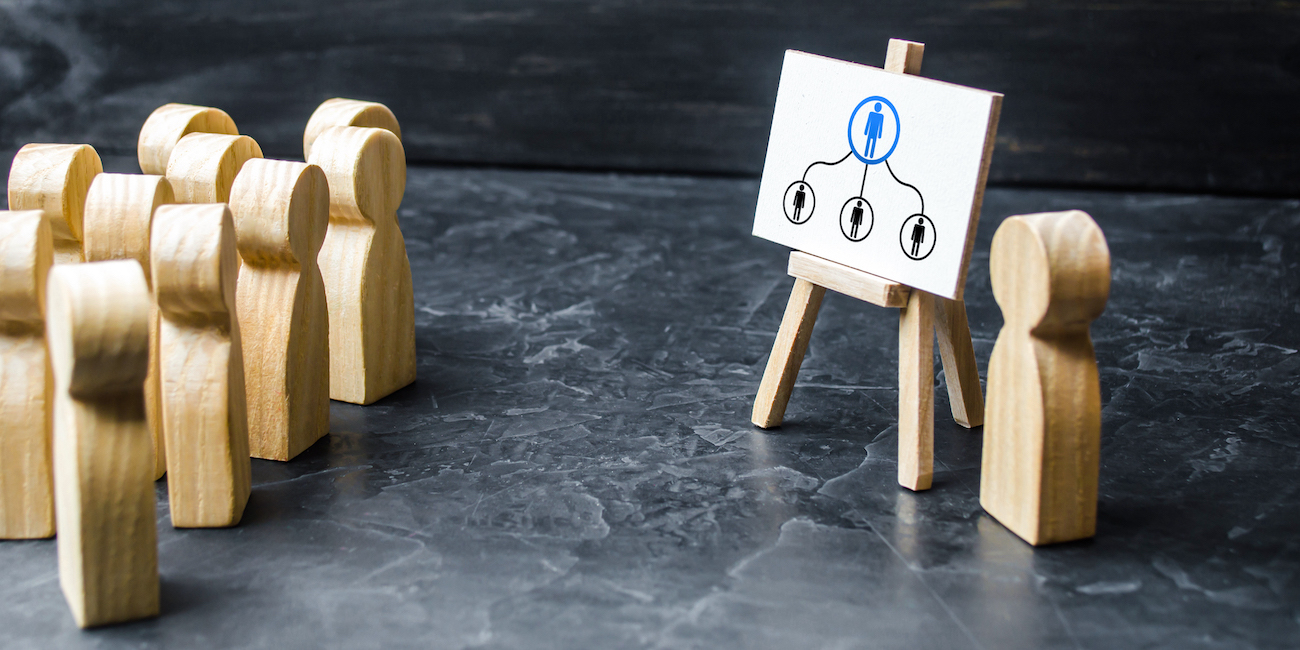
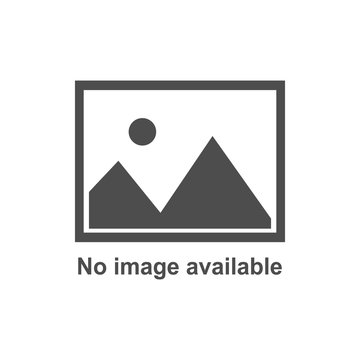
FEATURE – To get the results we want from a system, or prevent it from generating undesirable events, we need to understand how it works and behaves in the real world. That’s exactly what Jidoka does.
