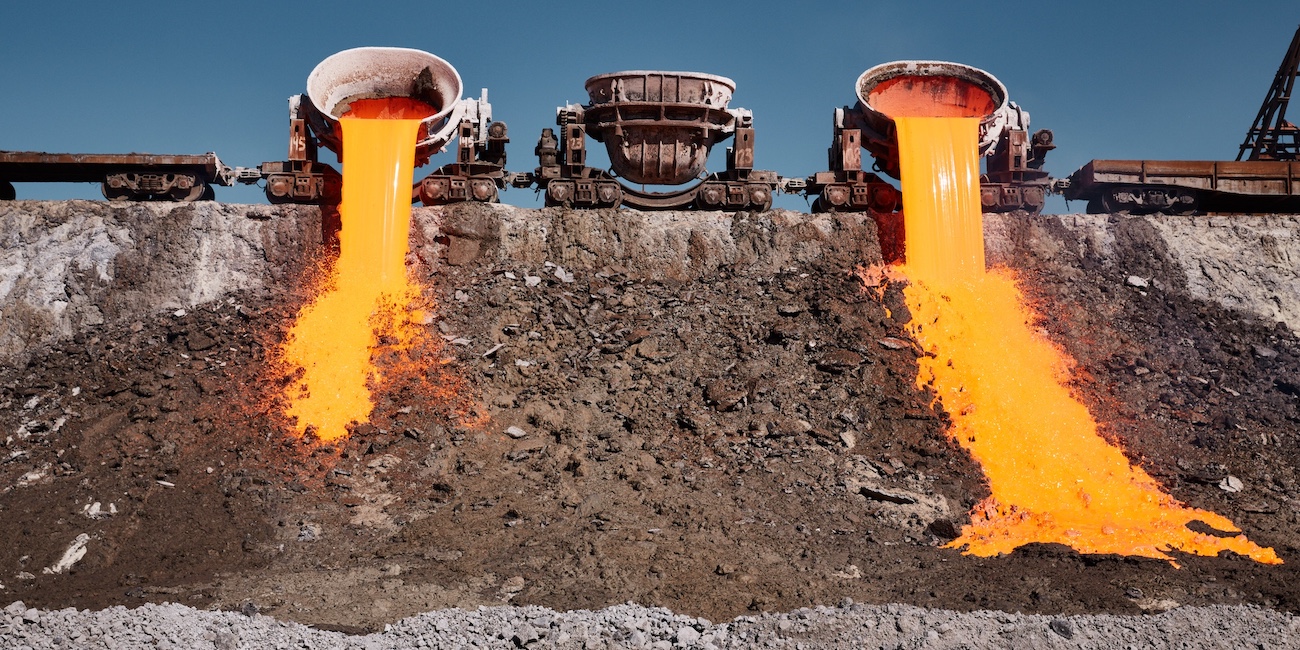
Igniting efficiency
CASE STUDY – This nickel smelting operation in Indonesia used the Lean Transformation Framework to optimize furnace inspections and minimize delays.
Words: Teuku Mirwan, Dhonny Suwazan and Fikran Sahid
In the fast-paced world of nickel smelting, where every second counts, maintaining smooth, uninterrupted operations is essential for efficiency and cost-effectiveness. The smelting process, which involves transforming raw materials into refined nickel through intense heat and chemical reactions, requires furnaces to run continuously with minimal disruptions. Any unexpected delay or shutdown can cause production losses, leading to significant financial costs and operational inefficiencies.
However, furnace inspection procedures, while crucial for detecting and preventing issues, often require temporary shutdowns, which slow production. Traditionally, these inspections take 30 to 40 minutes, during which operations halt, impacting output and increasing costs. While these checks are necessary for safety and quality control, there is a pressing need to optimize them without compromising effectiveness.
To address this challenge, a cross-functional team applied the Lean Transformation Framework, focusing on reducing delays caused by inefficient inspection processes. By eliminating waste, improving workflows, and streamlining procedures, the team has significantly reduced inspection time and minimized furnace downtime, leading to improved productivity and a more resilient operation.
Let’s look at this lean-driven change as outlined by the framework’s five questions.
1. What problem are we trying to solve?
Reducing delays in nickel smelting operations requires a structured approach to improving inspection efficiency and minimizing downtime. Nickel smelting is a continuous and high-temperature process where calcine (nickel ore concentrate) is heated to separate impurities. This process forms slag (waste material) while leaving behind nickel-rich matte, which is further refined.
