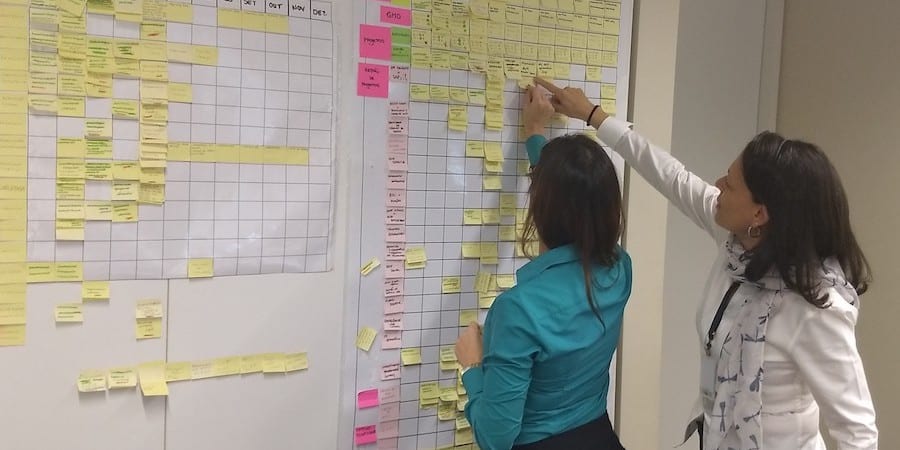
The elements of a successful lean healthcare transformation
INTERVIEW – In this follow-up conversation with the Hospital Moinhos de Vento in Brazil, we learn about the elements that are helping them to make lean stick.
Interviewee: Frederico C. Tarrago, Innovation and Process Specialist, Hospital Moinhos de Vento – Porto Alegre, Brazil
Lean Institute Brasil: Planet Lean recently ran an interview with you. Let’s remind their readers about your hospital and its lean efforts to date.
Frederico Tarrago: Hospital Moinhos de Vento (HMV) opened in Porto Alegre, Brazil in 1927. We have 500 beds for hospitalization, intensive care, and maternity. Our demand grew by almost 100% between 2004 and 2014, which has made the occupancy rate in the Inpatient Units into a big problem for us (it was constantly above the critical level of 85%).
Faced with this challenge, the hospital decided to embrace lean thinking (a number of lean experiments had begun two years prior). What we didn't expect, however, was that the results would be so impressive. The waiting time between a patient being medically cleared and discharge has been reduced by 30% (this was critical to increase patient satisfaction and reduce the bed occupancy rate), while the time of reoccupation of the bed was reduced by 33% (which generated an excellent source of incremental revenue to the hospital).
LIB: What do you consider to be the greatest learning experience you had throughout your lean journey?
FT: I am often asked whether lean can be used on a “project basis”, as a tool to improve a problematic area in an organization without really having to do all the work of creating a new culture. The answer to this question is more complex than a simple yes or no.
The hospital was introduced to lean thinking in 2012, before I joined. They achieved excellent results in a specific project in the Surgery Department. You are likely to get very good results even just by applying lean like that. There are, however, two very serious problems with this approach: first of all, there is no guarantee that the results will be sustained over time; secondly, the benefits that one loses by not embracing lean fully far outweigh whatever gain you might get. Losing out doesn’t always mean having less than you had before, but also having less than what you could have. Using lean only for individual projects is the same as traveling to Paris and spending a whole week staring at the Eiffel Tower: as imposing and beautiful as it is, after a while you would get bored. Why would you stop at the Eiffel Tower, with so many more amazing places to see in the city?
LIB: What are the essential elements of a successful lean journey?
FT: For far too long, companies have worked in departmental silos, with each manager or supervisor taking care of their own turf without worrying about parts of the organization. Too bad you can only manage a company well (and in a lean way) with a multi-functional, holistic approach. An easy way out would be to find that one superhero who can control all the elements of an organization, but unfortunately (or luckily) that person doesn’t exist. Nobody can effectively control all areas at all times. Therefore, in my mind, the success of a transformation is intrinsically linked to our ability to communicate and collaborate effectively across silos.
