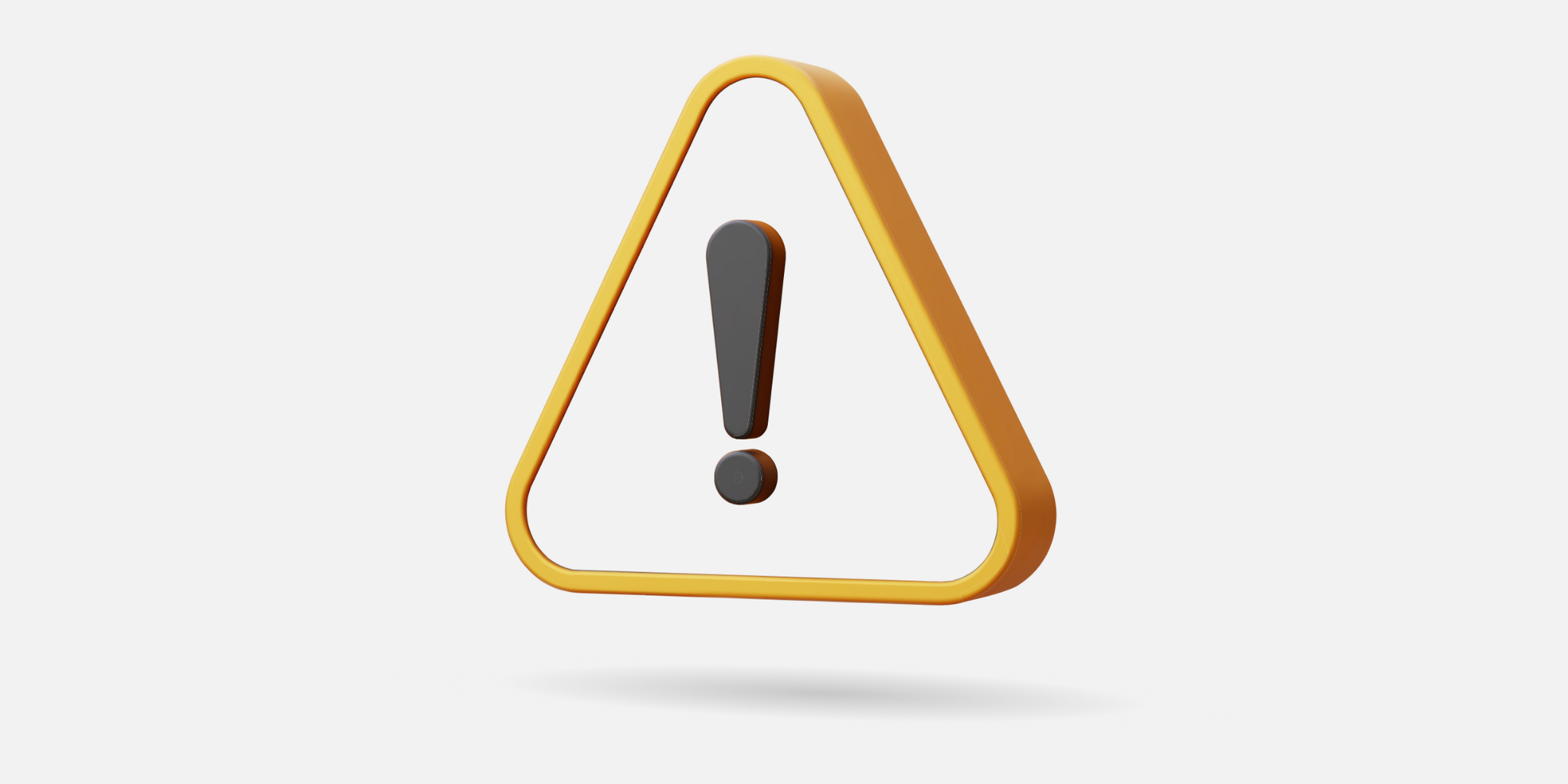
Five lean mistakes to avoid
FEATURE – Based on her experience at Lean Institute Colombia, the author lists five common mistakes hindering a lean transformation. Take note!
