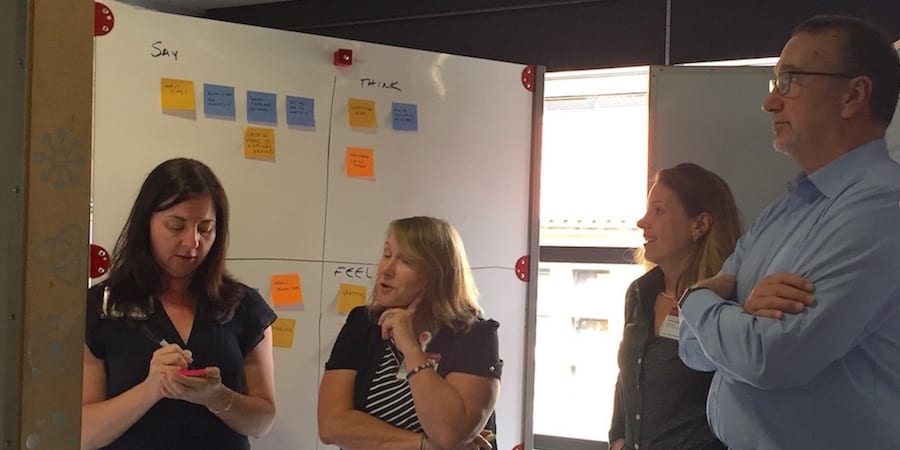
A COO at his third lean healthcare transformation
PROFILE – In this new section, Planet Lean features some of the most inspirational lean leaders out there. For the first profile, we have selected James Hereford, a former high school teacher who is now leading his third healthcare transformation.
Profile on: James Hereford, COO, Stanford Hospital and Clinics
Words: Roberto Priolo, Editor, Planet Lean
As far as career evolutions go, James Hereford’s is pretty peculiar. You just don’t hear every day of a former small-town math teacher/basketball coach working as the COO of a large healthcare organization.
“Mine was a random walk through career space,” Hereford admits, fresh off the stage at a lean healthcare conference in Brussels where he shared the lessons he learned over the past 15 years while leading three large-scale healthcare transformations.
As non-linear as his career might sound, I must say it is not too difficult to picture Hereford explaining algebra or teaching kids how to dribble. His presence is commanding (not just a result of his height) but benevolent, and his demeanor resembling that of a teacher committed to his students but humble enough to know none of us ever stops learning.
Hereford’s career began in a high school in Lewistown, Montana. He coached basketball and taught math there for seven years, until his wife and he decided to move to Seattle, where Hereford pursued his PhD in statistics at the University of Washington.
“During my first year of PhD we found out we were pregnant with our first child, and on my third year with our second. That’s when I got revenue motivated,” he says, smiling.
Hereford didn’t have to wait long for a better opportunity to come. One day in the early 1990s (he taught statistics for business in the summer months back then), the department secretary sent a note from Boeing, the plane manufacturer located in nearby Renton. The organization, which was using Total Quality Management as part of its 777 program, was looking for someone with platform skills who could teach SPC (Statistical Process Control) and DOE (Design of Experiments).
“I had no idea what any of that meant, but the job seemed to be a good opportunity, so I took it. That was such an odd, pivotal time in my career. What really attracted me was the idea of putting simple statistical tools in the hands of the people actually doing the work and having them manage their own quality,” Hereford explains.
Hereford soon began consulting with Boeing suppliers to help them meet the company’s standards and strict requirements. It so happened that one of his clients was Group Health, a healthcare organization in Seattle providing care to some 600,000 people. The then VP of Quality soon asked Hereford to join the organization and help them implement TQM, and at that point the math teacher from Lewistown got intrigued.
He recounts: “I was so naïve about healthcare at the time and didn’t know much about it, but I had loved the people I had interacted with. So smart, so mission-oriented. I thought I’d stay in healthcare for just a bit, to learn more about it. Twenty-five years later, I am still here.”