LIB: As lean facilitator, how did you interact with the hospital’s professionals?
FT: At Hospital Moinhos de Vento, we had a lean specialist (me) with little understanding of the work of a hospital on one side and professionals with a lot practical knowledge of the work but no understanding of lean on the other. It won’t surprise you to hear that what made our efforts successful was our team spirit. Physicians shared insights with me about patient care, medications, etc, and I shared with them the principles and practices typical of a lean organization.
LIB: Which techniques do you use to involve and engage the team?
FT: Lean thinking is not about short-term gains. To achieve a complete transformation, a cultural shift must take place. And that takes time. At the same time, it is important to remember that, as we begin our lean work in an organization, those involved in the journey are often not familiar with lean. They will lose interest if they don’t see quick results coming from the lean initiative. So, it is important to do everything we can to help them believe in change, because without them there can be no transformation. (Quick gains will also help top management engaged, which is critical to ensure buy-in.)
With this in mind, at HMV I decided to start the lean journey in the support areas, which is where I saw the biggest opportunities for quick and impactful improvements. In just 15 days, the takt time of the production line for food preparation was reduced by 40%!
These results engaged the whole team, from the lowest to the highest levels, and helped develop in people the resilience (and patience) necessary to embark on a never-ending lean journey.
LIB: Once people are engaged, they must be developed. How important is the development of capabilities in your opinion?
FT: It’s fundamental. After the first gains in the support areas, the lean journey reached the hospital's main process – the flow of patients. To make that possible, we realized that we had to develop the people involved.We began with a number of internal courses on the most fundamental lean principles and tools.
At the end of the training, the 20 “students” were responsible for delivering individual projects, which allowed us to combine theoretical learning with practice at the gemba. More groups were trained in the following years, and the results we have seen is a team that is tighter and more engaged in continuous improvement and knowledge sharing.
LIB: Knowing that a lean journey never really ends, how does one’s view of the results change?
FT: Our diligence in going to the gemba regularly, mapping processes with the PDCA cycle and the A3 process, reducing takt times, using kaizen and hoshin, and eliminating waste has allowed us to achieve many excellent results. And there is no doubt we couldn’t have gotten them without bringing all of our people together and engaging them in improving care. However, we know lean is a life-long commitment and understand that we can always do better.
Therefore, the results we have achieved so far are not the end of the road. In fact, they are not even the middle of the road. They are simply a specific point in an endless journey, something that must be clear from the very beginning (however challenging this might be).
LIB: What suggestion would you give a person who is starting their lean journey?
FT: Too many healthcare organizations give up their lean efforts after experiencing their initial struggles. Most of the time, their “failure to launch” is due to the lack of engagement of employees and, above all, of the top management. So, my number one tip for lean practitioners who are just starting out is this: if you really want to transform your organization, start by transforming the people who work on it.
Indeed, team engagement and development are vital elements of any successful lean turnaround, as are the understanding that lean is a way of thinking and acting and not just a set of tools and that embracing the methodology means to continuously pursue perfection (though it will often feel like you will never attain it). To me, the key is to see the whole and invest in people.
