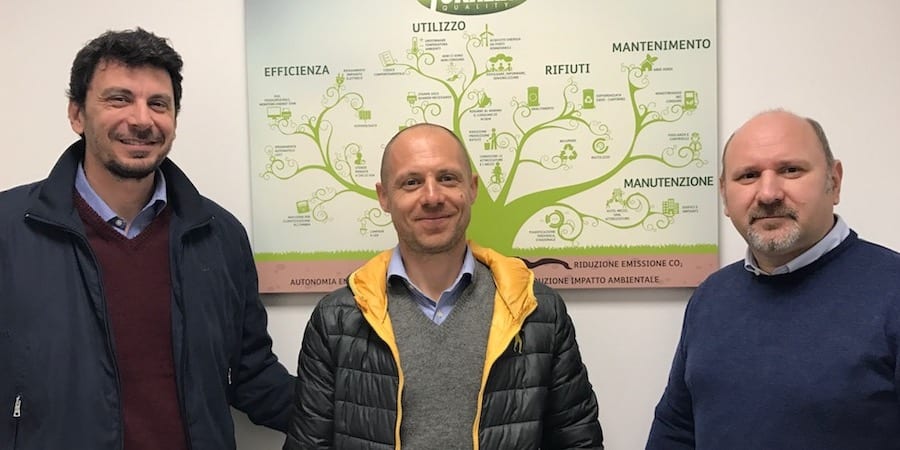
How Tokheim uses 5s to boost its environmental performance
FEATURE – The many benefits of 5S are well known, but few people realize the positive impact the technique can have on our environmental performance, says our lean and green correspondent after visiting Tokheim Italia.
Words: Kelly Singer, Director, Lean Green Institute and board member of Institut Lean France
Certain green stories get all the love. Solar power and passive buildings, for example, make for attractive headlines because they pique interest about what our future holds. By contrast, the real-life stories about the day-to-day work happening to help us reach a green future are often overlooked. So, let me share one such story, which takes place at a service company in the quiet town of Garbagnate, 15 kilometers outside of Milan.
Tokheim began as a manufacturer of fuel dispensers in 1901, but now offers a suite of products and services including project management, installation and maintenance on fuel dispensers (both for Tokheim products and competitors), and technology and payment solutions in over 30 countries. The Garbagnate location provides services to the greater Milan region.
Tokheim Milan COO Furio Clerico and his directors Mauro Cartello and Raffaele Romagnolo are careful stewards of Tokheim's investments and infrastructure. However, this frugality and resourcefulness is not just for the sake of improving the bottom line. Furio said: "The greenest building is the one that is already standing. In all our decisions, we consider the environmental waste we'd create by replacing our fixed assets with eco-friendly options. Most of what we'd replace would go straight to the landfill and, on a carbon and Life Cycle Analysis scorecard, that just doesn't make sense. We can still compete on environmental performance with what we have, starting today."
The trio created a Green Manifesto to act as a "true north" to align company decisions with its long-term vision. That was a year ago, and their environmental results have been outstanding. So much so that their Manifesto and eco-improvement activities are now being shared and implemented at Tokheim locations across Italy.
But perhaps the most remarkable point of this ongoing "lean and green" transformation is that Tokheim has been able to realize as great an environmental performance as companies two or three times its size, and without a dedicated Corporate Social Responsability team.
How did they do it? By focusing on encouraging all employees to partake in one of the great lean basics: 5S. The practice of this workplace organization approach is known for its contribution to improved safety, quality, costs, and delivery time. Now, Tokheim has shown that 5S can produce environmental performance, too.
5S was developed at Toyota and can be translated from the Japanese words as "sort", "set in order", "shine", "standardize", and "sustain". The idea is a simple one: organize a work space for efficiency and effectiveness by sorting out just the necessary work objects, setting these objects in a dedicated place, keeping a tidy order and providing regular maintenance, and sustaining it all. An employee-centric workplace is the foundation of a thinking organization and encourages all team members to adopt an "ownership" attitude – the lynchpin of a lean and green transformation.
Tokheim focused first on the low-hanging fruit of the unused and excess: through 5S, employees eliminated the excess of inventory, unnecessary boxes and storage, machines, and freed up unused warehouse space. They were ruthless in their judgement, evaluating based on the question, "Does this item make us more effective?" Whenever the answer was no, the item got removed.
