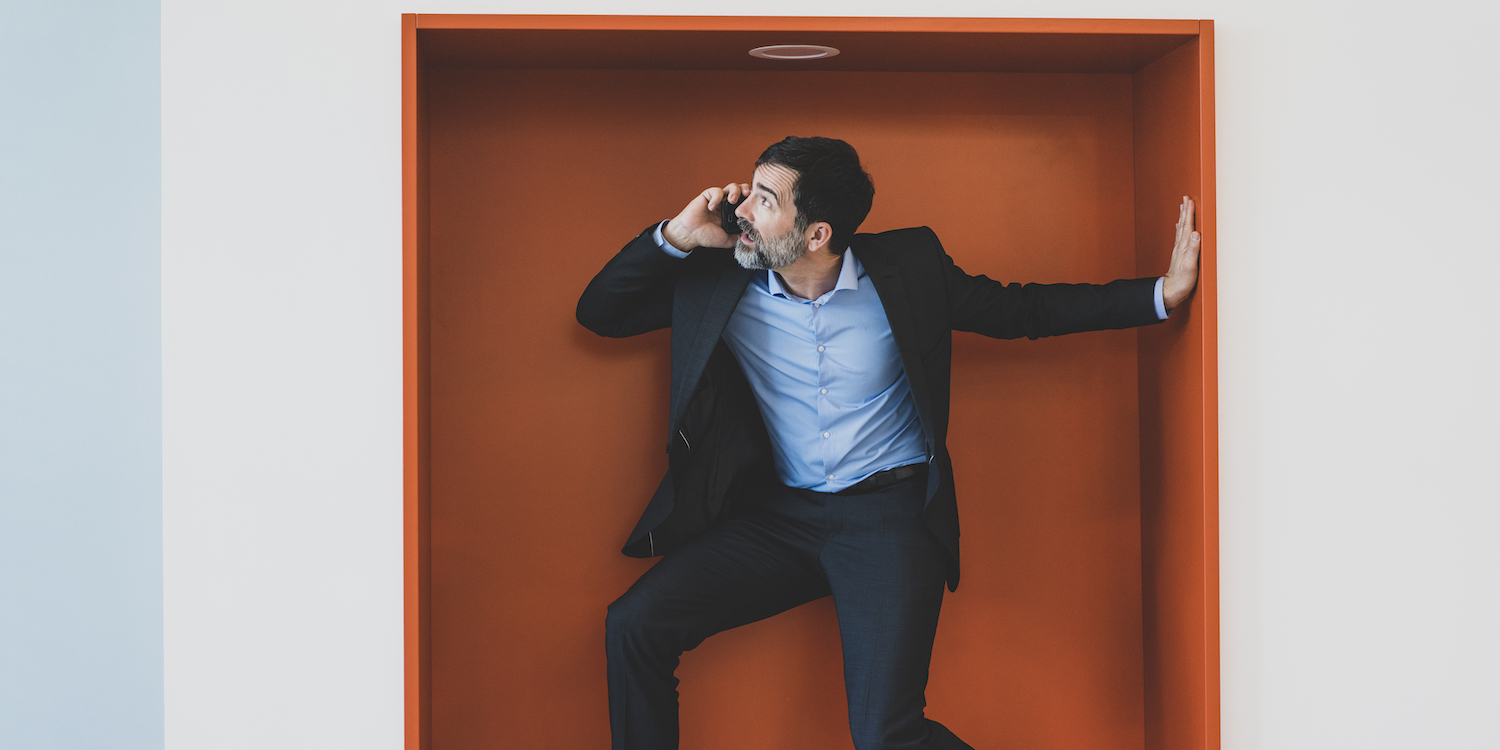
When the lean team is the problem
FEATURE – How does the improvement department of a company become a hindrance to the transformation? The author answers this question and discusses how this can be avoided.
Words: Maria del Mar Revelo
The role of the continuous improvement department in a lean transformation cannot be understated. It provides teams with direction, guidance, and support – both emotional and practical. However, in some cases, improvement areas are responsible for generating the very same waste they set out to eliminate. On these occasions, they end up representing an obstacle to the successful implementation of Lean Thinking.
