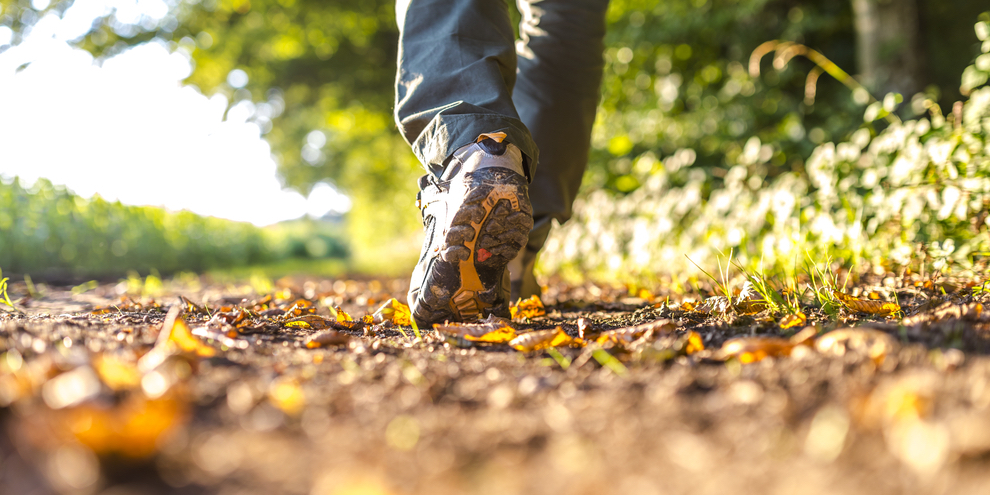
It’s the pebble in our shoe that wears us down
FEATURE – We assume that what holds our transformations back is the lack of high-price resources, but more often than not it is the simplest of items.
Words: Sharon Visser
As a runner, you can have the best track, the best coach and the most expensive pair of running shoes, but if you have a pebble in your shoe it is unlikely that you will win the race. At best, you will struggle to maintain focus during the race; at worst, you will develop a blister.
When I coach people, I constantly hear them say that they will be to start their lean transformation as soon as they get a new piece of equipment, a bigger building, or a new management software. Yet, it is rarely the high-price items that slow down our momentum. Often, it is the pebble in the shoe that hinders the progress of our transformation.
Let’s take just one of the most common hindrances I have come across in organizations I have worked in: the purchase of sundry items, things you need but can’t find in the stationery cupboard.
Say one has to get petty cash or a purchase order to buy a small item required to carry out an experiment or solve a problem – something like a spray bottle, a bigger broom, colored boards, duct tape, marking pens, or A3 paper.
Let’s look at the process for the simplest of purchases: when the organization has a purchasing account with the supplier. In most organizations, the person who needs the item will first have to get a quote (up to three quotes in some companies). The quote or quotes are then taken to the department manager who signs the agreed quote. This document is then taken to accounts so it can be allocated an expense code and signed as approved. An order is made up. The item then needs to be purchased, so a driver has to be found, to collect the item, or delivery has to be organized. The signed invoice or receipt is then returned to accounts to finalize the transaction.
Depending on where you are in the world and how cumbersome the system actually is, it will take a minimum of an hour to get this done. If all sourcing is done by a procurement department, one can extend this process to at least a day if not more. The bigger the organization, the greater the delay.
As I am writing this, I am wondering to myself how long it takes for someone working in Amazon to get an item through their own procurement system for an experiment. (If anyone knows, please tell me!)
Let me give a little example of the impact the procurement of small items can have.
A couple of weeks ago, I went for my first Covid vaccination here in Botswana. I arrived at opening time and there was already a long line of people waiting. When I eventually got into the building, I watched the process with great interest. There were three stages, showing some single lane flow. I was impressed. The chairs were all set out at the standard two-meter intervals. However, there was not a sign in site and everyone coming in was reliant on the nurse looking up, in the moments in between patients, and tell them what to do next. Bolder and less considerate people pushed their way to the front ignoring the elderly and disabled until the nurse broke her flow to intervene.