Because furnaces must operate non-stop, any undetected issue can escalate into a major breakdown, leading to an emergency shutdown and production losses. Regular inspections help detect potential failures early, preventing costly disruptions. However, traditional inspection methods are time-consuming, requiring operators to pause production for extended periods.
On average, each inspection lasts around 34 minutes, which, when multiplied across multiple shifts and furnaces, results in significant lost productivity. The goal is to optimize this process and reduce the total inspection time to 20 minutes, ensuring early issue detection while minimizing operational downtime.
2. What is the work and how do we improve it?
To enhance efficiency, a time-motion study was conducted using a Ka-Te-U chart, a tool used to analyze work processes. This study categorized tasks into three groups:
- Value-added activities (essential tasks that directly contribute to the inspection process)
- Non-value-added activities (unnecessary steps that add no real benefit)
- Conveyance (time spent on movement and transitioning between tasks)
The study highlighted several opportunities for optimization, leading to the implementation of ERACS (Eliminate, Reduce, Automate, Combine, Simplify) principles:
- Removing redundant steps in the inspection workflow
- Combining similar tasks to reduce repetition
- Performing multiple processes simultaneously to enhance productivity
One of the most effective strategies was distributing roles across different floor levels. By allowing parallel processing, team members could complete multiple tasks at once, reducing overall inspection time. Additionally, ensuring critical spare parts, such as rod bars, are readily available eliminated delays caused by waiting for replacements.
3. How do we develop our capabilities?
A standardized work inspection guide was created to establish a clear, step-by-step process for each team member. This guide includes clearly-defined roles and responsibilities, equipment checklists for pre-inspection verification, and photo documentation protocols to ensure consistency in reporting.
By implementing standardized work, inspection quality remains consistent, and the team can execute tasks more efficiently. Additionally, operators received specialized training on lean principles and inspection protocols. This training not only improved their technical skills but also reinforced a culture of continuous improvement, where employees actively seek ways to enhance processes.
4. What management system and leadership behaviors do we need?
To sustain improvements, a layered management system known as the “Onion Concept” was introduced. This system provides structured oversight, ensuring that inspection efficiency remains a priority at all organizational levels.
Key elements of this system included:
- Routine supervision from direct managers to ensure adherence to the new process
- Regular gemba walks, where leaders follow the principles of “Go See, Ask Why, and Show Respect” to identify process inefficiencies and problems
- Technical review meetings, where team members discuss challenges and propose solutions, fostering a culture of continuous improvement and accountability
5. What is our basic thinking?
The core mindset shift in this approach was moving from reactive maintenance to proactive maintenance. Instead of waiting for failures to occur, the new inspection process detects issues earlier, allowing teams to address potential problems before they cause major disruptions.
Key advantages of this new approach include:
- Faster inspections without compromising accuracy
- Early identification of furnace issues, preventing costly breakdowns
- Simultaneous execution of multiple tasks, improving overall efficiency
These improvements have transformed nickel smelting operations, making them not only faster and more reliable but also better equipped to handle challenges.
The future of furnace inspections
By applying the LTF, the team has unlocked a more efficient and streamlined way of managing nickel smelting operations. Through optimized work processes, targeted skill development, and proactive maintenance strategies, furnace delays were significantly reduced, ensuring that production runs at peak efficiency.
This approach also reinforced a commitment to continuous improvement, where teams are empowered to challenge inefficiencies and drive innovation. By eliminating waste and focusing on value-driven work, these enhancements have not only reduced operational delays but also strengthened the company’s ability to adapt quickly to future challenges.
Ultimately, these innovations ensure that nickel smelting operations are faster, safer, and more efficient, allowing the company to meet customer demands while maintaining a cost-effective and resilient production system.
