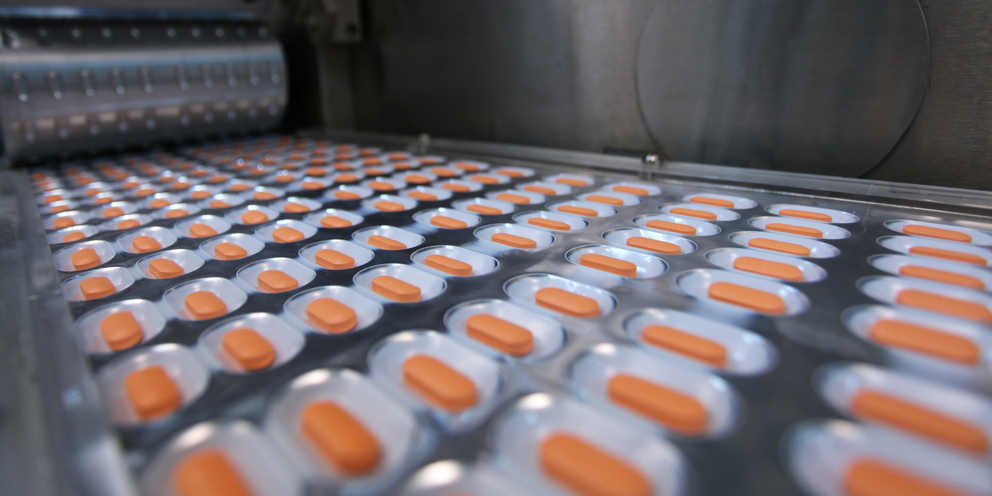
Lean in internal supply logistics
CASE STUDY – The implementation of lean in the internal logistics of a pharmaceutical company in Brazil proved key to increasing productivity and quality in the organization.
Words: Alvair Silveira Torres Jr., Project Manager, Lean Institute Brasil
Every company wants to grow. However, growing your market share comes with the challenge of increasing production with the existing equipment to meet customer demand. A large pharmaceutical company in Brazil recently encountered this very challenge and turned to Lean Thinking to boost its production capacity. Their focus was to improve on-time delivery for a wide variety of materials and inputs at different points in the production process, in the face of limited space. For this company, growth brought logistical difficulties.
The situation presented itself as the common problem of making the well-known “seven rights” a reality in their internal supply logistics: delivering the right material, in the right place, at the right time, at the right cost, in the right quality, in the right quantity, and to the right person. They also had to deal with the many restrictions imposed on pharmaceutical companies by national and international legislation with regards to the occupation of spaces and the handling of materials in the production and storage areas.
At first the company invested in logistics automation, which required a major readjustment of the factory and actually had a negative impact on profitability. Seeking a simpler and more effective solution, the company decided to bring Lean Thinking (already in use on the manufacturing floor) in internal logistics, introducing just-in-time and a milk run (a system of delivery of materials to the point of use at takt time – only what’s necessary in a short production cycle is provided).
The implementation benefited from a strong interaction between the internal teams, leading to the creation of a road map that ultimately yielded the expected results. Lean was added to the traditional seven rights – service and logistical execution using the right method and tools, synthesized in the expression of “right-sized tool” used by Jim Womack and Dan Jones in their seminal book Lean Thinking.
UNDERSTANDING THE PROBLEM
In 2017, the company was trying to improve its processes and tackle the problems brought about by its growth, but without resorting to large investments. A typical lean challenge: to do more with less, respecting people, and tapping into their knowledge.
The first step was to draw a value stream map, which revealed the root cause of the problem of increasing capacity: the lack of connection between flows. Materials were pushed in batches from one operation to the other in large containers, which made the situation worse, as space and time were wasted in unnecessary movement.

Figure 1: Current State Map (Estado Atual = Current State)
The team then deployed some countermeasures based on their findings to try and reach its profitability goals. Managers and leaders met and developed a set of three A3s based on the “mother A3” of logistics.
These reports and the countermeasures they identified led the company to more accurately plan their problem-solving steps and, subsequently, to deploy them using hoshin kanri. The internal supply A3 had the role of kick-starting the transformation and connecting the outbound and inbound flows of material considering the continuous production flow the team wanted to achieve.
