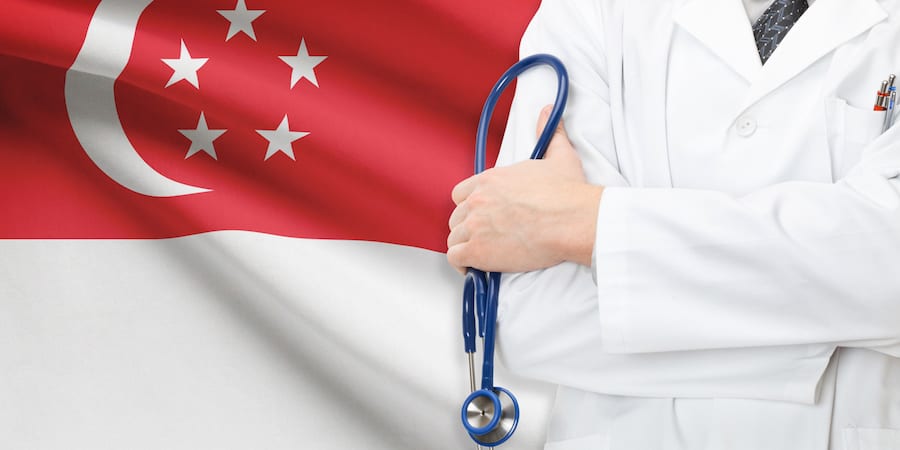
Teaching lean to secure the future of Singapore healthcare
FEATURE – After Singapore Institute of Technology staff was introduced to lean thinking, a course was launched to provide healthcare workers with the lean skills they need to transform their organizations.
Words: Dr Genedine Lim, Associate Professor of Health and Social Sciences and Programme Director of Nursing, Singapore Institute of Technology
In 2000, the World Health Organization ranked Singapore’s healthcare system as number 6 in the world. In 2014, Bloomberg deemed it the most efficient in the world; the following year, it said Singapore is the healthiest country in the world. Indeed, our country is widely recognized to have a good healthcare system that provides high-quality care to its citizens.
The fact the Singapore ranks high in a number of indices, however, does not mean we are not facing any challenges. The main one we have is meeting the healthcare needs of an aging population: in 2015, there were 460,000 Singaporeans aged over 65, a number that is projected to grow to 610,000 by the year 2020 and to 960,000 by the year 2030. Combined with a rise of chronic diseases, this will lead to a higher demand for healthcare and aged care services, requiring Singapore’s healthcare system to transform itself to retain its responsiveness and ability to produce good outcomes for patients.
To enable such transformation, in 2016, the Ministry of Health and Workforce Singapore formulated the Healthcare Manpower Plan 2020: Caring for the Nation, Transforming Tomorrow’s Healthcare. Among other things, underpinning the past and current success of the Singapore healthcare system is its formidable workforce. Hence, in his foreword, Minister for Health Gan Kim Yong highlighted that, given the challenges posed by a rapidly ageing population, healthcare professionals will need to develop new skills and to learn to leverage technology to innovate and chart new frontiers in healthcare delivery. Only then will they be able to improve the lives of Singaporeans.
Against this ever-changing backdrop, it is clear that the education programs that seek to develop the knowledge and professional competencies of its graduates also need to evolve. With this mind, the Singapore Institute of Technology (SIT), jointly with the University of Glasgow in Scotland, has launched a new two-year program. One of the most important features of this program is the course called Health Innovation and Informatics, which includes learning about the principles and methods of lean and Design Thinking to inform service and technological innovation in healthcare. (The fact that we can teach lean as part of this program is a direct result of our collaboration with the Lean Global Network, which aims to not only develop lean capabilities in Singaporean organizations, but also among SIT staff, so that we ourselves can act as drivers of lean change in our city.)
A key learning outcome for the course is to move from quality improvement to value creation. Hence, to enable the students to have a good understanding of the "value" that nursing brings into the healthcare system and how this can be enhanced continuously to bring about cost-effective and patient-centered care, the following key lean principles and methods were taught to the class: PDCA, value stream mapping, and waste elimination.