In this article, we will discuss why this happens and how you can avoid it.
FOCUS ON QUANTITY INSTEAD OF QUALITY
A common mistake of improvement teams is to try and “cover” many areas at once, prioritizing the speed of the implementation over the quality of the initiative and the pursuit of maturity in the journey. With such a focus on quantity, the transformation often turns into a corporate race to show volume, seeking productivity gains without considering whether the changes implemented truly create value for the end customer. This is nothing more than Taylorism disguised as lean.
This approach can result in overproduction (training hours, involved areas, conducted kaizen events, chatbots, etc.), disconnecting from the true purpose of a transformation, which is to link up the entire organization to deliver products and services in an agile manner.
BUREAUCRATIZATION OF THE WORKFLOW
Another problem that can arise in improvement areas is the segmentation of the workflow due to bureaucratic structures. When seeking improvements in individual departments or areas without considering the business as a whole and following the organization’s rigid bureaucratic structure, bottlenecks, constraints, and inefficiencies are easily generated in other parts of the organization. This results in more work in inventory processing, longer waiting times, and a generally slower workflow. Surprisingly, when the improvement department is bigger in size and more powerful (for example, with a direct report to top management), they tend to centralize everything, and in the worst cases, information and knowledge are not transferred or multiplied internally.
WEAK FOCUS ON WASTE ELIMINATION
Lean Thinking seeks to eliminate waste in all forms. However, if improvement areas focus only on the allocation of resources or the implementation of new technologies without actively addressing the elimination of activities that do not add value, they risk creating more waste. Currently, with digitization efforts taking place in many organizations, it is common to find teams who consider a Power BI dashboard as the solution to all their problems, when what they’d really need is a daily management routine that systematically seeks to identify, address, and eliminate the root cause of problems.
Using Art Smalley's categorization on the four types of problems, we can say that improvement begins when dealing with Type-3 problems (improving the current standard) and Type-4 problems (Innovation). Yet, we often see improvement teams spending more than 70% of their time putting out fires (Type-1 problems) and trying to reach the standard (Type-2 problems), which should be the responsibility of the leaders in each department instead. This has led to confusion about what improvement is and, worse, to its outsourcing, disconnecting leaders from their true purpose and role.
HOW TO OVERCOME THESE OBSTACLES
So, what can you do to prevent your improvement areas from becoming an obstacle to change? It is essential you adopt a more strategic and holistic approach, keeping the following in mind.
FOCUS ON CUSTOMER VALUE AND THEIR JOURNEY
Regardless of the model you use, connecting everything you do with value for the user and/or end customer is crucial. Furthermore, associating each action with the overall business problem is essential to prioritize and make sense of the work of improvement teams.
TRANSFER KNOWLEDGE
Promote the transfer of knowledge, set aside ego, and accept once and for all that the intention is not for the improvement area to shine, but allow others to shine. Their role is to help leaders across the organization who are generating value to achieve their results in a simpler way and relying on a lean approach.
BE LEAN INSIDE AND OUT
It is totally incoherent to say you are “lean” if your improvement area behaves in the opposite way. You need to engage in reflection (hansei) and ensure you have an internal improvement plan. Measuring the time spent on each type of problem is crucial to avoid falling into the trap of doing other people’s work and losing sight of the goal. More gemba and lean coaching and less Excel sheets and boring meetings. Also, more addressing of small problems and less huge, never-ending projects.
Finally, we can’t ignore the all-important role of management in defining the role of the improvement area. Top leaders should promote the transfer of knowledge, clarify what the improvement team should not do, and even promote the idea that, in the future, the organization should develop the ability to improve without depending on an improvement team or area.