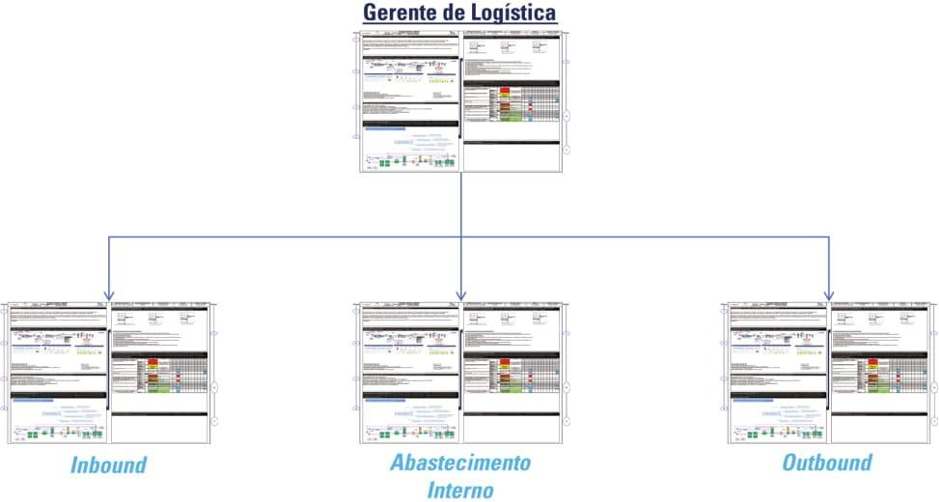
Figure 2: A3 set in logistics operation (Gerente de Logística = Logistics Manager; Abastecimento Interno = Internal Supply)
The main objectives the team set were increasing capacity by 30% in 2018, to meet the increased demand and growth prospects without any major investments, as well as decreasing the inventory of materials by 20%.
REVIEWING THE CONCEPTS OF LEAN INTERNAL LOGISTICS
The concept of continuous flow is central to building waste-free internal logistics and meeting standards. In logistics, this concept reflects itself in the practice of just-in-time: delivering the materials only when they are necessary. In the internal supply, one of the tools to bring this to life with a high degree of precision is the milk run.
Marrying just-in-time deliveries with production demand makes it possible to build a working network of flows. We can make the analogy with a tributary freely flowing into a river, with no dams or waterfalls interrupting its flow. Similarly, in a milk run a set of towed carts moves continuously, delivering parts to the production line.
Deliveries are carried out by the supplier using a standard: they follow a pre-defined route, with planned movements and containers, stopping for loading and offloading carts at pre-defined stops. Any delay or advance in the production and delivery cycle will be quickly identified. This system works like a poka-yoke for flow, warning of any deviation from the plan. In this way, there is no excess of materials, which could potentially hide failures that might occur. The goal is to achieve synchronization between deliveries and the pace of production.
Standard work also impacts activities in warehouses, and movement across the business more in general. The content of packages is pre-defined, and storage addresses are established to expedite the loading of the carts. Standard work also couples offloading points with the operators of the machines, who know and follow the material supply cycle time (supported by visual management indicating the production schedule for the day, on an hourly basis).
This approach ensures people always know what is going on in the business. If an anomaly occurs – a delay in delivery, for example – everyone quickly learns what happened and the help chain can be triggered before the problem actually impacts production. The anomaly is studied and tackled, so that it no longer occurs, by investigating its root cause and pursuing the seven rights.
Strict adherence to schedules and quality of delivery are achieved as the standard work for the entire team and its synchronization at the points of coupling flows is perfected in such a way that, at any given moment in the implementation, the necessary stability to initiate pull is achieved. Planning is informed by the supermarket levels, visualized in the Kanban boards.
STARTING THE LEAN TRANSFORMATION
In the pharmaceutical company, it all started by connecting and synchronizing production with internal logistics, line after line, through milk runs and the establishment of supermarkets in the entrance and exit warehouses. Each milk run route was designed to deliver all materials and supplies at each point of use of the equipment within an hour.
