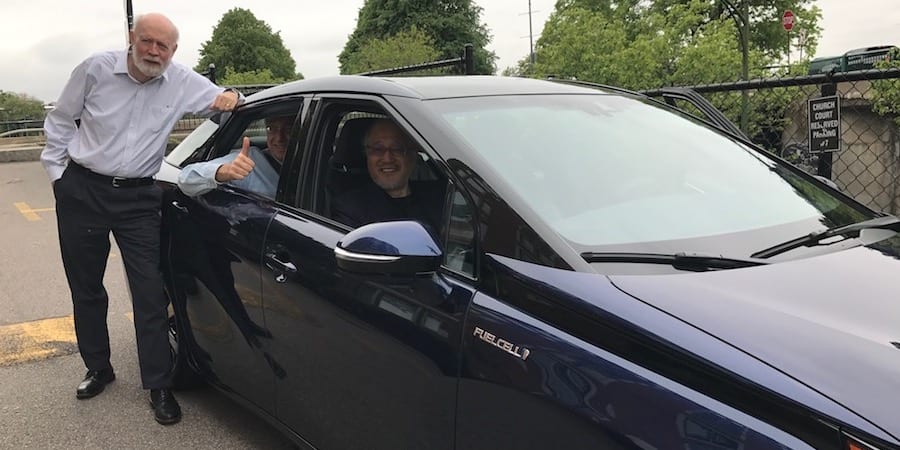
Jim Womack drives the Toyota Mirai and talks lean and green
WOMACK’S YOKOTEN – After a road trip from Boston to Philadelphia driving Toyota’s hydrogen fuel-cell Mirai, Jim reflects on lean and green and why the two are not necessarily the same.
Words: Jim Womack, Founder and Senior Advisor, Lean Enterprise Institute
I have always been perplexed when people ask me whether lean is green. Getting leaner means creating more value for consumers with less resources – time, space, human effort, capital expenditure, inventories, etc. – by eliminating waste. And doing this might be greener as well by simultaneously reducing burdens on the environment. But this depends on what use is made of the freed-up resources.
Let’s imagine an extreme case where cars are developed and produced using leaner methods. Because they are cheaper (less waste) they are bought in larger numbers and driven more miles by happy customers but produce additional CO2 as a by-product. Leaner but not greener.
We can also imagine an opposite case where resources freed-up by application of lean methods are used to add features to cars – like hydrogen fuel cells or batteries – at no extra cost to the customer, technologies that dramatically reduce the CO2 produced per mile. Leaner and greener. So how can we tell which is which in our practice?
I recently found time to ponder this question while driving Toyota’s hydrogen-fueled Mirai sedan (“mirai” means “future” in Japanese) down the Interstate from Boston to Philadelphia with Taka Fujimoto of the University of Tokyo (a sublime lean thinker and author of The Evolution of a Manufacturing System at Toyota), and José Ferro, Founder and President of Lean Institute Brasil. (Pictured.)
We were on our way to a reunion of MIT’s International Motor Vehicle Program (IMVP) – nearly 40 years after its inception – featuring an afternoon of hansei (critical self-reflection on what we achieved) and a dinner for dozens of participants in the program over the years. These included John Krafcik, who came up with the term “lean” in 1987 and who is now the CEO of the Google self-driving car program, recently renamed Waymo.
Given the importance of the IMVP for validating the advantages of the Toyota production and business systems (for a global audience, through its 1990 report The Machine That Changed the World), it was appropriate that Toyota provided us a hydrogen-powered fuel-cell Mirai for our hansei trip. This vehicle is sold in the USA only in California and there are no fueling points for the public on the East Coast. As a consequence, the vehicle had to be transported to Boston from an industrial hydrogen producer in Connecticut and picked up in Philly for transport (by way of the same hydrogen source in Connecticut) to its next user by car carrier, a substantial task that must have cost a bundle. Thank you Toyota!
We were not performing a rigorous road test but I should note that the Mirai worked fine – I would have thought it was a Camry with a different skin if I had not known otherwise. From a user standpoint, including range, there was nothing discovered in our 312-mile trip that was not to like about a hydrogen future.
Round about Manhattan, after Taka took over driving, it occurred to me that we can only provide an answer to the “leaner and/or greener” question by looking jointly at the internal resources saved in design and manufacture of a product (always a good thing) and the negative externalities created by the use of the product – mainly carbon dioxide in the case of cars. So a car powered by hydrogen might be leaner but not greener or greener but not leaner or either or both.
