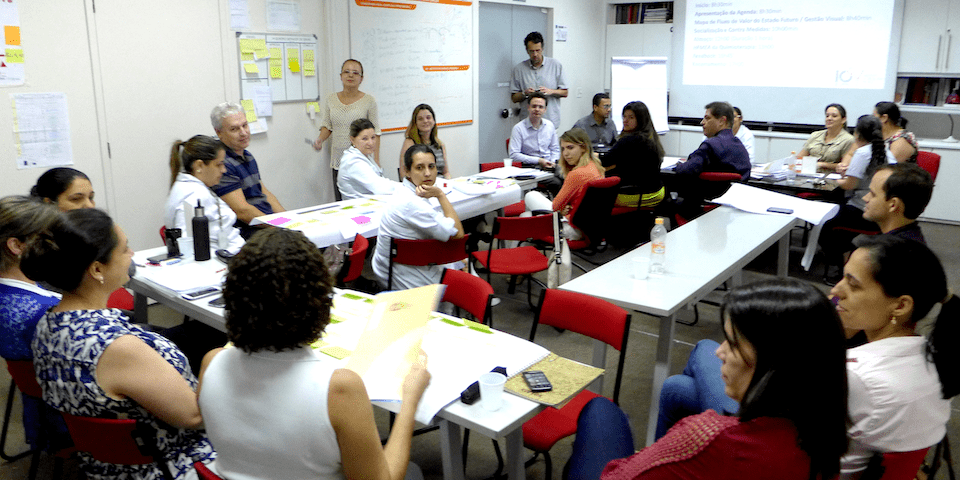
Lean learning happens across sectors too
CASE STUDY – The power of cross-pollination: learning from a manufacturing company has helped a cancer treatment center in Brazil to thrive in its lean transformation.
Words: Stela Maris Coelho, Lean Office Manager, and Carlos Frederico Pinto, CEO, Instituto de Oncologia do Vale - Brazil
At oncology group IOV (Instituto de Oncologia do Vale), we have been working with other organizations since our lean journey started in 2008. We have always been very open to learning from others and sharing our learnings with them.
We have been supported on our journey by Lean Institute Brazil as well as other lean companies. For example, Parker Hannifin, the manufacturer of motion and control systems and technologies, has shared its knowledge and time with us on many occasions. It is the relationship with Parker Hannifin that I would like to discuss in this short article.
In 2013, as we worked hard to develop our lean management system, we received monthly visits from organizations interested in learning about lean and willing to share their experience. Parker was one of the organizations that asked for a visit.
On that occasion, we had the chance to meet the Parker Business System Manager for LATAM, Marcelo Lopes, and the LATAM Controller, Tadeu Nunes. There was great chemistry from the very beginning. They liked what they saw at IOV and we were thrilled to have access to their expertise. From that day onwards, our two organizations began an informal partnership, with several teams from IOV visiting Parker and vice versa.
Ours was an open-door policy. We supported each other as we ran kaizen weeks, delivered training sessions, and experimented with daily management practices. We couldn’t be more grateful for the help we have gotten from them. We know we still have a lot to be introduced to in their best lean plant worldwide (luckily, it is located just 20 minutes away from our headquarters).
WHAT WE LEARNED
If I had to summarize what we have learned from Parker over the years in one word, that word would have to “method”. After several visits to their facility, we were able to implement TPM (Total Productive Maintenance), OEE (Overall Equipment Effectiveness), Kamishibai, a Versatility Matrix, Milk Runs and visual production management. We also improved our 5S instruction methods and gemba visits.
- Total Productive Maintenance
When it comes to TPM, we have learned loads from Parker. For example, we have realized that each machine needs an owner, responsible for its operation during working hours. After seeing TPM in action at Parker, we implemented a visual maintenance schedule, increased our focus on preventive maintenance to reduce interruptions in the process, and began to monitor the parts that need frequent changes using a Kanban system and to better manager those being maintained.
- Overall Equipment Effectiveness
Part of the TPM approach, OEE quickly became a game changer for IOV after we began to use it in our radiotherapy service. It allows us to check how well we are using the available resources of machines, manpower and materials in our “production” function. Back in 2013, we had three Radiotherapy facilities with five Clinical Linear Accelerators (CLINACs), which had a history of stopping machines and overtime. Our initial average OEE score was 40%! By reorganizing the engineering team, redesigning the maintenance flow, creating standards for maintaining and manning equipment and introducing daily Maintenance and Engineering meetings, our OEE score went up to an average of 80%.