THE AUTHORS
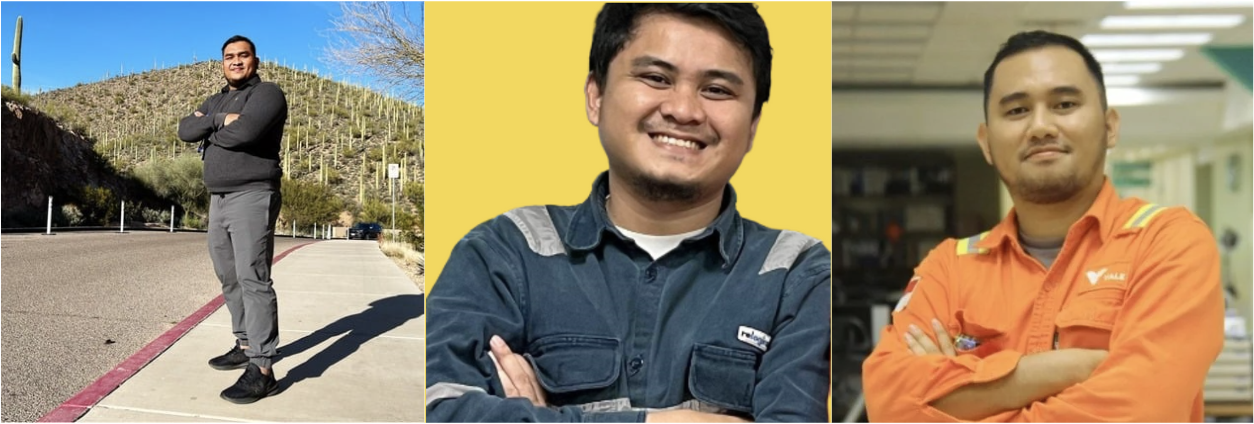
Read more
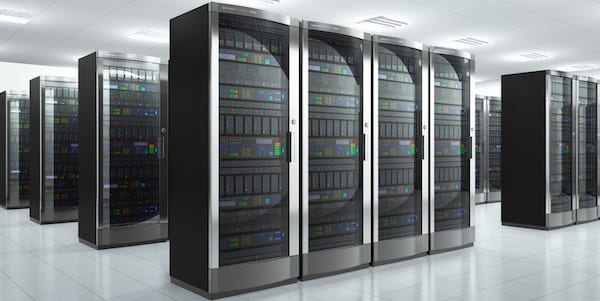
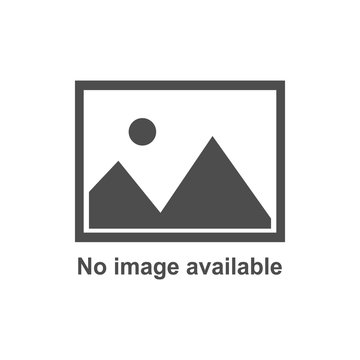
FEATURE - London-based startup Elastera may represent the example of a company aspiring to be lean from the outset rather than trying to fix itself later through a transformation.