After working on this for several months, the reduction was significant and Furio realized they could operate in a much smaller warehouse and office. So, they moved to another, smaller location. Mauro said: "Waste generates waste. The better we become at eliminating waste and identifying things of real value, the smaller our impact on nature and use of natural resources, and the greater our business success." Tokheim's new office space is a third smaller, and so is its carbon footprint, while rent has been reduced almost by half.
TACKLING SCRAP
Tokheim employees continued the practice of 5S in their new location, this time tackling the organization of waste and scrap metals. Having a place for each kind of metal keeps the warehouse neat, but the real benefit is that the sorting makes problems visible. Employees can identify when there's isn't a solution available for a new type of waste, or when there is a deviation from a standard – like when a similar looking, but much more rare metal is placed in the wrong bin.
Sorting also raises the probability that materials end up in the right destination, a critical practice for the transition to the circular economy – a high priority for the European Union. (Materials of the same type and quality maintain their value when they are recycled together, whereas recycling mixed metals results in a substance that can only be used for lower quality products, requiring more precious metals to be extracted for production.) Tokheim can also resell its "waste" to another company at a higher cost when it's separated, and there is a lower pick-up fee from the city's waste management when recyclables and landfill trash are separated.
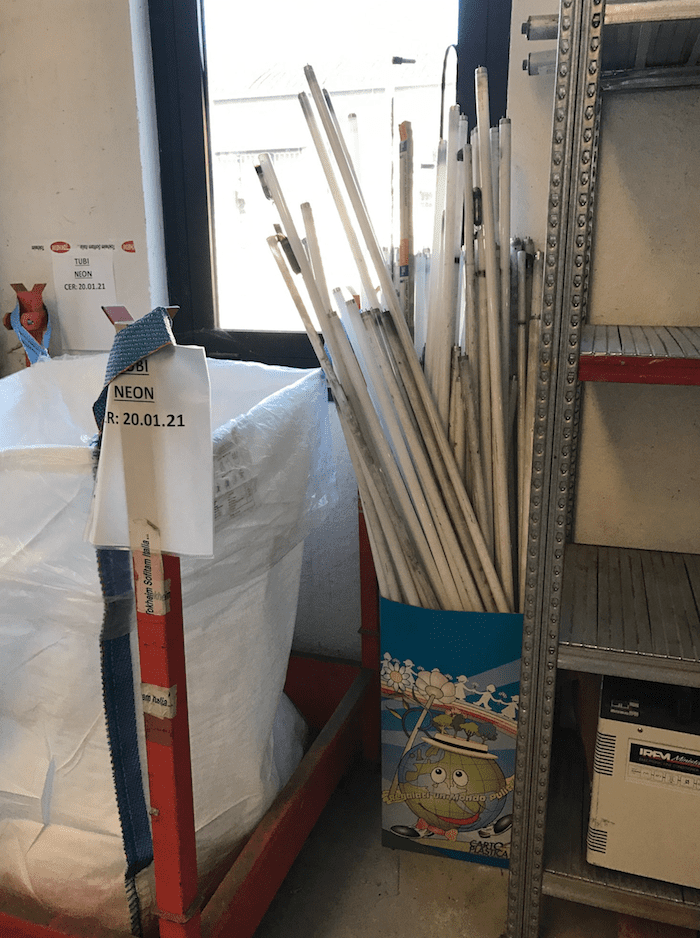
The practice of 5S showed warehouse employees how much packaging waste there was. They challenged themselves to reduce this by 50% through the coordination of many other departments, offices, and suppliers. In the end, they surpassed their goal (measured by weight) by implementing the use of reusable containers for shipments between internal offices in Italy. Externally, they worked with suppliers to find containers which could be refilled with installation materials and delivered more frequently, reducing the size of bins in the warehouse. This eliminated landfill waste of plastic packaging and even resulted in a small discount from the supplier. Currently, the warehouse team is investigating the possibility of buying more packaging-free supplies and expanding reusable containers for all service activities.