THE AUTHOR
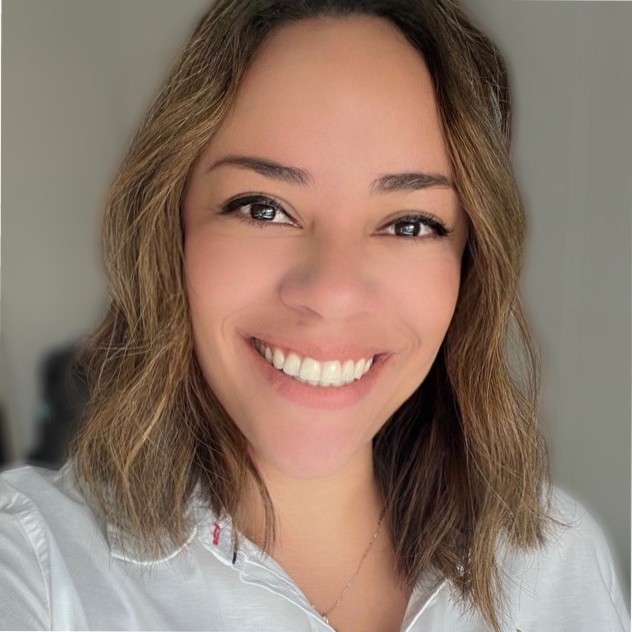
Read more
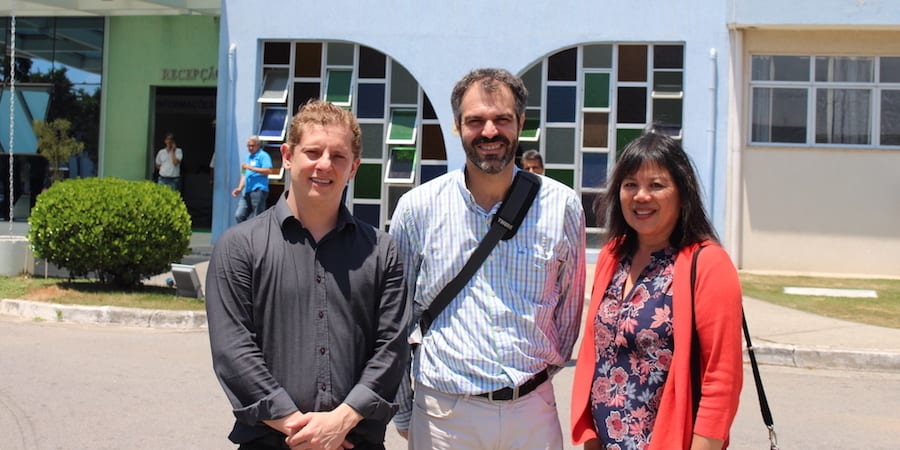
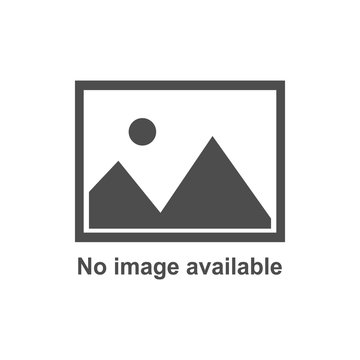
VIDEO INTERVIEW – Last year, the Lean Global Network launched an initiative to leverage the knowledge of our institutes to positively impact the healthcare industry. We caught up with the group in São Paulo this week.
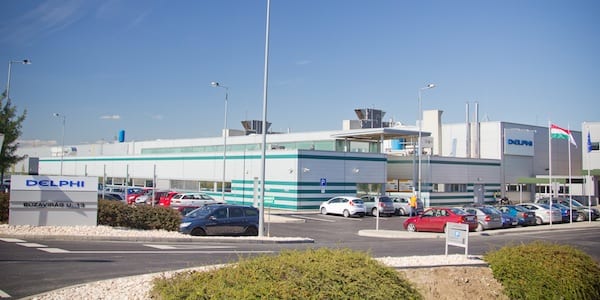
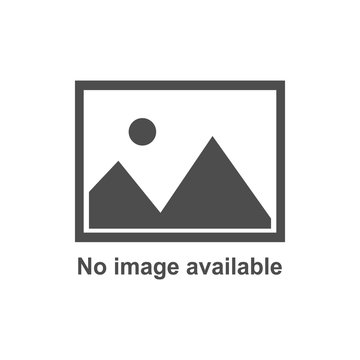
INTERVIEW - The General Manager of a Delphi plant in Hungary talks about the lean transformation the site went through and the challenges automotive suppliers face in this day and age.