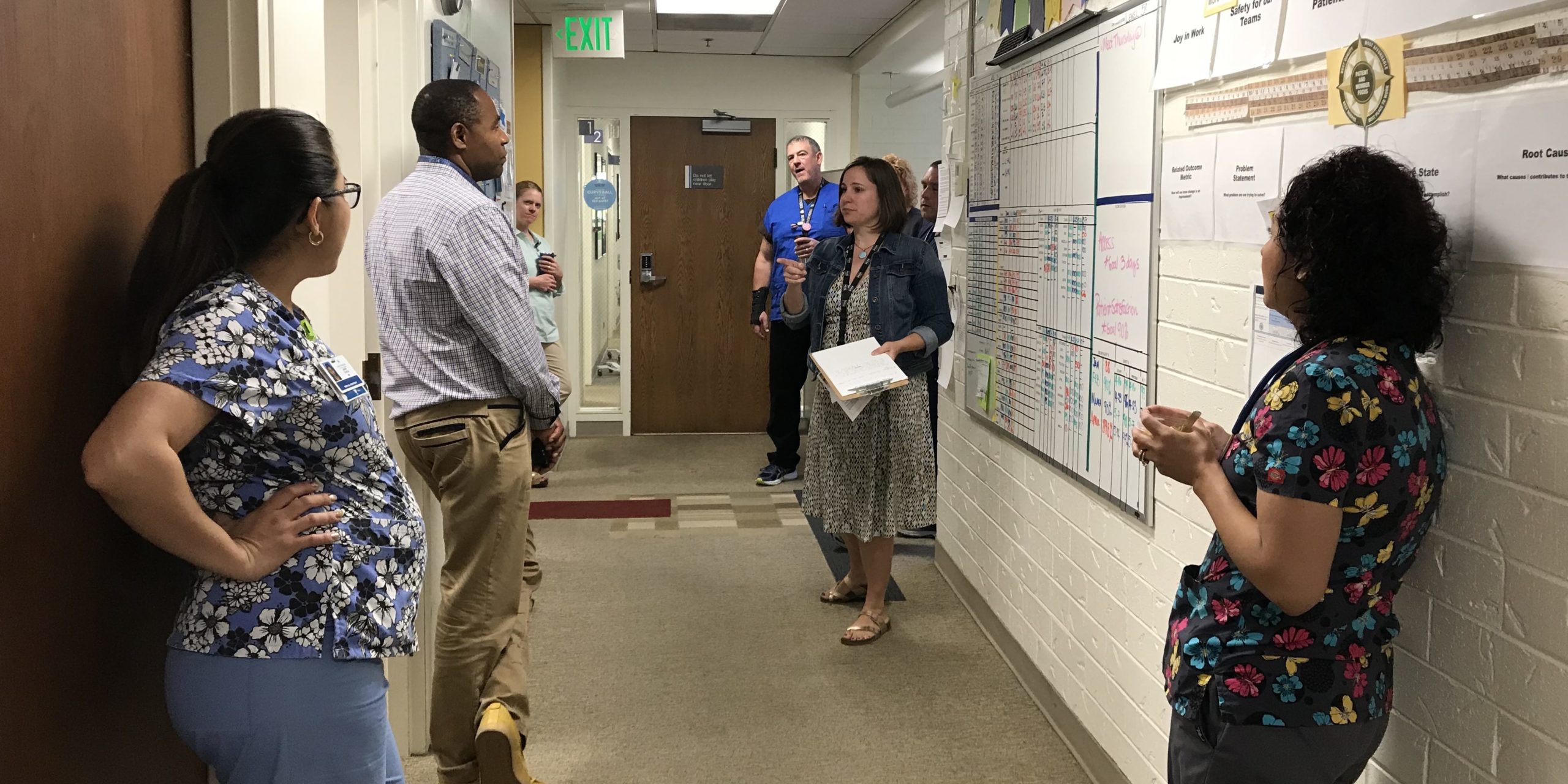
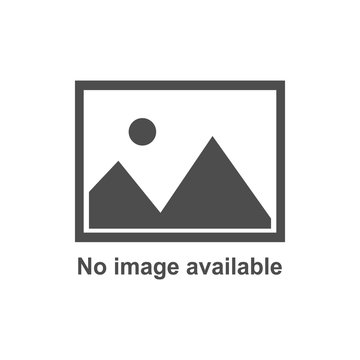
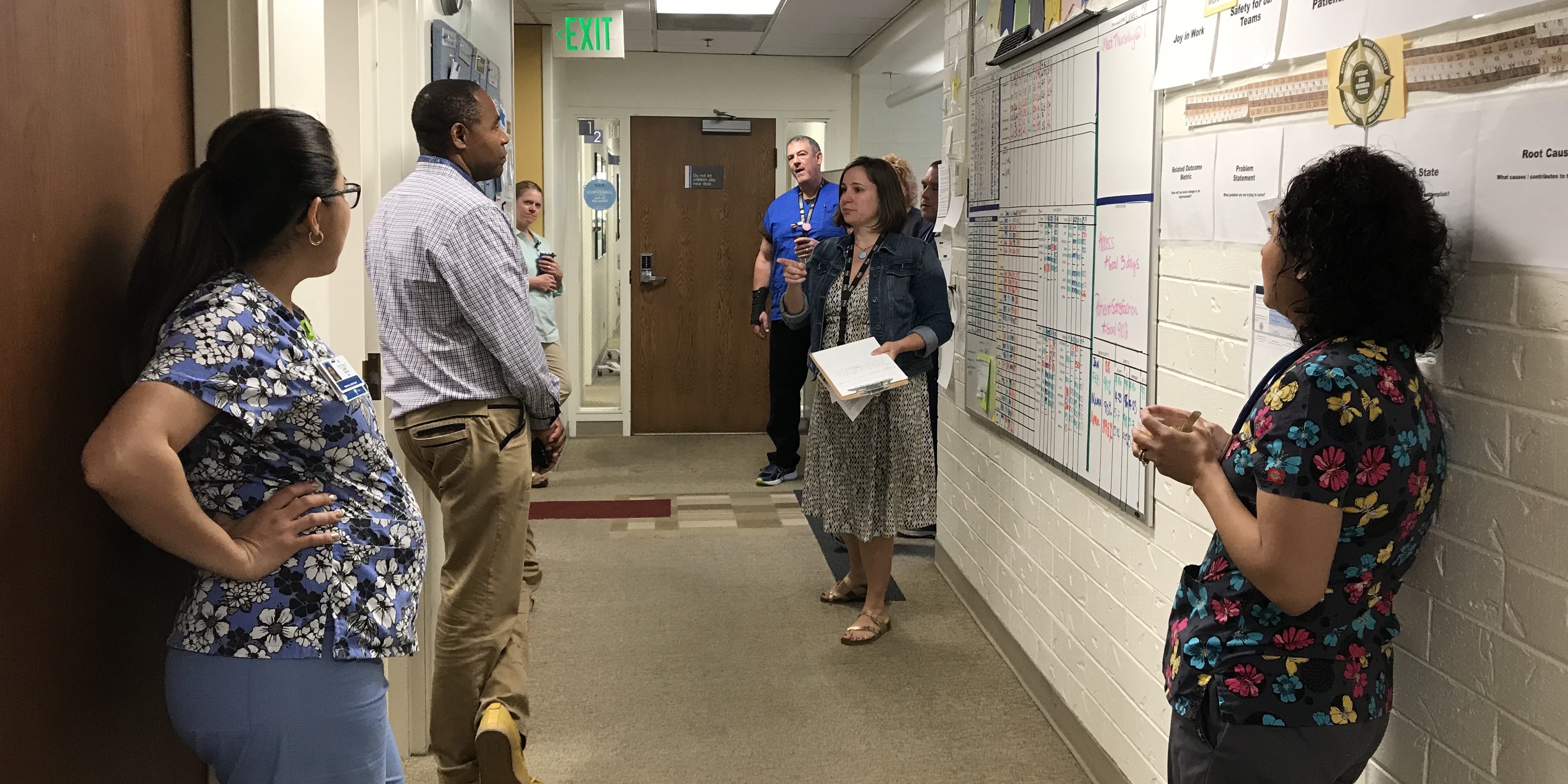
CASE STUDY – A physician tells PL the story of how the East Denver Medical Office became a catalyst for the lean transformation at Colorado Permanente Medical Group.