This brings me back to the Mirai with its fuel cell (yes, the “fool cell” ridiculed by Elon Musk) that turns hydrogen into electricity to drive the wheels. Let’s give Toyota a pass for the moment on the leanness of the design and production system, remembering that the Mirai uses a new technology (which can doubtless be produced with fewer resources over time) made in tiny volumes at a supplier lacking the advantage of scale economies. As/if the technology matures and production reaches normal automotive scale in Toyota facilities, I’m confident it will get steadily leaner. And this is critically important because the Mirai, with its exotic new technologies, is currently very expensive.
But for the greener part we need to know where the hydrogen came from to fill the Mirai’s two tanks (to 14,000 pounds per square inch!) How many negative externalities were created per mile in relation to conventional vehicles?
Fortunately, a number of analysts have been thinking about this, including my former MIT colleague Professor John Heywood, who uses the GREET model developed by the Argonne National Laboratory in the US. His team’s ballpark conclusion is that compared with a comparably sized ICE (internal combustion engine) vehicle on a comparable trip, a hydrogen fuel-cell vehicle will emit 35 to 70 percent less CO2.
The vehicle itself, of course, doesn’t emit any CO2, only water as the hydrogen is recombined with oxygen in the fuel cell to yield H2O. The emissions and the differences in emissions are caused by the method used to create the hydrogen. Doing this with water-methane reforming is pretty cheap and pretty easy (possible in any gas station on a natural gas line) but no better in terms of CO2 reductions than plug-in hybrid-electric vehicles (such as the Toyota Prius Prime) which currently cost much less. Producing the hydrogen with water electrolysis (which readers probably used in high school science class to create hydrogen) utilizing electricity from solar, wind or hydro is for the moment extremely expensive but impressively greener, reducing CO2 emissions by two-thirds.
This analysis suggests that the Mirai will be dubious proposition until (a) lean methods dramatically reduce production costs and (b) a very efficient (leaner?) way is found to produce hydrogen from water through electrolysis and to get it to the vehicle. So, the Mirai is greener than conventional ICE vehicles but can only take us part of the way on the green journey. Or maybe we were just driving the wrong fuel-cell vehicle?
As it happens, Toyota has just commenced testing a semi-truck (a tractor pulling a large trailer of sea containers) at the Port of Los Angeles. The vehicle uses fuel cells like the ones in the Mirai to pull a vehicle weighing as much as 80,000 pounds (vs. 4,078 for the Mirai) to deliver containers from the Port to points of use in the Los Angeles area. These trips are no more than 200 miles round-trip and the vehicles always return to their starting point, usually carrying out-bound containers.
The Port of Los Angeles is next door to a massive complex of oil refineries that produce hydrogen as a by-product of refining gasoline and diesel fuel. This hydrogen can easily be pumped the short distance to a single refueling point for fuel-cell semis and would otherwise be flared for lack of a cost-effective way to convey it to industrial users. This concept is potentially much greener by providing large amounts of energy at low cost with no additional production of CO2. There are 16,000 tractor loads a day leaving the Port for points in the LA area and many ports around the world have similar adjacencies of container shipping and refining. So this could be a big deal and Toyota should be congratulated for this experiment.
But wait: The hydrogen produced with no incremental CO2 for fuel-cell trucks is only available as long as refineries near ports produce massive amounts of diesel fuel and gasoline, which will be turned into CO2 plus water by conventional ICE vehicles. (No greenness there.) And in any case there aren’t enough adjacent ports and refineries to provide more than a small fraction of the hydrogen needed by the world’s big rigs. Fuel cell trucks are a step in the right direction in the world's ports, but are not a viable way to make the whole green journey.
Questions about lean and green can be answered in the same way about battery-electric vehicles like Teslas. How lean is the production process to offset the costs of new “lean” technologies? Where does the energy to charge the battery come from? Are these vehicles greener than traditional internal combustion engine vehicles?
I’m not suspecting that Tesla is currently very lean given the number of workers needed at Fremont (the old NUMMI GM/Toyota joint venture plant) to produce the S and X models and the amount of capital expenditure that seems to be required. (And this means in turn that these models are very expensive.) However, unlike Toyota, which has always been very open about its production system – including at NUMMI where we performed the first of our global quality and productivity audits in 1986 – the Tesla system remains a mystery.