The program also aims to develop among its graduates the following four traits, which we believe will give our students the ability to lead healthcare innovation into the future and positively contribute to addressing Singapore’s healthcare needs:
- Thinking Tinkerers – we want our students to not only be passionate about hands-on experimentation, but to also be able to think and apply the knowledge gained in the process. Through on-the-job training and classroom learning, we want them to be constantly looking to improve things and solve practical problems with innovative solutions.
- Able to Learn, Unlearn, and Relearn – they will embrace change and continue learning beyond school, aware of the fact that new knowledge leads to new opportunities.
- Catalyst for Transformation – they will be able to affect change by increasing efficiency and creating value through innovation. SIT graduates seek to understand their organizations at the process and system levels, and find ways to improve their efficiency. They also bring in new ideas or create new products and services to pursue growth opportunities.
- Grounded in the Community – in the wider Singapore scenario, our students work together across various disciplines to engage with their communities and understand their needs in order to make improvements that really impact them from a social, economic and environmental standpoint.
The Health Innovation and Informatics course covers the use of technology and how lean and Design Thinking can support innovation in healthcare. During it, students undergo 36 hours of face-to-face teaching with their faculty members, followed by a project that asks them to apply what they learned in the classroom into the real-world setting of their healthcare organizations. In the last academic year, 54 students formed sub-groups and undertook projects in their organizations: they applied the principles and techniques they had learned to innovate the provision of care – thus addressing the organizations’ current needs.
The students presented their projects to the Lean Global Network’s John Shook during the CXO Summit held at the Singapore Institute of Technology in March 2017. One of these projects addressed the following challenging clinical problem presented by a nursing home to the students: “How do we enable healthcare workers who work with patients with psychiatric conditions to comply with hand hygiene guidelines and thus support the prevention of health care associated infections (HAIs)?”