Words: Angélica Gutiérrez
No matter where you are on your lean journey, you have surely made some mistakes. They might have caused one or more false starts or stopped you in your tracks just when you thought you were getting somewhere in your transformation. No matter when or where they might occur, rest assured… you are not alone.
In our experience coaching organizations here in Colombia, we have observed a number of mistakes that most organizations end up making. Read carefully and you might just avoid making them yourself.
- Think of lean as a program or a tool
Every organization that views lean as a program or just as tool for the improvement of a process doesn’t achieve more than some low-hanging fruit. They see some early results – often remarkable ones – but nothing else comes out of it. After a while, things go back to the way they were, and people are left with the impression that lean was something the manager brought in, that they liked but wouldn’t know how to do again. This short-term view of lean prevents the business from achieving real cultural change and from having a real impact on its deeper problems.
- Lack of leadership engagement
Without the full support of top management, no lean effort can reach its full potential. Lean requires leaders to be examples, inspiring and unstoppable in their pursuit of continuous improvement within the organization. Without the proper leadership attitude, whatever improvement is made won’t survive in the long term. Lean calls for a shift in mindset and it is up to leadership to spearhead the development of those new habits and behaviors that shape a new culture within the teams. They may be few and far in between, but top management teams that are fully engaged in a lean transformation carry a lot of charisma, which they can leverage to get everyone on board.
- Weak communication
– “Did you know the Distribution Center is doing kaizen?”
– “What is that for?”
– “It’s meant to cut costs… and reduce headcount.”
If you hear conversations like this, chances are you are not doing a very good job at communicating the purpose of the transformation, the reason why the company is pursuing change, and the victories and learnings that appear along the way. When people don’t understand something, they find it extremely hard to support it – they have too much doubt and the fear of change often overwhelms them.
The stronger and more bidirectional the communication, the higher the chances that people get rid of doubt, start to highlight problems, and grow confident in the value of the improvement initiative. Expecting change when your management team doesn’t communicate properly is a recipe for failure.
- HR not involved
A lean transformation profoundly changes the work, so it’s only natural that people’s skillset, career paths, professional profiles the company is after, and even remuneration should evolve, too. All of this is normally a prerogative of the HR Department. What we see is that when HR is not aware of what the lean transformation is trying to achieve and not involved in it, it will struggle to respond to business needs and hire the right people.
I remember a manager complaining to me that a new hire had a very traditional, mass-production way of thinking and that he didn’t know how long it would take the organization – which had already turned to pull and lean production – to “convert” them.
- Lack of understanding
This mistake is directly related to training and educational activities. Some managers will say they have no time to get involved and participate in the lean training; others explain that they already know about lean because they got a “belt”. Their understanding of lean is limited to the amount of money they were able to save by improving a certain process. There is nothing wrong with that, per se. The problem is when, during a momentous cultural transformation, some leaders continue to see lean as cost reduction and don’t participate in lean training or coaching sessions. This lack of understand of what lean is all about ends up generating a lot of waste and potentially water down any efforts to transform. Another recipe for disaster.
To understand the essence of lean thinking and practice means to understand that continuous improvement is not just for the company – it’s also for you as a leader and learner. We want results, but we fail to see that we are the ones who need to change before they can appear.
Mistakes are a part of any transformation. Indeed, they are a part of life. The point of lean is not being perfect in every aspect of its implementation, but to ask the questions that will highlight the gaps that we need to address, recognizing that this is a journey of continuous learning and self-development that happens to also provide great benefits to organizations and society.