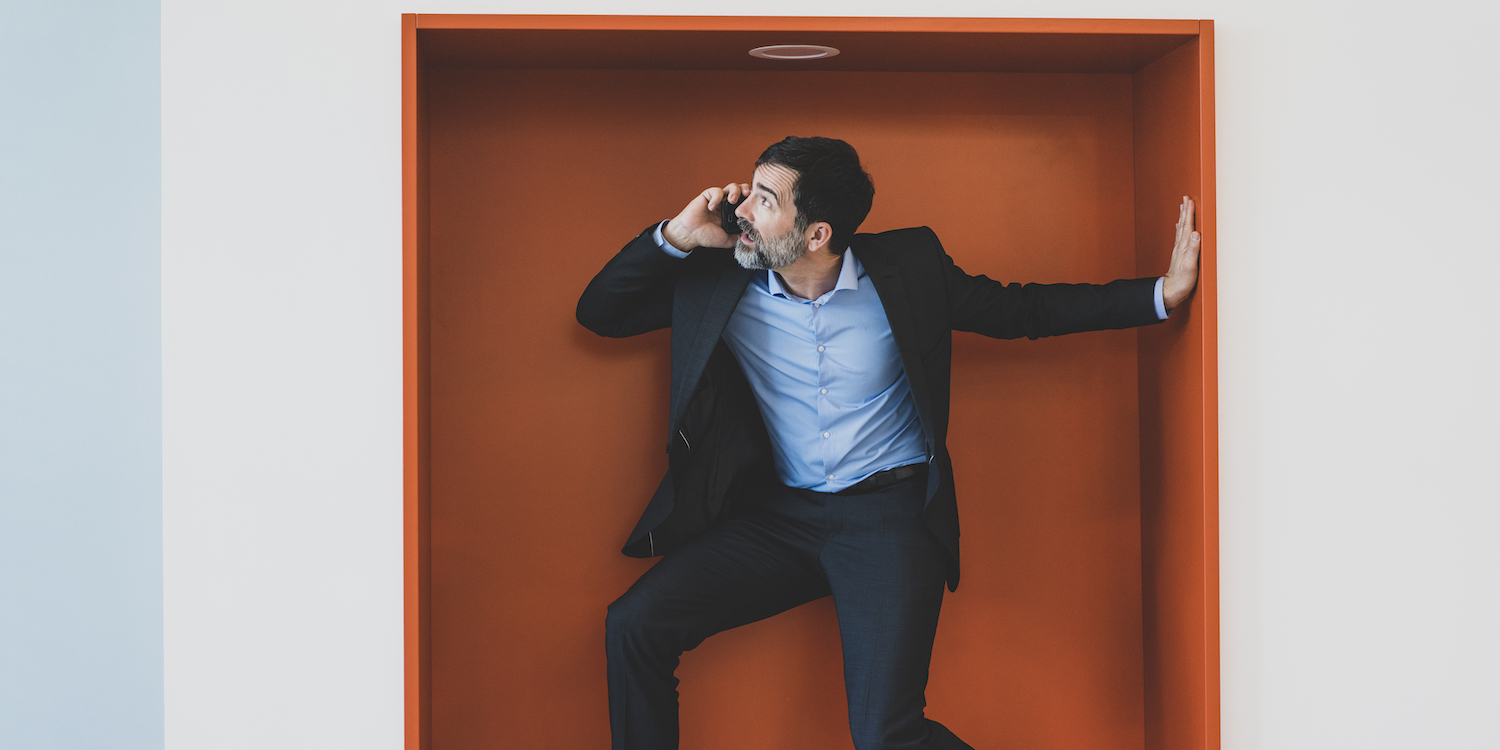
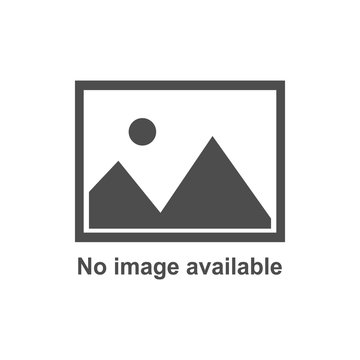
FEATURE – How does the improvement department of a company become a hindrance to the transformation? The author answers this question and discusses how this can be avoided.