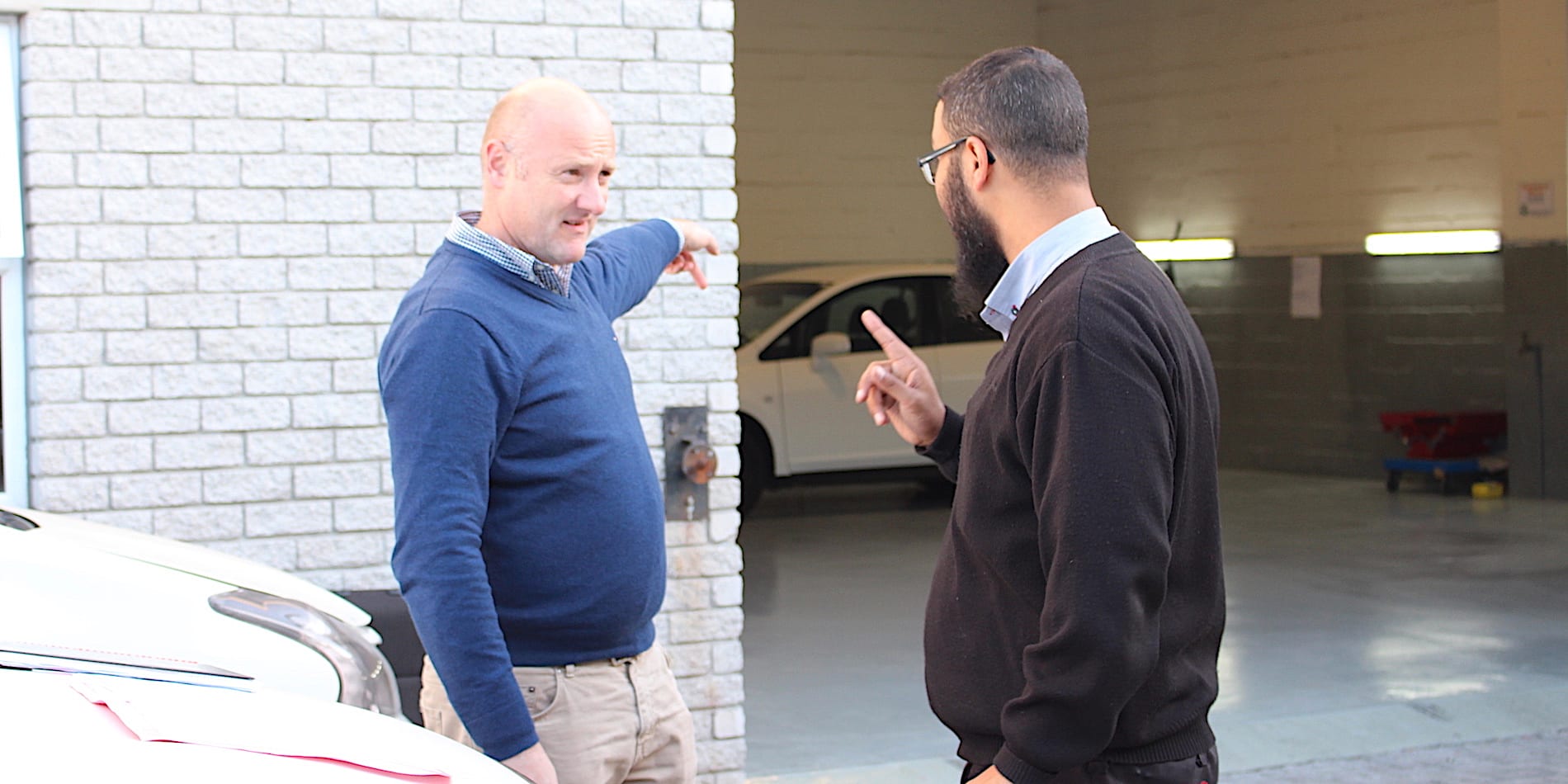
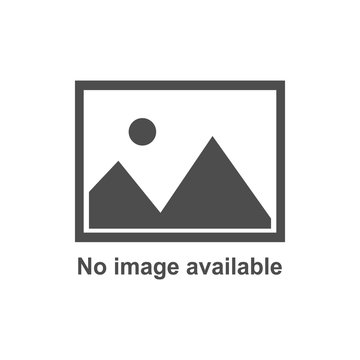
FEATURE – The role of the coach in a lean transformation is an often-debated topic. The author discusses his experience building the architecture of the Halfway turnaround.