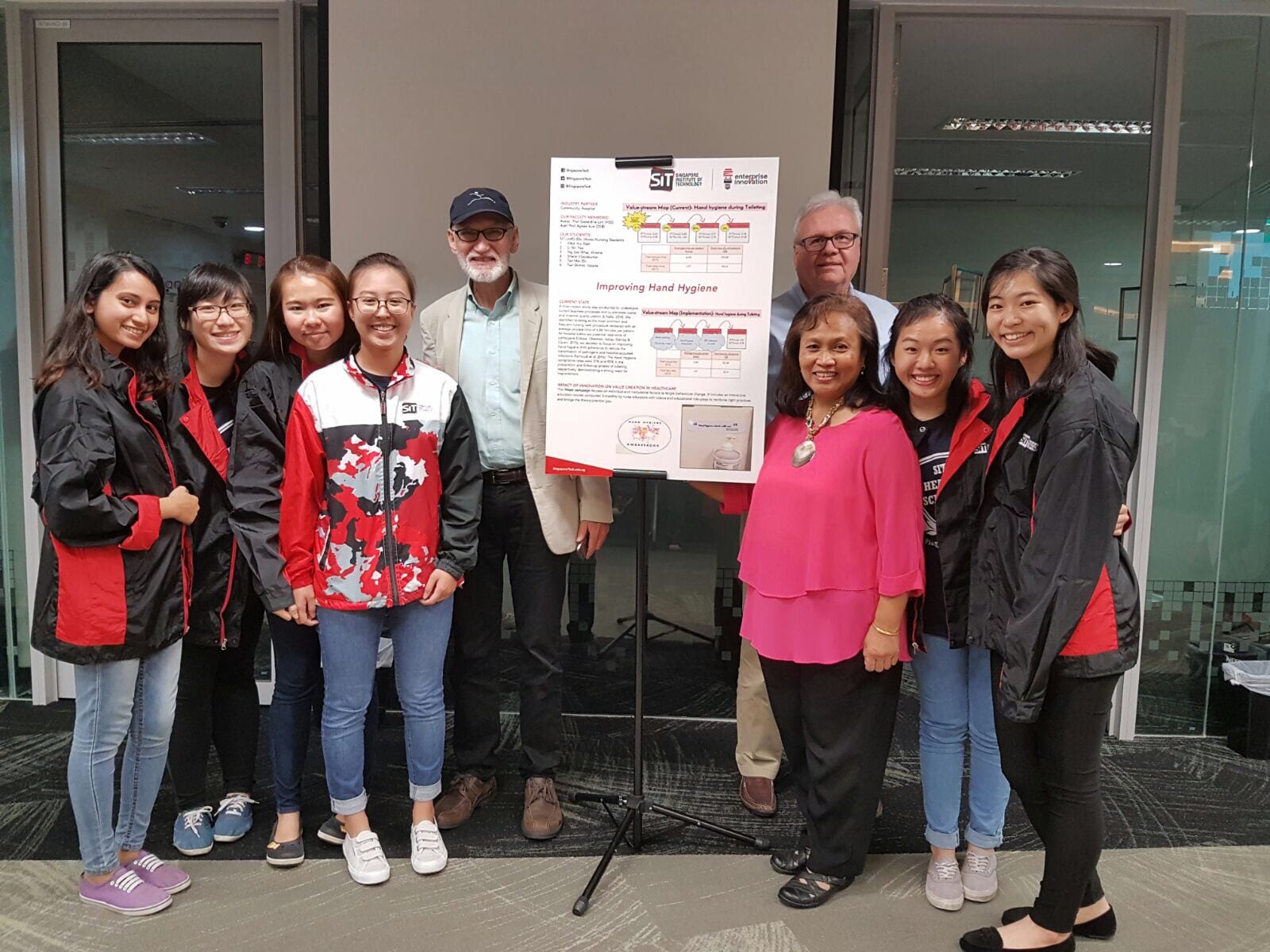
Normally, an easy way to improve handwashing among healthcare workers is to place hand sanitizer dispensers where they are visible and readily accessible. However, this could not work at the nursing home because of the risk that mental health patients might ingest the liquid. Because of this, the staff had to hide the dispensers from view, which of course made it harder for staff to see them and therefore comply with handwashing guidelines.
Using lean and Design Thinking, the nursing students worked with the staff of the nursing home to overcome this challenge. Together, they developed a value stream map of the current state and the future state of handwashing. They then proposed the development of an automated security sensor handwashing points (AHSSP) and determined where the best spots in the ward to place these would be. These locations were specifically chosen to make the AHSSPs readily available to workers while keeping them out of reach for patients. Based on these recommendations, our engineering students developed the AHSSP prototype, which is now being tested in the clinical areas.
Other projects that stemmed from the course include: a safe way to use hoists to assist with patient mobility; prevention of falls; serving meals in a safe, efficient and timely fashion; an efficient process to wash and prepare linen for patients; and safe, effective, and efficient medication administration via IT-enabled vending machines.
A few weeks ago, the Ministry of Health announced a new set of guidelines to improve healthcare productivity. These include: working with healthcare providers to streamline workflows, so that healthcare staff can better focus their time and energy on patient care; scale up the use of cost-effective technology and equipment to make work easier, especially for Singapore’s ageing healthcare workforce; and introduce innovative and patient-centric solutions, and test them in new hospital developments.
We have no doubt that, for these guidelines to be followed, lean and Design Thinking have to remain a fundamental part of the SIT-UofG Bachelor of Science with Honours in Nursing.