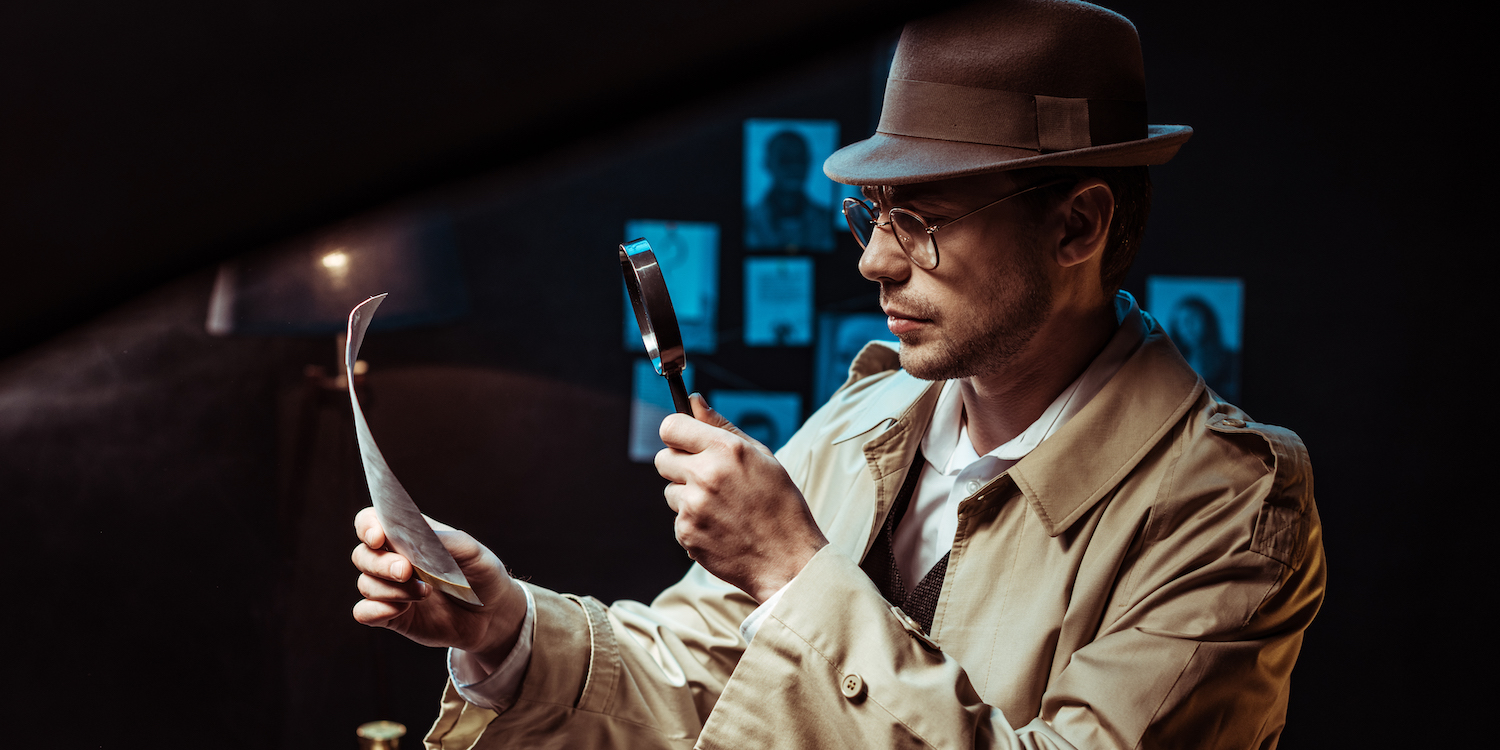
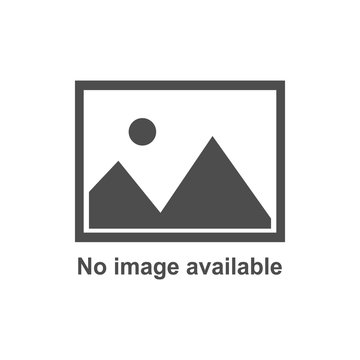
FEATURE – This insightful piece explores the true meaning of problem solving, looking at the common mistakes leaders make when they adopt some of its key practices.