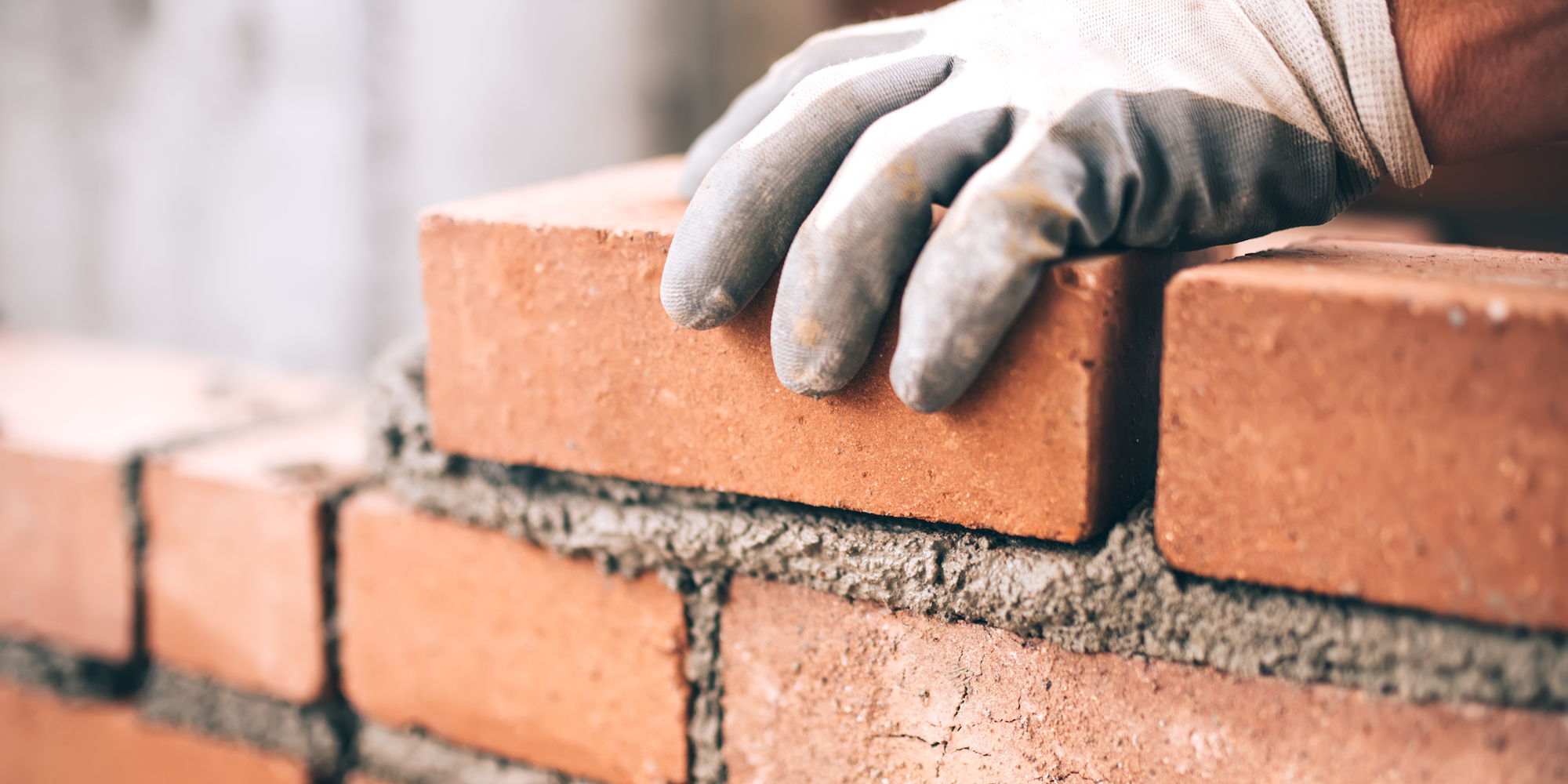
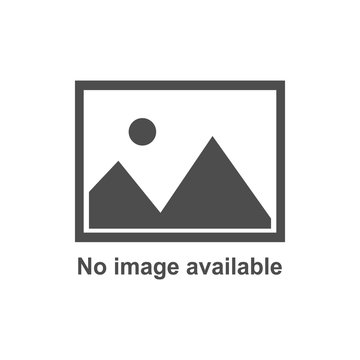
INTERVIEW – The editors of Planet Lean and Lean Post recently met with a senior executive of Turner Construction in New York City. Together, they discussed leadership development, respect for people, and the future of the industry.