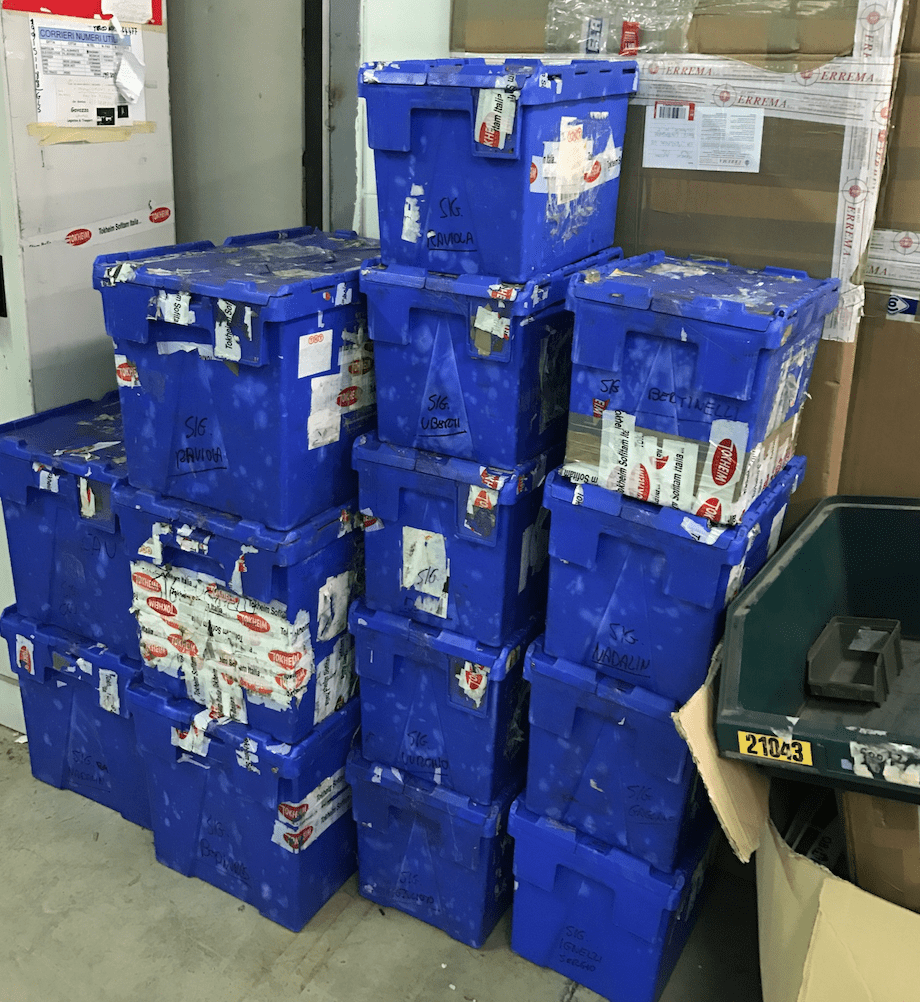
Outside the warehouse, the service and technician team have also seen environmental success with 5S. They are on the road every day installing new products and fixing others for customers, and all this travel results in air and other environmental pollution, the reduction of which is part of Tokheim's Lean Green Manifesto. "We know there are better options than fossil fuel vehicles with which to provide our services. We are working towards making clean energy a reality for our company. In the meantime, however, we will do the best we can by maximizing our van's fuel efficiency and reducing unnecessary travel. We're not just going to sit on our hands until we have the perfect solution," said Raffaele.
Vehicle weight and engine power are two of the most important parameters that influence a vehicle's fuel consumption and CO2 emissions, so the service and technician team decided to focus their efforts first on organizing the service vans for better fuel efficiency.
The vans were cleaned out from time to time, but everyone knew they carried "just-in-case" parts and unnecessary tools that had accumulated over the years. The team gutted the vehicles and reorganized them based on the critical few tools and equipment that were necessary to complete the majority of jobs. The tools and parts needed for specialized jobs were kept out of the vans and only taken when needed. This simple change reduced the van's weight by 140 kg. An MIT study found that for every 100-kg reduction, the combined city/highway fuel consumption could decrease by about 0.4 L/100 km for light trucks and vans. This improvement has prevented the release of thousands of tons of carbon emissions, and saved Tokheim thousands in fuel costs.