THE AUTHOR
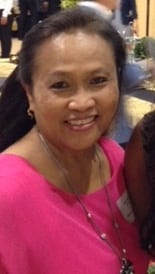
Read more
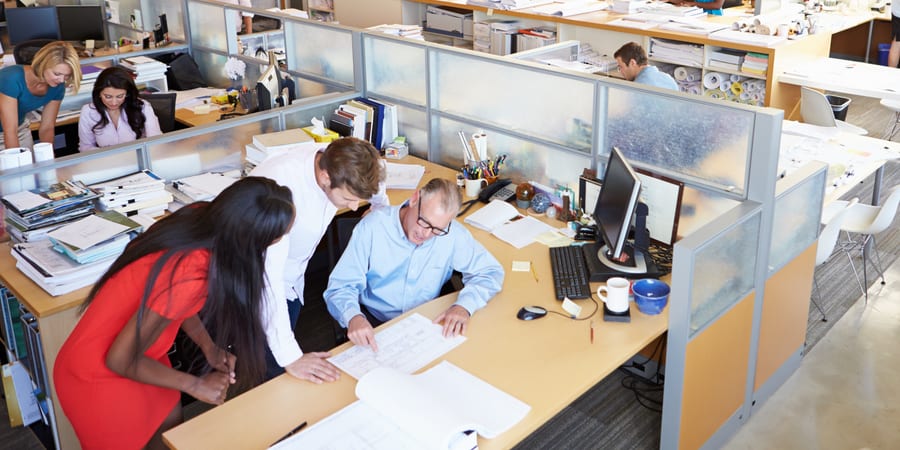
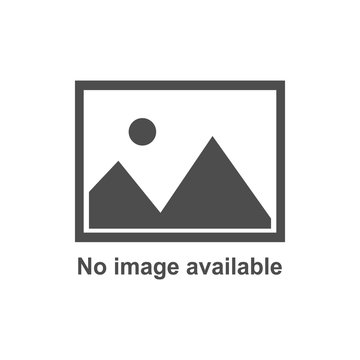
VIDEO – We constantly talk about the role of leadership, but perhaps we don't realize just how intertwined leadership transformation and business transformation really are. This short video discusses why.
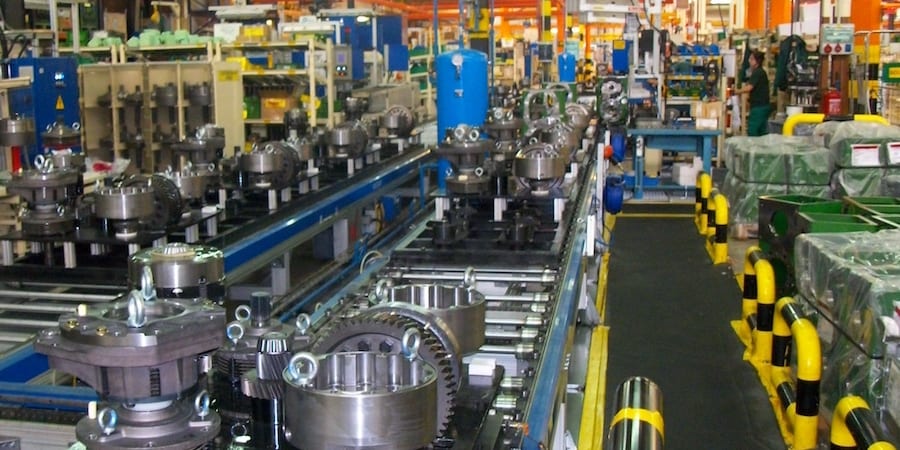
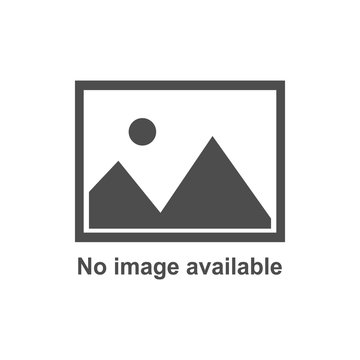
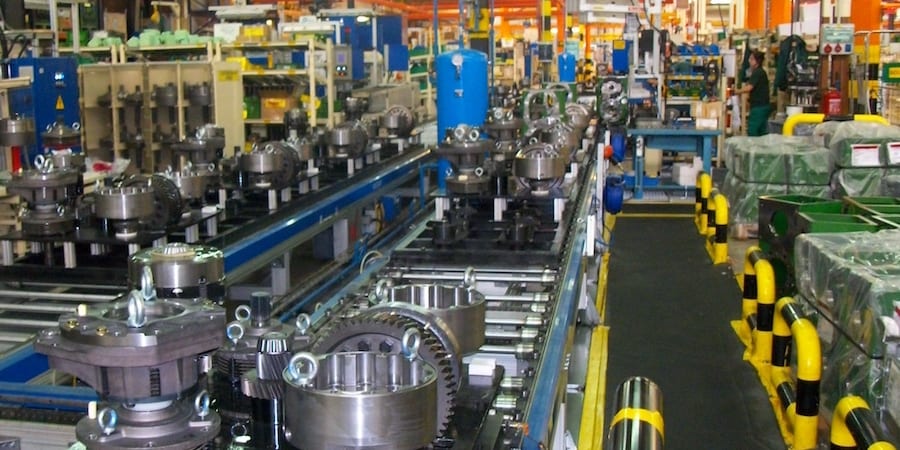