It would be great fun someday soon – when the Model 3 is in high-volume production – to subject the Tesla production system to the same analysis that the International Motor Vehicle Program applied to all of the world’s conventional car plants over many years. (I’ll be happy to volunteer my time and pay for my travel if Tesla wants to participate.) I hope to find that the Model 3 production system achieves a big leap in leanness – more value with less waste – compared with conventional production systems led by Toyota, because if it doesn’t I’m skeptical that Teslas will ever be cost-competitive for any but hard-core green buyers.
But what about greener? The evidence from the CREET model is that a typical battery-electric vehicle will create about half the emissions per mile of a comparable sized ICE vehicle. But there is also a wide range of results depending on the source of the electricity. The 50% reduction presumes that the batteries are charged by power generators using the typical US fuel mix (1/3 coal, 1/3 gas, 1/5 nuclear, and only a small fraction renewable.) By contrast, vehicles powered solely by solar cells will have much lower emissions per mile and those powered by coal-fired generating plants will have emissions almost equal to conventional ICE vehicles. Again, the degree of greenness depends on where the energy comes from.
My concern in this column is not about the specific greener/leaner findings for specific products, although it has been fun to speculate. My objective instead is to spur thinking in the Lean Community about ways we can talk about reducing waste of the conventional sort within production and use systems and about reducing wastes often overlooked because they are externalities not paid for by consumers. To be relevant to society at large and convince the world to make leaner, greener journeys, we need to be able to talk authoritatively and constructively about how to do both at the same time.
THE AUTHOR
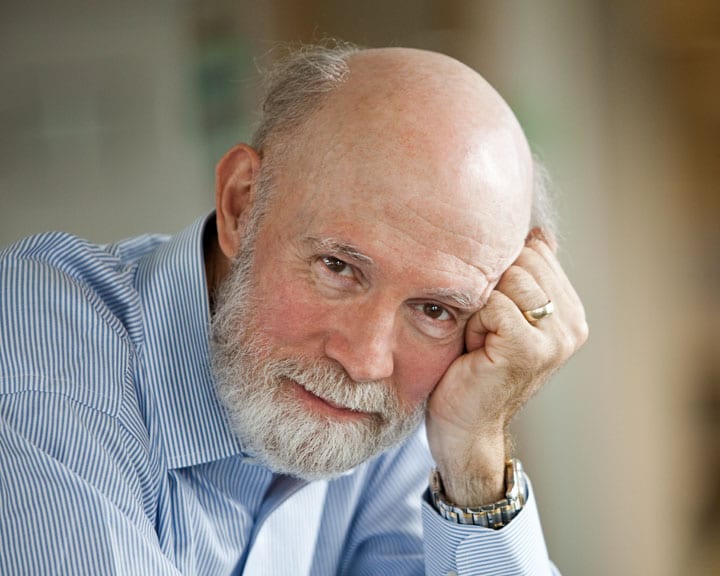
Read more
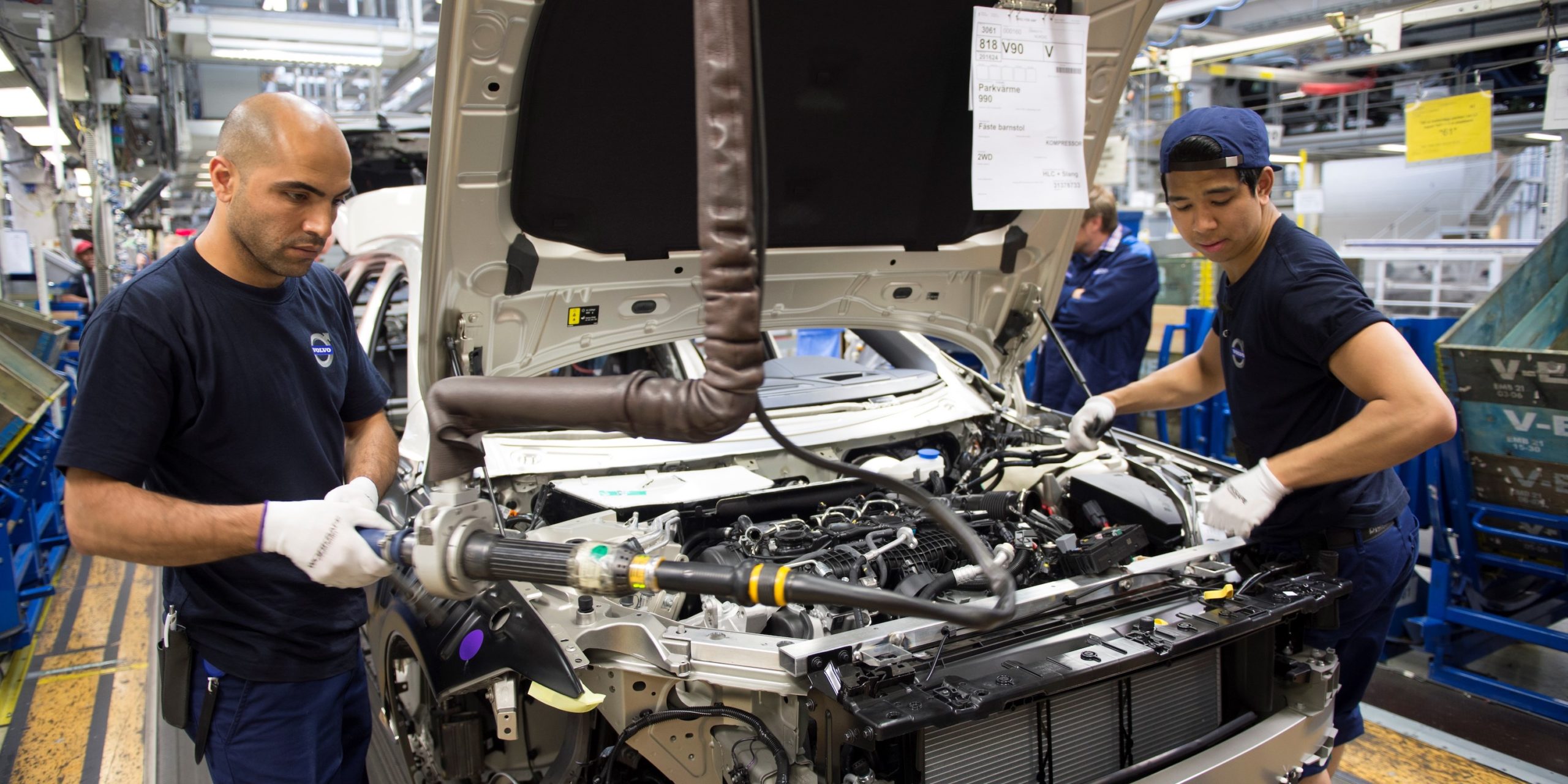
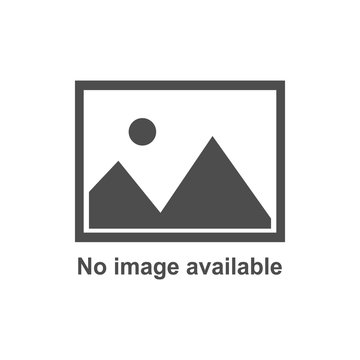
CASE STUDY – What is the approach to people development used at Volvo Cars? The authors explain how the organization has created a production system fully owned by operators and managers.