When my turn came, I asked her if I could come and help her in the morning before everyone arrived. I would bring tape and signs. She was surprised, but grateful for the help.
I could have handled this differently by telling her what would help her control the crowd, but I already knew she would hit a major obstacle that would prevent her progress. She would have had to go through the process of justifying the need of floor tape and signage with senior Government administration staff. If they agreed to her plan, she would then have had to go through the complex procurement system that is designed by Government to prevent shrinkage.
So, I printed out some signs and arrows on cards and laminated them and packed up some tape and scissors. Within an hour of arrival, we had a designated a disabled area right next to first stage. Arrows showed people to move to the empty seat to the right of them. We designated a waiting area for after vaccination and created a flip over sign to put up when the space had reached capacity, telling people that when one person comes out the next person in line can go in.
When we had completed this, I looked around me and found that the other nurse was sweeping the vast floor space with an ordinary household broom that was very worn. To clean the floor was going to take her at least an hour. Without her at her station, however, the process of inoculation could not start.
To get a new industrial broom, she would have had to have gone through the same cumbersome process as her colleagues.
So one full hour of vaccination time was going to be spent cleaning. With the average time per station being 7 minutes, that means that during that one-hour period 8 extra people could be vaccinated. That is an additional 40 people a week, 160 per month, or 1,920 per year.
I bigger broom would have helped, but a cleaner coming in for an hour a day would have been of great assistance allowing the nurses to get on with the task at hand.
We could talk about improving the takt time by removing waste at the stations, but as I was giving unsolicited assistance this would have become a problem.
All the workers were busy doing their jobs to the best of their ability. Nurses, administration staff, procurement officers, all trying their best to meet the demands of their positions. They are the “willing workers” that Deming talked about.