INTERVIEW – For the past year, agricultural equipment manufacturer John Deere Ibérica has worked to spread lean thinking to the supply chain. We met with them in Madrid to understand how they’re going about it.
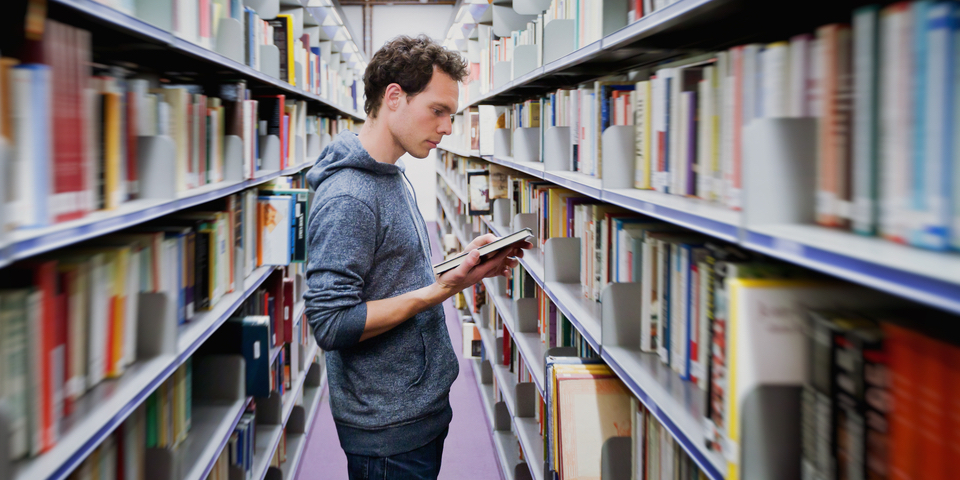
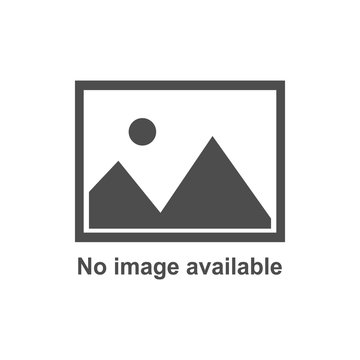
FEATURE – What can the world of lean and the world of education learn from one another? The author reflects on the synergies between these two realities.