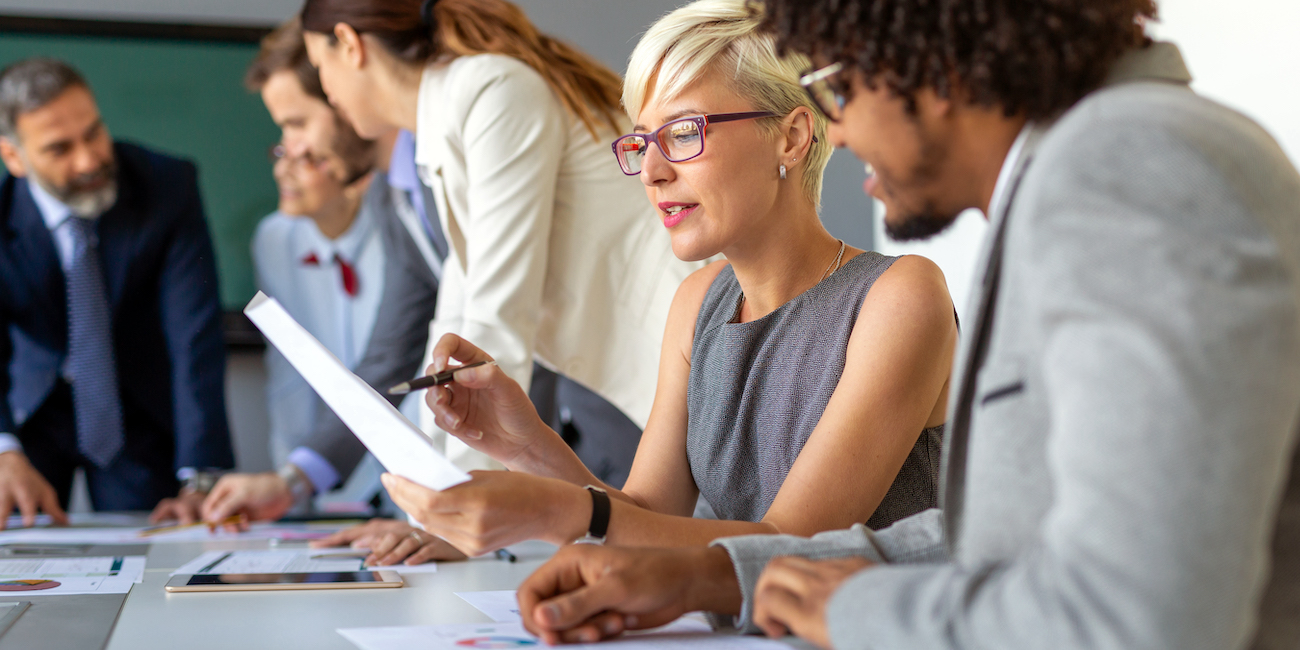
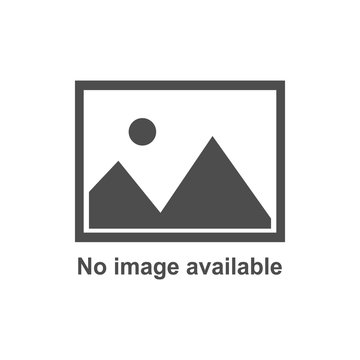
FEATURE – Variety in sensei approaches can cause a lot of confusion. The author sheds light on the subject by describing a sensei’s five modes of interacting with individuals and teams.
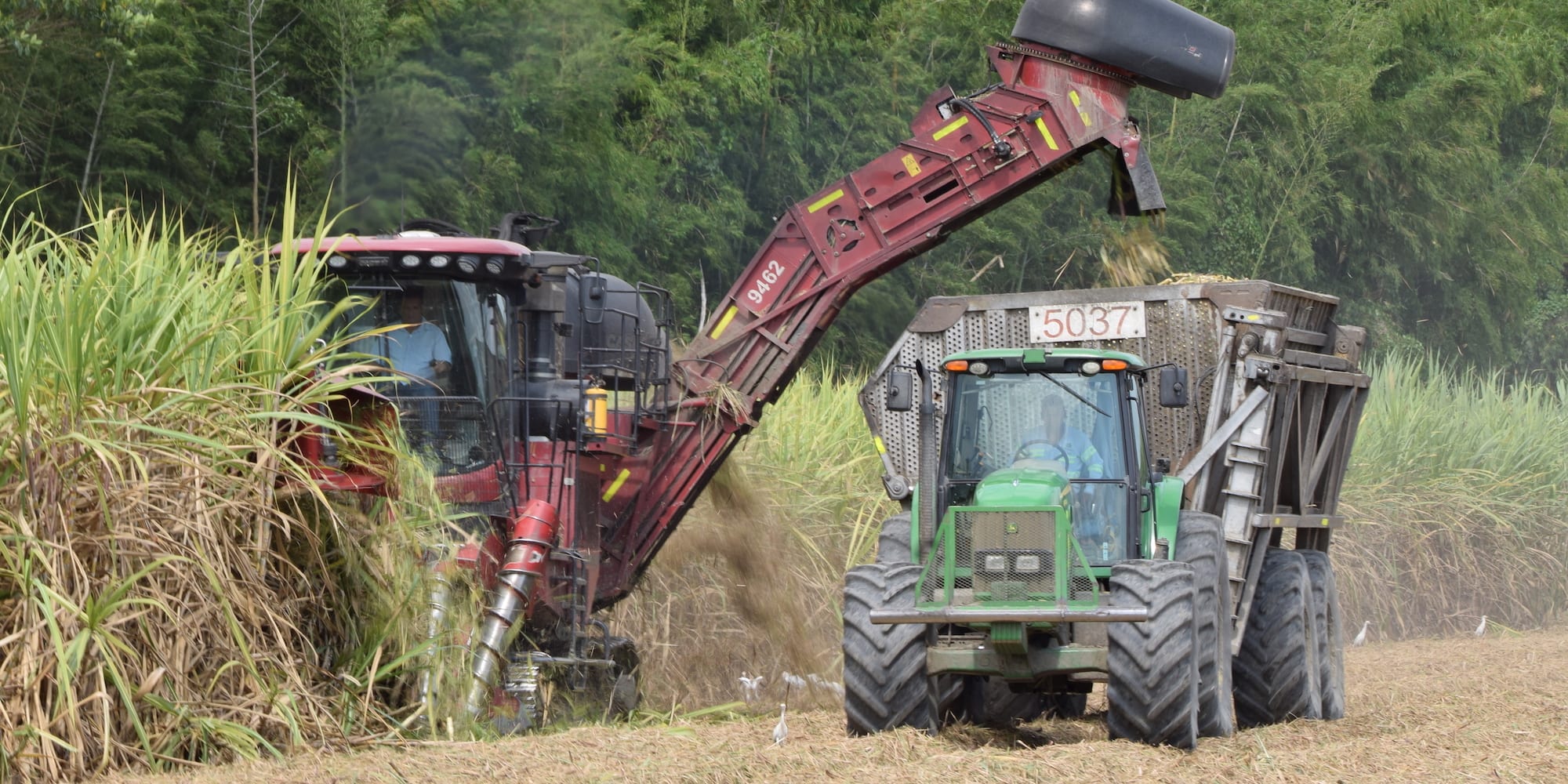
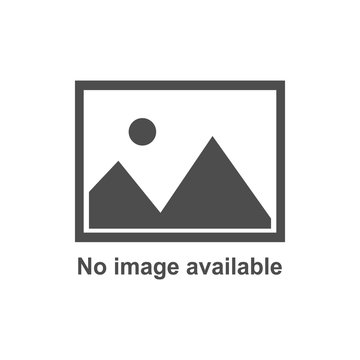