THE INTERVIEWEE
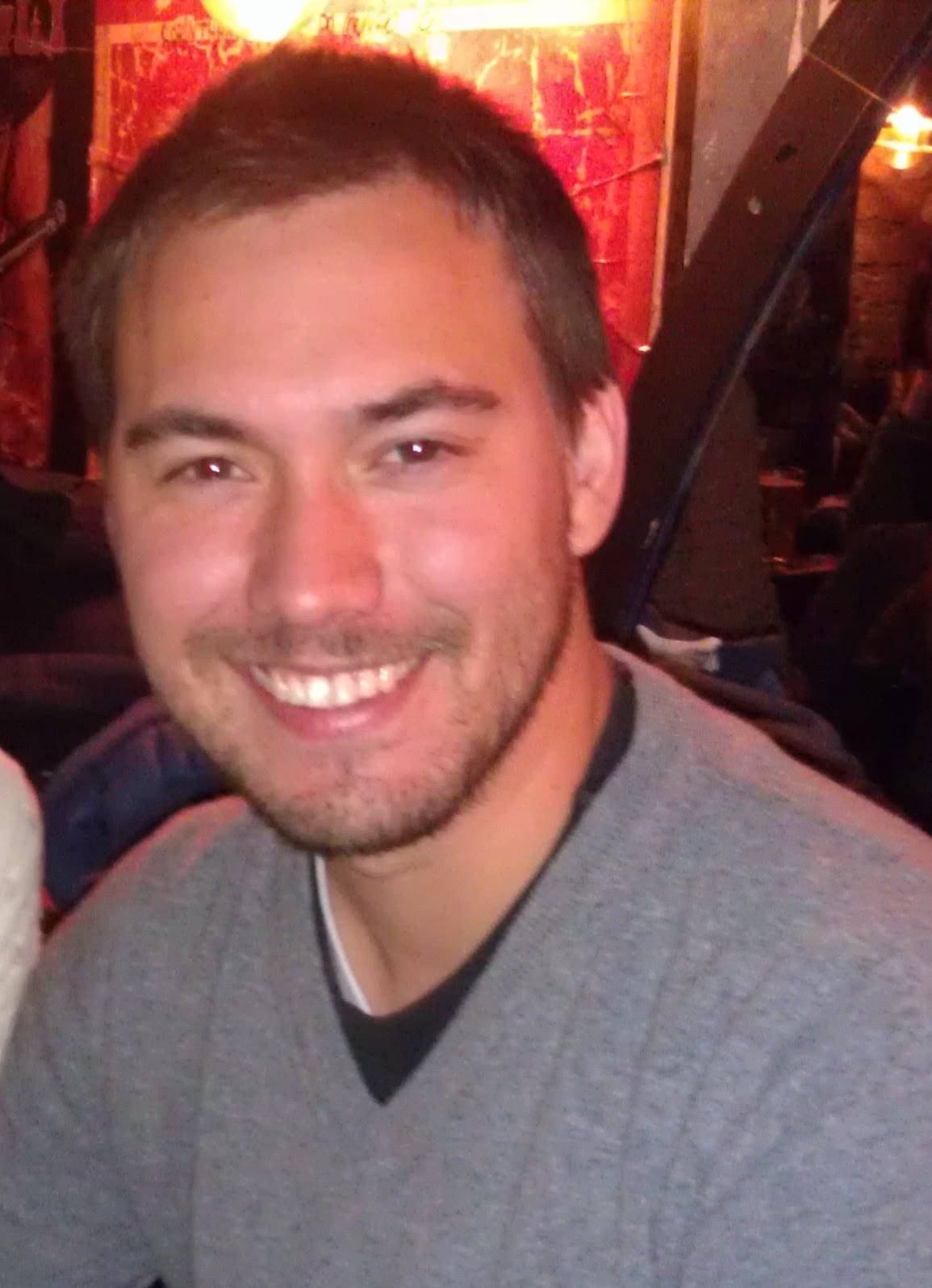
Read more
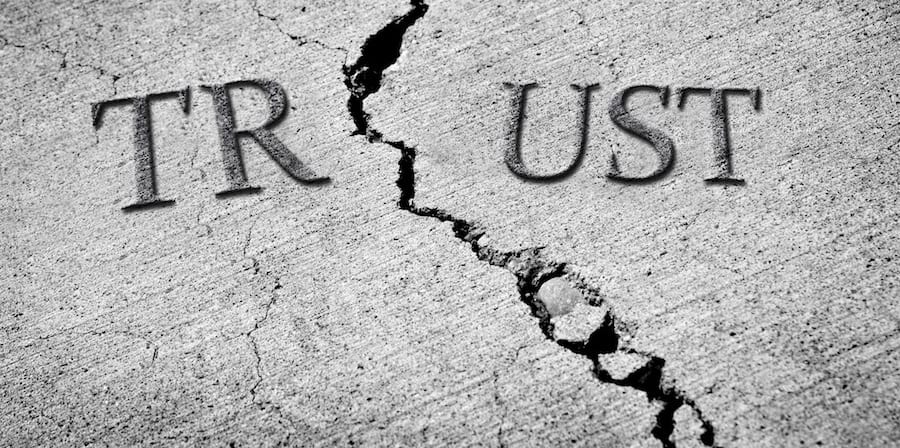
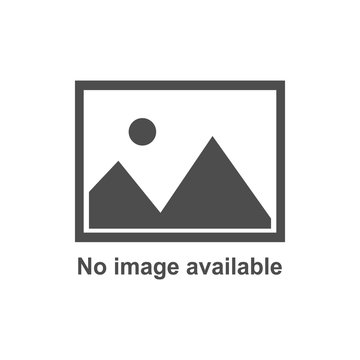
FEATURE – In this interesting piece, the author explains why living up to the ideal of mutual trust is hard, and how lean tools can help us build a workplace based on respect.