Read more
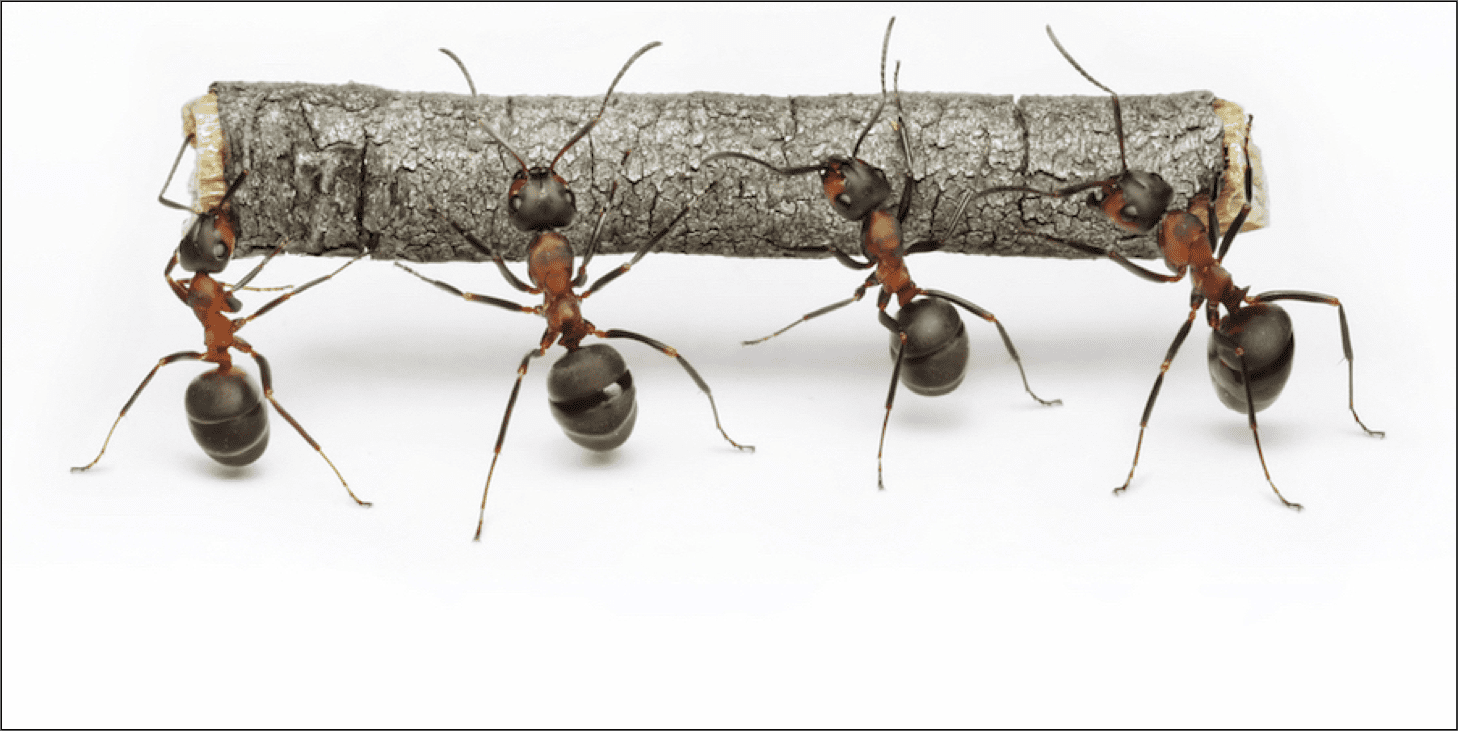
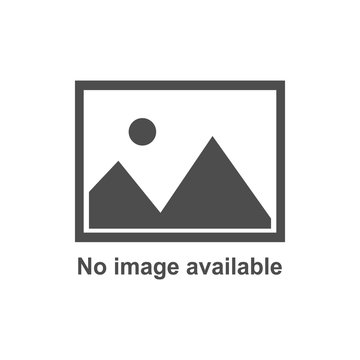
OPINION – Development managers and start-up entrepreneurs are under the illusion that innovation is just the work of especially talented individuals, but in today's world resource sharing and teamwork are preferable.