Like the willing workers, I have no power to make a change in the vast machinery of Government, but I did what I could to remove a pebble in a shoe hoping that it might give someone a better day at work.
When I went for my second dose, the facility was no longer open. Upon asking, it seems that they finished their allocated vaccines so early in the day that it was considered wasteful to keep that facility open. As a result, everything was moved up to the main hospital.
It was a strong reminder to me that we don’t all see waste in the same way and that there is still much work to do to help people to measure to understand.
Sharon's unique book - Lean Houses for Dragons - is available now.
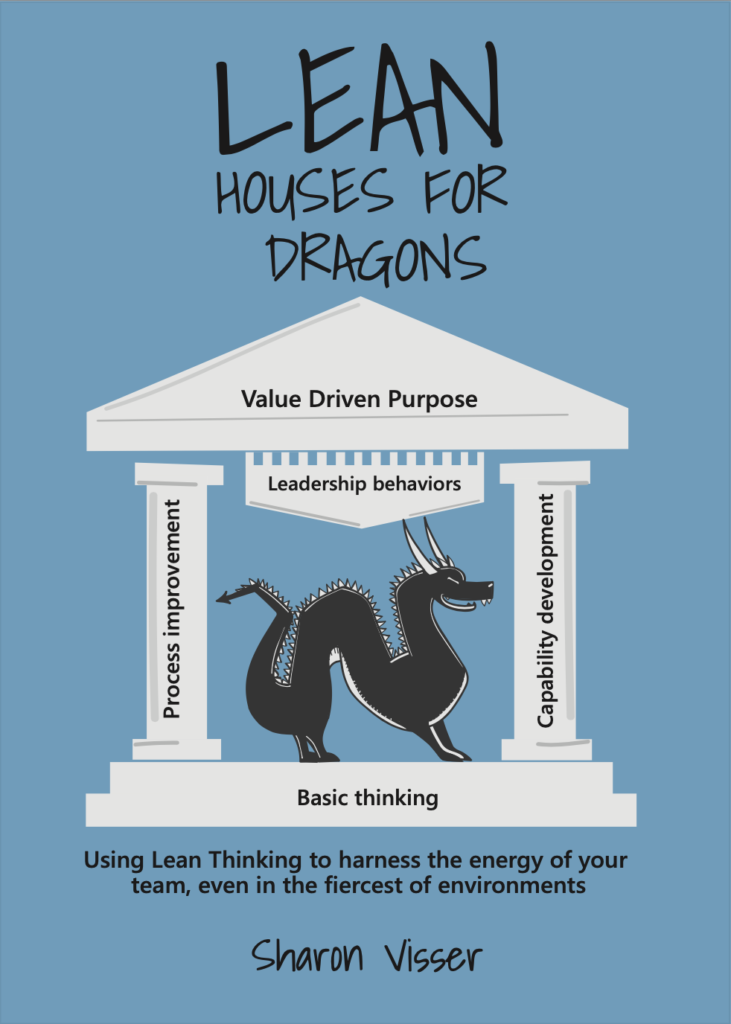
THE AUTHOR
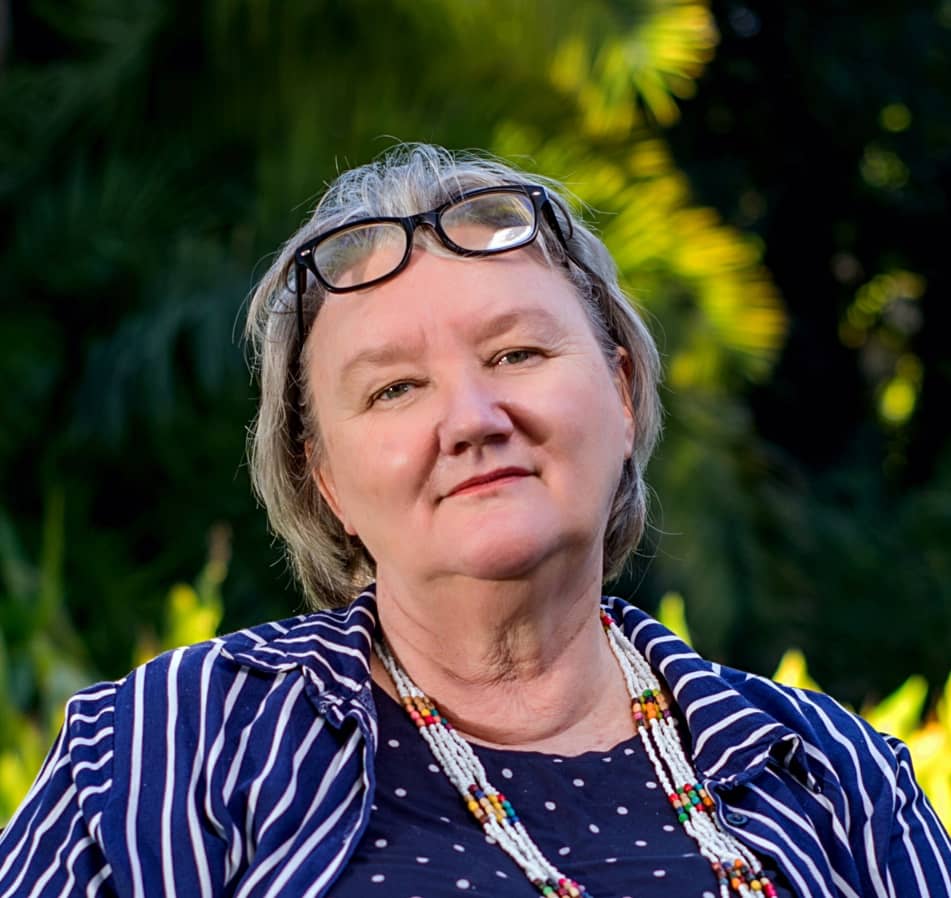
Read more
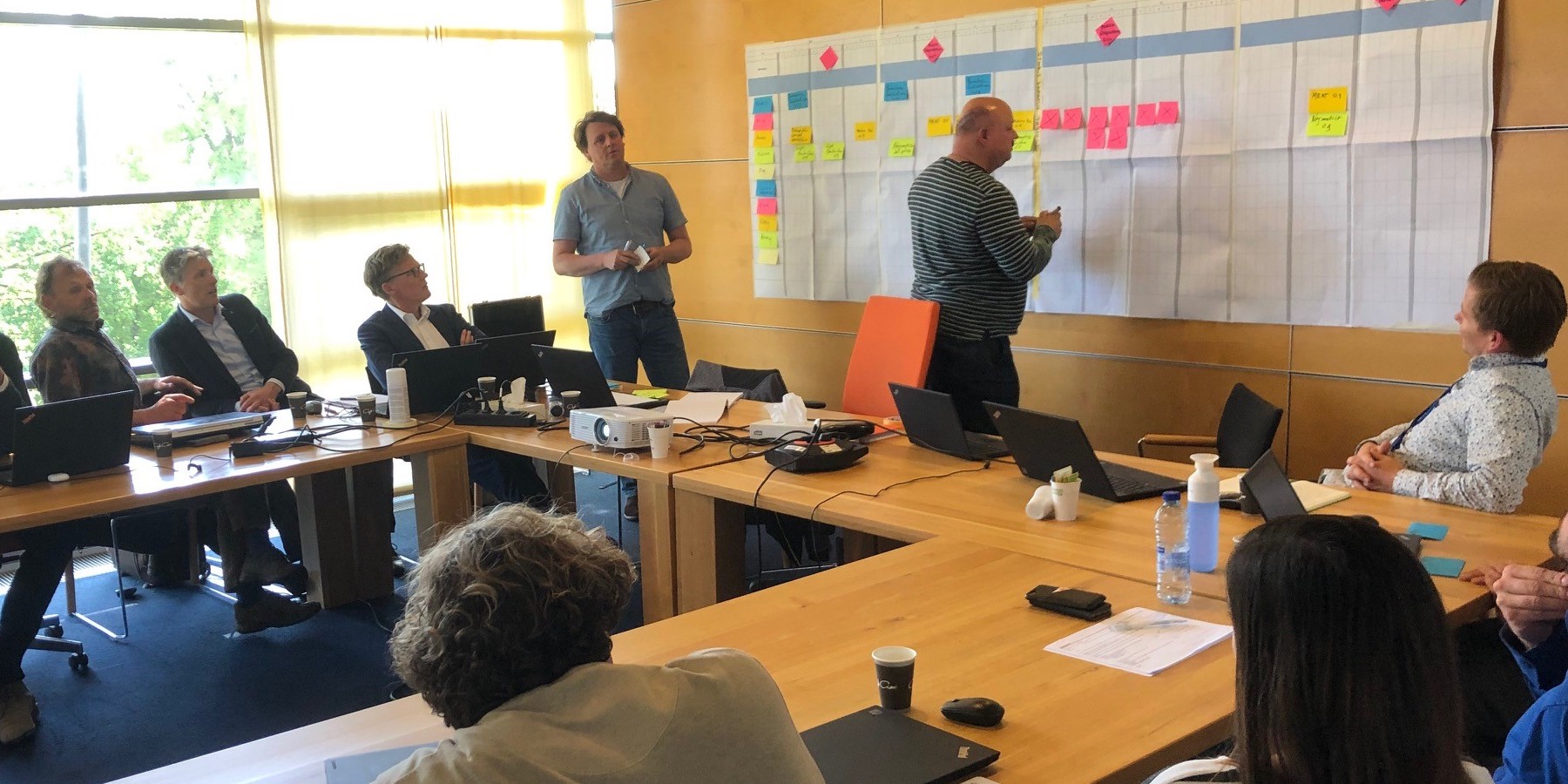
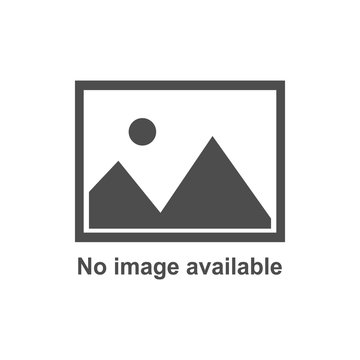
FEATURE – A Dutch transmission system operator is using Lean Planning – built around the Last Planner System – to better manage its complex infrastructure projects.