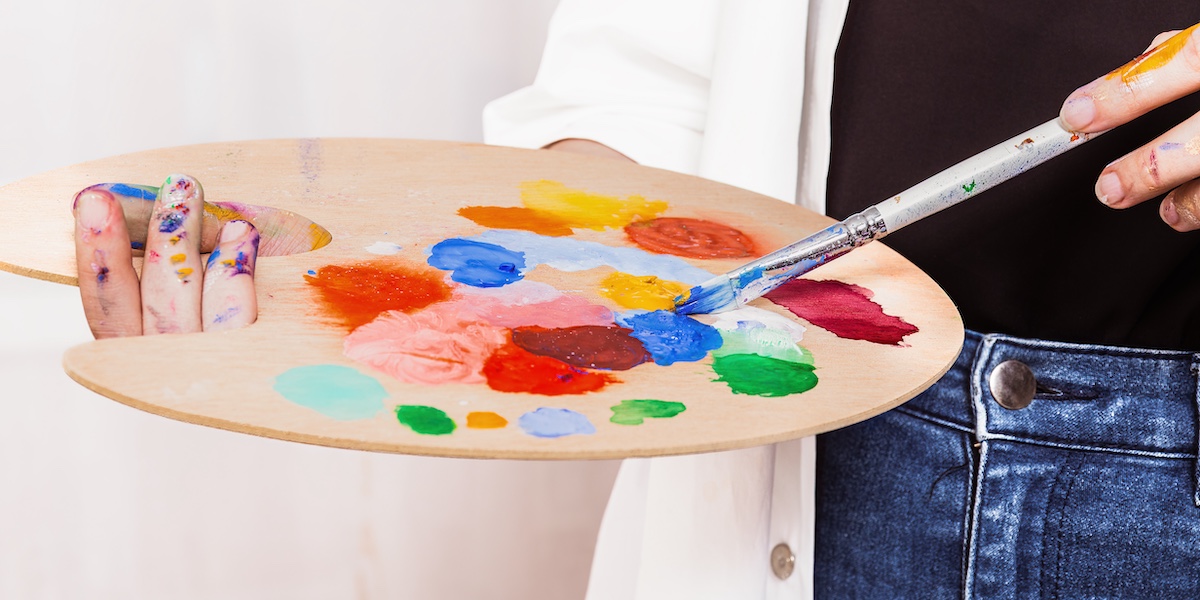
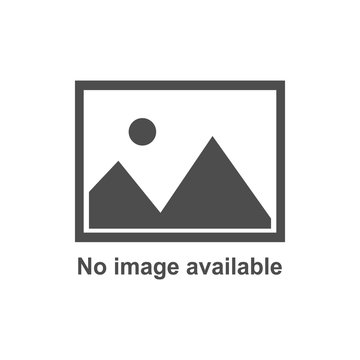
FEATURE – Embracing lean is like painting: tools are colors, respect for people is the brush, and true change blends both with intention.