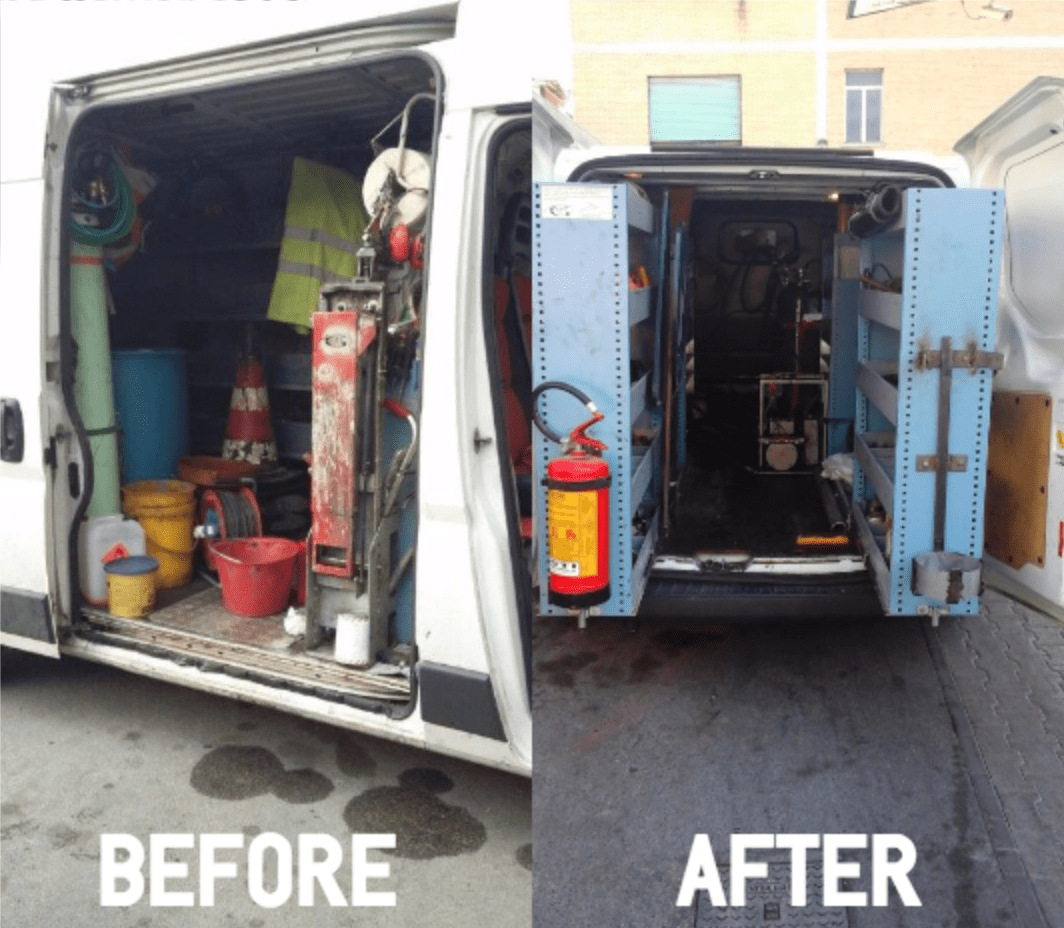
The improved organization of the vans also meant fewer rescheduled services because technicians could easily confirm they had all parts and equipment necessary in working order to get the job done. Seeing the reduction of C02 and increase in profitability from fewer trips, the service schedulers were asked to join the challenge to increase service trip efficiency. From their experience, technicians knew that their trips could be planned better to save considerable emissions, as they would often zig-zag across town driving to jobs on demand and back to the warehouse to pick up parts in between. A new standard was set up to schedule service trips in proximity to each other. When an urgent request was received, it was dispatched to the technician already in that area.
Tokheim has demonstrated that one of the most responsible things we can do for the environment is to take care of what we have so it lasts longer and find ways to make it work better. It's just as easy to make small, daily green improvements as it is to continue to waste and degrade our planet. Abraham Lincoln said, "The future comes one day at a time."