This way, operators received the material (ready to use to feed the machines) on trolleys, in returnable containers with the exact amount needed for one hour of production rather than in cardboard boxes. The operator simply had to remove the container from the cart and load it in the automated feeders of the equipment. The logistics operator, in turn, took the loaded trolleys on his outward journey, distributing them at each stop, and collected the empty containers on the return trip. The routes were connected to the previous supermarkets with inbound materials and to the later ones with outbound materials to be shipped.
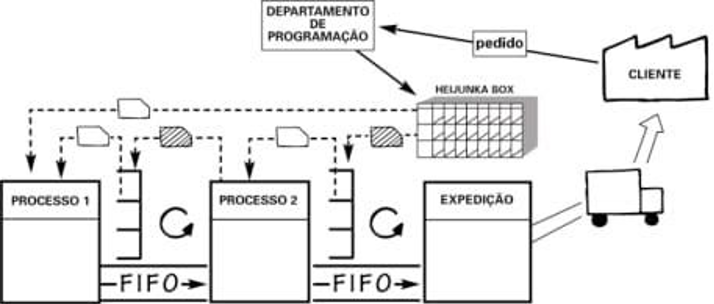
Figure 3: Continuous flow of materials and information
This implementation took place in the period between May and October 2017 as indicated in the internal supply A3. Steps were carried out monthly with deliverables established in the action plan below:
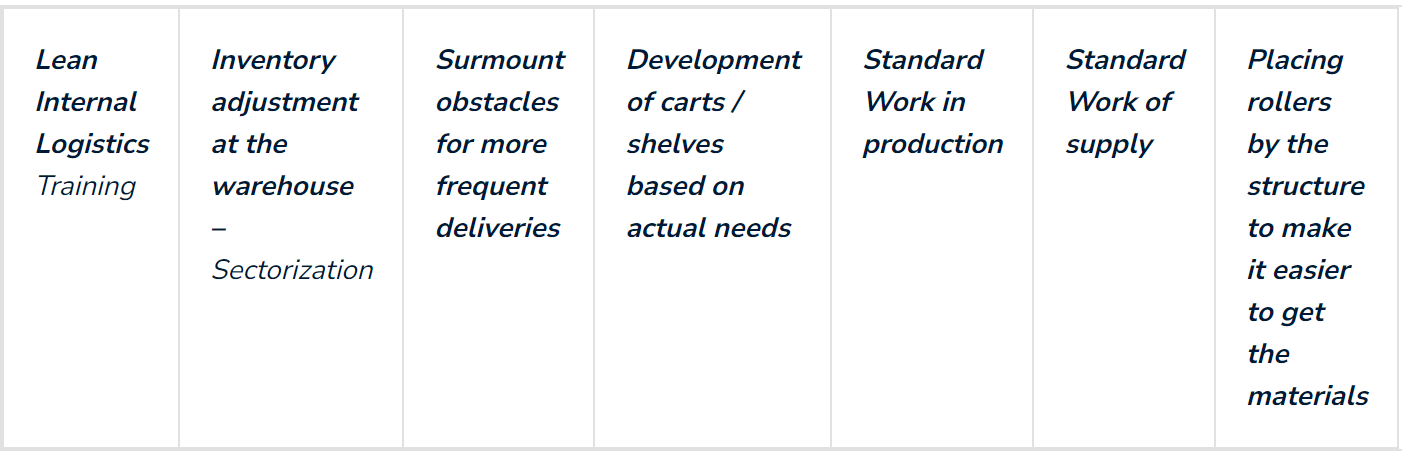
Figure 4: Action plan
In November 2017, the first internal milk run route was paired with the supermarkets in the warehouses. In pursuing the future state, bounded experiments and simulations had been carried out since May 2017.
This was a peculiar strategy to adopt in the pharmaceutical industry, where the application of lean is still new and regulation plays a very important role. This is why the first experiments were carried out outside of the production environment, in a space in which the future state was easier to visualize using low-cost, low-fidelity materials. The objective was to establish a proof of concept and a level of understanding among the participants.