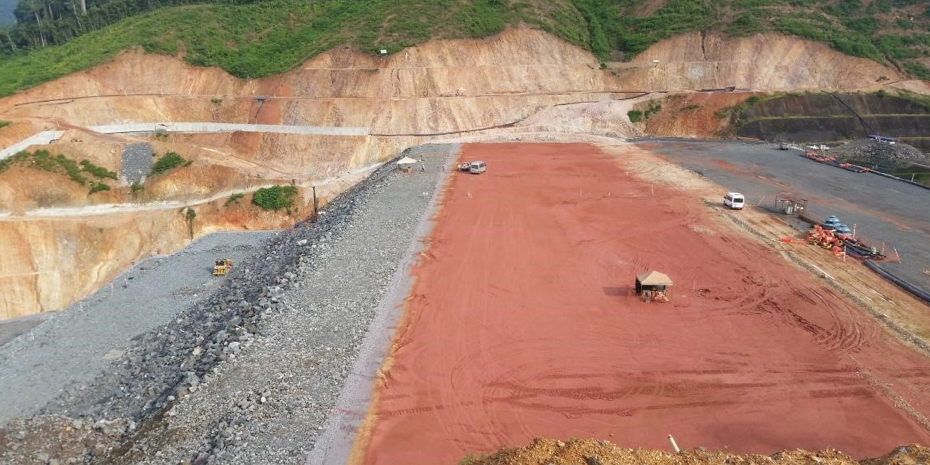
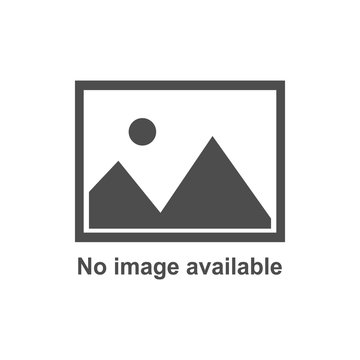
FEATURE – How lean daily management helped a Brazilian construction company to stabilize production in a tailing dam elevation project.
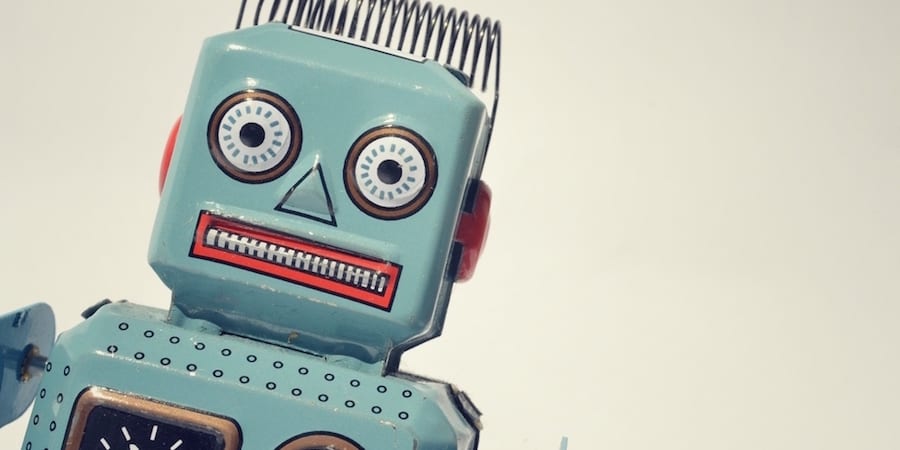
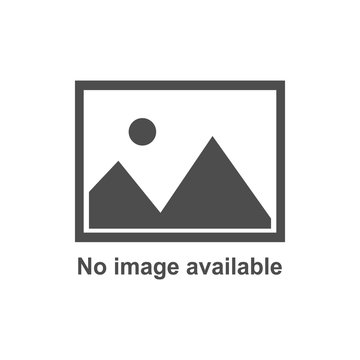
OPINION – In a competitive and unpredictable market, the temptation to rely on technology is always strong, but experience proves that there is no better support than people's ability to learn and adapt to new situations.