THE AUTHOR
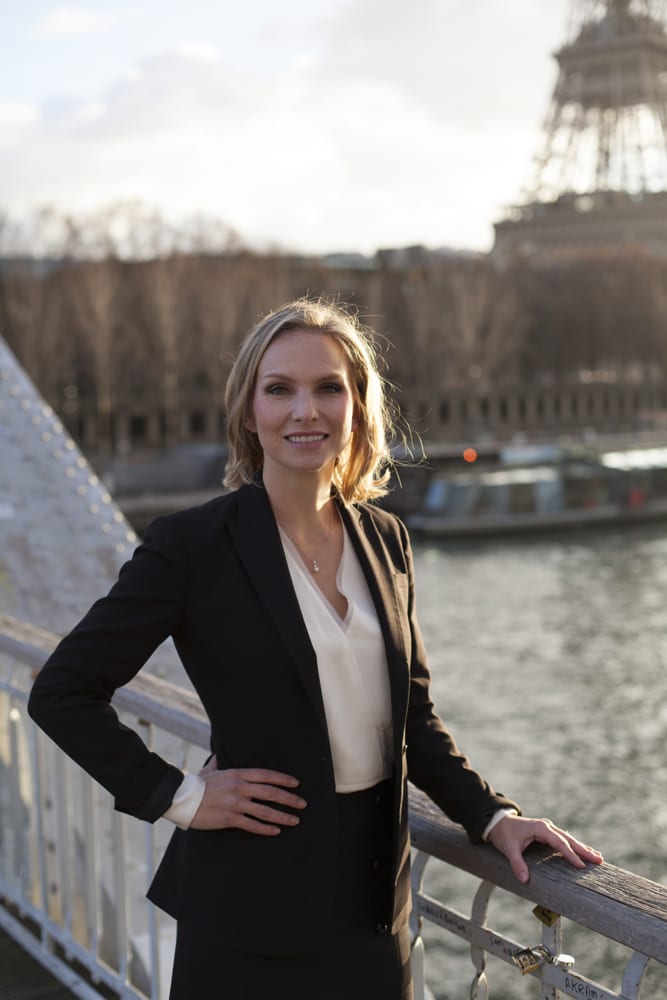
Read more
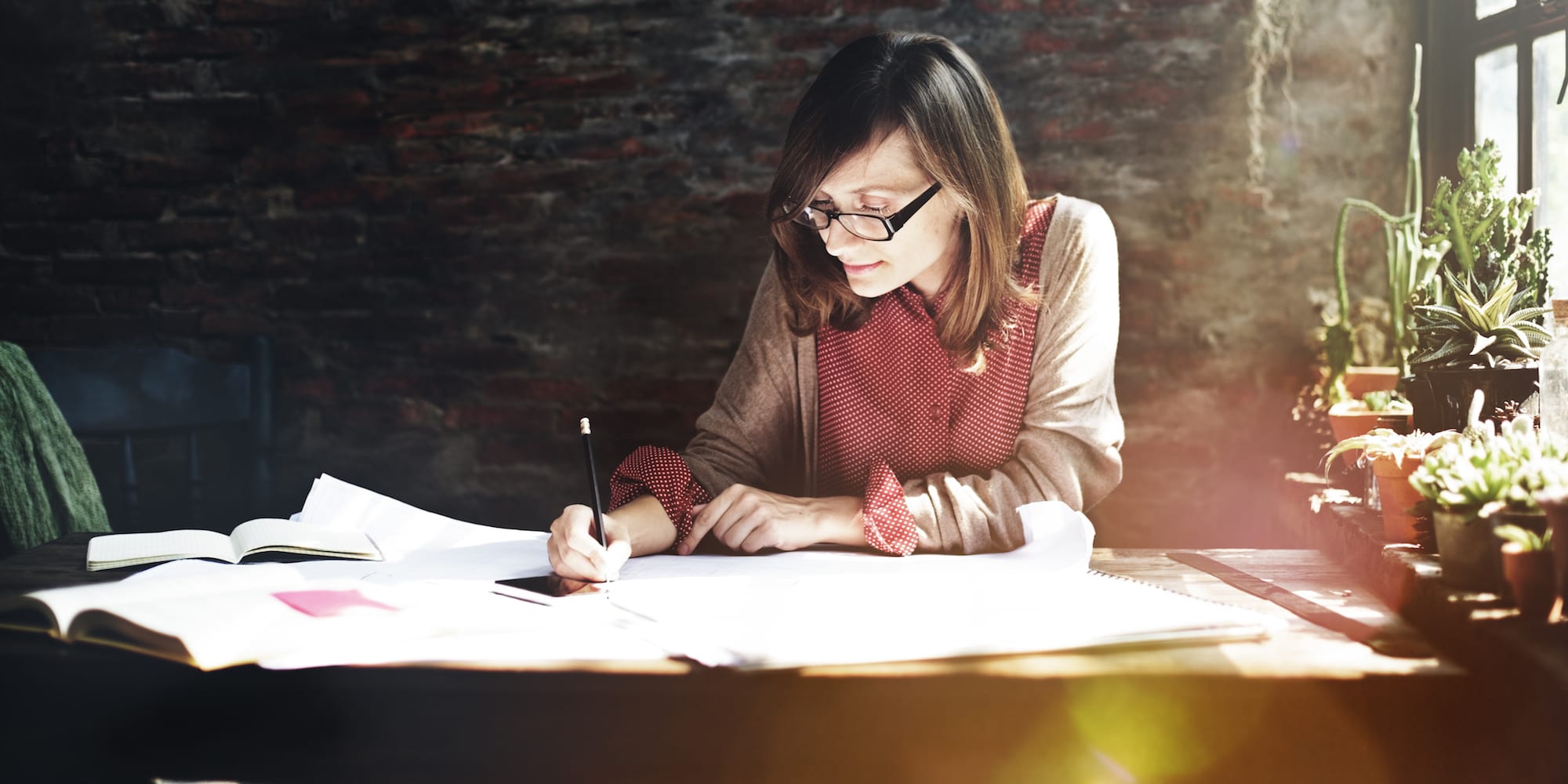
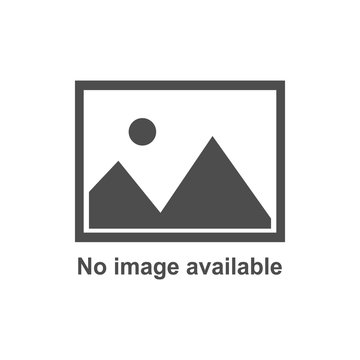
FEATURE – This article offers an exhaustive explanation of how to prepare a Concept Paper and why this is a tool that will help us to succeed in the execution of large change projects.