Following that, the group gradually moved to small experiments in the production environment: the circulation of a test vehicle on the proposed route; trials with cart prototypes and packaging; timing and detailing of methods and movements with production and logistics operators. Improvements were being made with each test, until the final solution was reached.
THE RESULTS
At the beginning of 2018, what we had learned with the pilot milk run was applied to other supply routes. In all of them, observations at the gemba revealed a reduction in operator movements and greater control over the takt time with subsequent adherence to planned schedules. The internal milk run worked as a belt that delivered the right materials to operators at the right pace.
Productivity increased by 22%, with a more efficient organization of the operators’ work within each one-hour block of delivery. Movement, for example, was reduced between the points of use and the supply station, as shown in the before-and-after Spaghetti Charts below.
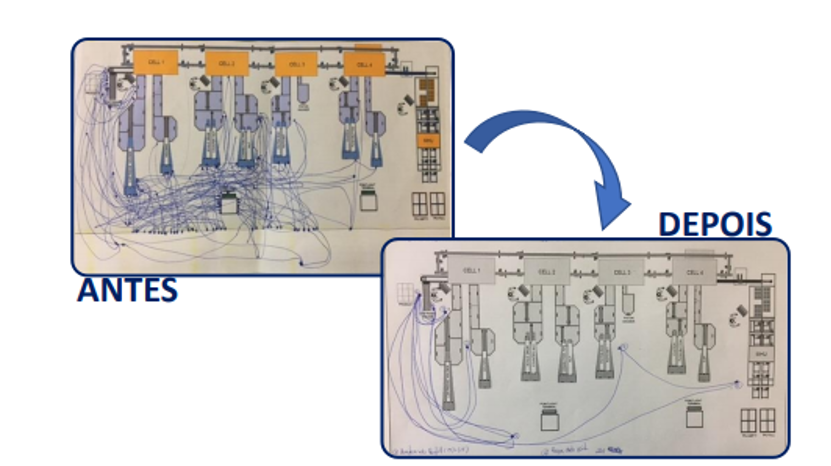
Figure 5: Comparison of Spaghetti Charts before and after implantation (Antes = before; Depois = after)
Moreover, having the right materials available at the right time reduced shortages, increasing the OEE. Combined, greater productivity and improved equipment efficiency made it possible to meet the increase in capacity without any further investment. In terms of inventory, a 30% reduction was achieved in inventory (the goal was 20%), with the idea of improving it even further in the future. A list of other results achieved can be seen below:
- 95% reduction in handling of materials;
- 40% reduction in production order preparation time;
- 66% reduction in material transport;
- 97% reduction in production inventory;
- Zero ergonomic problems in production;
- 22% increase in productivity (two operators per shift).
Finally, this case also provides great learnings with regards to the application of Lean Thinking to logistics in a highly regulated environment like the pharmaceutical industry. The practice of iterative, gradual experimentation for an understanding of how to reach the future state allowed the team to repurpose the actions and processes tried out during the experiment in the real-world setting, which made people at all levels feel safer and more confident about the change. Furthermore, adequately standardizing tools, trolleys and supply methods promoted incorporation of an eighth element in the “seven rights” of logistics: the right tool and method.
Originally published in Portuguese on Mundo Logística Magazine.