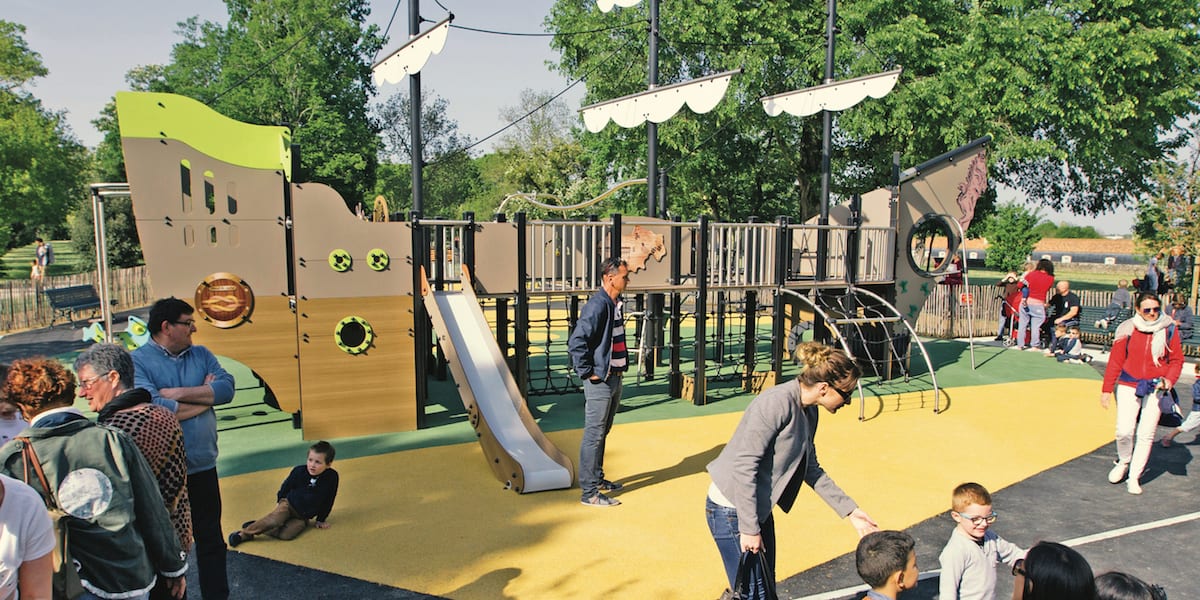
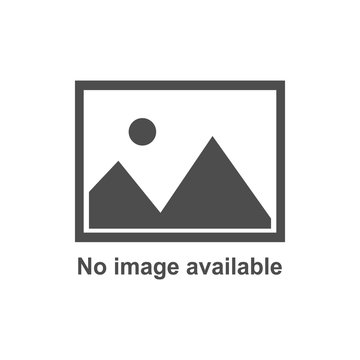
FEATURE – Enabling its people to think autonomously about problems and fostering collaboration among departments is allowing a French company that makes and installs playgrounds to thrive.