THE AUTHOR
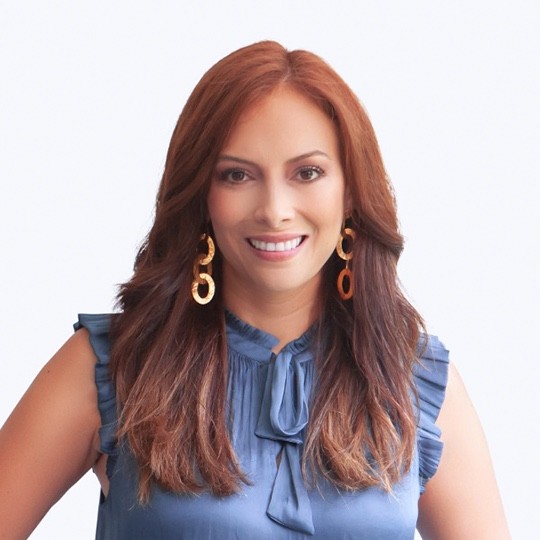
Read more
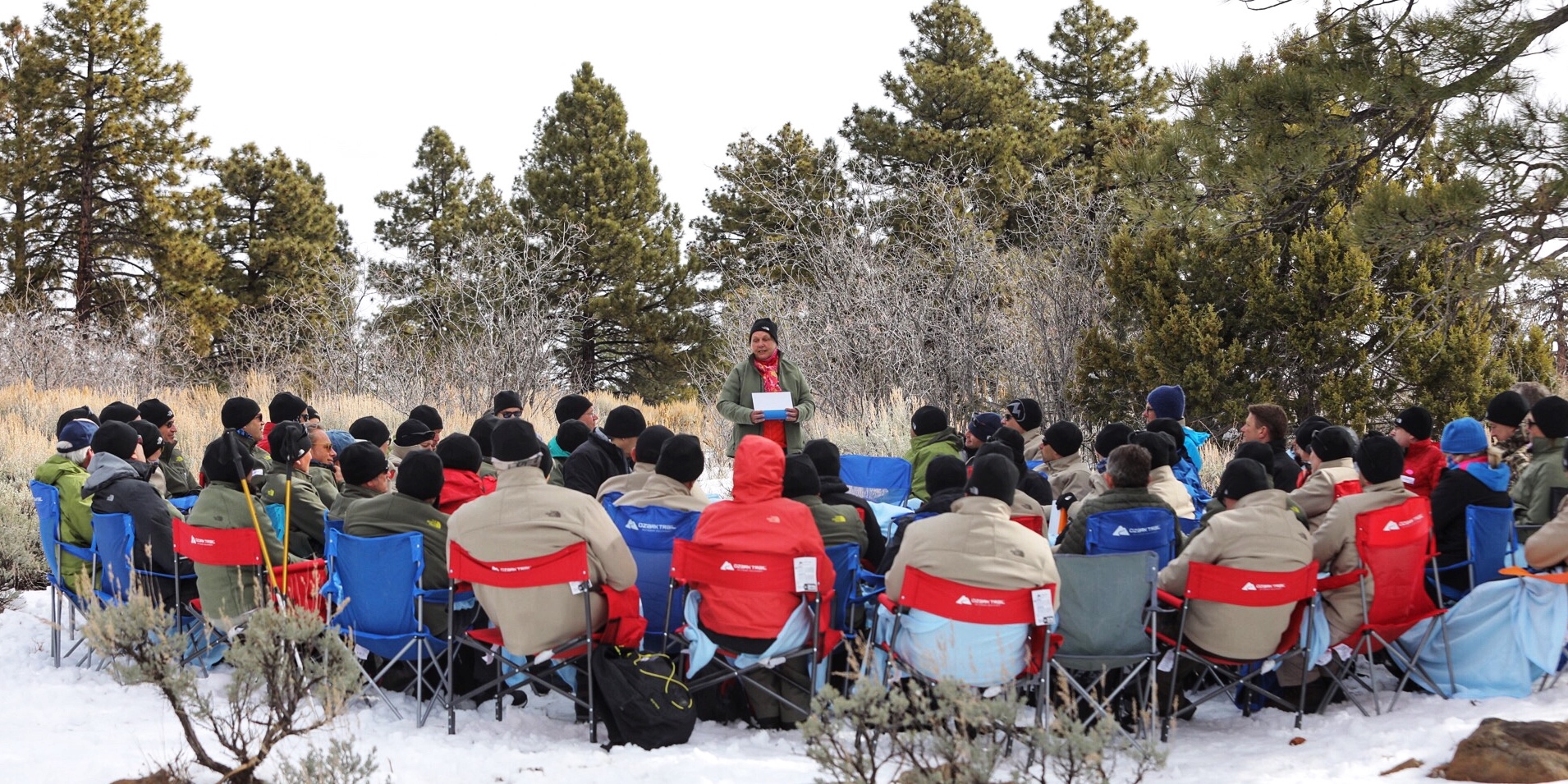
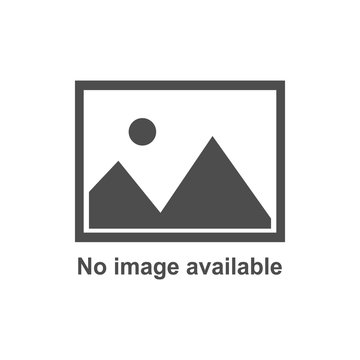
FEATURE – A few weeks ago, we learned how Philips is leading their lean transformation. In this follow-up article, the authors provide some great tips based on the company’s experience.