- Kamishibai
Another great introduction to our processes was the Kamishibai, a framework for visual control that allows us to perform daily audits in a simple way within a given process. Thanks to the kamishibai board, we now spend a mere two minutes a day auditing our standard work in most clinical areas. Gone are the days when we had to work extra hours to keep our documents updated. We also have safer processes, and is very easy to meet Accrediting Standards with these boards (we have three different quality certificates to abide to).

- Versatility Matrix
During a visit to IOV, a team from Parker suggested we develop a matrix to manage employees' capabilities, as we were having a hard time to understand who had what knowledge within and among our many teams. The Versatility Matrix makes this very easy, also helping us hugely when it comes to organizing training for our people.

- Milk runs
In one of the visits at Parker we saw a milk run in action. This is a practice that comes from the old days of dairy farming in the United States: empty gallons were left at the door of the supplying farms and full gallons were collected in their place, thus getting access to the raw material exactly when necessary. We applied the same thinking to medical records, because we had chemotherapy and radiation therapy patients being treated at the same time in the same, long corridor of one of our facilities. It was a long walk for our people each time they had to fetch a record. So, we created a visual management for medical records, introduced a Kanban system, and organized a milk run on the established routes every two hours, leaving the medical records for the treatment or appointments according to schedule.

- Visual management
We drew inspiration from Parker’s Visual Production Management (the hourly production pace set by a visual document at the operators' stations) to develop our Chemotherapy Schedule Management. This entailed embedding a framework to identify our daily workload and performance into our electronic medical record.

CROSS-POLLINATION, A DRIVER OF LEAN LEARNING
Time and time again, Parker Hannifin supported us by sending in their experts to participate in our kaizen events. Many of the improvements to our practice at IOV were introduced with the guidance and support of their people – from workload balance to bottleneck management, cell-like workstations to flow improvement.
At the beginning of our lean journey, we struggled to understand how to translate tools and associated activities that had been developed for manufacturing equipment and production lines to our clinical practices. Several of the tools and techniques we observed at Parker ended up being adapted for IOV. The kamishibai is a great example: when we started using it (“Wow! This may be useful, let’s try it”), the cards were merely for audits. In time, we realized how to best deploy them and we were able to connect them to a planned auditing process and our TWI (Training Within Industry) training methods. Nowadays, kamishibai cards refer to our clinical best practice, standard work, training materials, the versatility matrix and human resources department annual performance evaluation, helping us to manage how we learn and evolve as an organization.
The opportunity to see tools and practices at work in other organizations and understand the meaning of that practice was crucial to our journey, but it certainly took time. Our learning curve was steep at first, but our persistence paid off. Learning to make the most of Parker’s experience and ensuring their “solutions” became ours was our focus as we tried to progress on our lean transformation. There is no doubt these exchanges have been one of the great catalysts of IOV’s lean transformation. Had we done it all by ourselves, it would have taken us a lot more time to understand how to use and leverage and integrate those lean tools. Parker’s experience helped us to connect the dots as we tackled our real-world challenges.
Sharing between different organizations cultures and industries is an incredible valuable activity, especially in healthcare, where management is often reluctant to consider a lean journey a serious undertaking. Parker is a large and mature lean enterprise, and their humble support allowed us to make great leaps. Without them, our lean journey today would be much harder.
For more stories on IOV, click here.
THE AUTHORS