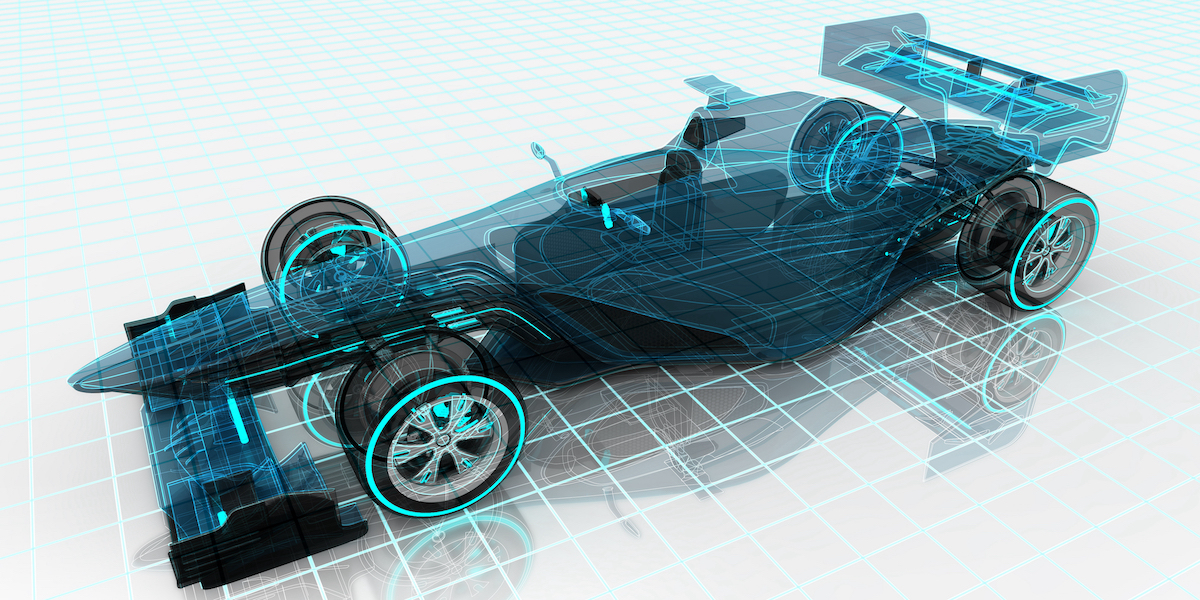
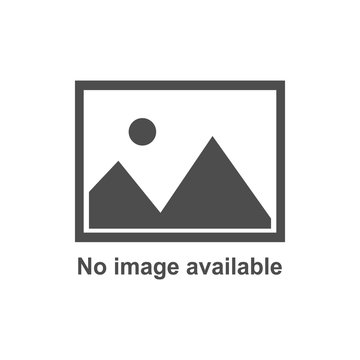
SERIES – In the final article in their series on lean process development, the authors discuss what it takes to get started with their 6CON process development model.