Read more
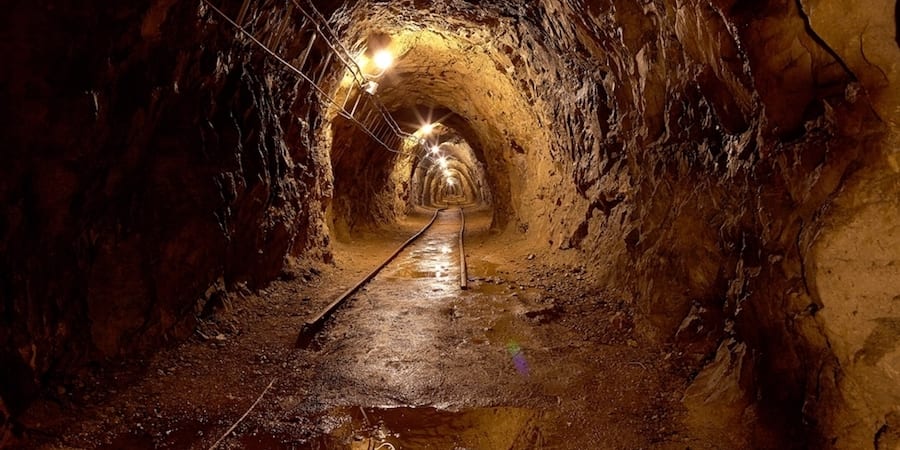
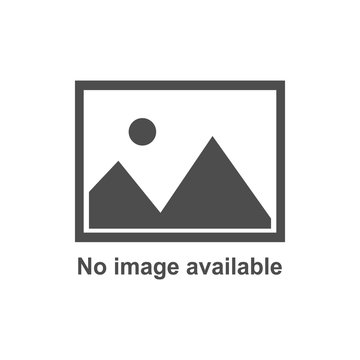
FEATURE – Lean thinking is still largely absent from the mining industry. The author explains the great opportunities that lie ahead for an industry with a huge potential to improve.
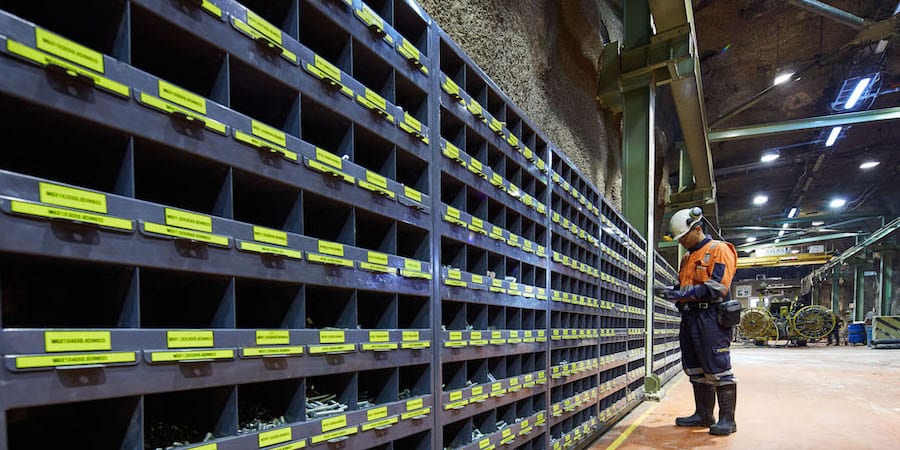
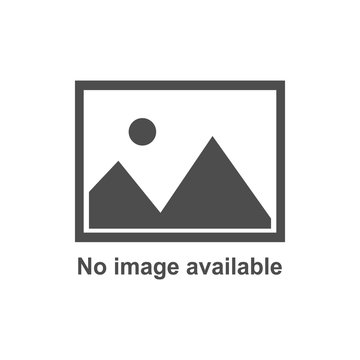
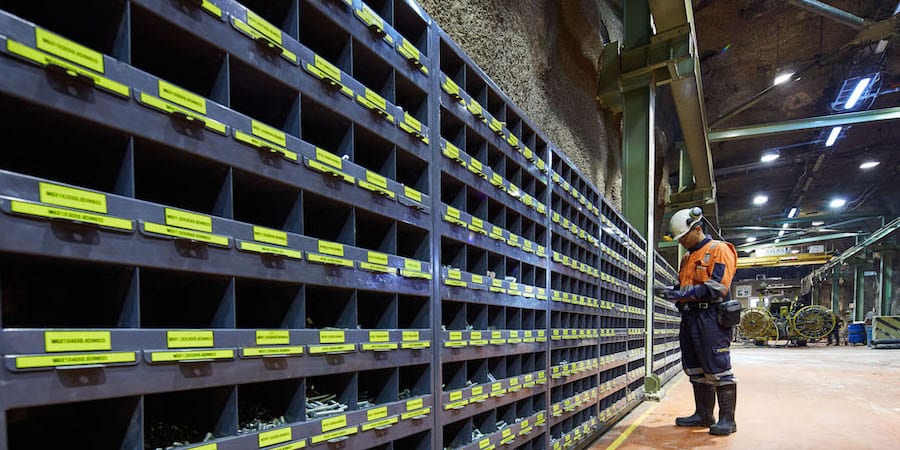
CASE STUDY – Over the past four years, by developing its kaizen capabilities and crafting a better approach to maintenance, a Turkish gold mine has significantly reduced its extraction costs.