After TQM was introduced (not an entire success, which Hereford blames on his own “sheer stupidity” for not managing to connect the pursuit of quality with the group’s management system), Hereford helped lead the implementation of the electronic medical record and the construction of a call center, among other projects. His career within Group Health followed a more traditional trajectory, which led him to become responsible for quality, technology, human resources and strategy within a few years. He had people, technology and process functions reporting to him. He calls it “the dream job.”
That’s when Group Health’s COO and CEO asked him to lead an effort around cultural change.
Hereford had been keeping his hand into quality improvement, reading a lot and watching closely what was going on at Virginia Mason in those years. He soon became convinced that lean was a game-changing approach. Studying and embracing its principles ultimately gave him a better understanding of the management system, and of its interaction with the improvement system.
That’s when Hereford’s career took another fortuitous turn. In 2011, he left Group Health to take on the role of COO at Palo Alto Medical Foundation, while more recently he became COO of Stanford Hospital and Clinics.
LESSONS LEARNED IN THREE TRANSFORMATIONS
Hereford is convinced that healthcare is by far the most complex environment one can work in. Even compared to Boeing.
“Both at a plane manufacturer and in a healthcare organization, the ultimate goal is to keep people safe, but in healthcare this need is more immediate. Because patients go to a hospital when they are not well, the complexity of what we do to them, for them and with them is absolutely daunting,” he explains.
Healthcare, he continues, is both very capital intensive and very labor intensive. While the purchase of new equipment on a shop floor will often result in a decrease in human labor, installing a new MRI machine in a hospital will lead to the hiring of extra professionals who are able to use it. That’s what makes healthcare so complex: it is a socio-technical system.
There’s more. Healthcare is a unique service environment (and one that is heavily regulated and highly litigious, at least in the United States), and for it to improve the patient has to be involved and their expectations integrated into the decision planning process (relative risks they want to assume, treatments, path of care, and so on).
It’s by managing this sort of complexity that, over time, Hereford has become an example of successful lean leadership for many in the healthcare community.
Each of the transformations he led taught him something different.
At Group Health, Hereford developed a deep understanding of how continuous improvement relates to an organization’s management system, both from a daily management perspective and a hoshin perspective.
At Palo Alto Medical Foundation, he learned how to spread lean across an organization. “You need to let people put their fingerprint on the improvement activities they carry out. At PAMF, we were able to spread much more capably because we allowed each site to tailor the system to their own circumstances, which is what Toyota does with its plants,” he says. “My time at PAMF also helped me to develop trust in people.”
At Stanford, where Hereford is experiencing an even higher level of complexity (as an academic institution, the organization cares for patients, but also teaches and researches), he is learning that there is always a very specific set of initial conditions that allow a transformation to succeed. These initial conditions are critical and must be taken into account when designing a transformation strategy.
“There is another learning, which I have reinforced in all three transformations: the importance of the partnership between physicians and operations and the fact that the lean system you put in place must be designed to allow people to create value within it,” he continues.
LEADERSHIP LESSONS ON THE BASKETBALL COURT
Most leaders interested in lean have to learn how to become teachers, a very difficult process not everybody is able to complete. Hereford learned to be a teacher right at the beginning of his career, which – he admits – is an advantage.
According to him, what’s changed in his leadership style over the years is that there is less dependency on the rational part of the brain and more openness towards accepting people for where they are at and helping them progress from there.
“In many ways, I think I have learned all the most important lessons about leadership by being a small-town basketball coach in Montana,” he comments. “My job as a teacher was to help students progress, no matter their starting point. My job today is exactly the same: to help people progress. If they don’t, it’s on me.”
If Hereford’s experience is any indication, perhaps we should try to turn more basketball coaches and math teachers into lean leaders, or at very least begin to teach coaching skills (and of course lean principles) to executives in the world’s business schools. That would be a great way to slam-dunk those traditional management principles that too often seem to hinder our lean efforts.