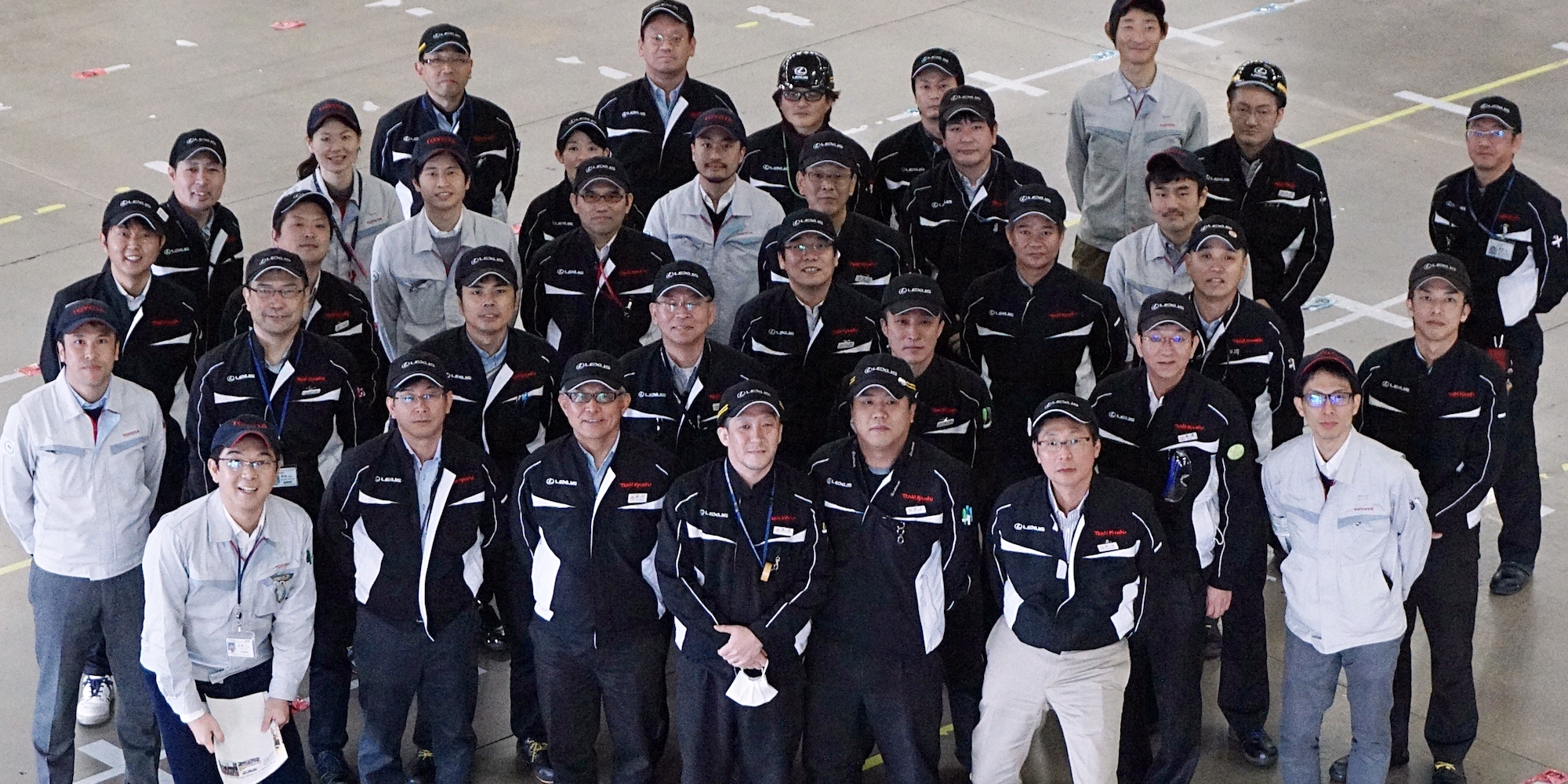
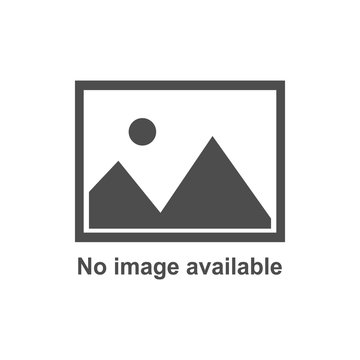
INTERVIEW – A team from LGN just spent a week on the gemba with Toyota veteran Hideshi Yokoi for a jishuken exercise. We asked him to explain to us how he used this practice while at Toyota Motor Kyushu.