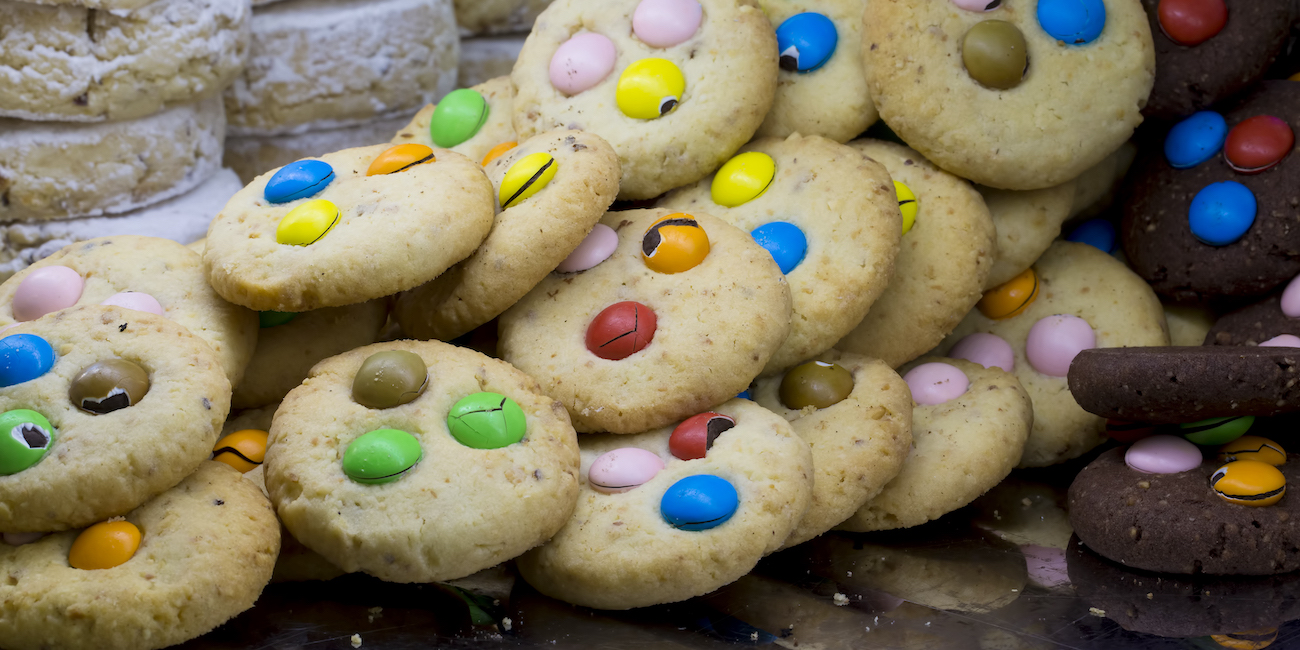
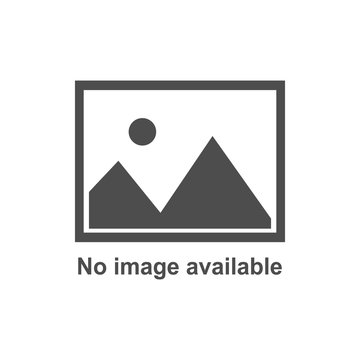
FEATURE – The successful project discussed in this article shows how Lean Thinking can bring huge benefits to small and medium enterprises and paves the way to a new way of looking at lean coaching.
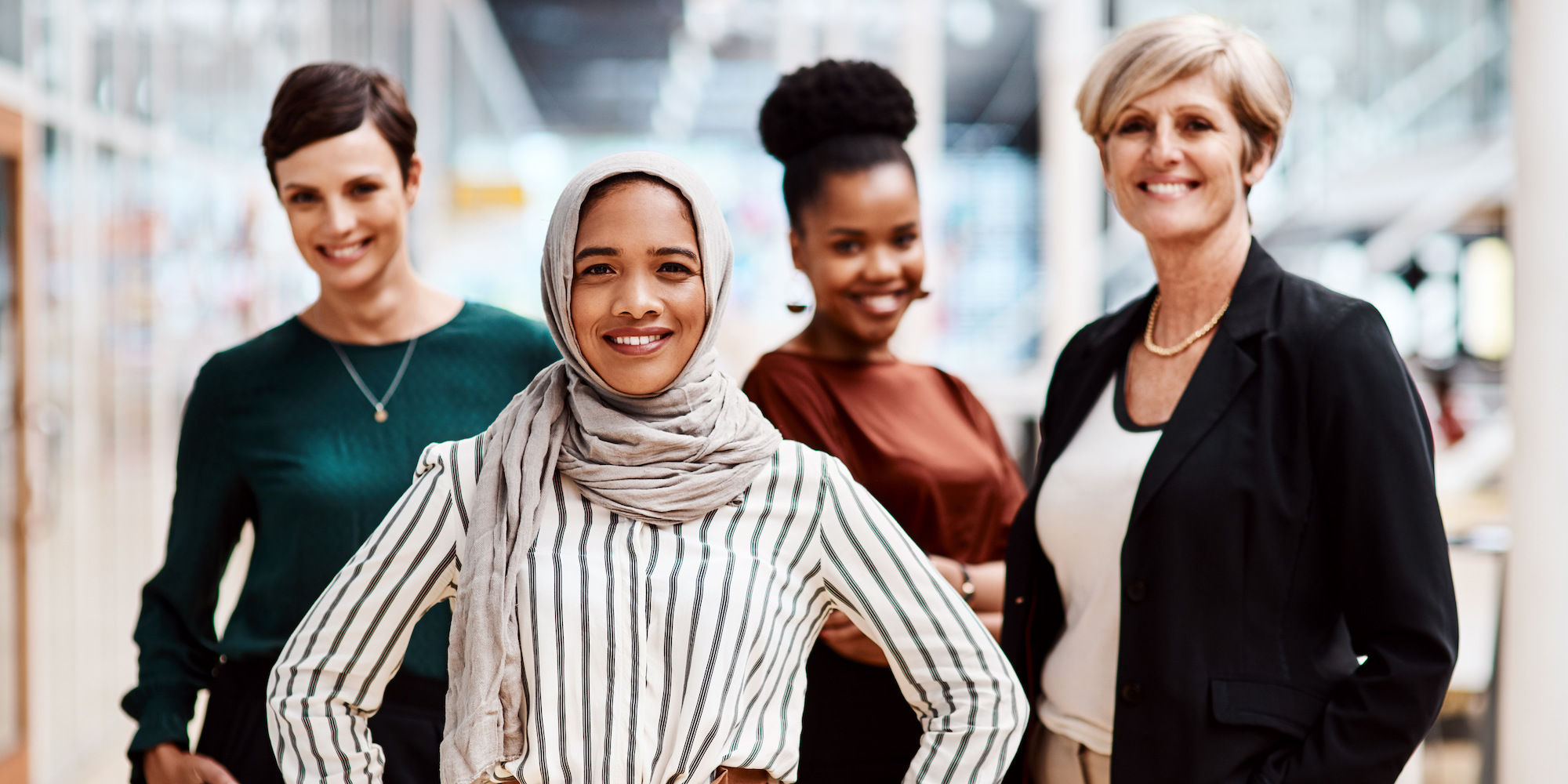
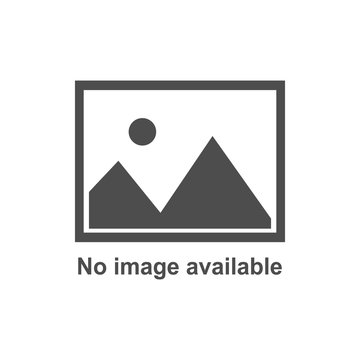