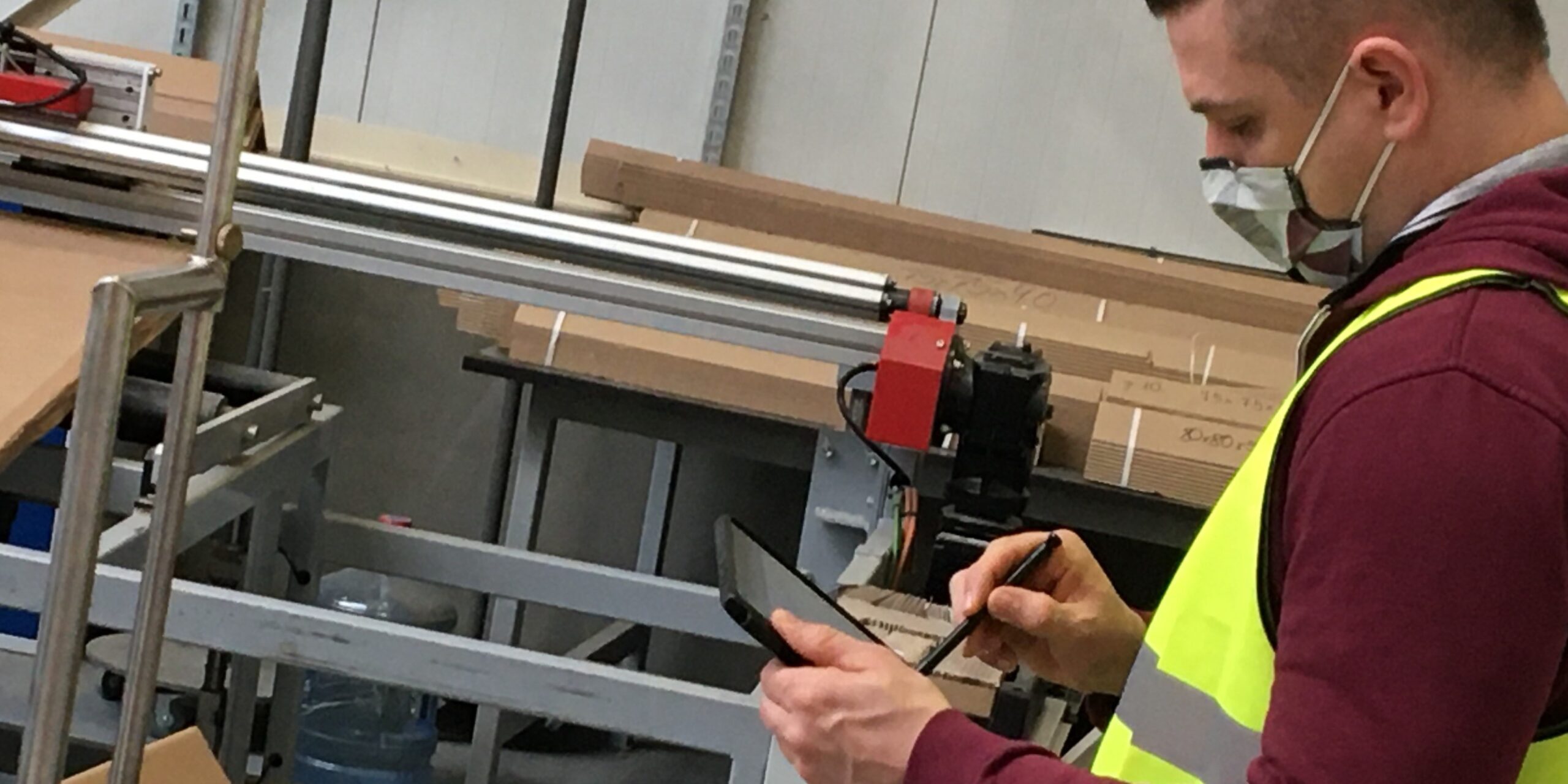
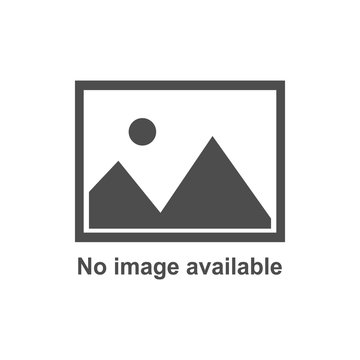
FEATURE – During a recent Jishuken workshop, Poland-based Schumacher Packaging experimented with a newly-developed App to quickly create standardized work instructions at the gemba.