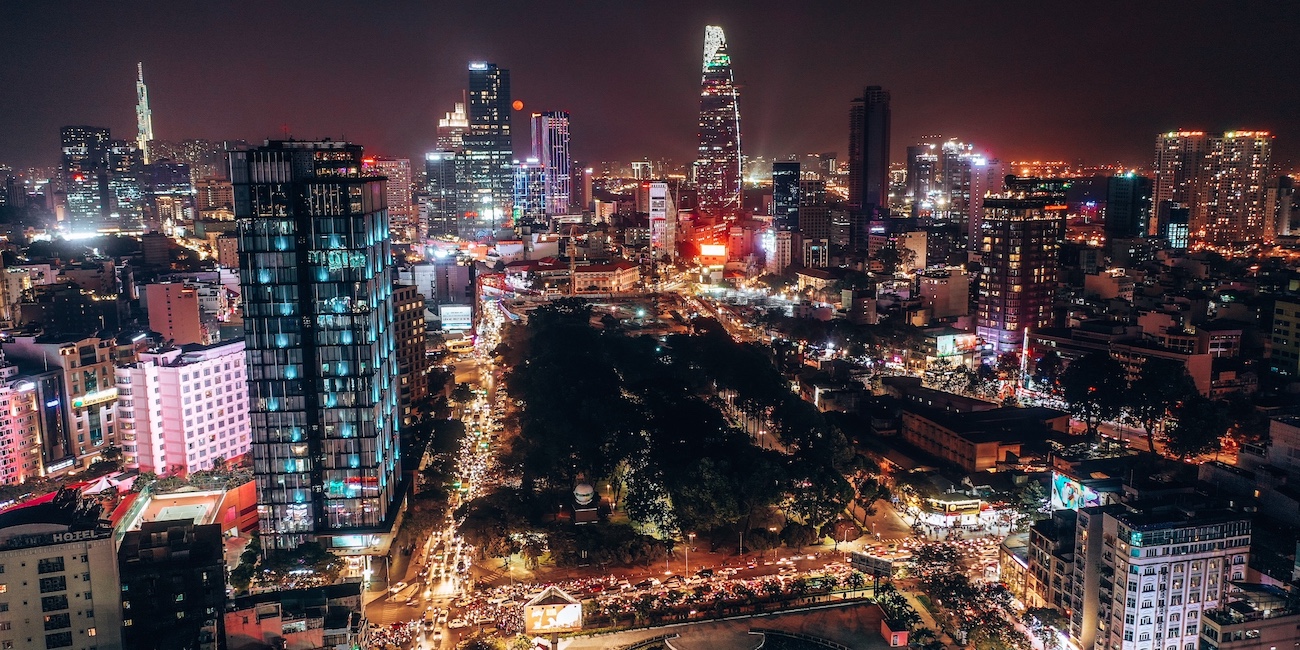
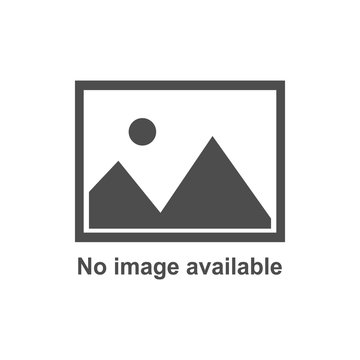
INTERVIEW - On April 18th, Lean Global Network and KD Consulting will hold a not-to-be-missed event in Ho Chi Minh City for the Vietnamese lean community. In this Q&A, Tony and Khoa tell us what to expect from the summit.