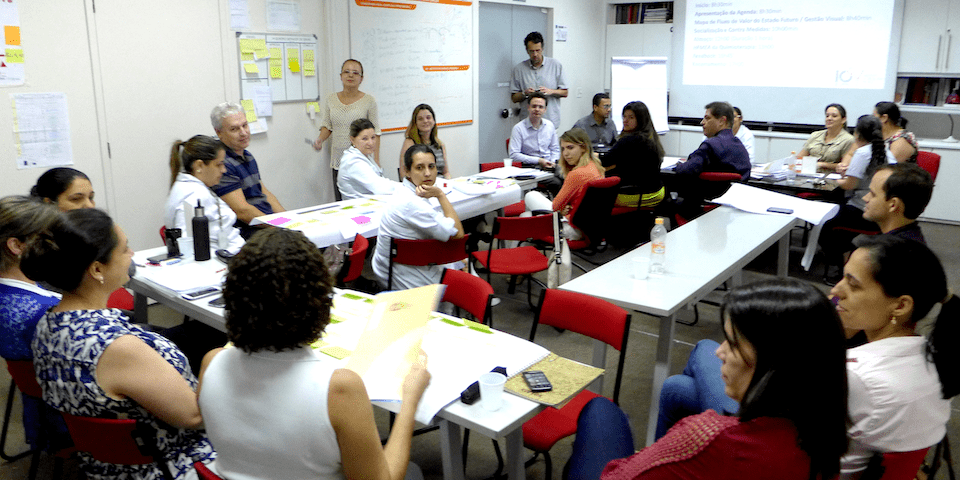
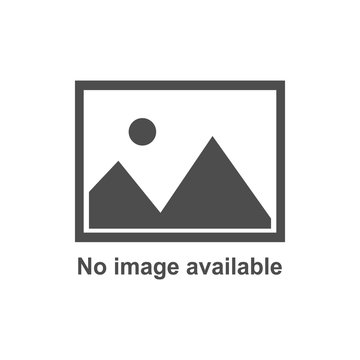
FEATURE – The power of cross-pollination: learning from a manufacturing company has helped a cancer treatment center in Brazil to thrive in its lean transformation.
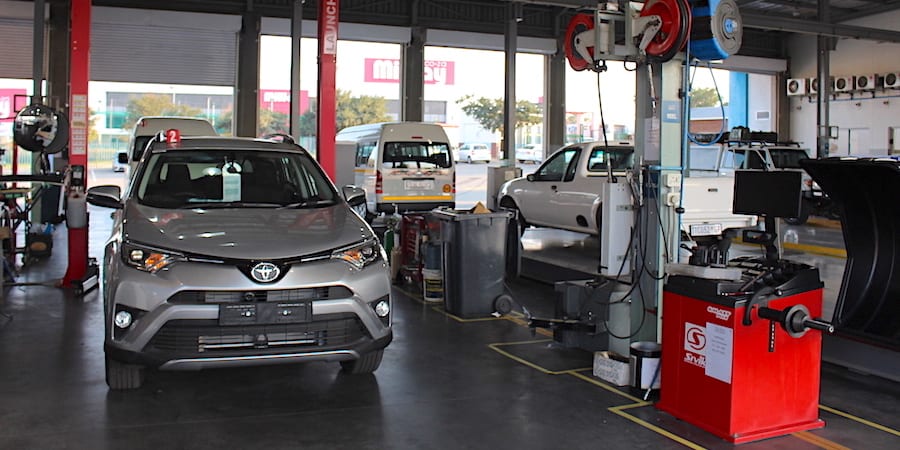
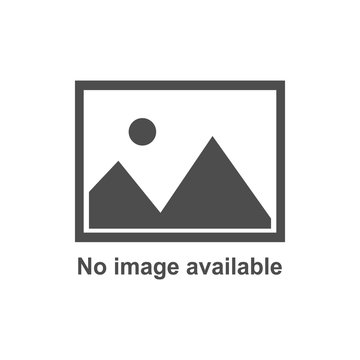
CASE STUDY – One-piece flow and a focus on lean leadership and kaizen have allowed the Halfway Production Centre in Johannesburg to turn itself around in just 14 months.