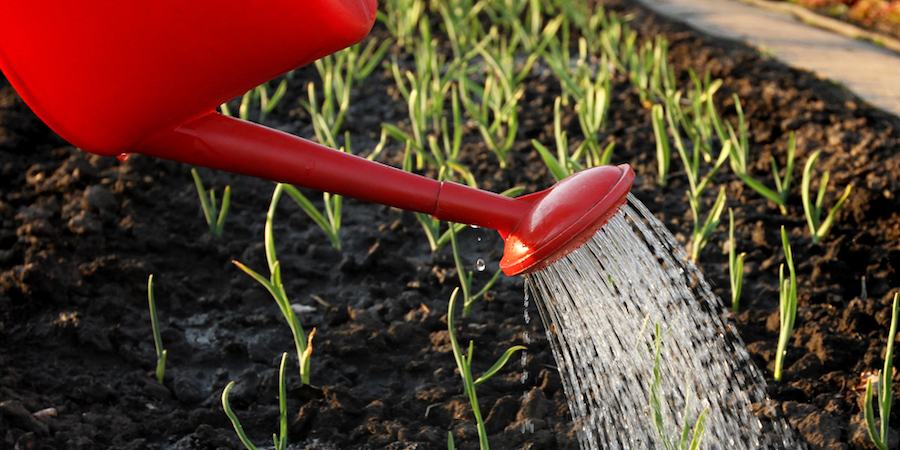
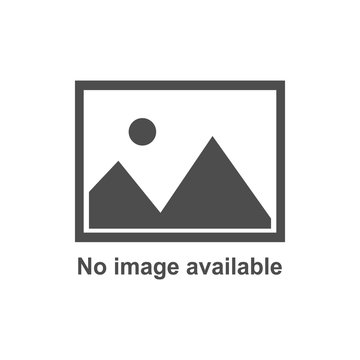
FEATURE – When middle managers are stressed and overworked, there is no time left for them to improve. Changing the interaction between leaders and teams, using lean principles and empowering people, can truly ignite your transformation.
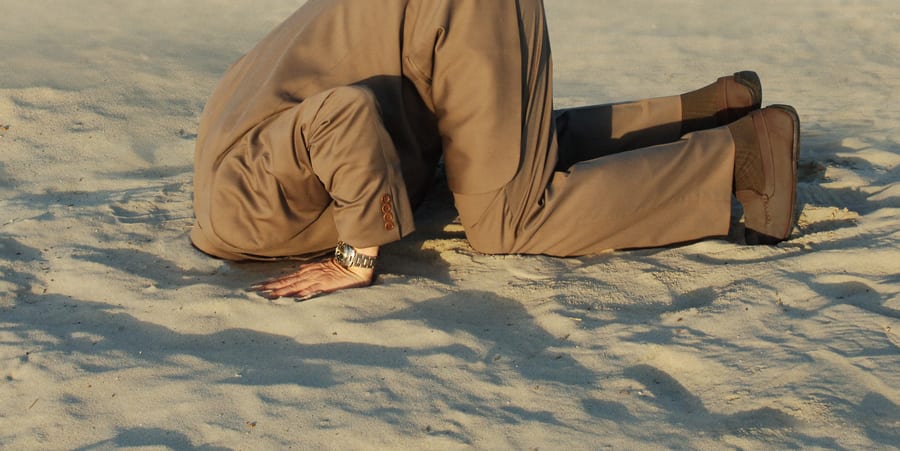
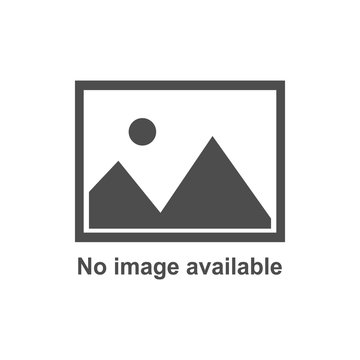
FEATURE – There are five dimensions to a lean transformation – purpose, process, people, management behaviors, and mental models – and it is the role of leadership to adjust its stance to each of them.