Source: Lean Institute Brasil
THE AUTHOR
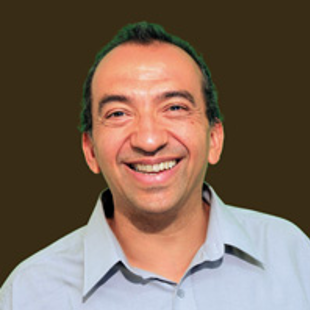
Read more
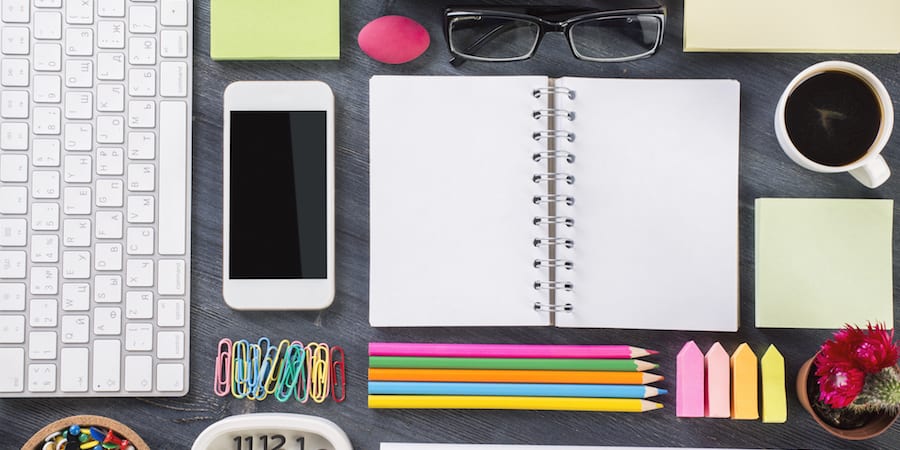
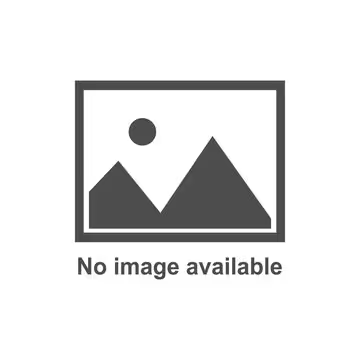
WOMACK’S YOKOTEN – 5S seems to mean different things to different people. What’s common, however, is the difficulty to sustain it. The author offers a few tips.
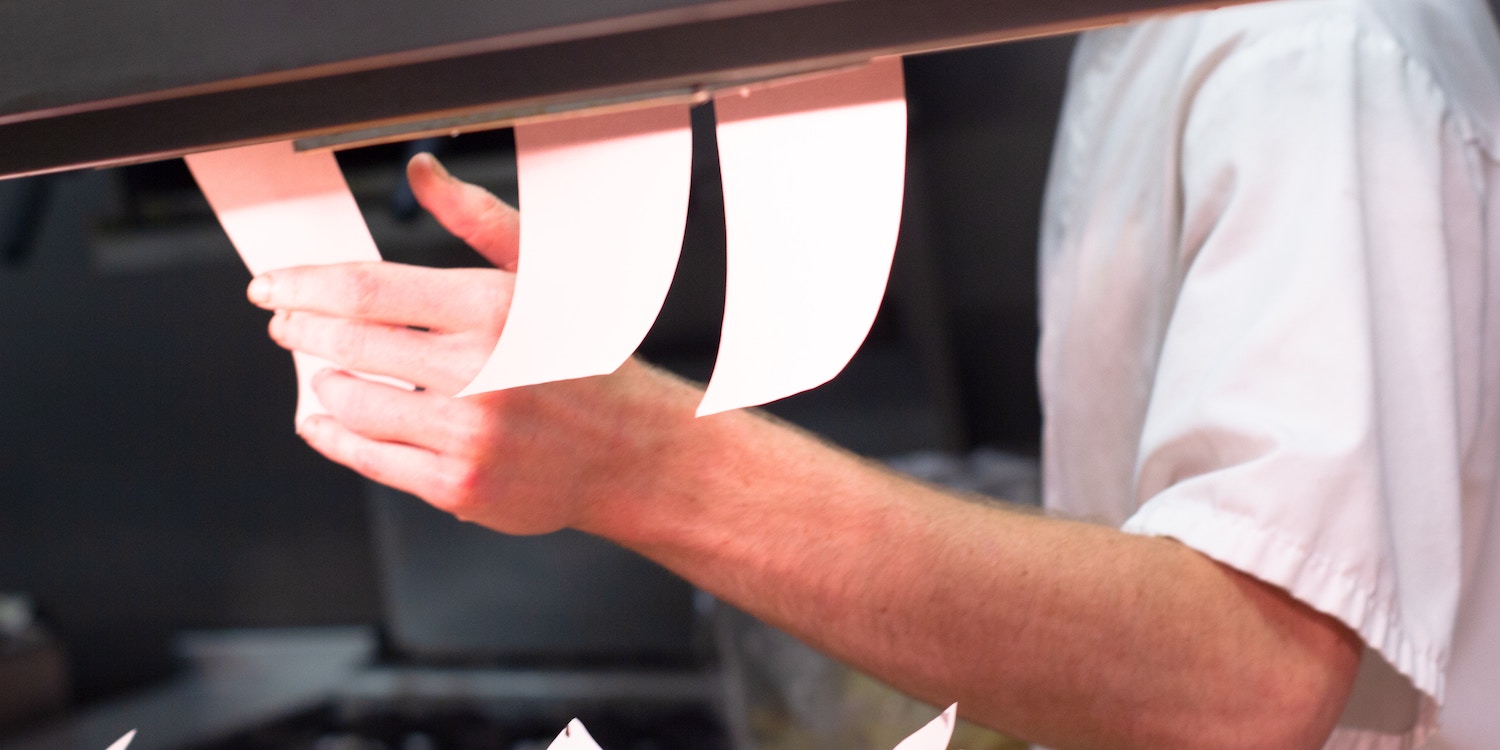
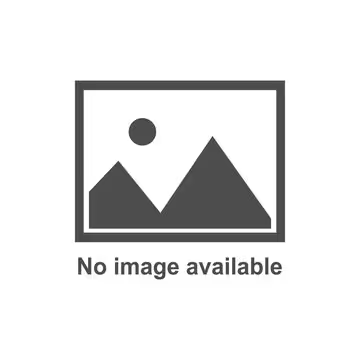
FEATURE – The author explores the relationship between kanban and improvement and discusses how using it can impact our lean transformation.