INTERVIEW – This agro-industrial business in Colombia is applying lean thinking to its harvesting process. The harvest manager explains the difficulties and opportunities encountered on the journey so far.
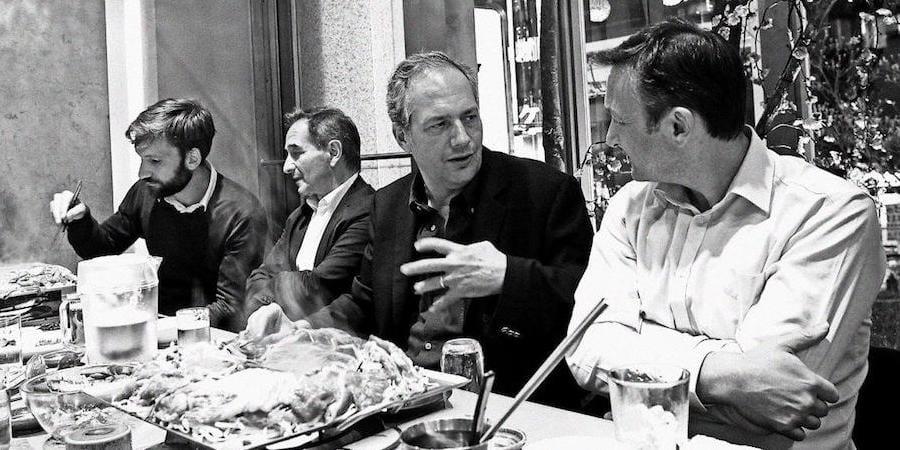
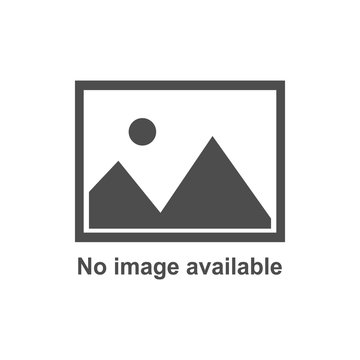
FEATURE – Following a visit to a Toyota supplier in Japan, the authors reflect on the nature of kaizen and explain why we might be looking for it in the wrong place.