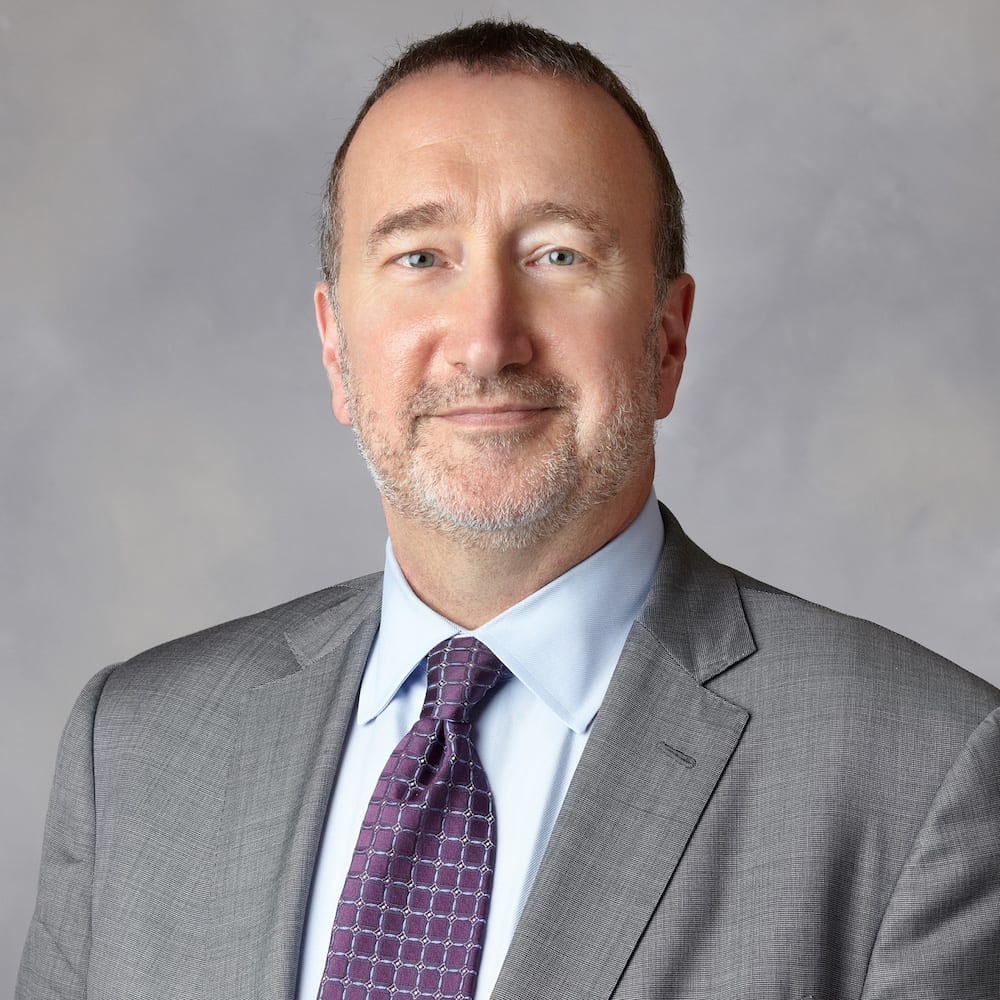
Read more
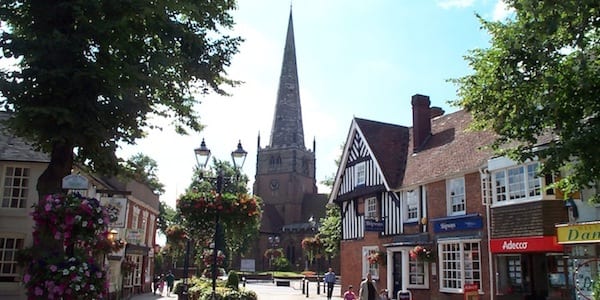
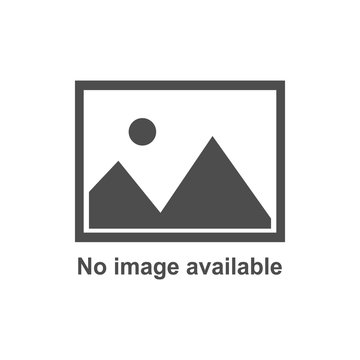
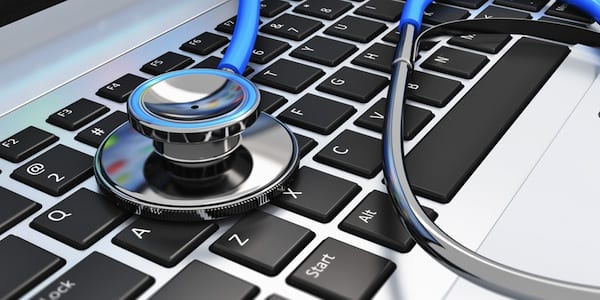
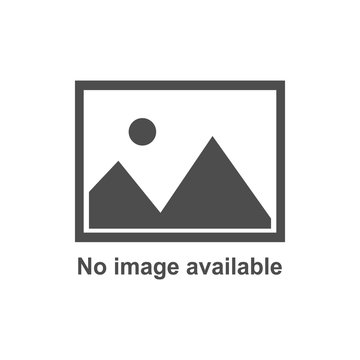
COLUMN - In the third article of our series, the CEO of a healthcare institution in Catalonia, Spain, discusses the implementation