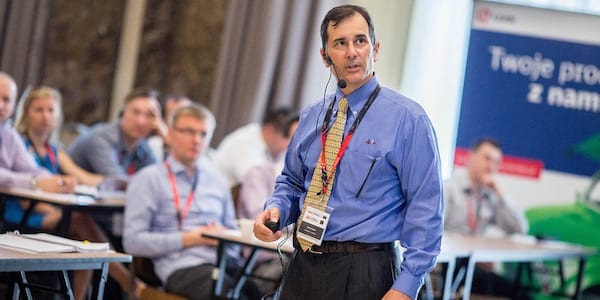
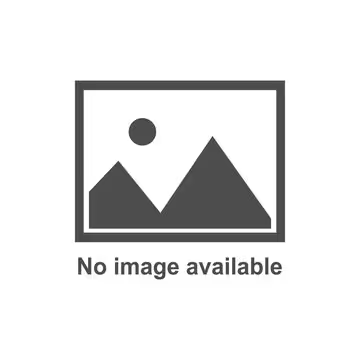
INTERVIEW - What lies at the core of kaizen activity? How has the concept of kaizen evolved over time? Planet Lean’s editor Roberto Priolo discusses these and other topics with kaizen expert Mark Hamel.
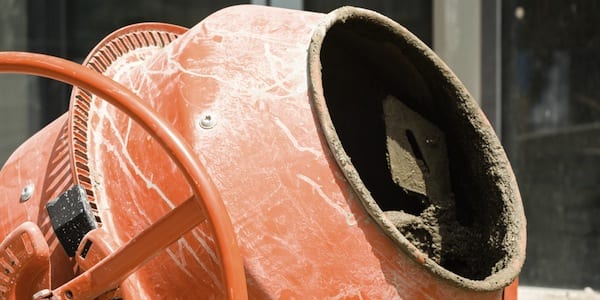
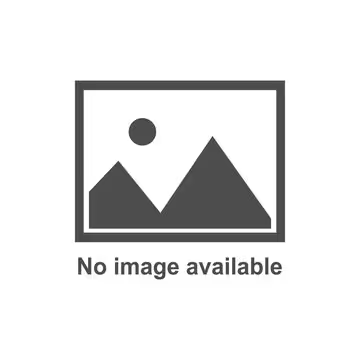
CASE STUDY - Addressing failure cost and introducing a new quoting process are only two of the ways in which Dutch construction company Dura Vermeer is successfully achieving a lean transformation.