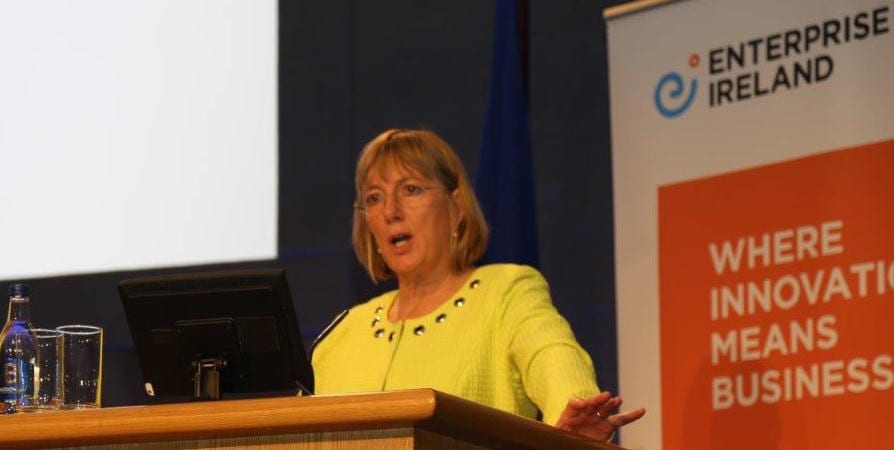
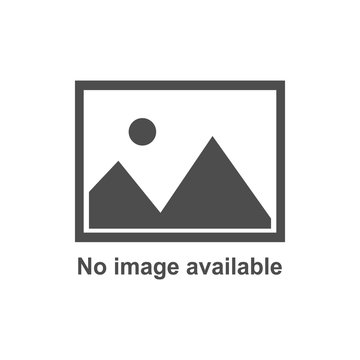
RESEARCH – This insightful paper explains how the Irish government is encouraging organizations to adopt lean thinking to improve their competitiveness with the Lean Business Offer.
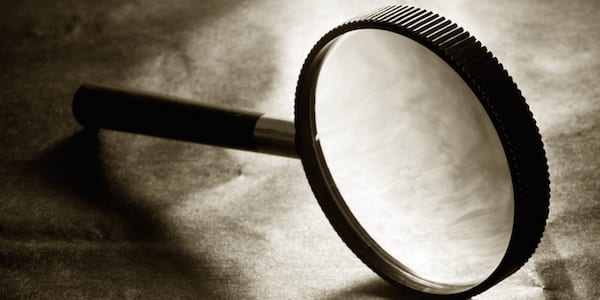
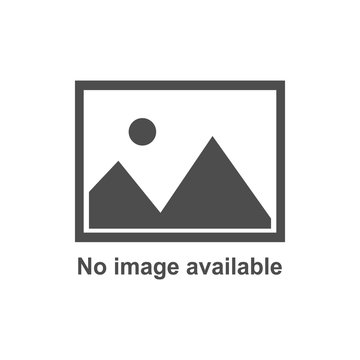
FEATURE – Until “check” and “act” become a natural part of daily work, we will always need formal audits to keep people focused and to sustain results. Here’s a few tips to make them work.
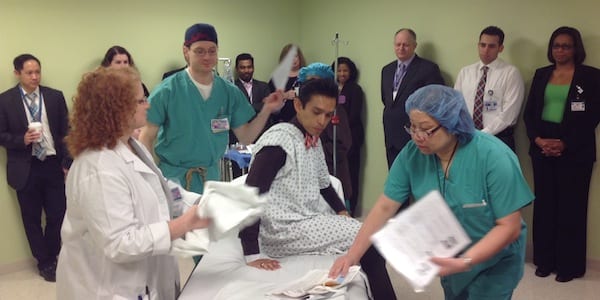
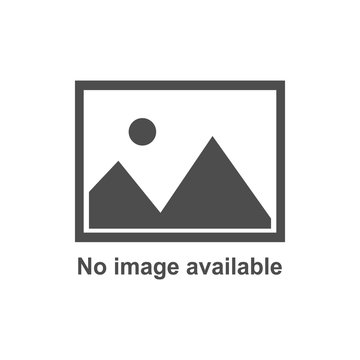
INTERVIEW - New York City's public hospitals system leveraged lean principles and techniques to improve the quality of care and boost organizational performance.