of lean as a mindset that has its foundations in continuous improvement.
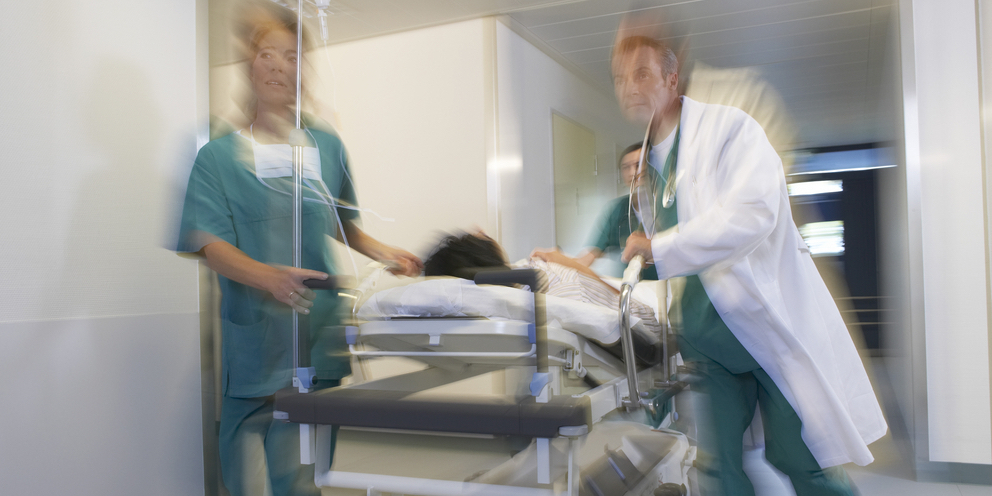
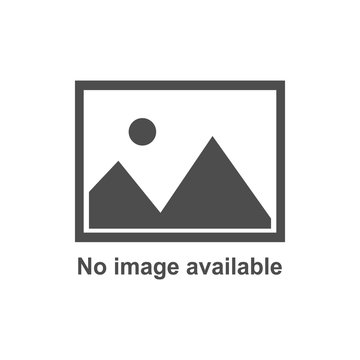
FEATURE – Our coverage of the Covid-19 emergency continues with an article discussing how lean healthcare principles can support and protect the professionals at the front line of this war.