Read more
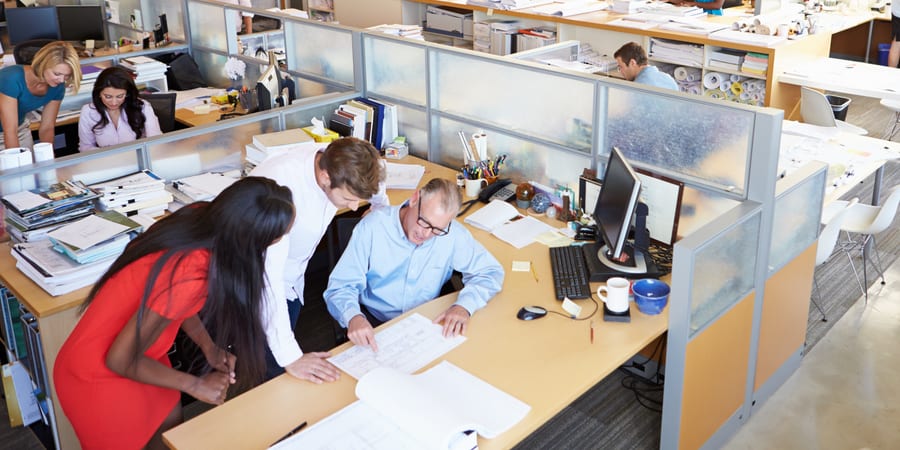
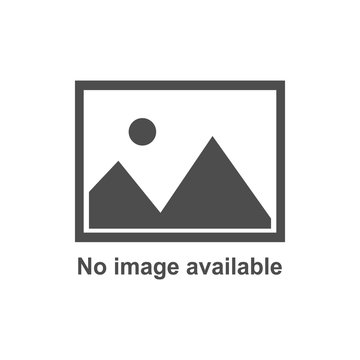
VIDEO – We constantly talk about the role of leadership, but perhaps we don't realize just how intertwined leadership transformation and business transformation really are. This short video discusses why.
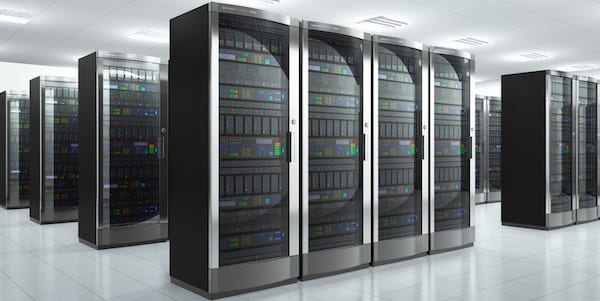
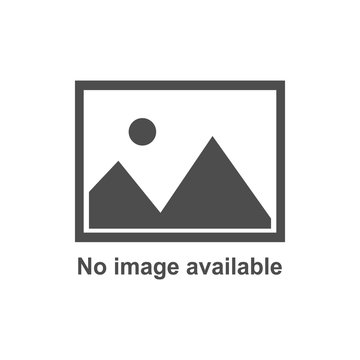
FEATURE - London-based startup Elastera may represent the example of a company aspiring to be lean from the outset rather than trying to fix itself later through a transformation.

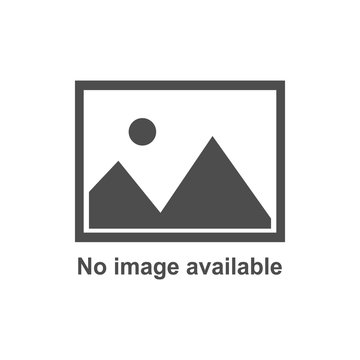
ROUND-UP – Looking back at the year that just ended, our editor Roberto Priolo reflects on the power and reach of lean thinking, and offers us a round-up of the best content from 2017.

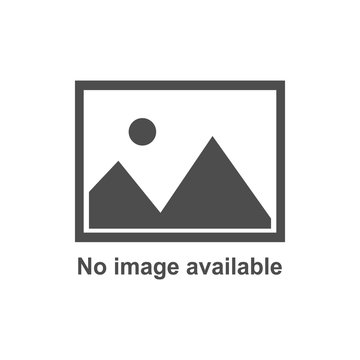
FEATURE – Taiwan-based Machan International Co. manufactures sheet metal products, tool storage and medical trolleys, and smart energy storage cabinets. Last year, they turned to lean to improve their product development process.