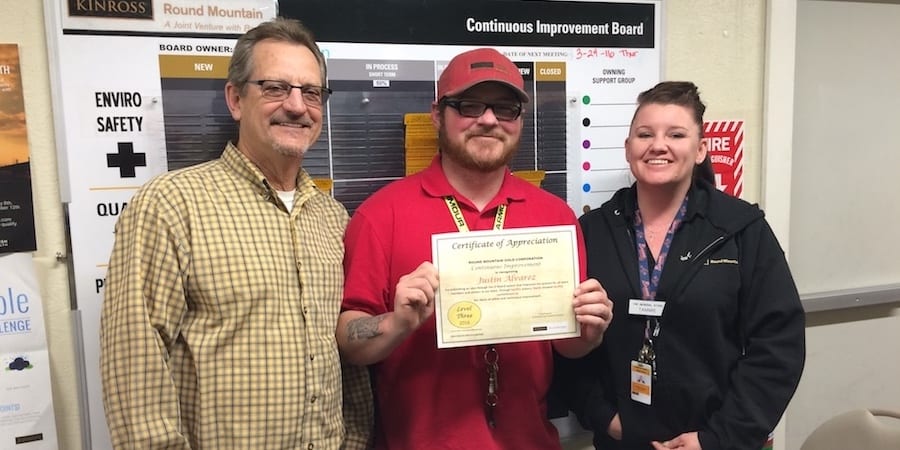
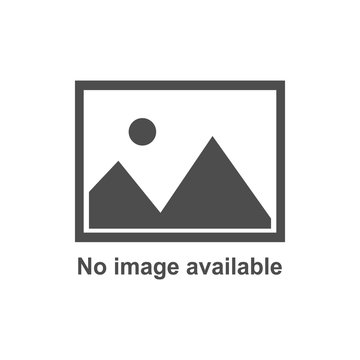
FEATURE – The Continuous Improvements Boards at the Round Mountain mining site have been critical to shifting the company's culture... the secret, it turns out, is always providing feedback on people's suggestions.

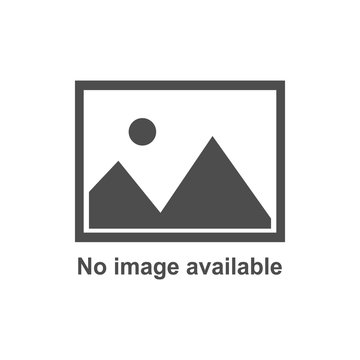
CASE STUDY – The extraordinary transformation of Kinross' Round Mountain gold mine in Nevada over the past six years shows that lean thinking can – quite literally – move mountains.