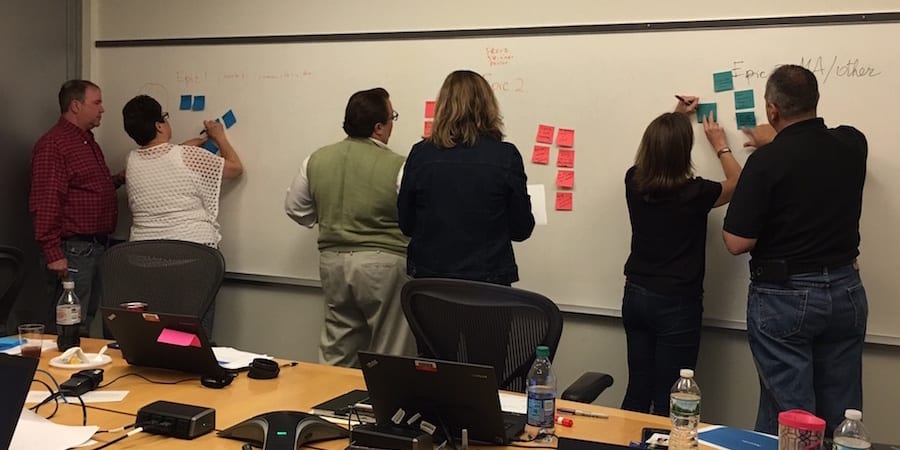
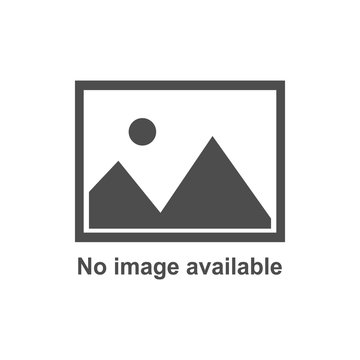
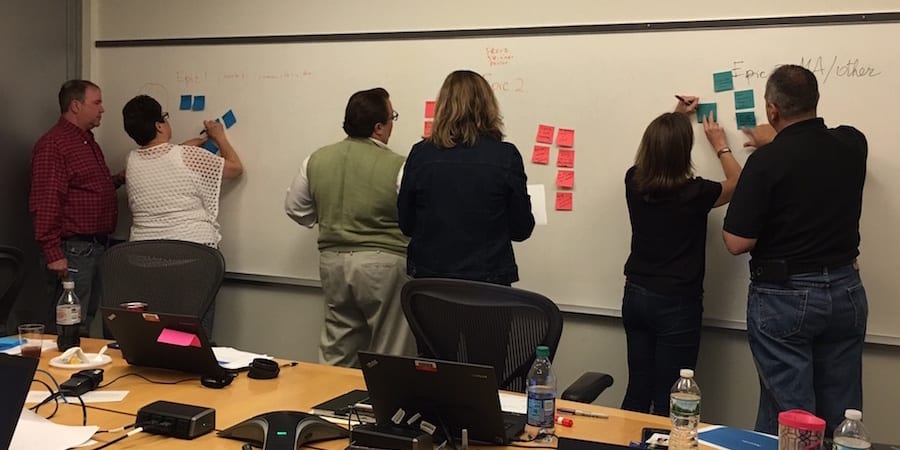
INTERVIEW – Business services company Dun & Bradstreet learned that the best way to tackle organizational challenges is using a combination of agile, lean startup and more traditional lean principles.