FEATURE – This article applauds the tenacity of women leaders and seeks to illustrate how they motivate others to take on the sustainability challenge through lean practices.
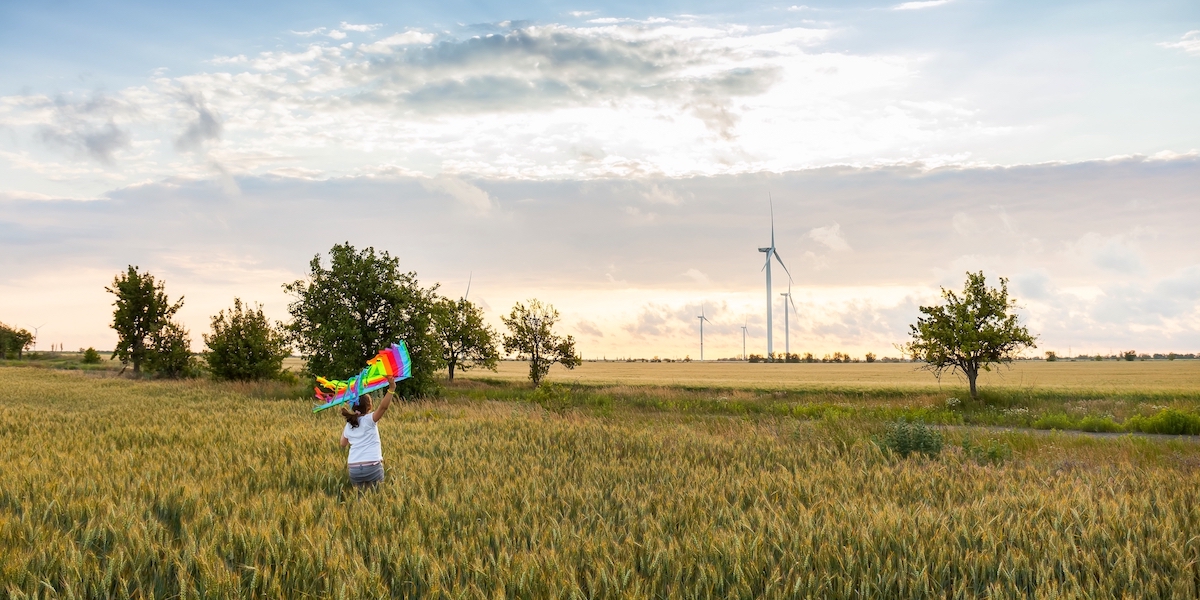
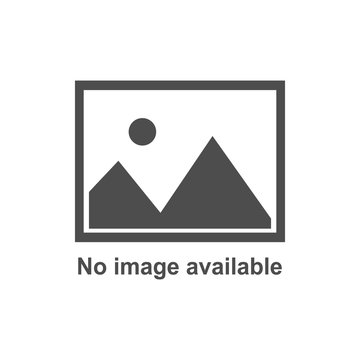
FEATURE – When it comes to the fight against climate change, we can’t expect to achieve much until we fundamentally challenge the way we think about resource consumption. Lean is our tool to do that.