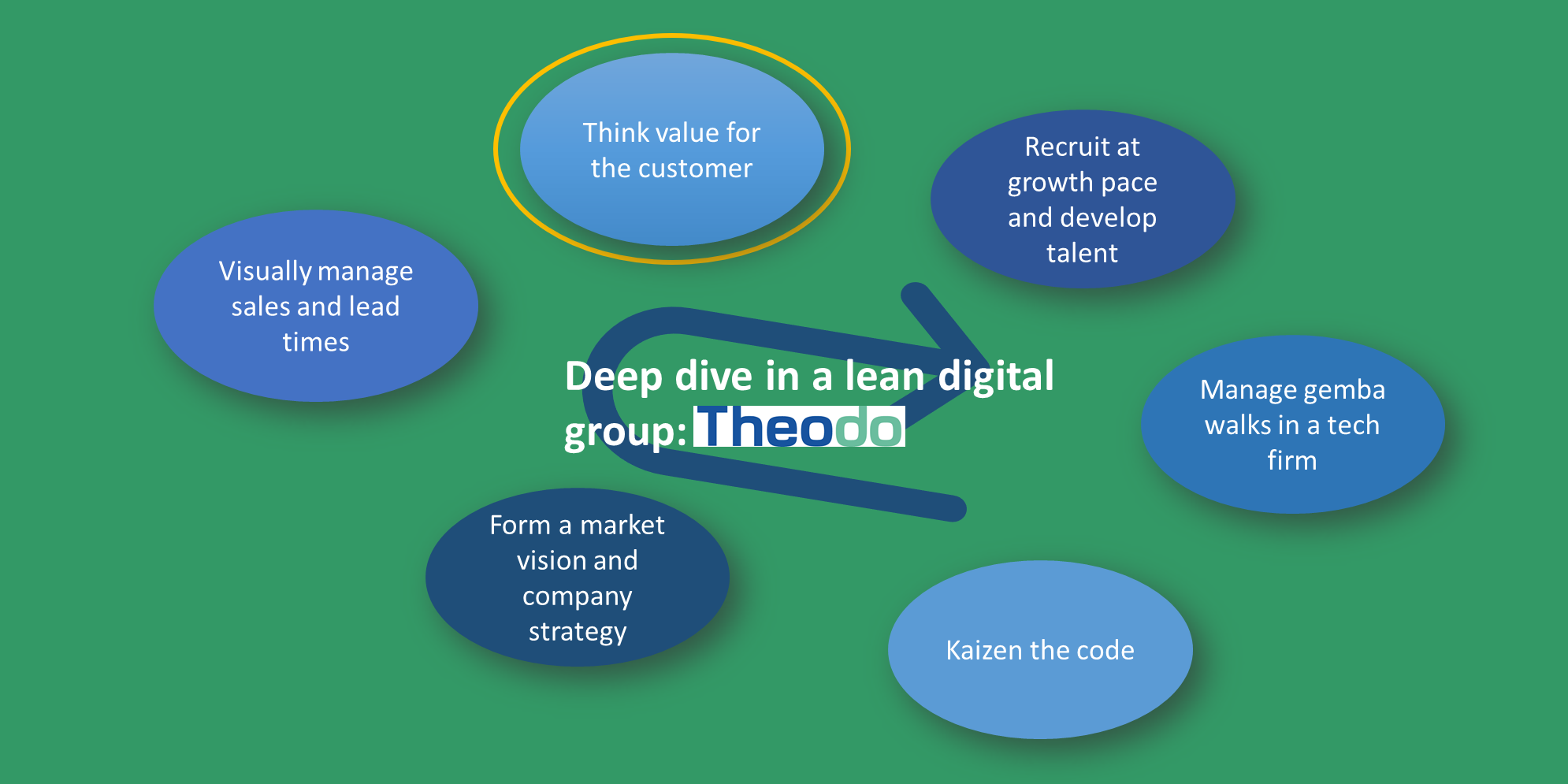
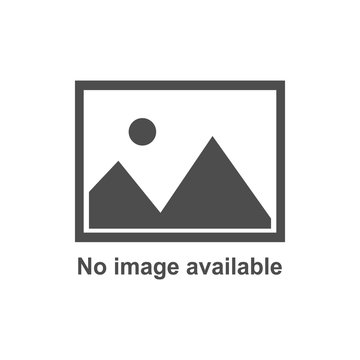
FEATURE – In the second article in her new series, the author discusses how focusing on customer value helped a fintech start-up to grow fivefold just last year.